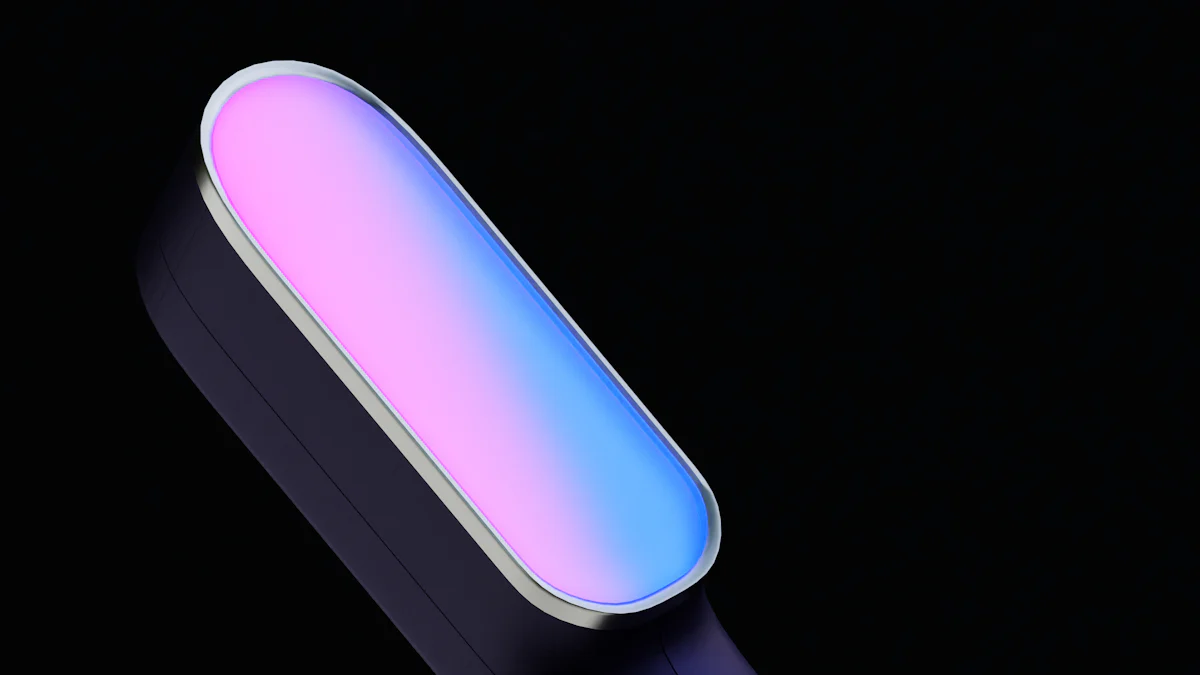
A UV LED susceptor plays a critical role in UV LED applications by efficiently absorbing electromagnetic energy and converting it into heat. This process ensures optimal thermal management, which is essential for the performance and longevity of UV LED systems. The top three types of UV LED susceptors—graphite, ceramic, and metal—stand out due to their unique material properties and application-specific advantages. Selecting the right susceptor significantly impacts the efficiency, durability, and overall success of UV LED technologies, especially in industries experiencing rapid growth, such as semiconductors and new energy solutions.
Key Takeaways
- Understanding the role of UV LED susceptors is crucial for optimizing thermal management in UV LED systems, which enhances performance and longevity.
- Graphite susceptors are ideal for high-temperature applications due to their exceptional thermal conductivity and cost-effectiveness, making them suitable for industries like semiconductor fabrication.
- Ceramic susceptors excel in environments requiring electrical insulation and chemical resistance, making them perfect for precision applications such as photolithography and chemical vapor deposition.
Metal susceptors provide excellent thermal and electrical conductivity, making them versatile for various applications, including UV curing and disinfection systems.
- Selecting the right susceptor type based on application requirements—thermal management, durability, and environmental conditions—can significantly impact the efficiency and reliability of UV LED systems.
Consider coatings like silicon carbide (SiC) or aluminum nitride (AlN) to enhance the performance of susceptors, particularly in demanding UV LED applications.
Graphite Susceptors
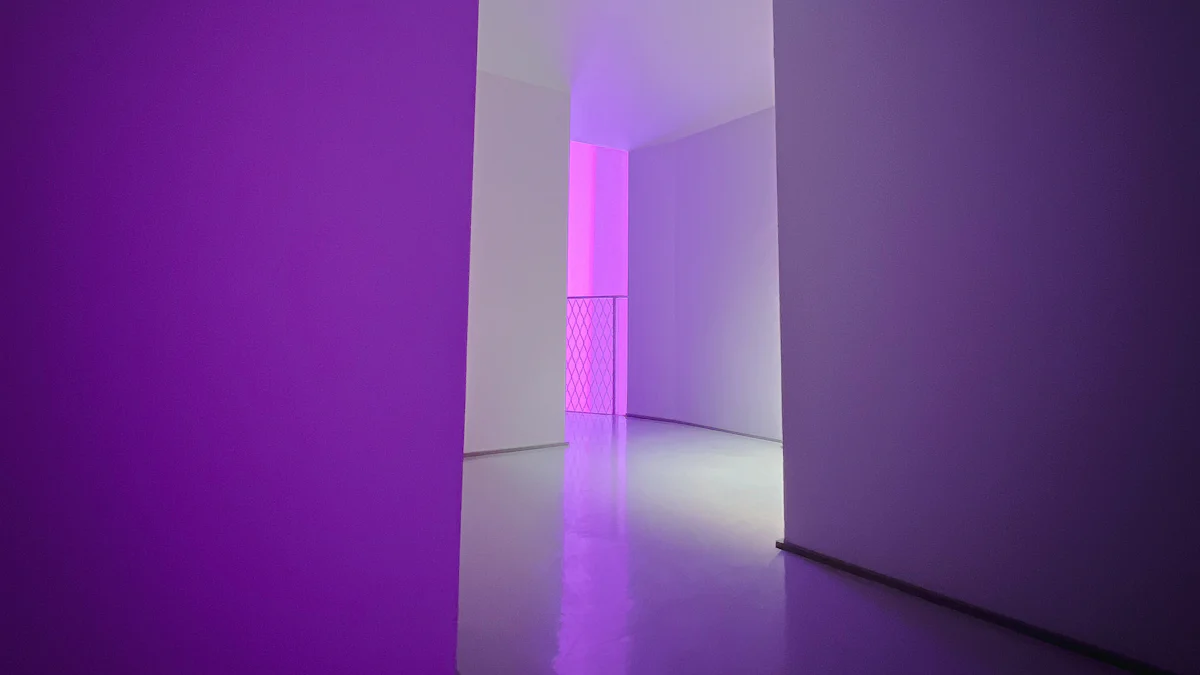
Characteristics of Graphite Susceptors
Graphite susceptors exhibit exceptional thermal conductivity and heat resistance, making them a preferred choice for high-performance UV LED applications.
Another notable feature of graphite susceptors is their lightweight yet durable nature. Despite their low density, they maintain structural integrity under high temperatures, providing long-term reliability. Additionally, graphite’s inherent stability and resistance to corrosion, except against strong oxidizers, enhance its suitability for demanding environments.
Applications of Graphite Susceptors
For instance, industries utilizing deep UV LED technologies often rely on graphite susceptors with specialized coatings, such as silicon carbide (SiC) or aluminum nitride (AlN).
In industrial settings, graphite susceptors play a crucial role in processes like UV curing and semiconductor fabrication. Their ability to withstand temperatures up to 950°C, combined with a lower ramp rate, makes them indispensable for precision applications. Moreover, their compatibility with harsh environments ensures consistent results in challenging conditions.
Advantages of Graphite Susceptors
Graphite susceptors offer several advantages that set them apart from other materials. Their excellent thermal management capabilities ensure efficient heat transfer, which is critical for maintaining the performance and longevity of UV LED systems. This efficiency not only enhances operational reliability but also reduces energy consumption.
Cost-effectiveness is another significant benefit of graphite susceptors. Their durability and long lifespan make them a practical choice for industrial applications, where minimizing downtime and maintenance costs is essential. Furthermore, their versatility allows them to adapt to various UV LED applications, providing a flexible solution for diverse industry needs.
Ceramic Susceptors
Characteristics of Ceramic Susceptors
High electrical insulation properties
Ceramic susceptors exhibit exceptional electrical insulation, making them indispensable in applications where electrical conductivity must be minimized. This property ensures that ceramic susceptors can effectively isolate electrical currents, preventing interference with sensitive UV LED systems. Materials like silicon carbide (SiC) enhance this insulation capability while maintaining structural integrity under extreme conditions.
The high electrical insulation of ceramics also contributes to their reliability in precision applications. This characteristic allows them to perform consistently in environments where electrical disturbances could compromise the functionality of UV LED technologies.
Resistance to chemical corrosion
Ceramic susceptors demonstrate remarkable resistance to chemical corrosion, even in aggressive environments. Silicon carbide, a common material in ceramic susceptors, resists oxidation and chemical degradation, ensuring long-term performance. This resistance makes ceramics suitable for processes involving harsh chemicals, such as chemical vapor deposition (CVD) and photolithography.
The ability to withstand chemical attacks enables ceramic susceptors to maintain their structural and functional properties over extended periods. This durability reduces the need for frequent replacements, enhancing their cost-effectiveness in industrial applications.
Applications of Ceramic Susceptors
Suitable for UV LED systems in harsh environments
Ceramic susceptors excel in harsh environments where other materials may fail. Their resistance to extreme temperatures, chemical exposure, and mechanical stress makes them ideal for UV LED systems operating in challenging conditions. For instance, industries utilizing deep UV LED technologies often rely on ceramic susceptors to ensure consistent performance and reliability.
These susceptors also play a critical role in applications requiring precise thermal management. Their ability to maintain stability under fluctuating temperatures ensures optimal heat distribution, which is essential for the efficiency of UV LED systems.
Used in precision applications like photolithography and CVD
Ceramic susceptors are widely used in precision applications such as photolithography and chemical vapor deposition (CVD). In photolithography, their high thermal stability and electrical insulation properties enable accurate patterning of semiconductor devices. This precision is crucial for producing high-quality electronic components.
In CVD processes, ceramic susceptors provide a stable platform for depositing thin films on substrates. Their resistance to thermal cycling and chemical attack ensures consistent results, even in demanding production environments. These qualities make ceramics a preferred choice for industries requiring meticulous attention to detail.
Advantages of Ceramic Susceptors
Long lifespan and reliability
The durability of ceramic susceptors translates into a long operational lifespan. Their resistance to wear, corrosion, and thermal degradation ensures consistent performance over time. This reliability reduces maintenance requirements, minimizing downtime in industrial processes.
Ceramic susceptors also maintain their structural integrity under extreme conditions, further enhancing their longevity. This robustness makes them a cost-effective solution for applications demanding high reliability and minimal interruptions.
Superior performance in chemically aggressive settings
Ceramic susceptors outperform other materials in chemically aggressive environments. Their ability to resist oxidation and chemical corrosion ensures stable performance, even when exposed to harsh substances. This advantage is particularly valuable in industries like semiconductor manufacturing, where chemical stability is critical.
The superior performance of ceramic susceptors in such settings enhances the efficiency and effectiveness of UV LED systems. By maintaining their properties under challenging conditions, they contribute to the overall success of precision applications.
Metal Susceptors
Characteristics of Metal Susceptors
High strength and durability
Metal susceptors exhibit exceptional strength and durability, making them a reliable choice for demanding UV LED applications. Their robust mechanical properties allow them to withstand significant stress and maintain structural integrity under high temperatures. This durability ensures consistent performance over extended periods, even in challenging industrial environments. Materials like stainless steel and molybdenum are commonly used due to their ability to endure mechanical wear and thermal cycling without degradation.
Excellent thermal and electrical conductivity
Metals are renowned for their superior thermal and electrical conductivity. Metal susceptors efficiently transfer heat, ensuring uniform temperature distribution across UV LED systems. This property is critical for applications requiring precise thermal management, such as UV curing processes. Additionally, their excellent electrical conductivity supports applications where electromagnetic energy absorption and conversion to heat must occur seamlessly. These characteristics make metal susceptors indispensable in high-performance UV LED technologies.
Applications of Metal Susceptors
Commonly used in UV curing and disinfection systems
Metal susceptors play a pivotal role in UV curing and disinfection systems. Their ability to handle high thermal loads ensures efficient heat transfer, which is essential for curing adhesives, coatings, and inks. In disinfection systems, metal susceptors enhance the performance of UV LEDs by maintaining optimal operating temperatures. This capability ensures consistent and effective sterilization, particularly in medical and water treatment applications.
Ideal for applications requiring robust mechanical support
Industries requiring robust mechanical support often rely on metal susceptors. Their strength and stability make them suitable for heavy-duty applications, such as semiconductor manufacturing and industrial heating processes. Metal susceptors provide a stable platform for substrates, ensuring precision and reliability during production. Their mechanical resilience also makes them ideal for environments with high vibration or mechanical stress, where other materials might fail.
Advantages of Metal Susceptors
High efficiency in heat transfer
Metal susceptors excel in heat transfer efficiency, a critical factor in UV LED applications. Their ability to rapidly absorb and distribute heat enhances the performance and longevity of UV LED systems. This efficiency reduces energy consumption and minimizes thermal stress on components, ensuring consistent operation. Industries prioritizing energy efficiency and thermal management often choose metal susceptors for their superior performance.
Versatility across various UV LED applications
The versatility of metal susceptors allows them to adapt to a wide range of UV LED applications. From UV curing and disinfection to semiconductor fabrication, their unique properties meet diverse industry requirements. Their compatibility with different coatings and surface treatments further expands their usability. This adaptability makes metal susceptors a practical and cost-effective solution for industries seeking reliable and high-performing materials.
Comparing the Top 3 Susceptor Types
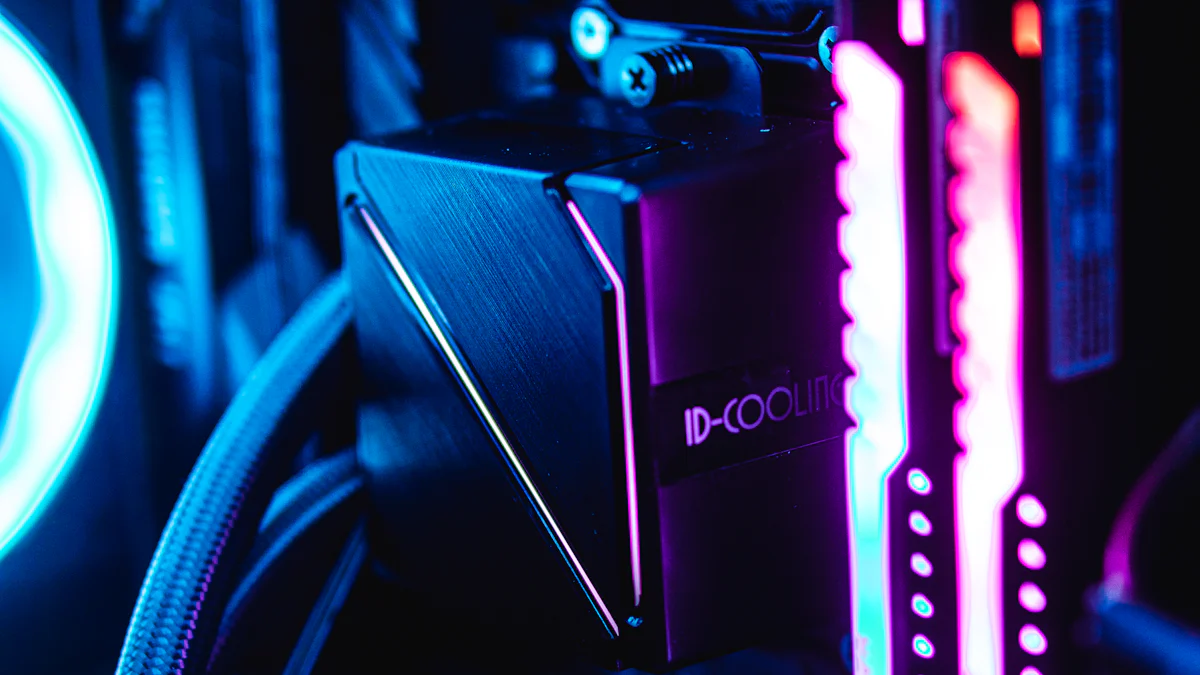
Key Differences in Material Properties
Thermal conductivity and heat resistance
The thermal conductivity and heat resistance of a susceptor significantly influence its performance in UV LED applications. Graphite susceptors excel in this area, offering exceptional thermal conductivity and stability at high temperatures. Their ability to uniformly distribute heat ensures consistent thermal management, even in demanding processes like Atomic Layer Deposition (ALD). Coatings such as silicon carbide (SiC) or aluminum nitride (AlN) further enhance their resistance to thermal cycling and chemical attack, making them ideal for high-precision environments.
Ceramic susceptors, on the other hand, provide moderate thermal conductivity but stand out for their resistance to extreme temperatures. Their structural integrity remains intact even under fluctuating thermal conditions, which is crucial for applications like chemical vapor deposition (CVD). While not as thermally conductive as graphite, ceramics compensate with their durability and reliability in harsh environments.
Metal susceptors offer excellent thermal conductivity, rivaling that of graphite. Their ability to rapidly absorb and transfer heat makes them suitable for applications requiring efficient thermal management, such as UV curing. However, metals may face limitations in extreme temperature environments compared to ceramics and graphite.
Electrical insulation and chemical resistance
Electrical insulation and chemical resistance are critical factors when selecting a susceptor for specific applications. Ceramic susceptors lead in electrical insulation, effectively isolating electrical currents and preventing interference in sensitive UV LED systems. This property, combined with their resistance to chemical corrosion, makes ceramics indispensable in chemically aggressive settings like photolithography and etching.
Graphite susceptors, while not electrically insulating, exhibit excellent chemical resistance, except against strong oxidizers. Their stability under chemical exposure ensures long-term performance in industrial applications. Coatings like SiC further enhance their resistance to oxidation and chemical degradation.
Metal susceptors, though highly conductive, lack the electrical insulation properties of ceramics. However, their chemical resistance varies depending on the type of metal used. Stainless steel and molybdenum, for instance, offer good resistance to corrosion, making them suitable for less chemically aggressive environments.
Suitability for Different Applications
Industrial vs. precision applications
The choice of susceptor material often depends on whether the application is industrial or precision-based. Graphite susceptors are well-suited for industrial applications requiring high-temperature resistance and rapid heat dissipation. Their cost-effectiveness and durability make them a practical choice for large-scale operations like UV curing and semiconductor fabrication.
Ceramic susceptors shine in precision applications where electrical insulation and chemical stability are paramount. Processes like photolithography and CVD benefit from the accuracy and reliability provided by ceramics. Their ability to maintain consistent performance under stringent conditions ensures high-quality results in these specialized fields.
Metal susceptors offer versatility across both industrial and precision applications. Their strength and thermal efficiency make them ideal for robust mechanical support in industrial settings, while their adaptability allows them to meet the demands of precision processes like UV disinfection.
Environmental considerations (e.g., harsh conditions)
Environmental factors play a crucial role in determining the suitability of a susceptor. Ceramic susceptors excel in harsh conditions, resisting extreme temperatures, chemical exposure, and mechanical stress. Their long lifespan and reliability make them a preferred choice for environments where durability is essential.
Graphite susceptors, with their lightweight yet durable properties, also perform well in challenging environments. Their resistance to thermal deformation and chemical attack ensures consistent results in high-temperature and chemically aggressive settings.
Metal susceptors provide robust mechanical support in environments with high vibration or mechanical stress. However, their performance may vary in chemically aggressive or extremely high-temperature conditions, where ceramics or graphite might be more suitable.
Graphite, ceramic, and metal susceptors each offer distinct advantages tailored to specific UV LED applications. Graphite excels in thermal conductivity and cost-effectiveness, making it ideal for high-temperature industrial processes. Ceramic provides unmatched chemical resistance and electrical insulation, ensuring reliability in precision applications like photolithography. Metal stands out for its strength and versatility, supporting robust mechanical needs in UV curing and disinfection systems.
Selecting the right UV LED susceptor depends on application requirements. Consider factors such as thermal management, durability, and environmental conditions. For optimal performance, prioritize materials with properties that align with the operational demands of the system.
FAQ
What is the purpose of this FAQ section?
This FAQ section provides clear and concise answers to common questions about UV LED susceptors. It aims to help readers understand their characteristics, applications, and advantages. By addressing frequently asked questions, this section ensures that users can make informed decisions when selecting the right susceptor for their needs.
What is a UV LED susceptor?
A UV LED susceptor is a material designed to absorb electromagnetic energy and convert it into heat. This process ensures effective thermal management in UV LED systems, which is essential for maintaining performance and extending the lifespan of the equipment. Common materials used for susceptors include graphite, ceramic, and metal, each offering unique benefits for specific applications.
Why is thermal management important in UV LED systems?
Thermal management plays a critical role in ensuring the efficiency and longevity of UV LED systems. Excessive heat can degrade the performance of UV LEDs and shorten their lifespan. Susceptors help regulate temperature by efficiently transferring or dissipating heat, which enhances the system’s reliability and operational stability.
How do graphite susceptors differ from ceramic and metal susceptors?
Graphite susceptors excel in thermal conductivity and heat resistance, making them ideal for high-temperature applications. Ceramic susceptors offer superior electrical insulation and chemical resistance, which makes them suitable for precision applications in harsh environments. Metal susceptors provide excellent thermal and electrical conductivity, along with robust mechanical support, making them versatile for various industrial uses.
What industries commonly use UV LED susceptors?
UV LED susceptors are widely used in industries such as semiconductors, photovoltaics, new energy, and metallurgy. Applications include UV curing, disinfection, photolithography, chemical vapor deposition (CVD), and deep UV LED technologies. Each industry selects susceptor materials based on specific operational requirements.
Can a single susceptor type meet all application needs?
No single susceptor type can meet all application needs. Each material—graphite, ceramic, and metal—has distinct properties that make it suitable for specific uses. For example, graphite is ideal for high-temperature industrial processes, while ceramics excel in chemically aggressive settings. Metals offer versatility but may not perform as well in extreme conditions compared to ceramics or graphite.
How does the choice of susceptor impact UV LED system performance?
The choice of susceptor directly affects the efficiency, durability, and overall performance of UV LED systems. Materials with high thermal conductivity, like graphite and metal, ensure effective heat transfer. Ceramics, with their chemical resistance and electrical insulation, enhance reliability in precision applications. Selecting the right susceptor optimizes system functionality and reduces maintenance costs.
Are there coatings available to enhance susceptor performance?
Yes, coatings such as silicon carbide (SiC) and aluminum nitride (AlN) can enhance the performance of susceptors.
How can one determine the best susceptor for a specific application?
To determine the best susceptor, consider factors such as thermal management needs, environmental conditions, and application requirements. For high-temperature industrial processes, graphite may be the best choice. For precision applications in chemically aggressive settings, ceramics are more suitable. Metals work well for applications requiring robust mechanical support. Consulting with experts or manufacturers can also provide valuable guidance.
Where can high-quality UV LED susceptors be sourced?
High-quality UV LED susceptors can be sourced from specialized manufacturers like Ningbo VET Energy Technology Co., Ltd. Companies with expertise in advanced materials, such as graphite, ceramics, and surface treatments, offer tailored solutions for various industries. Look for suppliers with certifications like ISO 9001:2015 to ensure product quality and reliability.