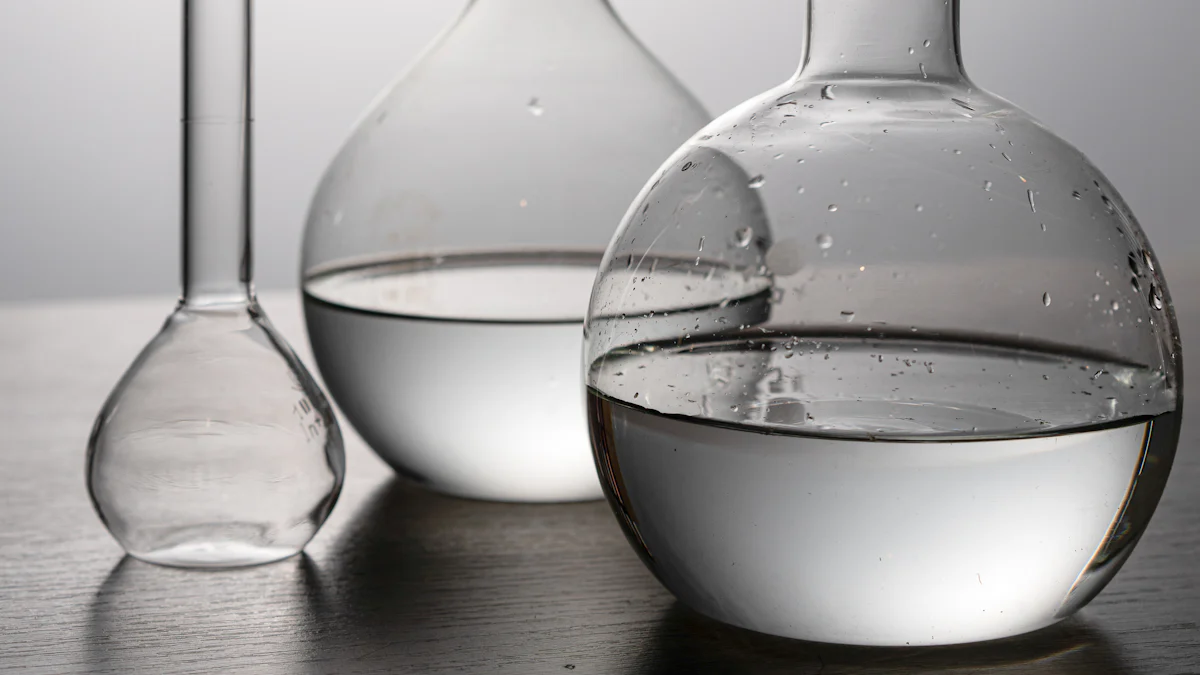
Quartz boats serve as essential tools in chemical reactions and high-temperature processes. Their unique properties, such as thermal stability and chemical inertness, make them indispensable in both laboratory and industrial settings. High purity quartz ensures these boats can withstand extreme conditions without compromising performance. For instance, a quartz boat for furnace applications provides a stable environment for precise material synthesis. Additionally, the quartz wafer boat plays a critical role in semiconductor manufacturing, ensuring contamination-free handling of wafers. Innovations like the MTI quartz boat further enhance efficiency, showcasing the importance of advanced designs in modern industries.
Key Takeaways
- Quartz boats are essential for high-temperature processes, capable of withstanding temperatures up to 1,200°C without losing integrity.
- Their chemical inertness prevents contamination, making quartz boats ideal for sensitive applications like semiconductor manufacturing.
- Durability and longevity of quartz boats reduce the need for frequent replacements, leading to cost savings in laboratory and industrial settings.
- Proper maintenance, including thorough cleaning and careful storage, is crucial for maximizing the lifespan and performance of quartz boats.
- Customization options allow quartz boats to meet specific industry needs, enhancing their effectiveness in diverse applications.
- Quartz boats contribute to sustainability by minimizing waste and supporting renewable energy technologies, such as solar cell manufacturing.
- Investing in high-purity quartz boats improves operational efficiency and product quality, making them a valuable asset in modern scientific and industrial processes.
Unique Properties of Quartz Boats
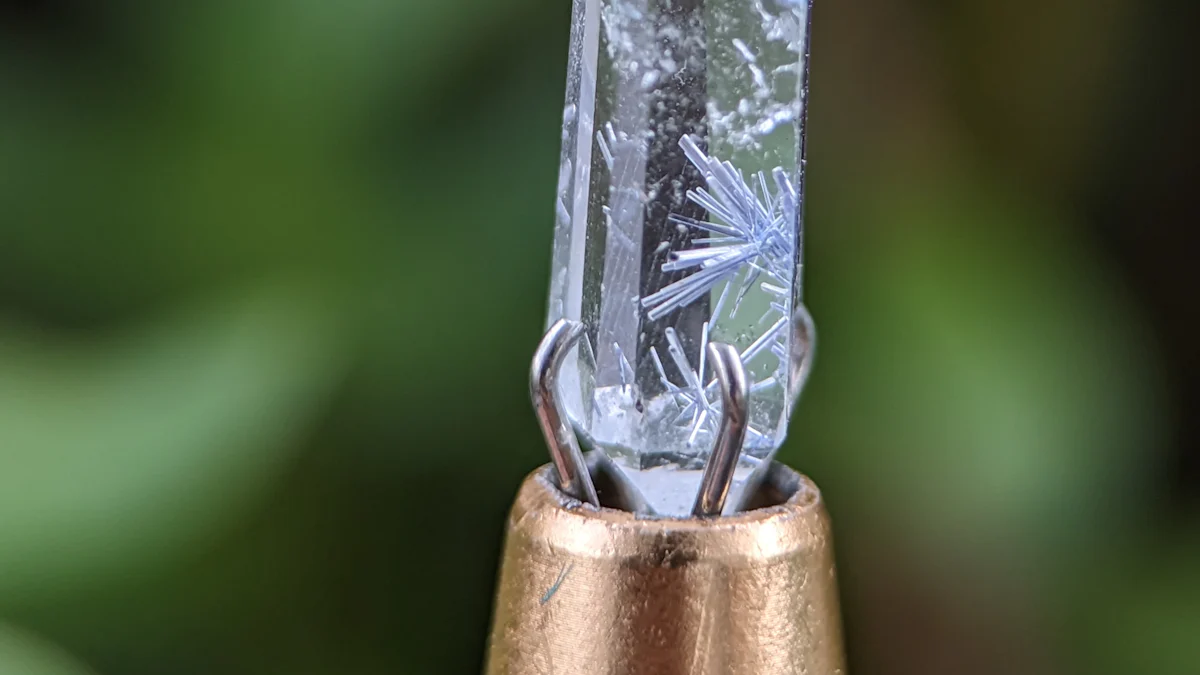
High-Temperature Resistance
Quartz boats exhibit exceptional resistance to high temperatures, making them indispensable in processes that demand extreme heat. These boats can endure temperatures up to 1,200°C without losing their structural integrity. This capability ensures their reliability in high-temperature applications such as material synthesis and chemical reactions. The low thermal expansion coefficient of quartz further enhances its performance by minimizing the risk of cracking or deformation under rapid temperature changes. This property allows quartz boats to maintain stability even during sudden heating or cooling cycles, ensuring consistent results in demanding environments.
Chemical Inertness
The chemical inertness of quartz boats sets them apart from other materials. Quartz resists reactions with most elements and compounds, providing a stable environment for sensitive chemical processes. This resistance ensures that no unwanted contaminants interfere with the reactions, preserving the purity of the materials involved. For instance, in semiconductor manufacturing, quartz boats prevent contamination during wafer oxidation, ensuring precise control over oxide layer formation. Their inert nature also makes them suitable for handling corrosive substances, further expanding their range of applications in both laboratory and industrial settings.
Thermal Stability
Thermal stability is another defining feature of quartz boats. They maintain their physical and chemical properties even under prolonged exposure to extreme temperatures. This stability is crucial for processes requiring consistent thermal conditions, such as chemical vapor deposition (CVD) and heat treatment. Quartz’s high thermal conductivity ensures uniform heat distribution, which is essential for achieving accurate and reproducible results. Additionally, its ability to withstand thermal shock enhances its durability, reducing the need for frequent replacements and ensuring long-term cost-effectiveness.
Durability and Longevity
Quartz boats demonstrate exceptional durability and longevity, making them a reliable choice for demanding applications. Their robust structure ensures they can endure repeated use under extreme conditions without significant wear or degradation. This resilience stems from the inherent properties of quartz, including its high purity and resistance to thermal shock.
The low thermal expansion coefficient of quartz minimizes the risk of cracking or deformation during rapid temperature changes. This feature allows quartz boats to maintain their structural integrity even when exposed to sudden heating or cooling cycles. For instance, in high-temperature processes like material synthesis or chemical vapor deposition, quartz boats consistently perform without compromising their form or function.
Quartz’s chemical inertness further enhances its longevity. Unlike other materials, quartz resists reactions with most elements and compounds, preventing corrosion or surface damage over time. This characteristic ensures that quartz boats remain unaffected by harsh chemicals, preserving their usability across multiple cycles. In industries such as semiconductor manufacturing, this durability translates to reduced downtime and lower replacement costs.
Additionally, quartz boats exhibit excellent resistance to mechanical stress. Their ability to withstand physical impacts during handling or transportation adds to their long-term reliability. Advanced manufacturing techniques, such as precision molding and high-purity material selection, contribute to their robust design, ensuring consistent performance over extended periods.
Why Quartz Boats Are Essential in Laboratory Applications
Quartz boats play a pivotal role in laboratory environments, where precision and reliability are paramount. Their unique properties, including high-temperature resistance, chemical inertness, and thermal stability, make them indispensable for various scientific applications. Laboratories rely on these tools to ensure accurate results and maintain the integrity of sensitive processes.
Sample Heating and Analysis
Quartz boats provide an ideal platform for sample heating and analysis. Their ability to withstand temperatures up to 1,200°C ensures consistent performance during high-temperature experiments. Researchers use quartz boats to heat samples uniformly, which is critical for obtaining reproducible results. The low thermal expansion coefficient of quartz minimizes the risk of cracking or deformation, even during rapid temperature changes.
In analytical chemistry, quartz boats serve as containers for materials undergoing thermal analysis, such as thermogravimetric analysis (TGA) or differential scanning calorimetry (DSC). These techniques require stable and inert environments to measure changes in a material’s properties accurately. Quartz boats meet these requirements by maintaining their structural integrity and preventing contamination during the process.
Supporting Chemical Reactions
Quartz boats act as reliable vessels for supporting chemical reactions in laboratory settings. Their chemical inertness ensures that they do not react with most elements or compounds, preserving the purity of the reaction environment. This property is especially valuable in experiments involving corrosive substances or high-purity materials.
For example, in oxidation reactions, quartz boats provide a stable platform for precise control over reaction conditions. Their thermal stability allows them to endure prolonged exposure to extreme temperatures without compromising the reaction’s outcome. This reliability makes quartz boats essential for researchers conducting experiments that demand high levels of accuracy and consistency.
Material Synthesis and Research
Material synthesis often requires controlled environments and high temperatures, making quartz boats an essential tool for researchers. These boats facilitate the synthesis of advanced materials, such as nanomaterials, ceramics, and semiconductors. Their ability to maintain uniform heat distribution ensures that the synthesized materials exhibit consistent properties.
In research involving chemical vapor deposition (CVD), quartz boats play a crucial role in supporting substrates and ensuring even deposition of thin films. Their durability and resistance to thermal shock enhance their performance in these demanding processes. Additionally, quartz boats contribute to the development of new materials by providing a reliable platform for testing and experimentation.
Scientific Research Findings: Studies highlight the exceptional thermal stability and chemical resistance of quartz boats, emphasizing their importance in laboratory-grade applications. Their ability to withstand thermal shock and maintain structural integrity under extreme conditions makes them indispensable for material synthesis and chemical research.
Industrial Applications of Quartz Boats
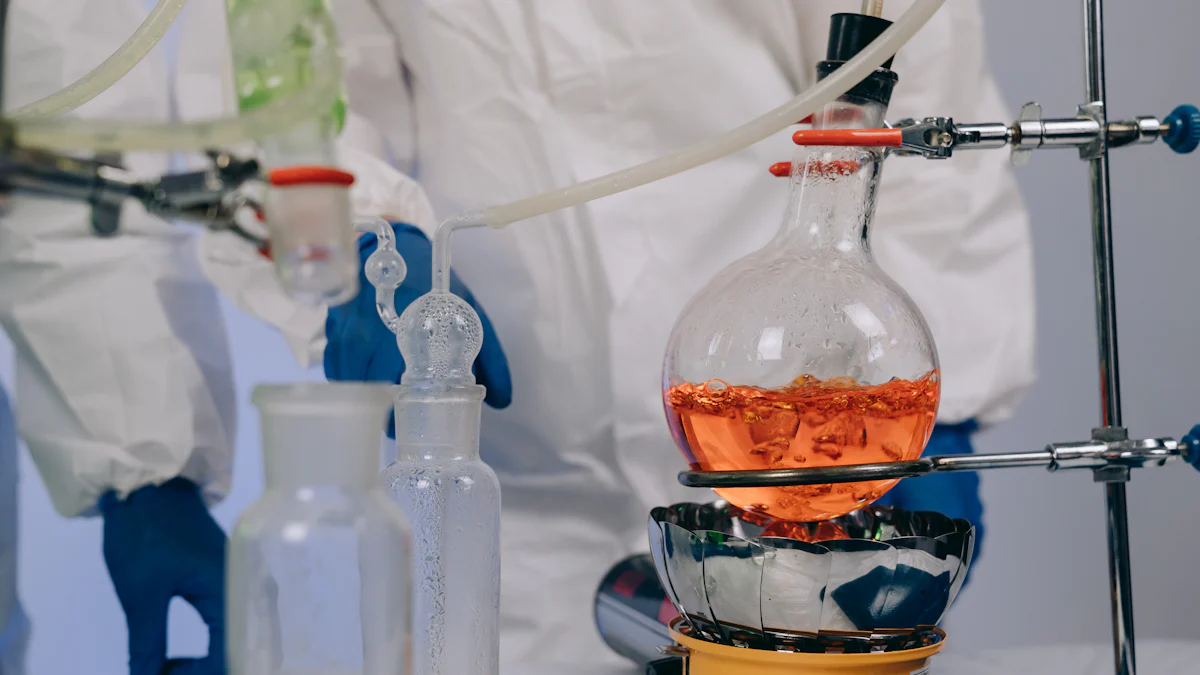
Quartz boats play a pivotal role in various industrial processes, where their unique properties ensure efficiency, precision, and reliability. Industries such as semiconductors, chemical manufacturing, and heat treatment rely heavily on these tools to maintain high standards of performance and quality.
Semiconductor Manufacturing
In the semiconductor industry, quartz boats are indispensable for wafer processing. These boats provide a contamination-free environment, ensuring the purity of silicon wafers during critical stages like oxidation and diffusion. The high-temperature resistance of quartz allows it to endure the extreme heat required for these processes without compromising structural integrity.
Quartz boats also support the precise handling of wafers, minimizing the risk of damage or contamination. Their chemical inertness ensures that no unwanted reactions occur, preserving the quality of the semiconductor materials. This reliability makes quartz boats a cornerstone in the production of advanced electronic devices, where even minor impurities can lead to significant performance issues.
Fact: The use of high-purity quartz materials in semiconductor manufacturing has significantly improved the efficiency and yield of wafer production, contributing to advancements in microelectronics.
Chemical Vapor Deposition (CVD)
Chemical vapor deposition processes demand materials that can withstand high temperatures and corrosive environments. Quartz boats excel in this application due to their thermal stability and chemical resistance. They provide a stable platform for substrates during the deposition of thin films, ensuring uniformity and precision.
The inert nature of quartz prevents contamination, which is crucial for achieving high-quality coatings. Industries use quartz boats in CVD processes to produce materials like semiconductors, solar cells, and advanced ceramics. Their ability to maintain consistent performance under extreme conditions enhances the reliability and efficiency of these manufacturing techniques.
Insight: Recent advancements in quartz boat design have optimized their performance in CVD applications, enabling the production of thinner and more uniform films for cutting-edge technologies.
Heat Treatment Processes
Heat treatment processes require materials that can endure prolonged exposure to high temperatures without degrading. Quartz boats meet this requirement with their exceptional durability and thermal shock resistance. They serve as reliable containers for materials undergoing annealing, sintering, or other heat treatment procedures.
The low thermal expansion coefficient of quartz minimizes the risk of cracking or deformation, even during rapid temperature changes. This stability ensures consistent results, making quartz boats a preferred choice for industries involved in metallurgy, material science, and energy production.
Example: In solar cell manufacturing, quartz boats play a critical role in the heat treatment of silicon wafers, enhancing their efficiency and performance. The use of ultra-pure quartz materials has further reduced impurities, contributing to the sustainability of solar energy solutions.
Advantages of Quartz Boats Over Alternative Materials
Comparison with Ceramic Boats
Quartz boats surpass ceramic boats in several critical aspects, making them the preferred choice for high-temperature and chemical applications. While ceramic boats offer decent thermal resistance, quartz boats excel due to their superior thermal stability and lower thermal expansion coefficient. This ensures that quartz boats maintain their structural integrity even during rapid temperature fluctuations, reducing the risk of cracking or deformation.
The chemical inertness of quartz also provides a significant advantage. Ceramic materials often react with certain chemicals under extreme conditions, potentially contaminating the process. Quartz, on the other hand, resists reactions with most elements and compounds, ensuring a contamination-free environment. This property proves essential in industries like semiconductor manufacturing, where purity directly impacts product quality.
Expert Testimony:
High Purity Quartz Market Analyst, a specialist in market analysis, highlights, “High purity quartz boats are used in the doping and deposition processes during semiconductor manufacturing, where contamination-free environments are essential for creating high-quality products.”
Durability further sets quartz apart. Ceramic boats, though robust, tend to degrade faster under prolonged exposure to high temperatures or corrosive substances. Quartz boats, with their exceptional resistance to thermal shock and chemical wear, offer extended longevity, reducing replacement costs and downtime in industrial operations.
Comparison with Metal Boats
Quartz boats also outperform metal boats in various applications, particularly those involving high temperatures and corrosive environments. Metals, despite their strength, often suffer from oxidation and corrosion when exposed to extreme heat or reactive chemicals. Quartz boats, being chemically inert, eliminate this concern, providing a stable and reliable platform for sensitive processes.
Thermal performance is another area where quartz boats shine. Metals typically expand significantly when heated, which can lead to warping or structural instability. Quartz, with its low thermal expansion coefficient, maintains its shape and functionality even under intense heat. This makes quartz boats ideal for processes requiring precise thermal control, such as chemical vapor deposition (CVD) or wafer oxidation.
Insight: In solar cell manufacturing, quartz boats play a pivotal role in the deposition processes of silicon wafers. A Solar Cell Manufacturing Expert emphasizes, “Quartz boats, known for their high thermal stability and low contamination levels, play a crucial role in the deposition processes of silicon wafers, which are the backbone of solar cells.”
Additionally, quartz boats offer better resistance to thermal shock compared to metal alternatives. Rapid heating or cooling cycles can cause metals to crack or deform, compromising their usability. Quartz boats withstand these conditions with ease, ensuring consistent performance across multiple cycles.
Maintenance and Care for Quartz Boats
Proper maintenance and care ensure the longevity and optimal performance of quartz boats. Following specific cleaning and storage practices helps preserve their structural integrity and chemical properties, even under demanding conditions.
Cleaning Procedures
Cleaning quartz boats requires precision to maintain their chemical inertness and thermal stability. Residue from previous processes can compromise their performance, so thorough cleaning is essential.
-
Initial Rinse: Begin by rinsing the quartz boat with deionized water to remove loose particles and surface contaminants. Deionized water prevents mineral deposits that could affect the boat’s purity.
-
Chemical Cleaning: For stubborn residues, use a diluted acid solution, such as hydrochloric acid, to dissolve impurities. Avoid hydrofluoric acid, as it reacts with quartz and damages its surface. Always handle acids with proper safety equipment to prevent accidents.
-
Ultrasonic Cleaning: Employ ultrasonic cleaning for deep cleaning. This method uses high-frequency sound waves to dislodge particles from hard-to-reach areas. It ensures a thorough cleanse without causing physical damage to the quartz.
-
Final Rinse and Drying: After cleaning, rinse the quartz boat again with deionized water to remove any remaining chemicals. Dry it using a lint-free cloth or air drying in a clean environment to avoid introducing new contaminants.
Tip: Regular cleaning after each use prevents the buildup of residues, extending the lifespan of the quartz boat.
Storage Guidelines
Proper storage protects quartz boats from physical damage and environmental contamination. Adhering to these guidelines ensures their readiness for future use.
-
Dedicated Storage Area: Store quartz boats in a clean, dust-free environment. Use designated shelves or cabinets to prevent accidental contact with other materials that could cause scratches or contamination.
-
Protective Covers: Place quartz boats in protective covers or containers when not in use. This shields them from airborne particles and reduces the risk of physical damage during handling or transportation.
-
Temperature Control: Maintain a stable storage temperature to avoid thermal stress. Sudden temperature fluctuations can weaken the quartz structure over time.
-
Avoid Chemical Exposure: Keep quartz boats away from corrosive chemicals during storage. Even though quartz is chemically inert, prolonged exposure to certain substances may compromise its surface quality.
Best Practice: Label storage areas clearly to ensure that quartz boats are handled only by trained personnel, minimizing the risk of mishandling or contamination.
By following these cleaning and storage practices, users can maximize the efficiency and durability of quartz boats. Proper care not only reduces replacement costs but also ensures consistent performance in critical applications.
Innovations in Quartz Boat Design
Advanced Manufacturing Techniques
The evolution of quartz boat design owes much to advancements in manufacturing techniques. Modern production processes prioritize precision and efficiency, ensuring that quartz boats meet the rigorous demands of contemporary applications. Manufacturers now employ cutting-edge technologies, such as CNC machining and laser cutting, to achieve unparalleled accuracy in shaping and finishing quartz components. These methods allow for the creation of intricate designs that enhance the functionality and performance of quartz boats.
High-purity quartz materials undergo meticulous processing to eliminate impurities. This ensures that the final product exhibits superior thermal stability and chemical resistance. Advanced molding techniques, such as vacuum forming, further improve the structural integrity of quartz boats. These methods minimize defects, such as air pockets or inconsistencies, which could compromise performance under extreme conditions.
Insight: Industry experts highlight that precision manufacturing has significantly reduced the failure rate of quartz boats in high-temperature applications, enhancing their reliability and lifespan.
Innovative surface treatments also play a crucial role in modern quartz boat production. Techniques like plasma polishing create ultra-smooth surfaces, reducing the risk of contamination during sensitive processes. This innovation proves particularly valuable in industries like semiconductor manufacturing, where even microscopic impurities can impact product quality.
Customization for Industry Needs
Customization has become a cornerstone of quartz boat design, addressing the unique requirements of various industries. Manufacturers now offer tailored solutions to meet specific operational challenges, ensuring optimal performance in diverse applications. Customization options include variations in size, shape, and material composition, allowing quartz boats to adapt to specialized processes.
For instance, the semiconductor industry often requires quartz boats with precise dimensions to accommodate specific wafer sizes. Manufacturers respond by producing custom designs that ensure a perfect fit, minimizing the risk of damage or contamination during wafer handling. Similarly, industries involved in chemical vapor deposition (CVD) benefit from quartz boats engineered to support uniform film deposition, enhancing the quality of the final product.
Example: A leading photovoltaic company collaborated with quartz manufacturers to develop custom boats for solar cell production. These designs optimized heat distribution, improving the efficiency of the manufacturing process.
Customization extends beyond physical attributes. Manufacturers also offer quartz boats with enhanced properties, such as increased resistance to thermal shock or improved durability. These innovations cater to industries operating under extreme conditions, ensuring that quartz boats deliver consistent performance and reliability.
Fact: The growing demand for customized quartz solutions reflects the increasing complexity of modern industrial processes. Tailored designs enable businesses to achieve greater precision, efficiency, and scalability in their operations.
Environmental and Economic Impact of Quartz Boats
Sustainability in Manufacturing
Quartz boats contribute significantly to sustainable manufacturing practices. Their production relies on high-purity fused quartz, a material derived from abundant natural resources like silica sand. Manufacturers prioritize eco-friendly processes to minimize waste and energy consumption during production. Advanced techniques, such as precision molding and vacuum forming, enhance material efficiency by reducing defects and scrap rates.
The durability of quartz boats further supports sustainability. Their resistance to thermal shock and chemical wear ensures extended lifespans, reducing the frequency of replacements. This longevity minimizes the environmental impact associated with manufacturing and disposal. Industries benefit from fewer discarded materials, aligning with global efforts to reduce industrial waste.
Fact: Studies in material science highlight that fused quartz, used in quartz boats, exhibits exceptional recyclability. Manufacturers can repurpose quartz waste into new products, promoting a circular economy.
Quartz boats also play a role in enabling green technologies. In solar cell manufacturing, they support processes that enhance the efficiency of renewable energy solutions. Their use in semiconductor production contributes to advancements in energy-efficient electronics, further underscoring their environmental value.
Cost-Effectiveness in Long-Term Use
Quartz boats offer unparalleled cost-effectiveness over their operational lifespan. Their exceptional durability reduces the need for frequent replacements, translating to lower procurement costs for laboratories and industries. Unlike alternative materials, quartz maintains its structural integrity under extreme conditions, ensuring consistent performance across multiple cycles.
The chemical inertness of quartz eliminates the risk of contamination, which can lead to costly process failures. Industries relying on high-purity environments, such as semiconductor manufacturing, benefit from reduced downtime and improved product yields. This reliability enhances overall operational efficiency, saving both time and resources.
Insight: A market analysis of high-purity quartz highlights its role in reducing operational costs. The report emphasizes that quartz boats, with their extended lifespans, significantly lower maintenance expenses in high-temperature applications.
Energy efficiency also adds to the economic advantages of quartz boats. Their high thermal conductivity ensures uniform heat distribution, reducing energy consumption during processes like chemical vapor deposition (CVD) and heat treatment. This efficiency not only lowers operational costs but also aligns with sustainability goals.
The Role of Quartz Boats in Advancing Technology
Contributions to Semiconductor Advancements
Quartz boats have become indispensable in the semiconductor industry, where precision and purity are critical. Their ability to withstand extreme temperatures and maintain chemical inertness ensures contamination-free environments during wafer processing. This reliability supports essential processes such as oxidation, diffusion, and deposition, which are fundamental to semiconductor manufacturing.
The high-purity quartz used in these boats plays a pivotal role in enhancing the quality of silicon wafers. Manufacturers rely on quartz boats to provide stable platforms for wafer handling, minimizing the risk of damage or impurities. This precision has directly contributed to advancements in microelectronics, enabling the production of smaller, faster, and more efficient devices.
Fact: According to industry experts, the use of high-purity quartz boats has significantly improved wafer yields, reducing defects and increasing the efficiency of semiconductor production.
Innovations in quartz boat design have further propelled technological progress. Custom quartz boats tailored to specific wafer sizes and processes have optimized manufacturing workflows. These advancements have allowed semiconductor companies to meet the growing demand for high-performance electronic components, driving innovation in consumer electronics, telecommunications, and computing.
Supporting Emerging Technologies
Quartz boats are also at the forefront of emerging technologies, where their unique properties enable groundbreaking developments. In fields like nanotechnology, material science, and renewable energy, quartz boats provide the stability and precision required for experimental and production processes.
In nanotechnology, researchers use quartz boats to synthesize and analyze nanomaterials. Their thermal stability and chemical resistance ensure consistent results, which are crucial for developing applications such as drug delivery systems, advanced coatings, and nanosensors. Similarly, in material science, quartz boats facilitate the creation of innovative materials with enhanced properties, such as lightweight composites and high-strength ceramics.
Scientific Research Findings: Studies highlight the increasing demand for high-purity quartz boats in research laboratories. These tools are essential for advancing scientific knowledge in chemistry, material science, and nanotechnology.
Quartz boats also play a vital role in renewable energy technologies. In solar cell manufacturing, they support processes like chemical vapor deposition (CVD) and heat treatment, which enhance the efficiency of photovoltaic cells. Manufacturers are investing in sustainable innovations to reduce the carbon footprint of quartz boat production, aligning with global environmental goals.
Insight: Recent advancements in quartz boat manufacturing have focused on eco-friendly materials and energy-efficient processes. These efforts not only support sustainability but also improve the performance and longevity of quartz boats in high-tech applications.
By enabling precision, reliability, and innovation, quartz boats continue to drive progress across a wide range of industries. Their contributions to both established and emerging technologies underscore their importance in shaping the future of science and technology.
Quartz boats have established themselves as indispensable tools in both laboratory and industrial environments. Their unmatched thermal stability, chemical inertness, and durability make them essential for processes such as semiconductor manufacturing, chemical synthesis, and material analysis. As industries continue to innovate, the demand for high-purity quartz boats grows, driven by advancements in microelectronics, solar energy, and optoelectronics. By leveraging these unique properties, businesses achieve greater precision, efficiency, and sustainability, ensuring progress in science and technology while meeting the evolving needs of modern applications.
FAQ
What are quartz boats made of?
Quartz boats are crafted from high-purity fused quartz, which contains over 99.99% silica. This material ensures exceptional thermal stability, chemical resistance, and durability, making quartz boats ideal for high-temperature and chemically demanding applications.
Why are quartz boats preferred over other materials?
Quartz boats outperform alternatives like ceramic or metal due to their superior thermal shock resistance, low thermal expansion, and chemical inertness. These properties ensure consistent performance in extreme conditions, such as rapid heating or exposure to corrosive substances, without compromising structural integrity.
How do quartz boats contribute to semiconductor manufacturing?
Quartz boats play a critical role in semiconductor manufacturing by providing contamination-free environments for wafer processing. Their chemical inertness and high-temperature tolerance ensure precise oxidation, diffusion, and deposition processes, which are essential for producing high-quality electronic components.
Fact: High-purity quartz boats have significantly improved wafer yields, reducing defects and enhancing the efficiency of semiconductor production.
Can quartz boats withstand rapid temperature changes?
Yes, quartz boats exhibit excellent thermal shock resistance. Their low thermal expansion coefficient allows them to endure sudden heating or cooling cycles without cracking or deforming. This makes them reliable for processes requiring rapid temperature fluctuations.
What industries benefit from using quartz boats?
Quartz boats are widely used in industries such as semiconductors, photovoltaics, metallurgy, and chemical manufacturing. They support processes like wafer oxidation, chemical vapor deposition (CVD), material synthesis, and heat treatment, contributing to advancements in science and technology.
How do quartz boats enhance sustainability in manufacturing?
Quartz boats promote sustainability through their durability and long lifespan. Their resistance to thermal and chemical wear reduces the need for frequent replacements, minimizing waste. Additionally, their role in solar cell manufacturing supports renewable energy solutions, aligning with global environmental goals.
Insight: Studies highlight the recyclability of fused quartz, enabling manufacturers to repurpose quartz waste into new products, fostering a circular economy.
What maintenance practices ensure the longevity of quartz boats?
Proper cleaning and storage are essential for maintaining quartz boats. Cleaning involves rinsing with deionized water, using diluted acid solutions for stubborn residues, and employing ultrasonic cleaning for thorough results. Storing quartz boats in clean, dust-free environments with protective covers prevents contamination and physical damage.
Are quartz boats customizable for specific applications?
Yes, manufacturers offer customization options to meet industry-specific needs. Custom designs include variations in size, shape, and material composition. For example, semiconductor manufacturers often require quartz boats tailored to specific wafer dimensions to ensure precise handling and optimal performance.
How do quartz boats support emerging technologies?
Quartz boats enable advancements in fields like nanotechnology, material science, and renewable energy. Their thermal stability and chemical resistance provide reliable platforms for synthesizing nanomaterials, developing innovative materials, and enhancing the efficiency of photovoltaic cells.
Example: In nanotechnology, researchers rely on quartz boats for consistent results in creating nanosensors and advanced coatings.
What makes quartz boats cost-effective in the long term?
Quartz boats offer exceptional durability, reducing replacement frequency and associated costs. Their chemical inertness prevents contamination-related process failures, improving operational efficiency. Additionally, their high thermal conductivity ensures energy-efficient performance in processes like CVD and heat treatment.
Insight: Market analysis reveals that quartz boats significantly lower maintenance expenses in high-temperature applications, making them a cost-effective choice for laboratories and industries.