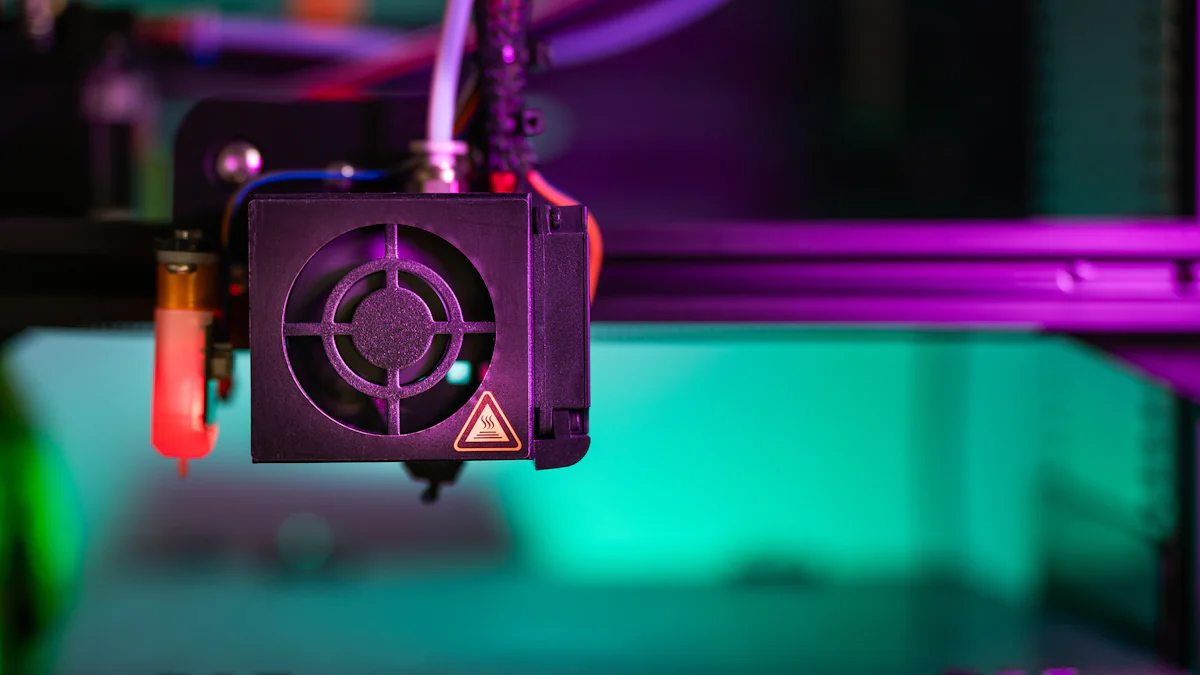
Epitaxial growth has revolutionized LED manufacturing by enabling precise control over material properties. This process creates high-quality crystalline layers essential for producing efficient and durable LEDs. Applied Materials epitaxy has emerged as a game-changer in this field, offering advanced solutions that enhance production efficiency and reduce costs. By utilizing innovative technologies like applied materials epitaxy trays, manufacturers achieve superior performance and reliability in LED devices. The growing demand for LEDs in lighting, displays, and automotive applications underscores the importance of these advancements, positioning applied materials epi as a leader in driving the next generation of LED innovation.
Key Takeaways
- Epitaxial growth is crucial for producing high-quality LEDs, ensuring defect-free crystalline layers that enhance efficiency and longevity.
- Applied Materials epitaxy introduces innovative techniques like remote epitaxy and hybrid vapor phase epitaxy (HVPE) to reduce costs and improve production efficiency.
- The use of advanced materials such as gallium nitride (GaN) and indium gallium nitride (InGaN) is essential for achieving high brightness and durability in LEDs.
- Innovative epitaxial methods enable the creation of flexible and transparent LEDs, expanding their applications in industries like automotive and wearable technology.
- By optimizing manufacturing processes, Applied Materials epitaxy helps manufacturers meet the growing demand for sustainable and cost-effective LED solutions.
- The integration of advanced epitaxial techniques positions Applied Materials as a leader in driving the next generation of LED innovation.
The Fundamentals of Epitaxial Growth in LED Manufacturing
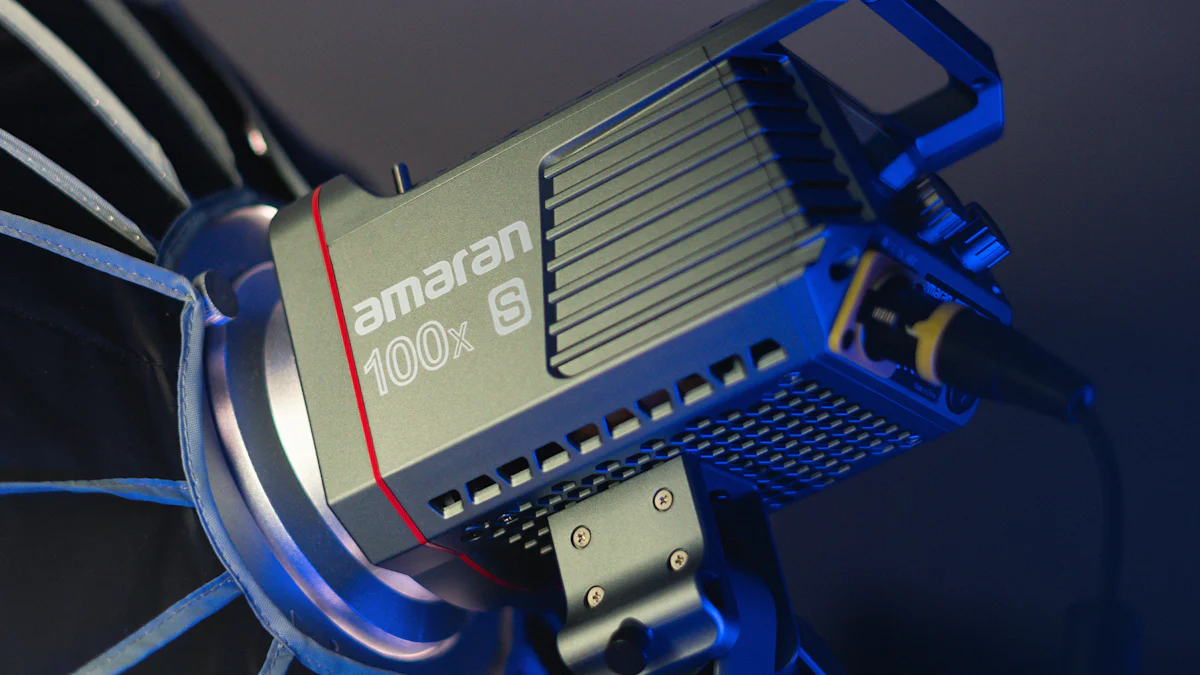
Defining Epitaxial Growth
Epitaxial growth refers to the process of depositing a crystalline layer on a substrate, where the deposited layer mimics the crystal structure of the underlying material. This technique ensures the creation of high-quality layers with precise control over thickness, composition, and uniformity. In LED manufacturing, epitaxial growth plays a pivotal role by forming the foundation for efficient light-emitting devices. The process involves advanced methods such as metal-organic chemical vapor deposition (MOCVD) and hydride vapor phase epitaxy (HVPE), which enable manufacturers to achieve exceptional crystal quality and performance.
The importance of epitaxial growth lies in its ability to produce defect-free layers, which directly impacts the efficiency and longevity of LEDs. By ensuring a seamless crystalline structure, this method minimizes energy loss and enhances the internal quantum efficiency of the devices. Applied Materials epitaxy has further refined this process, introducing innovative systems that optimize throughput and reduce production costs.
The Role of Epitaxial Growth in LED Production
Epitaxial growth serves as the backbone of LED production, influencing every aspect of device performance. It enables the creation of high-brightness LEDs (HB-LEDs) by providing a stable and uniform platform for subsequent layers. This stability is crucial for achieving consistent light output and color accuracy, which are essential for applications in lighting, displays, and automotive industries.
Manufacturers rely on epitaxial growth to enhance the thermal and electrical properties of LEDs. By precisely controlling the layer composition, they can improve heat dissipation and reduce power consumption. Advanced epitaxial techniques, such as remote epitaxy and van der Waals epitaxy, offer additional benefits like cost reduction and scalability. These methods allow for the reuse of substrates, further driving down production expenses while maintaining high crystal quality.
Key Materials in Epitaxial Growth for LEDs
The choice of materials in epitaxial growth significantly impacts the performance and efficiency of LEDs. Gallium nitride (GaN) stands out as the most widely used material due to its excellent optical and electrical properties. GaN-based LEDs exhibit high brightness and durability, making them ideal for various applications. Indium gallium nitride (InGaN) is another critical material, often used in multi-layer structures to achieve specific wavelengths and colors.
Silicon carbide (SiC) and sapphire are commonly employed as substrates in epitaxial growth. These materials provide the necessary thermal conductivity and mechanical stability for high-performance LEDs. Recent advancements in hybrid vapor phase epitaxy (HVPE) have enabled the integration of these materials with greater precision, resulting in improved device efficiency and reduced manufacturing costs.
Applied Materials epitaxy has revolutionized the use of these materials by developing multi-chamber tools that combine MOCVD and HVPE processes. This innovation ensures optimal layer quality while minimizing downtime, setting new benchmarks in LED manufacturing.
Applied Materials Epitaxy: Revolutionizing LED Manufacturing
Remote Epitaxy and Its Benefits
Remote epitaxy has emerged as a groundbreaking technique in LED manufacturing. This method allows the growth of crystalline layers on a substrate while maintaining the ability to separate the layers for reuse. By leveraging this approach, manufacturers achieve significant cost savings and reduce material waste. The process relies on the precise alignment of atomic structures, ensuring high-quality layers with minimal defects.
Applied Materials epitaxy integrates remote epitaxy into its advanced systems, enabling manufacturers to enhance production efficiency. This technology supports the creation of ultra-thin layers, which are essential for next-generation LEDs. The ability to reuse substrates further drives down production costs, making LED manufacturing more sustainable and economically viable. Remote epitaxy also facilitates the development of flexible and lightweight LED designs, opening new possibilities for innovative applications in industries such as wearable technology and automotive lighting.
Van der Waals Epitaxy for Next-Generation LEDs
Van der Waals epitaxy represents another transformative advancement in LED manufacturing. This technique involves the deposition of crystalline layers on substrates without requiring a perfect lattice match. Instead, it relies on weak van der Waals forces to bond the layers, allowing greater flexibility in material selection. This method enables the integration of diverse materials, paving the way for the development of high-performance LEDs with unique properties.
Applied Materials epitaxy incorporates van der Waals epitaxy to address the growing demand for next-generation LEDs. By utilizing this technique, manufacturers can produce LEDs with enhanced efficiency and color accuracy. The ability to combine different materials expands the range of achievable wavelengths, making it possible to create LEDs tailored for specific applications. Van der Waals epitaxy also supports the production of transparent and flexible LEDs, which are ideal for advanced display technologies and architectural lighting.
Hybrid Vapor Phase Epitaxy (HVPE) for Cost-Effective Production
Hybrid Vapor Phase Epitaxy (HVPE) has become a preferred method for cost-effective LED production. This technique offers faster growth rates compared to traditional methods like MOCVD, significantly reducing manufacturing time. HVPE also ensures excellent run-to-run wavelength uniformity, which is critical for maintaining consistent LED performance.
Applied Materials epitaxy utilizes HVPE technology to optimize LED manufacturing processes. The unique chamber architecture of their systems ensures repeatability and precision, resulting in highly uniform films with low defect levels. This approach minimizes downtime and maximizes throughput, enabling manufacturers to meet the increasing demand for LEDs in a cost-efficient manner. HVPE also supports the integration of advanced materials like gallium nitride (GaN) and silicon carbide (SiC), further enhancing the performance and durability of LEDs.
By combining remote epitaxy, van der Waals epitaxy, and HVPE, Applied Materials epitaxy sets new standards in LED manufacturing. These technologies not only improve production efficiency but also enable the creation of innovative LED designs that cater to a wide range of applications.
Real-World Applications of Applied Materials Epitaxy in LEDs
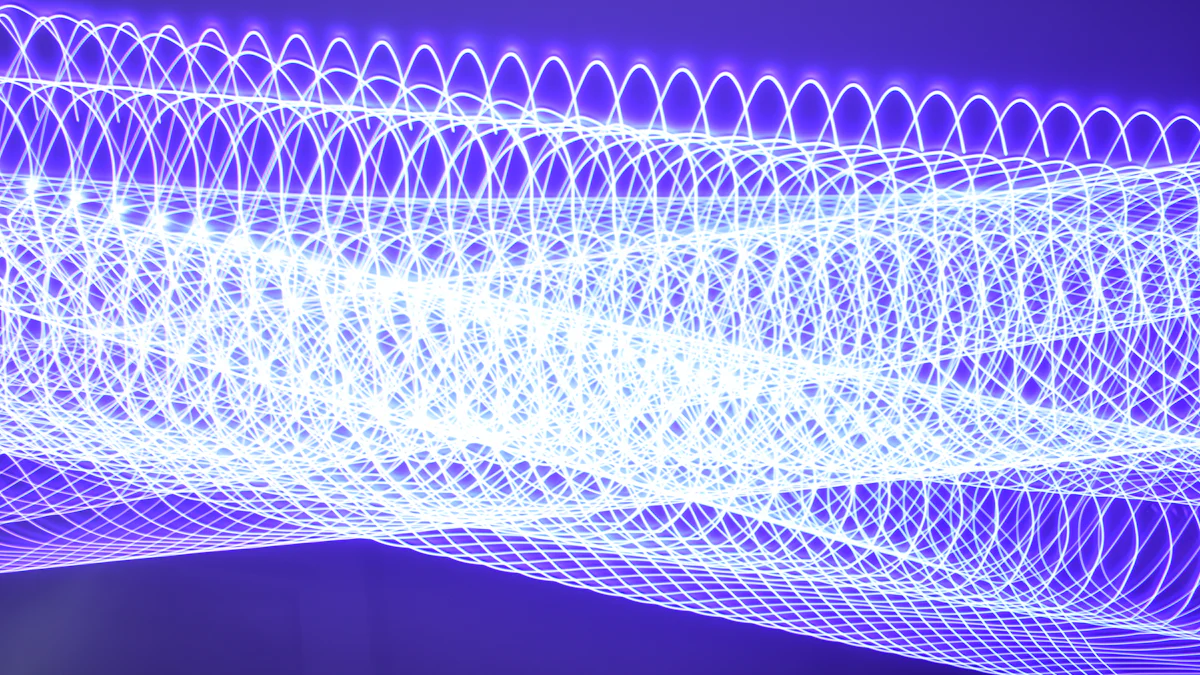
Enhancing LED Efficiency and Longevity
Applied Materials epitaxy plays a critical role in improving the efficiency and lifespan of LEDs. By utilizing advanced epitaxial growth techniques, manufacturers achieve precise control over the crystalline layers, which directly impacts the internal quantum efficiency of the devices. This precision reduces energy loss during operation, resulting in brighter and more energy-efficient LEDs.
The integration of gallium nitride (GaN) in epitaxial processes further enhances thermal management, allowing LEDs to operate at higher temperatures without compromising performance. This improvement significantly extends the lifespan of the devices, making them ideal for applications in demanding environments such as automotive lighting and outdoor displays.
“The advanced epitaxial growth system developed by Applied Materials decreases operating costs while increasing internal quantum efficiency,” a testament to its transformative impact on LED manufacturing.
These advancements ensure that LEDs not only perform better but also maintain their efficiency over extended periods, meeting the growing demand for reliable and sustainable lighting solutions.
Reducing Costs Through Advanced Epitaxial Techniques
Cost reduction remains a priority in LED manufacturing, and Applied Materials epitaxy addresses this challenge through innovative approaches. Techniques like remote epitaxy and hybrid vapor phase epitaxy (HVPE) enable manufacturers to reuse substrates, significantly lowering material costs. The ability to grow high-quality crystalline layers at faster rates further reduces production time, enhancing overall efficiency.
The adoption of multi-chamber tools that combine metal-organic chemical vapor deposition (MOCVD) and HVPE processes optimizes throughput while maintaining exceptional layer quality. This integration minimizes downtime and ensures consistent production, which is crucial for meeting the rising demand for LEDs in various industries.
By streamlining manufacturing processes and reducing material waste, Applied Materials epitaxy makes LED production more economically viable. These cost-saving measures benefit manufacturers and contribute to the affordability of LEDs for end-users, accelerating their adoption in residential, commercial, and industrial applications.
Enabling Innovative LED Designs
Applied Materials epitaxy opens new possibilities for innovative LED designs by supporting the development of ultra-thin, flexible, and transparent devices. Techniques like van der Waals epitaxy allow the integration of diverse materials, enabling the creation of LEDs with unique properties tailored to specific applications.
Flexible LEDs, made possible through advanced epitaxial methods, are revolutionizing industries such as wearable technology and automotive lighting. Transparent LEDs, another breakthrough, are gaining traction in architectural lighting and advanced display technologies, offering seamless integration into modern designs.
The ability to produce LEDs with enhanced color accuracy and a broader range of wavelengths further expands their applications. From high-resolution displays to specialized lighting for medical and horticultural purposes, Applied Materials epitaxy drives innovation across multiple sectors.
These advancements position Applied Materials epitaxy as a leader in shaping the future of LED technology, enabling manufacturers to meet evolving market demands with cutting-edge solutions.
Challenges in Adopting Advanced Epitaxy Methods
Technical Hurdles in Scaling Epitaxial Growth
Scaling epitaxial growth for mass production presents significant technical challenges. Manufacturers must ensure that the crystalline layers maintain uniformity and defect-free structures across larger substrates. Any deviation in layer quality can compromise LED performance, leading to inefficiencies and reduced product reliability. Achieving this level of precision requires advanced equipment and meticulous process control.
Traditional LED manufacturing methods often rely on a single metal-organic chemical vapor deposition (MOCVD) chamber for each layer. This approach slows production and demands frequent cleaning, which increases downtime. Advanced epitaxy techniques, such as those developed by Applied Materials, address these issues by using separate MOCVD chambers for each layer. These chambers include self-cleaning mechanisms, which enhance efficiency and reduce contamination risks. However, implementing such systems on a large scale requires substantial investment and expertise.
The integration of innovative methods like remote epitaxy and hybrid vapor phase epitaxy (HVPE) also introduces complexities. These techniques demand precise alignment of atomic structures and advanced material handling capabilities. Manufacturers must invest in specialized training and infrastructure to adopt these technologies effectively. Despite these challenges, the potential benefits of improved efficiency and reduced costs make overcoming these hurdles a priority for the industry.
Economic Barriers and Market Competition
Economic factors pose another significant challenge in adopting advanced epitaxy methods. The initial investment in state-of-the-art equipment and facilities can be prohibitively high for many manufacturers. Advanced epitaxy systems, such as multi-chamber tools combining MOCVD and HVPE processes, require substantial capital expenditure. Smaller companies may struggle to compete with larger players who can afford these investments.
Market competition further intensifies these economic pressures. The LED industry faces constant demand for cost reductions while maintaining high-quality standards. Manufacturers must balance the need for innovation with the imperative to remain competitive in pricing. Advanced epitaxy techniques, while cost-effective in the long term, require a strategic approach to justify the upfront costs.
Additionally, the global LED market experiences fluctuations in demand due to economic conditions and technological advancements. Companies must navigate these uncertainties while committing to the adoption of advanced epitaxy methods. Strategic partnerships and collaborations can help mitigate these risks, enabling manufacturers to share resources and expertise.
“Traditional methods slow production and increase costs, but advanced epitaxy techniques optimize throughput and reduce downtime,” highlighting the economic advantages of innovation despite the initial barriers.
By addressing these technical and economic challenges, manufacturers can unlock the full potential of advanced epitaxy methods. These efforts will drive the next wave of innovation in LED manufacturing, ensuring sustainable growth and competitiveness in the global market.
Opportunities for the Future of LED Manufacturing with Applied Materials Epitaxy
Expanding LED Applications Across Industries
The future of LED manufacturing holds immense potential as industries continue to explore innovative applications. LEDs have already transformed lighting, displays, and automotive sectors. However, advancements in epitaxial growth technologies are unlocking new possibilities. Applied materials epitaxy enables the production of high-performance LEDs tailored for specialized uses, such as wearable technology, horticultural lighting, and medical devices.
In the display industry, the development of ultra-high brightness Micro-LEDs is a game-changer. These LEDs, built on wafer-scale uniform GaN-on-silicon epilayers, deliver unprecedented brightness and resolution. Their integration with silicon-based circuits allows for compact designs, making them ideal for augmented reality (AR) and virtual reality (VR) devices. Unlike traditional OLEDs, Micro-LEDs offer superior durability and energy efficiency, addressing the challenges of burn-in and short lifespans. With pixel densities reaching up to 3400 ppi, these LEDs are revolutionizing AR/VR headsets, wearable displays, and advanced mobile devices.
Automotive lighting is another area poised for growth. LEDs with enhanced thermal management and longevity are essential for high-performance headlights and interior lighting. Applied materials epitaxy supports the creation of LEDs that withstand extreme conditions, ensuring reliability in demanding environments. Additionally, transparent and flexible LEDs are gaining traction in architectural lighting, offering seamless integration into modern designs.
The trend toward larger wafer sizes and multi-wafer epitaxy systems is further expanding LED applications. These systems increase throughput and reduce costs, enabling manufacturers to meet the growing demand across industries. By accommodating multiple wafers simultaneously, epitaxy platforms maintain high process uniformity and efficiency, paving the way for scalable production.
Innovations in Epitaxial Growth Technologies
Innovations in epitaxial growth technologies are driving the next wave of LED manufacturing advancements. Techniques like GaN-on-silicon epitaxy are gaining popularity due to their cost-effectiveness and compatibility with existing silicon-based electronics. This approach reduces production expenses while enabling seamless integration with other semiconductor devices. Applied materials epitaxy plays a pivotal role in refining these methods, ensuring high-quality growth and minimal defects.
Remote epitaxy and van der Waals epitaxy are also transforming the industry. Remote epitaxy allows for substrate reuse, significantly lowering material costs and waste. This technique supports the creation of ultra-thin layers, essential for flexible and lightweight LED designs. Van der Waals epitaxy, on the other hand, enables the deposition of crystalline layers without requiring a perfect lattice match. This flexibility expands material options, fostering the development of LEDs with unique properties.
Hybrid Vapor Phase Epitaxy (HVPE) continues to gain traction as a cost-effective solution. Its faster growth rates and excellent wavelength uniformity make it a preferred choice for high-volume production. By combining HVPE with metal-organic chemical vapor deposition (MOCVD), manufacturers achieve exceptional layer quality while optimizing throughput. These innovations ensure that applied materials epitaxy remains at the forefront of LED manufacturing, setting new benchmarks in efficiency and performance.
The development of ultra-high brightness green Micro-LEDs exemplifies the potential of these technologies. Researchers have overcome challenges like low-quality growth on silicon and poor light extraction efficiency, creating scalable solutions for micro-display technology. These LEDs, with their unmatched brightness and resolution, are poised to disrupt industries such as AR/VR, automotive displays, and wearable tech. Their integration with silicon CMOS circuits further enhances their appeal, enabling compact and high-resolution designs.
As epitaxial growth technologies evolve, they will continue to shape the future of LED manufacturing. Applied materials epitaxy stands as a key enabler, driving innovation and expanding the possibilities for LEDs across diverse applications.
Applied Materials epitaxy has redefined LED manufacturing by delivering advanced solutions that enhance efficiency, reduce costs, and improve performance. Its innovative methods, such as separate MOCVD chambers with self-cleaning capabilities, optimize production processes and ensure superior crystal quality. These advancements empower manufacturers to achieve higher yields and superior LED performance while addressing the growing demand for sustainable and cost-effective lighting solutions. By driving innovation in epitaxial growth technologies, Applied Materials epitaxy continues to shape the future of LEDs, enabling breakthroughs across industries and setting new standards for excellence.
FAQ
What is the impact of epitaxy on LED manufacturing?
Epitaxy significantly influences the quality and performance of LEDs. This process ensures the creation of defect-free crystalline layers, which directly enhance the efficiency and longevity of LED devices. Manufacturers focus on advanced materials, optimized designs, and refined processes to achieve higher yields and superior performance in LED production.
How has Applied Materials contributed to LED manufacturing?
Applied Materials has revolutionized LED manufacturing by introducing an advanced epitaxial growth system tailored for gallium nitride (GaN) LED devices. This system reduces operating costs, improves internal quantum efficiency, and enhances binning yields. These innovations enable manufacturers to produce high-quality LEDs more efficiently and cost-effectively.
What are some technological advancements in the LED epitaxy susceptor market?
The LED epitaxy susceptor market has seen remarkable advancements. Manufacturers now utilize materials with superior thermal conductivity, chemical resistance, and mechanical strength. Multi-wafer epitaxy systems and effective thermal management techniques further enhance production efficiency and device performance.
What is the role of Applied Materials in epitaxy?
Applied Materials plays a leading role in epitaxy by developing cutting-edge technologies that redefine LED manufacturing. Their systems integrate advanced methods like remote epitaxy, van der Waals epitaxy, and hybrid vapor phase epitaxy (HVPE), setting new benchmarks in efficiency, cost reduction, and innovation.
What is the focus of epitaxial growth in LED manufacturing?
Epitaxial growth in LED manufacturing emphasizes precision and innovation. Techniques such as advanced growth on van der Waals materials enable the creation of high-performance LEDs with unique properties. These methods support the development of next-generation devices tailored for specialized applications.
What are the opportunities in epitaxy growth equipment systems?
Epitaxy growth equipment systems present significant opportunities for innovation and efficiency. Technologies like metal-organic chemical vapor deposition (MOCVD), molecular beam epitaxy (MBE), and chemical vapor deposition (CVD) offer diverse options based on technical performance and cost considerations. These systems drive advancements in LED manufacturing by ensuring high-quality layer growth.
How does epitaxy enhance LED efficiency and longevity?
Epitaxy ensures precise control over crystalline layers, which directly impacts the internal quantum efficiency of LEDs. This precision minimizes energy loss and improves thermal management, allowing LEDs to operate at higher temperatures without compromising performance. These factors contribute to brighter, more energy-efficient LEDs with extended lifespans.
What materials are commonly used in epitaxial growth for LEDs?
Gallium nitride (GaN) and indium gallium nitride (InGaN) are widely used in epitaxial growth due to their excellent optical and electrical properties. Substrates like silicon carbide (SiC) and sapphire provide the necessary thermal conductivity and mechanical stability. These materials form the foundation for high-performance LEDs.
How do advanced epitaxial techniques reduce manufacturing costs?
Techniques like remote epitaxy and hybrid vapor phase epitaxy (HVPE) enable substrate reuse, significantly lowering material costs. Faster growth rates and optimized processes reduce production time and enhance throughput. These advancements make LED manufacturing more economically viable while maintaining high-quality standards.
What innovative LED designs are enabled by Applied Materials epitaxy?
Applied Materials epitaxy supports the development of ultra-thin, flexible, and transparent LEDs. These designs cater to emerging applications in wearable technology, automotive lighting, and advanced displays. By enabling diverse material integration, epitaxy expands the possibilities for creating LEDs with unique properties and tailored functionalities.