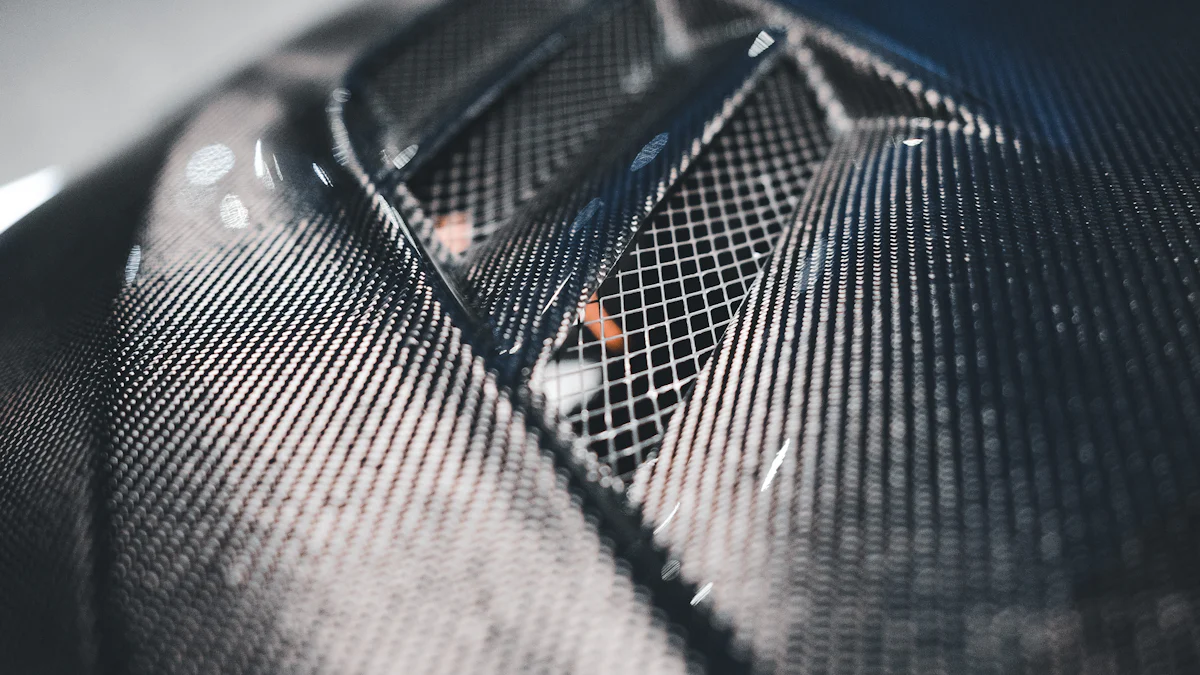
Carbon carbon silicon carbide composites represent a breakthrough in materials science. These advanced materials combine carbon carbon compounds with silicon carbide, creating a composite that excels in strength, thermal stability, and lightweight properties. To understand what is carbon composites, it’s essential to recognize their role in industries like aerospace and automotive, which rely on these composites for their exceptional performance. For instance, the aerospace sector dominated 63.2% of the market share in 2024, driven by the demand for lightweight materials. Continuous fibers, known for their mechanical properties, held 60.6% of the market share the same year. These composites also outperform traditional carbon fiber carbon plate materials, offering superior oxidation resistance and durability.
Key Takeaways
- C/C-SiC composites combine carbon fibers with a silicon carbide matrix, resulting in materials that excel in strength, thermal stability, and lightweight properties, making them ideal for high-performance applications.
- These composites are particularly valuable in aerospace and automotive industries due to their ability to withstand extreme temperatures and mechanical stress, ensuring reliability in critical components like rocket nozzles and brake systems.
- Recent advancements in manufacturing techniques, such as additive manufacturing and reactive melt infiltration, are enhancing the production efficiency and accessibility of C/C-SiC composites, paving the way for broader applications across various sectors.
What Is Carbon Composites and How Do They Relate to C/C-SiC?
Definition and Composition of Carbon Carbon Silicon Carbide Composites
When discussing what is carbon composites, it’s essential to understand the unique structure of carbon carbon silicon carbide (C/C-SiC) composites. These materials belong to a new class of structural composites that combine carbon fiber reinforcements with a silicon carbide matrix. This combination creates a material with exceptional properties, including high strength, low density, and excellent thermal stability.
C/C-SiC composites are designed to perform in extreme conditions. Their low thermal expansion and high thermal shock resistance make them ideal for applications like rocket nozzles and thermal protection panels. The stiffness of the carbon fibers and the silicon carbide matrix is comparable, ensuring uniform stress distribution. This balance enhances the composite’s mechanical performance, even at high temperatures.
Additionally, these composites exhibit good tribological behavior, meaning they perform well in applications requiring low friction and wear resistance. Industries use them in brake disks, clutches, and furnace charging devices due to these advantages.
Key Differences Between C/C-SiC and Other Carbon Composites
C/C-SiC composites stand apart from traditional carbon composites due to their ceramic matrix. This matrix significantly enhances their stiffness and thermal stability, making them suitable for high-temperature environments. For instance, while standard carbon composites may degrade above 450°C, C/C-SiC composites maintain their mechanical properties even in oxidizing atmospheres.
Another key distinction lies in their damage tolerance. The fiber/matrix bonding in C/C-SiC composites allows for tailored performance, offering better thermal stability and durability. Traditional carbon composites, on the other hand, lack this level of customization and are more prone to oxidation. This makes C/C-SiC composites a preferred choice for demanding applications in aerospace and industrial sectors.
Understanding what is carbon composites and how C/C-SiC differs highlights the advancements in materials science. These composites not only outperform traditional options but also open new possibilities for high-performance applications.
Properties and Characteristics of Carbon Carbon Silicon Carbide Composites
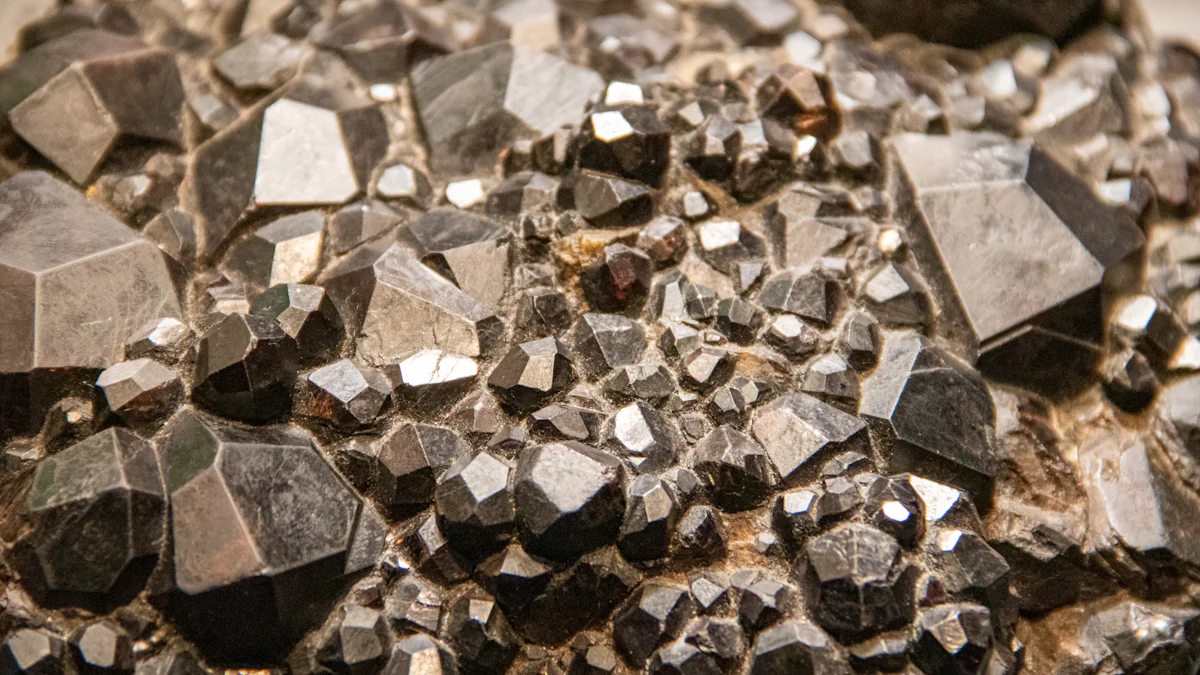
High Strength and Fracture Toughness
I find the mechanical properties of carbon carbon silicon carbide composites fascinating. These materials offer a unique balance of strength and toughness. While their flexural strength and Young’s modulus are lower than traditional ceramics, they compensate with greater strain to rupture. This means they fail less catastrophically, which is critical for applications requiring uniform load distribution. The tensile strength of these composites depends on the thickness of the interface layer. A thicker interface enhances tensile strength, but a higher matrix volume fraction can reduce both strength and toughness. This interplay between interphase properties and mechanical performance makes these composites highly adaptable for demanding environments.
Thermal Stability and Oxidation Resistance
Thermal stability is one of the standout features of carbon carbon silicon carbide composites. I’ve observed that their carbon fibers can endure temperatures exceeding 2000°C, making them ideal for extreme heat applications. However, in oxidizing environments above 450°C, they require external oxidation protection. The anisotropic thermal expansion of these composites complicates this protection, as it can lead to cracks in coatings at high temperatures. Despite these challenges, their ability to maintain structural integrity under intense heat sets them apart from other advanced materials.
Lightweight and Tribological Advantages
The lightweight nature of these composites is another reason they excel in high-performance applications. Their low density reduces overall system weight, which is crucial in aerospace and automotive industries. Additionally, their tribological properties, such as high friction coefficients and excellent wear resistance, make them ideal for braking systems. I’ve seen how their superior wear resistance, achieved through liquid silicon infiltration, enhances durability in brakes and clutches for high-speed vehicles and trains. These properties ensure reliable performance under extreme mechanical stress.
Applications of Carbon Carbon Silicon Carbide Composites
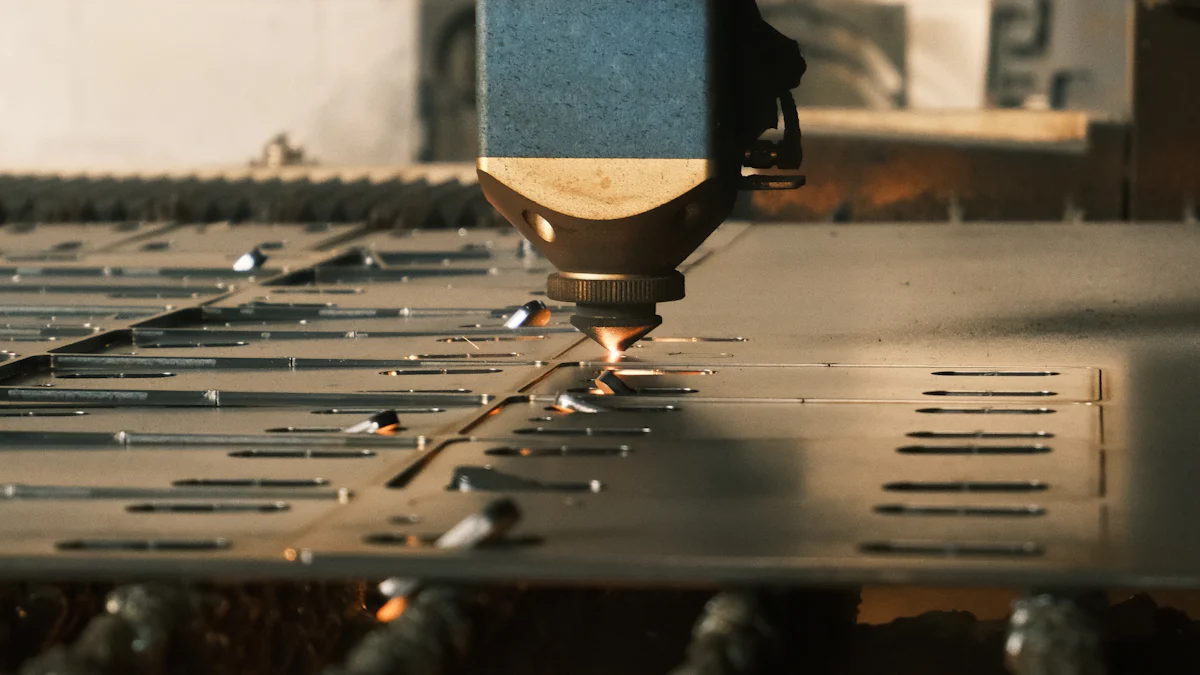
Aerospace and Defense Applications
I’ve seen how carbon carbon silicon carbide composites revolutionize aerospace and defense industries. Their ability to withstand extreme temperatures makes them indispensable in high-performance applications. For example, these composites are used in aerospace structures, high-temperature trim, and faceplates. They also play a critical role in internal combustion engines and turbines.
Application Area | Description |
---|---|
Aerospace Structures | Used in various aerospace components due to high-temperature resistance. |
High-Temperature Trim | Suitable for components exposed to extreme temperatures. |
Faceplates | Employed in protective applications within aerospace systems. |
Internal Combustion Engines | Utilized in engine components requiring high strength and lightweight. |
Turbines | Applied in turbine components for enhanced performance. |
In military jet engines, C/C-SiC composites are essential for components like flame-holders and exhaust cones. I’ve noticed their use in outer flaps of the S-M88-2 engine, where they reduce weight by 50%. These materials also enhance thrust direction in rocket motors through vanes and nozzles.
Automotive and Motorsports Uses
In motorsports, performance depends on advanced materials. I’ve observed how C/C-SiC composites improve braking and clutch systems in high-speed vehicles. Their superior tribological properties, such as high friction coefficients and wear resistance, make them ideal for these applications. These composites ensure reliable performance under extreme mechanical stress, which is critical for competitive racing.
Industrial and Energy Sector Applications
The industrial and energy sectors benefit greatly from the unique properties of C/C-SiC composites. Their thermal resistance and damage tolerance enhance operational safety in nuclear reactors. These materials also resist radiation, enabling higher operational temperatures. I’ve read that they could potentially double electricity generation in fusion reactors, making them more commercially viable.
Application Area | Benefits | Market Trends |
---|---|---|
Nuclear Reactors | Enhances efficiency and safety in energy production systems | Critical for the development of reactors and energy-efficient systems |
High-Temperature Gas Turbines | Suitable for high-temperature applications, improving thermal efficiency | Growing demand in automotive for lighter, fuel-efficient materials |
Sustainability | Offers long-lasting solutions aligned with environmental concerns | Rapid R&D for cost-efficient production methods, increasing market attractiveness |
These composites also find applications in high-temperature gas turbines, where they improve thermal efficiency. Their alignment with sustainability goals makes them a preferred choice for industries focusing on long-term solutions.
Manufacturing Processes and Advancements
Overview of Production Techniques
I’ve always found the manufacturing of carbon carbon silicon carbide composites fascinating due to its complexity and precision. These composites are produced using advanced techniques that ensure their exceptional properties. Common methods include chemical vapor infiltration (CVI) and polymer infiltration and pyrolysis (PIP). While effective, these processes are time-intensive and require meticulous control.
Other techniques, such as liquid silicon infiltration (LSI), involve infusing liquid silicon into a carbon matrix to form the composite. Precursor infiltration and pyrolysis (PIP) use a polymer precursor that undergoes pyrolysis to create the final material. Slurry infiltration combined with hot pressing (SI-HP) enhances the composite’s mechanical properties.
Technique | Description |
---|---|
Liquid Silicon Infiltration (LSI) | Involves infiltrating liquid silicon into a carbon matrix. |
Precursor Infiltration and Pyrolysis (PIP) | Uses a polymer precursor followed by pyrolysis to form the composite. |
Slurry Infiltration and Hot Pressing (SI-HP) | Combines slurry infiltration with hot pressing for better properties. |
Chemical Vapor Infiltration (CVI) | Gaseous precursors infiltrate a carbon matrix to form silicon carbide. |
Each method offers unique advantages, allowing manufacturers to tailor composites for specific applications.
Role of Silicon Carbide in Enhancing Properties
Silicon carbide plays a pivotal role in improving the performance of these composites. I’ve noticed how its addition significantly boosts flexural strength and durability. For instance, the S-C/C-SiC composite achieves a flexural strength of 325 MPa, which is 89% higher than traditional carbon carbon composites. Its density, at 1.84 g/cm³, remains relatively low compared to other materials, ensuring lightweight properties.
This balance of strength and density makes C/C-SiC composites ideal for high-performance applications. Silicon carbide also enhances thermal stability and oxidation resistance, enabling these materials to perform reliably in extreme environments. I’ve seen how this combination of properties sets them apart from other advanced materials.
Innovations in Manufacturing Technology
Recent advancements in manufacturing technology have revolutionized the production of C/C-SiC composites. One innovative approach combines additive manufacturing with reactive melt infiltration. This process involves impregnating carbon fiber tows with a thermoplastic polymer, followed by layer-by-layer deposition. After pyrolysis, the matrix converts to carbon, and reactive melt infiltration with silicon forms dense C/C-SiC composites.
This method offers several advantages. It reduces processing time, minimizes material waste, and improves design flexibility. I’ve also observed the development of sandwich-structured composites using electromagnetic-coupling chemical vapor infiltration. These innovations enhance fabrication efficiency and lower costs, making C/C-SiC composites more accessible for various industries.
Challenges and Limitations of C/C-SiC Composites
Oxidation Resistance and Environmental Concerns
I’ve observed that oxidation resistance remains a critical challenge for carbon carbon silicon carbide composites. These materials degrade under oxidative conditions, especially beyond 450°C. In such environments, silica forms on the surface but can volatilize at intermediate oxygen partial pressures. This compromises the material’s structural integrity. The carbon layer at the fiber/matrix interface is particularly sensitive to oxidation, which complicates the composite’s behavior in dynamic conditions.
To address these issues, manufacturers often apply external oxidation protection. Higher heat treatment temperatures and high modulus carbon fibers can improve resistance. However, even sophisticated coatings only mitigate degradation within specific temperature ranges. They cannot entirely prevent oxidation under fluctuating environmental conditions. This limitation requires careful consideration when deploying these composites in high-temperature applications.
Cost and Scalability Challenges
Scaling up the production of C/C-SiC composites presents significant cost challenges. I’ve noticed that achieving uniform fiber distribution and alignment is a complex task. Ensuring strong interfacial bonding between fibers and the matrix adds another layer of difficulty. Defects like porosity, delamination, and microcracks often arise during fabrication, further complicating the process.
Conventional methods, such as chemical vapor infiltration (CVI) and polymer infiltration and pyrolysis (PIP), involve multi-step processes that are both time- and cost-intensive. These techniques require precise control over processing parameters to achieve the desired microstructure and properties. While these composites offer unmatched performance in extreme environments, the high production costs have limited their widespread adoption across industries.
Thermal Expansion and Compatibility Issues
Thermal expansion poses another challenge for C/C-SiC composites. I’ve seen how the anisotropic nature of these materials can lead to mismatches in thermal expansion when integrated with other components. This mismatch creates stress at the interfaces, potentially causing cracks or delamination during thermal cycling.
Compatibility issues also arise when these composites are used in multi-material systems. The differences in thermal behavior between C/C-SiC and adjoining materials require careful design considerations. Engineers must account for these factors to ensure the long-term reliability of the composite in demanding applications.
Carbon carbon silicon carbide composites represent a significant leap in advanced materials science. Their unique properties include:
- Low density and thermal expansion.
- High strength and thermal shock resistance.
- Excellent oxidation resistance and mechanical stability at high temperatures.
These qualities make them indispensable for applications like rocket nozzles, thermal protection panels, and brake discs.
I’ve observed exciting advancements in this field. Automation and AI integration are enhancing production efficiency. The demand for lightweight, high-strength materials continues to grow, especially in aerospace and automotive industries. Innovative technologies are also improving functionality, paving the way for broader applications. The future of C/C-SiC composites looks incredibly promising.
FAQ
What makes C/C-SiC composites unique compared to traditional materials?
C/C-SiC composites combine carbon fibers with a silicon carbide matrix. This blend offers high strength, lightweight properties, and exceptional thermal stability, outperforming traditional carbon composites in extreme environments.
How are C/C-SiC composites used in aerospace applications?
I’ve seen these composites used in rocket nozzles, thermal protection panels, and jet engine components. Their ability to withstand extreme heat makes them indispensable in aerospace engineering.
Why is silicon carbide important in these composites?
Silicon carbide enhances oxidation resistance, thermal stability, and mechanical strength. It ensures the composite performs reliably under high temperatures and mechanical stress, making it ideal for demanding applications.