
The Silicon Carbide Dummy Wafer stands as a cornerstone in semiconductor testing, offering unmatched precision, durability, and heat resistance. Its advanced properties address critical challenges in the industry, such as ensuring cost efficiency, maintaining structural integrity, and achieving precise measurements. By serving as a reliable testing substrate, it simplifies complex processes and enhances the accuracy of semiconductor fabrication. This innovation not only withstands extreme conditions but also supports the development of cutting-edge electronic components, making it indispensable for modern manufacturing.
Key Takeaways
- Silicon carbide dummy wafers are cost-effective alternatives to traditional silicon wafers, reducing material wastage and operational expenses in semiconductor testing.
Their exceptional durability allows them to withstand extreme temperatures and mechanical stress, minimizing the need for frequent replacements and enhancing workflow efficiency.
- These wafers ensure high precision and reliability in testing, providing consistent performance that leads to accurate measurements and high-quality semiconductor devices.
Silicon carbide dummy wafers support various applications, from quality assurance to high-temperature processing, making them versatile tools in semiconductor manufacturing.
- By adopting silicon carbide dummy wafers, manufacturers can achieve long-term cost savings and improve overall production efficiency, driving innovation in the electronics industry.
- Their ability to handle extreme conditions makes silicon carbide dummy wafers indispensable for testing advanced materials and technologies, such as those used in 5G networks and electric vehicles.
Overview of Semiconductor Testing Challenges
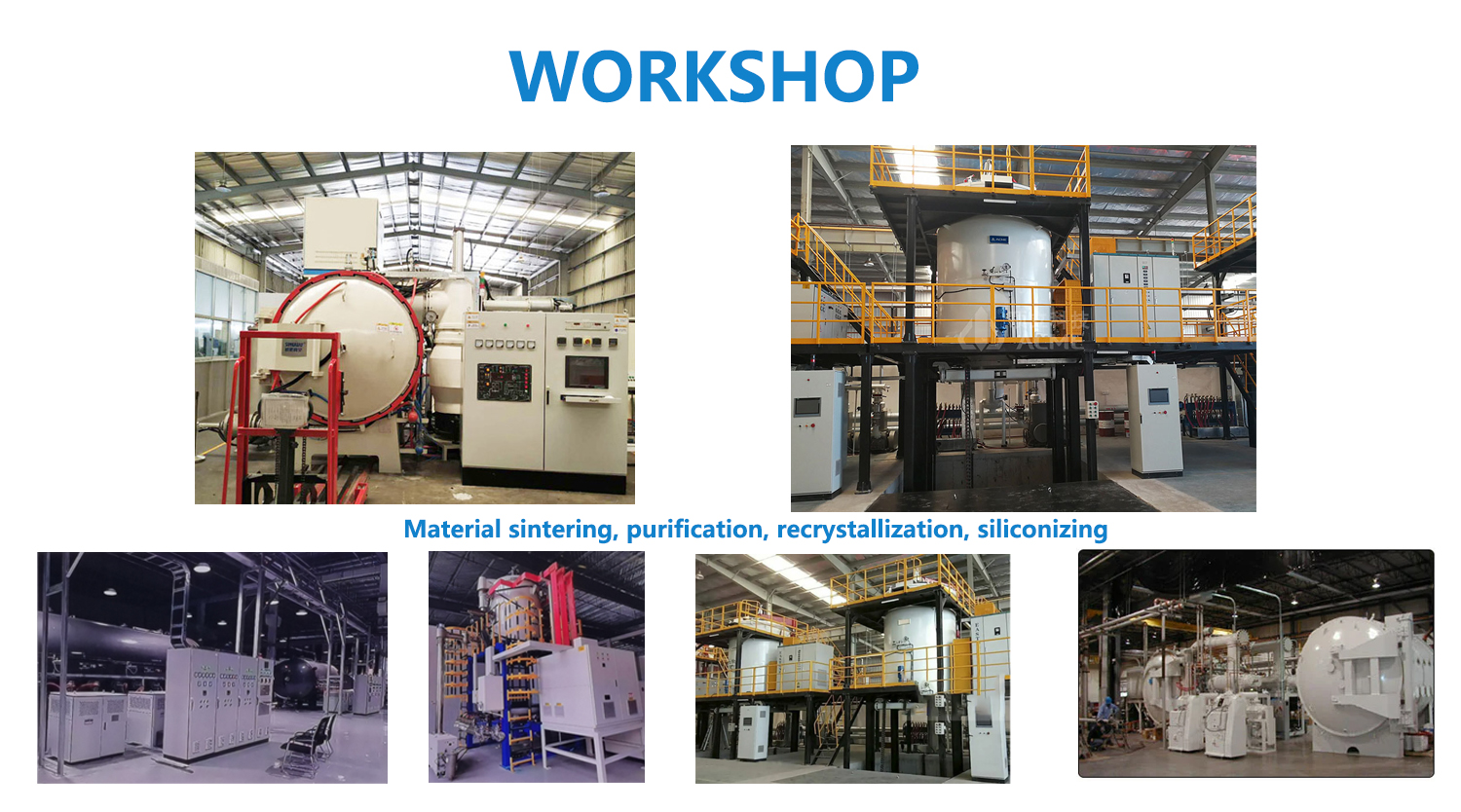
Semiconductor testing plays a critical role in ensuring the performance and reliability of electronic components. However, this process presents several challenges that manufacturers must address to maintain efficiency and quality.
High Costs of Testing
Testing semiconductor wafers often incurs significant expenses due to the use of production-grade materials. Regular silicon wafers, commonly employed in manufacturing, are costly and prone to damage during testing. Replacing these wafers increases operational costs, especially when defects or errors occur. Manufacturers require a cost-effective alternative to minimize financial losses without compromising testing accuracy.
Silicon carbide dummy wafers provide a solution by serving as testing and calibration tools. These wafers eliminate the need to risk production-grade silicon wafers, reducing material wastage and overall expenses. Their durability ensures repeated use, further contributing to cost savings over time.
Durability Issues
Durability remains a major concern in semiconductor testing. Regular silicon wafers often fail to withstand the extreme conditions involved in testing, such as high temperatures and mechanical stress. This lack of resilience leads to frequent replacements, disrupting workflows and increasing downtime.
Silicon carbide dummy wafers address this issue with their exceptional durability. Their high thermal conductivity and resistance to extreme conditions make them ideal for rigorous testing environments. By enduring harsh processes without degradation, these wafers enhance operational efficiency and reduce interruptions.
Precision and Reliability Concerns
Achieving precision and reliability is essential in semiconductor testing. Regular silicon wafers may introduce inconsistencies due to their limited structural integrity under demanding conditions. These inconsistencies can compromise the accuracy of measurements and the reliability of test results.
Silicon carbide dummy wafers excel in maintaining precision and reliability. Their superior structural integrity ensures consistent performance, even under high-pressure scenarios. This consistency allows manufacturers to obtain accurate data, enabling the development of high-quality semiconductor devices.
What Are Silicon Carbide Dummy Wafers?
Silicon carbide dummy wafers are specialized tools designed for semiconductor testing and manufacturing. These wafers, crafted from silicon carbide, serve as non-functional substrates during the development and testing phases of semiconductor devices. Their unique properties make them indispensable in ensuring the efficiency and accuracy of testing processes.
Composition and Properties
Silicon carbide dummy wafers are composed of silicon carbide, a compound known for its exceptional material properties. This compound exhibits a larger bandgap compared to silicon, which enhances its ability to operate under high temperatures and voltages. Additionally, silicon carbide offers superior thermal conductivity, allowing devices to maintain performance even in extreme conditions.
The structural integrity of these wafers ensures resistance to mechanical stress, making them ideal for rigorous testing environments. Their high dielectric breakdown strength and low specific on-resistance further contribute to their reliability in power electronics applications. These properties enable silicon carbide dummy wafers to withstand the demands of modern semiconductor manufacturing processes.
Purpose in Semiconductor Testing
Silicon carbide dummy wafers play a critical role in semiconductor testing by acting as reliable test substrates. Manufacturers use these wafers to simulate real production conditions without risking damage to functional silicon wafers. This approach minimizes material wastage and reduces costs associated with testing errors.
In high-temperature processing, these wafers provide a stable platform for evaluating new materials and technologies. For instance, they support the testing of advanced materials like gallium oxide and aluminum nitride, which are essential for next-generation electronic components. Their precision and durability ensure accurate measurements of parameters such as film thickness and pressure resistance, contributing to the validation of production processes.
Moreover, silicon carbide dummy wafers are instrumental in quality assurance. They enable manufacturers to detect defects, measure pattern sizes, and ensure geometric accuracy during lithography. By maintaining consistency and reliability, these wafers help streamline semiconductor fabrication and improve overall production efficiency.
How Silicon Carbide Dummy Wafers Address Testing Challenges
Improved Durability
Durability plays a pivotal role in semiconductor testing, where materials must endure extreme conditions without compromising performance. Silicon carbide dummy wafers excel in this aspect due to their exceptional thermal conductivity and mechanical strength. Unlike regular silicon wafers, these wafers withstand high temperatures and mechanical stress, ensuring consistent performance during rigorous testing processes.
The structural integrity of silicon carbide dummy wafers minimizes the risk of damage, even under prolonged usage. This resilience reduces the frequency of replacements, allowing manufacturers to maintain uninterrupted workflows. By addressing durability concerns, these wafers enhance the reliability of testing environments and contribute to the longevity of semiconductor fabrication tools.
"Wide-bandgap materials, such as silicon carbide, have gained prominence in power electronics due to their superior electrical properties." This statement underscores the material’s ability to endure challenging conditions, making it an ideal choice for testing applications.
Cost Reduction
The high costs associated with semiconductor testing often stem from the use of production-grade silicon wafers, which are both expensive and prone to damage. Silicon carbide dummy wafers offer a cost-effective alternative by serving as reusable testing substrates. Their durability ensures multiple cycles of use, significantly reducing material wastage and operational expenses.
Manufacturers benefit from the long-term cost savings provided by these wafers. By minimizing the need for frequent replacements, silicon carbide dummy wafers lower overall testing costs while maintaining accuracy and efficiency. This cost reduction proves especially valuable in large-scale production environments, where testing constitutes a substantial portion of operational budgets.
Additionally, the versatility of silicon carbide dummy wafers supports various applications, from quality assurance to high-temperature processing. This adaptability further enhances their value, enabling manufacturers to optimize their testing processes without incurring additional expenses.
Enhanced Accuracy and Reliability
Precision and reliability are critical in semiconductor testing, where even minor inconsistencies can compromise the quality of electronic components. Silicon carbide dummy wafers address these challenges by providing a stable and consistent platform for testing. Their superior structural integrity ensures accurate measurements, even under high-pressure scenarios.
These wafers play a crucial role in validating production processes by enabling precise evaluations of parameters such as film thickness and pressure resistance. Their high thermal stability and low specific on-resistance contribute to consistent performance, ensuring reliable test results across various conditions.
In lithography, silicon carbide dummy wafers serve as benchmarks for detecting defects and measuring pattern sizes. Their precision supports the development of advanced semiconductor devices, where geometric accuracy is essential. By enhancing accuracy and reliability, these wafers streamline testing processes and improve the overall quality of semiconductor fabrication.
Benefits of Using Silicon Carbide Dummy Wafers
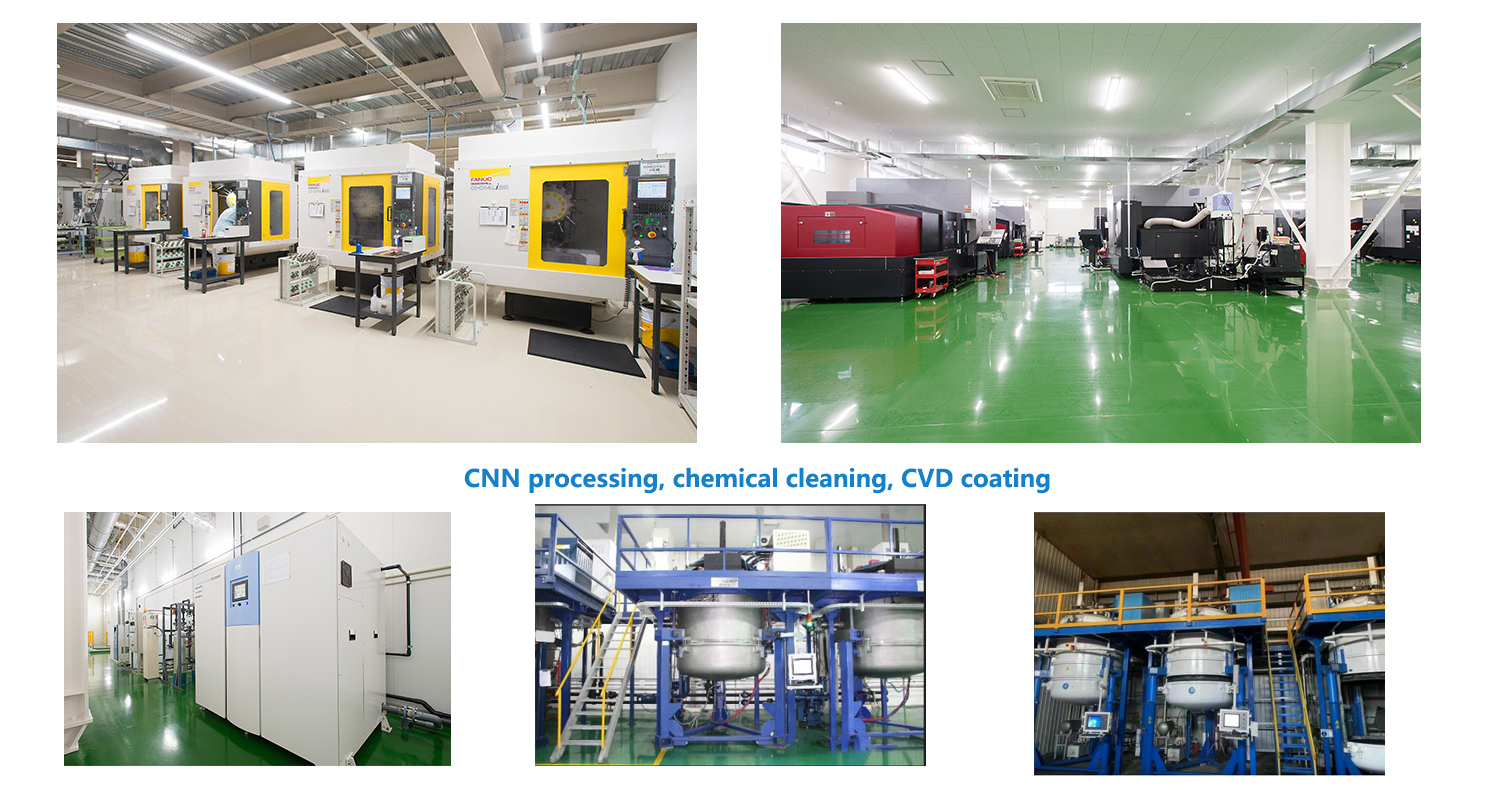
Long-Term Cost Savings
Silicon carbide dummy wafers provide significant financial advantages for semiconductor manufacturers. Their durability allows repeated use, reducing the need for frequent replacements. Unlike regular silicon wafers, which often degrade under extreme testing conditions, these wafers maintain their structural integrity over time. This longevity minimizes material wastage and operational expenses.
The high thermal conductivity and mechanical strength of silicon carbide dummy wafers ensure consistent performance during rigorous testing. Manufacturers benefit from lower costs associated with errors and defects, as these wafers help maintain precision in testing processes. By investing in silicon carbide dummy wafers, companies achieve substantial cost savings, particularly in large-scale production environments where testing constitutes a major expense.
Industry Experts highlight that "automation and innovative technologies are helping reduce costs and improve efficiency" in the production of silicon carbide dummy wafers. These advancements further enhance their affordability and accessibility for manufacturers.
Increased Reliability
Reliability remains a critical factor in semiconductor testing, and silicon carbide dummy wafers excel in this area. Their superior structural integrity ensures consistent performance, even under high-pressure scenarios. This consistency allows manufacturers to obtain accurate data, which is essential for developing high-quality semiconductor devices.
The ability of these wafers to withstand extreme temperatures and mechanical stress makes them indispensable for advanced chip production. Their high dielectric breakdown strength and low specific on-resistance contribute to reliable testing outcomes. By using silicon carbide dummy wafers, manufacturers can confidently validate production processes and ensure the quality of their products.
According to Industry Experts, "silicon carbide dummy wafers play a critical role in testing and validating manufacturing equipment." Their reliability supports the development of cutting-edge technologies, including 5G networks and electric vehicles.
Greater Efficiency
Efficiency in semiconductor testing directly impacts production timelines and overall productivity. Silicon carbide dummy wafers streamline testing processes by providing a stable and consistent platform. Their precision reduces the likelihood of errors, enabling faster evaluations of parameters such as film thickness and pressure resistance.
These wafers also support high-temperature processing, which is essential for testing advanced materials like gallium oxide and aluminum nitride. Their ability to maintain performance under extreme conditions enhances the efficiency of testing and calibration procedures. As a result, manufacturers can optimize their workflows and accelerate the development of next-generation electronic components.
The versatility of silicon carbide dummy wafers further contributes to their efficiency. They adapt to various applications, from quality assurance to lithography, ensuring seamless integration into different stages of semiconductor fabrication. This adaptability allows manufacturers to maximize their resources and achieve higher productivity.
Industry Experts emphasize that "the applications of silicon carbide dummy wafers span multiple industries," highlighting their role in improving efficiency across sectors such as renewable energy and automotive.
Silicon carbide dummy wafers have revolutionized semiconductor testing by addressing critical challenges such as high costs, durability issues, and precision concerns. Their advanced properties, including exceptional thermal stability and structural integrity, make them indispensable for modern manufacturing. These wafers streamline testing processes, reduce material wastage, and ensure reliable outcomes, enabling manufacturers to achieve cost-effective and efficient operations.
By adopting silicon carbide dummy wafers, industries can enhance the quality of semiconductor devices while driving innovation in high-power and high-frequency applications. Their role in advancing technology underscores their importance in shaping the future of electronics.
FAQ
What are silicon carbide dummy wafers?
Silicon carbide dummy wafers, often referred to as SiC Dummy Wafers, are non-functional wafers crafted from silicon carbide. These wafers play a vital role in semiconductor manufacturing by serving as test substrates during the development and testing phases of semiconductor devices. Their unique properties, such as high thermal conductivity and exceptional durability, make them ideal for evaluating new fabrication processes and materials. Silicon carbide dummy wafers ensure suitability for high-power, high-frequency, and high-temperature applications.
Why are silicon carbide dummy wafers important in semiconductor testing?
Silicon carbide dummy wafers simplify semiconductor testing by providing a reliable platform for evaluating production processes. They reduce the risk of damaging functional silicon wafers during testing, ensuring cost efficiency and material preservation. Their ability to withstand extreme conditions, such as high temperatures and mechanical stress, ensures consistent performance and accurate test results. This reliability makes them indispensable for maintaining quality and precision in semiconductor fabrication.
What are the applications of silicon carbide dummy wafers?
Silicon carbide dummy wafers find applications across various stages of semiconductor manufacturing. They act as testing and calibration tools, ensuring the precision and quality of production equipment without risking damage to actual production wafers. Industries such as renewable energy and automotive also utilize these wafers for testing advanced technologies, including solar cells and power electronics. Their versatility extends to high-temperature processing, lithography, and quality assurance.
How do silicon carbide dummy wafers contribute to cost savings?
Silicon carbide dummy wafers significantly reduce costs in semiconductor testing. Their durability allows repeated use, minimizing the need for frequent replacements. By serving as reusable testing substrates, they lower material wastage and operational expenses. Manufacturers benefit from long-term cost savings, especially in large-scale production environments where testing constitutes a substantial portion of the budget.
Can silicon carbide dummy wafers handle extreme conditions?
Yes, silicon carbide dummy wafers excel in handling extreme conditions. Their high thermal conductivity and mechanical strength enable them to endure high temperatures and mechanical stress without degradation. These properties make them suitable for rigorous testing environments, ensuring consistent performance and reliability even under demanding scenarios.
What makes silicon carbide a preferred material for dummy wafers?
Silicon carbide stands out due to its exceptional material properties. It offers a larger bandgap compared to silicon, enhancing its ability to operate under high temperatures and voltages. Its superior thermal conductivity and structural integrity ensure durability and precision in testing processes. These characteristics make silicon carbide an ideal choice for dummy wafers in advanced semiconductor manufacturing.
How do silicon carbide dummy wafers improve testing accuracy?
Silicon carbide dummy wafers enhance testing accuracy by providing a stable and consistent platform for evaluations. Their superior structural integrity ensures precise measurements of parameters such as film thickness and pressure resistance. This consistency allows manufacturers to obtain reliable data, enabling the development of high-quality semiconductor devices.
Are silicon carbide dummy wafers environmentally friendly?
Silicon carbide dummy wafers contribute to environmental sustainability by reducing material wastage in semiconductor testing. Their durability and reusability minimize the need for frequent replacements, lowering the consumption of raw materials. This efficiency aligns with the industry’s efforts to adopt eco-friendly practices in manufacturing.
What industries benefit from silicon carbide dummy wafers?
Several industries benefit from the use of silicon carbide dummy wafers. The semiconductor industry relies on these wafers for testing and quality assurance. Renewable energy sectors use them in the development of solar cells, while the automotive industry employs them in testing power electronics for electric vehicles. Their versatility supports advancements in high-power and high-frequency applications across multiple fields.
How do silicon carbide dummy wafers support innovation?
Silicon carbide dummy wafers play a crucial role in driving innovation in the semiconductor industry. They provide a reliable platform for testing emerging materials like gallium oxide and aluminum nitride. These materials are essential for next-generation technologies, including 5G networks and high-performance electronic devices. By enabling precise evaluations, silicon carbide dummy wafers support the development of cutting-edge solutions that shape the future of electronics.