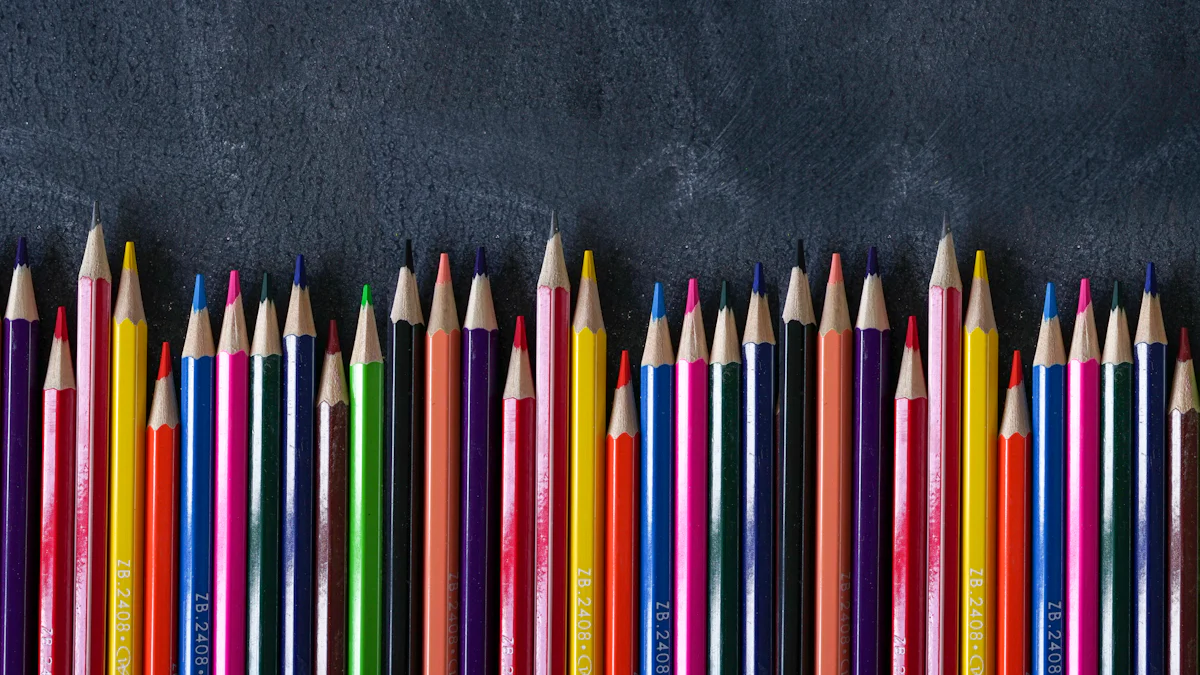
The semiconductor industry relies on precision and durability, making the sic coated graphite carrier an essential component in modern manufacturing. These carriers excel in high-performance environments due to their exceptional thermal stability and chemical resistance. Their ability to withstand extreme temperatures and corrosive conditions ensures consistent performance during critical processes like wafer handling and thin film growth. Additionally, their advanced coating technology enhances longevity, reducing maintenance needs and operational costs. As demand for high-quality semiconductors grows, these carriers play a pivotal role in meeting the industry’s rigorous standards.
Key Takeaways
- SiC coated graphite carriers provide exceptional durability, making them ideal for high-stress environments in semiconductor manufacturing.
- The silicon carbide coating significantly extends the lifespan of these carriers, reducing maintenance needs and operational costs.
- These carriers excel in extreme temperatures and corrosive conditions, ensuring consistent performance during critical manufacturing processes.
- Precision-engineered surfaces of SiC coated carriers support intricate semiconductor designs, enhancing production accuracy.
- By minimizing contamination risks, SiC coated graphite carriers contribute to the production of reliable and defect-free semiconductor components.
- Their ability to maintain performance under demanding conditions boosts production efficiency and supports high-volume manufacturing.
- Investing in SiC coated carriers leads to long-term cost savings through lower maintenance and reduced downtime.
Key Benefits of SiC Coated Graphite Carriers
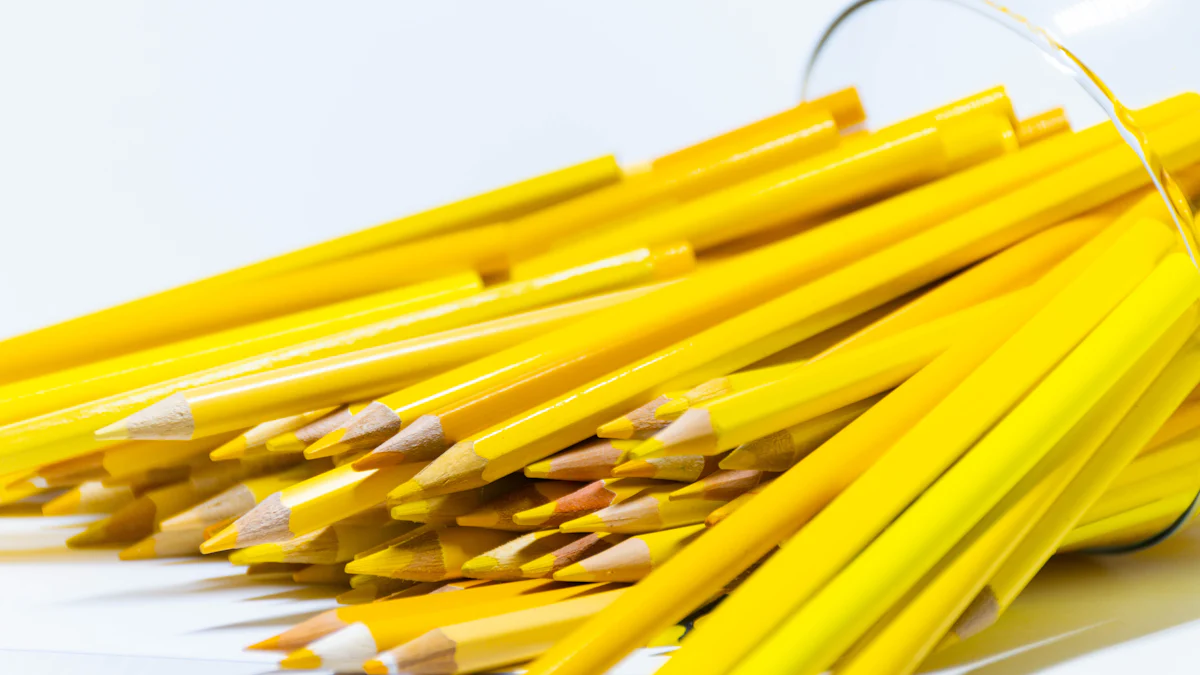
Durability and Longevity
Resistance to wear and tear in high-stress environments
The SiC coated graphite carrier demonstrates exceptional durability, making it ideal for high-stress environments in semiconductor manufacturing. The silicon carbide coating acts as a protective barrier, shielding the graphite base from physical damage and erosion. This resistance to wear ensures that the carrier maintains its structural integrity even under rigorous operational conditions. By reducing the impact of mechanical stress, these carriers provide a reliable solution for demanding production processes.
Extended lifespan compared to uncoated graphite carriers
The silicon carbide coating significantly extends the lifespan of graphite carriers. Unlike uncoated graphite, which is prone to oxidation and degradation at high temperatures, the SiC layer offers robust protection. This enhancement minimizes the need for frequent replacements, reducing downtime and operational costs. Manufacturers benefit from a longer-lasting product that maintains performance over extended periods, ensuring consistent results in semiconductor fabrication.
Thermal and Chemical Stability
Withstanding extreme temperatures without degradation
The SiC coated graphite carrier excels in high-temperature environments, a critical requirement in semiconductor manufacturing. Silicon carbide’s outstanding thermal stability allows these carriers to endure extreme heat without losing their structural or functional properties. This capability is particularly vital during processes like chemical vapor deposition (CVD), where maintaining stable temperatures is essential for producing high-quality thin films.
Resistance to corrosive gases and chemicals in semiconductor processes
Semiconductor manufacturing often involves exposure to corrosive gases and chemicals. The SiC coating provides excellent chemical resistance, protecting the graphite base from harmful reactions. This resistance ensures that the carrier remains unaffected by aggressive substances, preserving its purity and functionality. By preventing contamination and degradation, these carriers contribute to the production of reliable and defect-free semiconductor components.
Precision and Performance in High-Tech Applications
Supporting intricate and precise semiconductor designs
The SiC coated graphite carrier plays a crucial role in supporting the intricate designs of modern semiconductors. Its precision-engineered surface ensures uniformity and stability during wafer handling and processing. This level of accuracy is essential for achieving the detailed structures required in advanced semiconductor devices, such as those used in microelectronics and high-performance computing.
Consistent performance in demanding manufacturing conditions
Consistency is a hallmark of the SiC coated graphite carrier. Its ability to maintain performance under demanding conditions makes it indispensable in high-tech applications. The combination of thermal stability, chemical resistance, and mechanical strength ensures that these carriers deliver reliable results across various manufacturing stages. This consistency enhances production efficiency and supports the development of cutting-edge technologies.
Role in Semiconductor Manufacturing
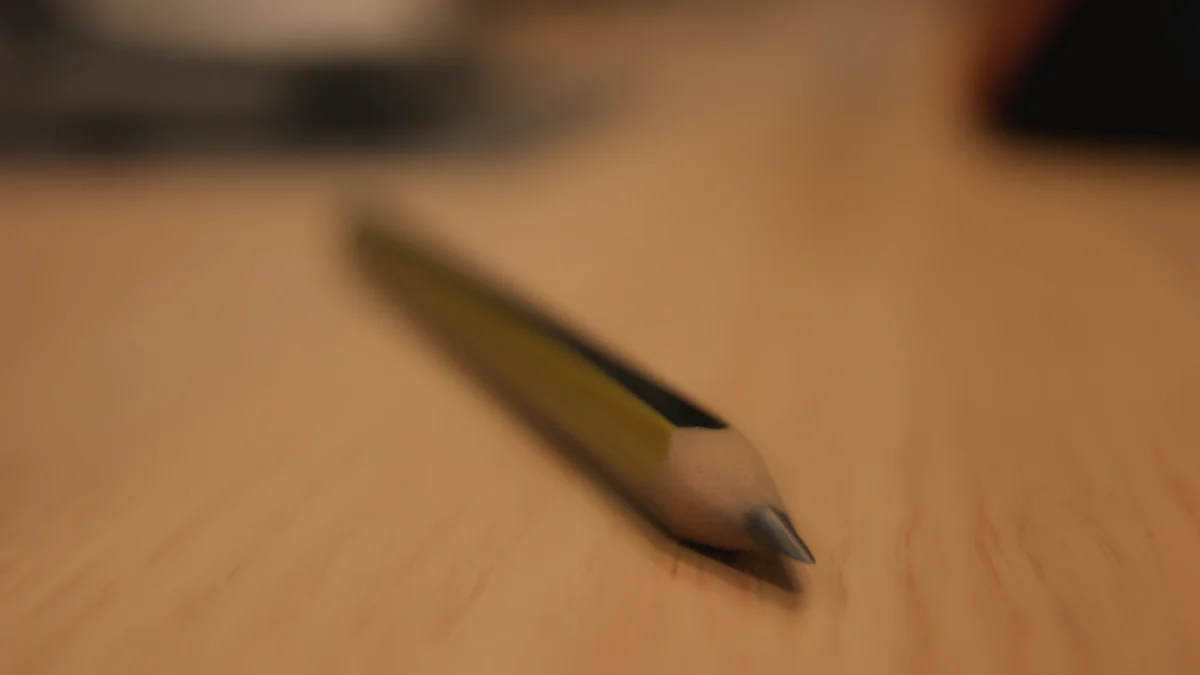
Importance in Wafer Processing
Ensuring uniformity and precision during wafer handling
The sic coated graphite carrier ensures precise and uniform wafer handling, a critical aspect of semiconductor manufacturing.
Reducing contamination risks in critical processes
Contamination poses a significant threat to semiconductor production. The sic coated graphite carrier acts as a protective barrier, preventing harmful particles from coming into contact with delicate wafers. Its silicon carbide coating resists chemical reactions and degradation, maintaining a clean and stable environment during critical processes. This feature reduces the likelihood of defects, ensuring the production of reliable and high-quality semiconductors.
Contribution to Yield and Quality Control
Minimizing defects and improving production efficiency
Defect reduction is essential for maintaining high yields in semiconductor manufacturing. The sic coated graphite carrier plays a pivotal role in this regard by providing a stable and contamination-resistant platform. Its thermal and chemical stability ensures consistent performance, reducing the chances of errors during production. This reliability enhances efficiency, allowing manufacturers to produce more functional devices with fewer resources.
Enhancing the reliability of semiconductor devices
The quality of semiconductor devices depends on the precision and stability of the manufacturing process. The sic coated graphite carrier contributes to this reliability by supporting uniform wafer processing and minimizing contamination risks. Its robust design ensures that each wafer undergoes consistent treatment, resulting in devices that meet stringent performance standards. This reliability is crucial for applications in advanced technologies, where even minor defects can lead to significant issues.
Compatibility with Advanced Manufacturing Techniques
Supporting next-generation technologies like 3D stacking
The evolution of semiconductor technology demands innovative manufacturing solutions. The sic coated graphite carrier supports next-generation techniques such as 3D stacking, which requires precise handling and stable thermal conditions. Its ability to maintain structural integrity under extreme temperatures makes it an ideal choice for these advanced processes. By enabling the production of complex designs, these carriers drive innovation in the semiconductor industry.
Enabling high-volume production with consistent results
High-volume production requires equipment that can deliver consistent performance over extended periods. The sic coated graphite carrier excels in this area, offering durability and reliability in demanding environments. Its silicon carbide coating resists wear and tear, ensuring that it maintains functionality throughout intensive manufacturing cycles. This consistency allows manufacturers to meet large-scale production demands without compromising quality, making it a cornerstone of modern semiconductor fabrication.
Comparison with Alternatives
Why SiC Coating Outperforms Other Materials
Superior thermal and chemical resistance compared to metals or ceramics
The sic coated graphite carrier surpasses metals and ceramics in thermal and chemical resistance. Silicon carbide (SiC) coatings provide unmatched stability under extreme temperatures, a critical requirement in semiconductor manufacturing. Unlike metals, which may warp or degrade under high heat, SiC maintains its structural integrity. Ceramics, while heat-resistant, often lack the chemical resilience needed to withstand corrosive gases and chemicals used in processes like chemical vapor deposition (CVD). SiC-coated carriers excel in both areas, ensuring consistent performance and reliability in demanding environments.
"SiC coatings provide excellent corrosion resistance, effectively protecting the graphite base from harmful gases encountered in semiconductor manufacturing."
This dual advantage makes SiC-coated carriers indispensable for producing high-quality semiconductors. Their ability to endure harsh conditions without compromising functionality sets them apart from alternative materials.
Enhanced mechanical strength and reduced risk of failure
SiC coatings significantly enhance the mechanical strength of graphite carriers. The silicon carbide layer acts as a robust shield, reducing the risk of fractures or deformation during high-stress operations. Metals, though strong, are prone to fatigue over time, while ceramics can be brittle and susceptible to cracking. SiC-coated carriers combine the best of both worlds—durability and resilience—ensuring long-term reliability.
This enhanced strength minimizes operational disruptions caused by carrier failures. Manufacturers benefit from fewer replacements and repairs, leading to smoother production cycles. The superior mechanical properties of SiC-coated carriers make them a preferred choice for advanced semiconductor manufacturing techniques.
Cost-Effectiveness Over Time
Lower maintenance and replacement costs
The sic coated graphite carrier offers significant cost advantages over time. Its durability and resistance to wear reduce the frequency of maintenance and replacements. Uncoated graphite carriers, metals, and ceramics often require more frequent servicing due to oxidation, corrosion, or mechanical damage. SiC coatings protect the graphite base, extending the carrier’s lifespan and lowering overall maintenance expenses.
"Applying SiC and TaC coatings to protect graphite from oxidation enhances the durability of graphite components in semiconductor manufacturing."
This longevity translates into substantial savings for manufacturers. By investing in SiC-coated carriers, companies can allocate resources more efficiently, focusing on innovation and production rather than equipment upkeep.
Improved operational efficiency and reduced downtime
Operational efficiency is a cornerstone of successful semiconductor manufacturing. SiC-coated carriers contribute to this by minimizing downtime caused by equipment failures or replacements. Their ability to withstand rigorous conditions ensures uninterrupted production, even during high-volume manufacturing cycles. In contrast, alternatives like metals and ceramics may require frequent adjustments or replacements, disrupting workflows.
The market for SiC-coated graphite wafer carriers, valued at USD 450 million in 2022, reflects the growing demand for materials that enhance efficiency and reliability. By reducing downtime and improving operational consistency, SiC-coated carriers enable manufacturers to meet tight production schedules and maintain competitive advantages.
SiC coated graphite carriers have become indispensable in semiconductor manufacturing, driving advancements in efficiency and innovation. Their exceptional properties, such as durability, thermal stability, and chemical resistance, ensure reliable performance in demanding environments. These carriers support intricate processes like epitaxial growth and wafer handling, maintaining high purity and consistent results. As semiconductor technologies evolve, the role of these carriers will only grow, solidifying their position as a cornerstone of high-quality production. By enabling precise, efficient, and contamination-free manufacturing, they continue to shape the future of the semiconductor industry.
FAQ
What makes SiC coated graphite carriers essential in semiconductor manufacturing?
SiC coated graphite carriers provide unmatched thermal stability, chemical resistance, and mechanical strength. These properties ensure reliable performance during high-temperature and corrosive processes like chemical vapor deposition (CVD). Their precision and durability make them indispensable for producing high-quality semiconductors.
How does the SiC coating enhance the lifespan of graphite carriers?
The silicon carbide (SiC) coating acts as a protective barrier, shielding the graphite base from oxidation, wear, and chemical degradation.
What are the primary raw materials used in manufacturing SiC coated graphite carriers?
Silicon carbide (SiC), a compound of silicon and carbon, serves as the primary material for the coating. The graphite base provides structural support. Together, these materials create a carrier capable of withstanding extreme conditions in semiconductor manufacturing.
How do SiC coated graphite carriers contribute to contamination control?
The SiC coating resists chemical reactions and prevents the release of particles, maintaining a clean environment during wafer processing. This feature minimizes contamination risks, ensuring the production of defect-free semiconductor components.
Why are SiC coated graphite carriers preferred over metal or ceramic alternatives?
SiC coated graphite carriers outperform metals and ceramics in thermal and chemical resistance.
What role do SiC coated graphite carriers play in advanced manufacturing techniques?
These carriers support next-generation technologies like 3D stacking by providing precise handling and stable thermal conditions. Their ability to maintain structural integrity under extreme temperatures makes them ideal for complex and innovative semiconductor processes.
How do SiC coated graphite carriers improve production efficiency?
Their durability and resistance to wear reduce downtime caused by equipment failures. By maintaining consistent performance during high-volume manufacturing cycles, these carriers enhance operational efficiency and support tight production schedules.
What factors influence the cost of SiC coated graphite carriers?
The cost depends on the quality of raw materials, such as silicon carbide and graphite, and the complexity of the manufacturing process. Advanced coating technologies and precision engineering also contribute to the final price.
Are SiC coated graphite carriers environmentally sustainable?
SiC coated graphite carriers offer extended lifespans, reducing waste from frequent replacements. Their durability and efficiency contribute to more sustainable manufacturing practices by minimizing resource consumption and operational disruptions.
What trends are shaping the future of SiC coated graphite carriers?
The growing demand for high-performance semiconductors and advanced technologies like 5G and AI drives innovation in SiC coated graphite carriers. Their role in supporting intricate designs and high-volume production ensures their continued relevance in the evolving semiconductor industry.