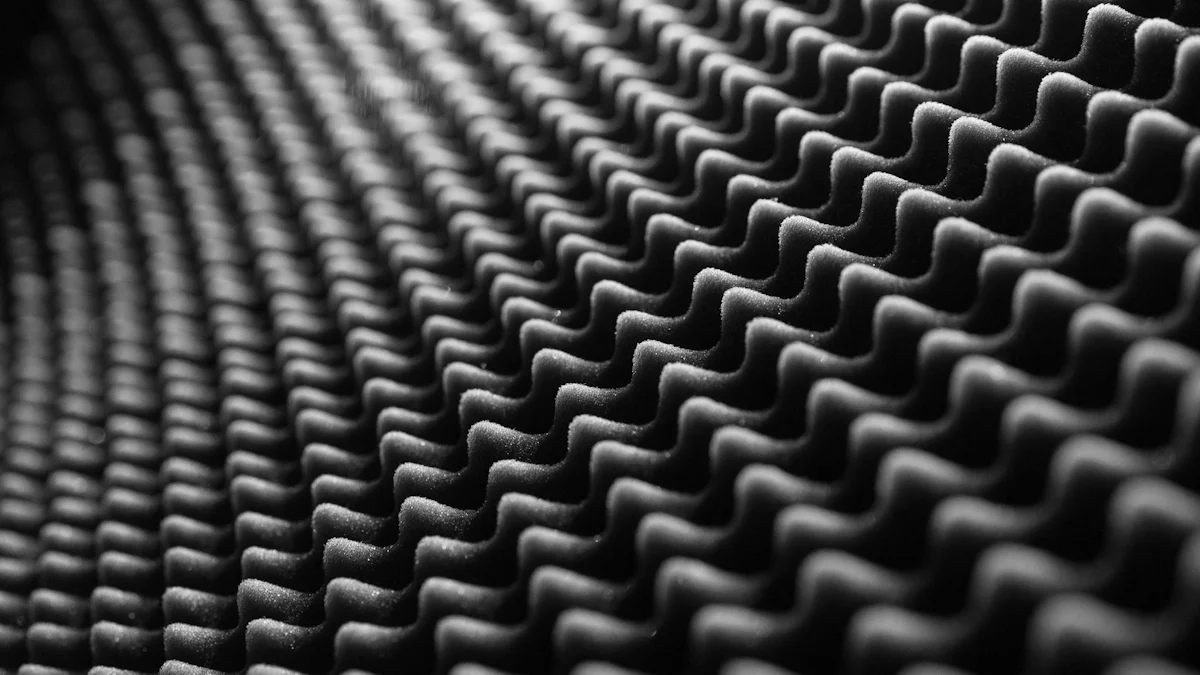
Carbon carbon composites are advanced materials known for their exceptional strength, lightweight nature, and thermal stability. These materials consist of carbon fiber carbon plate reinforced with a carbon matrix, which provides superior performance in demanding environments. For instance, they exhibit a density of 1.55 g/cm³, making them significantly lighter than aluminum or steel. Their high Young’s modulus of 90.5 GPa ensures excellent rigidity, while a low thermal expansion coefficient of 2 × 10⁻⁶°C⁻¹ enhances dimensional stability under heat.
Selecting the right material for an application requires understanding the trade-offs between carbon carbon composites and other options. While carbon carbon compounds excel in aerospace and defense due to their durability, other composites may offer advantages like cost efficiency or broader versatility. Comparing these materials helps engineers and designers make informed decisions tailored to specific needs, particularly when considering the unique properties of carbon fiber carbon plate in various applications.
Key Takeaways
- Carbon carbon composites excel in strength and thermal stability, making them ideal for high-performance applications in aerospace and defense.
- Other composites offer cost efficiency and versatility, with simpler manufacturing processes and a broader range of applications across various industries.
- While other composites are lighter and easier to produce, they often lack the durability and high-temperature resistance that carbon carbon composites provide.
- Environmental considerations are crucial; some other composites are recyclable, but many are non-biodegradable, posing long-term waste challenges.
- Engineers must carefully evaluate the specific needs of their projects, balancing the cost and versatility of other composites against the superior performance of carbon carbon composites.
Advantages of Other Composites Compared to Carbon Carbon Composites
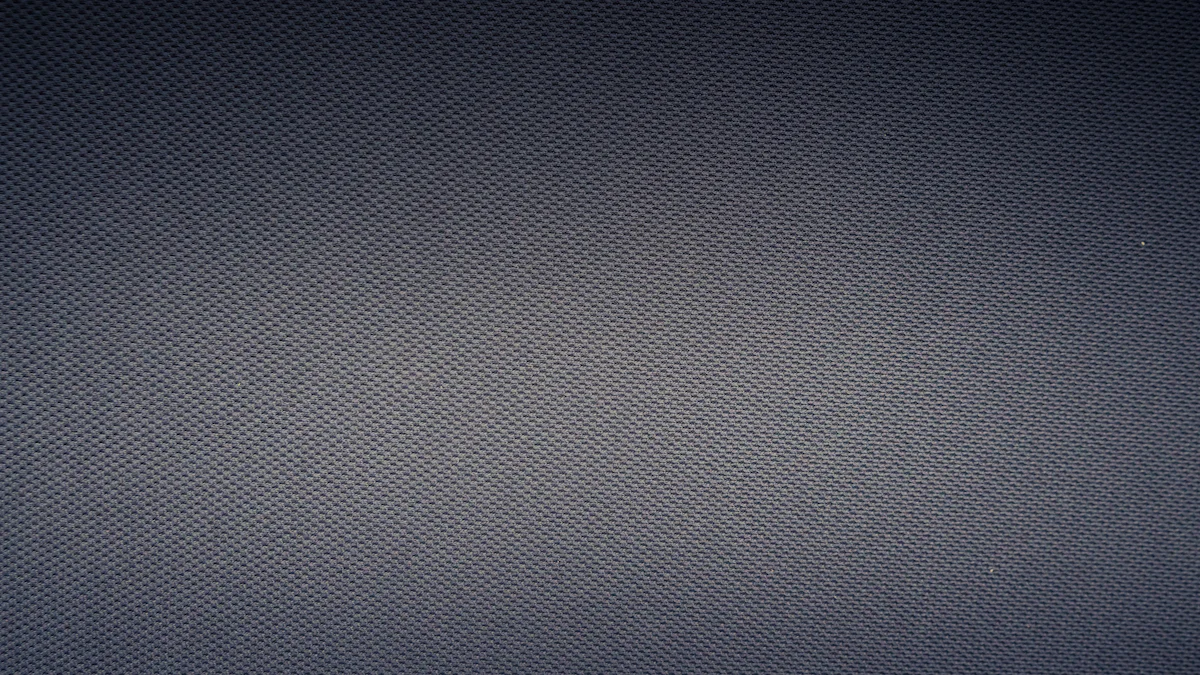
Cost Efficiency
Lower Production Costs
Other composites often have lower production costs compared to carbon carbon composites. This cost advantage stems from simpler manufacturing techniques and the use of less expensive raw materials. For instance, thermoset and thermoplastic resins, commonly used in other composites, are more affordable than the carbon matrix required for carbon carbon composites. Additionally, the manufacturing process for other composites, such as hand layup or automated fiber placement, involves fewer steps, reducing labor and energy expenses.
Availability of Raw Materials
The raw materials for other composites are widely available, making them easier to source. Thermoset and thermoplastic resins, along with reinforcing fibers like glass or aramid, are produced in large quantities globally. This accessibility ensures a steady supply chain, which is crucial for industries requiring high-volume production. In contrast, the specialized materials for carbon carbon composites often face supply constraints, increasing their overall cost.
Versatility in Applications
Broader Application Range
Other composites offer a broader range of applications due to their diverse material properties. Industries such as construction, sports, and consumer goods benefit from their adaptability. For example, glass fiber composites are widely used in wind turbine blades, while polymer composites find applications in medical devices. This versatility makes them suitable for both high-performance and everyday applications.
Customization for Specific Needs
Manufacturers can tailor other composites to meet specific requirements. By adjusting the resin type, fiber orientation, or reinforcement material, they can create composites with unique properties. This customization allows engineers to design materials optimized for strength, flexibility, or thermal resistance, depending on the application. Such flexibility is harder to achieve with carbon carbon composites, which are primarily designed for high-performance environments.
Ease of Manufacturing
Simpler Manufacturing Processes
The manufacturing processes for other composites are generally simpler than those for carbon carbon composites. Techniques like hand layup and automated fiber placement require less specialized equipment and expertise. In contrast, carbon carbon composites involve complex steps such as impregnation and pyrolysis, which demand precise control and longer production times.
Manufacturing Process | Carbon-Carbon Composites | Other Composites |
---|---|---|
Matrix Material | Carbon matrix | Thermoset/Thermoplastic resins |
Key Techniques | Impregnation, Pyrolysis | Hand layup, Automated Fiber Placement |
Complexity | More complex | Less complex |
Reduced Complexity
The reduced complexity of other composites’ manufacturing processes translates to faster production cycles and lower costs. For example, thermoplastic composites can be molded and cured in a single step, streamlining production. This simplicity makes them an attractive choice for industries prioritizing efficiency and scalability.
Environmental Considerations
Recyclability of Certain Composites
Many composites, particularly polymer-based ones, offer recyclability advantages over carbon carbon composites. Thermoplastic composites, for instance, can be melted and reformed, allowing manufacturers to reuse materials in new products. This capability reduces waste and supports sustainable practices. Glass fiber composites also exhibit partial recyclability, as the fibers can be recovered and repurposed. These features make other composites more appealing for industries prioritizing environmental responsibility. In contrast, the recycling process for carbon carbon composites is more complex due to their high-temperature manufacturing and specialized materials.
Lower Energy Requirements
Producing other composites often requires less energy compared to carbon carbon composites. Manufacturing thermoset or thermoplastic composites involves lower processing temperatures and shorter production cycles. For example, thermoplastic composites can be molded and cured in a single step, minimizing energy consumption. This efficiency reduces the environmental footprint of production. Carbon carbon composites, on the other hand, demand energy-intensive processes like pyrolysis, which increase their overall environmental impact.
Weight Considerations
Lightweight Properties in Polymer Composites
Polymer composites are significantly lighter than carbon carbon composites, making them ideal for weight-sensitive applications. For instance, polymer composites can be up to 75% lighter than steel and 25% lighter than aluminum. This weight advantage enhances fuel efficiency and performance in industries like aerospace and automotive. The reduced weight also simplifies handling and installation, further increasing their appeal.
Material Type | Weight Comparison |
---|---|
Polymer Composites | Up to 75% lighter than steel |
Up to 25% lighter than aluminum | |
Carbon Carbon Composites | Heavier than polymer composites |
Advantages in Aerospace and Automotive
The lightweight nature of polymer composites provides significant benefits in aerospace and automotive sectors. Aircraft and spacecraft manufacturers use these materials to reduce fuel consumption and improve payload capacity. In automotive design, lighter materials contribute to better mileage and lower emissions. While carbon carbon composites also find use in these industries, their heavier weight limits their application in scenarios where extreme weight reduction is critical.
Disadvantages of Other Composites Compared to Carbon Carbon Composites
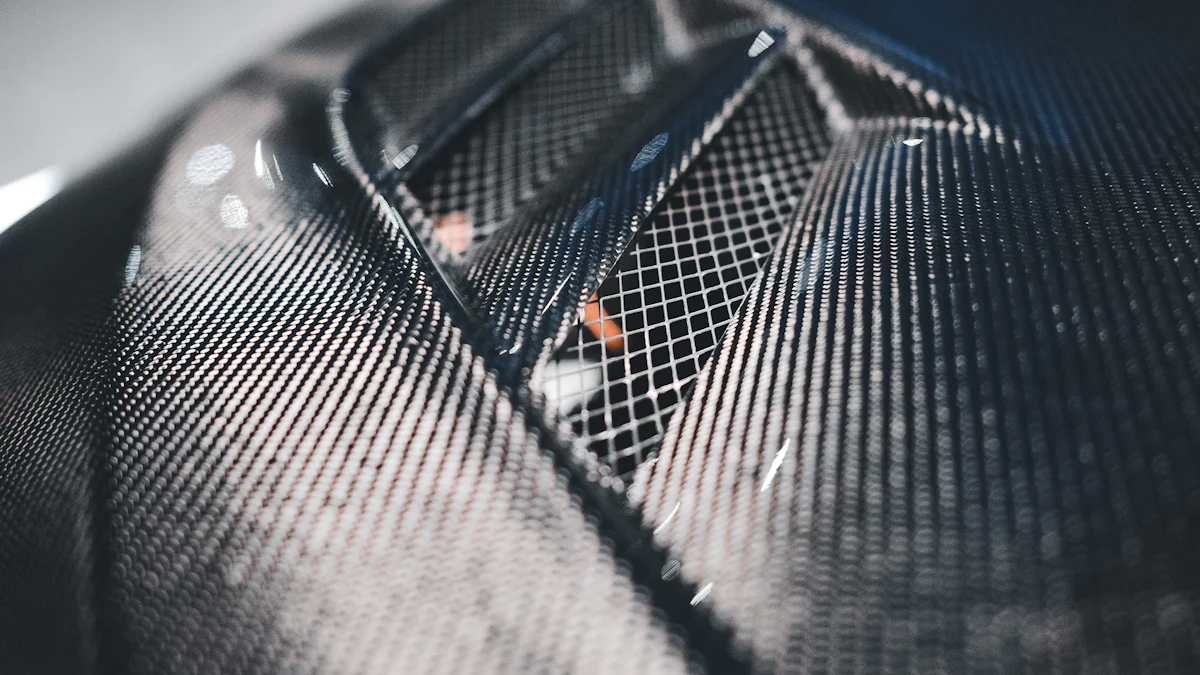
Strength and Durability
Lower Strength-to-Weight Ratio
Other composites often fall short in strength-to-weight ratio when compared to carbon carbon composites. Carbon fiber, a key component of carbon carbon composites, offers 2 to 5 times more rigidity than aluminum and steel, depending on the fiber type. A carbon fiber component of the same thickness as aluminum provides 31% more rigidity, weighs 42% less, and has 60% more strength. This superior performance makes carbon carbon composites the preferred choice for applications requiring high strength and low weight, such as aerospace and defense.
- Carbon fiber composites have a density of 1.55 g/cm³, nearly half that of aluminum (2.7 g/cm³) and significantly less than steel (7.9 g/cm³).
- Other composites, while versatile, cannot match this combination of strength and lightweight properties.
Reduced Durability in Extreme Conditions
In extreme environments, other composites often degrade faster than carbon carbon composites. The latter demonstrates exceptional resilience under multi-factor coupling, where environmental parameters and temperature interact. Limited research on mitigating these factors for other composites highlights their reduced durability in such conditions. This limitation makes them less suitable for applications involving high mechanical stress or fluctuating environmental conditions.
Thermal Resistance
Poor High-Temperature Performance
Carbon carbon composites excel in thermal resistance, maintaining stability at temperatures exceeding 3000°C. Other composites, however, struggle under high heat. Their matrix materials, such as thermosets or thermoplastics, degrade at much lower temperatures. This makes them unsuitable for applications like rocket nozzles or heat shields, where extreme thermal stability is critical.
Limited Use in High-Heat Environments
The low coefficient of thermal expansion in carbon carbon composites allows them to absorb heat without deforming. They also exhibit excellent ablation resistance and thermal shock resistance. Other composites lack these properties, limiting their use in high-heat environments. Industries requiring materials that withstand intense thermal and mechanical stress often favor carbon carbon composites for their superior performance.
Longevity and Wear Resistance
Shorter Lifespan in Harsh Environments
Other composites tend to have a shorter lifespan in harsh environments compared to carbon carbon composites. The latter’s ability to endure high temperatures and mechanical loads ensures a longer operational life. In contrast, other composites degrade more quickly when exposed to extreme conditions, reducing their reliability in demanding applications.
Susceptibility to Wear and Degradation
Wear and degradation rates for other composites are higher than those for carbon carbon composites. For instance, carbon carbon composites exhibit wear rates of 0.05–0.1 mm in the fiber direction and 0.1–0.3 mm in the perpendicular direction, showcasing their durability under load. Other composites, while effective in wet or corrosive environments, lack the same level of wear resistance, making them less durable in high-stress applications.
Performance in Extreme Conditions
Inability to Withstand Thermal and Mechanical Stress
Other composites struggle to perform under extreme thermal and mechanical stress compared to carbon carbon composites. These materials exhibit drastic deterioration when exposed to high temperatures, often losing structural integrity beyond 300°C. In contrast, carbon carbon composites maintain stability at temperatures exceeding 3000°C. Their low coefficient of thermal expansion, ranging from 0.3 to 0.5 mm in the fiber direction, ensures minimal deformation under heat.
Property | Carbon-Carbon Composites | Other Composites |
---|---|---|
Thermal Stability | Excellent up to 3000°C | Drastic deterioration |
Coefficient of Thermal Expansion | 0.3–0.5 mm (fiber) | Higher values leading to deformation |
Ablation Resistance | High | Lower |
Additionally, carbon carbon composites exhibit superior dimensional stability and ablation resistance, making them ideal for high-stress environments. Other composites, including advanced ceramics and metals, lack these properties, limiting their use in applications requiring extreme thermal and mechanical resilience.
Limited Use in Aerospace and Defense
The aerospace and defense industries demand materials that can withstand extreme conditions while maintaining low weight. Carbon carbon composites excel in these areas due to their high strength, lightweight nature, and exceptional thermal stability. These properties make them suitable for rockets, spacecraft, and aircraft, where performance under stress is critical.
- Carbon carbon composites reduce mass, enhancing fuel efficiency and payload capacity.
- They provide comparable stiffness and strength to aluminum and titanium alloys while offering superior thermal shock resistance.
- Their use results in lighter, stronger assemblies, improving overall system efficiency.
Other composites, while versatile, cannot match the performance of carbon carbon composites in these demanding sectors.
Environmental Impact
Non-Biodegradability of Certain Composites
Many composites, particularly polymer-based ones, pose environmental challenges due to their non-biodegradable nature. These materials persist in landfills for decades, contributing to long-term waste issues. Carbon carbon composites, while also non-biodegradable, offer a longer lifespan, reducing the frequency of replacement and waste generation. This durability makes them a more sustainable choice for applications requiring extended operational life.
Recycling Challenges Compared to Carbon Carbon Composites
Recycling other composites presents significant challenges. Carbon fiber-reinforced composites, for instance, are embedded in a thermoset polymer matrix, complicating the recycling process. Current methods often involve shredding, which damages the fibers and limits their reuse in high-performance applications.
- Recycling processes degrade the quality of recovered fibers, restricting their use to lower-value products.
- The embedded polymer matrix makes it difficult to separate and recover intact fibers.
- High-quality recycling methods remain costly and inefficient, further limiting their adoption.
In comparison, carbon carbon composites, though challenging to recycle, maintain their structural integrity longer, reducing the need for frequent recycling and replacement.
Other composites offer several advantages over carbon carbon composites, making them appealing for various industries. These include:
- Cost efficiency due to simpler manufacturing techniques and more affordable raw materials.
- Versatility, as they can be tailored for diverse applications, from construction to consumer goods.
- Ease of manufacturing, with reduced complexity and faster production cycles.
However, these benefits come with trade-offs. Other composites often lack the strength, thermal resistance, and durability that carbon carbon composites provide. Their performance in extreme conditions, such as high temperatures or mechanical stress, remains limited.
Material selection depends on specific application needs. Engineers must weigh the cost and versatility of other composites against the superior performance of carbon carbon composites in demanding environments.
FAQ
What are carbon carbon composites primarily used for?
Carbon carbon composites are used in aerospace, defense, and high-temperature applications. Their exceptional thermal resistance and strength make them ideal for rocket nozzles, heat shields, and aircraft components.
How do other composites differ from carbon carbon composites?
Other composites often use polymer matrices, making them lighter and more versatile. However, they lack the high-temperature stability and strength of carbon carbon composites, limiting their use in extreme environments.
Are other composites more environmentally friendly?
Some other composites, like thermoplastics, offer recyclability, reducing waste. However, many polymer-based composites remain non-biodegradable. Carbon carbon composites, while durable, require energy-intensive production, impacting their environmental footprint.
Why are carbon carbon composites more expensive?
The production of carbon carbon composites involves complex processes like pyrolysis and specialized materials. These factors increase manufacturing costs compared to simpler methods used for other composites.
Can other composites replace carbon carbon composites in aerospace?
Other composites can replace carbon carbon composites in some aerospace applications requiring lightweight materials. However, they cannot match the thermal resistance and durability needed for extreme conditions like re-entry or propulsion systems.