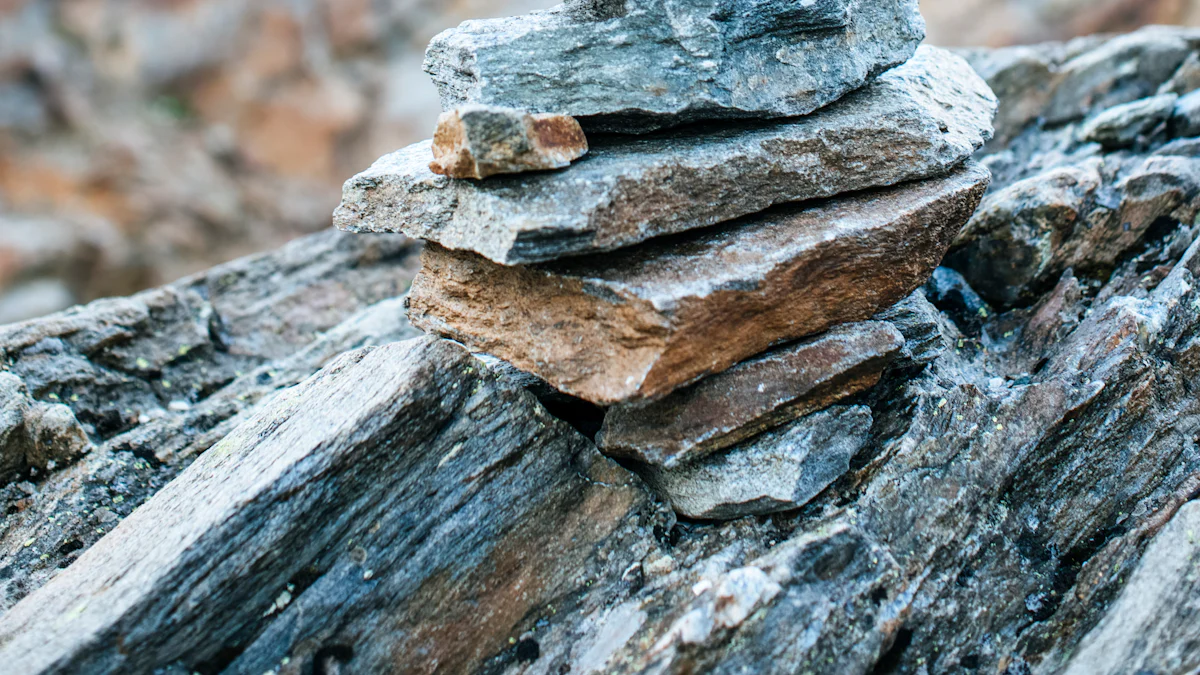
SiC coated graphite carriers stand out as advanced industrial components, combining the lightweight nature of graphite with the durability of silicon carbide. This unique pairing delivers exceptional performance in demanding environments. The graphite core ensures excellent thermal conductivity, while the SiC coating enhances resistance to wear, oxidation, and chemical corrosion. Industries such as semiconductor manufacturing rely on these carriers for their high purity and ability to withstand extreme temperatures. By reducing surface roughness and porosity, the SiC coating simplifies maintenance and minimizes contamination risks, making these carriers indispensable in precision-driven applications.
Key Takeaways
- SiC coated graphite carriers combine the lightweight properties of graphite with the durability of silicon carbide, making them ideal for high-performance applications.
These carriers excel in high-temperature environments, maintaining structural integrity and thermal stability, which is crucial for processes like semiconductor manufacturing.
- The exceptional thermal conductivity of SiC coated graphite carriers ensures efficient heat transfer, leading to improved process efficiency and higher production yields.
- Their silicon carbide coating provides excellent chemical and corrosion resistance, protecting the graphite core and extending the lifespan of the carriers.
- With high purity and low particle generation, these carriers minimize contamination risks, making them essential for precision-driven applications in semiconductor fabrication.
SiC coated graphite carriers are cost-effective due to their durability and reduced maintenance needs, leading to significant savings over time.
- These carriers are versatile and can be customized for specific applications, enhancing their performance across various industries, including aerospace and chemical processing.
Key Features of SiC Coated Graphite Carriers
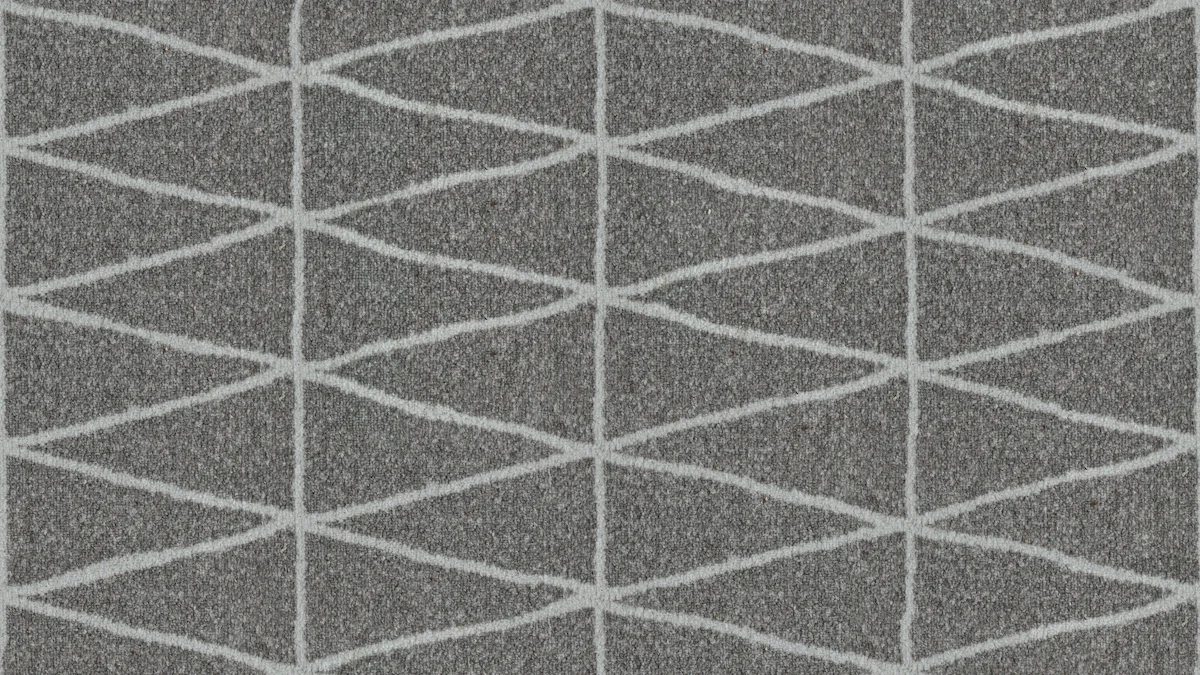
High Temperature Resistance
SiC coated graphite carriers excel in environments where extreme temperatures are the norm. The silicon carbide coating provides exceptional thermal stability, allowing these carriers to maintain their structural integrity even under intense heat. This feature makes them indispensable in processes like semiconductor manufacturing, where precise temperature control is critical. The graphite core, combined with the SiC coating, ensures that the carriers can withstand rapid temperature fluctuations without compromising performance. This resilience enhances their reliability in high-temperature applications, ensuring consistent results over extended periods.
Exceptional Thermal Conductivity
The combination of graphite and silicon carbide creates a material with outstanding thermal conductivity. Graphite, known for its ability to transfer heat efficiently, forms the core of these carriers. The SiC coating complements this by providing a uniform surface that optimizes heat distribution. This property is particularly valuable in processes like epitaxy, where maintaining a consistent temperature across the wafer is essential for uniform film growth. By facilitating efficient heat transfer, SiC coated graphite carriers contribute to improved process efficiency and higher production yields.
Chemical and Corrosion Resistance
The silicon carbide coating acts as a robust barrier against chemical reactions and corrosion. This resistance ensures that the carriers remain unaffected by harsh chemicals and corrosive gases commonly encountered in industrial environments. In semiconductor manufacturing, where purity is paramount, the SiC coating prevents contamination and preserves the integrity of the wafers. Additionally, the coating protects the graphite core from oxidation, extending the carrier’s lifespan and reducing maintenance requirements. This combination of chemical inertness and durability makes SiC coated graphite carriers a reliable choice for demanding applications.
High Purity and Low Particle Generation
SiC coated graphite carriers deliver exceptional performance in environments where high purity is essential. The silicon carbide coating minimizes surface roughness and seals the porous structure of the graphite core. This process significantly reduces particle generation, ensuring a cleaner operational environment. In industries like semiconductor manufacturing, where even microscopic contamination can compromise product quality, this feature proves invaluable.
The high purity of these carriers stems from the chemical inertness of silicon carbide. The coating resists reactions with corrosive gases and chemicals, maintaining the integrity of the carrier and preventing contamination of sensitive materials. This property ensures consistent results in processes such as epitaxy and chemical vapor deposition (CVD), where precision and cleanliness are critical.
Manufacturers achieve this purity by using graphite materials with controlled particle properties as the base. The SiC coating enhances uniformity, creating a stable and reliable platform for high-precision applications. This meticulous production process ensures that SiC coated graphite carriers meet the stringent requirements of modern semiconductor fabrication.
By combining high purity with low particle generation, these carriers not only improve product quality but also reduce maintenance needs. Their ability to maintain a clean environment minimizes downtime and enhances operational efficiency, making them an indispensable component in advanced industrial processes.
Benefits of SiC Coated Graphite Carriers
Increased Efficiency and Performance
SiC coated graphite carriers significantly enhance operational efficiency and performance in industrial applications. The combination of a lightweight graphite core and a durable silicon carbide coating ensures optimal thermal management. This design allows for rapid heat transfer and uniform temperature distribution, which are critical in processes like epitaxy and chemical vapor deposition (CVD). By maintaining consistent thermal conditions, these carriers improve the quality of wafer processing and reduce the likelihood of defects.
The smooth surface provided by the silicon carbide coating minimizes surface roughness and porosity. This feature reduces particle generation, ensuring a cleaner environment during manufacturing. A clean operational setting directly contributes to higher production yields and better product quality. Furthermore, the high purity of these carriers prevents contamination, making them indispensable in semiconductor manufacturing, where precision and cleanliness are paramount.
Longevity and Durability
The durability of SiC coated graphite carriers stems from the robust properties of silicon carbide. The coating acts as a protective barrier, shielding the graphite core from oxidation, chemical reactions, and physical wear. This resistance to harsh environments extends the lifespan of the carriers, reducing the frequency of replacements and maintenance.
Research highlights the ability of silicon carbide coatings to withstand extreme temperatures and corrosive conditions. These properties ensure that the carriers maintain their structural integrity even under demanding operational circumstances. The enhanced durability not only lowers operational costs but also ensures consistent performance over time. Industries benefit from this reliability, as it minimizes downtime and enhances overall productivity.
Cost-Effectiveness
SiC coated graphite carriers offer a cost-effective solution for industries requiring high-performance materials. Their extended lifespan reduces the need for frequent replacements, leading to significant cost savings over time. The durability of the silicon carbide coating minimizes maintenance requirements, further lowering operational expenses.
The high efficiency of these carriers also contributes to their cost-effectiveness. By improving thermal management and reducing contamination risks, they enhance production yields and minimize waste. This efficiency translates into better resource utilization and higher profitability for manufacturers.
Additionally, advancements in production techniques have made these carriers more accessible. Research efforts focus on improving the uniformity and quality of silicon carbide coatings while reducing manufacturing costs. These developments ensure that industries can benefit from the superior properties of SiC coated graphite carriers without incurring excessive expenses.
Comparison with Alternative Materials
SiC Coated Graphite vs. Pure CVD SiC
SiC coated graphite carriers and pure CVD SiC materials serve similar purposes in high-temperature and high-purity applications, but they differ significantly in their properties and performance. SiC coated graphite carriers combine a lightweight graphite core with a silicon carbide coating, offering a unique balance of thermal conductivity, durability, and cost-effectiveness. In contrast, pure CVD SiC materials consist entirely of silicon carbide, which provides exceptional hardness and chemical resistance but at a higher cost and with increased weight.
The thermal conductivity of SiC coated graphite carriers ranges between 250-300 watts per meter kelvin, ensuring uniform temperature distribution across the wafer’s surface. This property enhances production yields in semiconductor manufacturing. Pure CVD SiC, while also thermally conductive, lacks the lightweight nature of graphite, making it less efficient in applications requiring rapid heat transfer and temperature stability.
Durability is another key differentiator. The SiC coating on graphite carriers protects the core from oxidation and chemical corrosion, extending the carrier’s lifespan. Pure CVD SiC materials, though inherently resistant to wear and corrosion, are more brittle and prone to cracking under mechanical stress. This makes SiC coated graphite carriers a more reliable choice for processes involving frequent handling or temperature fluctuations.
Cost considerations further highlight the advantages of SiC coated graphite carriers. The combination of a graphite core and a thin SiC coating reduces material costs without compromising performance. Pure CVD SiC, being a monolithic material, incurs higher production expenses, making it less accessible for cost-sensitive industries.
SiC Coated Graphite vs. Traditional Graphite
Traditional graphite carriers, while widely used in industrial applications, fall short when compared to SiC coated graphite carriers in terms of performance and reliability. The addition of a silicon carbide coating transforms the properties of graphite, addressing its inherent limitations and enhancing its suitability for demanding environments.
Thermal conductivity is a critical factor in this comparison. Traditional graphite carriers excel in heat transfer due to their natural properties, but their porous structure can lead to uneven temperature distribution. SiC coated graphite carriers overcome this limitation by sealing the graphite core with a uniform SiC layer. This coating ensures consistent thermal performance, which is essential for processes like epitaxy and chemical vapor deposition (CVD).
Chemical resistance is another area where SiC coated graphite carriers outperform traditional graphite. The SiC coating acts as a barrier against corrosive gases and chemicals, preventing contamination and preserving the carrier’s integrity. Traditional graphite, lacking this protective layer, is more susceptible to oxidation and chemical degradation, leading to shorter lifespans and higher maintenance requirements.
Durability also sets these two materials apart. The SiC coating enhances the structural stability of graphite carriers, enabling them to withstand extreme temperatures and mechanical stress. Traditional graphite, while robust, cannot match the longevity and reliability offered by its SiC-coated counterpart.
In terms of purity, SiC coated graphite carriers provide a significant advantage. The SiC layer minimizes particle generation and seals the porous graphite surface, creating a cleaner operational environment. This feature is particularly valuable in semiconductor manufacturing, where even minor contamination can compromise product quality. Traditional graphite carriers, with their higher particle generation, pose a greater risk in such precision-driven applications.
In summary, SiC coated graphite carriers offer superior thermal conductivity, chemical resistance, and durability compared to both pure CVD SiC and traditional graphite. These attributes make them an ideal choice for industries requiring high-performance materials in challenging environments.
Applications in Semiconductor Manufacturing
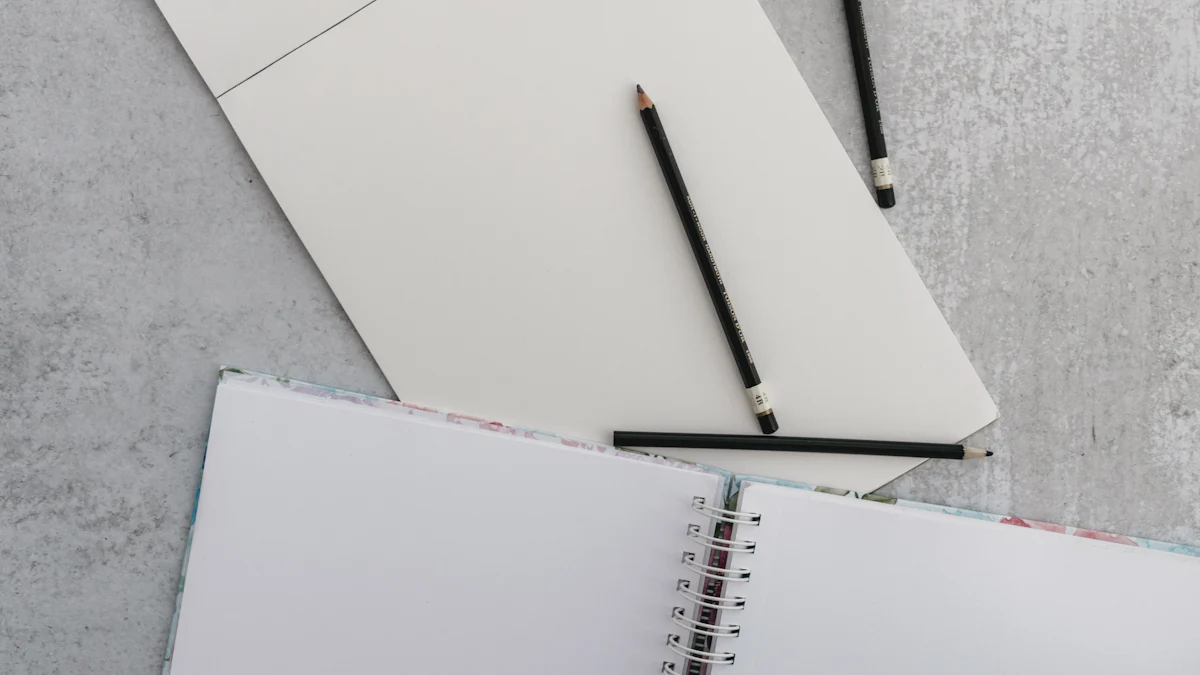
Role in Wafer Processing
SiC coated graphite carriers play a pivotal role in wafer processing, a critical step in semiconductor manufacturing. These carriers provide a stable platform for wafers during high-temperature processes, ensuring uniform heat distribution and minimizing thermal stress. The silicon carbide coating enhances the carrier’s thermal stability, allowing it to withstand rapid temperature fluctuations without compromising structural integrity. This capability ensures consistent wafer quality, which is essential for producing reliable semiconductor devices.
The smooth surface of the SiC coating reduces surface roughness and porosity, which significantly lowers the risk of wafer contamination. By creating a cleaner processing environment, these carriers help maintain the purity required for advanced semiconductor fabrication. Their lightweight graphite core also facilitates easier handling and reduces the mechanical stress on wafers, further improving production efficiency.
In epitaxial processes, where thin films are deposited onto wafers, SiC coated graphite carriers excel due to their ability to maintain precise temperature control. This precision ensures uniform film growth, which is crucial for achieving the desired electrical properties in semiconductor devices. The combination of thermal conductivity, chemical resistance, and durability makes these carriers indispensable in wafer processing applications.
Use in Chemical Vapor Deposition (CVD) Processes
Chemical Vapor Deposition (CVD) processes demand materials that can endure extreme conditions while maintaining high purity. SiC coated graphite carriers meet these requirements by offering exceptional performance in high-temperature and corrosive gas environments.
The high thermal conductivity of the graphite core, combined with the uniformity of the SiC coating, enables efficient heat transfer during CVD. This efficiency is critical for achieving consistent thin film growth, which directly impacts the quality of semiconductor devices. The carriers’ ability to withstand temperature fluctuations further enhances their reliability, making them a preferred choice for CVD applications.
SiC coated graphite carriers also contribute to improved production yields by reducing particle generation. The SiC coating seals the porous structure of the graphite core, creating a smooth and clean surface. This feature minimizes contamination risks, ensuring a controlled environment for depositing high-purity materials. Manufacturers rely on these carriers to achieve the precision and cleanliness required for advanced semiconductor technologies.
In summary, SiC coated graphite carriers are integral to both wafer processing and CVD processes. Their unique combination of thermal stability, chemical resistance, and high purity ensures optimal performance in semiconductor manufacturing.
SiC coated graphite carriers stand out as indispensable components in high-performance industries. Their exceptional thermal conductivity, chemical resistance, and durability ensure reliable operation under extreme conditions. These carriers enhance efficiency and longevity, offering a cost-effective solution compared to alternatives like pure CVD SiC or traditional graphite. Their ability to maintain high purity and reduce contamination risks makes them vital in semiconductor manufacturing. By supporting processes such as wafer processing and epitaxy, they contribute to the production of high-quality devices, reinforcing their role as a cornerstone in precision-driven applications.
FAQ
What are SiC coated graphite carriers?
SiC coated graphite carriers are advanced industrial components that combine a lightweight graphite core with a silicon carbide (SiC) coating. This design enhances durability, thermal conductivity, and chemical resistance, making them ideal for high-temperature and high-purity applications such as semiconductor manufacturing.
Why are SiC coated graphite carriers preferred in semiconductor manufacturing?
These carriers offer exceptional thermal stability and high purity, which are critical in semiconductor processes. The SiC coating minimizes particle generation and contamination risks, ensuring a clean environment for wafer processing and chemical vapor deposition (CVD). Their ability to maintain consistent temperature distribution also improves production yields.
How do SiC coated graphite carriers compare to pure CVD SiC materials?
SiC coated graphite carriers provide a lightweight and cost-effective alternative to pure CVD SiC materials. While both offer excellent thermal conductivity and chemical resistance, the graphite core in SiC coated carriers ensures better heat transfer and reduces weight. Pure CVD SiC, though durable, is heavier and more expensive, making it less practical for certain applications.
What makes SiC coated graphite carriers more durable than traditional graphite?
The silicon carbide coating acts as a protective barrier against oxidation, chemical reactions, and physical wear. This coating enhances the structural integrity of the graphite core, allowing the carriers to withstand extreme temperatures and corrosive environments. Traditional graphite lacks this protective layer, making it more susceptible to damage and shorter lifespans.
Can SiC coated graphite carriers handle rapid temperature changes?
Yes, these carriers excel in environments with rapid temperature fluctuations. The combination of a graphite core and SiC coating ensures thermal stability and prevents structural degradation. This capability makes them reliable for processes like epitaxy, where precise temperature control is essential.
How do SiC coated graphite carriers reduce contamination risks?
The SiC coating seals the porous structure of the graphite core, creating a smooth and uniform surface. This design minimizes particle generation and prevents chemical reactions that could lead to contamination. In industries like semiconductor manufacturing, this feature ensures a cleaner operational environment and higher product quality.
Are SiC coated graphite carriers cost-effective?
Yes, these carriers offer a cost-effective solution due to their extended lifespan and reduced maintenance requirements. The combination of a durable SiC coating and a lightweight graphite core lowers material costs while maintaining high performance. Their efficiency in improving production yields further enhances their cost-effectiveness.
What role do SiC coated graphite carriers play in MOCVD processes?
In Metal-Organic Chemical Vapor Deposition (MOCVD) processes, these carriers provide stable base support and thermal stability. The SiC coating ensures consistent temperature distribution, promoting the growth of high-quality epitaxial films. This precision is crucial for achieving uniform thin film layers in semiconductor devices.
How are SiC coated graphite carriers customized for specific applications?
Manufacturers can tailor the thickness of the SiC coating and the dimensions of the graphite core to meet specific operational requirements. This customization ensures optimal performance in various applications, including wafer processing, CVD, and MOCVD processes.
What industries benefit from using SiC coated graphite carriers?
While semiconductor manufacturing is the primary industry, other sectors such as aerospace, heating technologies, and chemical processing also benefit from these carriers. Their high thermal conductivity, chemical resistance, and durability make them versatile for a wide range of high-performance applications.