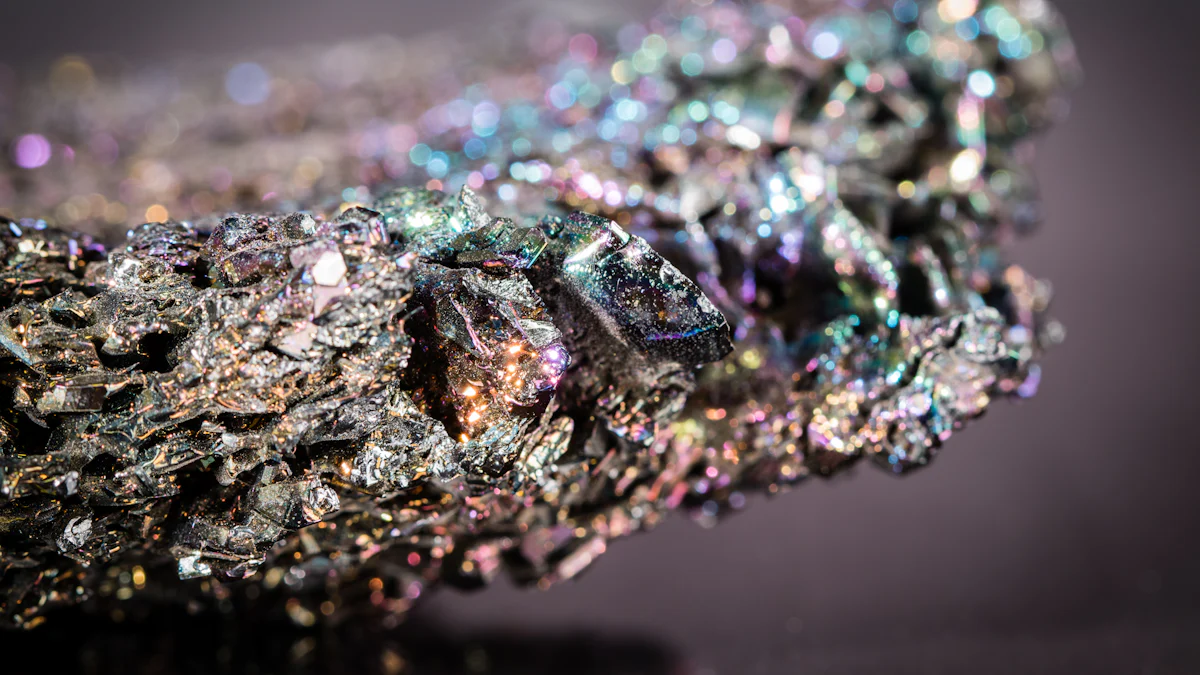
Silicon carbide, a compound of silicon and carbon, is recognized as a groundbreaking material in modern industries. Known for its exceptional hardness, which competes with that of diamond, the Carbon SiC Material is truly remarkable. Its high thermal conductivity allows for efficient heat transfer, and its chemical resistance shields it from corrosion and oxidation. These outstanding properties make the Carbon sic Material essential in challenging environments. From electronics to aerospace and manufacturing, this Carbon SiC Material fuels innovation and boosts performance in a wide range of applications.
Key Takeaways
- Silicon carbide is a highly durable material, second only to diamond in hardness, making it ideal for abrasives and cutting tools that require precision and longevity.
- With exceptional thermal conductivity, silicon carbide effectively manages heat in electronic devices, enhancing performance and preventing overheating in applications like power inverters and thermal management systems.
- The material’s strong chemical resistance allows it to thrive in harsh environments, making it indispensable in industries such as chemical processing and heavy manufacturing.
- Silicon carbide’s lightweight nature and structural integrity make it a game-changer in aerospace and automotive sectors, improving fuel efficiency and performance without compromising safety.
- In renewable energy technologies, silicon carbide enhances efficiency in solar inverters and wind turbines, contributing to sustainable energy solutions by reducing energy losses and extending device lifespan.
Properties of Carbon SiC Material
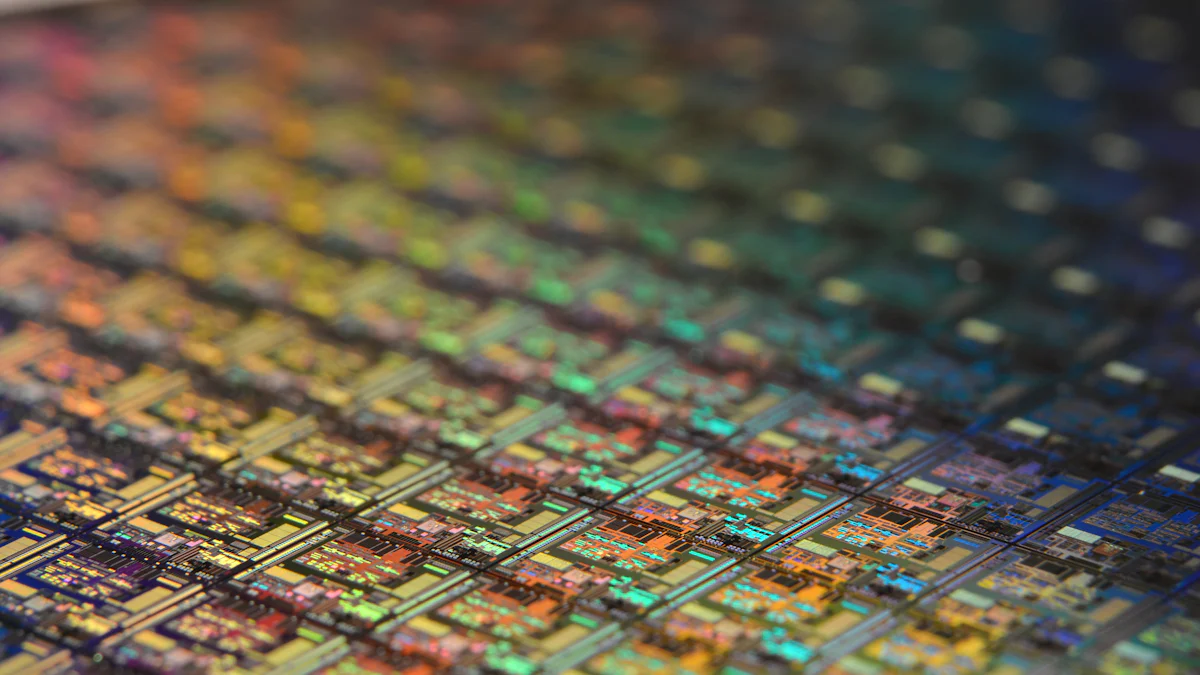
Hardness and Wear Resistance
Comparison with diamond and tungsten carbide
You might already know that hardness is a critical property for materials used in industrial applications. The Carbon SiC Material stands out with its exceptional hardness, second only to diamond. It surpasses tungsten carbide in wear resistance, making it a preferred choice for demanding environments. This material’s crystalline structure contributes to its ability to withstand extreme mechanical stress without deformation.
Applications in abrasives and cutting tools
The hardness of the Carbon SiC Material makes it ideal for abrasives and cutting tools. You’ll find it in grinding wheels, sandpapers, and polishing compounds. These tools deliver precision and durability, even when working with tough materials like metals and ceramics. Its wear resistance ensures a longer lifespan, reducing the need for frequent replacements.
Thermal Conductivity and Stability
Role in heat dissipation and thermal management
Efficient heat dissipation is crucial in many industries, and the Carbon SiC Material excels in this area. Its high thermal conductivity allows it to transfer heat quickly, preventing overheating in electronic devices and machinery. You’ll see it used in heat sinks and thermal management systems where maintaining optimal temperatures is essential.
Performance in high-temperature environments
This material also performs exceptionally well in high-temperature environments. It retains its structural integrity and thermal stability even at temperatures exceeding 1,000°C. This makes it a reliable choice for applications like furnaces, kilns, and other high-heat industrial processes.
Chemical Resistance and Durability
Resistance to corrosion and oxidation
The Carbon SiC Material resists corrosion and oxidation, even when exposed to harsh chemicals or extreme conditions. Its chemical stability ensures that it doesn’t degrade over time, making it suitable for environments where other materials might fail.
Usability in harsh industrial conditions
You’ll find this material in industries that demand durability and reliability. It withstands abrasive chemicals, high pressures, and fluctuating temperatures. This makes it indispensable in sectors like chemical processing, oil and gas, and heavy manufacturing.
Electrical and Semiconductor Properties
Wide bandgap and high efficiency in power electronics
The Carbon SiC Material offers a wide bandgap, which makes it a standout choice in power electronics. This property allows it to handle higher voltages and temperatures compared to traditional silicon-based materials. You’ll notice that devices made with this material operate more efficiently, reducing energy losses during power conversion. Its ability to minimize heat generation also extends the lifespan of electronic components.
In power electronics, efficiency is everything. The Carbon SiC Material enables the creation of smaller, lighter, and more energy-efficient devices. For instance, it plays a critical role in power inverters used in renewable energy systems, ensuring optimal performance under demanding conditions.
Applications in high-frequency and high-voltage devices
High-frequency and high-voltage devices demand materials that can perform reliably without overheating or breaking down. The Carbon SiC Material excels in these applications. Its high thermal conductivity and electrical stability make it ideal for use in radio frequency (RF) amplifiers, high-voltage diodes, and MOSFETs.
You’ll find this material in devices that power telecommunications, radar systems, and industrial machinery. Its ability to operate at high frequencies ensures faster data transmission and improved system performance. Additionally, its durability under high-voltage conditions makes it a preferred choice for electric grids and power distribution systems.
Lightweight and Structural Integrity
Benefits in aerospace and automotive industries
The lightweight nature of the Carbon SiC Material makes it invaluable in aerospace and automotive industries. Reducing weight is crucial for improving fuel efficiency and performance. You’ll see this material used in components like brake discs, engine parts, and structural panels. Its high strength-to-weight ratio ensures durability without adding unnecessary bulk.
In aerospace, this material contributes to the development of heat shields and lightweight armor. These applications enhance safety and efficiency in aircraft and spacecraft, where every ounce matters.
Comparison with traditional materials like steel and aluminum
When compared to steel and aluminum, the Carbon SiC Material offers superior performance in many areas. It is lighter than steel yet provides comparable strength. Unlike aluminum, it maintains its structural integrity at high temperatures. This makes it a better choice for applications requiring both heat resistance and mechanical strength.
For example, in automotive manufacturing, replacing steel components with this material reduces vehicle weight, leading to better fuel economy. In aerospace, it outperforms aluminum in high-stress environments, ensuring reliability during critical missions.
Applications of Carbon SiC Material in Modern Industries
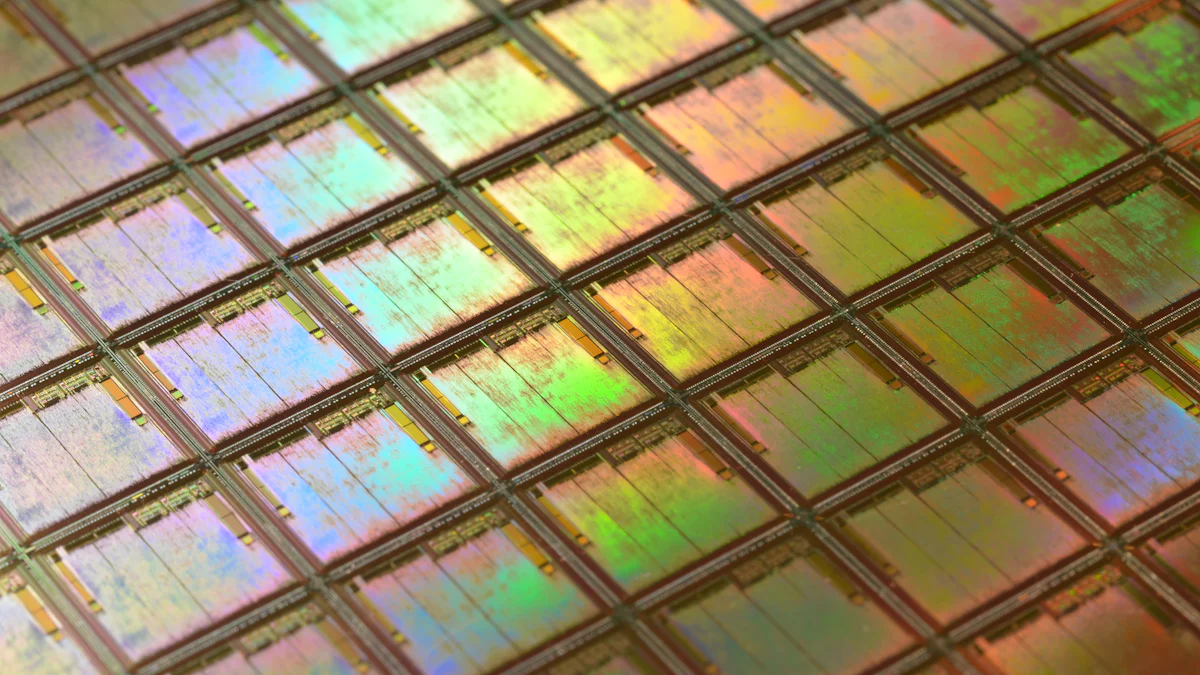
Electronics and Power Devices
Use in MOSFETs, diodes, and other semiconductors
You’ll find the Carbon SiC Material playing a vital role in modern semiconductors like MOSFETs and diodes. Its wide bandgap allows these devices to handle higher voltages and operate efficiently under extreme conditions. This material enhances the performance of power electronics by reducing energy losses and improving switching speeds. For instance, in renewable energy systems, it ensures smooth power conversion, making it a preferred choice for solar inverters and electric grids.
Advantages in high-temperature and high-voltage systems
High-temperature and high-voltage systems demand materials that can endure stress without compromising performance. The Carbon SiC Material excels in these environments. It maintains stability at elevated temperatures and supports efficient energy transfer in high-voltage applications. This makes it indispensable in industries like telecommunications, where reliability and efficiency are critical.
Automotive and Transportation
Role in electric vehicle (EV) components
Electric vehicles rely on advanced materials to improve efficiency and reduce weight. The Carbon SiC Material is a game-changer in this field. It’s used in power inverters and chargers, ensuring faster charging and better energy management. By enhancing thermal conductivity, it prevents overheating in EV components, contributing to longer battery life and improved vehicle performance.
Use in braking systems and engine parts
In braking systems, the Carbon SiC Material provides exceptional wear resistance and durability. You’ll see it in brake discs, where it ensures consistent performance under high friction and heat. It’s also used in engine parts, where its lightweight nature and thermal stability improve fuel efficiency and reduce emissions. These benefits make it a valuable material in modern transportation.
Aerospace and Defense
Applications in lightweight armor and heat shields
The aerospace and defense sectors demand materials that combine strength and lightness. The Carbon SiC Material meets these requirements. It’s used in lightweight armor, offering protection without adding unnecessary weight. In heat shields, it withstands extreme temperatures, ensuring safety during re-entry or high-speed flight.
Use in turbine components and space exploration
Turbine components require materials that can endure high temperatures and mechanical stress. The Carbon SiC Material delivers exceptional performance in these applications. In space exploration, it’s used in spacecraft components, where its durability and lightweight nature are critical for mission success. Its ability to perform in harsh environments makes it a cornerstone of aerospace innovation.
Energy and Renewable Technologies
Role in solar inverters and wind turbines
You’ll find the Carbon SiC Material playing a crucial role in renewable energy systems. In solar inverters, it ensures efficient power conversion by reducing energy losses. This material’s high thermal conductivity helps manage heat, allowing inverters to operate reliably under intense sunlight. Its durability also extends the lifespan of these devices, making them more cost-effective over time.
In wind turbines, this material contributes to the efficiency of power electronics. It supports high-voltage operations, ensuring smooth energy transfer from the turbine to the grid. Its lightweight nature reduces the overall weight of turbine components, improving performance and reducing maintenance needs.
Use in nuclear and thermal power plants
In nuclear and thermal power plants, you’ll see this material used in critical components. Its resistance to extreme temperatures and harsh chemicals makes it ideal for reactor cores and heat exchangers. It maintains its structural integrity even under intense radiation, ensuring safety and reliability.
Thermal power plants benefit from its ability to withstand high heat and mechanical stress. It’s used in boiler linings and other high-temperature equipment, where its durability reduces wear and tear. This ensures uninterrupted operation and lowers maintenance costs, making it an invaluable asset in energy production.
Industrial and Manufacturing Processes
Applications in abrasives, cutting tools, and grinding wheels
The Carbon SiC Material is a cornerstone in industrial manufacturing. You’ll find it in abrasives, cutting tools, and grinding wheels. Its exceptional hardness allows it to cut through tough materials like metals and ceramics with precision. This material’s wear resistance ensures these tools last longer, reducing downtime and replacement costs.
Grinding wheels made with this material deliver consistent performance, even under heavy use. They’re essential in industries like automotive and aerospace, where precision and durability are critical.
Use in kiln furniture and refractory materials
In high-temperature manufacturing, this material shines in kiln furniture and refractory applications. Kiln furniture made from it supports heavy loads while withstanding extreme heat. This ensures uniform firing in ceramics and glass production.
Refractory materials made with this compound resist thermal shock and chemical corrosion. You’ll see them used in furnaces, where they maintain stability under fluctuating temperatures. This reliability improves efficiency and reduces operational costs in manufacturing processes.
Silicon carbide stands out with its unmatched hardness, excellent thermal conductivity, and strong chemical resistance. These properties make it a versatile material for industries like electronics, aerospace, and energy. You’ve seen how it enhances efficiency in power devices, strengthens lightweight components, and withstands extreme conditions. Its ability to improve performance and durability drives innovation in modern technologies. By choosing silicon carbide, you embrace a material that not only meets today’s industrial challenges but also paves the way for future advancements.
FAQ
What makes silicon carbide better than traditional materials like steel or aluminum?
Silicon carbide offers superior strength-to-weight ratio, higher thermal stability, and better wear resistance. Unlike steel, it is lightweight and resists corrosion. Aluminum cannot match its performance in high-temperature environments. These advantages make it ideal for industries like aerospace and automotive.
Can silicon carbide be recycled?
Yes, you can recycle silicon carbide. Many industries collect and reuse it in applications like abrasives or refractory materials. Recycling helps reduce waste and lowers production costs, making it an eco-friendly option for sustainable manufacturing.
Is silicon carbide safe to use in high-temperature environments?
Absolutely! Silicon carbide maintains its structural integrity and thermal stability even at temperatures exceeding 1,000°C. This makes it a reliable choice for furnaces, kilns, and other high-heat applications where safety and durability are critical.
How does silicon carbide improve energy efficiency in electronics?
Its wide bandgap and high thermal conductivity reduce energy losses in power devices. You’ll notice improved efficiency in applications like solar inverters and electric vehicle chargers. It also minimizes heat generation, extending the lifespan of electronic components.
Where can I find silicon carbide in everyday products?
You’ll find it in grinding wheels, sandpapers, and cutting tools. It’s also present in electric vehicle components, solar panels, and even lightweight armor. Its versatility ensures its presence in both industrial and consumer products.