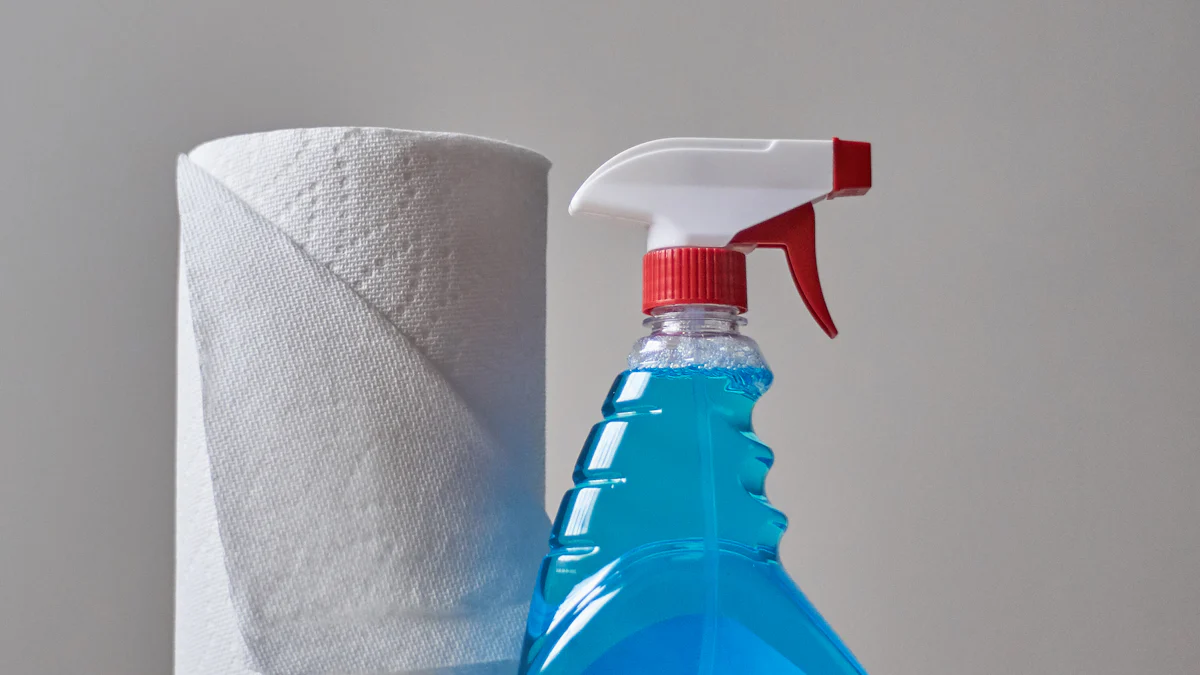
Si epitaxy susceptor cleaning plays a vital role in maintaining the efficiency of chemical vapor deposition (CVD) reactors. These components endure high temperatures and chemical exposure, leading to the accumulation of contaminants like carbon and residual particles. Without proper cleaning, these deposits can compromise the quality of epitaxial growth and reduce reactor performance. Studies highlight that combining wet and dry cleaning methods yields optimal results, ensuring thorough contaminant removal. Regular cleaning not only extends the lifespan of susceptors but also supports consistent semiconductor manufacturing by eliminating impurities that could affect the final product.
Key Takeaways
- Regular cleaning of Si epitaxy susceptors is essential for maintaining reactor efficiency and ensuring high-quality semiconductor production.
- Combining wet and dry cleaning methods optimizes contaminant removal, preventing defects in epitaxial layers.
- Establish a consistent cleaning schedule based on reactor usage to minimize contamination buildup and reduce maintenance downtime.
- Use appropriate cleaning agents, such as sulfuric acid and hydrogen peroxide mixtures, to effectively remove organic and metallic residues without damaging the susceptor.
- Implement thorough inspection processes post-cleaning to ensure the susceptor is free from contaminants before reinstallation.
- Train staff on proper cleaning techniques and safety protocols to enhance operational efficiency and reduce the risk of errors.
- Invest in high-quality inspection tools to monitor the cleanliness of susceptors and maintain consistent production quality.
Importance of Cleaning Si Epitaxy Susceptors
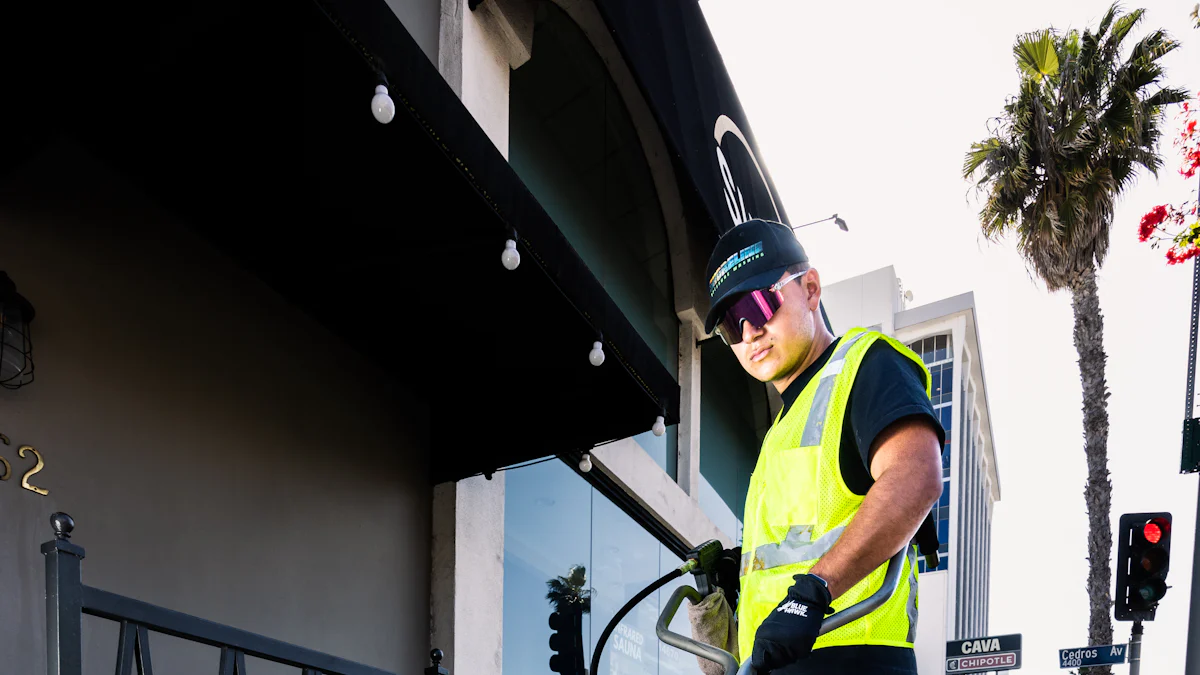
Role of Si Epitaxy Susceptors in CVD Reactors
Si epitaxy susceptors serve as the foundation for substrates during chemical vapor deposition (CVD) processes. These components ensure uniform heating and provide structural support, which are essential for achieving precise epitaxial growth. Their ability to withstand extreme temperatures and chemical exposure makes them indispensable in semiconductor manufacturing. However, their performance directly impacts the quality of the deposition process. Contaminants on the susceptor surface can disrupt the uniformity of heat distribution, leading to defects in the deposited layers. Maintaining clean susceptors ensures that the substrates receive consistent thermal and chemical conditions, which are critical for high-quality production.
Impact of Contamination on Reactor Efficiency
Contamination on si epitaxy susceptors can significantly reduce reactor efficiency. Deposits such as carbon residues and other particles accumulate over time, creating uneven surfaces. These irregularities interfere with the deposition process, causing variations in layer thickness and composition. Additionally, contaminants can lead to hotspots, which compromise the thermal stability of the reactor. This instability increases the likelihood of defects in the final product. Cleaning methods, such as plasma cleaning or a combination of wet and dry techniques, effectively remove these deposits. For instance, microwave plasma cleaning offers a quick and efficient solution, while O2 plasma etching is particularly effective for non-metallic surfaces. By eliminating contaminants, manufacturers can optimize reactor performance and reduce downtime caused by maintenance issues.
Benefits of Regular Cleaning for Epitaxial Growth
Regular cleaning of si epitaxy susceptors provides multiple benefits for epitaxial growth. First, it ensures a contaminant-free surface, which is essential for achieving uniform deposition. Second, it extends the lifespan of the susceptor by preventing the buildup of corrosive materials. Third, it minimizes the risk of defects in the epitaxial layers, which enhances the overall quality of the semiconductor devices. Cleaning methods, such as combining dry and wet techniques, have proven to be highly effective. These approaches reduce the reliance on harsh chemicals and deionized water, making the process more sustainable. Consistent cleaning practices not only improve the efficiency of the CVD reactor but also contribute to cost savings by reducing the frequency of susceptor replacements.
Tools and Materials Needed for Cleaning Si Epitaxy Susceptors
Proper cleaning of a si epitaxy susceptor requires the right combination of cleaning agents, equipment, and inspection tools. Each component plays a crucial role in ensuring the process is efficient, safe, and effective. Below is a detailed guide to the essential tools and materials needed.
Cleaning Agents
Recommended Chemical Solutions for SiC Susceptors
Cleaning agents are vital for removing contaminants from the surface of silicon carbide (SiC) susceptors. Commonly used solutions include a mixture of sulfuric acid and hydrogen peroxide, which effectively oxidizes and dissolves organic debris and metal ion contamination. Wet cleaning methods, such as RCA cleaning and IMEC cleaning, are widely recommended for their ability to eliminate oxidized residues and photoresist films. These chemical solutions not only clean the surface but also prepare it for subsequent processes by making it water-compatible. Manufacturers should always select cleaning agents specifically designed for SiC susceptors to avoid damaging the material.
Safety Guidelines for Handling Cleaning Chemicals
Handling cleaning chemicals requires strict adherence to safety protocols. Always wear protective gloves and goggles to prevent direct contact with hazardous substances. Work in a well-ventilated area or under a fume hood to minimize exposure to harmful fumes. Store chemicals in labeled, airtight containers away from heat sources. Before use, consult the Material Safety Data Sheet (MSDS) for each chemical to understand its properties and risks. Proper disposal of used chemicals is equally important to ensure environmental safety.
Cleaning Equipment
Essential Tools: Brushes, Wipes, and More
Mechanical tools complement chemical cleaning by physically removing stubborn residues. Soft-bristle brushes are ideal for scrubbing without scratching the susceptor surface. Lint-free wipes help in applying cleaning agents evenly and drying the surface without leaving fibers behind. For more advanced cleaning, ultrasonic baths can be used to dislodge particles from hard-to-reach areas. These tools ensure thorough cleaning while preserving the integrity of the susceptor.
Protective Gear for Safe Cleaning
Safety during the cleaning process cannot be overstated. Protective gear, including gloves, goggles, and lab coats, shields workers from chemical exposure and physical injuries. Heat-resistant gloves are particularly important when handling susceptors that have been exposed to high temperatures. Anti-static wrist straps can also be used to prevent electrostatic discharge, which could damage sensitive components.
Inspection Tools
Microscopes and Magnifiers for Surface Analysis
Inspection tools are essential for verifying the cleanliness of a si epitaxy susceptor. Microscopes and magnifiers allow for detailed surface analysis, helping to identify residual contaminants that may not be visible to the naked eye. High-magnification microscopes are particularly useful for detecting microscopic particles and ensuring the surface is free of defects. Regular inspection ensures that the cleaning process meets the required standards.
Surface Testing Equipment for Contaminant Detection
Advanced surface testing equipment provides quantitative data on the cleanliness of the susceptor. Tools such as surface profilometers and contact angle measurement devices assess the presence of contaminants and the uniformity of the cleaned surface. These instruments help manufacturers maintain consistent quality by identifying areas that require additional cleaning. Investing in reliable inspection tools enhances the overall efficiency of the cleaning process.
Step-by-Step Cleaning Process for Si Epitaxy Susceptors
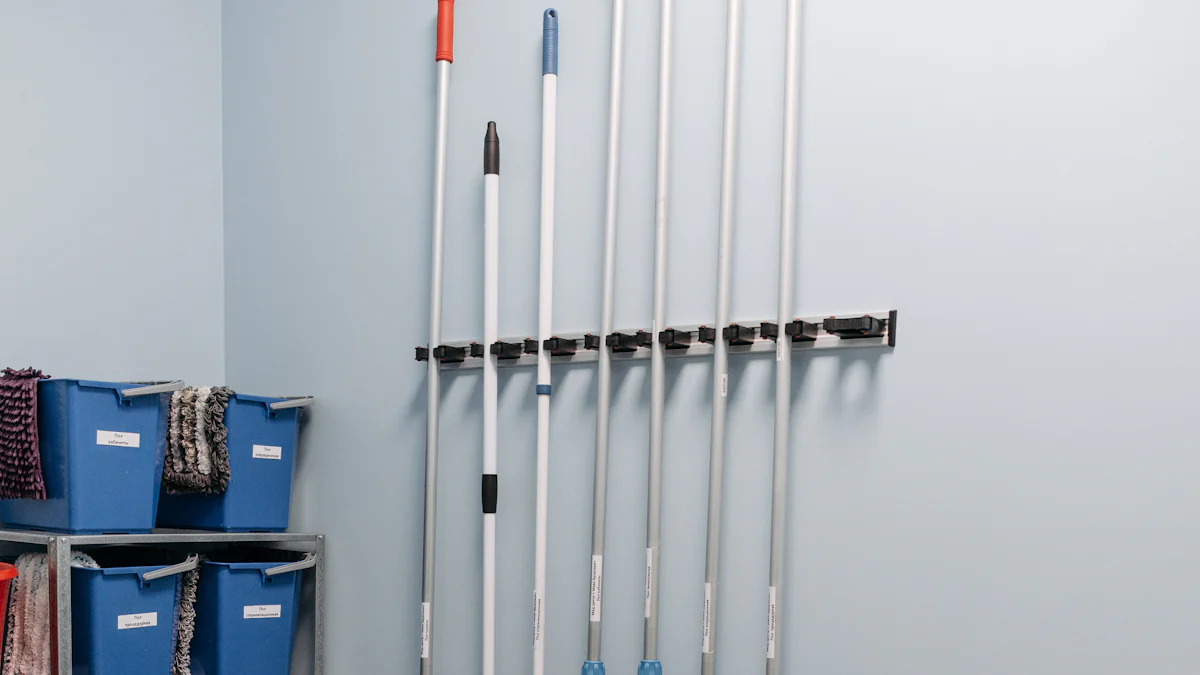
Preparation Phase
Safely Shutting Down the Reactor
The cleaning process begins with shutting down the reactor safely. Operators must follow the reactor’s specific shutdown procedures to ensure safety and prevent damage. This step typically involves cooling the reactor to a safe temperature and disconnecting it from power sources. Proper shutdown minimizes the risk of thermal shock to the susceptor and ensures a safe working environment for the cleaning process.
Removing the Susceptor from the Reactor
Once the reactor has cooled, the susceptor must be carefully removed. Operators should use appropriate tools to avoid scratching or damaging the surface. Handling the susceptor with clean, heat-resistant gloves prevents contamination from oils or particles. Proper removal ensures the susceptor remains intact and ready for the next cleaning phase.
Initial Cleaning
Removing Loose Particles and Debris
The initial cleaning phase focuses on eliminating loose particles and debris from the susceptor’s surface. Using a soft-bristle brush or compressed air effectively removes visible contaminants without causing scratches. This step is crucial because it prepares the surface for deeper cleaning by clearing away materials that could interfere with the application of cleaning agents.
Applying Cleaning Agents to the Surface
After removing loose debris, cleaning agents are applied to dissolve stubborn contaminants. Solvent-based solutions, such as a mixture of sulfuric acid and hydrogen peroxide, are highly effective in breaking down organic materials and metal residues. Operators should apply the solution evenly using lint-free wipes to ensure thorough coverage. This step not only cleans the surface but also enhances its compatibility for subsequent processes.
"The use of solvents is classified as the most effective method to remove impurities on the surface of silicon wafers." This principle applies equally to cleaning a si epitaxy susceptor, as solvents ensure optimal contaminant removal.
Deep Cleaning
Effective Scrubbing and Rinsing Techniques
Deep cleaning involves scrubbing the susceptor surface to remove any remaining contaminants. Soft-bristle brushes or ultrasonic baths are ideal for this step, as they provide thorough cleaning without damaging the material. After scrubbing, rinsing the susceptor with deionized water removes residual cleaning agents and particles. Proper rinsing ensures no chemical residues remain, which could affect the susceptor’s performance.
Thoroughly Drying the Susceptor
Drying the susceptor is the final step in the cleaning process. Operators should use lint-free wipes or air-drying techniques to ensure the surface is completely dry. Any remaining moisture can lead to oxidation or contamination during reinstallation. Thorough drying prepares the susceptor for inspection and ensures it is ready for optimal performance in the reactor.
Inspection and Reinstallation
Checking for Residual Contaminants
Inspecting the si epitaxy susceptor for residual contaminants is a critical step to ensure its readiness for reinstallation. Operators should use high-magnification microscopes or magnifiers to examine the surface meticulously. These tools help identify any remaining particles, stains, or residues that may compromise the susceptor’s performance. Surface testing equipment, such as profilometers or contact angle measurement devices, provides quantitative data on cleanliness. This ensures that the susceptor meets the required standards for optimal operation.
Residual contaminants, even in trace amounts, can disrupt the uniformity of epitaxial growth. Organic materials, for instance, may hinder the cleaning solution’s effectiveness during subsequent processes. Removing these impurities is essential to maintain the integrity of the deposition process. If contaminants are detected, operators should repeat the cleaning process, focusing on the affected areas. This step guarantees a contaminant-free surface, which is vital for achieving consistent and high-quality results.
"The use of solvents is classified as the most effective method to remove impurities on the surface of silicon wafers." This principle underscores the importance of thorough inspection and solvent-based cleaning to ensure the susceptor’s surface is free from defects.
Reinstalling the Susceptor for Optimal Performance
Reinstalling the susceptor requires precision and adherence to best practices. Operators must handle the susceptor with clean, heat-resistant gloves to prevent contamination from oils or particles. Aligning the susceptor correctly within the reactor ensures uniform heating and structural stability during the deposition process. Using appropriate tools minimizes the risk of scratches or misalignment, which could affect reactor efficiency.
Before powering up the reactor, operators should verify that all components are securely in place. This step prevents operational disruptions and ensures the susceptor functions as intended. Proper reinstallation not only optimizes the reactor’s performance but also extends the susceptor’s lifespan by reducing wear and tear caused by improper handling.
Regular inspection and careful reinstallation practices contribute significantly to the overall efficiency of the chemical vapor deposition process. These steps ensure that the susceptor remains in optimal condition, supporting consistent and defect-free epitaxial growth.
Common Mistakes to Avoid When Cleaning Si Epitaxy Susceptors
Using Harsh or Incompatible Cleaning Agents
Selecting the wrong cleaning agents can severely damage silicon carbide (SiC) susceptors. Harsh chemicals, such as strong acids or bases not designed for SiC surfaces, may corrode or weaken the material. Incompatible agents can also leave residues that interfere with epitaxial growth. For instance, while sulfuric acid and hydrogen peroxide mixtures are effective for organic debris removal, they must be used in controlled concentrations to avoid over-etching.
The RCA cleaning process, developed in 1965, serves as a foundational method for cleaning silicon surfaces. It emphasizes the importance of using appropriate chemical solutions tailored to specific materials. Following this principle ensures that cleaning agents effectively remove contaminants without compromising the susceptor’s integrity. Manufacturers should always verify the compatibility of cleaning solutions with SiC susceptors to maintain their performance and longevity.
"The use of solvents is classified as the most effective method to remove impurities on the surface of silicon wafers." This insight highlights the importance of selecting cleaning agents that align with the material’s properties.
Skipping Critical Steps Like Drying
Neglecting the drying phase after cleaning can lead to significant issues. Residual moisture on the susceptor surface promotes oxidation, which can create defects during the deposition process. Additionally, water droplets may trap contaminants, negating the benefits of prior cleaning steps. Proper drying ensures a contaminant-free and stable surface, ready for reinstallation.
Operators should prioritize thorough drying techniques, such as using lint-free wipes or air-drying methods. These approaches prevent watermarks and ensure no chemical residues remain. The solvent cleaning method, widely recognized for its effectiveness, underscores the importance of complete drying. By eliminating moisture, operators safeguard the susceptor’s performance and extend its lifespan.
Applying Excessive Force During Cleaning
Excessive force during cleaning can cause irreversible damage to SiC susceptors. Scratches or abrasions on the surface disrupt the uniformity required for epitaxial growth. These imperfections compromise heat distribution and lead to defects in the deposited layers. Operators must exercise caution when using mechanical tools, such as brushes or wipes, to avoid applying unnecessary pressure.
Soft-bristle brushes and ultrasonic baths offer effective yet gentle cleaning solutions. These tools remove stubborn residues without harming the susceptor’s surface. The use of advanced analysis techniques, such as those employed in ultra-high vacuum chemical vapor deposition (UHVCVD) conditions, further emphasizes the need for precision. Regular inspections with microscopes or magnifiers help identify potential damage early, ensuring the susceptor remains in optimal condition.
By avoiding these common mistakes, manufacturers can enhance the efficiency of their cleaning processes. Proper handling, appropriate chemical selection, and adherence to best practices ensure that SiC susceptors deliver consistent and high-quality performance in chemical vapor deposition reactors.
Neglecting a Regular Cleaning Schedule
Failing to establish a consistent cleaning schedule for Si epitaxy susceptors can lead to significant operational challenges. Over time, contaminants such as carbon residues, organic materials, and metal particles accumulate on the susceptor surface. These deposits disrupt the uniformity of epitaxial growth, resulting in defects that compromise the quality of semiconductor devices. Regular cleaning ensures that these impurities are removed before they can impact reactor performance.
A structured cleaning routine minimizes the risk of contamination buildup. Operators who neglect this practice often face increased downtime due to unplanned maintenance. For example, irregular cleaning schedules may allow stubborn residues to harden, making them more difficult to remove. This not only prolongs the cleaning process but also increases the likelihood of damage to the susceptor material. By adhering to a regular schedule, manufacturers can maintain optimal reactor efficiency and reduce the frequency of costly repairs.
"The RCA cleaning process, developed in 1965, laid the groundwork for many modern cleaning techniques." This principle highlights the importance of consistency in cleaning practices. Just as the RCA process revolutionized silicon wafer cleaning, a disciplined approach to susceptor maintenance ensures long-term reliability.
Implementing a cleaning schedule also supports the longevity of the susceptor. Deposits that remain on the surface for extended periods can corrode or weaken the material, leading to premature wear. Solvent cleaning methods, widely recognized for their effectiveness, play a crucial role in preventing such damage. These methods eliminate organic impurities and oils, ensuring that the susceptor remains in optimal condition for longer periods.
To establish an effective cleaning schedule, operators should consider the specific conditions of their reactors. Factors such as deposition frequency, material type, and operating temperatures influence the rate of contamination. Regular inspections using advanced analysis techniques, such as those employed under ultra-high vacuum chemical vapor deposition (UHVCVD) conditions, help identify the ideal cleaning intervals. These evaluations ensure that the schedule aligns with the reactor’s unique requirements.
Maintenance Tips for Long-Term Performance of Si Epitaxy Susceptors
Establishing a Consistent Cleaning Schedule
A consistent cleaning schedule ensures the long-term performance of a si epitaxy susceptor. Over time, contaminants such as carbon residues and metallic particles accumulate on the surface. These impurities disrupt the uniformity of epitaxial growth, leading to defects in semiconductor devices. Regular cleaning prevents this buildup and maintains optimal reactor efficiency.
The RCA cleaning process, introduced in 1965, revolutionized silicon wafer cleaning by emphasizing systematic and regular cleaning practices. This principle applies equally to susceptors. Operators should determine cleaning intervals based on reactor usage, deposition frequency, and material type. For example, high-frequency operations may require weekly cleaning, while less intensive processes might allow for monthly maintenance. A structured schedule minimizes downtime and reduces the risk of unexpected contamination-related issues.
"The RCA cleaning process laid the groundwork for many modern cleaning techniques." This historical insight highlights the importance of consistency in maintaining cleanliness standards.
Monitoring Reactor Conditions for Early Detection of Issues
Monitoring reactor conditions plays a critical role in identifying potential issues before they escalate. Parameters such as temperature, pressure, and gas flow rates directly affect the performance of the susceptor. Deviations from standard operating conditions often indicate contamination or wear. Early detection allows operators to address these problems promptly, preventing further damage.
Advanced diagnostic tools, including thermal imaging cameras and gas analyzers, provide real-time data on reactor conditions. These instruments help identify irregularities, such as hotspots or uneven heating, which may result from a contaminated susceptor. Regular inspections using microscopes or surface testing equipment further ensure that the susceptor remains in optimal condition. Proactive monitoring not only enhances reactor efficiency but also extends the lifespan of the susceptor.
Replacing Worn or Damaged Susceptors Promptly
Timely replacement of worn or damaged susceptors is essential for maintaining reactor performance. Prolonged use of a compromised susceptor can lead to severe defects in epitaxial layers, affecting the quality of semiconductor devices. Signs of wear, such as surface cracks, discoloration, or persistent contamination, indicate the need for replacement.
Operators should prioritize high-quality replacements that meet the specific requirements of their reactors. Proper handling during installation minimizes the risk of damage and ensures alignment within the reactor. Investing in durable susceptors reduces the frequency of replacements, contributing to cost savings and operational efficiency. By addressing wear and damage promptly, manufacturers can maintain consistent production quality and avoid costly downtime.
Training Staff on Proper Cleaning and Maintenance Techniques
Proper training equips staff with the knowledge and skills to clean and maintain Si epitaxy susceptors effectively. A well-trained team ensures consistent cleaning practices, reduces errors, and enhances the overall performance of chemical vapor deposition (CVD) reactors. Companies must prioritize structured training programs to standardize procedures and improve operational efficiency.
Key Components of Effective Training Programs
-
Understanding Material Properties
Training should begin with an overview of SiC susceptors and their role in CVD reactors. Staff must understand the material’s properties, such as its resistance to high temperatures and susceptibility to scratches. This foundational knowledge helps employees appreciate the importance of careful handling and proper cleaning techniques.
-
Step-by-Step Cleaning Procedures
Employees should receive detailed instructions on each phase of the cleaning process. This includes preparation, initial cleaning, deep cleaning, inspection, and reinstallation. Demonstrations using real equipment and tools enhance comprehension. For example, trainers can showcase the correct application of solvent-based cleaning agents, emphasizing their effectiveness in removing impurities.
-
Safety Protocols
Safety training is essential to protect staff from chemical exposure and physical injuries. Workers must learn to handle cleaning agents like sulfuric acid and hydrogen peroxide safely. Trainers should emphasize the use of protective gear, such as gloves, goggles, and lab coats, and demonstrate proper disposal methods for hazardous materials.
-
Inspection and Quality Assurance
Staff must develop skills to inspect susceptors for residual contaminants or damage. Training should include hands-on practice with microscopes, magnifiers, and surface testing equipment. Employees should learn to identify common issues, such as scratches or discoloration, and understand how these defects impact reactor performance.
Benefits of Regular Training Updates
Regular updates to training programs ensure that staff stays informed about advancements in cleaning techniques and equipment. For instance, the introduction of ultrasonic baths or new chemical solutions may require adjustments to existing procedures. Continuous education fosters adaptability and keeps the team aligned with industry best practices.
"The RCA cleaning process, introduced in 1965, revolutionized silicon wafer cleaning by establishing systematic methods." This historical milestone underscores the importance of structured and consistent training. Just as the RCA process standardized silicon wafer cleaning, regular staff training ensures uniformity and precision in susceptor maintenance.
Encouraging a Culture of Accountability
A culture of accountability motivates employees to adhere to cleaning protocols and maintain high standards. Supervisors should conduct periodic evaluations to assess staff performance and provide constructive feedback. Recognizing and rewarding employees who excel in their roles reinforces positive behavior and encourages others to follow suit.
Leveraging Technology for Training
Modern technology enhances training effectiveness. Virtual reality (VR) simulations, for example, allow employees to practice cleaning techniques in a controlled environment. Online modules and video tutorials provide accessible resources for self-paced learning. These tools complement hands-on training and ensure that staff gains a comprehensive understanding of susceptor maintenance.
By investing in thorough and ongoing training, companies can optimize the cleaning and maintenance of Si epitaxy susceptors. A knowledgeable and skilled workforce minimizes errors, extends the lifespan of susceptors, and supports the consistent production of high-quality semiconductor devices.
Proper cleaning of a si epitaxy susceptor ensures the efficiency and longevity of CVD reactors. Following systematic steps, using appropriate tools, and avoiding common errors guarantees optimal performance. Regular maintenance eliminates contaminants that compromise epitaxial growth and reduces downtime. Industry experts emphasize the importance of refining cleaning techniques, such as matching megasonic energy with cleaning solutions, to achieve superior results. Consistent cleaning practices not only extend the lifespan of susceptors but also support high-quality semiconductor manufacturing, ensuring reliable and defect-free production.
FAQ
What is the primary purpose of cleaning Si epitaxy susceptors?
Cleaning Si epitaxy susceptors ensures the removal of contaminants like carbon residues and metallic particles.
How often should Si epitaxy susceptors be cleaned?
The cleaning frequency depends on reactor usage and deposition processes. High-frequency operations may require weekly cleaning, while less intensive processes might allow for monthly maintenance. Regular inspections help determine the ideal cleaning intervals to prevent contamination buildup and maintain optimal performance.
What are the most effective cleaning agents for SiC susceptors?
Chemical solutions such as a mixture of sulfuric acid and hydrogen peroxide are highly effective for removing organic debris and metal ion contamination. Wet cleaning methods like RCA cleaning are widely recommended for their ability to eliminate oxidized residues. It is crucial to use cleaning agents specifically designed for SiC susceptors to avoid material damage.
Can cleaning be performed without removing the susceptor from the reactor?
Yes, in situ cleaning methods allow for cleaning without removing the susceptor. Techniques such as plasma cleaning or hydrogen-based processes minimize downtime while effectively removing contaminants. However, these methods may not address deep-seated residues, making periodic removal and thorough cleaning necessary.
What tools are essential for cleaning Si epitaxy susceptors?
Key tools include soft-bristle brushes, lint-free wipes, and ultrasonic baths for physical cleaning. Inspection tools like microscopes and surface testing equipment ensure thorough contaminant removal. Protective gear, such as gloves and goggles, is also essential for safe handling of cleaning agents.
How does contamination affect the performance of CVD reactors?
Contamination on susceptors creates uneven surfaces, disrupting heat distribution and causing defects in epitaxial layers. This leads to reduced reactor efficiency and compromised semiconductor quality. Regular cleaning eliminates these issues, ensuring consistent and defect-free production.
What safety precautions should be taken during the cleaning process?
Operators must wear protective gloves, goggles, and lab coats to prevent chemical exposure. Cleaning should be conducted in well-ventilated areas or under fume hoods. Proper storage and disposal of cleaning agents, along with adherence to Material Safety Data Sheets (MSDS), ensure safety during the process.
What are the benefits of using ultrasonic baths for cleaning?
Ultrasonic baths provide a non-invasive method to dislodge particles from hard-to-reach areas. They use high-frequency sound waves to create microscopic bubbles that effectively remove contaminants. This technique ensures thorough cleaning without damaging the susceptor surface.
How can operators ensure the susceptor is free of contaminants after cleaning?
Inspection tools like high-magnification microscopes and surface profilometers help identify residual contaminants. Surface testing equipment provides quantitative data on cleanliness. Operators should repeat the cleaning process if any impurities remain to ensure the susceptor meets required standards.
Why is a consistent cleaning schedule important?
A consistent cleaning schedule prevents the buildup of contaminants that can corrode or weaken the susceptor material. It reduces downtime caused by unplanned maintenance and ensures the reactor operates efficiently. Regular cleaning also extends the lifespan of susceptors, supporting long-term performance.