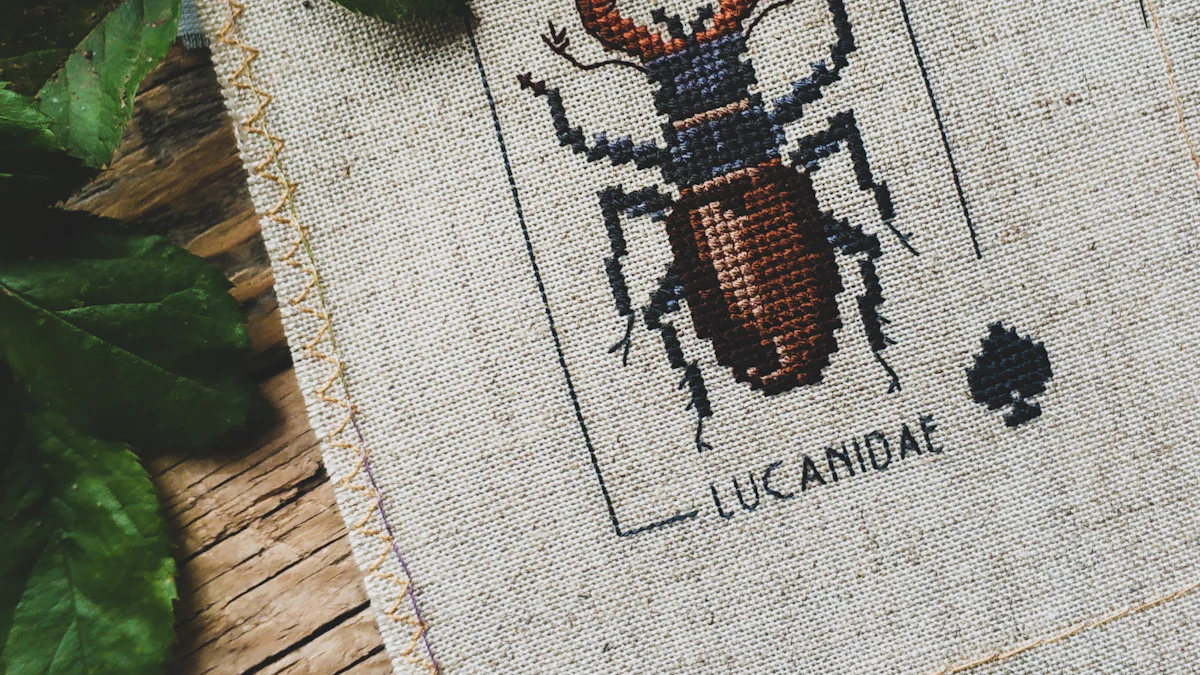
Uniformity in silicon carbide (SiC) deposition plays a pivotal role in advancing industries reliant on high-performance materials. Achieving consistent SiC layers ensures superior device functionality and reliability, particularly in electronics and microelectromechanical systems (MEMS). Shower head technology has emerged as a critical component in chemical vapor deposition (CVD) systems. Its innovative design optimizes gas distribution, enabling precise and uniform SiC deposition. Researchers continue to refine the cvd sic shower head to enhance its efficiency, addressing the growing demand for high-quality SiC coatings in cutting-edge applications.
Key Takeaways
- Uniform SiC deposition is crucial for enhancing the performance and reliability of electronic devices and MEMS, ensuring they operate efficiently under extreme conditions.
- The design of CVD SiC shower heads significantly impacts gas distribution, which is essential for achieving consistent layer thickness and high-quality SiC coatings.
- Maintaining stable temperature conditions during the deposition process is vital; temperature gradients can lead to defects that compromise the quality of SiC layers.
- Optimizing gas flow rates and shower head geometry can minimize defects and improve the uniformity of SiC coatings, leading to better device performance.
- Innovative materials and manufacturing techniques for shower heads enhance their durability and efficiency, supporting the growing demand for high-quality SiC products.
- Scalable uniform deposition processes reduce material waste and production costs, aligning with sustainability goals in industrial manufacturing.
- Future advancements in shower head technology, including smart monitoring systems, promise to further improve deposition uniformity and efficiency in SiC applications.
Overview of SiC Deposition and CVD SiC Shower Head Technology
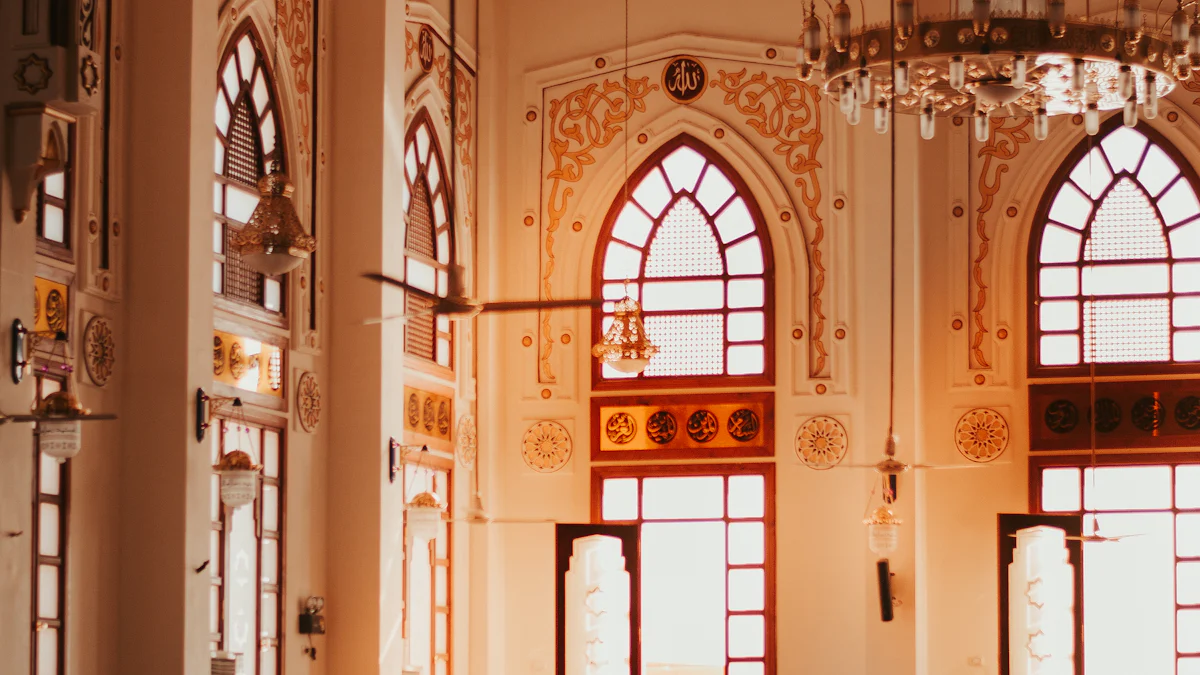
Basics of SiC Deposition
Chemical Vapor Deposition (CVD) process for SiC
The chemical vapor deposition (CVD) process is a widely used method for producing high-quality silicon carbide (SiC) layers. This process involves the reaction of gaseous precursors, such as silicon and carbon-containing compounds, within a controlled environment. The reaction occurs on a heated substrate, where SiC forms as a thin, uniform layer. The precision of this method allows manufacturers to tailor the thickness and properties of the SiC coating to meet specific application requirements.
CVD offers several advantages over other deposition techniques. It ensures excellent adhesion between the SiC layer and the substrate. It also produces coatings with superior mechanical strength, thermal stability, and chemical resistance. These qualities make CVD an essential process for industries that demand high-performance materials.
Applications of SiC in electronics, MEMS, and other industries
Silicon carbide has become a critical material in various industries due to its exceptional properties. In electronics, SiC is used to manufacture power devices, such as diodes and transistors, which operate efficiently under high temperatures and voltages. These devices play a vital role in renewable energy systems, electric vehicles, and aerospace technologies.
In microelectromechanical systems (MEMS), SiC enhances the durability and reliability of sensors and actuators. Its ability to withstand harsh environments makes it ideal for applications in automotive, medical, and industrial sectors. Beyond electronics and MEMS, SiC is also utilized in coatings for cutting tools, heat exchangers, and other components requiring wear resistance and thermal stability.
Role of CVD SiC Shower Heads in Deposition Systems
Functionality of shower heads in gas distribution
Shower heads in CVD systems serve as critical components for distributing precursor gases evenly across the substrate surface. These devices ensure that the gases flow uniformly, preventing variations in the deposition process. A well-designed shower head maintains consistent gas pressure and flow rates, which are essential for achieving high-quality SiC layers.
The cvd sic shower head plays a pivotal role in optimizing the deposition environment. By controlling the gas distribution, it minimizes defects and irregularities in the SiC coating. This functionality is particularly important for applications requiring precise material properties, such as electronic devices and MEMS components.
Advantages of shower head designs for deposition uniformity
Innovative shower head designs offer significant advantages for improving deposition uniformity. Engineers optimize the geometry and configuration of the cvd sic shower head to enhance gas flow patterns. These improvements reduce the risk of uneven coatings, which can compromise the performance and reliability of SiC-based devices.
Advanced shower head designs also contribute to better thermal management within the deposition chamber. By maintaining stable temperatures, they prevent thermal gradients that could affect the quality of the SiC layer. These features make the cvd sic shower head an indispensable tool for industries striving to achieve consistent and reliable SiC coatings.
Key Factors Influencing Deposition Uniformity
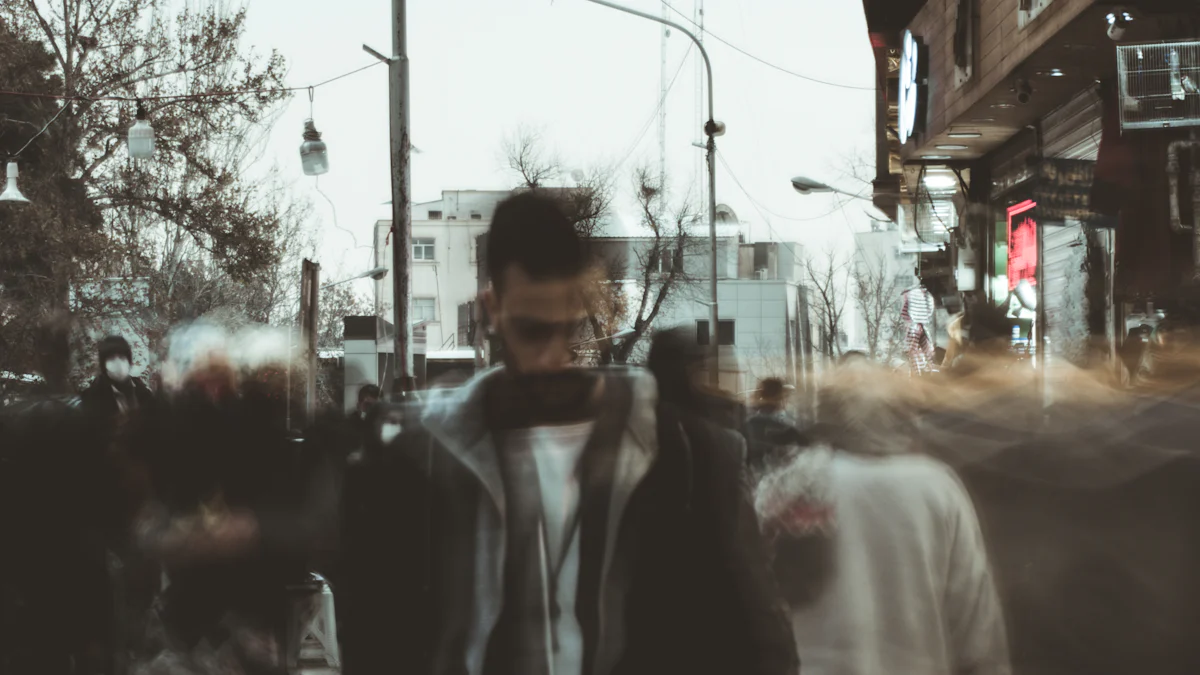
Temperature Control
Impact of temperature gradients on SiC layer quality
Temperature gradients within the deposition chamber can significantly affect the quality of silicon carbide (SiC) layers. Uneven temperatures lead to variations in the growth rate of the SiC film, resulting in non-uniform thickness and inconsistent material properties. These inconsistencies can compromise the performance of devices that rely on SiC coatings, such as power electronics and MEMS components. Maintaining a stable thermal environment is essential to ensure the deposition process produces high-quality, uniform layers.
Researchers have identified that even minor temperature fluctuations can introduce defects into the SiC layer. These defects may reduce the mechanical strength and thermal stability of the coating. By addressing temperature gradients, manufacturers can achieve more reliable and durable SiC films, which are critical for advanced industrial applications.
Thermal management capabilities of CVD SiC shower heads
The cvd sic shower head plays a crucial role in managing thermal conditions during the deposition process. Its design ensures uniform heat distribution across the substrate, minimizing the risk of temperature gradients. This capability helps maintain consistent deposition rates and improves the overall quality of the SiC layer.
Advanced shower head designs incorporate materials with high thermal conductivity to enhance heat transfer efficiency. These features allow the system to regulate temperatures effectively, even under demanding operating conditions. By optimizing thermal management, the cvd sic shower head contributes to the production of SiC coatings with superior uniformity and performance.
Gas Flow Dynamics
Importance of precursor gas flow rates and distribution
The flow rate and distribution of precursor gases directly influence the uniformity of SiC deposition. Precise control over gas flow ensures that the reactive species reach the substrate evenly, promoting consistent layer growth. Uneven gas distribution can lead to localized variations in the deposition process, resulting in defects or irregularities in the SiC coating.
Maintaining optimal gas flow rates is essential for achieving high-quality SiC films. Excessive flow rates may cause turbulence, while insufficient flow can limit the availability of reactive species. Both scenarios negatively impact the uniformity of the deposited layer. Proper calibration of gas flow parameters is critical for ensuring reliable and repeatable results.
Influence of shower head geometry on gas flow patterns
The geometry of the cvd sic shower head significantly affects gas flow patterns within the deposition chamber. Engineers design the shower head to distribute gases uniformly across the substrate surface. Features such as nozzle size, spacing, and orientation are carefully optimized to minimize flow disturbances and ensure even coverage.
Innovative shower head geometries enhance the mixing of precursor gases, improving the efficiency of the chemical reactions that form the SiC layer. These designs also reduce the risk of stagnation zones, where gas flow becomes uneven. By refining the geometry of the cvd sic shower head, manufacturers can achieve greater control over the deposition process and produce SiC coatings with exceptional uniformity.
Reactor Design and Configuration
Reactor geometry and its effect on deposition uniformity
The overall geometry of the reactor plays a pivotal role in determining the uniformity of SiC deposition. Factors such as chamber size, shape, and internal components influence gas flow dynamics and thermal distribution. A well-designed reactor ensures that the deposition environment remains stable and consistent throughout the process.
Reactor geometry must accommodate the specific requirements of the cvd sic shower head to maximize its effectiveness. Proper alignment of the shower head with the substrate and other reactor components minimizes disruptions to gas flow and heat transfer. This alignment is essential for achieving uniform SiC layers across the entire substrate surface.
Integration of CVD SiC shower heads into reactor systems
Integrating the cvd sic shower head into the reactor system requires careful consideration of its placement and compatibility with other components. The shower head must be positioned to deliver gases evenly while maintaining optimal thermal conditions. Engineers often customize reactor designs to accommodate the unique features of the shower head, ensuring seamless integration.
Successful integration enhances the overall performance of the deposition system. It allows for precise control over key process parameters, such as gas flow and temperature, which are critical for achieving uniform SiC coatings. By optimizing the interaction between the shower head and the reactor, manufacturers can produce high-quality SiC films that meet the stringent demands of modern industries.
Scientific Studies and Findings
Experimental Studies
Key findings on deposition uniformity from laboratory experiments
Laboratory experiments have provided valuable insights into the factors influencing SiC deposition uniformity. Researchers observed that the design of the cvd sic shower head directly impacts gas distribution and layer consistency. Experiments demonstrated that optimized shower head geometries significantly reduce defects in SiC coatings. Uniform gas flow across the substrate surface resulted in consistent film thickness and improved material properties.
Studies also highlighted the importance of temperature stability during deposition. Controlled thermal environments, supported by advanced shower head designs, minimized temperature gradients. This stability enhanced the quality of SiC layers, ensuring their suitability for high-performance applications. These findings underscore the critical role of precise engineering in achieving uniform deposition.
Challenges in scaling uniformity for industrial applications
Scaling laboratory findings to industrial applications presents unique challenges. Larger reactors and substrates introduce complexities in maintaining uniform gas flow and temperature distribution. Engineers face difficulties in replicating the precise conditions achieved in controlled laboratory settings. Variations in reactor size and operational parameters often lead to inconsistencies in SiC coatings.
Another challenge lies in adapting the cvd sic shower head for high-volume production. While laboratory-scale designs excel in uniformity, they may require modifications to meet industrial throughput demands. Addressing these challenges requires innovative approaches to reactor design and shower head optimization. Overcoming these obstacles is essential for translating experimental success into scalable manufacturing solutions.
Computational Models
Numerical modeling of gas flow and deposition processes
Numerical modeling has emerged as a powerful tool for understanding gas flow dynamics and deposition processes. Simulations allow researchers to visualize how precursor gases interact within the reactor. These models reveal the influence of shower head geometry on gas distribution and deposition uniformity. By analyzing flow patterns, engineers can identify areas of improvement in shower head designs.
Computational studies also provide insights into the chemical reactions occurring during SiC deposition. Models simulate the behavior of reactive species, helping researchers optimize process parameters. This approach reduces the need for extensive physical testing, saving time and resources. Numerical modeling plays a pivotal role in refining the performance of the cvd sic shower head and enhancing deposition outcomes.
Insights into optimizing CVD SiC shower head designs
Modeling results have guided the development of more efficient shower head designs. Engineers use simulation data to adjust nozzle configurations, spacing, and angles. These adjustments improve gas flow uniformity and minimize stagnation zones. Optimized designs ensure even coverage of the substrate, resulting in high-quality SiC layers.
Thermal management also benefits from computational insights. Models help identify areas where heat distribution can be improved. Incorporating materials with superior thermal conductivity into the shower head design enhances temperature stability. These advancements contribute to the production of SiC coatings with exceptional uniformity and reliability.
Innovations in CVD SiC Shower Head Technology
Advances in materials and manufacturing techniques
Recent innovations in materials and manufacturing techniques have revolutionized cvd sic shower head technology. Engineers now utilize advanced materials with high thermal conductivity and chemical resistance. These materials enhance the durability and performance of shower heads under demanding conditions. Improved manufacturing processes, such as precision machining and additive manufacturing, enable the creation of complex geometries.
These advancements allow for greater customization of shower head designs. Engineers can tailor features to specific deposition requirements, ensuring optimal gas flow and thermal management. The integration of cutting-edge materials and techniques has elevated the capabilities of cvd sic shower heads, meeting the evolving needs of modern industries.
Case studies of improved deposition uniformity
Case studies highlight the tangible benefits of innovative shower head designs. In one instance, a redesigned cvd sic shower head achieved a 20% improvement in deposition uniformity. The optimized geometry reduced defects and enhanced the quality of SiC coatings. This improvement translated to better performance and reliability in electronic devices.
Another study demonstrated the impact of advanced thermal management features. A shower head incorporating high-conductivity materials maintained consistent temperatures across the substrate. This stability resulted in uniform SiC layers, even in large-scale industrial reactors. These examples showcase the potential of innovative shower head technology to drive advancements in SiC deposition processes.
Practical Applications and Benefits
Applications in Electronics and MEMS
Enhanced performance and reliability of SiC-based devices
Silicon carbide (SiC) has transformed the electronics and MEMS industries by enabling devices to operate under extreme conditions. SiC-based power devices, such as diodes and transistors, exhibit exceptional thermal stability and electrical efficiency. These characteristics make them ideal for high-temperature and high-voltage applications, including electric vehicles and renewable energy systems. The uniformity achieved through advanced deposition techniques ensures consistent material properties, which directly enhances device performance.
MEMS devices, such as sensors and actuators, benefit significantly from SiC coatings. The material’s durability and resistance to wear extend the lifespan of these components. Uniform SiC layers reduce the likelihood of defects, ensuring reliable operation in harsh environments. This reliability is critical for applications in automotive, aerospace, and medical industries, where precision and consistency are paramount.
Role of uniformity in device efficiency and longevity
Uniform SiC deposition plays a vital role in determining the efficiency and longevity of electronic and MEMS devices. Consistent layer thickness ensures optimal electrical conductivity and thermal management. Devices with uniform coatings experience fewer performance fluctuations, even under demanding conditions. This stability leads to improved energy efficiency and reduced operational costs.
Longevity also depends on the absence of defects in the SiC layer. Non-uniform coatings can introduce stress points, which may lead to premature failure. By achieving uniform deposition, manufacturers enhance the structural integrity of devices. This improvement translates to longer service life and reduced maintenance requirements, benefiting both consumers and industries.
Benefits for Industrial Manufacturing
Cost savings through reduced material waste
Uniform SiC deposition minimizes material waste during the manufacturing process. Precise control over deposition parameters ensures that only the required amount of material is used. This efficiency reduces production costs and conserves valuable resources. Manufacturers can achieve higher yields by avoiding defects caused by uneven coatings, further lowering expenses.
Reduced waste also aligns with sustainability goals. Industries can decrease their environmental impact by optimizing material usage. Uniform deposition processes contribute to greener manufacturing practices, which are increasingly important in today’s environmentally conscious market.
Scalability of uniform deposition processes
The scalability of uniform deposition processes enables manufacturers to meet the growing demand for SiC-based products. Advanced technologies, such as the cvd sic shower head, ensure consistent results across substrates of varying sizes. This capability is essential for transitioning from laboratory-scale production to industrial-scale manufacturing.
Scalable processes maintain uniformity even in large reactors, ensuring high-quality SiC coatings for mass production. Industries can expand their operations without compromising product quality. This scalability supports the widespread adoption of SiC in applications ranging from consumer electronics to heavy industrial equipment.
Future Trends and Opportunities
Emerging applications of SiC in new industries
The versatility of SiC continues to open doors to new applications across various industries. In renewable energy, SiC is being explored for use in solar inverters and wind turbine components. Its ability to withstand high temperatures and harsh environments makes it a promising material for energy storage systems and grid infrastructure.
The aerospace industry is also leveraging SiC for lightweight, high-strength components. Its thermal stability and resistance to radiation make it suitable for spacecraft and satellite applications. As industries seek materials that combine performance with durability, SiC’s potential continues to grow.
Potential for further optimization of CVD SiC shower head designs
Ongoing research focuses on optimizing the design of the cvd sic shower head to enhance deposition uniformity further. Engineers are exploring innovative geometries and materials to improve gas flow dynamics and thermal management. These advancements aim to address challenges in scaling up production while maintaining high-quality results.
Future developments may include the integration of smart technologies into shower head designs. Sensors and real-time monitoring systems could provide precise control over deposition parameters, ensuring consistent performance. These innovations will drive the evolution of SiC deposition processes, supporting the development of next-generation devices and applications.
Uniformity in SiC deposition remains a cornerstone for advancing high-performance materials and technologies. CVD SiC shower heads play a pivotal role in achieving this uniformity by optimizing gas flow and thermal management. Scientific studies have highlighted their impact on improving coating quality and reliability, which directly benefits industries like electronics and MEMS. Continued research and innovation in shower head designs will unlock new possibilities for scaling production and enhancing efficiency. SiC’s potential to revolutionize manufacturing and technology underscores its importance as a material for the future.