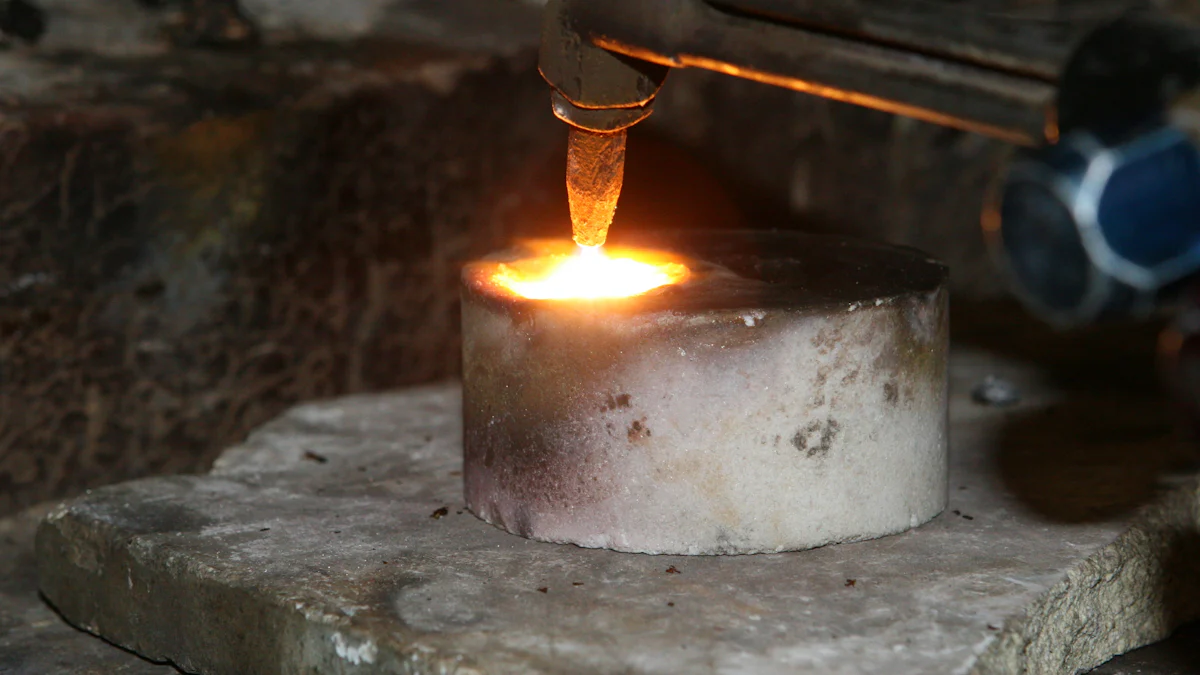
Silicon carbide ceramic coating stands out for its remarkable ability to endure extreme heat and stress. Its high thermal conductivity of 120 W/m•K ensures efficient heat dissipation, while a low coefficient of thermal expansion (4.0 x10–6/°C) minimizes structural changes during temperature shifts. This unique combination allows it to maintain integrity under harsh conditions. Industries rely on this coating to protect tools and equipment exposed to temperatures as high as 1600°C. When comparing sio2 vs ceramic coating, silicon carbide spray coating often emerges as a superior choice due to its enhanced durability and performance. Whether in semiconductor manufacturing or other demanding environments, its performance remains unmatched, making it one of the best sio2 ceramic coatings available.
Key Takeaways
- Silicon carbide coatings excel in high-temperature environments, maintaining integrity at temperatures up to 1600°C, making them ideal for industries like aerospace and energy.
- The unique crystal structure of silicon carbide provides exceptional hardness and durability, ranking just below diamond on the Mohs scale, ensuring resistance to wear and mechanical stress.
- Passive oxidation forms a protective silica layer on silicon carbide at elevated temperatures, enhancing its durability and preventing further oxidation, crucial for long-lasting performance.
- Silicon carbide’s low coefficient of thermal expansion minimizes thermal shock, allowing it to withstand rapid temperature changes without cracking, essential for power generation applications.
- Advanced preparation methods like Chemical Vapor Deposition (CVD) and thermal spray techniques ensure high-quality coatings tailored to specific industrial needs, enhancing performance and longevity.
- Industries benefit from silicon carbide coatings by reducing maintenance costs and improving operational efficiency, particularly in semiconductor manufacturing and energy systems.
- Ongoing research and advancements in coating technologies promise even greater efficiency and durability, positioning silicon carbide as a leading choice for future industrial applications.
Material Properties of Silicon Carbide Ceramic Coating
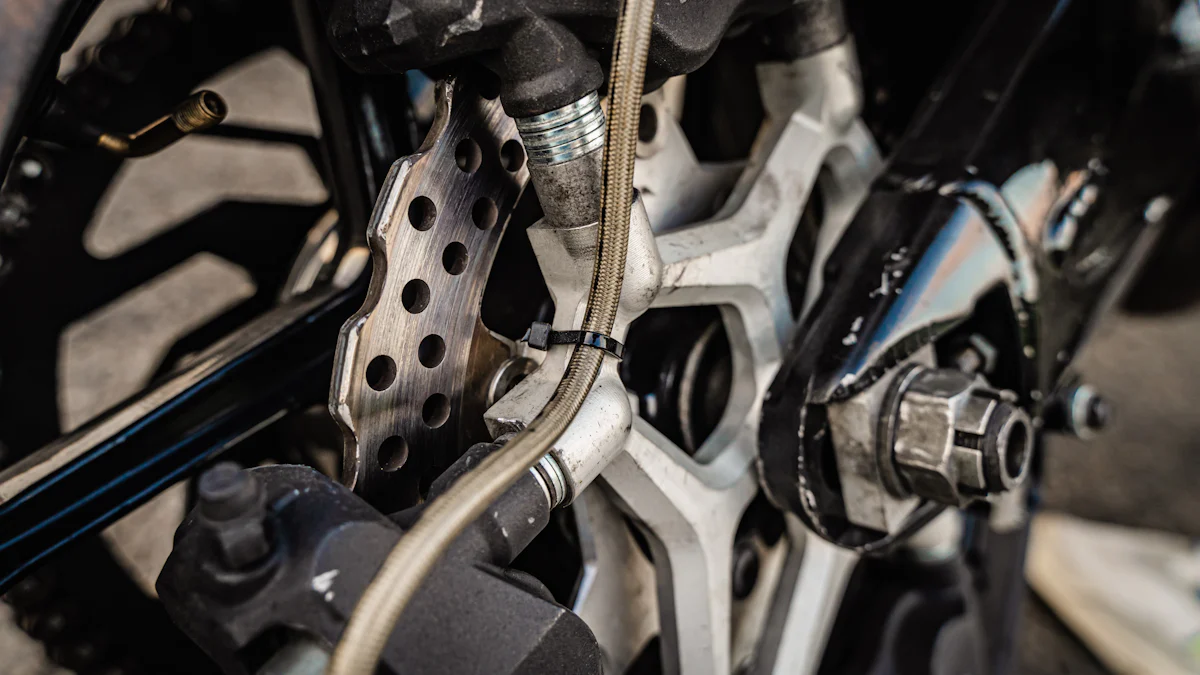
Crystal Structure and Bonding
Silicon carbide (SiC) owes much of its strength and durability to its unique crystal structure. It forms a covalent bond between silicon and carbon atoms, creating a robust lattice. This bond is one of the strongest in materials science, which explains why SiC can endure extreme conditions. The tightly packed structure minimizes atomic movement, even under high stress or temperature. This stability makes it an ideal choice for environments where other materials might fail.
The crystalline arrangement also contributes to its hardness. SiC ranks just below diamond on the Mohs scale, making it incredibly resistant to wear and abrasion. This property ensures that silicon carbide ceramic coating remains intact, even when exposed to mechanical stress or harsh operating conditions. Its structural integrity plays a key role in its widespread industrial applications.
Thermal and Mechanical Properties
Silicon carbide ceramic coating stands out for its exceptional thermal properties. It boasts a high thermal conductivity, which allows it to transfer heat efficiently. This feature is crucial in industries like semiconductor manufacturing, where precise temperature control is essential. Additionally, its low coefficient of thermal expansion ensures minimal dimensional changes during rapid temperature shifts. This combination prevents cracking or warping, even in extreme heat.
Mechanical properties further enhance its performance. SiC exhibits remarkable hardness and structural stability, making it resistant to deformation under pressure. Its ability to withstand high temperatures without losing strength sets it apart from many other materials. For example, it remains stable at temperatures up to 1600°C, making it suitable for harsh environments.
Moreover, silicon carbide ceramic coating resists chemical corrosion, adding another layer of protection. This resistance ensures longevity and reliability, even in chemically aggressive settings. Industries rely on these properties to safeguard equipment and maintain operational efficiency.
Mechanisms of High-Temperature Resistance
Passive Oxidation and Silica Layer Formation
Silicon carbide ceramic coating demonstrates remarkable resistance to high temperatures, thanks to a process called passive oxidation. When exposed to air at elevated temperatures, silicon carbide reacts with oxygen to form a thin layer of silicon dioxide (SiO2) on its surface. This silica layer acts as a protective barrier, preventing further oxidation and shielding the underlying material from damage. The formation of this layer typically begins around 1200°C and continues to enhance the coating’s durability as temperatures rise.
This protective mechanism is particularly valuable in harsh environments. The silica layer not only resists chemical attacks but also maintains its stability under extreme heat. Industries that operate in high-temperature settings, such as aerospace and energy, rely on this property to extend the lifespan of their equipment. The ability of silicon carbide to self-generate this shield ensures consistent performance, even in the most demanding conditions.
Scientific Research Findings: Studies have shown that the passive oxidation of silicon carbide occurs efficiently between 800°C and 1100°C, providing critical protection during thermal exposure (J. Am. Ceram. Soc., 1989). This natural defense mechanism makes silicon carbide coatings an indispensable choice for applications requiring thermal stability.
Resistance to Thermal Shock
Thermal shock resistance is another standout feature of silicon carbide ceramic coating. Rapid temperature changes can cause materials to crack or fail due to uneven expansion and contraction. However, silicon carbide’s low coefficient of thermal expansion minimizes these stresses, allowing it to endure sudden shifts in temperature without compromising its structural integrity.
This property proves essential in industries where equipment frequently transitions between high and low temperatures. For example, in power generation, components often face abrupt heating and cooling cycles. Silicon carbide coatings excel in these scenarios, maintaining their performance and preventing costly failures.
Additionally, the material’s high thermal conductivity plays a crucial role in managing thermal shock. By efficiently dissipating heat, silicon carbide reduces the risk of localized stress points that could lead to fractures. This combination of properties ensures that the coating remains reliable, even under the most challenging thermal conditions.
Scientific Research Findings: Research highlights that refining the grain size of silicon carbide enhances its resistance to thermal shock, further improving its performance in high-temperature environments (Surf. Coat. Technol., 2017). This advancement underscores the material’s adaptability and effectiveness in protecting critical components.
Preparation Methods for Silicon Carbide Ceramic Coating
Silicon carbide ceramic coating owes its exceptional performance to advanced preparation methods. These techniques ensure the coating achieves the desired properties, such as high thermal stability and mechanical strength. Let’s explore three widely used methods that make this possible.
Chemical Vapor Deposition (CVD)
Chemical Vapor Deposition (CVD) stands out as one of the most effective methods for producing silicon carbide ceramic coatings. This process involves introducing gaseous precursors into a vacuum chamber, where they react and deposit a thin, uniform layer of silicon carbide onto a substrate. The result is a dense, high-purity coating with superior thermal and mechanical properties.
CVD coatings exhibit remarkable resistance to oxidation and wear, making them ideal for demanding applications. For instance, industries use CVD-coated silicon carbide in semiconductor manufacturing, where precision and durability are critical. Additionally, CVD enables the production of lightweight, monolithic silicon carbide components, such as mirrors for telescopes and laser systems. These components benefit from the material’s isotropic characteristics, ensuring consistent performance across various conditions.
Fun Fact: CVD technology for silicon carbide coatings dates back to the 1960s, with significant advancements made by researchers at Bell Labs. Their work paved the way for widespread industrial applications, including aerospace and optics.
Thermal Spray Techniques
Thermal spray techniques offer another popular method for applying silicon carbide ceramic coatings. This process involves heating silicon carbide particles to a molten or semi-molten state and spraying them onto a surface at high velocity. The particles bond to the substrate, forming a durable coating layer.
Thermal spray coatings excel in protecting equipment exposed to extreme wear and heat. Industries like power generation and manufacturing rely on this method to enhance the lifespan of critical components. The versatility of thermal spray techniques allows for the coating of complex shapes and large surfaces, making it a practical choice for various applications.
One notable advantage of thermal spray methods is their ability to produce coatings with tailored thicknesses. This flexibility ensures the coating meets specific performance requirements, whether for corrosion resistance or thermal insulation.
Sintering and Advanced Methods
Sintering represents a traditional yet highly effective method for creating silicon carbide ceramic coatings. This process involves compacting silicon carbide powder into a desired shape and heating it to a temperature just below its melting point. The heat causes the particles to bond, forming a solid, dense coating.
Modern advancements have introduced innovative sintering techniques, such as hot pressing and spark plasma sintering. These methods enhance the coating’s density and mechanical properties, making them suitable for high-performance applications. For example, sintered silicon carbide coatings are often used in chemical processing equipment due to their excellent resistance to corrosion and thermal shock.
In addition to sintering, researchers continue to develop advanced methods for silicon carbide coating preparation. Techniques like plasma-enhanced CVD and laser-assisted deposition push the boundaries of what these coatings can achieve. These innovations promise even greater efficiency and performance in the future.
Real-World Applications of Silicon Carbide Ceramic Coating
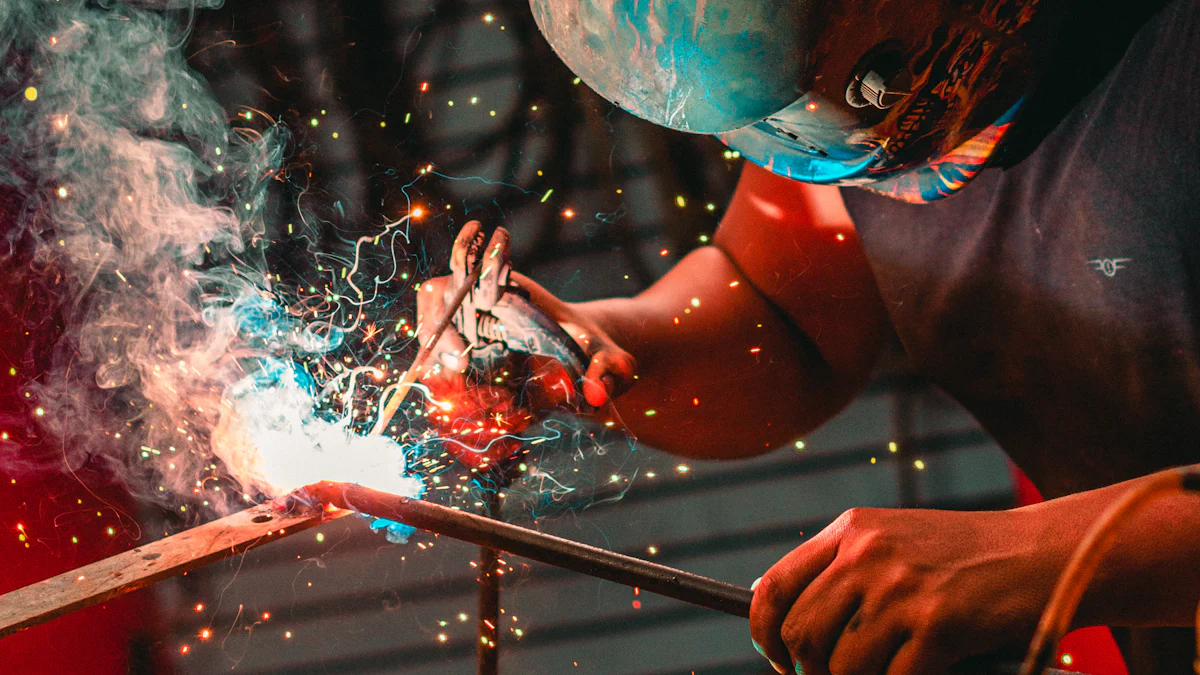
Silicon carbide ceramic coating has become a game-changer across various industries. Its unique properties, such as high-temperature resistance, exceptional strength, and durability, make it indispensable in demanding environments. Let’s explore how different sectors benefit from this advanced material.
Aerospace and Defense
The aerospace and defense industries rely heavily on silicon carbide ceramic coating for its ability to withstand extreme conditions. Aircraft engines, rocket nozzles, and heat shields use this coating to endure high temperatures and intense mechanical stress. Its lightweight nature also contributes to fuel efficiency, which is critical in aerospace applications.
In defense, silicon carbide coatings protect equipment like missile components and armored vehicles. The material’s hardness and resistance to wear ensure long-lasting performance, even in harsh environments. By enhancing the durability of critical components, this coating plays a vital role in ensuring safety and reliability in these industries.
Did You Know? Silicon carbide materials are also used in nuclear applications, where their resistance to radiation and thermal stress proves invaluable.
Energy and Power Generation
Energy and power generation sectors benefit significantly from silicon carbide ceramic coating. Power plants, especially those using gas turbines, require materials that can handle rapid temperature changes. Silicon carbide’s thermal shock resistance makes it an ideal choice for these applications. It prevents cracking and ensures consistent performance during heating and cooling cycles.
The renewable energy industry also takes advantage of this coating. Solar panels and LED production processes often involve high temperatures, where silicon carbide coatings provide the necessary protection. Additionally, its high thermal conductivity improves efficiency in heat exchangers and other energy systems.
Fun Fact: Silicon carbide’s ability to transfer heat efficiently makes it a popular choice for heating elements in industrial furnaces.
Industrial and Manufacturing Applications
In industrial and manufacturing settings, silicon carbide ceramic coating enhances the performance of tools and machinery. Its resistance to wear and corrosion ensures that equipment lasts longer, reducing maintenance costs. Industries like automotive manufacturing and metallurgy use this coating to protect components exposed to extreme heat and abrasive conditions.
Semiconductor manufacturing also relies on silicon carbide coatings. The material’s stability at high temperatures and resistance to chemical corrosion make it essential for producing wafers and other semiconductor components. This coating ensures precision and reliability, which are crucial in the electronics industry.
Moreover, silicon carbide coatings are versatile enough to be applied to various substrates, including metals, ceramics, and glass. This adaptability allows manufacturers to use the coating in a wide range of applications, from protective layers on tools to advanced components in electronic devices.
Pro Tip: When selecting a coating for industrial use, consider factors like thermal conductivity and hardness to ensure optimal performance.
Silicon carbide ceramic coating continues to impress with its ability to endure extreme temperatures and harsh conditions. Its unique properties, like passive oxidation and thermal shock resistance, make it a reliable choice for demanding applications. Advanced preparation methods, such as CVD and thermal spraying, further enhance its performance by tailoring coatings to specific needs. Industries like aerospace, energy, and manufacturing benefit greatly from these innovations. As research progresses, the potential for silicon carbide coatings grows, promising even more efficient and durable solutions for future challenges.
FAQ
What makes silicon carbide coatings unique?
Silicon carbide coatings stand out due to their exceptional ability to handle extreme temperatures and harsh environments. Their high thermal conductivity ensures efficient heat transfer, while their low coefficient of thermal expansion minimizes structural changes during temperature shifts. These properties make them reliable for industries requiring durability and precision.
How do silicon carbide coatings resist chemical damage?
Silicon carbide’s chemical durability plays a key role in its performance. It resists chemical attacks, ensuring long-lasting reliability even in aggressive environments. This feature proves especially valuable in semiconductor manufacturing, where purity and resistance to chemical reactions are critical for operational success.
Can silicon carbide coatings handle rapid temperature changes?
Yes, silicon carbide coatings excel at managing rapid temperature changes. Their low coefficient of thermal expansion reduces stress caused by sudden heating or cooling. This thermal shock resistance ensures the coating remains intact, making it ideal for applications like power generation and aerospace.
What industries benefit the most from silicon carbide coatings?
Several industries rely on silicon carbide coatings, including aerospace, energy, manufacturing, and semiconductors. For example, aerospace uses these coatings for heat shields and engine components, while semiconductor manufacturing benefits from their chemical stability and precision.
How does the silica layer protect silicon carbide at high temperatures?
When exposed to high temperatures, silicon carbide forms a thin silica (SiO2) layer on its surface through passive oxidation. This layer acts as a protective barrier, preventing further oxidation and shielding the material from damage. It enhances durability and ensures consistent performance in extreme conditions.
Quick Fact: The silica layer begins forming around 1200°C, providing critical protection during thermal exposure.
Are there different methods to apply silicon carbide coatings?
Yes, several methods exist to apply silicon carbide coatings. Chemical Vapor Deposition (CVD) produces dense, high-purity coatings, while thermal spray techniques allow for tailored thicknesses and coverage of complex shapes. Sintering and advanced methods like plasma-enhanced CVD further enhance the coating’s properties.
Why is silicon carbide used in semiconductor manufacturing?
Silicon carbide’s stability at high temperatures and resistance to chemical corrosion make it indispensable in semiconductor manufacturing. It ensures precision and reliability during wafer production and other processes, where maintaining purity is essential.
How durable are silicon carbide coatings?
Silicon carbide coatings are incredibly durable. Their hardness ranks just below diamond on the Mohs scale, making them resistant to wear and abrasion. This durability ensures they can withstand mechanical stress and maintain performance over time.
Can silicon carbide coatings improve energy efficiency?
Absolutely. Silicon carbide’s high thermal conductivity enhances energy efficiency by transferring heat effectively. This property proves useful in applications like heat exchangers, industrial furnaces, and renewable energy systems, where efficient heat management is crucial.
What advancements are being made in silicon carbide coatings?
Researchers continue to develop innovative methods to improve silicon carbide coatings. Techniques like laser-assisted deposition and plasma-enhanced CVD push the boundaries of performance, promising even greater efficiency and durability for future applications. These advancements aim to meet the growing demands of modern industries.