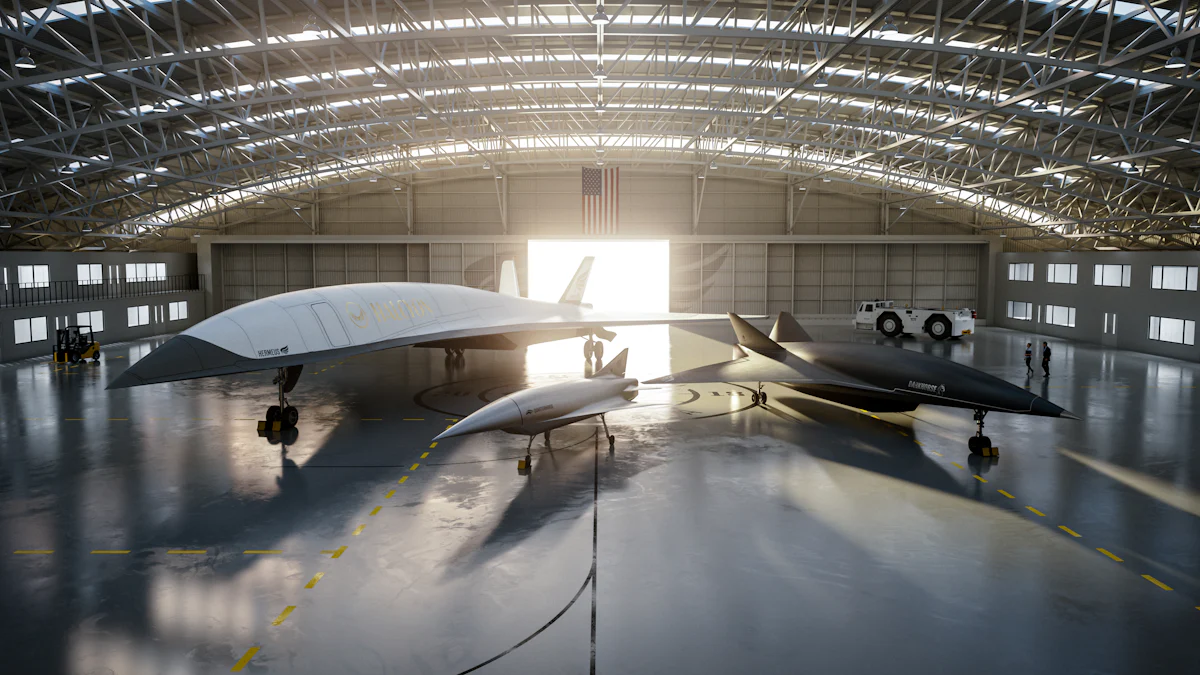
Maintaining cleanliness in Aixtron reactor components is essential for ensuring optimal performance, safety, and extended operational life. Contaminants can compromise the precision of processes, leading to defects and inefficiencies. Regular cleaning prevents imperfections on wafers and enhances reproducibility, as confirmed by advanced systems like AIXTRON’s G10-AsP. Automated cleaning technologies, in use since 2005, have significantly improved reactor efficiency by reducing downtime and maintaining material accuracy. Proper cleaning practices not only safeguard the integrity of the reactor but also contribute to higher yields and better uniformity in production.
Key Takeaways
- Regular cleaning of Aixtron reactor components is crucial for optimal performance and longevity, preventing defects and inefficiencies in semiconductor manufacturing.
- Implement a structured maintenance schedule that includes daily inspections, weekly light cleaning, and monthly deep cleaning to ensure consistent performance.
- Use the right tools and cleaning agents, such as soft-bristle brushes and isopropyl alcohol, to effectively remove contaminants without damaging sensitive surfaces.
- Prioritize safety by equipping maintenance personnel with protective gear and following proper shutdown procedures to mitigate risks during cleaning.
- Document all maintenance activities, including inspections and cleaning processes, to create a comprehensive history that supports future maintenance efforts.
- Avoid common mistakes like using incorrect cleaning agents or skipping safety precautions, as these can lead to costly damage and operational inefficiencies.
- Leverage automated cleaning technologies to enhance productivity, reduce downtime, and maintain consistent cleanliness in Aixtron reactors.
Why Cleaning and Maintenance Are Critical
Proper cleaning and maintenance of Aixtron reactor components play a pivotal role in ensuring their efficiency and longevity. Neglecting these essential tasks can lead to significant operational challenges, while regular upkeep offers numerous benefits that enhance reactor performance and reliability.
Risks of Neglecting Aixtron Reactor Component Maintenance
Failing to maintain Aixtron reactor components can result in severe consequences. Contaminants and residues left unaddressed may compromise the precision of semiconductor manufacturing processes. This can lead to defects in wafers, reducing production quality and yield. Over time, neglect can cause corrosion or heat-stress-induced cracks in critical components, such as reactor pipes. These issues, if undetected, may escalate into leaks or system failures, jeopardizing safety and operational stability.
For instance, routine maintenance checks in industrial systems have identified tiny cracks caused by heat stress. Without timely intervention, such issues could lead to catastrophic failures, as seen in other industries where maintenance lapses resulted in extended shutdowns and reduced availability.
Additionally, skipping maintenance increases the risk of contamination within the reactor. Contaminants can disrupt the stability of the susceptor coating film, a critical element in Aixtron reactors. This instability can degrade the reactor’s performance, leading to inefficiencies and higher operational costs. Neglect also shortens the lifespan of components, necessitating frequent replacements and increasing downtime.
Benefits of Regular Cleaning and Maintenance
Regular cleaning and maintenance provide numerous advantages for Aixtron reactor components. By removing contaminants and residues, these practices ensure consistent and precise manufacturing processes. Clean components contribute to higher wafer quality, improved uniformity, and better reproducibility in production. This directly translates to increased yields and reduced waste.
Standardized cleaning methods, widely adopted in the semiconductor industry, help maintain the integrity of reactor components. These methods prevent contamination and ensure optimal performance, even under demanding operational conditions.
Preventive maintenance programs also enhance the reliability of Aixtron reactors. Detailed procedures for cleaning, lubrication, and testing of critical components minimize the risk of unexpected failures. Automated self-cleaning features in modern reactors further streamline maintenance efforts, reducing downtime and improving operational efficiency.
Moreover, regular upkeep extends the lifespan of reactor components. Proper cleaning prevents corrosion and wear, preserving the structural integrity of parts. This reduces the need for frequent replacements, saving costs and resources in the long run. Maintenance also ensures compliance with safety standards, protecting both personnel and equipment.
Tools and Materials Needed for Cleaning Aixtron Reactor Components
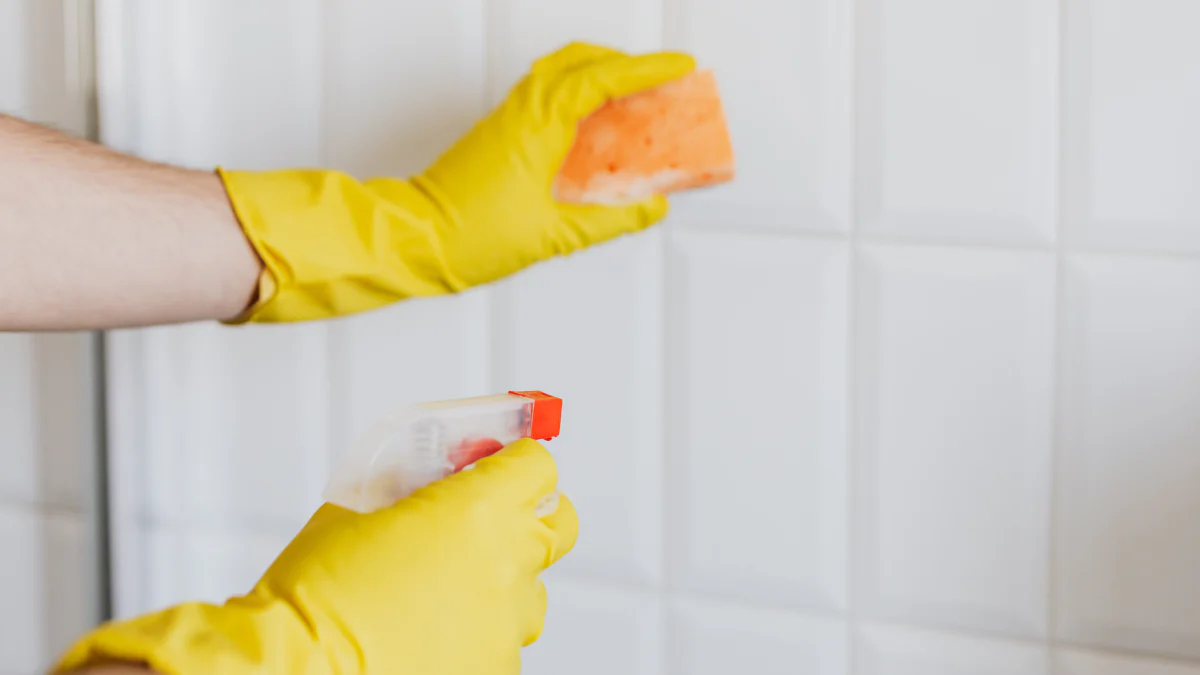
Proper cleaning of Aixtron reactor components requires the right tools, agents, and safety equipment. Using appropriate materials ensures effective cleaning while maintaining the integrity of the components. This section outlines the essential items needed for the cleaning process.
Essential Cleaning Tools
Cleaning Aixtron reactor components demands precision and efficiency. The following tools are indispensable for achieving thorough results:
- Soft-Bristle Brushes: These brushes help remove debris and contaminants without scratching sensitive surfaces.
- Non-Abrasive Sponges: Ideal for cleaning delicate parts, these sponges prevent damage to coatings and finishes.
- Microfiber Cloths: These cloths effectively trap dust and particles, ensuring a spotless finish.
- Vacuum Systems: High-efficiency vacuum systems remove fine particles and residues from hard-to-reach areas.
- Disassembly Tools: Screwdrivers, wrenches, and other tools facilitate the safe removal of components for detailed cleaning.
Standardized cleaning tools, such as those used in semiconductor manufacturing, ensure consistent results and prevent contamination during maintenance.
Recommended Cleaning Agents
Selecting the right cleaning agents is critical for maintaining the performance and longevity of Aixtron reactor components. The following agents are highly recommended:
- Isopropyl Alcohol (IPA): This solvent effectively removes grease, oils, and other residues without leaving streaks.
- Deionized Water: Essential for rinsing, deionized water prevents mineral deposits and ensures a residue-free surface.
- Mild Detergents: These detergents clean surfaces gently, preserving the integrity of coatings and materials.
- Specialized Cleaning Solutions: Certain components may require industry-specific solutions designed for semiconductor equipment.
AIXTRON’s advanced reactors, such as the G10-AsP, incorporate in-situ cleaning mechanisms that utilize specialized etching agents. These agents enhance cleaning efficiency and reduce manual intervention.
Safety Equipment
Safety remains a top priority when cleaning Aixtron reactor components. Proper protective gear minimizes risks and ensures compliance with safety standards. Essential safety equipment includes:
- Gloves: Nitrile or latex gloves protect hands from chemicals and contaminants.
- Safety Goggles: These goggles shield eyes from splashes and debris during cleaning.
- Respirators: Respirators prevent inhalation of harmful fumes or particles.
- Protective Clothing: Lab coats or coveralls safeguard skin and clothing from exposure to cleaning agents.
- Chemical Spill Kits: These kits provide immediate response tools for accidental spills, ensuring a safe work environment.
Training maintenance personnel on the correct use of safety equipment enhances the effectiveness of cleaning protocols and reduces workplace hazards.
By equipping maintenance teams with the right tools, agents, and safety gear, organizations can ensure the proper upkeep of Aixtron reactor components. This approach not only preserves the functionality of the equipment but also promotes a safe and efficient working environment.
Step-by-Step Cleaning Process for Aixtron Reactor Components
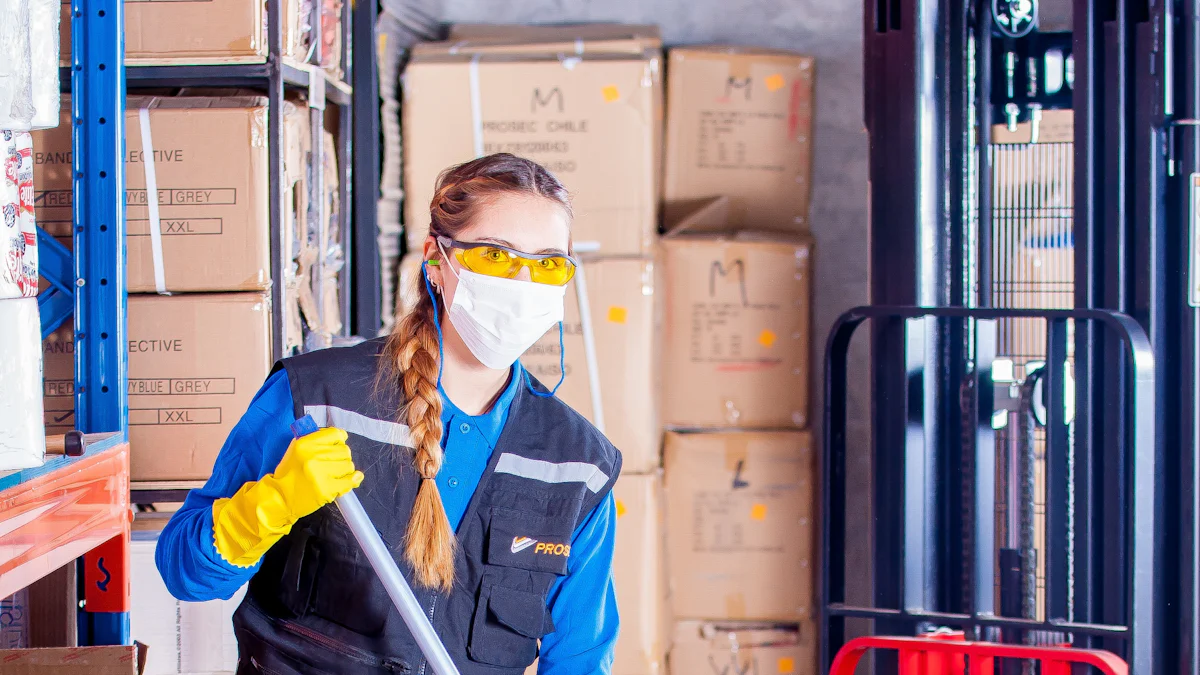
Proper cleaning of Aixtron reactor components requires a systematic approach to ensure thoroughness and precision. Following a step-by-step process minimizes risks, maintains component integrity, and enhances operational efficiency.
Preparation
Preparation is the foundation of an effective cleaning process. Maintenance personnel must gather all necessary tools, cleaning agents, and safety equipment before beginning. This ensures a smooth workflow and reduces the likelihood of errors.
- Inspect the Reactor: Conduct a visual inspection to identify areas with visible contaminants or residues. Note any signs of wear or damage that may require attention during cleaning.
- Assemble Tools and Materials: Collect essential cleaning tools such as soft-bristle brushes, microfiber cloths, and vacuum systems. Ensure the availability of recommended cleaning agents like isopropyl alcohol and deionized water.
- Set Up a Clean Workspace: Establish a contamination-free environment by cleaning the workspace and organizing tools systematically. This step prevents external particles from interfering with the cleaning process.
- Wear Safety Gear: Equip personnel with gloves, safety goggles, and respirators to protect against chemical exposure and airborne particles.
AIXTRON’s advanced reactors, such as the G10-AsP, incorporate in-situ cleaning mechanisms. These features reduce manual preparation efforts by addressing contaminants during operation.
Disassembly
Disassembling the reactor components allows for detailed cleaning and inspection. Proper handling during this stage ensures the safety of both personnel and equipment.
- Power Down the Reactor: Shut down the reactor and disconnect it from power sources to eliminate electrical hazards.
- Refer to Manufacturer Guidelines: Follow the disassembly instructions provided by the reactor’s manufacturer. This ensures that components are removed in the correct sequence without causing damage.
- Remove Critical Components: Carefully detach parts such as the susceptor, quartz tubes, and graphite plates. Place these components on a clean, non-abrasive surface to prevent scratches or contamination.
- Label and Organize Parts: Use labels or containers to keep track of disassembled components. This step simplifies reassembly and reduces the risk of misplaced parts.
The stability of the susceptor coating film is crucial during disassembly. Mishandling can compromise its integrity, leading to performance issues in subsequent operations.
Cleaning
The cleaning stage focuses on removing contaminants and restoring the components to their optimal condition. Using the right techniques and materials ensures effective results without damaging sensitive surfaces.
- Clean with Soft Tools: Use soft-bristle brushes and non-abrasive sponges to remove debris and residues. Avoid applying excessive force to prevent scratches or damage.
- Apply Cleaning Agents: Use isopropyl alcohol to dissolve grease and oils. Rinse with deionized water to eliminate any remaining particles or streaks. For stubborn contaminants, apply specialized cleaning solutions recommended for semiconductor equipment.
- Dry Thoroughly: After rinsing, dry the components using lint-free microfiber cloths or air-drying methods. Ensure no moisture remains, as it can lead to corrosion or contamination.
- Inspect Cleaned Components: Examine each part for cleanliness and structural integrity. Address any persistent residues or signs of wear before proceeding to reassembly.
Standardized cleaning methods, as seen in semiconductor manufacturing, maintain the integrity of Aixtron reactor components. These practices ensure consistent results and prevent contamination.
By following these steps, maintenance teams can effectively clean Aixtron reactor components, ensuring their longevity and performance. Proper preparation, careful disassembly, and meticulous cleaning contribute to the overall efficiency and reliability of the reactor.
Reassembly
Reassembling Aixtron reactor components requires precision and adherence to proper procedures to ensure the equipment functions optimally after cleaning. Maintenance personnel must handle each component carefully to avoid damage and ensure correct placement.
- Inspect Components Before Reassembly: Examine all cleaned parts for any signs of wear, cracks, or damage. Replace any defective components to maintain the reactor’s integrity and performance.
- Follow Manufacturer Guidelines: Refer to the reactor’s manual for specific reassembly instructions. This ensures that each part is installed in the correct sequence and orientation.
- Secure Components Properly: Use appropriate tools to fasten screws, bolts, and other fixtures. Avoid over-tightening, which can cause stress or damage to sensitive parts.
- Reinstall Critical Components: Place essential parts, such as the susceptor and quartz tubes, back into their designated positions. Ensure that the susceptor coating film remains intact during this process, as its stability is crucial for reactor performance.
- Double-Check Connections: Verify that all electrical and mechanical connections are secure. Loose connections can lead to operational issues or safety hazards.
Proper reassembly not only restores the functionality of the reactor but also prevents potential contamination or inefficiencies during operation. AIXTRON’s advanced systems, such as the G10-AsP, emphasize the importance of precise component alignment for optimal performance.
Testing
Testing the Aixtron reactor after reassembly ensures that all components function correctly and that the cleaning process has not introduced any issues. This step validates the reactor’s readiness for operation and helps identify any remaining concerns.
- Perform a Visual Inspection: Check the reactor for any visible signs of misalignment, loose connections, or residual contaminants. Address any issues before proceeding with functional tests.
- Conduct a Dry Run: Power up the reactor without initiating production processes. Monitor the system for unusual noises, vibrations, or error messages. This step helps identify mechanical or electrical problems early.
- Test Critical Functions: Evaluate the performance of key components, such as the susceptor and heating elements. Ensure that temperature control, gas flow, and other critical parameters meet the manufacturer’s specifications.
- Verify Cleaning Effectiveness: Inspect the reactor’s interior for any remaining residues or particles. If necessary, repeat the cleaning process to achieve the desired level of cleanliness.
- Document Test Results: Record the outcomes of all tests, including any adjustments or repairs made during this stage. Maintaining detailed records supports future maintenance efforts and ensures compliance with industry standards.
AIXTRON’s in-situ cleaning technologies, as seen in the G10-AsP system, streamline post-cleaning testing by reducing the likelihood of contamination and defects. These innovations enhance the reliability and efficiency of the testing process.
By following these steps, maintenance teams can ensure that the Aixtron reactor component is fully operational and ready for production. Thorough testing minimizes the risk of downtime and maintains the reactor’s performance and safety.
Maintenance Tips for Prolonging the Lifespan of Aixtron Reactor Components
Establishing a Routine Maintenance Schedule
A structured maintenance schedule ensures the consistent performance of Aixtron reactor components. Regular intervals for cleaning, inspection, and testing prevent the accumulation of contaminants and identify potential issues early. Maintenance teams should define specific timelines based on operational intensity and environmental conditions.
- Daily Inspections: Conduct visual checks to detect visible residues, wear, or damage. Address minor issues immediately to avoid escalation.
- Weekly Cleaning: Perform light cleaning using soft-bristle brushes and deionized water to remove surface contaminants. This prevents buildup that could compromise component integrity.
- Monthly Deep Cleaning: Disassemble critical components, such as the susceptor and quartz tubes, for thorough cleaning. Use recommended cleaning agents like isopropyl alcohol to ensure optimal results.
- Quarterly Testing: Test the reactor’s functionality after reassembly to validate its performance. Load bank testing can verify system efficiency and operational reliability.
A routine maintenance schedule not only optimizes system efficiency but also ensures safety and prolongs the lifespan of components.
Preventive Measures for Aixtron Reactor Components
Preventive measures reduce the likelihood of unexpected failures and extend the operational life of Aixtron reactor components. These proactive steps focus on minimizing wear and contamination while maintaining system stability.
- Use High-Quality Cleaning Agents: Select cleaning solutions specifically designed for semiconductor equipment. Avoid harsh chemicals that may damage sensitive surfaces.
- Monitor Environmental Conditions: Maintain a clean and controlled environment around the reactor. Dust and airborne particles can infiltrate the system and cause contamination.
- Train Maintenance Personnel: Provide comprehensive training on cleaning protocols and safety procedures. Skilled personnel ensure proper handling of components and adherence to best practices.
- Inspect Coating Stability: Regularly check the susceptor coating film for signs of degradation. A stable coating enhances cleaning efficiency and supports consistent reactor performance.
Preventive maintenance programs, including cleaning and testing, play a crucial role in maintaining the operational integrity of Aixtron reactor components.
Documentation and Record-Keeping
Accurate documentation supports effective maintenance and ensures compliance with industry standards. Maintenance teams should record all activities, including inspections, cleaning, and repairs, to create a comprehensive history of the reactor’s condition.
- Log Maintenance Activities: Record the date, time, and details of each maintenance task. Include observations, such as the presence of contaminants or signs of wear.
- Track Component Lifespan: Monitor the usage and replacement history of critical parts. This helps predict when components may require replacement, reducing downtime.
- Store Test Results: Keep records of functional tests conducted after cleaning and reassembly. These results validate the reactor’s readiness for operation and highlight any recurring issues.
- Review and Update Procedures: Periodically review maintenance logs to identify patterns or areas for improvement. Update cleaning protocols based on findings to enhance efficiency.
Comprehensive documentation ensures traceability and supports informed decision-making for future maintenance efforts.
By implementing these maintenance tips, organizations can maximize the lifespan and performance of Aixtron reactor components. A proactive approach to scheduling, preventive measures, and record-keeping safeguards the reactor’s integrity and operational efficiency.
Common Mistakes to Avoid When Cleaning Aixtron Reactor Components
Using Incorrect Cleaning Agents
Selecting the wrong cleaning agents can severely damage Aixtron reactor components. Some cleaning solutions contain harsh chemicals that may corrode sensitive surfaces or compromise the integrity of coatings, such as the susceptor coating film. This film plays a critical role in maintaining reactor performance and stability. For instance, improper cleaning agents can degrade the coating, leading to inefficiencies and increased defect levels in semiconductor production.
Beckers, an industry expert, highlighted that in-situ reactor cleaning with appropriate agents significantly reduces defect levels and ensures optimal particle control.
To avoid this mistake, maintenance teams should always use cleaning agents specifically designed for semiconductor equipment. Isopropyl alcohol and deionized water are excellent choices for removing grease and residues without leaving harmful deposits. Mild detergents and specialized solutions recommended by manufacturers also ensure safe and effective cleaning. Teams must consult the reactor’s manual or seek expert advice when selecting cleaning agents.
Skipping Safety Precautions
Neglecting safety precautions during the cleaning process can lead to accidents and equipment damage. Cleaning Aixtron reactor components often involves handling chemicals and disassembling intricate parts, which pose risks to both personnel and the reactor. For example, failing to wear gloves or goggles may result in chemical burns or eye injuries. Similarly, ignoring proper shutdown procedures can expose workers to electrical hazards.
Holger Jürgensen, co-founder of Aixtron, emphasized the importance of safety during early reactor operations. Fans were used during the cool-down phase to enhance productivity while ensuring safe handling conditions.
To mitigate risks, maintenance personnel must prioritize safety at every step. Wearing nitrile gloves, safety goggles, and respirators protects against chemical exposure and airborne particles. Properly shutting down the reactor and disconnecting power sources eliminates electrical dangers. Additionally, training staff on safety protocols ensures they handle components and cleaning agents responsibly.
Improper Reassembly
Reassembling Aixtron reactor components incorrectly can compromise the reactor’s functionality and lead to costly downtime. Misaligned parts or loose connections may disrupt critical processes, such as gas flow and temperature control. For instance, improper reinstallation of the susceptor can destabilize the coating film, reducing its effectiveness and increasing contamination risks.
AIXTRON’s advanced systems, like the G10-AsP, emphasize precise component alignment to maintain performance and reduce defects.
To prevent errors, maintenance teams should follow the manufacturer’s reassembly guidelines meticulously. Inspecting each component for wear or damage before reinstallation ensures only functional parts are used. Labeling and organizing disassembled components simplifies the process and minimizes confusion. Double-checking connections and securing fixtures properly guarantees the reactor operates efficiently after maintenance.
By avoiding these common mistakes, organizations can ensure the longevity and reliability of Aixtron reactor components. Proper cleaning agents, strict adherence to safety measures, and accurate reassembly practices safeguard both personnel and equipment, enhancing overall operational efficiency.
Regular cleaning and maintenance of Aixtron reactor components are essential for ensuring optimal performance, safety, and longevity. By following the outlined steps, organizations can prevent contamination, reduce downtime, and maintain the integrity of critical parts. These practices not only enhance operational efficiency but also support higher yields and better uniformity in production. As Dr. Felix Grawert highlighted, achieving the lowest defect levels and highest uniformity rates is crucial in advanced technologies. Implementing these maintenance strategies empowers teams to extend the lifespan of their equipment while maintaining industry standards.
FAQ
What is the importance of cleaning Aixtron reactor components?
Cleaning Aixtron reactor components ensures optimal performance and extends their lifespan. Contaminants can disrupt manufacturing processes, leading to defects and inefficiencies. Regular cleaning maintains the integrity of critical parts, reduces downtime, and enhances wafer quality.
Automated self-cleaning features, such as those in the AIXTRON G10-AsP system, significantly improve productivity by reducing maintenance time and ensuring consistent cleanliness.
How often should Aixtron reactor components be cleaned?
The frequency of cleaning depends on operational intensity and environmental conditions. Daily inspections, weekly light cleaning, and monthly deep cleaning are recommended. Establishing a routine maintenance schedule ensures consistent performance and prevents contamination buildup.
What tools are essential for cleaning Aixtron reactor components?
Maintenance teams require specific tools for effective cleaning:
- Soft-bristle brushes for removing debris.
- Non-abrasive sponges to clean delicate surfaces.
- Microfiber cloths for trapping fine particles.
- Vacuum systems to access hard-to-reach areas.
- Disassembly tools for safe removal of components.
Using the right tools prevents damage and ensures thorough cleaning.
Which cleaning agents are safe for Aixtron reactor components?
Safe cleaning agents include:
- Isopropyl alcohol (IPA) for dissolving grease and residues.
- Deionized water for rinsing without leaving mineral deposits.
- Mild detergents for gentle cleaning.
- Specialized solutions designed for semiconductor equipment.
Avoid harsh chemicals that may corrode sensitive surfaces or compromise coatings.
What safety precautions should be taken during cleaning?
Safety is crucial when cleaning Aixtron reactor components. Maintenance personnel should:
- Wear nitrile gloves, safety goggles, and respirators.
- Shut down the reactor and disconnect power sources.
- Use a clean workspace to prevent contamination.
- Follow proper handling procedures for chemicals and tools.
Holger Jürgensen, co-founder of Aixtron, emphasized the importance of safety during reactor operations to protect both personnel and equipment.
How does automated cleaning technology benefit Aixtron reactors?
Automated cleaning technology, like the G10-AsP system, enhances productivity by reducing manual intervention. It ensures consistent cleanliness, minimizes wafer defects, and decreases maintenance downtime. This innovation supports higher yields and better uniformity in production.
What are the risks of using incorrect cleaning agents?
Incorrect cleaning agents can damage reactor components. Harsh chemicals may corrode surfaces or degrade critical coatings, such as the susceptor coating film. This can lead to inefficiencies, increased defect levels, and higher operational costs. Always use manufacturer-recommended solutions.
Why is proper reassembly important after cleaning?
Proper reassembly ensures the reactor functions optimally. Misaligned parts or loose connections can disrupt processes like gas flow and temperature control. Following manufacturer guidelines and double-checking connections prevent operational issues and maintain performance.
How can maintenance teams optimize reactor efficiency?
Maintenance teams can optimize efficiency by:
- Following a structured maintenance schedule.
- Using high-quality cleaning agents and tools.
- Conducting regular inspections and functional tests.
- Training personnel on cleaning protocols and safety measures.
Testing with load banks validates component performance, reduces wear, and enhances equipment lifespan.
What documentation should be maintained during cleaning and maintenance?
Accurate documentation supports effective maintenance. Teams should:
- Log all cleaning and inspection activities.
- Track the lifespan and replacement history of components.
- Record test results after reassembly.
- Review and update maintenance protocols regularly.
Comprehensive records ensure traceability and compliance with industry standards.