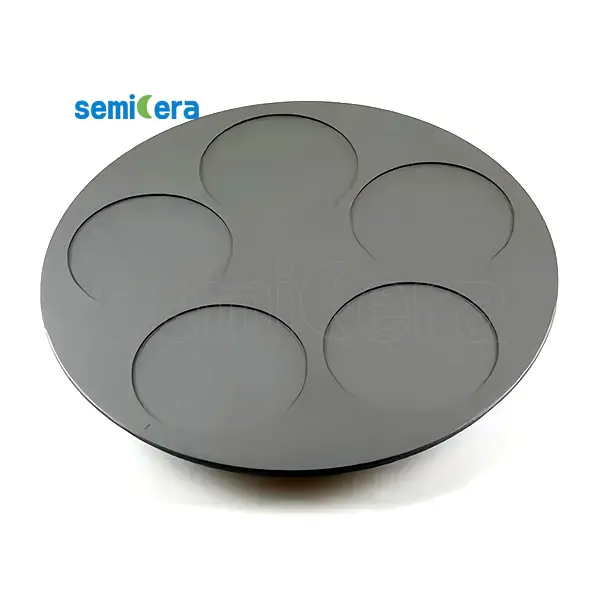
Corrosion poses significant challenges in the chemical industry. It damages equipment, disrupts production, and creates safety risks. Equipment failure caused by corrosion leads to downtime, environmental damage, and health hazards. Industry reports emphasize the financial benefits of corrosion management, with reduced costs and extended asset lifespans. Regulatory requirements further drive the need for reliable solutions.
Korea’s top five chemical companies have selected CVD SiC coating technology as their preferred corrosion prevention solution. This innovative CVD coating offers advanced properties that provide unmatched protection in aggressive environments. The effectiveness of CVD SiC coating technology reflects its ability to maintain operational efficiency and ensure long-term asset integrity, making it a vital component in the landscape of China semiconductor manufacturing.
Key Takeaways
- CVD SiC coating stops corrosion, making it great for tough chemical areas. It helps equipment last longer.
- This coating moves heat well, which is important for industries like airplanes and computer chip making.
- Using CVD SiC coating saves money by needing less fixing and cutting equipment breaks. Costs can drop by 30%.
- CVD SiC coating works on tricky shapes, giving full protection to all equipment types.
- Choosing CVD SiC coating helps the planet by cutting waste and saving energy. It’s a smart pick for today’s industries.
Understanding CVD SiC Coating Technology
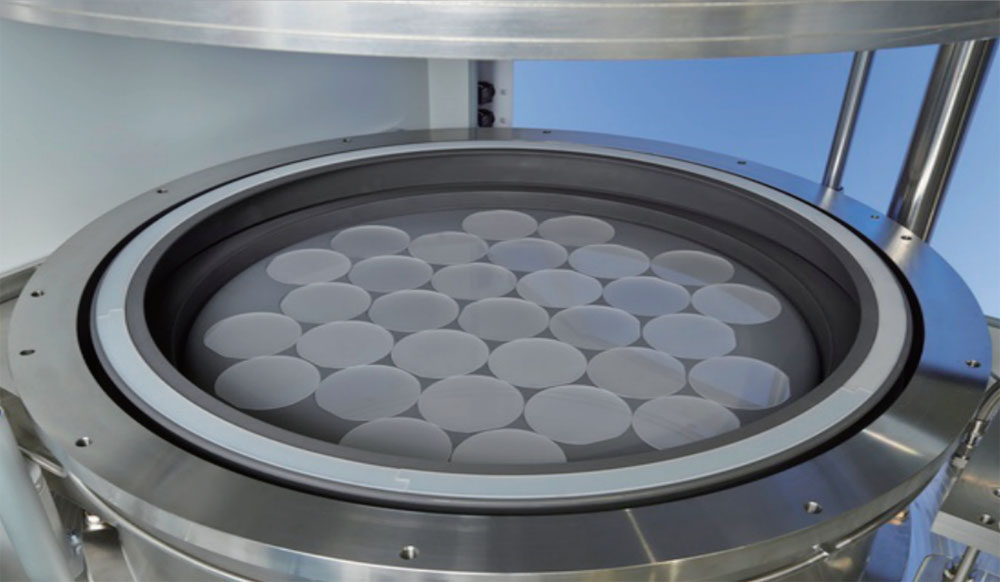
The CVD process and its role in creating SiC coatings
The Chemical Vapor Deposition (CVD) process plays a crucial role in producing high-quality silicon carbide (SiC) coatings. This method involves the chemical reaction of gaseous precursors on a heated substrate, forming a thin, uniform layer of SiC. The process ensures precise control over the coating’s thickness and uniformity, making it suitable for complex geometries.
CVD SiC coatings are widely used in industries requiring wear resistance and protection against corrosion. For example, they enhance the durability of metal cutting tools and safeguard components in harsh environments. The process also supports the creation of bulk SiC materials, such as high-purity mirrors for telescopes, demonstrating its versatility across various applications.
Key properties of CVD SiC coatings
CVD SiC coatings exhibit exceptional properties that make them ideal for demanding environments. These include:
Property | Description |
---|---|
Crystal Structure | The coating features a β 3C (cubic) crystal structure, offering optimal corrosion protection. |
Density and Porosity | With a density of 3200 kg/m³ and 0% porosity, the coating ensures effective resistance to corrosion. |
Thermal and Electrical Properties | High thermal conductivity (200 W/m·K) and excellent electrical resistivity (1MΩ·m) enable efficient heat management and insulation. |
Mechanical Strength | An elastic modulus of 450 GPa enhances the structural integrity of coated components. |
Application Process | The CVD method allows precise control over layer thickness and ensures uniform coverage. |
Research highlights that CVD SiC coatings achieve a hardness of approximately 35 GPa at room temperature. Their elastic modulus ranges from 340 to 400 GPa, showcasing their remarkable mechanical strength and stability.
How CVD SiC coating stands out from other technologies
CVD SiC coating surpasses alternative technologies in performance and adaptability. Its ability to maintain structural integrity at temperatures exceeding 1,500°C makes it invaluable in aerospace applications. For instance, Rolls-Royce’s Trent XWB engines achieve 15% higher fuel efficiency due to CVD-coated components.
In the semiconductor industry, 78% of dielectric layer applications now rely on CVD-processed films. These coatings reduce dielectric breakdowns by 40% compared to physical deposition methods. Additionally, the CVD process enables the creation of thin, uniform coatings on intricate shapes, offering unmatched versatility.
Compared to other methods like dip coating or spray coating, CVD provides superior uniformity, durability, and precision. While dip coating is cost-effective, it often results in high solution wastage and requires post-deposition treatments. Spray coating, though quick, struggles with uniformity and thickness control. CVD SiC coating eliminates these limitations, making it the preferred choice for high-performance applications.
Advantages of CVD SiC Coating
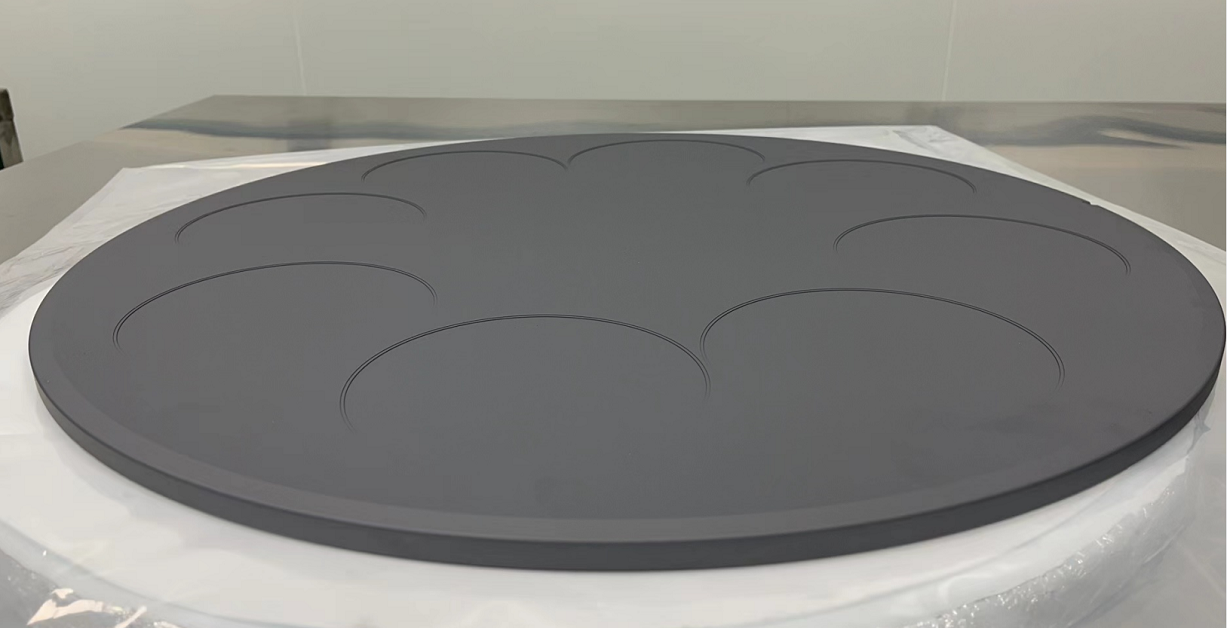
Superior corrosion resistance in harsh environments
CVD SiC coating provides exceptional protection against corrosion, even in the most aggressive chemical environments. Its non-porous structure acts as a robust barrier, preventing harmful substances from penetrating and damaging the underlying material. This feature makes it highly effective in environments where exposure to acids, alkalis, and other corrosive agents is common.
Industries such as chemical processing and power generation benefit significantly from this technology. Equipment coated with CVD SiC remains operational for longer periods, reducing the need for frequent replacements. This durability ensures uninterrupted production and minimizes the risk of costly downtime.
Tip: Using CVD SiC coating on critical components like reactors and pipelines can significantly extend their lifespan, even under extreme conditions.
High thermal conductivity and heat resistance
CVD SiC coating excels in managing heat efficiently. Its high thermal conductivity allows it to dissipate heat quickly, making it ideal for applications involving high temperatures. This property ensures that equipment remains stable and performs reliably, even when exposed to intense heat.
The coating also withstands temperatures exceeding 1,500°C without losing its structural integrity. This makes it a preferred choice for industries like aerospace and semiconductor manufacturing, where thermal stability is crucial. For example, in semiconductor fabrication, the coating helps maintain precise temperature control, ensuring consistent product quality.
Research shows that materials with high thermal conductivity, like CVD SiC, improve energy efficiency and reduce the risk of thermal damage to equipment.
Durability and adaptability to complex shapes
CVD SiC coating offers unmatched durability, making it resistant to wear and mechanical stress. Its hardness and strength ensure that coated surfaces remain intact, even under heavy usage. This durability translates to fewer repairs and replacements, saving both time and resources.
Additionally, the CVD process allows the coating to be applied uniformly on components with intricate shapes. This adaptability makes it suitable for a wide range of applications, from small, detailed parts to large industrial equipment. The ability to coat complex geometries ensures comprehensive protection, regardless of the component’s design.
Note: The precision of the CVD process ensures that every corner and curve of a component receives equal protection, enhancing its overall performance.
Long-term cost savings and reduced maintenance
CVD SiC coating offers significant financial benefits by reducing maintenance costs and extending the lifespan of industrial equipment. Its durability minimizes the need for frequent repairs or replacements, which translates to lower operational expenses over time. Companies that adopt this technology often experience a noticeable reduction in downtime, as equipment coated with CVD SiC remains functional even under extreme conditions.
The non-porous structure of the coating prevents corrosive substances from penetrating the surface. This feature reduces wear and tear, ensuring that components maintain their integrity for longer periods. For example, reactors and pipelines in chemical plants often face constant exposure to aggressive chemicals. Without adequate protection, these components require frequent maintenance, leading to increased costs and production delays. CVD SiC coating eliminates this issue by providing a robust barrier against corrosion.
Tip: Investing in CVD SiC coating upfront can lead to substantial savings in the long run by reducing the frequency of equipment replacements.
Another advantage lies in the coating’s ability to withstand high temperatures without degrading. Equipment exposed to extreme heat often suffers from thermal damage, which necessitates costly repairs. CVD SiC coating’s high thermal conductivity and heat resistance ensure that such equipment remains operational, further reducing maintenance expenses.
Additionally, the adaptability of the CVD process allows the coating to be applied to complex shapes and intricate designs. This ensures comprehensive protection for all components, regardless of their geometry. As a result, companies can avoid the hidden costs associated with partial or uneven protection.
Research indicates that industries using CVD SiC coating report up to a 30% reduction in maintenance-related expenses over a five-year period. This highlights the long-term economic advantages of adopting this advanced technology.
Applications of CVD SiC Coating in the Chemical Industry
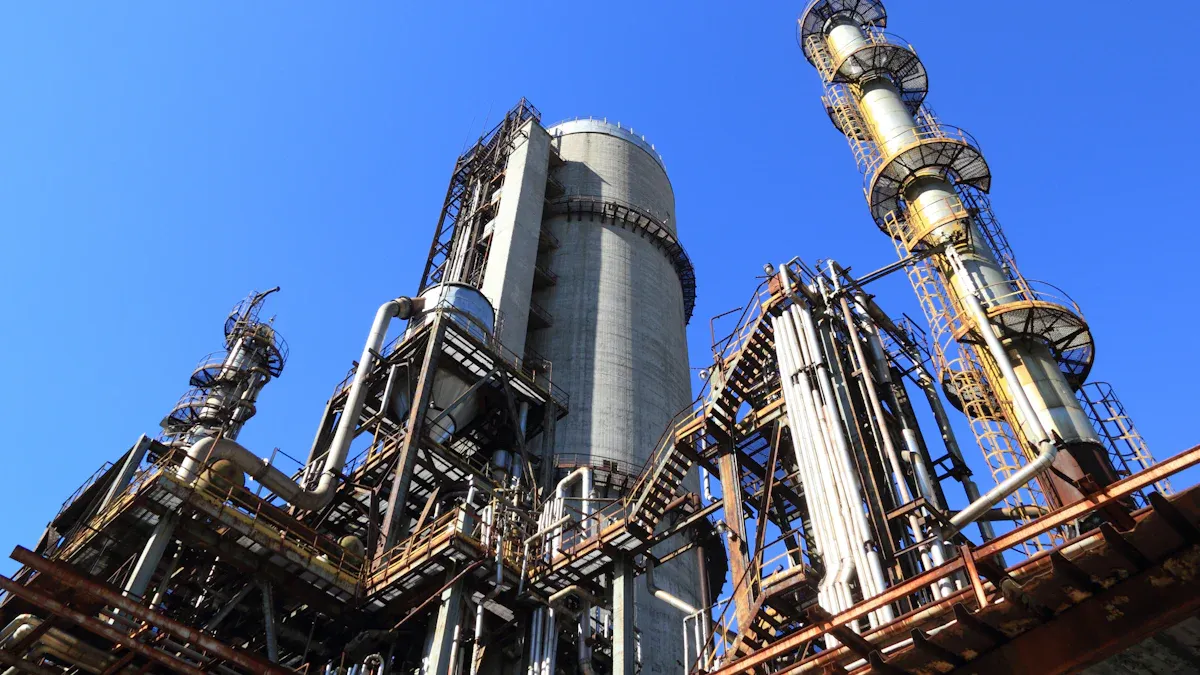
Protecting equipment in corrosive and high-temperature environments
CVD SiC coating plays a vital role in safeguarding equipment exposed to extreme conditions. Its non-porous structure and high thermal stability make it an excellent choice for industries dealing with corrosive chemicals and high temperatures. For instance, in chemical processing plants, this coating protects reactors and pipelines from acid and alkali damage. Similarly, in power generation, it ensures the longevity of components exposed to intense heat and pressure.
The versatility of CVD SiC coating extends to various sectors. The following table highlights its applications across industries:
Industry Sector | Application Details |
---|---|
Aerospace & Defense | High-performance materials for extreme conditions, such as turbine blades and engine parts. |
Automotive | Enhances durability and performance in automotive components. |
Electronics | Used in electronic devices for improved thermal stability and wear resistance. |
Energy | Applied in solar panels and energy-efficient technologies to withstand harsh environmental conditions. |
Industrial | Enhances performance and longevity in chemical processing and heavy machinery applications. |
Note: The ability of CVD SiC coating to resist both chemical and thermal degradation ensures reliable performance in even the harshest environments.
Enhancing the lifespan of reactors, pipes, and valves
Reactors, pipes, and valves are critical components in the chemical industry. These parts often face constant exposure to corrosive substances, leading to wear and tear. CVD SiC coating provides a robust barrier that prevents chemical penetration, significantly extending the lifespan of these components.
For example, pipelines coated with this technology remain resistant to acid corrosion, reducing the need for frequent replacements. Similarly, valves and reactors benefit from the coating’s durability, ensuring uninterrupted operation. This not only enhances equipment reliability but also minimizes maintenance costs and downtime.
Tip: Regularly applying CVD SiC coating to high-risk components can prevent unexpected failures and improve overall operational efficiency.
Use in semiconductor manufacturing and power generation
CVD SiC coating has become indispensable in semiconductor manufacturing and power generation. In semiconductor fabrication, it is used as a susceptor-coating material for growing high-quality 4H-SiC epilayers. Research shows that carbon-based coatings outperform SiC-coated susceptors in producing superior films, making them ideal for this application.
In power generation, CVD SiC coating enhances the performance of SiC/SiC composites. These composites, when coated with boron nitride using the CVD process, exhibit improved resistance to oxidation and crack propagation. This makes them suitable for high-temperature applications, such as gas turbine combustors.
The following table summarizes key findings from research on these applications:
Aspect | Details |
---|---|
Focus | Susceptor-coating materials for growth of 4H-SiC |
Method | CVD process for growing 4H-SiC epilayers |
Findings | High-quality SiC films produced with carbon-based coatings; SiC-coated susceptors showed poor quality and degradation. |
Conclusion | Carbon-based coatings are more suitable for epitaxial growth of high-quality 4H-SiC. |
Aspect | Details |
---|---|
Focus | SiC/SiC composites with improved boron nitride coatings |
Method | CVD for fiber/matrix interfacial layers |
Findings | Improved resistance to oxidation and crack propagation in composites due to BN coatings. |
Conclusion | Enhanced performance in high-temperature applications, relevant for power generation. |
Insight: The adaptability of CVD SiC coating to advanced manufacturing processes ensures its relevance in cutting-edge industries like semiconductors and energy.
Why Korea’s Top Chemical Companies Prefer CVD SiC Coating
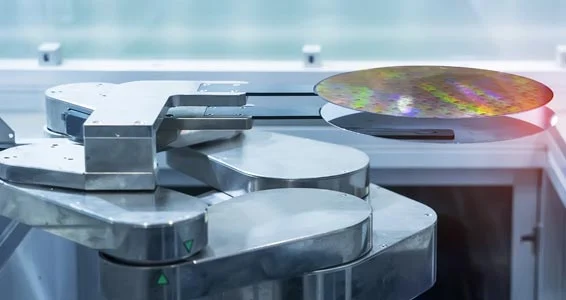
Proven performance in aggressive chemical environments
Korea’s leading chemical companies prioritize solutions that can withstand the harshest conditions. CVD SiC coating has consistently demonstrated its ability to protect equipment in aggressive chemical environments. Its non-porous structure prevents corrosive substances from penetrating, ensuring long-term durability. This makes it an ideal choice for industries where exposure to acids, alkalis, and other reactive agents is unavoidable.
For example, in chemical processing plants, reactors and pipelines coated with CVD SiC remain operational for extended periods. This reduces the frequency of replacements and minimizes production interruptions. The coating’s ability to maintain its integrity under extreme conditions has earned it a reputation as a reliable solution for corrosion prevention.
Tip: Regular application of CVD SiC coating on critical components can significantly enhance their resistance to chemical damage, ensuring uninterrupted operations.
Alignment with industry-specific operational needs
CVD SiC coating aligns seamlessly with the operational requirements of Korea’s top chemical companies. Its adaptability to complex shapes ensures comprehensive protection for equipment of all sizes and designs. This versatility allows companies to coat intricate components like valves and connectors, which are often exposed to high stress and corrosive substances.
The coating’s high thermal conductivity also supports efficient heat management, a critical factor in industries dealing with high-temperature processes. For instance, in semiconductor manufacturing, CVD SiC coating helps maintain precise temperature control, ensuring consistent product quality. Similarly, in power generation, it enhances the performance of components exposed to intense heat, such as turbine blades.
Note: The precision of the CVD process ensures uniform coverage, making it suitable for even the most intricate equipment designs.
Contribution to sustainability and operational efficiency
CVD SiC coating contributes significantly to sustainability and operational efficiency. Its durability reduces the need for frequent replacements, leading to less waste and lower resource consumption. Additionally, the coating’s high thermal conductivity improves energy efficiency in various applications.
The following table highlights how CVD SiC coating enhances efficiency across different industries:
Industry | Benefit Description | Efficiency Improvement |
---|---|---|
Coal-fired power plants | Improved heat transfer efficiency leading to reduced fuel consumption and emissions | Up to 15% |
Steel manufacturing | Energy savings through enhanced waste heat recovery | 8-12% |
Chemical processing | Extended equipment lifespan reducing waste | 60% longer service life |
Aviation | Better fuel efficiency in turbine engines | 15% better fuel efficiency |
Moreover, advancements in the production processes for SiC-coated substrates are reducing environmental impacts. These include:
- Minimizing waste and lowering carbon footprints during manufacturing.
- Improving coating quality through advanced chemical vapor deposition methods.
- Developing recycling initiatives to create a circular economy for SiC technology.
Life cycle assessments also reveal that SiC components can significantly lower energy consumption and greenhouse gas emissions in applications like electric vehicles. These sustainability benefits align with the global push for greener industrial practices, making CVD SiC coating a forward-thinking choice for Korea’s chemical companies.
Insight: By adopting CVD SiC coating, companies not only enhance their operational efficiency but also contribute to a more sustainable future.
Cost-effectiveness and reduced downtime
CVD SiC coating offers significant economic advantages for industries by reducing operational costs and minimizing equipment downtime. Its durability ensures that coated components last longer, requiring fewer replacements. This longevity directly translates to lower expenses for purchasing and installing new equipment. Companies that adopt this technology often experience a noticeable reduction in their overall maintenance budgets.
The coating’s ability to resist corrosion and withstand extreme temperatures plays a key role in maintaining uninterrupted operations. Equipment failures caused by corrosion or thermal damage often lead to costly production halts. By protecting critical components, CVD SiC coating helps industries avoid these disruptions. For example, chemical plants using this coating on reactors and pipelines report fewer breakdowns, allowing them to maintain consistent production schedules.
Another advantage lies in the reduced need for frequent maintenance. Traditional coatings often degrade quickly, requiring regular inspections and repairs. In contrast, CVD SiC coating provides a robust and long-lasting solution. This reduces the time and labor costs associated with maintenance activities. Workers can focus on other essential tasks, improving overall productivity.
Industries also benefit from the coating’s adaptability to complex shapes. This ensures comprehensive protection for all components, regardless of their design. As a result, companies can avoid the hidden costs associated with partial or uneven protection. The precision of the CVD process guarantees that every surface receives equal coverage, enhancing the reliability of the equipment.
Tip: Investing in high-quality coatings like CVD SiC can lead to long-term savings by reducing the frequency of equipment failures and maintenance needs.
Research shows that industries using CVD SiC coating report up to a 30% reduction in maintenance-related expenses over a five-year period. This highlights the coating’s potential to deliver both immediate and long-term financial benefits. By minimizing downtime and extending the lifespan of equipment, this technology proves to be a cost-effective solution for modern industries.
CVD SiC coating technology has revolutionized corrosion prevention across industries. Its unmatched durability, thermal stability, and adaptability make it indispensable for protecting equipment in harsh environments. From aerospace to semiconductor manufacturing, this coating enhances performance, reduces maintenance, and supports sustainability. The global market growth reflects its increasing adoption, driven by advancements like chemical vapor deposition. Korea’s top chemical companies recognize its value as a trusted solution, ensuring operational efficiency and long-term cost savings.
Application Area | Benefits |
---|---|
Aerospace | Enhances turbine blade performance in high-temperature, corrosive conditions. |
Energy | Extends the lifespan of renewable energy components, improving efficiency. |
Semiconductor | Enables devices to operate at higher temperatures and voltages, crucial for modern systems. |
The adoption of CVD SiC coating aligns with the industry’s shift toward eco-friendly practices, making it a cornerstone of sustainable innovation.
FAQ
What is CVD SiC coating technology?
CVD SiC coating technology uses chemical vapor deposition to create a thin, uniform silicon carbide layer. This coating protects equipment from corrosion, heat, and wear, making it ideal for harsh industrial environments.
How does CVD SiC coating improve equipment lifespan?
The coating forms a non-porous barrier that resists corrosion and thermal damage. This protection reduces wear and tear, extending the lifespan of reactors, pipelines, and other components.
Why is CVD SiC coating preferred over other methods?
CVD SiC coating offers superior uniformity, durability, and adaptability. Unlike spray or dip coatings, it provides precise coverage on complex shapes, ensuring comprehensive protection and long-term performance.
In which industries is CVD SiC coating commonly used?
Industries like chemical processing, aerospace, and semiconductor manufacturing use CVD SiC coating. It protects equipment in corrosive and high-temperature environments, ensuring reliability and efficiency.
What are the cost benefits of using CVD SiC coating?
CVD SiC coating reduces maintenance costs and downtime by preventing equipment failures. Its durability minimizes replacements, leading to significant long-term savings for industries.
Tip: Regularly applying CVD SiC coating can maximize cost savings and operational efficiency.