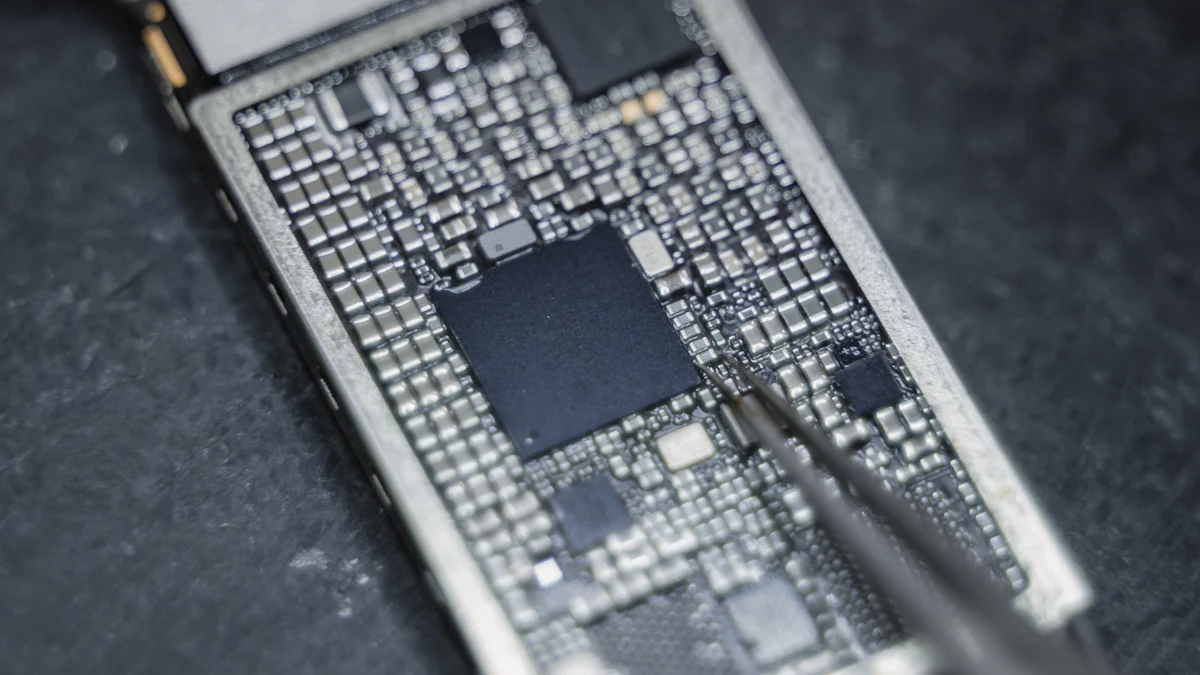
Silicon stands as the backbone of modern semiconductor technology. Its unique combination of properties, including high thermal stability and excellent electrical conductivity, makes it indispensable for electronic applications. Found abundantly in the Earth’s crust, silicon ensures a steady and cost-effective supply for industrial needs. The ability to refine silicon to an ultra-high purity level of 99.9999999% further enhances its suitability for manufacturing integrated circuits and microprocessors. Additionally, silicon wafers dominate the global market, with their applications spanning industries such as consumer electronics, healthcare, and aerospace, driving innovation and technological advancement.
Key Takeaways
Silicon’s unique properties make it essential for modern semiconductor technology.
- The abundance of silicon in the Earth’s crust ensures a steady and cost-effective supply, supporting large-scale production in various industries.
- Silicon’s optimal bandgap of approximately 1.1 electron volts allows for efficient energy conversion, making it ideal for integrated circuits and microprocessors.
- The ability to easily dope silicon wafers enables precise customization for specific electronic applications, enhancing their versatility.
- Silicon wafers exhibit exceptional mechanical strength, ensuring durability during manufacturing and operation, which reduces the risk of damage.
Silicon remains a cost-effective choice for wafer production, outperforming alternatives like germanium and gallium arsenide in terms of affordability and scalability.
- The formation of a stable silicon dioxide layer is crucial for creating reliable transistors and integrated circuits, enhancing the performance of electronic devices.
Silicon’s Physical and Chemical Properties
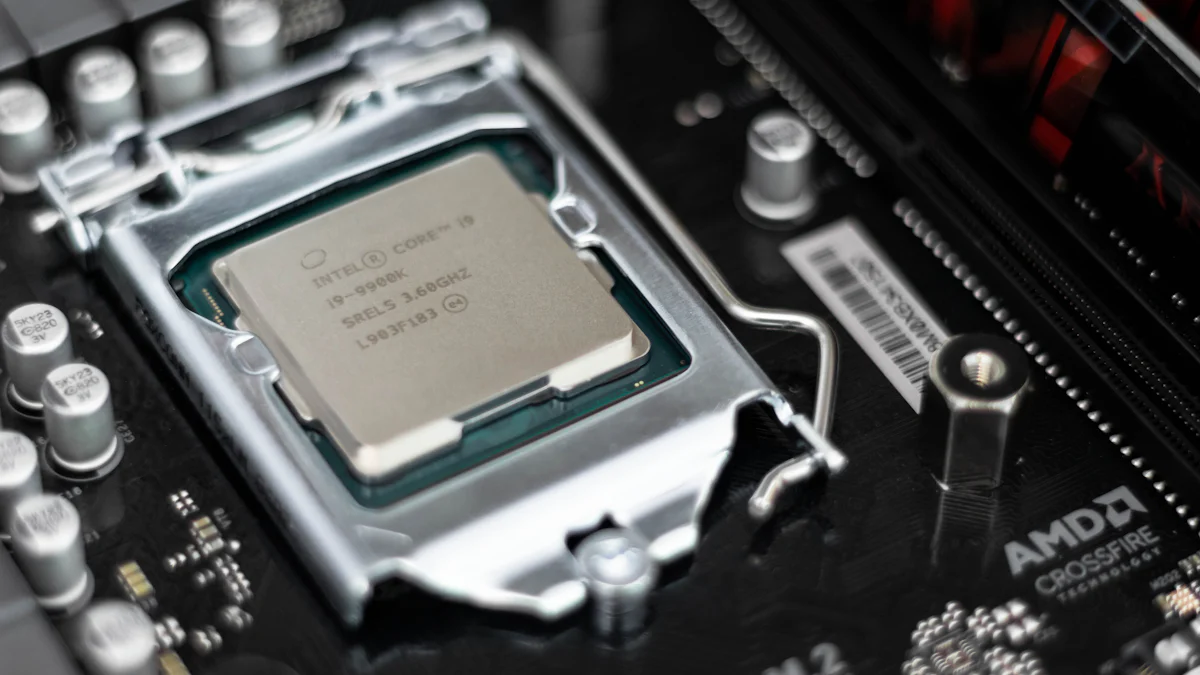
Stability and Abundance
High thermal and chemical stability
Silicon exhibits remarkable thermal and chemical stability, making it a cornerstone of semiconductor technology. Its ability to withstand high temperatures without degrading ensures reliable performance in electronic devices. This stability also allows silicon to endure harsh chemical environments during manufacturing processes, maintaining its integrity and functionality. These characteristics make it an ideal material for producing durable and efficient silicon wafers.
Earth’s crust contains an abundant supply of silicon
Silicon ranks as the second most abundant element in the Earth’s crust, following oxygen. Found in the form of silica and silicates, it is readily available for industrial use. This abundance ensures a consistent and cost-effective supply, which is crucial for large-scale production. The widespread availability of silicon has solidified its position as the primary material for semiconductor manufacturing.
Semiconductor Band Structure
Optimal bandgap for electronic applications
Silicon’s bandgap, measuring approximately 1.1 electron volts, is perfectly suited for electronic applications. This optimal bandgap enables silicon to function effectively as a semiconductor, allowing precise control over electrical conductivity. It strikes a balance between energy efficiency and performance, making it ideal for integrated circuits and microprocessors.
Efficient energy conversion and minimal leakage
The band structure of silicon facilitates efficient energy conversion, reducing power loss during operation. Its ability to minimize leakage currents enhances the reliability of electronic devices. These properties contribute to the widespread adoption of silicon wafers in industries requiring high-performance semiconductors.
Ability to Form an Oxide Layer
Silicon dioxide as an excellent insulator
Silicon naturally forms a thin layer of silicon dioxide when exposed to oxygen. This oxide layer acts as an exceptional insulator, preventing electrical currents from leaking between components. Its insulating properties are critical for the development of advanced electronic devices, ensuring their safety and efficiency.
Essential for creating transistors and integrated circuits
The formation of a stable oxide layer is essential for manufacturing transistors and integrated circuits. Silicon dioxide serves as a dielectric material, enabling the precise control of electrical signals within devices. This capability has revolutionized the semiconductor industry, allowing the production of compact and powerful electronic components.
Practical Advantages of Silicon Wafers
Ease of Doping
Simple integration of impurities to control conductivity
Silicon wafers offer unmatched flexibility in tailoring electrical properties. Manufacturers can easily introduce controlled amounts of impurities, a process known as doping, to adjust the material’s conductivity. This precise manipulation allows silicon to function effectively in various electronic applications, from microprocessors to solar cells. The simplicity of doping silicon ensures consistent results, making it a preferred choice for semiconductor production.
Enables precise customization for various applications
The doping process enables engineers to customize silicon wafers for specific applications. By altering the type and concentration of impurities, they can create wafers with unique electrical characteristics. This adaptability supports the development of a wide range of devices, including high-speed processors, memory chips, and power management systems. The ability to fine-tune silicon’s properties underscores its versatility in the electronics industry.
Mechanical Strength
Durable and resistant to physical stress
Silicon wafers exhibit exceptional mechanical strength, which ensures their durability during manufacturing and operation. Their robust structure withstands physical stress, reducing the risk of damage during handling or processing. This resilience makes silicon an ideal material for producing reliable and long-lasting electronic components.
Suitable for handling in manufacturing processes
The mechanical properties of silicon wafers simplify their integration into industrial processes. Their strength allows them to endure rigorous manufacturing steps, such as cutting, polishing, and etching, without compromising quality. This reliability streamlines production workflows, ensuring efficiency and consistency in semiconductor fabrication.
Scalability and Cost-Effectiveness
Efficient for mass production of wafers
Silicon wafers support large-scale production due to their scalability. The material’s abundance and ease of processing enable manufacturers to produce wafers in significant quantities. Additionally, silicon’s ability to grow into large, defect-free single crystals ensures high yields, reducing waste and improving efficiency. This scalability meets the demands of industries requiring mass production, such as consumer electronics and automotive sectors.
Lower cost compared to alternative materials
Silicon remains a cost-effective option for wafer production. Its widespread availability in the Earth’s crust and established manufacturing techniques contribute to its affordability. In contrast, alternatives like silicon carbide, though stronger, are significantly more expensive and challenging to process. Silicon wafers strike a balance between performance and cost, making them the dominant choice for semiconductor applications.
Comparison with Other Materials
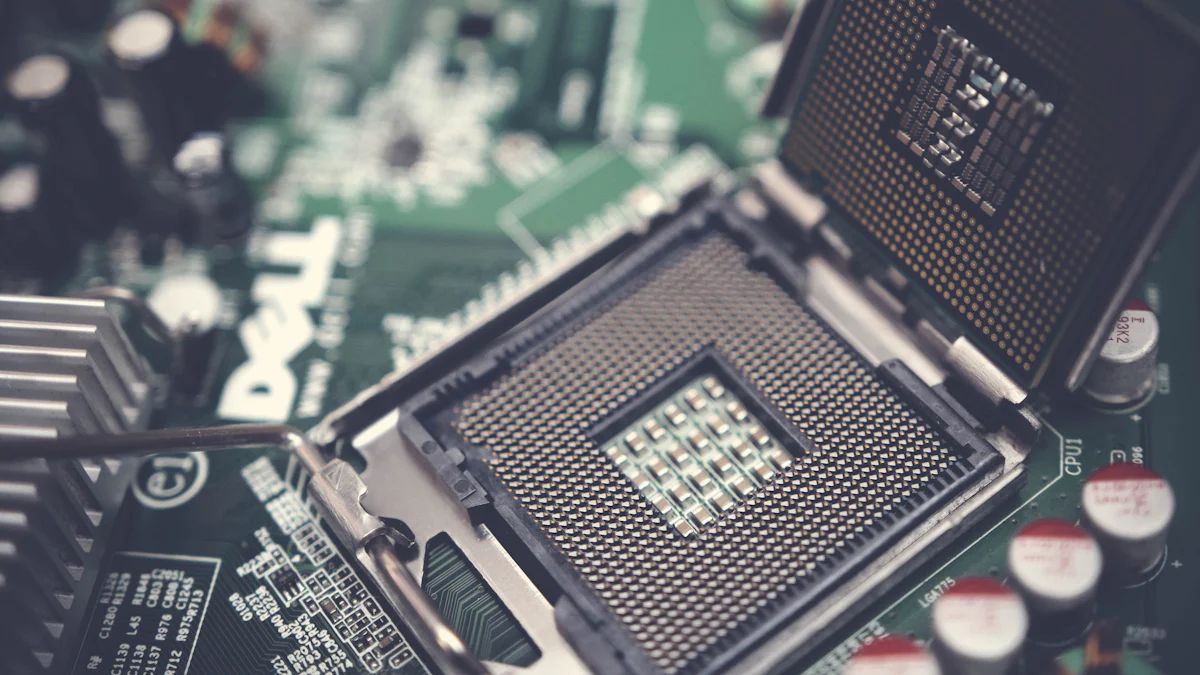
Germanium
Higher electron mobility but less stable than silicon
Germanium offers higher electron mobility compared to silicon, which allows for faster signal transmission in electronic devices. This property makes it an attractive option for certain high-speed applications. However, germanium lacks the thermal and chemical stability that silicon provides. Its lower stability limits its use in environments requiring durability and reliability. Silicon’s superior stability ensures consistent performance, making it the preferred choice for most semiconductor applications.
More expensive and less abundant
Germanium is significantly less abundant in the Earth’s crust than silicon. This scarcity increases its extraction and refinement costs, making it a more expensive material for wafer production. In contrast, silicon’s widespread availability and cost-effectiveness make it a more practical option for large-scale manufacturing. The affordability of silicon has solidified its dominance in the semiconductor industry.
Carbon (Diamond and Graphene)
Superior thermal conductivity but challenging to process
Carbon-based materials, such as diamond and graphene, exhibit exceptional thermal conductivity. These properties make them ideal for dissipating heat in high-performance electronic devices. However, their processing and integration into semiconductor manufacturing remain highly challenging. Diamond’s hardness complicates its fabrication, while graphene’s lack of a natural bandgap limits its application in digital logic circuits. Silicon, with its well-established processing techniques, remains a more viable option for practical use.
High production costs and limited scalability
The production of carbon-based wafers involves complex and costly processes. Diamond wafers require advanced synthesis methods, while graphene production struggles with scalability issues. These challenges hinder their adoption for mass production. Silicon, on the other hand, supports efficient large-scale manufacturing, making it the material of choice for industries requiring high volumes of wafers.
Other Alternatives
Gallium arsenide offers high electron mobility but is costly and difficult to manufacture
Gallium arsenide (GaAs) stands out for its high electron mobility and efficiency, which surpass those of silicon. These properties make it suitable for specialized applications, such as high-frequency and optoelectronic devices. However, GaAs is more expensive due to its rarity and the complexity of its manufacturing process. Its fragility further complicates handling during production. Silicon’s balance of performance, durability, and affordability ensures its continued dominance in the semiconductor market.
Silicon remains the preferred choice due to its balance of performance, cost, and scalability
While alternative materials like germanium, carbon, and gallium arsenide offer unique advantages, they fall short in terms of practicality and cost-effectiveness. Silicon provides an unmatched combination of stability, scalability, and affordability. Its ability to grow into large, defect-free single crystals supports high-yield production, reducing costs and waste. These qualities make silicon the most versatile and reliable material for semiconductor manufacturing, securing its position as the industry standard.
Silicon’s unique properties make it the cornerstone of semiconductor manufacturing. Its stability under extreme conditions, optimal band structure, and ability to form a reliable oxide layer ensure superior performance in electronic devices. Silicon wafers also offer practical advantages, including ease of doping, exceptional mechanical strength, and cost-effectiveness, which streamline production processes and enhance reliability. While alternative materials serve niche purposes, none match silicon’s versatility and scalability. Its widespread availability and proven efficiency solidify its position as the most reliable and adaptable material for advancing technology.
FAQ
What makes silicon the most commonly used material for wafers?
Silicon’s unique combination of properties, including its thermal stability, electrical conductivity, and abundance, makes it the most widely used material for wafers. Its ability to form a stable oxide layer and its scalability for mass production further enhance its suitability for semiconductor applications.
Why is silicon preferred over other materials like germanium or gallium arsenide?
Silicon offers a balance of performance, cost-effectiveness, and scalability that other materials cannot match. While germanium and gallium arsenide provide higher electron mobility, they are less stable, more expensive, and harder to manufacture. Silicon’s abundance and established processing techniques make it the preferred choice for most industries.
How does silicon’s abundance impact its use in wafer production?
Silicon ranks as the second most abundant element in the Earth’s crust, ensuring a steady and cost-effective supply for industrial use. This silicon’s abundance supports large-scale production and reduces costs, making silicon an ideal material for semiconductor manufacturing.
What role does silicon dioxide play in semiconductor devices?
Silicon dioxide acts as an excellent insulator in semiconductor devices. It prevents electrical currents from leaking between components and enables precise control of electrical signals. This property is essential for creating transistors and integrated circuits.
How does silicon’s bandgap benefit electronic applications?
Silicon’s bandgap of approximately 1.1 electron volts allows for efficient energy conversion and minimal leakage currents. This optimal bandgap ensures reliable performance in electronic devices, making silicon ideal for integrated circuits and microprocessors.
Can silicon wafers be customized for specific applications?
Yes, silicon wafers can be customized through a process called doping. By introducing controlled impurities, manufacturers can adjust the electrical properties of silicon to meet the requirements of various applications, such as high-speed processors or solar cells.
What advantages do silicon wafers offer in terms of mechanical strength?
Silicon wafers exhibit exceptional mechanical strength, making them durable and resistant to physical stress. This robustness ensures reliability during manufacturing processes and enhances the longevity of electronic components.
Are silicon wafers cost-effective compared to alternatives?
Silicon wafers are highly cost-effective due to the material’s abundance and well-established manufacturing techniques. Alternatives like gallium arsenide or diamond are significantly more expensive and challenging to process, making silicon the more practical option for large-scale production.
How does silicon support mass production in the semiconductor industry?
Silicon’s ability to grow into large, defect-free single crystals enables high-yield production. This scalability reduces waste and improves efficiency, meeting the demands of industries requiring mass production, such as consumer electronics and automotive sectors.
What industries benefit the most from silicon wafers?
Silicon wafers play a critical role in industries like consumer electronics, healthcare, aerospace, and automotive. Their applications include microprocessors, memory chips, solar cells, and advanced medical devices, driving innovation and technological progress across multiple sectors. silicon wafers