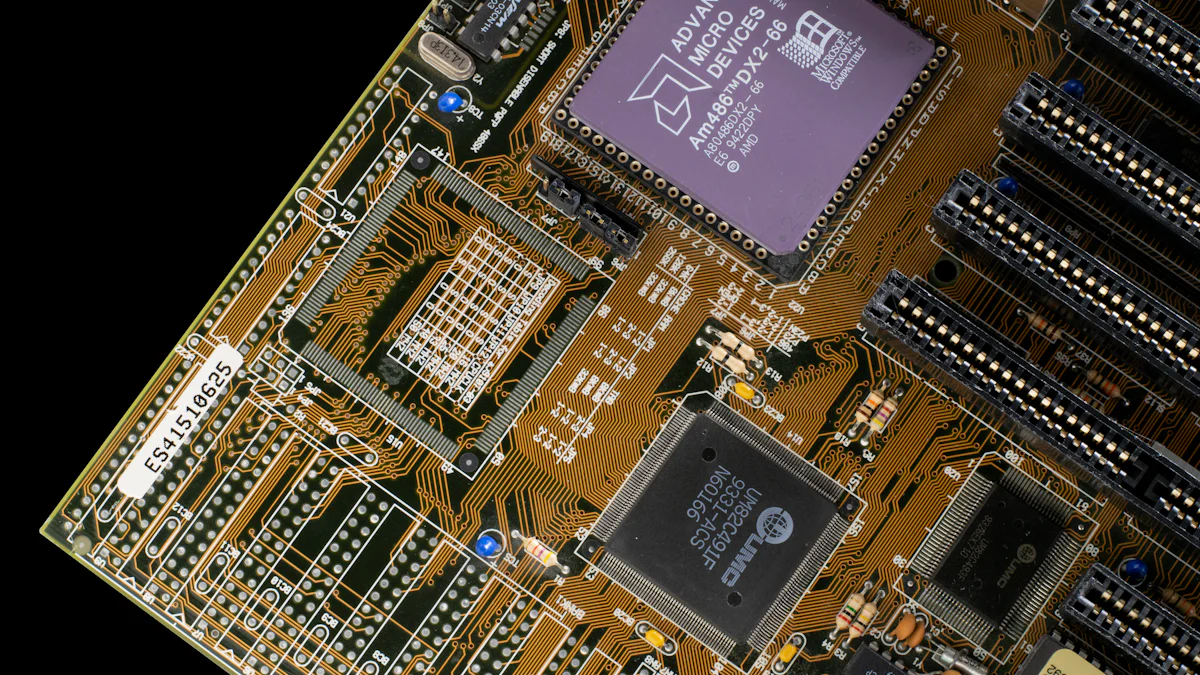
Applied Materials epitaxy has revolutionized the way mobile processors perform. By introducing advanced epitaxy technologies, the company has set a new benchmark for speed, efficiency, and power optimization in semiconductor manufacturing. These innovations enhance the electrical properties of wafers, enabling processors to handle complex tasks with ease. The introduction of applied materials epitaxy trays ensures precision and uniformity during deposition, while the applied materials epi prime process boosts transistor performance. As global demand for high-performance mobile devices grows, Applied Materials continues to lead the charge in shaping the future of mobile technology.
Key Takeaways
- Epitaxy is crucial for enhancing the performance of mobile processors by improving the electrical properties of semiconductor materials.
- Applied Materials’ advanced epitaxy technologies ensure precision and uniformity, leading to faster transistors that consume less power.
- The NMOS epitaxy deposition process developed by Applied Materials allows for the creation of ultra-thin, high-quality crystalline layers, essential for next-generation mobile devices.
- Material innovations, such as the use of gallium nitride (GaN) and silicon carbide (SiC), enhance the efficiency and thermal management of mobile processors.
- Applied Materials is committed to sustainability, focusing on energy-efficient manufacturing practices that minimize waste and environmental impact.
- The integration of AI and IoT technologies into epitaxy processes is revolutionizing semiconductor manufacturing, improving efficiency and product quality.
- Epitaxy’s applications extend beyond mobile processors, impacting industries like renewable energy, photonics, and advanced memory devices.
The Role of Applied Materials Epitaxy in Mobile Processors
How Epitaxy Enhances Semiconductor Performance
Epitaxy plays a vital role in boosting the performance of semiconductors. It involves growing a thin, crystalline layer on a substrate, which improves the electrical properties of the material. This process creates a foundation for building high-performance mobile processors. By enhancing the wafer’s surface, epitaxy ensures better conductivity and reduces defects, which directly impacts the speed and efficiency of processors.
Applied Materials epitaxy takes this process to the next level. Their advanced epitaxy technologies enable precise control over the deposition process, ensuring uniformity and consistency. This precision allows manufacturers to create transistors that operate faster and consume less power. As a result, mobile devices can handle demanding applications like gaming, video editing, and AI-driven tasks without compromising performance.
The integration of Internet of Things (IoT) and artificial intelligence (AI) technologies into epitaxial growth equipment has further revolutionized the manufacturing process. These advancements improve efficiency and product quality, making it easier to meet the growing demand for high-performance mobile processors. With these innovations, epitaxy has become a cornerstone of modern semiconductor manufacturing.
Applied Materials’ Leadership in Epitaxy Innovation
Applied Materials has established itself as a leader in epitaxy innovation. The company continuously pushes the boundaries of what is possible in semiconductor manufacturing. Their new NMOS epitaxy deposition process is a prime example of this commitment. This process is essential for creating faster transistors, which are the building blocks of next-generation mobile processors.
Material innovations are at the heart of Applied Materials’ success. By developing new materials and refining existing ones, the company ensures that its epitaxy technologies deliver unmatched performance. Their focus on precision and uniformity sets them apart from competitors, enabling them to produce wafers with superior electrical characteristics.
Applied Materials also invests heavily in research and development to stay ahead of industry trends. Their dedication to innovation has positioned them as a key player in the semiconductor market. By addressing challenges like scalability and cost, they make epitaxy technologies more accessible to manufacturers worldwide. This leadership not only strengthens their market position but also drives the adoption of advanced epitaxy processes across the industry.
Understanding Epitaxy in Semiconductor Manufacturing
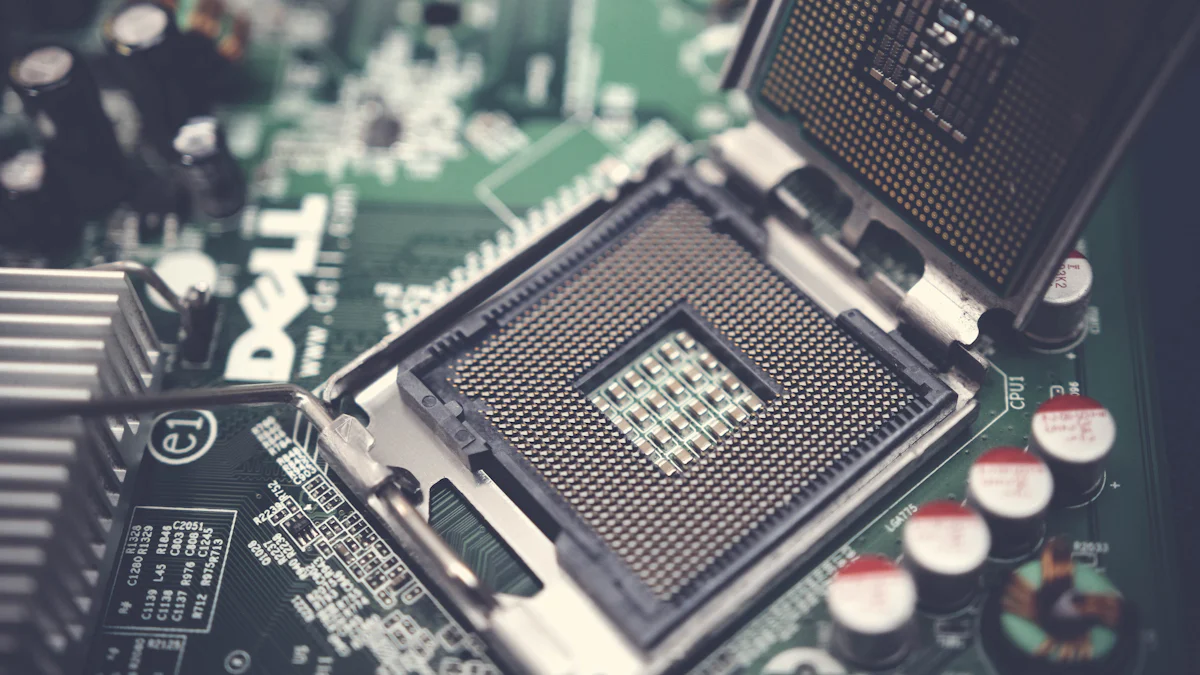
What is Epitaxy?
Epitaxy is a specialized process used in semiconductor manufacturing to grow or deposit a monocrystalline film on a substrate. This technique ensures that the crystalline structure of the film aligns perfectly with the underlying material. By doing so, epitaxy creates a flawless foundation for building advanced semiconductor devices.
In simpler terms, think of epitaxy as laying a smooth, uniform layer of bricks on an already solid base. This precision enhances the electrical properties of the material, making it ideal for creating high-performance microprocessors and memory devices. Applied materials epitaxy leverages this process to deliver exceptional results, ensuring that every layer contributes to the overall efficiency and speed of the final product.
Types of Epitaxy: Homoepitaxy vs. Heteroepitaxy
Epitaxy comes in two main types: homoepitaxy and heteroepitaxy. Each serves a unique purpose in semiconductor manufacturing.
-
Homoepitaxy: This involves growing a crystalline film on a substrate of the same material. For example, depositing silicon on a silicon wafer. This method is often used to enhance the quality of the existing material, improving its electrical conductivity and reducing defects.
-
Heteroepitaxy: In this process, the film is grown on a substrate with a different composition. For instance, depositing gallium nitride (GaN) on a silicon wafer. Heteroepitaxy is crucial for creating advanced electronic and optoelectronic devices, such as LEDs and power electronics. It allows manufacturers to combine the best properties of different materials, enabling innovative applications.
Both types of epitaxy play a significant role in modern semiconductor technology. They provide the flexibility needed to design and manufacture devices that meet the ever-growing demands of industries like telecommunications, computing, and mobile technology.
Importance of Epitaxy in Mobile Processors
Epitaxy is a cornerstone of mobile processor manufacturing. It ensures that the foundational layers of semiconductors are not only uniform but also optimized for performance. This process directly impacts the speed, efficiency, and power consumption of mobile processors.
By using epitaxy, manufacturers can create wafers with superior electrical characteristics. These wafers serve as the building blocks for transistors, which are the heart of any processor. Applied materials epitaxy, for instance, focuses on precision and uniformity during deposition. This attention to detail results in transistors that operate faster and consume less energy, making them perfect for mobile devices.
Moreover, epitaxy supports innovations like strain engineering, which enhances the performance of transistors by altering the mechanical properties of the material. This technique is especially important for mobile processors, where space is limited, and efficiency is critical. As mobile devices continue to evolve, epitaxy remains an essential tool for meeting the challenges of modern semiconductor design.
Applied Materials’ New Epitaxy Technologies
NMOS Epitaxy Deposition Process
The NMOS epitaxy deposition process developed by Applied Materials has redefined how transistors are built for mobile processors. This process focuses on creating ultra-thin, high-quality crystalline layers that enhance the electrical properties of semiconductors. By improving the uniformity and precision of these layers, manufacturers can produce transistors that operate at higher speeds while consuming less power.
Applied Materials integrates advanced techniques like atomic layer epitaxy (ALE) and molecular beam epitaxy (MBE) into their NMOS deposition process. These methods allow for atomic-level control during material growth, ensuring that each layer aligns perfectly with the substrate. This precision is critical for next-generation mobile processors, where even the smallest imperfections can impact performance.
The company also leads in selective deposition processes, enabling the precise placement of materials only where needed. This approach minimizes waste and reduces production costs, making it an efficient solution for manufacturers. With these innovations, Applied Materials ensures that their NMOS epitaxy deposition process meets the growing demands of the semiconductor industry.
Material Innovations in Epitaxy
Material innovation lies at the heart of Applied Materials’ success in epitaxy technologies. The company continuously develops new materials and refines existing ones to improve semiconductor performance. For example, their specialized tools for silicon carbide (SiC) and gallium nitride (GaN) devices enable the creation of high-performance components for mobile processors and other advanced applications.
Applied Materials’ epitaxial growth equipment supports the use of diverse materials, including those tailored for specific applications like power electronics and optoelectronics. By leveraging these materials, manufacturers can achieve better conductivity, reduced defects, and enhanced thermal management. These improvements directly translate to faster, more efficient mobile processors.
The company also invests in research to explore novel materials that push the boundaries of semiconductor technology. Their focus on material innovation ensures that Applied Materials remains a leader in the industry, providing solutions that meet the evolving needs of mobile technology.
Precision and Uniformity in Epitaxy Processes
Precision and uniformity are essential for achieving high-quality epitaxy, and Applied Materials excels in both areas. Their epitaxial growth systems are designed to deliver consistent results across every wafer, ensuring that each layer meets strict quality standards. This level of precision is crucial for creating transistors that perform reliably under demanding conditions.
Applied Materials employs advanced techniques like molecular beam epitaxy (MBE) and selective epitaxy to achieve unparalleled accuracy. These methods allow for the controlled deposition of materials, enabling the creation of intricate patterns and structures. By maintaining uniformity across all layers, the company ensures that their epitaxy processes deliver optimal performance for mobile processors.
The use of separate chambers for each layer in their epitaxial growth systems further enhances precision. This approach minimizes contamination and allows for better control over the growth process. As a result, Applied Materials’ epitaxy technologies set a new standard for quality and reliability in semiconductor manufacturing.
Performance Benefits of Applied Materials Epitaxy
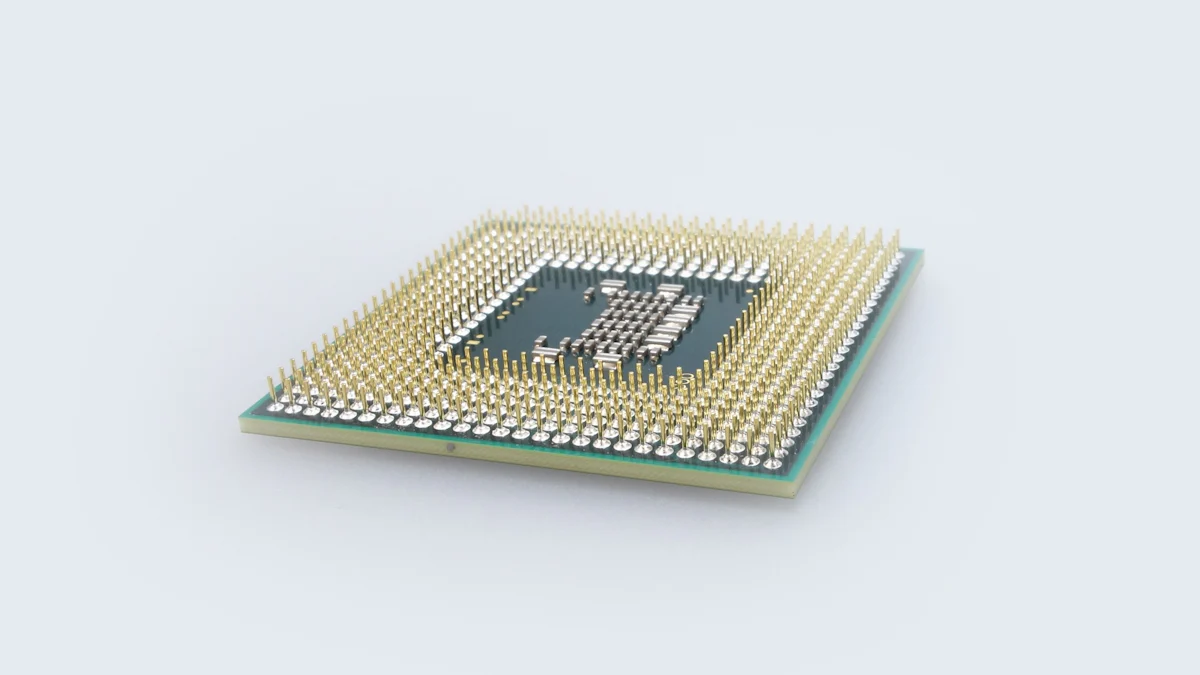
Enhancing Processor Speed and Efficiency
Applied Materials epitaxy significantly boosts the speed and efficiency of mobile processors. By using advanced epitaxial growth equipment, the company ensures that each crystalline layer is perfectly aligned with the substrate. This precision reduces defects and enhances electrical conductivity, which directly impacts processor performance. Faster transistors, created through their innovative NMOS epitaxy deposition process, allow mobile devices to handle complex tasks like gaming and AI-driven applications with ease.
Unlike traditional methods that rely on a single MOCVD chamber for each layer, Applied Materials employs separate chambers for every layer. This approach optimizes the deposition process and ensures a self-cleaning mechanism, resulting in higher-quality wafers. The improved uniformity and precision of these layers translate to processors that operate more efficiently, delivering a seamless user experience.
Reducing Power Consumption in Mobile Devices
Applied Materials epitaxy plays a crucial role in minimizing power consumption in mobile devices. The company’s focus on material innovation enables the creation of transistors that require less energy to function. By refining materials like silicon carbide (SiC) and gallium nitride (GaN), Applied Materials ensures that their epitaxy technologies support energy-efficient designs.
The use of selective deposition processes further enhances power efficiency. This technique places materials only where needed, reducing waste and optimizing performance. Mobile devices equipped with processors built using Applied Materials epitaxy can run longer on a single charge, making them ideal for users who rely on their devices throughout the day.
Improving Thermal Management for High Workloads
Thermal management becomes increasingly important as mobile processors handle more demanding workloads. Applied Materials epitaxy addresses this challenge by improving the thermal properties of semiconductor materials. The company’s advanced epitaxial growth systems create layers with superior heat dissipation capabilities, ensuring that processors remain cool even under heavy use.
By leveraging materials like gallium nitride, which offers excellent thermal conductivity, Applied Materials enhances the ability of processors to manage heat. This improvement not only prevents overheating but also extends the lifespan of mobile devices. Users can enjoy smoother performance during activities like video editing or multitasking without worrying about their devices overheating.
“Applied Materials epitaxy sets a new standard for performance, efficiency, and reliability in mobile processors,” highlighting its transformative impact on the semiconductor industry.
Industry Implications of Applied Materials’ Epitaxy Advancements
Strengthening Applied Materials’ Market Position
Applied Materials has solidified its position as a leader in the semiconductor industry. The company’s advanced epitaxy technologies have become essential for manufacturers aiming to produce high-performance devices. By offering a comprehensive range of epitaxial growth equipment, Applied Materials enables its customers to achieve superior device performance and efficiency. This capability has not only attracted new clients but also strengthened relationships with existing ones.
The growing demand for gallium nitride (GaN) epitaxy in power electronics and LEDs has further boosted Applied Materials’ market presence. Their focus on material innovation and precision aligns perfectly with the needs of these industries. Additionally, the adoption of 3D ICs and advanced packaging technologies has created new opportunities for the company to expand its influence. These trends highlight how Applied Materials epitaxy continues to shape the future of semiconductor manufacturing.
“Applied Materials epitaxy is not just a technology; it’s a game-changer for the semiconductor market,” as industry experts often note. This reputation has helped the company maintain a competitive edge and drive growth in a rapidly evolving market.
Enabling Next-Generation Mobile Technologies
The advancements in Applied Materials epitaxy are paving the way for next-generation mobile technologies. By enhancing the electrical properties of semiconductors, these innovations make it possible to create faster and more efficient processors. This progress is crucial for supporting the increasing complexity of mobile devices, which now require higher processing power for applications like augmented reality (AR) and virtual reality (VR).
Applied Materials’ focus on precision and uniformity ensures that their epitaxy processes meet the stringent requirements of modern mobile processors. The integration of atomic layer epitaxy (ALE) and molecular beam epitaxy (MBE) techniques allows for the creation of ultra-thin, high-quality crystalline layers. These layers serve as the foundation for transistors that can handle demanding tasks without compromising performance.
The company’s commitment to innovation doesn’t stop there. By incorporating Internet of Things (IoT) and artificial intelligence (AI) technologies into their epitaxial growth equipment, Applied Materials has revolutionized the manufacturing process. These advancements improve efficiency and product quality, making it easier to develop mobile technologies that push the boundaries of what’s possible.
Supporting AI and 5G Applications
Applied Materials epitaxy plays a vital role in enabling AI and 5G applications. The precision and material innovations offered by the company ensure that semiconductors can meet the high-performance demands of these technologies. AI-driven applications, such as machine learning and data analytics, require processors capable of handling massive amounts of data quickly and efficiently. Applied Materials’ epitaxy technologies provide the foundation for creating such processors.
The rise of 5G networks has also increased the need for advanced semiconductors. These networks demand devices that can process data at unprecedented speeds while maintaining energy efficiency. Applied Materials epitaxy addresses these challenges by improving the electrical conductivity and thermal management of semiconductor materials. This capability ensures that devices can operate reliably in high-speed, high-demand environments.
By supporting AI and 5G applications, Applied Materials epitaxy not only meets current technological needs but also anticipates future trends. This forward-thinking approach positions the company as a key player in the ongoing evolution of the semiconductor industry.
Challenges and Opportunities in Epitaxy Adoption
Overcoming Scalability and Cost Barriers
Scaling epitaxy processes to meet the growing demand for advanced semiconductors presents a significant challenge. Manufacturers often face high costs when implementing epitaxy technologies, especially for large-scale production. However, Applied Materials addresses these barriers by introducing innovative solutions that improve efficiency and reduce expenses.
One key approach involves the use of selective deposition techniques. This method places materials only where needed, minimizing waste and lowering production costs. Additionally, advancements in epitaxial growth equipment, such as atomic layer epitaxy (ALE) and molecular beam epitaxy (MBE), allow for precise material usage. These technologies ensure that manufacturers can scale production without compromising quality.
“Epitaxy is the only affordable method of high-quality crystal growth for many semiconductor materials,” making it indispensable for modern manufacturing. By refining processes and investing in research, Applied Materials helps manufacturers overcome scalability challenges while maintaining cost-effectiveness.
Ensuring Compatibility with Existing Processes
Integrating epitaxy technologies into existing semiconductor manufacturing processes requires careful planning. Compatibility issues can arise when new methods or materials are introduced. Applied Materials tackles this challenge by designing epitaxial growth systems that seamlessly align with current production workflows.
Their advanced equipment supports a wide range of materials, including silicon carbide (SiC) and gallium nitride (GaN). These materials are essential for creating high-performance devices like power electronics and LEDs. By ensuring compatibility, Applied Materials enables manufacturers to adopt epitaxy technologies without disrupting their operations.
The company’s focus on precision and uniformity also plays a crucial role. Their epitaxy processes produce consistent results, reducing the risk of defects and ensuring smooth integration. This approach not only simplifies adoption but also enhances the overall efficiency of semiconductor manufacturing.
Expanding Applications Beyond Mobile Processors
While epitaxy is vital for mobile processors, its potential extends far beyond this application. The growing demand for optoelectronic devices, such as LEDs and photodetectors, highlights new opportunities for epitaxy technologies. These devices rely on high-quality crystalline layers, which epitaxy excels at producing.
Emerging trends in the market also point to increasing demand for gallium nitride (GaN) epitaxy. GaN is widely used in power electronics due to its superior thermal and electrical properties. Applied Materials’ expertise in epitaxial growth systems positions them to capitalize on this trend, driving innovation in industries like renewable energy and telecommunications.
“Epitaxy process improvement leads to opportunities in epitaxy growth equipment systems,” opening doors for broader applications. By exploring new markets and refining their technologies, Applied Materials continues to expand the impact of epitaxy across various sectors.
Applied Materials’ Vision for the Future of Epitaxy
Commitment to Sustainable Manufacturing Practices
Applied Materials prioritizes sustainability in its manufacturing processes. The company actively develops technologies that minimize environmental impact while maintaining high performance. By focusing on energy-efficient epitaxial growth systems, Applied Materials reduces power consumption during production. This approach not only lowers operational costs but also supports global efforts to combat climate change.
The company also emphasizes waste reduction. Through selective deposition techniques, Applied Materials ensures that materials are used efficiently, leaving minimal waste behind. This method aligns with their broader goal of promoting responsible resource usage in semiconductor manufacturing.
“Our innovations make possible a better future,” Applied Materials states, reflecting their dedication to creating environmentally friendly solutions. Their commitment to sustainability extends beyond technology, influencing every aspect of their operations. This vision positions them as a leader in sustainable practices within the semiconductor industry.
Anticipating Trends in Semiconductor Technology
Applied Materials stays ahead by anticipating shifts in semiconductor technology. The company closely monitors industry trends to align its innovations with future demands. For instance, the rise of 3D ICs and advanced packaging technologies has driven Applied Materials to refine its epitaxy processes. These advancements enable the creation of compact, high-performance chips that meet the needs of modern devices.
The growing adoption of gallium nitride (GaN) and silicon carbide (SiC) materials also shapes their strategy. These materials are essential for next-generation applications like power electronics and renewable energy solutions. Applied Materials invests in tools and techniques that optimize the use of these materials, ensuring they remain at the forefront of technological progress.
By integrating artificial intelligence (AI) and Internet of Things (IoT) capabilities into their equipment, Applied Materials enhances efficiency and precision. These features improve product quality and streamline manufacturing, making it easier to adapt to emerging trends. Their proactive approach ensures they continue to lead in an ever-evolving industry.
Investing in Research and Development
Research and development (R&D) form the backbone of Applied Materials’ success. The company allocates significant resources to exploring new materials and refining existing technologies. This investment drives continuous improvement in epitaxy processes, enabling the production of faster, more efficient semiconductors.
Applied Materials collaborates with academic institutions and industry partners to push the boundaries of innovation. These partnerships foster knowledge exchange and accelerate the development of cutting-edge solutions. By staying connected to the latest scientific advancements, Applied Materials ensures its technologies remain relevant and impactful.
The company also focuses on long-term projects that anticipate future challenges. For example, their work on atomic-level precision in epitaxial growth addresses the increasing complexity of semiconductor designs. This forward-thinking mindset keeps Applied Materials at the forefront of the industry, ready to meet the demands of tomorrow.
“At Applied Materials, our innovations make possible a better future.” This philosophy underscores their unwavering commitment to R&D, ensuring they continue to shape the future of epitaxy and semiconductor technology.
Broader Applications of Epitaxy Technologies
Use in Photovoltaics and New Energy Solutions
Epitaxy has found a significant role in advancing photovoltaics and new energy solutions. By enabling the deposition of thin crystalline films, epitaxy enhances the efficiency of solar cells. These films improve the electrical characteristics of the materials, allowing solar panels to convert sunlight into energy more effectively. Manufacturers use epitaxial growth techniques to create high-quality silicon layers, which serve as the foundation for modern photovoltaic cells.
In the realm of new energy, epitaxy supports the development of power electronics used in renewable energy systems. Wide band-gap materials like gallium nitride (GaN) and silicon carbide (SiC), grown epitaxially, offer superior thermal and electrical properties. These materials are essential for devices that manage energy in wind turbines, electric vehicles, and smart grids. By improving energy conversion and reducing power loss, epitaxy contributes to a more sustainable future.
“Epitaxy is not just a manufacturing process; it’s a key to unlocking cleaner energy solutions,” as industry experts often emphasize. This transformative technology continues to drive innovation in the energy sector, making renewable energy more accessible and efficient.
Advancements in Graphite and Silicon Carbide Materials
Epitaxy has revolutionized the use of graphite and silicon carbide (SiC) in advanced applications. These materials, known for their exceptional thermal and electrical properties, benefit greatly from epitaxial growth processes. For instance, SiC epitaxy enables the production of high-performance semiconductors used in power electronics and high-frequency devices.
Graphite, when combined with epitaxial techniques, finds applications in emerging technologies like graphene-based electronics. Epitaxial growth allows for the precise layering of graphite, creating materials with enhanced conductivity and strength. These advancements open doors to innovations in flexible electronics, sensors, and even quantum computing.
Manufacturers rely on epitaxy to ensure uniformity and precision in these materials. This consistency is crucial for industries like telecommunications and automotive, where reliability and performance are non-negotiable. By pushing the boundaries of material science, epitaxy continues to expand the potential of graphite and SiC in cutting-edge technologies.
Potential for Growth in Other Semiconductor Markets
The versatility of epitaxy extends beyond mobile processors and energy solutions. Its potential for growth in other semiconductor markets is immense. In photonics, epitaxy enables the creation of high-quality layers for lasers, LEDs, and photodetectors. These devices play a critical role in communication systems, medical equipment, and consumer electronics.
Epitaxy also supports the development of advanced memory devices and microchips. By providing a flawless crystalline foundation, it ensures the production of semiconductors with superior electrical characteristics. This capability is essential for industries that demand high-performance computing, such as artificial intelligence and data centers.
The growing adoption of 3D integrated circuits (ICs) further highlights the importance of epitaxy. These ICs require precise layering of materials, which epitaxy excels at delivering. As the semiconductor industry evolves, epitaxy remains a cornerstone for innovation, driving advancements across various markets.
“The future of semiconductors lies in the precision and versatility of epitaxy,” according to leading researchers. This technology continues to shape the landscape of electronics, paving the way for breakthroughs in multiple industries.
Applied Materials’ epitaxy technologies represent a transformative leap in semiconductor manufacturing. By enabling precise deposition and uniformity at an atomic scale, these innovations enhance the performance and efficiency of mobile processors. The ability to grow semiconductor films epitaxially on wafers ensures a solid foundation for creating advanced devices. As demand for high-performance mobile technology surges, Applied Materials remains a pivotal force, driving progress with its comprehensive range of epitaxial growth equipment. Their commitment to innovation positions them as a leader in shaping the future of mobile processors and beyond.
FAQ
What is epitaxy, and why is it important in semiconductor manufacturing?
Epitaxy refers to the process of growing a thin, crystalline layer on a substrate. This layer aligns perfectly with the underlying material, creating a flawless foundation for advanced semiconductor devices. It plays a critical role in improving the electrical properties of wafers, which directly impacts the speed, efficiency, and power consumption of processors. Without epitaxy, modern mobile processors wouldn’t achieve the performance levels required for today’s demanding applications.
Which industries benefit the most from epitaxy equipment?
Epitaxy equipment finds applications in several industries, including semiconductors, photonics, and wide band-gap materials. In photonics, epitaxy enables the production of light-emitting diodes (LEDs), which are widely used in video displays, telecommunication equipment, and even computers. The semiconductor industry also relies heavily on epitaxy for creating high-performance microprocessors and memory devices.
How does Applied Materials contribute to the epitaxial growth equipment market?
Applied Materials stands out as a global leader in materials engineering solutions for the semiconductor and display industries. Since its founding in 1967, the company has built a reputation as a trusted supplier in the semiconductor market. Their advanced epitaxial growth equipment supports the creation of high-quality crystalline layers, ensuring superior performance and reliability for manufacturers worldwide.
What makes Applied Materials’ epitaxy technologies unique?
Applied Materials focuses on precision, uniformity, and material innovation in their epitaxy technologies. Their advanced processes, such as the NMOS epitaxy deposition process, allow for atomic-level control during material growth. This precision ensures that every layer aligns perfectly with the substrate, resulting in faster, more efficient transistors. Their commitment to research and development also keeps them ahead of industry trends.
How does epitaxy support the growing demand for LEDs?
The increasing global use of LEDs has created significant opportunities for epitaxy equipment manufacturers. Epitaxy enables the production of high-quality crystalline layers essential for LED performance. These layers improve light emission efficiency, making LEDs more reliable and energy-efficient. As a result, epitaxy plays a vital role in meeting the rising demand for LED applications in lighting, displays, and other technologies.
What are the key materials used in epitaxy, and why are they important?
Key materials in epitaxy include silicon, gallium nitride (GaN), and silicon carbide (SiC). Silicon serves as the foundation for most semiconductor devices. GaN and SiC, known as wide band-gap materials, offer superior thermal and electrical properties. These materials are essential for applications like power electronics, renewable energy systems, and high-frequency devices. Applied Materials’ expertise in these materials ensures high-quality results for diverse applications.
Can epitaxy technologies be applied beyond mobile processors?
Absolutely! While epitaxy is crucial for mobile processors, its applications extend to other areas like optoelectronics, power electronics, and renewable energy. For instance, epitaxy supports the development of lasers, photodetectors, and advanced memory devices. It also plays a role in creating efficient solar cells and energy management systems, showcasing its versatility across multiple industries.
What challenges do manufacturers face when adopting epitaxy technologies?
Manufacturers often encounter challenges like scalability and cost when implementing epitaxy technologies. High production costs and the need for precise equipment can pose barriers. However, companies like Applied Materials address these issues by introducing innovative solutions, such as selective deposition techniques, which reduce waste and optimize material usage. These advancements make epitaxy more accessible to manufacturers.
How does epitaxy contribute to sustainability in manufacturing?
Epitaxy supports sustainable manufacturing by enabling energy-efficient designs and reducing material waste. Techniques like selective deposition ensure that materials are used only where needed, minimizing excess. Additionally, epitaxy improves the efficiency of devices like LEDs and power electronics, which consume less energy during operation. Applied Materials’ commitment to sustainability further enhances the environmental benefits of epitaxy technologies.
What future trends can we expect in epitaxy technologies?
The future of epitaxy lies in advancements like atomic-level precision, integration with artificial intelligence (AI), and the use of novel materials. Trends such as 3D integrated circuits (ICs) and advanced packaging technologies will drive further innovation. Applied Materials continues to invest in research and development, ensuring their epitaxy technologies remain at the forefront of these emerging trends.