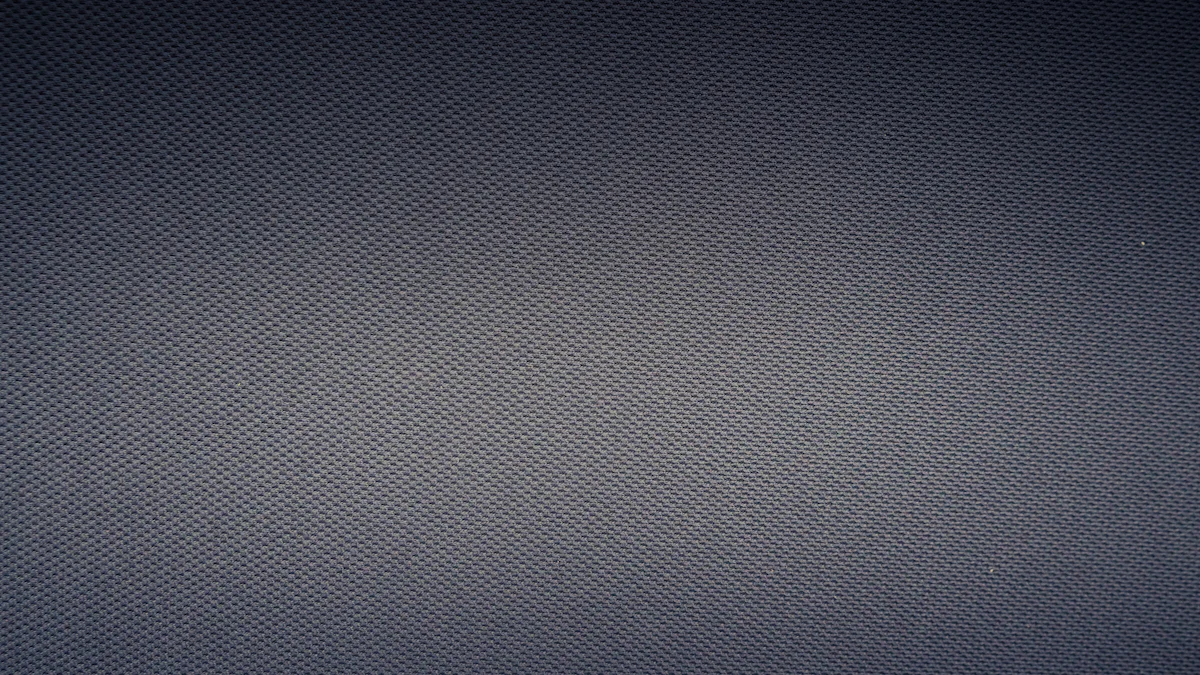
Choosing the right carbon fiber sheet can make or break your project. Whether you’re building a lightweight drone or reinforcing a structural component, the material you pick directly impacts performance and durability. But let’s be honest—this process isn’t always straightforward. Without the right knowledge, you might face challenges like high costs, limited availability, or even issues like delamination if the sheet isn’t handled properly.
I’ve seen people struggle with questions like, “What thickness should I choose?” or “Is a 1/8 carbon fiber sheet too heavy for my application?” These decisions can feel overwhelming, especially when you’re also trying to balance the carbon fiber sheet price with quality. That’s why I’m here to help. By breaking things down, I’ll guide you toward making informed choices that suit your needs, whether you’re working with a carbon fiber roll or a pre-cut sheet.
Key Takeaways
- Evaluate strength and stiffness: Choose carbon fiber sheets based on their tensile strength and modulus of elasticity to match your project’s performance needs.
- Consider weight and thickness: Lighter sheets improve efficiency in applications like drones and racing bikes, while thickness affects rigidity and flexibility.
- Select the right weave type: Different weave patterns (plain, twill, satin) impact both the aesthetics and functionality of the carbon fiber sheet.
- Choose the appropriate surface finish: Glossy finishes offer a high-end look, while matte finishes provide durability and scratch resistance.
- Assess durability and environmental resistance: Ensure the carbon fiber sheet can withstand heat, moisture, and chemicals based on your project’s conditions.
- Research suppliers thoroughly: Look for reputable manufacturers with quality certifications to ensure you receive reliable materials.
- Request samples before purchasing: Testing samples helps you evaluate the sheet’s quality, finish, and suitability for your project.
- Balance cost and quality: Prioritize essential features for your project to find a carbon fiber sheet that meets your needs without overspending.
Key Factors to Consider When Choosing a Carbon Fiber Sheet
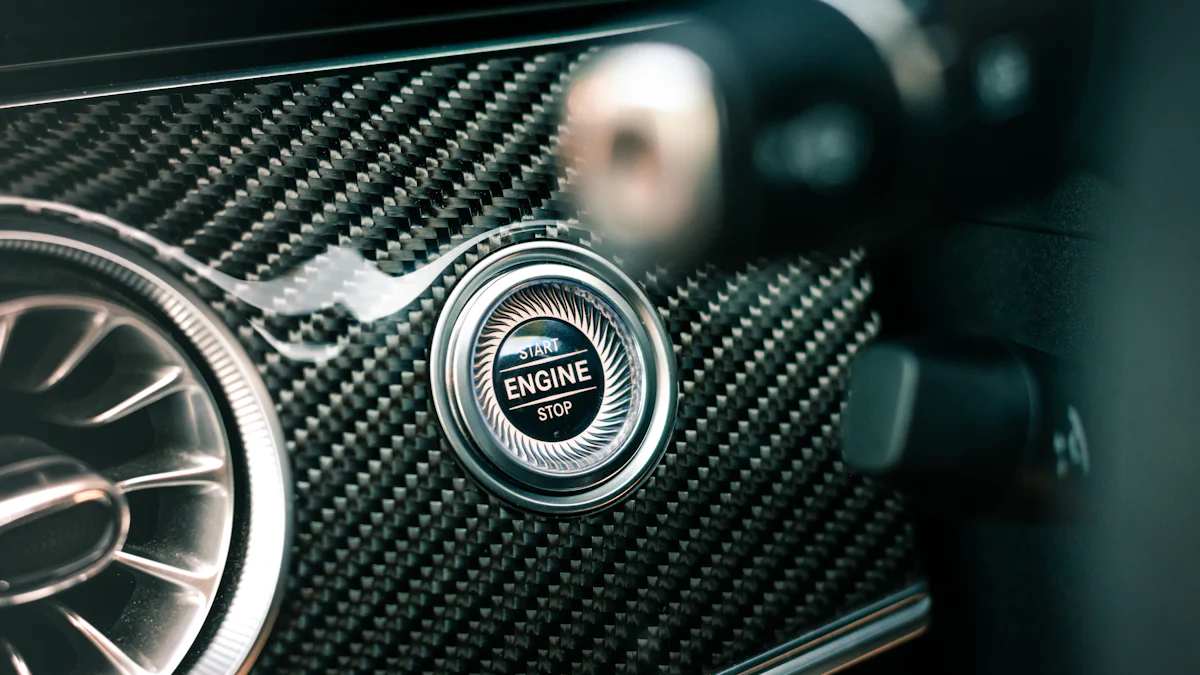
Strength and Stiffness
Understanding tensile strength and modulus of elasticity
When it comes to carbon fiber sheets, strength and stiffness are two of the most important factors to evaluate. Strength refers to how much force the material can handle before breaking, while stiffness (measured by the modulus of elasticity) determines how much the sheet will bend under pressure. These properties vary depending on the type of carbon fiber used. Here’s a quick breakdown:
Type of Carbon Fiber | Modulus of Elasticity (msi) | Tensile Strength (ksi) |
---|---|---|
Standard Modulus | 33-36 | 500-700 |
Intermediate Modulus | 43-47 | 800-1000 |
High Modulus | 57 | 640 |
Ultra High Modulus | 110 | 425 |
If you’re working on a project that requires high rigidity, like an aerospace component, you might want to choose a high or ultra-high modulus sheet. For general applications, standard or intermediate modulus sheets often strike the right balance between strength and flexibility.
How strength and stiffness impact performance
The strength and stiffness of a carbon fiber sheet directly affect its performance. For example:
- Higher stiffness means less deformation under load, which is critical for structural integrity.
- Carbon fiber can be up to 31% more rigid than aluminum at the same thickness, while also being 42% lighter and 60% stronger.
- High modulus sheets offer four times the rigidity of aluminum, making them ideal for demanding applications.
- Unlike metals, carbon fiber has a “spring back” effect, meaning it returns to its original shape after bending. This resilience is perfect for projects requiring durability and flexibility.
Weight and Thickness
Why weight matters for lightweight applications
Weight is a game-changer, especially in industries like aerospace, automotive, and sports. Carbon fiber is prized for being lightweight yet incredibly strong. A lighter sheet reduces overall weight, improving fuel efficiency in vehicles or enhancing performance in sporting equipment. If you’re designing a drone or a racing bike, every gram counts. Choosing a thinner, lighter sheet can make all the difference.
Choosing the right thickness for your project
Thickness plays a big role in determining how rigid or flexible a carbon fiber sheet will be. Here’s a handy table to help you decide:
Thickness | Rigidity | Flexibility | Usability |
---|---|---|---|
0.25mm | Very Low | Extremely High | Fine crafting |
0.4mm | Low | Very High | Intricate designs |
1.5mm | Moderate | High | Lightweight performance |
2mm | Moderate | Moderate | Balanced applications |
2.5mm | High | Low | Structural components |
5mm | High | Low | Heavy-duty structural uses |
For intricate designs, like custom parts for a hobby project, thinner sheets (0.25mm or 0.4mm) work best. For structural applications, thicker sheets (2.5mm or 5mm) provide the necessary rigidity.
Weave Type and Appearance
Common weave patterns (e.g., plain, twill, unidirectional)
The weave pattern of a carbon fiber sheet affects both its appearance and functionality. Here are the most popular options:
- Plain Weave: This pattern has a checkerboard look and is highly stable but less flexible. It’s great for flat surfaces and structural applications.
- Twill Weave: With its diagonal lines, this weave is more pliable and conforms to curves easily. It’s a favorite in automotive and sporting goods.
- Satin Weave: Known for its smooth, glossy finish, this weave is highly drapeable and ideal for luxury applications or complex contours.
How weave type affects aesthetics and functionality
The weave you choose can make or break your project. A plain weave offers a clean, symmetrical look and excellent stability, making it perfect for structural uses. Twill weave, on the other hand, combines strength with flexibility, allowing it to wrap around curved surfaces without stressing the fibers. Satin weave adds a touch of elegance with its glossy finish, but it sacrifices some stability for its pliability. Think about your project’s needs—do you prioritize strength, flexibility, or aesthetics? The right weave will depend on your answer.
Surface Finish
Glossy vs. matte finishes
When it comes to surface finishes, you’ve got two main options: glossy and matte. Each has its own vibe and practical benefits. Let me break it down for you.
A glossy finish gives carbon fiber sheets that sleek, glass-like appearance. It’s like looking into a mirror that highlights the intricate weave of the material. This finish screams high-end and is perfect if you want your project to stand out visually.
Gloss carbon fiber sheets should look like glass, with a perfectly clear gloss coat that showcases the texture of the material without any imperfections.
On the other hand, matte finishes are all about subtlety. They’re less reflective but still show off the carbon fiber’s texture beautifully. Plus, they’re tougher when it comes to scratches. If you’re working on something that needs to handle wear and tear, like a bike frame or a tool, matte might be your best bet.
Here’s a quick list of common finishes:
- Matte/satin finish: Durable and scratch-resistant.
- Sanded finish: Offers a textured look.
- Gloss finish: High shine and visually striking.
Protective coatings and their benefits
Protective coatings are like armor for your carbon fiber sheets. They shield the surface from damage and extend its lifespan. A good coating can protect against UV rays, moisture, and even minor impacts.
For glossy finishes, coatings help maintain that shiny, flawless look. For matte finishes, they enhance durability without compromising the understated aesthetic. Whether you’re using your sheet outdoors or in a high-stress environment, a protective coating is always a smart choice.
Durability and Environmental Resistance
Resistance to heat, moisture, and chemicals
Carbon fiber sheets are tough, but not all are created equal. Some handle extreme conditions better than others. If your project involves high temperatures, like in automotive or aerospace applications, you’ll need a sheet with excellent heat resistance.
Moisture is another factor. While carbon fiber itself doesn’t absorb water, the resin used in the sheet might. Look for sheets with moisture-resistant resins if you’re working in humid or wet environments.
Chemical resistance is equally important. If your sheet will come into contact with oils, solvents, or other chemicals, make sure it’s designed to withstand those substances.
Longevity in different environments
Durability isn’t just about surviving tough conditions—it’s about thriving in them. Carbon fiber sheets with the right finish and resin can last for years, even in challenging environments.
For outdoor projects, UV-resistant coatings are a must. Without them, prolonged sun exposure can weaken the material over time. In industrial settings, sheets with high chemical and impact resistance will hold up better.
By choosing the right combination of finish, coating, and material properties, you can ensure your carbon fiber sheet stays strong and looks great, no matter where you use it.
Matching the Carbon Fiber Sheet to Your Application
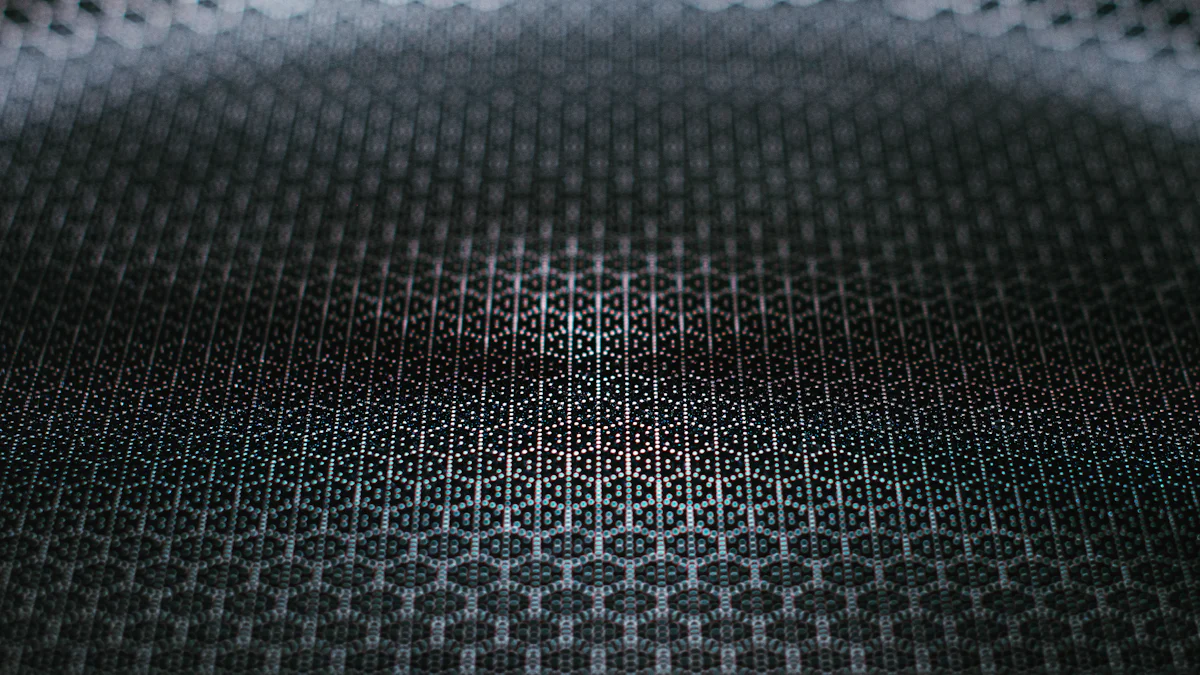
Automotive and Aerospace Applications
High-strength sheets for structural components
When it comes to cars and planes, strength is everything. Carbon fiber sheets are perfect for structural components because they’re incredibly strong and durable. They can handle heavy loads without breaking or bending. This makes them ideal for parts like chassis, wings, and other load-bearing structures.
What’s even better? Carbon fiber sheets can be molded into complex shapes. This flexibility allows engineers to design aerodynamic components that improve speed and stability. Plus, their high thermal conductivity helps manage heat in high-temperature environments, like near engines or exhaust systems.
If you’re working on a project that demands strength and precision, carbon fiber sheets are a no-brainer. They’ll keep your structure solid while staying lightweight.
Lightweight sheets for fuel efficiency
Weight is a big deal in both the automotive and aerospace industries. Lighter vehicles and aircraft consume less fuel, which saves money and reduces emissions. Carbon fiber sheets shine here because they offer a high strength-to-weight ratio.
For example, replacing metal body panels with carbon fiber can cut weight significantly without sacrificing durability. This means better fuel efficiency and improved performance. Whether it’s a race car or a commercial airplane, lightweight carbon fiber sheets make a noticeable difference.
Sporting Goods and Recreational Equipment
Sheets for performance and durability
Carbon fiber isn’t just for engineers—it’s a game-changer for athletes too. You’ll find it in bicycles, tennis rackets, golf clubs, and even helmets. Why? Because it combines strength and stiffness with a lightweight design.
Take bicycles, for instance. Carbon fiber frames are lighter than aluminum but just as strong. This makes them easier to handle and more durable, offering smoother rides. Tennis rackets made from carbon fiber provide better control and power, giving players a competitive edge.
Fun fact: Carbon fiber’s high specific strength and modulus outperform wood, making it a top choice for sports gear. It’s all about delivering performance without adding weight.
Customization options for specific sports
Every sport has unique demands, and carbon fiber sheets can meet them all. They’re easy to customize, whether you need a specific shape, size, or finish. For example, a cyclist might want a matte finish for a sleek look, while a golfer might prioritize stiffness for better swing control.
This adaptability makes carbon fiber a favorite for recreational equipment. You can tailor it to your exact needs, ensuring top-notch performance every time.
Industrial and Construction Uses
Reinforcement in heavy-duty applications
In construction, strength and durability are key. Carbon fiber sheets excel as reinforcement materials because they’re strong yet lightweight. They’re often used to strengthen beams, columns, and other structural elements.
Another bonus? Carbon fiber resists corrosion and chemical damage. This means it lasts longer and requires less maintenance compared to traditional materials like steel. If you’re working on a project that needs to stand the test of time, carbon fiber is a solid choice.
Sheets for precision tools and machinery
Carbon fiber isn’t just for big structures—it’s also great for precision tools and machinery. Its low weight and high stiffness make it ideal for parts that need to be both strong and easy to handle.
For example, in industrial settings, carbon fiber sheets are used to create lightweight machine components that improve efficiency. They’re also resistant to high temperatures, making them perfect for tools exposed to heat.
Whether you’re building a skyscraper or crafting a precision tool, carbon fiber sheets offer unmatched versatility and performance.
DIY and Hobbyist Projects
Affordable options for small-scale projects
If you’re diving into a DIY project, you don’t need to break the bank to work with carbon fiber sheets. Trust me, I’ve been there, and I know how tempting those high-end sheets can look. But for most hobbyist applications, affordable options get the job done beautifully.
Here’s what I’ve found:
- Recycled carbon fiber products are a fantastic choice. They’re not only cost-effective but also sustainable. You’ll save money and feel good about reducing waste.
- Standard carbon fiber sheets typically range from 20to20 to 20to100. These are perfect for small-scale projects like crafting, repairs, or custom parts.
- High-end sheets, which can cost over $1,000 per square foot, are overkill for most DIY needs. Stick with the basics unless your project demands something extraordinary.
If you’re just starting out, I recommend buying smaller sheets or even offcuts. Many suppliers sell these at discounted prices, and they’re ideal for experimenting without spending too much.
💡 Pro Tip: Check out local suppliers or online marketplaces for deals on recycled or surplus carbon fiber sheets. You’d be surprised at the quality you can get for a fraction of the price.
Tips for working with carbon fiber at home
Working with carbon fiber at home can feel intimidating at first, but it’s easier than you think. With the right tools and a bit of patience, you’ll be crafting like a pro in no time.
Here are some tips I’ve learned along the way:
- Use the right tools: A fine-tooth saw or a Dremel tool works great for cutting carbon fiber sheets. Always wear a mask and goggles to protect yourself from dust.
- Sand the edges: After cutting, sand the edges with fine-grit sandpaper. This smooths out rough spots and prevents splinters.
- Work in a ventilated area: Carbon fiber dust can irritate your lungs, so make sure you’re in a well-ventilated space or wear a respirator.
- Practice with epoxy resin: If your project involves bonding or coating, practice mixing and applying epoxy resin on scrap pieces first. It takes a bit of trial and error to get it just right.
- Secure your sheet: Use clamps or tape to hold the sheet in place while cutting or sanding. This prevents movement and ensures clean, precise work.
🛠️ Note: Carbon fiber is strong but brittle. Avoid bending it too much, as this can cause cracks or delamination.
For beginners, I suggest starting with simple projects like phone cases, keychains, or decorative panels. These let you get a feel for the material without overwhelming you. Once you’re comfortable, you can move on to more complex creations like drone frames or custom car parts.
Working with carbon fiber at home is incredibly rewarding. It’s lightweight, durable, and looks amazing when finished. Plus, there’s nothing quite like the satisfaction of saying, “Yeah, I made that.”
Balancing Cost and Quality: Understanding Carbon Fiber Sheet Price
Understanding Price Variations
Factors that influence the cost of carbon fiber sheets
Have you ever wondered why carbon fiber sheet prices vary so much? It’s not just about the brand name. Several factors come into play, and understanding them can help you make smarter choices.
Here’s what affects the price:
- Quality: Higher-quality sheets with better fiber alignment and fewer defects cost more.
- Thickness and Size: Thicker or larger sheets require more material, which increases the price.
- Fiber Modulus: Sheets with higher modulus fibers (like ultra-high modulus) are pricier due to their advanced properties.
- Maximum Temperature Rating: Sheets designed to withstand extreme heat cost more.
- Raw Material Costs: The price of carbon fiber fabric itself fluctuates based on demand and supply.
- Customization: Unique weaves, finishes, or dimensions add to the cost.
Manufacturing also plays a big role. Producing carbon fiber sheets requires high energy input and precision engineering during processes like oxidation and carbonization. Automation can reduce costs, but global supply chain disruptions or demand spikes often drive prices up.
Differences between high-end and budget options
Not all carbon fiber sheets are created equal. High-end sheets offer better flatness, smoother finishes, and straighter fiber orientation. These features ensure top-notch performance, especially for demanding applications. Budget options, while more affordable, might have minor imperfections or lower modulus fibers. They’re great for less critical projects but may not deliver the same durability or strength.
Finding the Right Balance
Prioritizing essential features over extras
When choosing a carbon fiber sheet, focus on what truly matters for your project. Do you need high strength, or is appearance more important? For structural uses, prioritize features like tensile strength and flatness. For decorative purposes, a glossy finish might take precedence.
I always recommend skipping unnecessary extras. For example, if your project doesn’t involve high temperatures, there’s no need to pay extra for a heat-resistant sheet. By narrowing down your must-haves, you can save money without compromising quality.
When to invest in premium sheets
Sometimes, it’s worth splurging on premium sheets. If your project involves safety-critical components, like in aerospace or automotive applications, don’t cut corners. High-end sheets ensure reliability and longevity. On the other hand, for DIY or hobby projects, standard sheets often work just fine.
Tips for Cost-Effective Purchases
Buying in bulk for large projects
If you’re tackling a big project, buying in bulk can save you a lot of money. Many suppliers offer discounts for larger orders, reducing the per-unit cost. It’s a smart move if you know you’ll need multiple sheets.
Comparing suppliers and reading reviews
Not all suppliers are equal. Take the time to compare prices and request quotes from different vendors. Look for reviews to ensure you’re dealing with a reputable manufacturer. A little research upfront can save you from costly mistakes later.
You can also explore hybrid composites or pre-preg options to cut costs without sacrificing too much quality. These alternatives balance performance and affordability, making them ideal for budget-conscious buyers.
💡 Pro Tip: Always inspect the sheet’s flatness, finish, and fiber orientation before purchasing. These details reveal a lot about the sheet’s quality.
Balancing cost and quality might seem tricky, but it’s all about knowing your priorities and doing your homework. With the right approach, you can find a carbon fiber sheet that fits your needs and budget perfectly.
Practical Tips for Evaluating and Purchasing Carbon Fiber Sheets
Researching Suppliers
Identifying reputable manufacturers and distributors
Finding the right supplier is the first step to getting high-quality carbon fiber sheets. I always recommend starting with well-known manufacturers or distributors. Reputable suppliers usually have a track record of producing reliable materials. They also provide detailed product information, which helps you make informed decisions.
When researching, look for suppliers who specialize in carbon fiber products. They’re more likely to understand the material’s unique properties, like its lightweight strength and durability. A good supplier will also offer guidance on choosing the right sheet for your project.
🛠️ Pro Tip: Check online reviews and forums to see what other buyers say about a supplier. It’s a great way to spot red flags or confirm their reliability.
Checking certifications and quality standards
Certifications are a big deal when it comes to carbon fiber sheets. They prove that the product meets industry standards for quality and performance. I always look for certifications like ISO 9001 or AS9100, especially for aerospace or automotive applications. These certifications ensure the sheets are manufactured with precision and care.
Quality standards also matter. For example, a high-quality sheet should lie perfectly flat without any waves or warps. If the sheet has a gloss finish, it should be smooth and clear, with no crushed fibers. Matte finishes should feel smooth but less reflective. Paying attention to these details can save you from buying low-quality or counterfeit products.
Requesting Samples
Why samples are important for evaluation
Samples are a lifesaver when you’re unsure about a product. They let you test the material before committing to a larger purchase. I always request samples when working on a new project. It’s the best way to evaluate the sheet’s quality, finish, and overall feel.
Samples also help you compare different options. For instance, you can test sheets with varying thicknesses or finishes to see which one works best for your needs. This hands-on approach ensures you’re getting exactly what you need without wasting money.
What to look for when testing samples
When testing samples, I focus on a few key things:
- Flatness: The sheet should lie perfectly flat without any bends or creases.
- Finish: Glossy sheets should look smooth and clear, while matte sheets should have a subtle, non-reflective texture.
- Fiber Orientation: The fibers should be straight and evenly aligned. Misaligned fibers can weaken the sheet and ruin its appearance.
I also check the sheet’s weight and thickness to ensure it matches the specifications. If the sample doesn’t meet your expectations, it’s a sign to look elsewhere.
Understanding Technical Specifications
Decoding product datasheets
Product datasheets can feel overwhelming at first, but they’re packed with valuable information. I like to focus on the key metrics that matter most for my project. For example, the datasheet will tell you about the sheet’s tensile strength, modulus of elasticity, and weight. These numbers help you understand how the sheet will perform under different conditions.
Another important detail is cutting tolerances. High-quality sheets should measure within ±.125” of the stated dimensions. This precision ensures the sheet fits perfectly into your design without extra adjustments.
Key metrics to focus on (e.g., strength, weight, thickness)
Here’s a quick table to help you understand the most important specifications:
Specification Type | Description |
---|---|
Flatness | The sheet should lie perfectly flat without waves, warps, bends, or creases. |
Finish Types | Gloss finish should be smooth and clear; matte finish should be less reflective but still smooth; textured finish is for bonding. |
Fiber Orientation | Fibers should be straight and correctly oriented to ensure cosmetic appearance and mechanical properties. |
Cutting Tolerances | High-quality sheets should measure within ±.125” of the stated dimensions. |
By focusing on these metrics, you can confidently choose a sheet that meets your project’s requirements. Whether you’re looking for a lightweight option or a sheet with a specific finish, understanding these details makes the process much easier.
Avoiding Common Pitfalls
Mistakes to avoid when buying carbon fiber sheets
Buying carbon fiber sheets can feel tricky, especially if you’re new to it. I’ve made a few mistakes myself, so let me share what I’ve learned to help you avoid the same pitfalls. Here’s a list of common errors and how to steer clear of them:
- Ignoring flatness: Always check if the sheet lies perfectly flat. A warped or wavy sheet can ruin your project’s precision.
- Overlooking the finish: For glossy sheets, look for a smooth, glass-like surface without bumps. Matte finishes should feel smooth but not overly reflective.
- Skipping fiber alignment checks: Misaligned fibers weaken the sheet and affect its appearance. Make sure the fibers are straight and evenly oriented.
- Forgetting to verify dimensions: Measure the sheet to ensure it matches the stated size. High-quality sheets should stay within ±.125″ of the listed dimensions.
- Choosing the wrong finish for your needs: Textured finishes work best for bonding, as they resemble fine fabric and improve adhesion.
I’ve learned that rushing through these checks can lead to costly mistakes. Take your time to inspect the sheet carefully. It’s worth the effort to get it right the first time.
🛠️ Pro Tip: Bring a straight edge or ruler when shopping in person. It’s a quick way to check flatness and dimensions on the spot.
How to spot counterfeit or low-quality products
Counterfeit or low-quality carbon fiber sheets are more common than you’d think. I’ve seen people fall for these, and it’s frustrating. But don’t worry—I’ve got some tips to help you spot the fakes.
- Inspect the weave pattern: Authentic carbon fiber sheets have consistent, tight weaves. Uneven or loose patterns are red flags.
- Check the finish quality: High-quality sheets have smooth finishes, whether glossy or matte. Rough or uneven surfaces often indicate poor craftsmanship.
- Look for certifications: Reputable sheets come with certifications like ISO 9001. If a seller can’t provide these, think twice before buying.
- Test the weight: Genuine carbon fiber is lightweight yet strong. If the sheet feels heavier than expected, it might be mixed with other materials.
- Examine the price: If the price seems too good to be true, it probably is. Counterfeit products often sell at unusually low prices to lure buyers.
💡 Note: Counterfeit sheets may also lack proper UV protection or durability, which can lead to premature wear and tear.
When in doubt, ask the supplier for a sample. Testing a small piece can reveal a lot about the sheet’s quality. Trust your instincts—if something feels off, it’s better to walk away.
Choosing the right carbon fiber sheet can feel overwhelming, but it doesn’t have to be. Let’s recap the key factors to keep in mind:
- Carbon fiber sheets are lightweight and incredibly strong, offering unmatched mechanical properties.
- Understanding their features—like strength, weight, weave type, and finish—helps you match them to your project.
- Researching manufacturers ensures you get high-quality materials that meet your needs.
Don’t forget to test samples before committing. A quality sheet should lie perfectly flat, with straight fibers and a flawless finish. Whether glossy or matte, the surface should look and feel just right.
Investing in high-quality sheets pays off in the long run. They deliver better performance, last longer, and reduce maintenance costs. From aerospace to DIY projects, the right sheet can transform your ideas into reality.
💡 Pro Tip: Take your time, do your research, and trust your instincts. The effort you put in now will lead to a successful outcome later.
FAQ
What is the best way to cut a carbon fiber sheet?
I recommend using a fine-tooth saw or a Dremel tool for clean cuts. Always secure the sheet with clamps to prevent movement. Don’t forget to wear a mask and goggles—carbon fiber dust can irritate your lungs and eyes.
Can I paint or customize a carbon fiber sheet?
Yes, you can! Sand the surface lightly to help the paint stick, then use a primer before applying your chosen paint. For the best results, use spray paint designed for carbon fiber or plastics.
How do I store carbon fiber sheets properly?
Store them flat in a cool, dry place away from direct sunlight. Avoid stacking heavy objects on top to prevent warping. If possible, keep them in their original packaging to protect the finish.
Are carbon fiber sheets waterproof?
The carbon fiber itself is waterproof, but the resin used in the sheet might not be. For outdoor or wet environments, choose sheets with moisture-resistant resins or apply a protective coating.
Can I use carbon fiber sheets for outdoor projects?
Absolutely! Just make sure the sheet has UV-resistant coatings to prevent sun damage. For humid or wet conditions, pick sheets with moisture-resistant resins to ensure long-lasting durability.
What’s the difference between pre-preg and standard carbon fiber sheets?
Pre-preg sheets come pre-impregnated with resin, making them easier to work with and offering consistent quality. Standard sheets require you to apply resin manually, which gives more flexibility but takes more effort.
How do I bond carbon fiber sheets to other materials?
Use a high-strength epoxy adhesive for the best results. Sand the bonding surface lightly to improve adhesion. Apply the adhesive evenly, then clamp the materials together until the epoxy cures.
Are carbon fiber sheets eco-friendly?
Not entirely. While they’re durable and reduce waste in the long run, manufacturing carbon fiber consumes a lot of energy. However, recycled carbon fiber sheets are a more sustainable option worth considering.
💡 Pro Tip: Always check with your supplier for recycled or eco-friendly options if sustainability is a priority for you.