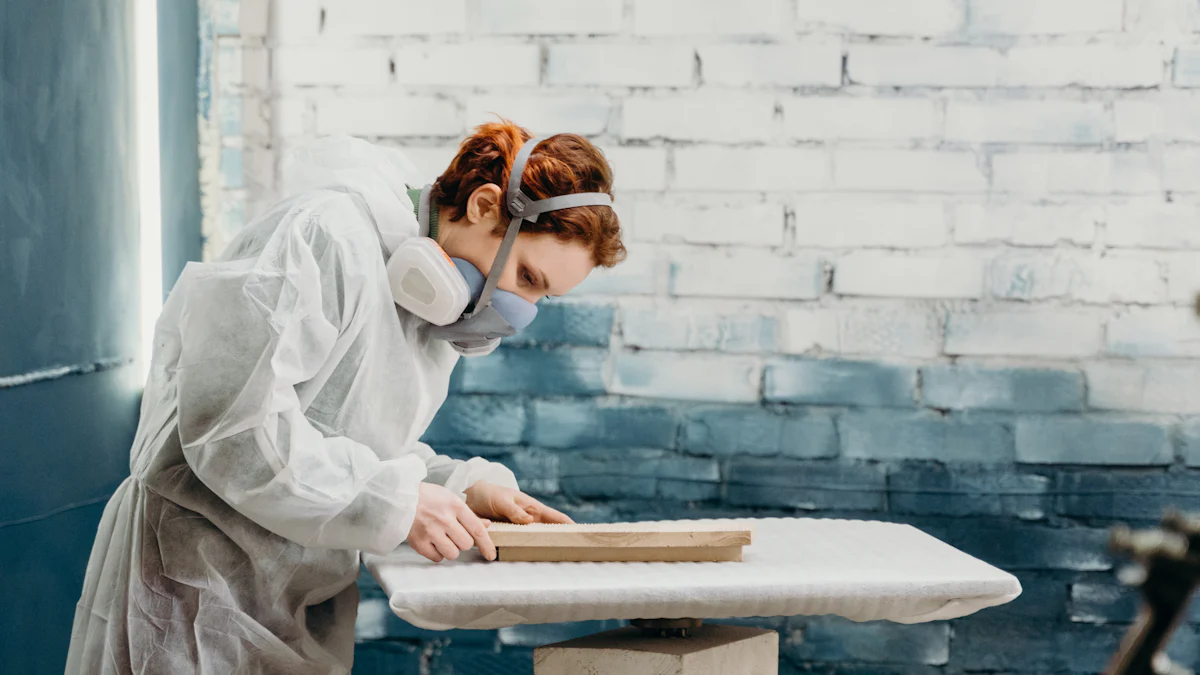
Silicon carbide coating on stainless steel plays a crucial role in industrial applications. Its exceptional properties, such as high hardness, superior wear resistance, and excellent thermal stability, make it indispensable for demanding environments. Industries rely on this coating to enhance the durability and performance of stainless steel components, especially in high-temperature or corrosive conditions. The development of advanced methods, including silicon carbide ceramic coating, has further expanded its applications. For those searching for silicon carbide ceramic coating near me, understanding its advantages compared to alternatives like silicon carbide ceramic coating vs ceramic coating becomes essential.
Key Takeaways
- Silicon carbide coatings significantly enhance the durability and performance of stainless steel, making them essential for industries facing extreme conditions.
- Chemical Vapor Deposition (CVD) offers high-quality, uniform coatings with excellent adhesion, ideal for high-performance applications despite its higher cost.
- Thermal spraying is a cost-effective method suitable for large surfaces, but it may result in lower adhesion and potential porosity in the coatings.
- TIG coating provides precise control over heat input, improving mechanical properties, but requires skilled operators to ensure consistent quality.
- Electrolytic coating is flexible for intricate geometries and offers a cost-effective alternative, though it may struggle with uniformity.
- Choosing the right coating method depends on specific application needs, budget constraints, and environmental conditions to optimize performance.
- Emerging techniques like overlaying technology show promise for future applications, enhancing surface properties while maintaining structural integrity.
Overview of Silicon Carbide Coating on Stainless Steel
Properties of Silicon Carbide
Hardness and Wear Resistance
Silicon carbide stands out for its exceptional hardness, ranking just below diamond on the Mohs scale. This property makes it highly resistant to wear and abrasion, even under extreme conditions. When applied as a coating, it significantly reduces surface degradation caused by friction or mechanical stress. Industries that rely on components exposed to aggressive environments benefit from this enhanced durability. For example, studies have shown that silicon carbide coatings can lower wear rates and extend the service life of materials, particularly in high-load applications.
Thermal and Chemical Stability
The thermal stability of silicon carbide allows it to withstand temperatures exceeding 1,000°C without losing its structural integrity. This makes it ideal for applications in high-temperature environments, such as furnaces or reactors. Additionally, its chemical stability ensures resistance to corrosive substances, including acids and alkalis. This dual stability protects stainless steel substrates from thermal damage and chemical corrosion, ensuring long-term performance. These properties make silicon carbide coatings indispensable for industries requiring reliable materials in harsh conditions.
Why Apply Silicon Carbide Coating on Stainless Steel?
Enhanced Durability and Corrosion Resistance
Applying silicon carbide coating on stainless steel enhances the material’s durability by creating a robust barrier against physical and chemical damage. The coating prevents surface wear and minimizes the risk of corrosion, even in environments with high humidity or exposure to corrosive agents. This improvement in corrosion resistance is particularly valuable for industries such as marine engineering and chemical processing, where stainless steel components face constant exposure to harsh elements.
Suitability for High-Temperature and Harsh Environments
Silicon carbide coatings enable stainless steel to perform effectively in extreme environments. The coating’s ability to maintain its properties at elevated temperatures ensures reliable operation in applications like aerospace, power generation, and semiconductor manufacturing. Furthermore, its resistance to oxidation and thermal shock makes it a preferred choice for components subjected to rapid temperature changes. By applying this coating, manufacturers can optimize the performance and lifespan of stainless steel in demanding conditions.
Methods for Applying Silicon Carbide Coating on Stainless Steel
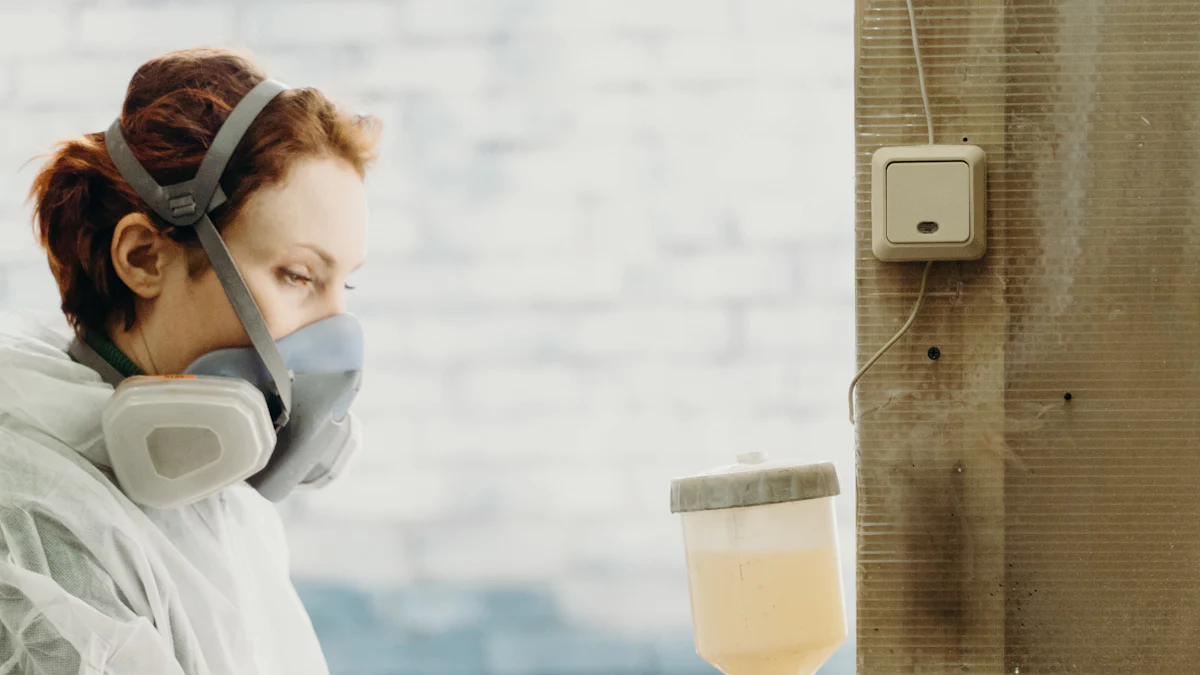
Chemical Vapor Deposition (CVD)
Process Overview
Chemical Vapor Deposition (CVD) involves the use of vaporized chemical precursors that react on or near the surface of stainless steel to form a solid silicon carbide coating. The process typically occurs in a controlled environment, ranging from high vacuum to atmospheric pressure. The chemical reaction deposits a uniform layer of silicon carbide, ensuring precise coverage. This method is widely used in industries requiring high-performance coatings, such as semiconductor manufacturing and aerospace.
Advantages: Uniform Coating, High Adhesion
CVD provides exceptional uniformity in coating thickness, making it ideal for applications demanding precision. The chemical bonding between the silicon carbide and the stainless steel substrate ensures strong adhesion, which enhances the durability of the coating. This method also allows for the deposition of coatings with excellent mechanical and thermal properties, suitable for extreme environments.
Limitations: High Cost, Complex Setup
The CVD process requires specialized equipment and precise control of temperature and pressure, leading to higher operational costs. The complexity of the setup makes it less accessible for smaller-scale applications. Additionally, the process may involve hazardous chemicals, necessitating strict safety measures.
Physical Vapor Deposition (PVD)
Process Overview
Physical Vapor Deposition (PVD) involves the physical transfer of material from a solid source to the stainless steel substrate. The process occurs in a vacuum chamber, where the material transitions from a condensed phase to a gas phase and then back to a condensed phase as a thin film. PVD offers a high degree of control over the coating’s composition and thickness, making it suitable for precision applications.
Advantages: Precise Control, Environmentally Friendly
PVD provides unparalleled control over the coating process, allowing for the creation of thin, uniform layers with tailored properties. This method is considered environmentally friendly, as it generates minimal waste and avoids the use of harmful chemicals. Its precision makes it a preferred choice for industries like electronics and optics.
Limitations: Limited Coating Thickness, Requires Vacuum
The PVD process is limited in its ability to produce thick coatings, which may restrict its use in certain applications. The requirement for a vacuum environment adds to the complexity and cost of the process. These factors make PVD more suitable for specialized applications rather than large-scale industrial use.
Thermal Spraying
Process Overview
Thermal spraying involves the projection of molten or semi-molten silicon carbide particles onto the stainless steel surface. A high-temperature heat source, such as a plasma or flame, melts the coating material, which is then sprayed onto the substrate. This method is commonly used for coating large surfaces and components.
Advantages: Cost-Effective, Suitable for Large Surfaces
Thermal spraying is a cost-effective solution for applying silicon carbide coating on stainless steel, particularly for large-scale projects. The process is versatile and can be adapted to coat complex geometries. Its relatively low operational costs make it an attractive option for industries like construction and automotive.
Limitations: Lower Adhesion, Potential Porosity
The adhesion of the coating to the substrate may be lower compared to other methods like CVD or PVD. Additionally, the process can result in coatings with porosity, which may affect their performance in highly demanding environments. Proper surface preparation and process optimization are essential to mitigate these issues.
TIG Coating Technique
Process Overview
The TIG (Tungsten Inert Gas) coating technique applies silicon carbide coating on stainless steel by utilizing a tungsten electrode to generate heat. This heat melts the silicon carbide material, which then bonds to the stainless steel surface. The process occurs in an inert gas environment, such as argon, to prevent oxidation during application. Operators can control the heat input precisely, ensuring the coating adheres effectively to the substrate. This method is particularly suitable for applications requiring enhanced mechanical properties and durability.
Advantages: Control Over Heat Input, Improved Mechanical Properties
TIG coating offers precise control over the heat input, allowing operators to tailor the coating process to specific requirements. This control minimizes thermal distortion of the stainless steel substrate, preserving its structural integrity. The technique also enhances the mechanical properties of the coated surface, such as wear resistance and hardness. Industries that demand robust and reliable components, such as aerospace and automotive, benefit significantly from this method.
Limitations: Requires Skilled Operation, Potential for Uneven Coating
The TIG coating technique demands a high level of skill and expertise from operators. Improper handling can lead to uneven coating thickness, which may compromise the performance of the silicon carbide layer. Additionally, the process can be time-consuming for large-scale applications, making it less efficient for mass production. Despite these challenges, TIG coating remains a valuable option for specialized applications requiring precision and durability.
Electrolytic Coating
Process Overview
Electrolytic coating involves immersing the stainless steel substrate in an electrolyte solution containing silicon carbide particles. An electric current passes through the solution, causing the silicon carbide particles to deposit onto the stainless steel surface. This method provides an alternative approach to applying silicon carbide coating on stainless steel, particularly for components with intricate geometries or specific application needs.
Advantages: Alternative Method, Suitable for Specific Applications
Electrolytic coating offers flexibility in coating complex shapes and surfaces. The process can be customized to achieve specific coating thicknesses, making it suitable for niche applications. It also provides a cost-effective alternative to more complex methods like CVD or PVD. Industries such as electronics and medical devices often utilize this technique for its adaptability and precision.
Limitations: Limited Coating Uniformity, Requires Precise Control
Achieving uniform coating thickness with the electrolytic method can be challenging. Variations in current density or particle distribution may result in uneven coatings. The process also requires precise control of parameters, such as voltage and electrolyte composition, to ensure optimal results. These limitations make it essential to carefully monitor and adjust the process for consistent performance.
Overlaying Technology
Process Overview
Overlaying technology represents an innovative approach to applying silicon carbide coatings. This method involves forming a composite layer of silicon carbide and metal on the stainless steel surface. The process enhances the surface properties of the substrate, creating a durable and wear-resistant layer. Overlaying technology is still under development but shows promise for advancing coating techniques.
Advantages: Enhances Surface Properties, Innovative Approach
Overlaying technology significantly improves the surface properties of stainless steel, including hardness, wear resistance, and thermal stability. Its innovative nature allows for the creation of advanced coatings tailored to specific industrial needs. This method holds potential for applications in emerging fields, such as renewable energy and advanced manufacturing.
Limitations: Still Under Development, Limited Industrial Adoption
As a relatively new technique, overlaying technology faces challenges in widespread industrial adoption. The lack of standardized processes and equipment limits its scalability. Further research and development are necessary to refine the method and expand its applications. Despite these limitations, overlaying technology offers exciting possibilities for the future of silicon carbide coatings.
Comparison of Coating Methods
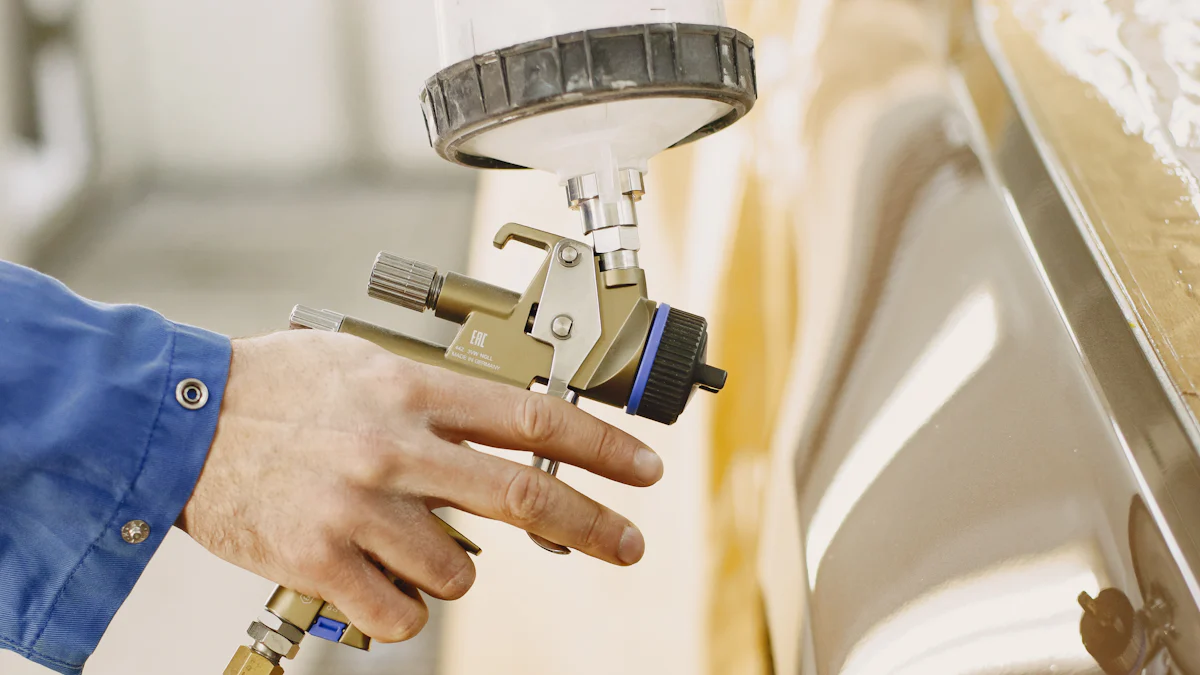
Key Factors for Comparison
Coating Quality and Durability
The quality and durability of a coating depend on its adhesion, uniformity, and resistance to wear and corrosion. Chemical Vapor Deposition (CVD) produces dense, high-purity coatings with excellent structural integrity. This method ensures superior adhesion and uniformity, making it ideal for high-performance applications. Physical Vapor Deposition (PVD) delivers precise, thin coatings with excellent hardness and abrasion resistance. However, its limited thickness may reduce durability in some cases. Thermal spraying, while cost-effective, often results in coatings with weaker adhesion and potential porosity, which can compromise long-term performance. TIG coating enhances mechanical properties and wear resistance but requires skilled operation to achieve consistent quality. Electrolytic coating offers flexibility for intricate geometries but struggles with uniformity. Overlaying technology, though innovative, remains under development and lacks widespread industrial adoption.
Cost and Complexity
Cost and complexity vary significantly across methods. CVD involves expensive equipment and a complex setup, making it suitable for industries with high budgets and precision requirements. PVD, while less costly than CVD, still requires a vacuum environment, adding to operational expenses. Thermal spraying stands out as a cost-effective option, particularly for large-scale projects. TIG coating demands skilled labor, which increases operational costs. Electrolytic coating provides a more affordable alternative but requires precise control to ensure quality. Overlaying technology, being in its early stages, involves high research and development costs, limiting its current affordability.
Suitability for Specific Applications
Each method offers unique advantages tailored to specific applications. CVD excels in high-temperature and high-performance environments, such as aerospace and semiconductor manufacturing. PVD is ideal for precision components in electronics and optics. Thermal spraying works well for large surfaces in construction and automotive industries. TIG coating suits applications requiring enhanced mechanical properties, such as aerospace and automotive parts. Electrolytic coating fits niche applications, including medical devices and electronics. Overlaying technology shows promise for emerging fields like renewable energy but requires further development for broader use.
Summary Table of Methods
Method | Advantages | Disadvantages | Best Use Cases |
---|---|---|---|
CVD | High-quality coating, excellent adhesion | High cost, complex setup | High-performance applications |
PVD | Precise, eco-friendly, thin coatings | Limited thickness, requires vacuum | Precision components |
Thermal Spraying | Cost-effective, suitable for large surfaces | Lower adhesion, potential porosity | Large-scale projects |
TIG Coating | Controlled heat input, improved properties | Requires skill, potential uneven coating | Mechanical property enhancement |
Electrolytic Coating | Alternative method, flexible for geometries | Limited uniformity, requires precise control | Niche applications |
Overlaying Technology | Innovative, enhances surface properties | Limited adoption, under development | Promising for future use |
This table highlights the strengths and limitations of each method, helping industries select the most appropriate technique for their needs. For instance, silicon carbide coating on stainless steel applied via CVD ensures exceptional durability and performance in extreme environments. Meanwhile, thermal spraying offers a practical solution for large-scale projects where cost efficiency is critical.
Selecting the right method for applying silicon carbide coating on stainless steel is crucial for achieving optimal performance and durability. Each method offers unique advantages tailored to specific industrial needs:
- CVD ensures high-quality coatings with superior adhesion, making it ideal for precision and high-performance applications.
- Thermal spraying provides a cost-effective solution for large-scale projects.
- TIG coating enhances mechanical properties, suitable for applications requiring durability under stress.
The evolving technology behind these methods continues to expand their potential. Industries can leverage these advancements to meet the demands of harsh environments and improve operational efficiency.
FAQ
What are the benefits of applying silicon carbide coatings on stainless steel?
Silicon carbide coatings enhance the durability and performance of stainless steel. They provide exceptional hardness, superior wear resistance, and excellent thermal and chemical stability. These coatings protect against corrosion, reduce surface wear, and extend the lifespan of components in harsh environments. Industries such as aerospace, marine engineering, and semiconductor manufacturing rely on these coatings for their ability to withstand extreme conditions.
How does the CVD method compare to other coating techniques?
The Chemical Vapor Deposition (CVD) method stands out for its ability to produce high-quality, uniform coatings with excellent adhesion. It offers superior durability and precision, making it ideal for high-performance applications. Compared to methods like Thermal Spraying or Electrolytic Coating, CVD provides denser and more reliable coatings. However, it requires a complex setup and higher costs, which may limit its use in large-scale or budget-sensitive projects.
Why is surface preparation important before applying silicon carbide coatings?
Surface preparation ensures proper adhesion of the silicon carbide coating to the stainless steel substrate. Techniques like SiC abrasive jet erosion optimize surface roughness, creating a suitable base for the coating. Without adequate preparation, the coating may not bond effectively, leading to reduced durability and performance. Proper preparation is crucial for achieving consistent and long-lasting results.
What industries benefit the most from silicon carbide coatings?
Industries that operate in extreme environments benefit significantly from silicon carbide coatings. These include aerospace, where components face high temperatures and mechanical stress, and the semiconductor industry, which demands precision and chemical stability. Marine engineering and chemical processing also rely on these coatings for their corrosion resistance and durability in harsh conditions.
What makes TIG coating unique among other methods?
The TIG (Tungsten Inert Gas) coating technique offers precise control over heat input during the application process. This control minimizes thermal distortion and enhances the mechanical properties of the coated surface. TIG coating is particularly suitable for applications requiring improved wear resistance and durability, such as aerospace and automotive components. However, it demands skilled operation to ensure consistent quality.
Can silicon carbide coatings improve energy efficiency?
Yes, silicon carbide coatings can improve energy efficiency by reducing friction and wear in mechanical systems. Their low friction coefficient minimizes energy loss due to surface interactions, while their thermal stability ensures efficient heat management. These properties make them valuable for applications in power generation, renewable energy, and advanced manufacturing.
What are the performance characteristics of CVD silicon carbide coatings?
CVD silicon carbide coatings exhibit exceptional high-temperature stability, oxidation resistance, and chemical compatibility. They also offer high hardness, superior wear resistance, and good thermal conductivity. These properties make them ideal for demanding applications in electronics, optics, aerospace, and the chemical industry. Their ability to maintain performance under extreme conditions sets them apart from other coating types.
How does overlaying technology differ from traditional coating methods?
Overlaying technology combines silicon carbide with metal to form a composite layer on the stainless steel surface. This innovative approach enhances surface properties, such as hardness and wear resistance, while maintaining the substrate’s structural integrity. Unlike traditional methods, overlaying technology focuses on creating advanced coatings tailored to specific industrial needs. Although still under development, it holds promise for future applications in renewable energy and advanced manufacturing.
Are silicon carbide coatings environmentally friendly?
Certain methods, such as Physical Vapor Deposition (PVD), are considered environmentally friendly due to their minimal waste generation and avoidance of harmful chemicals. Silicon carbide coatings also contribute to sustainability by extending the lifespan of components, reducing the need for frequent replacements. This durability minimizes resource consumption and waste, aligning with eco-friendly practices.
How should industries choose the right coating method?
Industries should consider factors such as application requirements, budget, and environmental conditions when selecting a coating method. For high-performance needs, CVD offers unmatched quality and durability. Thermal spraying provides a cost-effective solution for large-scale projects, while TIG coating suits applications requiring enhanced mechanical properties. Emerging methods like overlaying technology may be ideal for innovative and future-focused industries.