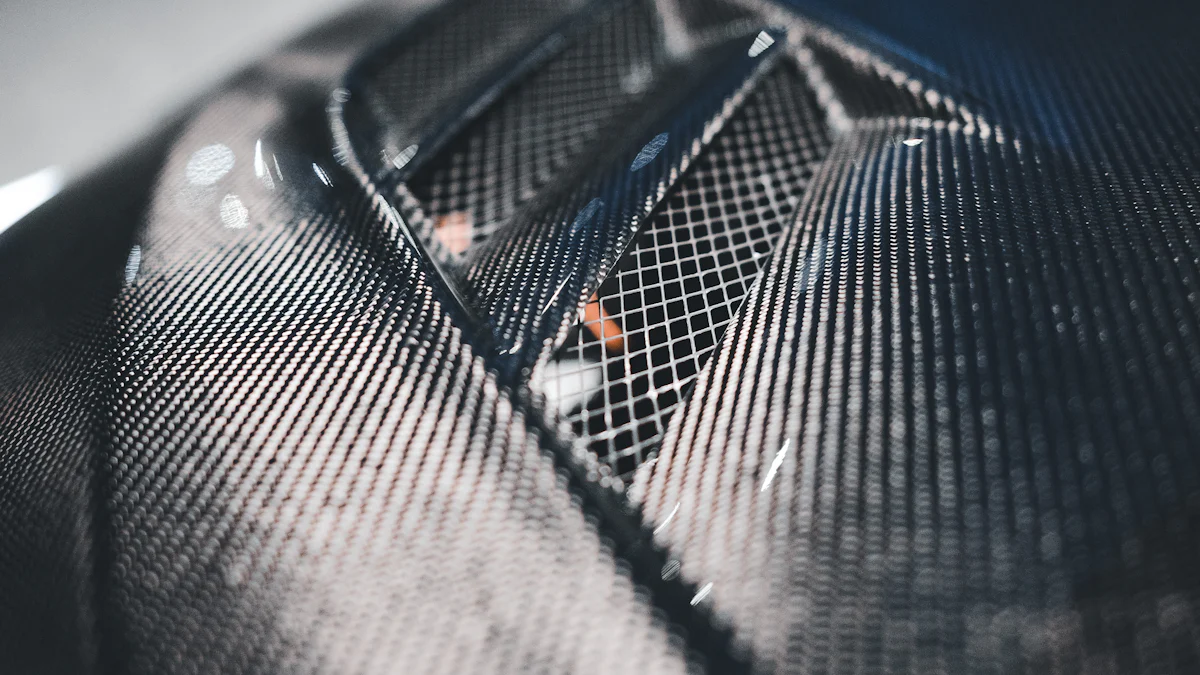
Carbon fiber carbon plates are advanced materials engineered from carbon fibers embedded in a carbon matrix. These plates are renowned for their exceptional strength-to-weight ratio, corrosion resistance, and long-term durability. Their lightweight nature makes them indispensable in industries requiring high-performance materials.
Key properties include:
- High strength-to-weight ratio, lighter yet stronger than steel.
- Resistance to corrosion, ensuring longevity in harsh environments.
- Versatility in extreme conditions, such as high temperatures or pressure.
Applications span across aerospace, automotive, and sports equipment. For instance, they reduce aircraft weight while maintaining structural integrity, enhance fuel efficiency in vehicles, and create high-performance sporting gear.
The manufacturing process involves layering carbon fibers with a resin or matrix, curing the material, and performing post-processing steps to achieve the desired shape and finish. This meticulous process ensures the production of high-quality carbon carbon composites for diverse applications.
Key Takeaways
- Carbon fiber carbon plates offer a superior strength-to-weight ratio, making them ideal for applications in aerospace, automotive, and sports equipment.
- The manufacturing process involves careful layering of carbon fibers with resin, followed by curing to ensure durability and performance.
- Quality control is crucial; regular inspections and mechanical testing help maintain the integrity and reliability of carbon fiber products.
- Innovations in automation and advanced materials are driving down production costs and expanding the applications of carbon fiber carbon plates.
- For DIY enthusiasts, investing in proper tools and safety gear is essential for creating high-performance carbon fiber components.
Overview of Carbon Fiber Carbon Plates
Composition and Properties
Carbon Fibers and Carbon Matrix
Carbon fiber carbon plates consist of two primary components: carbon fibers and a carbon matrix. Carbon fibers are thin strands of carbon atoms bonded together in a crystalline structure, providing exceptional tensile strength and stiffness. The carbon matrix, often a resin or polymer, binds these fibers together, creating a composite material that is lightweight yet incredibly durable. This combination results in a material significantly lighter than metals like aluminum or steel while offering superior mechanical properties.
The unique composition of these plates also ensures resistance to corrosion and stability under temperature fluctuations. These characteristics make them ideal for applications requiring long-term durability and minimal maintenance.
Key Features
Carbon fiber carbon plates stand out due to their remarkable properties:
- Strength-to-weight ratio: These plates are much stronger than steel while being significantly lighter, making them ideal for weight-sensitive applications.
- Heat resistance: They maintain structural integrity even under extreme temperatures, which is critical for aerospace and space exploration.
- Corrosion resistance: Unlike metals, these plates resist rust and chemical degradation, ensuring longevity in harsh environments.
- Fatigue resistance: They outperform traditional materials like steel and aluminum in withstanding repeated stress without failure.
Applications
Aerospace and Defense
Carbon fiber carbon plates play a vital role in aerospace and defense industries. Aircraft components such as fuselage panels, wing spars, and tail sections benefit from their lightweight nature, reducing overall weight by up to 75%. This weight reduction improves fuel efficiency and payload capacity. In spacecraft, these plates are used in heat shields and propulsion systems due to their exceptional heat resistance and structural integrity under extreme conditions.
Automotive and Motorsports
In the automotive sector, carbon fiber carbon plates enhance vehicle performance by reducing weight by up to 60%. This reduction improves fuel efficiency by approximately 25% and allows for sleeker, more aerodynamic designs. High-performance vehicles, including electric cars, utilize these plates to extend battery life and improve safety by absorbing impact energy during collisions. Their rigidity also enhances stability during high-speed maneuvers, making them indispensable in motorsports.
Industrial and Sporting Equipment
Industries and sports manufacturers leverage carbon fiber carbon plates for their strength-to-weight ratio. In industrial applications, they provide durable solutions for machinery and equipment exposed to extreme conditions. Sporting goods like bicycles, tennis rackets, and golf clubs use these plates to deliver high performance without adding unnecessary weight. Their ability to withstand repeated stress ensures reliability and longevity in demanding environments.
Materials and Equipment for Manufacturing
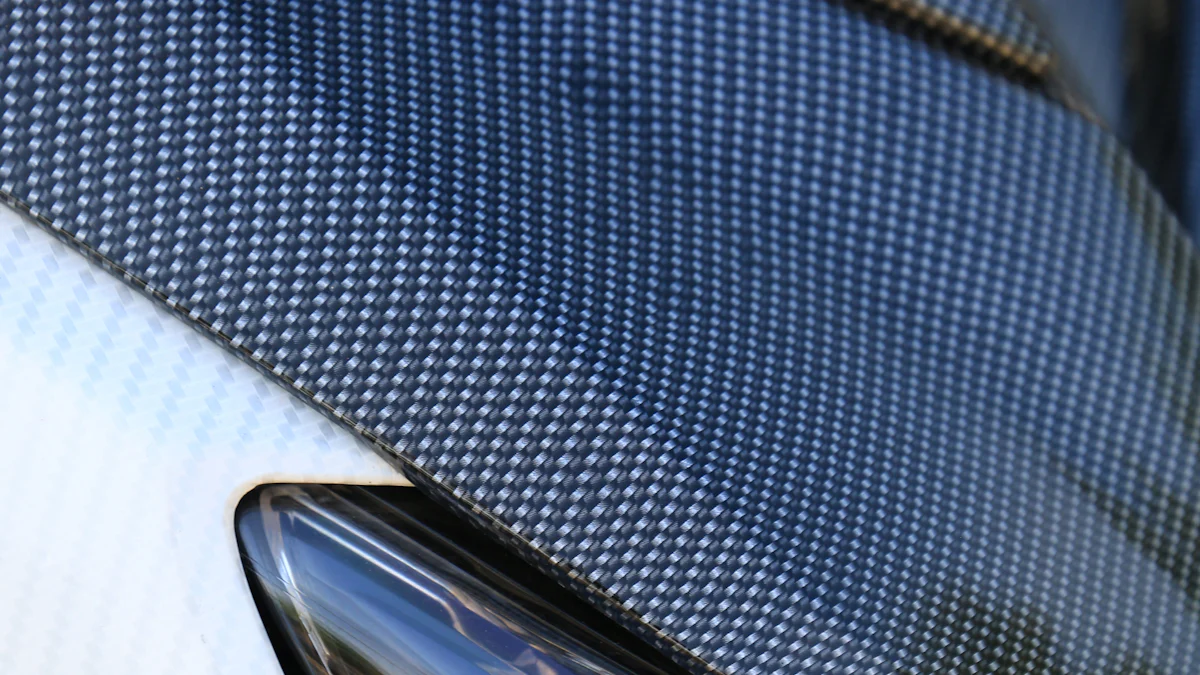
Materials
Types of Carbon Fibers
Carbon fibers are the backbone of carbon fiber carbon plate production. Manufacturers primarily use two types of carbon fibers, each offering unique characteristics and applications:
Type of Carbon Fiber | Raw Material | Characteristics | Applications |
---|---|---|---|
PAN-based Carbon Fiber | PAN (Polyacrylonitrile) | High tensile strength, high elastic modulus | Aerospace, industrial fields, sports products |
Pitch-based Carbon Fiber | Oil/Coal Pitch | Varies from low to ultra-high elastic modulus, high thermal/electric conductivity | High stiffness components, specialized applications |
PAN-based fibers dominate due to their superior strength and versatility, while pitch-based fibers excel in applications requiring high stiffness or conductivity.
Resins and Matrix Materials
Resins bind carbon fibers together, forming a robust composite structure. Commonly used resins include:
Resin | Pros | Cons | Curing |
---|---|---|---|
Epoxy | Highest strength, lightweight, long shelf life | Expensive, sensitive to temperature variations | Requires specific hardener, often heat-cured |
Polyester | Easy to use, UV resistant, low cost | Low strength, limited corrosion resistance | Cures with a catalyst (MEKP) |
Vinyl Ester | Combines epoxy’s performance with polyester’s cost | Lower strength than epoxy, higher cost than polyester | Cures with a catalyst (MEKP) |
Epoxy resins are preferred for high-performance applications due to their strength and durability.
Additives for Enhanced Properties
Additives improve the performance of carbon fiber carbon plates. Common additives include:
- Nanoparticles: Enhance thermal and electrical conductivity.
- Flame retardants: Increase fire resistance.
- UV stabilizers: Protect against sunlight degradation.
These additives tailor the material properties to meet specific industry requirements.
Equipment
Molds and Lay-Up Tools
Molds shape the carbon fiber layers into the desired form. Lay-up tools assist in arranging the fibers in precise orientations, optimizing the mechanical properties of the final product.
Autoclaves and Ovens
Autoclaves and ovens play a critical role in curing carbon fiber carbon plates:
- Autoclaves apply controlled heat and pressure, ensuring uniform bonding and eliminating voids.
- Ovens regulate airflow to maintain consistent temperatures, preventing defects like bubbles or incomplete curing.
Proper curing enhances the strength and durability of the composite material.
Cutting and Finishing Tools
Accurate cutting tools ensure precise dimensions of carbon fiber sheets. Finishing tools refine the edges and surfaces, preparing the plates for final applications. These tools contribute to the overall quality and performance of the finished product.
Step-by-Step Manufacturing Process
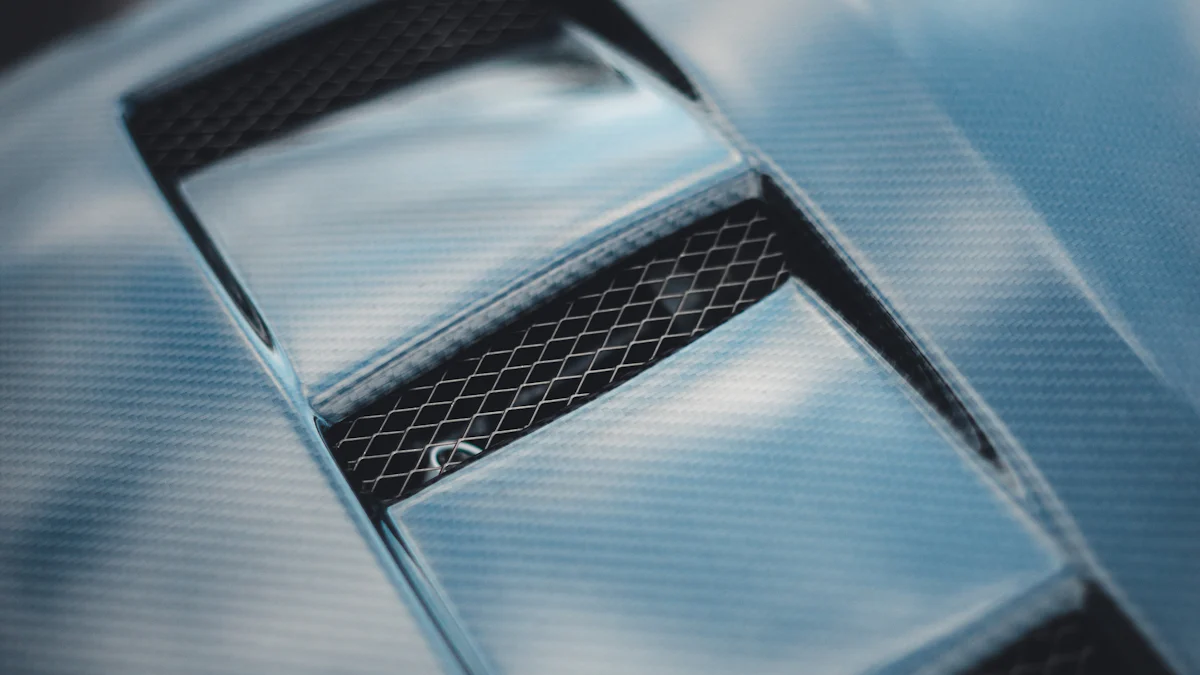
Preparing the Materials
Carbon Fiber Production and Carbonization
The production of carbon fibers begins with a polymeric feedstock known as a precursor, typically polyacrylonitrile (PAN). The process involves several key steps:
- Precursor Preparation: The precursor is prepared by mixing it with other materials.
- Spinning: The mixture is spun into fibers, forming the base structure.
- Stabilizing: The fibers undergo chemical alteration to enhance thermal stability.
- Carbonizing: The fibers are heated to temperatures between 1,000°C and 3,000°C in an oxygen-free environment. This step removes non-carbon atoms, leaving tightly bonded carbon chains.
- Surface Treatment: The fibers are treated to improve adhesion with the matrix resin.
This process ensures the structural integrity and high performance of the carbon fibers used in carbon fiber carbon plate manufacturing.
Preparing the Resin or Matrix
The resin or matrix material binds the carbon fibers together, forming a composite. Manufacturers carefully select the resin type based on the application requirements. The preparation process includes:
- Ensuring the correct ratio of resin to hardener for optimal curing.
- Mixing additives, such as flame retardants or UV stabilizers, to enhance specific properties.
- Maintaining a uniform consistency to avoid defects during layering.
Layering and Shaping
Wet Lay-Up Method
The wet lay-up method involves manually applying resin to carbon fiber layers. This technique typically results in a fiber-to-resin ratio of 40:60, making the composite heavier but suitable for less weight-sensitive applications. It is cost-effective and ideal for small-scale production.
Prepreg Lamination
Prepreg lamination uses pre-impregnated carbon fiber sheets with a controlled resin content. This method achieves a fiber-to-resin ratio of approximately 60:40, producing lighter and stronger composites. The layers are stacked in molds, ensuring precise alignment for optimal mechanical properties.
Resin Infusion Process
The resin infusion process involves placing dry carbon fibers in a mold and then introducing resin under vacuum pressure. This method also achieves a 60:40 fiber-to-resin ratio. It minimizes voids and ensures consistent quality, making it suitable for high-performance applications.
Curing and Solidifying
Autoclave Curing
Autoclave curing applies heat and pressure to the layered material. This process eliminates air pockets and ensures uniform bonding between the carbon fibers and resin. The controlled environment enhances the strength and durability of the final carbon fiber carbon plate.
Oven Curing
Oven curing involves heating the composite material in a regulated airflow environment. This method is less expensive than autoclave curing and is often used for larger components. Proper temperature control prevents defects such as incomplete curing or resin bubbling.
Post-Processing
Trimming and Cutting
Trimming and cutting are essential steps in the post-processing of carbon fiber plates. These processes refine the dimensions and edges of the material, ensuring it meets precise specifications. Due to the high strength and hardness of carbon fiber, manufacturers rely on specialized tools such as diamond-coated cutting tools and carbide drill bits. These tools minimize wear and maintain accuracy during operation.
Controlling processing parameters is equally important. Adjusting cutting speed, feed rate, and cutting depth prevents defects like delamination or tearing. Operators must monitor these parameters closely to achieve clean cuts and maintain the structural integrity of the material. Proper handling during this stage ensures the carbon fiber plate retains its mechanical properties and aesthetic appeal.
Surface Treatment and Coating
Surface treatment enhances the appearance and performance of carbon fiber plates. This step often begins with polishing, which smooths the surface and removes any imperfections left from the curing process. Polished surfaces not only improve the material’s visual appeal but also prepare it for subsequent coatings.
Coating applications provide additional protection and functionality. Manufacturers apply protective layers to shield the material from environmental factors such as UV radiation, moisture, and chemical exposure. These coatings extend the lifespan of the product and maintain its performance in demanding conditions. In some cases, functional coatings, such as anti-static or heat-resistant layers, are added to meet specific industry requirements.
By combining precise trimming, cutting, and surface treatments, manufacturers ensure the final product meets the highest quality standards. These post-processing techniques play a critical role in delivering durable and reliable carbon fiber components for various applications.
Quality Control and Finishing
Inspection and Testing
Visual Inspection for Defects
Visual inspection serves as the first line of defense in quality control. Technicians examine the carbon fiber plates for surface irregularities, such as cracks, voids, or delamination. This step ensures that the material meets aesthetic and structural standards before proceeding to advanced testing. Regular inspections during manufacturing help identify defects early, reducing waste and ensuring consistent quality.
In-service inspections and maintenance also play a critical role in lifecycle management. These inspections monitor the condition of carbon fiber components over time, ensuring their reliability in demanding applications. Damage assessments after incidents, such as impacts or extreme stress, help determine whether repairs or replacements are necessary.
Mechanical Testing (e.g., tensile strength, thermal resistance)
Mechanical testing evaluates the performance of carbon fiber plates under various conditions. Common methods include:
- Ultrasonic Testing: Detects internal flaws by sending sound waves through the material.
- X-ray Testing: Identifies hidden defects, such as voids or cracks, using imaging technology.
- Sensor Monitoring: Tracks changes in temperature and pressure during use, ensuring the material performs as expected.
These tests measure critical properties like tensile strength, thermal resistance, and fatigue performance. By combining these techniques, manufacturers ensure that each plate meets industry standards for safety and durability.
Surface Finishing
Polishing and Coating
Polishing enhances the appearance and smoothness of carbon fiber plates. This process removes surface imperfections, creating a uniform finish that improves both aesthetics and functionality. After polishing, manufacturers apply coatings to protect the material from environmental factors.
Coatings serve multiple purposes, including UV protection, moisture resistance, and chemical shielding. Specialized surface preparation ensures strong adhesion between the coating and the carbon fiber. For example, electroplating involves immersing the plate in an electrolyte solution and applying a direct current to deposit a protective metal layer. Post-treatments, such as rinsing and curing, further enhance durability.
Protective Layers for Durability
Protective layers extend the lifespan of carbon fiber plates by shielding them from wear and tear. The choice of finish depends on the application:
Finish Type | Description | Durability | Applications |
---|---|---|---|
Matte Finish | Low porosity, hides fingerprints, scratches less visible | Fairly durable | Suitable for most applications |
Gloss Finish | Smooth reflective look, shows imperfections over time | Less durable | Recommended for cosmetic applications |
Matte finishes are ideal for industrial and functional uses, while gloss finishes suit cosmetic applications. By selecting the appropriate finish, manufacturers ensure the plates meet both performance and aesthetic requirements.
Challenges and Innovations in Manufacturing
Common Challenges
High Manufacturing Costs
Producing carbon fiber carbon plates involves significant expenses, which can limit their adoption across industries. Several factors contribute to these high costs:
- The aerospace sector evaluates the material’s cost against its performance benefits, such as improved fuel efficiency and extended flight range.
- In industrial automation, engineers weigh the expense of carbon fiber against advantages like faster production speeds and reduced machinery wear.
- Material selection often requires balancing cost with performance gains, making affordability a critical consideration.
Despite these challenges, industries continue to invest in carbon fiber due to its unparalleled strength-to-weight ratio and durability.
Complexity of the Process
The manufacturing process for carbon fiber carbon plates is intricate and requires precision at every stage. From carbonization to curing, each step demands specialized equipment and expertise. Errors during layering or curing can lead to defects, such as voids or delamination, which compromise the material’s performance. This complexity increases production time and costs, making it essential for manufacturers to adopt advanced techniques to streamline operations.
Innovations
Automation and Robotics
Automation and robotics are transforming the production of carbon fiber carbon plates by enhancing efficiency and precision. Key advancements include:
- Automated Fiber Placement (AFP), which deposits over 100 pounds of material per hour, significantly increasing production rates.
- Lightweight robotic end effectors that improve speed and accuracy while reducing motor and actuator loads.
- Facilities leveraging automation achieve faster response times, lower production costs, and improved reliability in manufacturing processes.
These innovations enable manufacturers to produce high-quality plates at a reduced cost, making them more accessible for various applications.
Advanced Materials and Techniques
Recent developments in materials and techniques are enhancing the properties of carbon fiber carbon plates. For example:
- Carbitex’s CX6 product uses a specially developed binder to improve the flexibility of carbon fiber laminates without compromising tensile strength. This innovation has proven effective in high-precision applications like footwear components, where power transfer is critical.
- Carbon fiber-reinforced polyetheretherketone (CFR-PEEK) plates offer lightweight, biocompatible solutions for medical devices. Their radiolucency ensures clear imaging, while their durability reduces long-term costs.
These advancements expand the potential applications of carbon fiber carbon plates, making them indispensable in industries like aerospace, automotive, and healthcare.
Manufacturing carbon fiber carbon plates involves a meticulous process that ensures high-quality results. Key steps include preparing prepreg materials, optimizing curing parameters, and conducting real-time quality control to detect defects. Post-processing, such as trimming and surface treatment, requires precise tools and techniques to maintain the material’s integrity.
Quality control plays a pivotal role in ensuring the performance and reliability of these plates. Precise resin-to-fiber ratios and uniform impregnation are essential for high-strength applications. Real-time monitoring during curing further enhances quality by identifying potential defects early.
Innovation continues to drive advancements in this field. Sustainable production methods and advanced recycling techniques are making these materials more accessible. As industries evolve, carbon fiber carbon plates will remain at the forefront of technological and sustainable solutions.
For those interested in starting their own projects, resources such as proper cutting tools, safety gear, and adhesive options are readily available. Exploring these tools can help individuals create durable and high-performance components for various applications.
The versatility and durability of carbon fiber carbon plates make them indispensable across industries. By mastering the manufacturing process and embracing innovation, readers can unlock the full potential of this remarkable material.
FAQ
What are carbon fiber carbon plates made of?
Carbon fiber carbon plates consist of carbon fibers embedded in a carbon matrix. The fibers provide strength and stiffness, while the matrix binds them together, creating a lightweight yet durable composite material suitable for high-performance applications.
How are carbon fiber carbon plates used in aerospace?
In aerospace, these plates reduce aircraft weight while maintaining structural integrity. They are used in fuselage panels, wing spars, and heat shields, enhancing fuel efficiency and performance under extreme conditions.
What is the difference between PAN-based and pitch-based carbon fibers?
PAN-based fibers offer high tensile strength and versatility, making them ideal for general applications. Pitch-based fibers provide superior stiffness and thermal conductivity, which suit specialized uses like high-precision components.
Why is curing important in the manufacturing process?
Curing solidifies the resin and bonds it to the carbon fibers. This step ensures the composite achieves its desired strength, durability, and resistance to environmental factors like heat and moisture.
Can carbon fiber carbon plates be recycled?
Yes, recycling methods like pyrolysis recover carbon fibers from used composites. These fibers can be reused in less demanding applications, promoting sustainability and reducing waste in manufacturing processes.