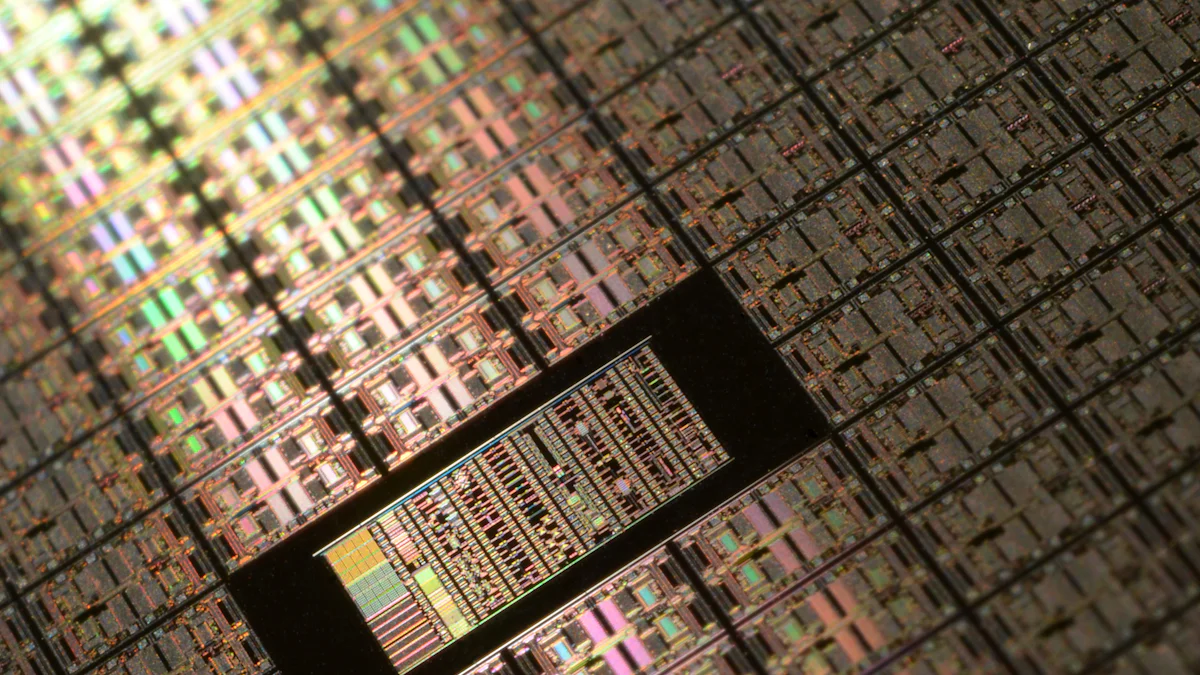
Silicon carbide (SiC) boats serve as indispensable components in the semiconductor industry. They play a pivotal role in facilitating the production of high-quality electronic devices. These boats hold semiconductor wafers during critical manufacturing processes, ensuring precision and uniformity. The demand for SiC boats continues to rise due to their ability to enhance efficiency, improve wafer quality, and minimize contamination risks. Their application spans various industries, including aerospace, defense, and chemical processing, highlighting their versatility and importance in modern technology.
Key Takeaways
- SiC boats are crucial for maintaining wafer integrity during semiconductor manufacturing, ensuring precision and reducing damage risks.
- Their exceptional thermal stability allows SiC boats to perform reliably in high-temperature processes, enhancing overall production efficiency.
- The chemical resistance of SiC boats minimizes contamination risks, leading to higher yields and improved quality of electronic components.
- Investing in SiC boats can result in long-term cost savings due to their durability and reduced need for frequent replacements.
- SiC boats facilitate uniform heat distribution during diffusion and oxidation, which is essential for achieving consistent semiconductor properties.
- The growing demand for SiC boats reflects their versatility across various industries, including aerospace and defense, highlighting their importance in modern technology.
- Ongoing innovations in SiC boat design promise to meet the evolving needs of the semiconductor industry, ensuring their continued relevance and effectiveness.
Applications of SiC Boats in Semiconductor Manufacturing
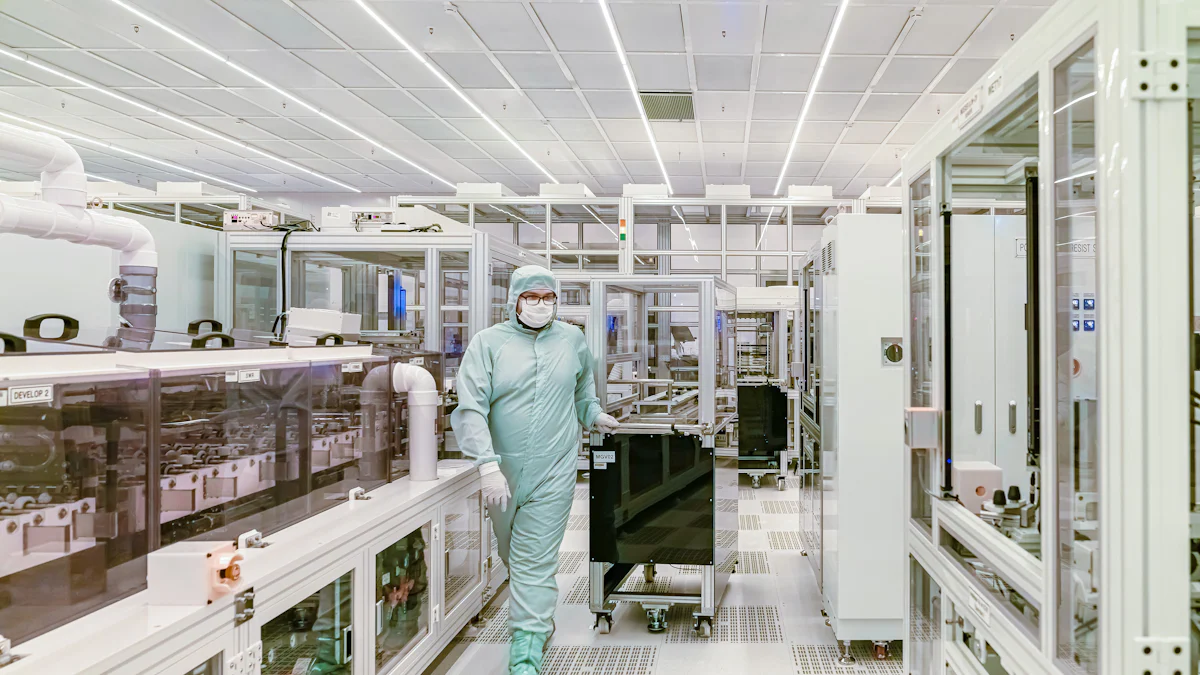
Wafer Processing
Role in Wafer Loading and Unloading
In semiconductor manufacturing, SiC boats play a crucial role in wafer processing. They serve as carriers for silicon wafers during various stages, such as etching, cleaning, and diffusion. The robust design of these boats ensures that wafers are loaded and unloaded with precision, minimizing the risk of damage. This precision is vital for maintaining the integrity of the wafers, which are the foundation of semiconductor devices.
Importance in Maintaining Wafer Integrity
Maintaining wafer integrity is paramount in semiconductor production. SiC boats excel in this aspect due to their superior mechanical strength and low thermal expansion. These properties prevent warping and cracking, ensuring that wafers remain intact throughout high-temperature processes. By preserving wafer integrity, manufacturers can achieve higher yields and produce more reliable electronic components.
High-Temperature Operations
Use in Diffusion and Oxidation Processes
SiC boats are indispensable in high-temperature operations, particularly in diffusion and oxidation processes. Their exceptional thermal conductivity allows for uniform heat distribution, which is essential for achieving consistent results. During diffusion, these boats facilitate the even doping of substrates, a critical step in defining the electrical properties of semiconductors. In oxidation, they ensure that the silicon dioxide layer forms evenly, enhancing device performance.
Performance in Extreme Thermal Environments
The ability of SiC boats to withstand extreme thermal environments sets them apart from traditional materials. Their high thermal stability makes them ideal for use in processes that require temperatures exceeding 1000°C. This resilience not only enhances process efficiency but also extends the lifespan of the boats, making them a cost-effective choice for manufacturers.
LPCVD and Boron Diffusion
Application in LPCVD Stage of TOPCon Production
In the LPCVD (Low-Pressure Chemical Vapor Deposition) stage of TOPCon (Tunnel Oxide Passivated Contact) production, SiC boats are essential. They provide a stable platform for wafers, ensuring uniform deposition of thin films. This uniformity is crucial for the development of advanced semiconductor devices, such as solar cells and high-performance transistors.
Enhancing Efficiency in Boron Diffusion Processes
Boron diffusion is a key process in semiconductor fabrication, and SiC boats significantly enhance its efficiency. Their chemical resistance prevents contamination, while their thermal properties ensure precise control over the diffusion process. By optimizing boron diffusion, manufacturers can improve the electrical characteristics of semiconductors, leading to better-performing electronic devices.
Advantages of Using SiC Boats
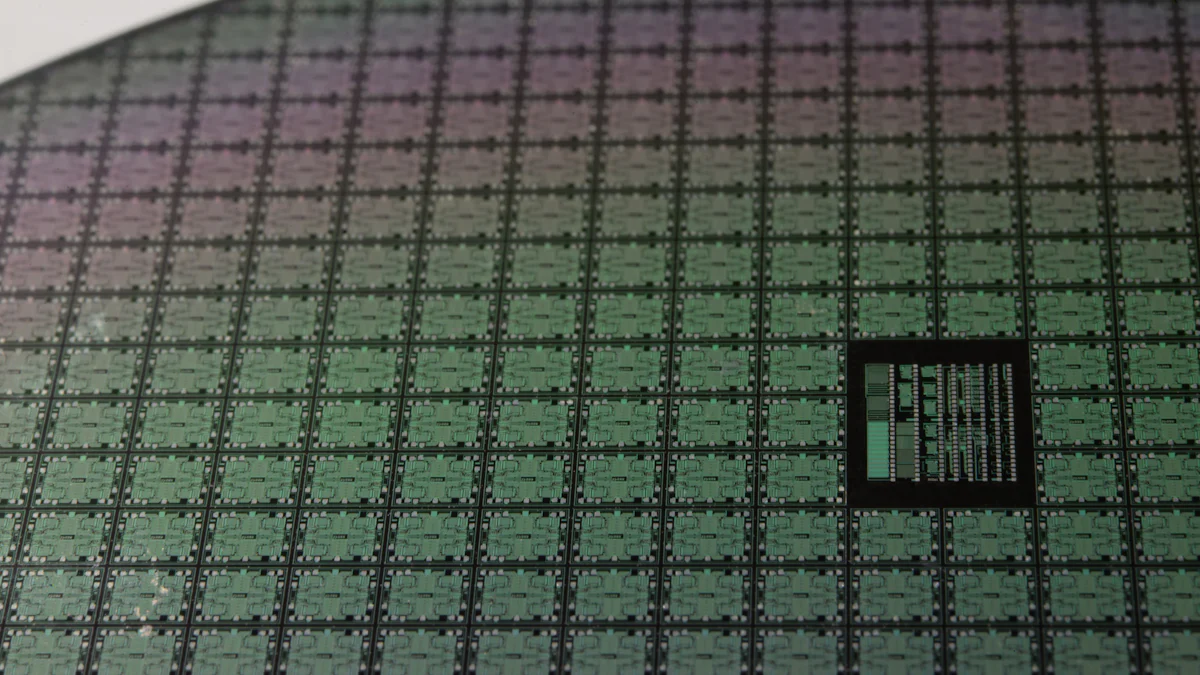
Durability and Longevity
Resistance to Wear and Tear
Silicon carbide (SiC) boats exhibit remarkable resistance to wear and tear, making them a preferred choice in semiconductor manufacturing. Their exceptional strength and hardness ensure that they withstand the rigors of repeated use without degrading. Unlike traditional graphite boats, SiC boats maintain their structural integrity over time, reducing the need for frequent replacements. This durability translates into significant cost savings for manufacturers, as they can rely on SiC boats for extended periods without compromising performance.
Cost-effectiveness Over Time
The long lifespan of SiC boats contributes to their cost-effectiveness. Although the initial investment may be higher compared to other materials, the reduced frequency of replacements and maintenance leads to lower overall costs. Manufacturers benefit from the consistent performance of SiC boats, which minimizes downtime and enhances productivity. By investing in SiC boats, companies can achieve a favorable return on investment, making them a financially sound choice for semiconductor applications.
Thermal Stability
Performance at High Temperatures
SiC boats excel in high-temperature environments, a critical requirement in semiconductor processing. Their ability to withstand extreme temperatures without losing mechanical stability sets them apart from other materials. This thermal stability ensures that SiC boats perform reliably during processes such as diffusion and oxidation, where temperatures often exceed 1000°C. The consistent performance of SiC boats at these temperatures enhances the quality and precision of semiconductor devices.
Impact on Process Efficiency
The thermal properties of SiC boats significantly impact process efficiency. Their low thermal expansion minimizes the risk of warping or cracking, ensuring that wafers remain intact throughout high-temperature operations. This stability allows for precise control over manufacturing processes, leading to higher yields and improved device performance. By maintaining consistent thermal conditions, SiC boats contribute to the overall efficiency and reliability of semiconductor production.
Chemical Resistance
Compatibility with Various Chemicals
SiC boats offer excellent chemical resistance, making them compatible with a wide range of chemicals used in semiconductor manufacturing. Their ability to resist chemical corrosion ensures that they maintain their structural integrity even when exposed to harsh environments. This compatibility reduces the risk of contamination, which is crucial for producing high-quality semiconductor devices. Manufacturers can rely on SiC boats to provide a stable and clean environment for wafer processing.
Reduction in Contamination Risks
The chemical resistance of SiC boats plays a vital role in minimizing contamination risks. By preventing chemical interactions that could compromise wafer integrity, SiC boats help maintain the purity of semiconductor materials. This reduction in contamination risks leads to higher yields and more reliable electronic components. The use of SiC boats in semiconductor manufacturing ensures that the final products meet stringent quality standards, enhancing their performance and longevity.
Case Studies and Examples
Industry Adoption
Examples of Companies Utilizing SiC Boats
Numerous companies in the semiconductor industry have embraced SiC boats due to their exceptional performance and reliability. For instance, leading semiconductor manufacturers have integrated SiC boats into their production lines to enhance wafer processing efficiency. These companies recognize the value of SiC boats in maintaining wafer integrity and reducing contamination risks. By adopting SiC boats, they achieve higher yields and produce superior electronic components.
Success Stories and Outcomes
The adoption of SiC boats has led to remarkable success stories within the semiconductor industry. One notable example involves a major semiconductor firm that reported a significant increase in production efficiency after implementing SiC boats. The company experienced a reduction in wafer defects and an improvement in overall product quality. This success underscores the critical role of SiC boats in advancing semiconductor manufacturing processes.
Technological Advancements
Innovations in SiC Boat Design
Recent technological advancements have spurred innovations in SiC boat design. Manufacturers are continually refining the quality and performance of SiC boats to meet the evolving demands of the semiconductor industry. These innovations include enhanced thermal stability and improved chemical resistance, which further solidify SiC boats as indispensable tools in semiconductor fabrication. The ongoing research and development efforts ensure that SiC boats remain at the forefront of technological progress.
Future Trends in Semiconductor Manufacturing
The future of semiconductor manufacturing looks promising with the continued integration of SiC boats. As the industry expands, the demand for high-performance materials like SiC boats will grow. The deployment of 5G networks and the rise of wide-bandgap semiconductors present significant opportunities for SiC boats. These trends highlight the importance of SiC boats in driving innovation and meeting the challenges of modern semiconductor production.
SiC boats have emerged as a cornerstone in semiconductor manufacturing, offering unparalleled benefits across various applications. Their high thermal conductivity and mechanical strength ensure efficient wafer processing and high-quality production. These boats significantly reduce contamination risks, enhancing the reliability of electronic devices. As industries like aerospace and defense increasingly rely on SiC boats for their resilience in harsh environments, their importance in advancing semiconductor technology becomes evident. The ongoing innovations in SiC boat design promise to meet the growing demands of modern high-tech applications, solidifying their role in the future of semiconductor fabrication.
FAQ
Why Choose Silicon Carbide Boats for Semiconductor Applications?
Silicon carbide (SiC) boats offer numerous advantages in semiconductor processing. They enhance efficiency, produce high-quality wafers, and reduce contamination risks. Their consistent performance in challenging environments enables semiconductor manufacturers to achieve better yield rates and maintain high product quality standards.
What are the Key Applications of SiC Boats?
SiC boats play a crucial role in holding semiconductor wafers during high-temperature diffusion processes. They ensure even exposure of wafers to gases and chemicals. Their high thermal conductivity facilitates uniform heating, which is essential for achieving consistent diffusion results.
What are the Advantages of SiC Boats in Wafer Processing?
SiC boats exhibit remarkable resistance to thermal shock and maintain their shape under extreme temperatures. This ensures consistent and reliable wafer positioning without deformation, making them ideal for wafer processing.
How are SiC Boats Used in Semiconductor Manufacturing?
In semiconductor manufacturing, SiC boats serve as essential components. They are used in the production of semiconductors, photovoltaic cells, and other high-performance electronic devices. Their high thermal conductivity, low thermal expansion, and superior mechanical strength make them suitable for high-temperature and harsh chemical environments.
What is the Market Size and Growth Projection for SiC Boats?
As of 2023, the market size for SiC boats was estimated at USD 2.0 billion. Projections indicate substantial growth, with expectations to reach USD 6.5 billion by 2032. This growth reflects a robust Compound Annual Growth Rate (CAGR) of approximately 14.0% from 2024 to 2032.
What are the Characteristics of SiC Wafer Boats?
SiC wafer boats, also known as silicon carbide boats, are vital in semiconductor manufacturing. They act as carriers for silicon wafers during various production stages, including etching, cleaning, and diffusion. Their design ensures that wafers remain stable and secure throughout these processes.