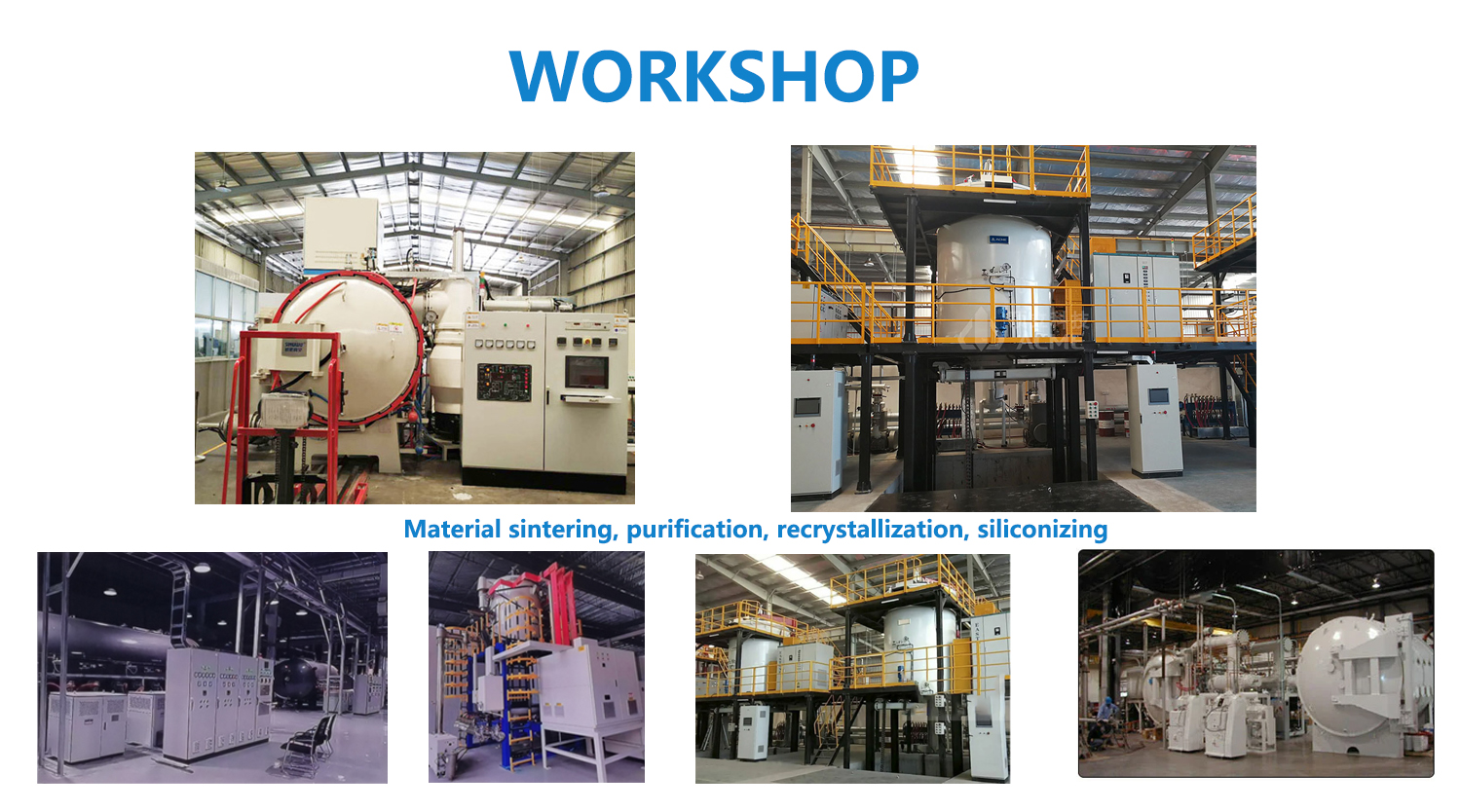
Silicon Carbide Ceramic Coating significantly enhances equipment longevity by providing a robust protective layer. This coating excels in several areas:
- Increased Hardness: It fortifies surfaces, making them resistant to wear and tear.
- Corrosion Resistance: The coating shields equipment from corrosive elements, ensuring durability.
- Thermal Stability: It maintains integrity under high temperatures, crucial for demanding environments.
These properties make Silicon Carbide Ceramic Coating an indispensable choice for industries seeking to extend the lifespan of their equipment.
Key Takeaways
- Silicon Carbide Ceramic Coating significantly enhances equipment longevity by providing a robust protective layer against wear, corrosion, and thermal degradation.
- The coating’s exceptional hardness and corrosion resistance make it ideal for industries like aerospace, automotive, and semiconductor, ensuring reliable performance in harsh environments.
- Applying Silicon Carbide Ceramic Coating can lead to substantial cost savings by reducing maintenance needs and extending the lifespan of equipment.
- Utilizing advanced application methods like Chemical Vapor Deposition (CVD) and Physical Vapor Deposition (PVD) ensures optimal adhesion and durability of the coating.
- Investing in Silicon Carbide Ceramic Coating not only improves equipment efficiency but also contributes to sustainability by minimizing waste and resource use.
- The coating’s ability to withstand high temperatures and corrosive elements makes it a preferred choice for critical components in demanding industrial applications.
- Calculating the return on investment (ROI) for Silicon Carbide Ceramic Coating reveals significant financial advantages through enhanced operational efficiency and reduced downtime.
Understanding Silicon Carbide Ceramic Coating
Composition and Properties
What is Silicon Carbide?
Silicon carbide, often abbreviated as SiC, is a semiconductor material celebrated for its remarkable thermal and mechanical properties. It boasts high thermal conductivity, impressive hardness, and exceptional resistance to oxidation and wear. These attributes make it an ideal candidate for use in extreme environments, such as those involving high temperatures, abrasive conditions, and corrosive chemicals. When applied as a coating, silicon carbide forms a protective layer that enhances the durability and performance of various substrates.
Key Properties of Silicon Carbide Ceramic Coating
The Silicon Carbide Ceramic Coating offers several key properties that contribute to its widespread application across industries:
- High Thermal Conductivity: This property ensures efficient heat dissipation, making it suitable for high-temperature applications.
- Exceptional Hardness: The coating provides a robust surface that resists wear and tear, extending the lifespan of equipment.
- Corrosion Resistance: Silicon carbide’s chemical inertness protects against corrosive elements, maintaining the integrity of the coated surface.
- Oxidation Resistance: The coating withstands oxidative environments, preventing degradation over time.
These properties make the Silicon Carbide Ceramic Coating a preferred choice for industries requiring reliable and durable protective solutions.
Application Process
Methods of Applying the Coating
The application of Silicon Carbide Ceramic Coating involves several advanced techniques to ensure optimal performance:
- Chemical Vapor Deposition (CVD): This method involves the chemical reaction of gaseous precursors to form a solid coating on the substrate. It provides a uniform and dense layer, enhancing the substrate’s properties.
- Physical Vapor Deposition (PVD): In this process, a thin film of silicon carbide is deposited onto the substrate through physical means, such as evaporation or sputtering. PVD coatings are known for their excellent adhesion and durability.
These methods ensure that the coating adheres effectively to various substrates, including ceramics, metals, glass, and plastics.
Industries Utilizing the Coating
The versatility of Silicon Carbide Ceramic Coating makes it applicable across a wide range of industries:
- Aerospace: Utilized for high-temperature components and thermal barrier coatings, ensuring reliability in extreme conditions.
- Automotive: Applied to engine components, brake discs, and clutches to enhance performance and longevity.
- Semiconductor: Used in wafer processing, ion implantation, and deposition processes, where precision and durability are crucial.
- Electronics: Provides protection for devices exposed to harsh environments, ensuring consistent performance.
These industries benefit from the coating’s ability to withstand challenging conditions, thereby improving the efficiency and lifespan of their equipment.
Increased Hardness and Wear Resistance
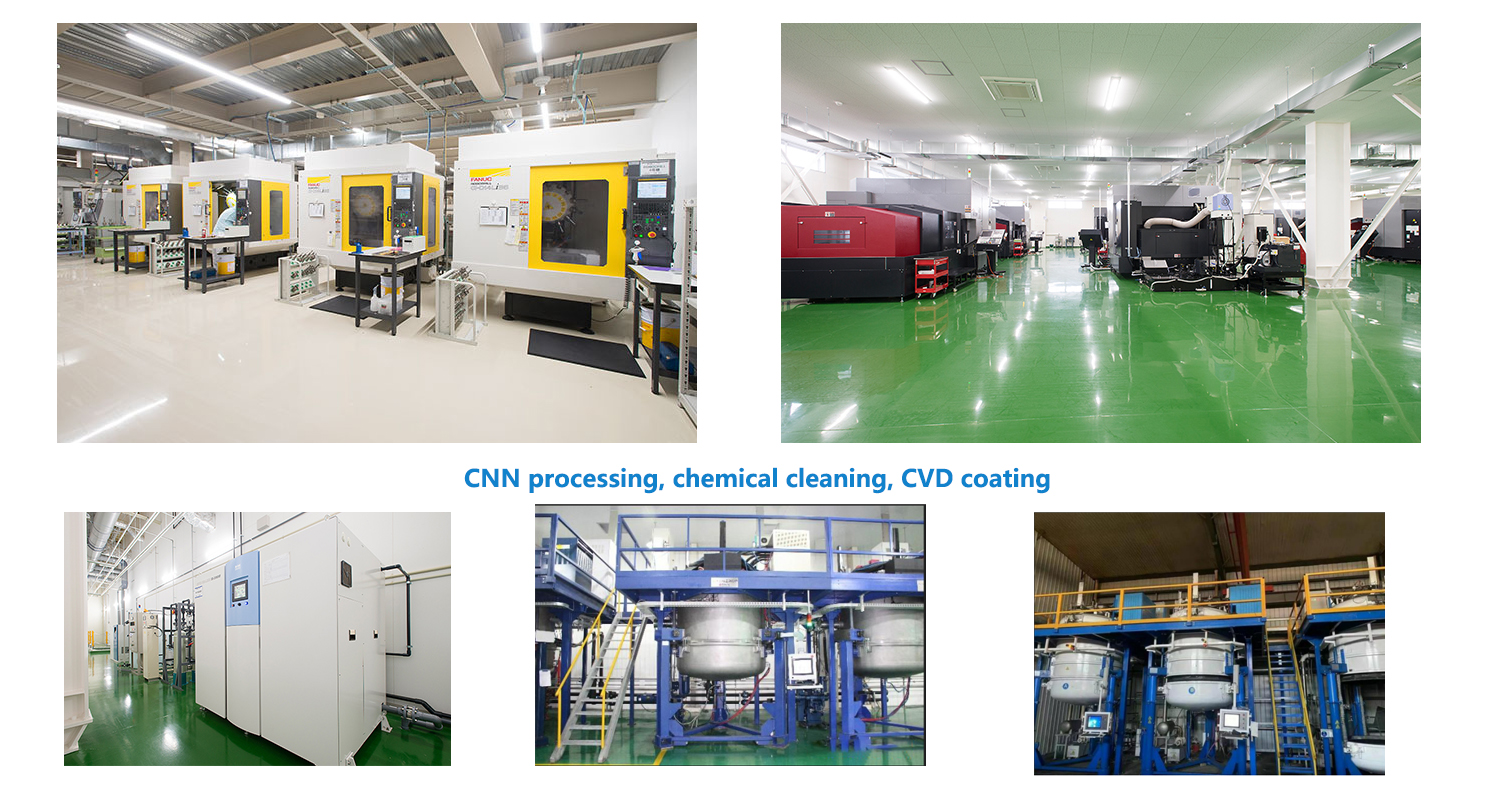
Science Behind Hardness
Mohs Scale and Silicon Carbide
Silicon carbide stands out as one of the hardest materials available, ranking third on the Mohs scale with a hardness of 9.5. This impressive ranking places it just below diamond and boron carbide. The Mohs scale measures a material’s ability to resist scratching, which directly correlates to its wear resistance. Silicon carbide’s high position on this scale highlights its exceptional durability, making it an ideal choice for applications that demand robust materials capable of withstanding significant mechanical stress.
Real-world Examples of Enhanced Hardness
In practical applications, silicon carbide’s hardness translates into superior performance in environments where abrasion and wear are prevalent. For instance, industries utilizing cutting tools and grinding wheels benefit from silicon carbide’s ability to maintain sharpness and structural integrity over extended periods. This material’s hardness ensures that equipment coated with silicon carbide ceramic coating remains operational longer, reducing the need for frequent replacements and maintenance.
Wear Resistance in Action
Case Studies of Wear Resistance
Several industries have documented the effectiveness of silicon carbide in enhancing wear resistance. In the automotive sector, components such as brake discs and clutches coated with silicon carbide demonstrate prolonged lifespans and improved performance. These components endure high friction and pressure, yet the silicon carbide ceramic coating provides a protective barrier that minimizes wear and tear. Similarly, in the aerospace industry, silicon carbide coatings on turbine blades and other high-stress parts ensure reliability and longevity, even under extreme conditions.
Long-term Benefits for Equipment
The long-term benefits of using silicon carbide ceramic coating extend beyond immediate wear resistance. Equipment coated with this material experiences reduced downtime due to maintenance and repairs, leading to increased productivity and cost savings. The coating’s ability to withstand harsh conditions without degrading ensures that machinery operates efficiently over its intended lifespan. By investing in silicon carbide ceramic coating, industries can achieve a significant return on investment through enhanced equipment durability and reduced operational costs.
Corrosion Resistance
Mechanisms of Corrosion Protection
How Silicon Carbide Prevents Corrosion
Silicon carbide ceramic coating offers exceptional corrosion protection due to its inherent chemical inertness. This property allows it to resist degradation even in harsh chemical environments. The coating forms a robust barrier that prevents corrosive agents from reaching the underlying material. Its ability to withstand strong acids and alkalis makes it an ideal choice for industries that operate in aggressive environments. By maintaining its integrity, silicon carbide ensures that equipment remains functional and durable over extended periods.
Comparison with Other Coatings
When compared to other materials, silicon carbide stands out for its superior corrosion resistance. For instance, tungsten carbide, while known for its hardness, is limited by its binder material, which can be vulnerable to strong acids. In contrast, silicon carbide’s chemical inertness provides a more reliable defense against corrosion. This distinction makes silicon carbide ceramic coating a preferred option for applications requiring long-term protection in corrosive settings.
Applications in Corrosive Environments
Examples from the Chemical Industry
In the chemical industry, equipment often encounters corrosive substances that can compromise performance. Silicon carbide ceramic coating plays a crucial role in protecting reactors, pipes, and storage tanks from chemical attacks. Its resistance to acids and alkalis ensures that these components maintain their structural integrity, reducing the risk of leaks and failures. By extending the lifespan of critical equipment, silicon carbide contributes to safer and more efficient chemical processing operations.
Success Stories in Marine Applications
Marine environments present unique challenges due to the presence of saltwater and other corrosive elements. Silicon carbide ceramic coating has proven effective in protecting marine equipment such as propellers, hulls, and offshore structures. Its ability to withstand the harsh conditions of the sea prevents corrosion-related damage, ensuring that vessels and installations remain operational. Success stories from the marine industry highlight the coating’s role in reducing maintenance costs and enhancing the longevity of maritime assets.
Thermal Stability
High-temperature Performance
Thermal Conductivity and Stability
Silicon carbide ceramic coating excels in high-temperature environments due to its outstanding thermal conductivity and stability. This material efficiently dissipates heat, preventing localized overheating and ensuring consistent performance. Its low coefficient of thermal expansion minimizes thermal shock, making it ideal for applications where rapid temperature changes occur. These properties allow silicon carbide to maintain its structural integrity and performance even under extreme conditions.
Benefits in High-heat Environments
In high-heat environments, silicon carbide ceramic coating offers several advantages. It protects equipment from thermal degradation, reducing the risk of failure and extending the lifespan of components. Industries such as metal processing and chemical manufacturing benefit from this coating’s ability to withstand intense heat without compromising performance. By maintaining equipment efficiency, silicon carbide ceramic coating contributes to increased productivity and reduced maintenance costs.
Case Studies
Applications in Aerospace
In the aerospace industry, silicon carbide ceramic coating plays a crucial role in enhancing the performance of high-temperature components. Turbine blades, for example, benefit from the coating’s ability to withstand extreme heat and mechanical stress. This protection ensures that the blades maintain their efficiency and reliability during flight, reducing the risk of failure and extending their operational life. The aerospace sector relies on silicon carbide’s thermal stability to meet the demanding requirements of modern aircraft.
Performance in Automotive Industry
The automotive industry also leverages the benefits of silicon carbide ceramic coating, particularly in high-performance vehicles. Engine components, such as exhaust systems and turbochargers, experience extreme temperatures during operation. Silicon carbide coating provides a protective barrier that prevents thermal degradation, ensuring that these components perform optimally. This protection not only enhances vehicle performance but also extends the lifespan of critical parts, offering significant cost savings over time.
Cost-effectiveness and Economic Benefits
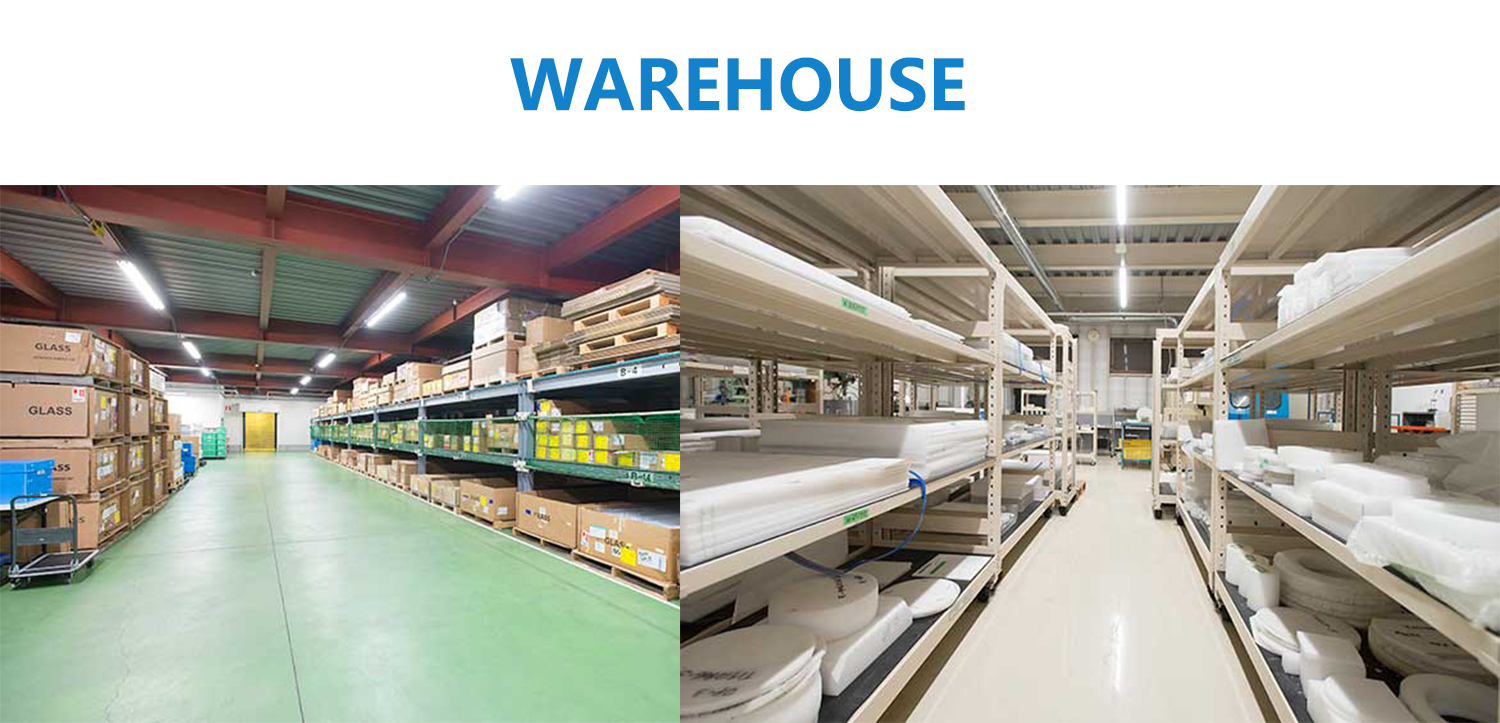
Long-term Cost Savings
Reduced Maintenance Costs
Industries that adopt Silicon Carbide Ceramic Coating experience significant reductions in maintenance costs. This coating provides a durable protective layer that minimizes wear and tear on equipment. As a result, companies spend less on repairs and replacements. The coating’s exceptional hardness and corrosion resistance ensure that machinery operates efficiently over extended periods. By reducing the frequency of maintenance, businesses can allocate resources more effectively, leading to substantial cost savings.
Extended Equipment Lifespan
Silicon Carbide Ceramic Coating extends the lifespan of equipment by protecting it from harsh environmental conditions. The coating’s ability to withstand high temperatures and corrosive elements ensures that machinery remains functional for longer durations. This longevity reduces the need for frequent equipment turnover, allowing companies to maximize their investments. By prolonging the operational life of machinery, businesses can achieve greater productivity and efficiency, ultimately enhancing their bottom line.
Return on Investment
Calculating ROI for Coating Applications
Calculating the return on investment (ROI) for Silicon Carbide Ceramic Coating involves assessing the initial cost of application against the long-term benefits. Companies should consider factors such as reduced maintenance expenses, extended equipment lifespan, and increased productivity. By quantifying these benefits, businesses can determine the financial advantages of adopting this coating. The ROI calculation often reveals that the initial investment in the coating pays off through significant cost savings and enhanced operational efficiency.
Testimonials from Industry Leaders
Industry leaders have shared positive testimonials regarding the impact of Silicon Carbide Ceramic Coating on their operations. Many report substantial improvements in equipment performance and longevity. For instance, a leading aerospace company noted a marked reduction in maintenance costs and downtime after applying the coating to critical components. Similarly, an automotive manufacturer highlighted the coating’s role in enhancing the durability of engine parts, resulting in fewer replacements and repairs. These testimonials underscore the economic benefits and effectiveness of Silicon Carbide Ceramic Coating in various industrial applications.
Environmental Impact
Sustainability of Silicon Carbide Coatings
Eco-friendly Production Processes
Silicon carbide coatings contribute to sustainability through eco-friendly production processes. Manufacturers prioritize reducing environmental footprints by using energy-efficient methods. Chemical Vapor Deposition (CVD) and Physical Vapor Deposition (PVD) techniques minimize waste and emissions. These processes ensure that the production of silicon carbide coatings aligns with sustainable practices. By adopting these methods, manufacturers demonstrate a commitment to environmental responsibility.
Reduction in Waste and Resource Use
Silicon carbide coatings significantly reduce waste and resource use. The durability of these coatings extends the lifespan of equipment, decreasing the need for frequent replacements. This longevity minimizes the consumption of raw materials. Additionally, the coatings’ resistance to wear and corrosion reduces maintenance requirements. As a result, industries experience less downtime and lower resource expenditure. The efficient use of resources underscores the environmental benefits of silicon carbide coatings.
Regulatory Compliance
Meeting Environmental Standards
Silicon carbide coatings meet stringent environmental standards. Manufacturers adhere to regulations that govern emissions and waste management. Compliance with these standards ensures that the production and application of coatings do not harm the environment. By meeting regulatory requirements, manufacturers maintain their commitment to sustainability. This compliance also reassures industries that silicon carbide coatings align with environmental goals.
Industry Certifications
Silicon carbide coatings often receive industry certifications for their environmental performance. These certifications validate the coatings’ adherence to eco-friendly practices. Organizations such as ISO and LEED recognize the coatings for their sustainability. Certifications provide assurance to industries seeking environmentally responsible solutions. By choosing certified silicon carbide coatings, companies demonstrate their dedication to sustainable operations.
Silicon Carbide Ceramic Coating offers numerous advantages that significantly enhance equipment longevity. Its exceptional hardness, corrosion resistance, and thermal stability make it a superior choice for industries operating in harsh environments. By adopting this technology, businesses can achieve improved performance and efficiency, leading to substantial cost savings. The growing demand across sectors such as aerospace, automotive, and semiconductor highlights its versatility and effectiveness. Industries should consider integrating Silicon Carbide Ceramic Coating to ensure durable and long-lasting equipment, ultimately boosting productivity and reducing maintenance costs.
FAQ
What is Silicon Carbide (SiC) Coating?
Silicon Carbide (SiC) coating is a high-performance protective layer applied to various substrates. It enhances the durability and longevity of equipment by providing exceptional hardness, corrosion resistance, and thermal stability. SiC coatings are widely used in industries that require robust materials capable of withstanding extreme conditions.
How does SiC Coating improve equipment longevity?
SiC coating improves equipment longevity by forming a protective barrier against wear, corrosion, and thermal degradation. Its exceptional hardness resists abrasion, while its chemical inertness prevents corrosion. The coating’s thermal stability ensures that equipment maintains its integrity even in high-temperature environments, reducing the need for frequent maintenance and replacements.
What industries benefit from SiC Coating?
Several industries benefit from SiC coating, including aerospace, automotive, semiconductor, and electronics. In aerospace, it protects high-temperature components like turbine blades. Automotive applications include engine parts and brake discs. The semiconductor industry uses SiC coating for wafer processing and deposition processes, while electronics benefit from its protective properties in harsh environments.
What methods are used to apply SiC Coating?
Two primary methods apply SiC coating: Chemical Vapor Deposition (CVD) and Physical Vapor Deposition (PVD). CVD involves a chemical reaction of gaseous precursors to form a solid coating, providing a uniform and dense layer. PVD deposits a thin film through physical means like evaporation or sputtering, known for excellent adhesion and durability.
How does SiC Coating compare to other coatings?
SiC coating stands out for its superior hardness and corrosion resistance compared to other coatings. While tungsten carbide offers hardness, its binder material can be vulnerable to strong acids. SiC’s chemical inertness provides a more reliable defense against corrosion, making it a preferred choice for long-term protection in corrosive settings.
Is SiC Coating environmentally friendly?
Yes, SiC coating is environmentally friendly. Manufacturers use eco-friendly production processes like CVD and PVD, which minimize waste and emissions. The durability of SiC coatings reduces the need for frequent replacements, decreasing raw material consumption and contributing to sustainability.
What are the cost benefits of using SiC Coating?
SiC coating offers significant cost benefits by reducing maintenance expenses and extending equipment lifespan. Its durability minimizes wear and tear, leading to fewer repairs and replacements. The coating’s ability to withstand harsh conditions ensures efficient machinery operation, resulting in increased productivity and substantial cost savings.
Can SiC Coating withstand high temperatures?
SiC coating excels in high-temperature environments due to its outstanding thermal conductivity and stability. It efficiently dissipates heat, preventing localized overheating. Its low coefficient of thermal expansion minimizes thermal shock, making it ideal for applications with rapid temperature changes.
How does SiC Coating contribute to sustainability?
SiC coating contributes to sustainability through eco-friendly production processes and reduced resource use. Its durability extends equipment lifespan, minimizing the need for replacements and conserving raw materials. The coating’s resistance to wear and corrosion reduces maintenance requirements, leading to less downtime and lower resource expenditure.
Are there any certifications for SiC Coating?
Yes, SiC coatings often receive industry certifications for their environmental performance. Organizations like ISO and LEED recognize these coatings for their sustainability. Certifications validate the coatings’ adherence to eco-friendly practices, providing assurance to industries seeking environmentally responsible solutions.