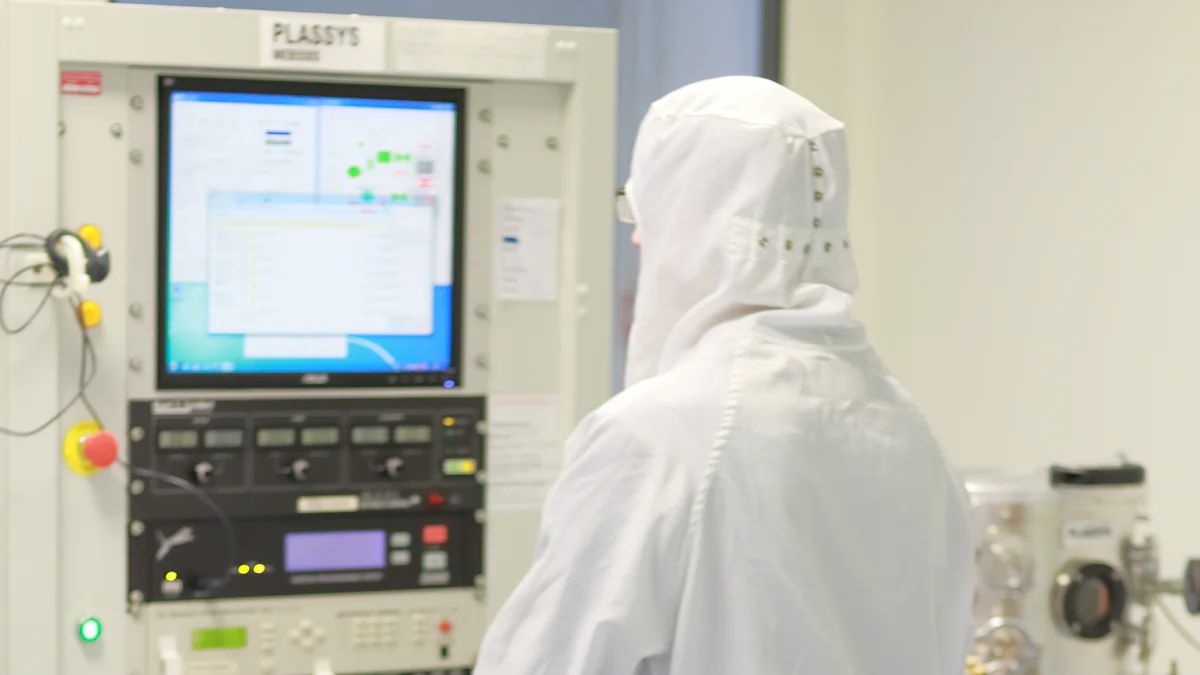
Silicon wafer carriers play a pivotal role in semiconductor manufacturing. They ensure the safe handling of wafers while maintaining cleanliness and preventing contamination. The right si wafer carrier enhances process efficiency by minimizing damage risks and supporting precise operations. Manufacturers must carefully align carrier selection with specific application requirements to achieve optimal performance. This decision directly impacts the quality and reliability of semiconductor devices, making it a critical factor in production success.
Key Takeaways
- Si wafer carriers are essential for protecting silicon wafers from damage and contamination during semiconductor manufacturing.
- Choosing the right carrier material—plastic, metal, composite, or high-end materials—affects performance, durability, and cost.
- Open cassette carriers offer flexibility and easy access, making them ideal for research and development, while closed pod carriers excel in contamination control for cleanroom environments.
- Automated wafer carriers enhance efficiency in high-volume production by reducing human error and ensuring precise handling.
- Custom-designed carriers can address specific manufacturing needs, improving compatibility with advanced equipment and enhancing overall process reliability.
- Selecting the appropriate wafer carrier is crucial for maintaining wafer integrity and ensuring the production of high-quality semiconductor devices.
Overview of Si Wafer Carriers
What Are Si Wafer Carriers?
Definition and purpose in semiconductor manufacturing.
Si wafer carriers serve as essential tools in semiconductor manufacturing. These carriers provide a secure platform for transporting and handling silicon wafers during various stages of production. Their primary purpose is to protect wafers from physical damage, contamination, and environmental exposure. By ensuring stability and cleanliness, they contribute to the overall quality and reliability of semiconductor devices.
Common applications and significance in wafer handling.
Manufacturers rely on si wafer carriers in multiple applications, including wafer storage, transportation, and processing. These carriers play a critical role in maintaining wafer integrity during high-precision operations such as etching, deposition, and lithography. Their use minimizes contamination risks and ensures that wafers remain free from defects. In cleanroom environments, they act as a barrier against airborne particles, safeguarding the delicate surfaces of silicon wafers.
Key Features of Si Wafer Carriers
Material composition and its impact on performance.
The material composition of a si wafer carrier significantly influences its performance. Common materials include plastics, metals, and composites, each offering unique benefits. Plastic carriers are lightweight and cost-effective, making them suitable for general applications. Metal carriers provide superior durability and thermal stability, ideal for high-temperature processes. Composite materials balance weight, strength, and customization, catering to specialized needs. The choice of material directly affects the carrier’s ability to withstand mechanical stress, temperature variations, and chemical exposure.
Design considerations for different manufacturing environments.
Design plays a pivotal role in adapting si wafer carriers to specific manufacturing environments. Open cassette designs offer flexibility and easy access, making them suitable for research and development settings. Closed pod designs, such as FOUPs and SMIF pods, provide enhanced contamination control, essential for cleanroom operations. Custom-designed carriers address unique process requirements, ensuring compatibility with advanced equipment and automation systems. Manufacturers must evaluate their operational needs to select the most appropriate design.
Functional requirements for modern semiconductor processes.
Modern semiconductor processes demand carriers that meet stringent functional requirements. High-temperature resistance is crucial for processes involving thermal treatments. Compatibility with automated systems ensures seamless integration into high-volume production lines. Contamination control features, such as sealed enclosures and anti-static properties, maintain wafer cleanliness. Additionally, carriers must support precise alignment and positioning to facilitate accurate processing. Meeting these requirements enhances efficiency and reduces the risk of defects in semiconductor devices.
Types of Si Wafer Carriers
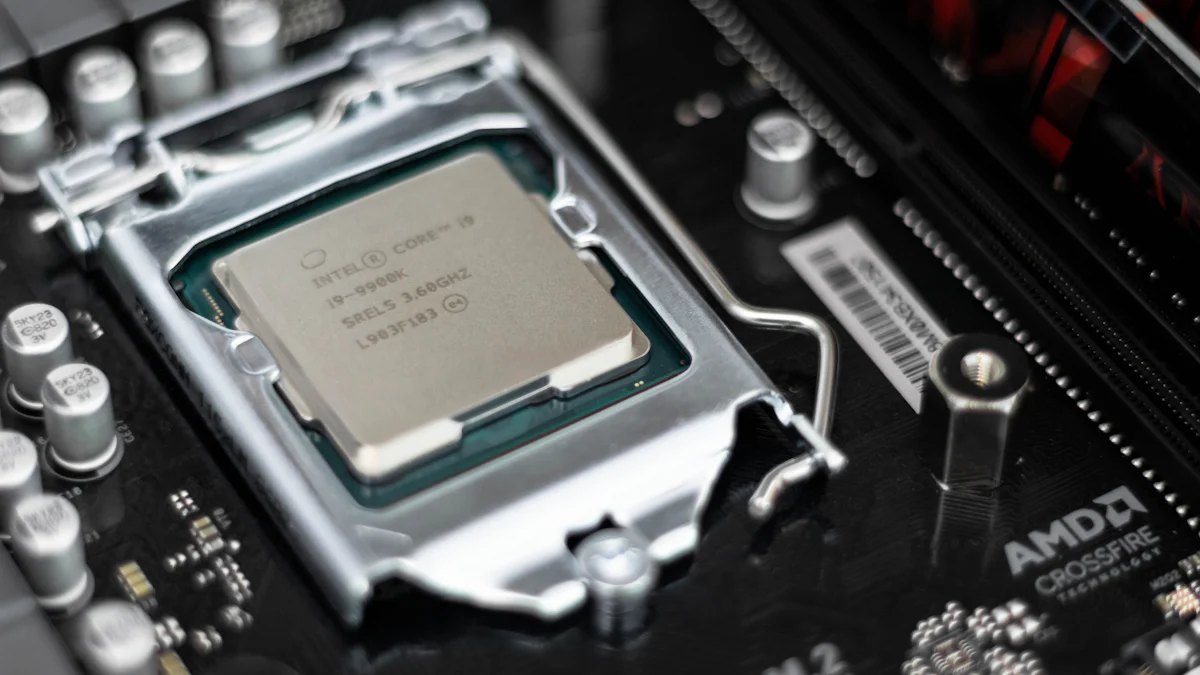
Categorization by Material
Plastic wafer carriers: Lightweight and cost-effective.
Plastic wafer carriers offer a practical solution for general semiconductor applications. Their lightweight nature simplifies handling and reduces strain during transportation. Manufacturers often choose these carriers for their affordability, making them a cost-effective option for high-volume production. Despite their economic advantages, plastic carriers maintain sufficient durability for standard processes. However, they may not withstand extreme temperatures or harsh chemical environments, limiting their use in specialized applications.
Metal wafer carriers: Durable with excellent thermal stability.
Metal wafer carriers excel in environments requiring high durability and thermal stability. These carriers resist mechanical stress and maintain structural integrity under elevated temperatures. Their robust design makes them suitable for processes such as thermal treatments and high-temperature deposition. While metal carriers provide superior performance, their higher cost and potential for particle generation require careful consideration. Proper maintenance and cleaning protocols can mitigate contamination risks, ensuring reliable operation.
Composite material carriers: Customizable and balanced performance.
Composite material carriers combine the strengths of multiple materials to deliver balanced performance. These carriers offer a unique blend of lightweight construction, durability, and customization options. Engineers can tailor composite carriers to meet specific process requirements, enhancing compatibility with advanced equipment. Their versatility makes them ideal for applications demanding both strength and adaptability. Although more expensive than plastic carriers, their long-term benefits often justify the investment.
High-end materials (e.g., glass, quartz, silicon): Superior thermal and chemical resistance.
High-end wafer carriers, crafted from materials like glass, quartz, or silicon, provide unmatched thermal and chemical resistance. These carriers perform exceptionally well in demanding processes involving extreme temperatures or corrosive chemicals. Their ultra-flat surfaces ensure precise wafer alignment, reducing the risk of defects during critical operations. Due to their premium properties, high-end carriers are often reserved for specialized applications where performance outweighs cost considerations.
Categorization by Design
Open cassette carriers: Flexible and accessible.
Open cassette carriers prioritize flexibility and accessibility. Their open design allows operators to load and unload wafers quickly, making them suitable for research and development environments. These carriers support easy inspection and manual handling, streamlining processes that require frequent wafer access. However, their open structure offers limited protection against contamination, restricting their use in cleanroom settings.
Closed pod carriers (FOUPs and SMIF): Enhanced contamination control.
Closed pod carriers, including FOUPs (Front Opening Unified Pods) and SMIF (Standard Mechanical Interface) pods, provide superior contamination control. Their sealed enclosures protect wafers from airborne particles and environmental exposure, ensuring cleanliness in sensitive manufacturing processes. These carriers integrate seamlessly with automated systems, enhancing efficiency in high-volume production lines. Although more expensive than open designs, their contamination prevention capabilities make them indispensable in cleanroom environments.
Custom-designed carriers: Tailored for specific processes.
Custom-designed carriers address unique manufacturing challenges by offering tailored solutions. Engineers design these carriers to meet specific process requirements, ensuring compatibility with specialized equipment and workflows. Custom carriers often incorporate advanced features, such as anti-static properties or enhanced thermal resistance, to optimize performance. While their development involves higher costs and longer lead times, the resulting precision and reliability justify the investment for critical applications.
Categorization by Functionality
Static wafer carriers: Simpler and cost-effective.
Static wafer carriers provide a straightforward solution for basic wafer handling needs. Their simple design minimizes complexity, making them an economical choice for low-volume or less demanding processes. These carriers perform well in environments where automation is unnecessary. However, their manual operation limits efficiency in large-scale production settings.
Automated wafer carriers: Ideal for high-volume production.
Automated wafer carriers support seamless integration with advanced manufacturing systems. These carriers enable precise wafer handling and alignment, reducing human intervention and minimizing errors. Their compatibility with robotics and automation enhances throughput in high-volume production environments. Although their initial cost is higher, automated carriers deliver long-term efficiency gains, making them a valuable asset for large-scale operations.
High-temperature-resistant carriers: Suitable for demanding processes.
High-temperature-resistant carriers withstand extreme thermal conditions, ensuring reliable performance in processes such as annealing and diffusion. These carriers maintain structural integrity and prevent wafer deformation under intense heat. Manufacturers often select materials like metal or specialized composites for these carriers to achieve optimal thermal stability. Their ability to endure harsh conditions makes them essential for demanding semiconductor applications.
Advantages and Disadvantages of Different Si Wafer Carriers
Plastic Wafer Carriers
Advantages: Lightweight, affordable, and versatile.
Plastic wafer carriers offer significant advantages for semiconductor manufacturing. Their lightweight structure simplifies handling and reduces operator fatigue during manual operations. Manufacturers often choose these carriers for their affordability, making them a cost-effective solution for high-volume production environments. Their versatility allows them to adapt to various wafer sizes and processes, ensuring compatibility with standard manufacturing equipment. These carriers also resist corrosion, which enhances their longevity in less demanding applications.
Disadvantages: Limited durability and thermal resistance.
Despite their benefits, plastic wafer carriers face limitations in durability and thermal resistance. They may deform or lose structural integrity when exposed to high temperatures, restricting their use in processes involving thermal treatments. Their susceptibility to mechanical stress increases the risk of damage during rigorous handling or transportation. Additionally, plastic carriers can generate static electricity, which may pose contamination risks in sensitive environments. These drawbacks make them less suitable for advanced or high-precision semiconductor applications.
Metal Wafer Carriers
Advantages: High durability and thermal stability.
Metal wafer carriers excel in applications requiring strength and thermal stability. Their robust construction withstands mechanical stress, ensuring reliable performance during demanding processes. These carriers maintain their structural integrity under extreme temperatures, making them ideal for thermal treatments such as annealing and diffusion. Their long lifespan reduces the need for frequent replacements, offering cost savings over time. Manufacturers value their ability to support precise wafer alignment, which enhances process accuracy.
Disadvantages: Higher cost and potential contamination risks.
The higher cost of metal wafer carriers often deters manufacturers with budget constraints. Their weight can also complicate handling, especially in manual operations. Metal surfaces may generate particles or react with certain chemicals, increasing the risk of wafer contamination. Regular maintenance and cleaning are essential to mitigate these risks, which adds to operational complexity. These factors require careful consideration when selecting metal carriers for specific applications.
Composite Material Carriers
Advantages: Balanced weight, durability, and customization.
Composite material carriers provide a balanced combination of lightweight design, durability, and adaptability. Engineers can customize these carriers to meet unique process requirements, ensuring compatibility with specialized equipment. Their resistance to mechanical stress and temperature variations makes them suitable for a wide range of semiconductor applications. These carriers also offer anti-static properties, which help maintain wafer cleanliness in sensitive environments. Their versatility supports both standard and advanced manufacturing processes.
Disadvantages: Higher cost compared to plastic carriers.
The primary drawback of composite material carriers lies in their cost. They are more expensive than plastic alternatives, which may limit their use in cost-sensitive operations. Customization options, while beneficial, often involve longer lead times and additional expenses. Manufacturers must weigh the long-term benefits of durability and adaptability against the initial investment. Despite these challenges, composite carriers remain a preferred choice for applications demanding high performance and reliability.
Open vs. Closed Designs
Open carriers: Easy access but less protection.
Open carriers provide a straightforward solution for wafer handling. Their design allows operators to load and unload wafers quickly, making them ideal for environments requiring frequent manual intervention. Research and development facilities often favor these carriers due to their accessibility and simplicity. Operators can inspect wafers directly without additional steps, which streamlines processes that demand flexibility.
However, open carriers offer limited protection against contamination. Airborne particles and environmental factors can easily reach the wafers, increasing the risk of defects. These carriers are less suitable for cleanroom environments or high-precision manufacturing processes. Manufacturers must weigh the benefits of accessibility against the potential for contamination when considering open carriers.
Closed carriers: Superior protection but higher cost.
Closed carriers, such as FOUPs (Front Opening Unified Pods) and SMIF pods, excel in contamination-sensitive environments. Their sealed enclosures shield wafers from airborne particles, moisture, and other contaminants. Cleanroom operations rely on these carriers to maintain wafer integrity during critical processes. Their compatibility with automated systems enhances efficiency in high-volume production lines.
The advanced design of closed carriers comes with higher costs. Their initial investment and maintenance requirements may deter manufacturers with budget constraints. Additionally, their sealed structure limits direct access to wafers, which can complicate manual inspections. Despite these challenges, closed carriers remain indispensable for applications prioritizing cleanliness and precision.
Static vs. Automated Carriers
Static carriers: Cost-effective but less efficient.
Static carriers offer a simple and economical option for wafer handling. Their straightforward design reduces manufacturing costs, making them suitable for low-volume or less demanding processes. Operators can use these carriers effectively in environments where automation is unnecessary. Their durability and ease of use make them a practical choice for basic applications.
However, static carriers lack the efficiency of automated solutions. Manual handling increases the risk of human error, which can lead to wafer misalignment or damage. These carriers also slow down production in high-volume settings, where speed and precision are critical. Manufacturers must consider the trade-off between cost savings and operational efficiency when selecting static carriers.
Automated carriers: High efficiency but expensive.
Automated carriers integrate seamlessly with advanced manufacturing systems. These carriers support precise wafer handling, reducing the need for human intervention. Robotics and automation enhance throughput, making automated carriers ideal for large-scale production. Their ability to maintain consistent alignment minimizes defects, which improves overall process reliability.
The high cost of automated carriers presents a significant barrier for some manufacturers. Their complex design requires a substantial initial investment and ongoing maintenance. Additionally, integrating these carriers into existing systems may involve significant time and resources. Despite these challenges, automated carriers deliver long-term benefits in efficiency and productivity, justifying their use in high-volume semiconductor manufacturing.
Application-Specific Recommendations
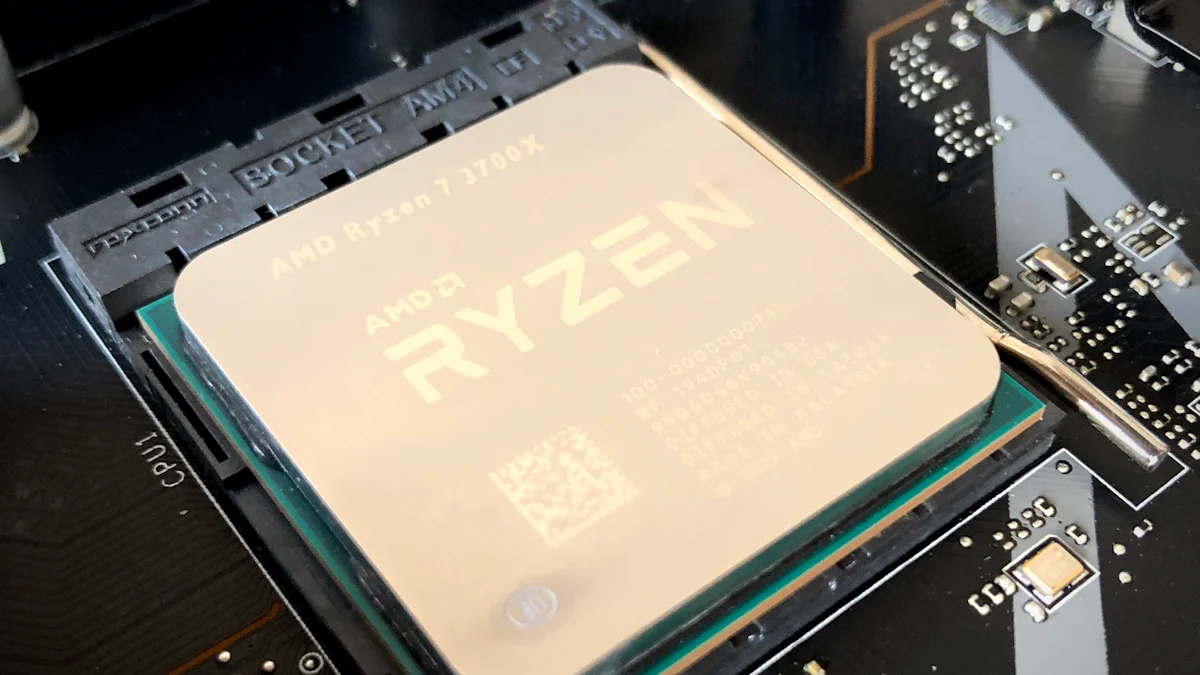
High-Volume Manufacturing
Recommended carriers: Automated closed pod carriers for efficiency.
High-volume manufacturing environments demand precision and speed. Automated closed pod carriers meet these requirements by integrating seamlessly with advanced production systems. These carriers ensure consistent wafer handling, reducing the risk of human error. Their sealed design protects wafers from contamination, maintaining cleanliness throughout the process. Manufacturers benefit from increased throughput and reduced downtime, as these carriers support efficient operations in cleanroom settings. The initial investment in automated closed pod carriers often pays off through long-term productivity gains and enhanced product quality.
Research and Development
Recommended carriers: Open cassette carriers for flexibility.
Research and development processes require flexibility to accommodate frequent adjustments and manual interventions. Open cassette carriers provide easy access to wafers, enabling researchers to inspect and handle them without delays. Their simple design supports quick loading and unloading, which is essential in experimental setups. These carriers also allow compatibility with various wafer sizes and equipment configurations. While they lack the contamination control of closed designs, their accessibility makes them ideal for non-cleanroom environments where adaptability takes precedence over stringent cleanliness requirements.
High-Temperature Processes
Recommended carriers: Metal or composite carriers with thermal resistance.
High-temperature processes, such as annealing and diffusion, place significant demands on wafer carriers. Metal carriers excel in these conditions due to their superior thermal stability and mechanical strength. They maintain structural integrity under extreme heat, ensuring reliable wafer support. Composite carriers offer an alternative solution, combining lightweight construction with excellent thermal resistance. Their customizable properties allow manufacturers to tailor them for specific high-temperature applications. Both options minimize the risk of wafer deformation, ensuring consistent results in demanding semiconductor processes.
Cleanroom Environments
Recommended carriers: Closed pod carriers for contamination control.
Cleanroom environments demand strict contamination control to ensure wafer integrity. Closed pod carriers, such as FOUPs (Front Opening Unified Pods) and SMIF pods, excel in maintaining cleanliness during wafer handling and transportation. Their sealed enclosures create a barrier against airborne particles, moisture, and other contaminants. This feature makes them indispensable for processes requiring ultra-clean conditions.
Manufacturers rely on closed pod carriers to protect wafers during critical stages of semiconductor production. These carriers integrate seamlessly with automated systems, reducing human intervention and minimizing contamination risks. Their robust design ensures compatibility with cleanroom protocols, supporting high-volume production without compromising wafer quality.
The advanced engineering of closed pod carriers enhances their functionality. Anti-static properties prevent the buildup of static electricity, which could attract particles to wafer surfaces. Their precise alignment mechanisms ensure wafers remain stable during transport, reducing the risk of damage. Although these carriers involve higher costs, their ability to safeguard wafers in cleanroom environments justifies the investment.
"In cleanroom manufacturing, contamination is the enemy of precision," as noted by industry experts. Closed pod carriers provide the necessary defense, enabling manufacturers to meet stringent cleanliness standards while maintaining operational efficiency.
Specialized Applications
Recommended carriers: High-end materials like quartz or silicon for demanding processes.
Specialized semiconductor applications often require carriers made from high-end materials such as quartz or silicon. These materials offer exceptional thermal stability and chemical resistance, making them ideal for processes involving extreme temperatures or corrosive chemicals. Their ultra-flat surfaces ensure precise wafer alignment, which is critical for achieving defect-free results in advanced manufacturing.
Quartz and silicon carriers perform exceptionally well in niche applications, including photolithography and etching. Their ability to withstand harsh conditions ensures consistent performance, even in the most demanding environments. Manufacturers select these carriers for their reliability and compatibility with cutting-edge equipment.
High-end carriers also support innovation in semiconductor technology. Their superior properties enable the production of next-generation devices with higher performance and smaller geometries. While their cost may be prohibitive for standard applications, their value becomes evident in processes where precision and durability are paramount.
According to recent advancements in semiconductor manufacturing, "High-end materials like quartz and silicon are redefining the limits of wafer carrier performance." These carriers empower manufacturers to push boundaries, delivering unparalleled results in specialized applications.
Selecting the right si wafer carrier is crucial for achieving efficiency and precision in semiconductor manufacturing. Each carrier type offers unique advantages and limitations, from the affordability of plastic carriers to the durability of metal and the advanced capabilities of high-end materials. Manufacturers must evaluate their specific needs, considering factors like cost, durability, and functionality. Aligning carrier selection with application requirements ensures optimal performance and minimizes risks. By making informed choices, manufacturers can enhance productivity, maintain wafer integrity, and support the development of high-quality semiconductor devices.
FAQ
What is the primary purpose of Si wafer carriers in semiconductor manufacturing?
Si wafer carriers ensure the safe handling and transportation of silicon wafers. They protect wafers from physical damage, contamination, and environmental exposure during various stages of production. Their role is critical in maintaining wafer integrity and ensuring high-quality semiconductor devices.
How do different materials impact the performance of Si wafer carriers?
The material composition of a wafer carrier directly affects its durability, thermal resistance, and chemical stability. For instance:
- Plastic carriers are lightweight and cost-effective but lack thermal resistance.
- Metal carriers offer superior durability and withstand high temperatures but may pose contamination risks.
Composite carriers balance strength, weight, and adaptability, making them suitable for specialized applications.
High-end materials like quartz or silicon provide exceptional thermal and chemical resistance for demanding processes.
What are the advantages of using closed pod carriers in cleanroom environments?
Closed pod carriers, such as FOUPs and SMIF pods, excel in contamination-sensitive environments. Their sealed design prevents airborne particles, moisture, and other contaminants from reaching the wafers. These carriers also integrate with automated systems, enhancing efficiency and maintaining cleanliness in high-volume production.
Why are automated wafer carriers preferred for high-volume manufacturing?
Automated wafer carriers streamline production by integrating with advanced manufacturing systems. They reduce human intervention, ensuring precise wafer handling and alignment. This minimizes errors and increases throughput, making them ideal for large-scale operations. Although their initial cost is higher, they deliver long-term efficiency and productivity gains.
Are plastic wafer carriers suitable for high-temperature processes?
Plastic wafer carriers are not ideal for high-temperature processes. They lack the thermal resistance required to maintain structural integrity under extreme heat. Manufacturers typically choose metal or composite carriers for applications involving thermal treatments like annealing or diffusion.
What factors should manufacturers consider when selecting a wafer carrier?
Manufacturers should evaluate several factors, including:
- Application requirements: High-temperature processes demand carriers with thermal resistance.
- Contamination control: Cleanroom environments require sealed designs like closed pod carriers.
- Cost considerations: Plastic carriers are affordable, while high-end materials involve higher costs.
- Durability and functionality: The carrier must withstand mechanical stress and integrate with automation systems if needed.
How do open cassette carriers differ from closed pod carriers?
Open cassette carriers prioritize accessibility and flexibility. They allow quick loading and unloading, making them suitable for research and development. However, they offer limited protection against contamination. Closed pod carriers, on the other hand, provide superior contamination control with sealed enclosures, making them essential for cleanroom environments.
Can custom-designed carriers improve manufacturing efficiency?
Custom-designed carriers address specific manufacturing challenges. Engineers tailor these carriers to meet unique process requirements, ensuring compatibility with specialized equipment. Features like anti-static properties or enhanced thermal resistance optimize performance, improving efficiency and reliability in critical applications.
What makes high-end wafer carriers suitable for specialized applications?
High-end wafer carriers, made from materials like quartz or silicon, offer unmatched thermal stability and chemical resistance. Their ultra-flat surfaces ensure precise wafer alignment, reducing defects in advanced manufacturing processes. These carriers perform exceptionally well in niche applications, such as photolithography and etching.
How does carrier selection impact semiconductor device quality?
The choice of wafer carrier directly influences wafer safety, cleanliness, and process efficiency. A well-suited carrier minimizes contamination risks, prevents physical damage, and supports precise operations. This ensures the production of high-quality semiconductor devices with consistent performance and reliability.