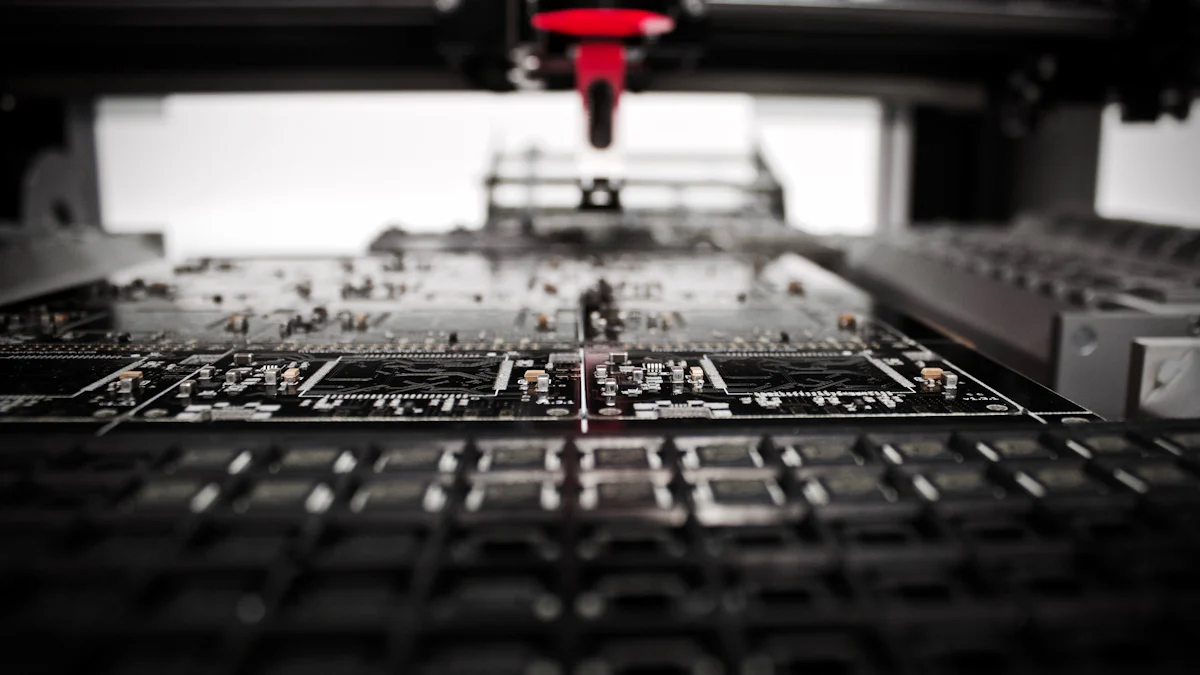
Graphite susceptors play a vital role in semiconductor manufacturing. These components handle extreme temperatures with ease, making them indispensable in processes like chemical vapor deposition (CVD) and epitaxy. Their high thermal conductivity ensures precise temperature control, while uniform heating improves the quality of silicon carbide (SiC) layers. Additionally, their resistance to corrosion and degradation enhances durability, reducing contamination risks. Advanced features like silicon carbide coating on graphite and sic coating further boost their performance. Pyrolytic graphite coatings also contribute to improved yield and extended lifespan, making graphite susceptors essential for cost-effective and high-quality semiconductor production.
Key Takeaways
- Graphite susceptors are important for making semiconductors. They keep heat steady and spread it evenly.
- They conduct heat well, helping control temperature for key processes like CVD.
- Graphite does not rust or break down easily, making it last longer and keeping production clean.
- Adding coatings like silicon carbide (SiC) makes graphite susceptors work better and last longer.
- They save money by needing fewer repairs and replacements.
- Graphite susceptors can be customized to fit specific needs, improving accuracy and performance.
- Recycling and energy-saving methods make them a greener, eco-friendly option.
- Using good-quality graphite susceptors improves results and lowers production costs.
Understanding Graphite Susceptors
What Are Graphite Susceptors?
Graphite susceptors are critical components in semiconductor manufacturing. They act as trays or bases that support silicon carbide (SiC) wafers during high-temperature processes. These susceptors are often coated with SiC to enhance their performance. Their primary role is to provide thermal stability and uniform heat distribution, which are essential for producing high-quality epitaxial materials.
In semiconductor production, these components must meet strict requirements. They need to resist extreme temperatures, maintain consistent thermal conductivity, and withstand chemical exposure. Their ability to handle thermal shock also ensures reliability in demanding environments. This combination of properties makes graphite susceptors indispensable in processes like chemical vapor deposition (CVD) and epitaxy.
Key Properties of Graphite
Graphite stands out due to its unique physical and chemical properties, which make it ideal for semiconductor applications. Here’s what makes it special:
- Thermal Conductivity: Graphite efficiently dissipates heat, ensuring stability in high-temperature processes.
- Chemical Stability: It resists corrosion and degradation, even in harsh chemical environments.
- Electrical Conductivity: Its hexagonal structure allows electrons to move freely, making it suitable for electrical applications.
- Mechanical Strength: Graphite can endure significant mechanical stress, ensuring durability during manufacturing.
- Self-Lubrication: Its layered structure reduces friction, improving machining efficiency and extending tool life.
Graphite also has a high specific heat capacity, which helps it maintain stability at elevated temperatures. It can withstand temperatures exceeding 2,700°C in inert atmospheres and has a low coefficient of thermal expansion. These properties ensure dimensional stability, even under fluctuating temperatures.
Why Graphite Is Ideal for Semiconductor Manufacturing
Graphite’s properties make it a top choice for semiconductor production. Its thermal conductivity surpasses many other materials, allowing it to handle the intense heat required for processes like silicon crystal growth. The material’s chemical stability ensures it resists corrosion, reducing contamination risks and extending its lifespan.
Compared to other materials, graphite offers several advantages. It is lightweight yet robust, making it easier to handle in manufacturing environments. When combined with SiC coatings, it provides enhanced heat absorption and distribution. This ensures uniform heating during epitaxial growth, which improves the quality of semiconductor wafers.
Graphite susceptors also contribute to cost-effectiveness. Their durability reduces the need for frequent replacements, saving time and resources. These benefits, combined with their ability to deliver precision and reliability, make graphite susceptors a cornerstone of modern semiconductor manufacturing.
Applications of Graphite Susceptors in Semiconductor Production
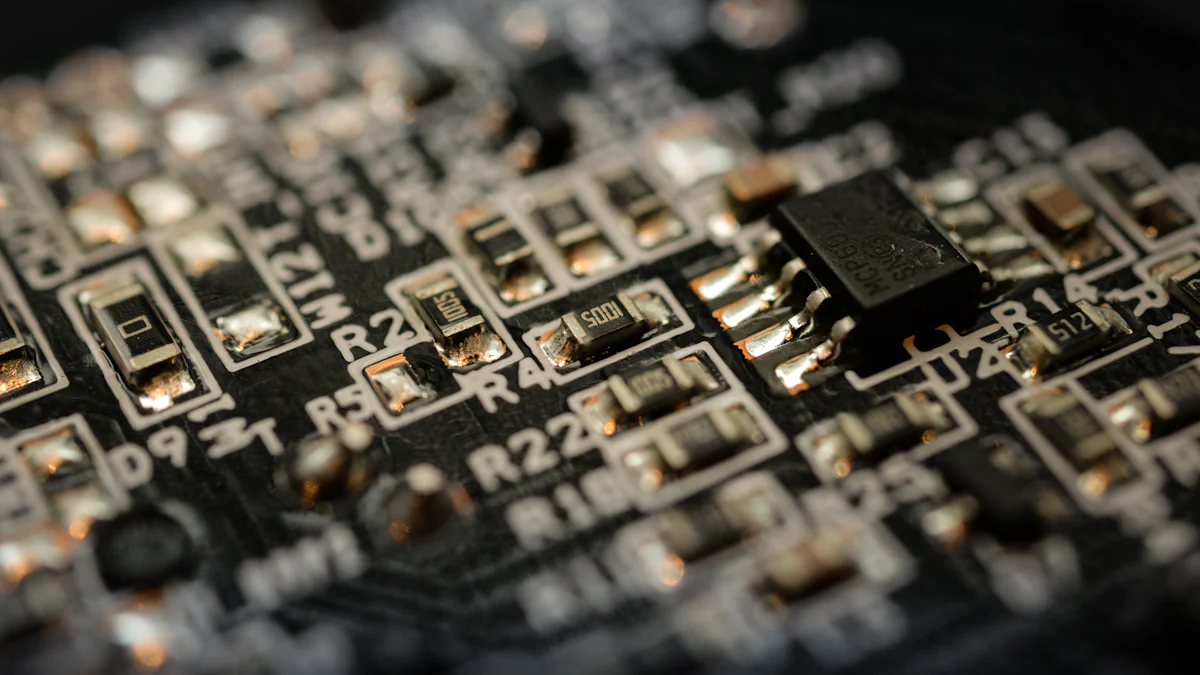
Role in Chemical Vapor Deposition (CVD)
Graphite susceptors are indispensable in the chemical vapor deposition (CVD) process. They serve as the foundation for single-crystal substrates, providing both support and heat. This ensures the uniformity and purity of the thin films deposited during the process. The high-temperature resistance and thermal conductivity of graphite susceptors allow them to maintain stable and consistent heating, even under the extreme conditions of CVD.
By ensuring thermal stability, these components directly impact the quality of epitaxial materials. The uniform heat distribution they provide helps prevent defects in the deposited layers. Additionally, their chemical stability ensures they can withstand the harsh chemical environment of CVD without degrading. This makes them a reliable choice for producing high-quality semiconductor materials.
Importance in Epitaxy and Thin-Film Deposition
In epitaxy and thin-film deposition, graphite susceptors play a critical role in achieving precision and quality. They act as a stable platform for substrates, ensuring uniform heating throughout the process. This uniformity is essential for the growth of high-quality epitaxial layers, which are vital for advanced semiconductor devices.
Graphite susceptors, often coated with silicon carbide, enhance heat transfer to the wafers. This controlled heat distribution ensures the thin films are deposited evenly, reducing the risk of defects. In metal-organic chemical vapor deposition (MOCVD), for example, the susceptor plate provides a stable surface for epitaxial growth. This stability and precision are key to producing semiconductor wafers with consistent properties.
Use in Wafer Production and Etching Processes
Graphite susceptors also play a significant role in wafer production and etching processes. Their ability to manage heat precisely ensures high-quality epitaxial growth and reduces defect rates. They can withstand extreme temperatures without warping or cracking, which is crucial for maintaining the integrity of the wafers.
Here are some of the benefits they bring to these processes:
- Enable precise thermal management.
- Maintain dimensional stability under extreme conditions.
- Ensure consistent results during heating and cooling cycles.
- Minimize the risk of defects during production.
By providing thermal stability and uniformity, graphite susceptors directly influence the quality of semiconductor devices. Their durability and efficiency make them a valuable asset in modern wafer production.
Benefits of Graphite Susceptors
Thermal Stability and Heat Resistance
Graphite susceptors excel in high-temperature environments, making them a cornerstone of semiconductor manufacturing. Their ability to resist degradation under extreme heat ensures long-term reliability. This is especially important in processes like chemical vapor deposition (CVD), where temperatures can soar. High-purity graphite provides the thermal stability needed to handle molten silicon, a critical step in producing high-quality wafers.
- Graphite maintains its structural integrity during intense heat exposure, such as in electrical discharge machining (EDM).
- It endures thermal shocks, ensuring consistent performance even in demanding conditions.
This combination of heat resistance and stability allows graphite susceptors to deliver reliable results, even in the most challenging manufacturing processes.
Uniform Heat Distribution for Precision
Precision is everything in semiconductor production, and graphite susceptors deliver it through uniform heat distribution. Their high thermal conductivity ensures even heating, which is crucial for processes like metal-organic chemical vapor deposition (MOCVD). This uniformity minimizes temperature variations, leading to better yields and higher-quality products.
Additionally, the mechanical stability of graphite susceptors prevents deformation under high heat. This is vital because even slight distortions can cause defects in the final product. By maintaining their shape and ensuring consistent heat transfer, these components help manufacturers achieve the precision required for advanced semiconductor devices.
Cost-Effectiveness and Longevity
Graphite susceptors offer a cost-effective solution for semiconductor manufacturing. Their durability reduces the need for frequent replacements, saving both time and resources. When coated with materials like silicon carbide (SiC), they gain enhanced thermal stability and chemical resistance. This extends their lifespan and makes them a preferred choice for high-quality semiconductor fabrication.
- SiC-coated susceptors combine excellent heat resistance with chemical inertness, ensuring long-term performance.
- Their ability to withstand harsh manufacturing conditions reduces maintenance costs over time.
By balancing performance and longevity, graphite susceptors provide a reliable and economical option for manufacturers aiming to optimize their production processes.
Challenges in Using Graphite Susceptors
Material Limitations and Oxidation Risks
Graphite susceptors, while highly effective, face certain material challenges. One of the most significant issues is their susceptibility to oxidation. When exposed to oxygen at high temperatures, graphite can degrade, leading to reduced performance and a shorter lifespan. This makes it essential to use protective coatings, such as silicon carbide (SiC), to shield the material from oxidation. These coatings not only enhance durability but also improve thermal resistance, making the susceptors more reliable in demanding environments.
Another limitation is the brittleness of graphite. Although it offers excellent thermal and mechanical properties, it can crack or chip under mechanical stress. This can pose challenges during handling or installation in manufacturing systems. Manufacturers often address this by optimizing the design and incorporating advanced surface treatments to strengthen the material.
Tip: Regular maintenance and proper handling can significantly extend the lifespan of graphite susceptors, even in harsh conditions.
Manufacturing Precision and Cost Challenges
Producing graphite susceptors with high precision is no small feat. The manufacturing process must ensure that each susceptor meets strict dimensional and thermal requirements. Even minor imperfections can lead to uneven heating, which affects the quality of semiconductor wafers. Traditional susceptors often suffer from wear and tear due to high temperatures, which can compromise their precision over time. Innovations like SiC coatings and inductively heatable designs have helped address these issues by improving durability and ensuring uniform heat distribution.
However, achieving this level of precision comes with cost implications. Advanced techniques, such as TaC coating and material optimization, have streamlined production processes, reducing expenses while maintaining quality. These advancements make high-performance susceptors more accessible to industries. Additionally, modern susceptors with enhanced thermal efficiency and mechanical stability contribute to consistent processing conditions, which improves product quality and reduces waste.
Despite these improvements, the initial investment in high-precision manufacturing equipment and materials remains significant. For manufacturers, balancing cost and performance is a constant challenge. Yet, the long-term benefits, such as reduced maintenance and higher yields, often outweigh the upfront expenses.
Note: Investing in high-quality graphite susceptors can lead to better results and lower operational costs in the long run.
Innovations in Graphite Susceptor Technology
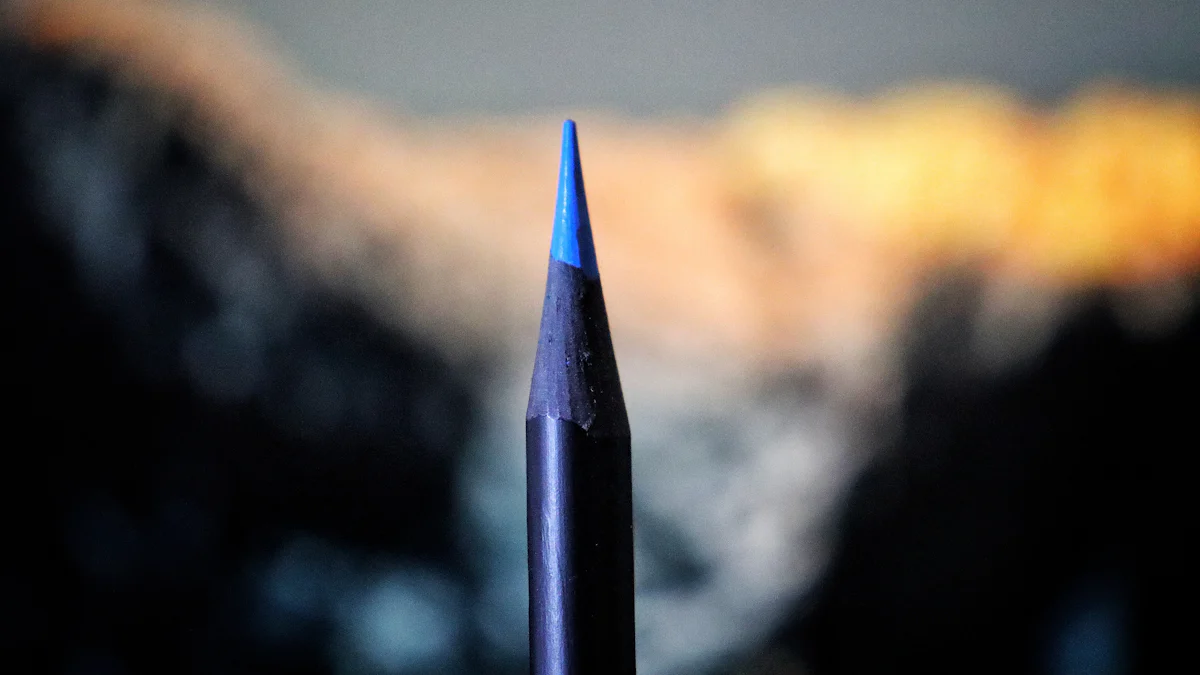
Advanced Coatings for Durability
Advancements in coating technology have significantly improved the durability of graphite susceptors. These coatings enhance mechanical strength, ensuring the susceptor maintains its shape even under extreme heat. This is crucial for precision in semiconductor manufacturing. Improved adhesion between the coating and the graphite substrate has also reduced the risk of delamination, extending the lifespan of these components.
One notable innovation is the introduction of SinTaC susceptors. These are specifically designed for epitaxial growth processes, delivering superior performance. They enhance the quality of semiconductor materials like silicon carbide and aluminum nitride single crystals.
Advancement Type | Description |
---|---|
Enhanced Mechanical Strength | Prevents deformation under high heat, crucial for maintaining precision in manufacturing processes. |
Improved Adhesion | Reduces the risk of delamination under high-stress conditions, translating to longer lifespan. |
Introduction of SinTaC | Designed for superior performance in epitaxial growth processes, improving quality of semiconductor materials. |
These innovations ensure that graphite susceptors remain reliable and efficient, even in demanding environments.
Customization for Emerging Semiconductor Technologies
The growing demand for advanced semiconductor devices has driven the need for customized graphite susceptors. Manufacturers now tailor these components to meet the specific requirements of individual applications, such as high-end LED production and advanced semiconductor manufacturing.
Customization often involves combining high-purity graphite with advanced coatings like silicon carbide. This enhances both thermal performance and mechanical stability, which are essential for modern semiconductor technologies.
- Customization allows susceptors to meet specific operational parameters.
- Tailored designs improve precision and performance.
- This trend is driving new business models and services in the industry.
As semiconductor technologies evolve, the ability to customize graphite susceptors ensures they remain a critical component in cutting-edge manufacturing processes.
Integration with Sustainable Manufacturing Practices
Sustainability has become a key focus in semiconductor production, and graphite susceptors are playing a role in greener manufacturing practices. Innovations in coating techniques have reduced production costs, making these technologies more accessible. Improved energy efficiency in applications has also contributed to more sustainable industrial processes.
Recycling innovations have further enhanced sustainability. Advanced techniques now allow for the recovery and purification of used graphite, reducing waste. Recycling graphite consumes 30% less energy compared to producing new material. This not only lowers costs but also minimizes the environmental footprint of semiconductor manufacturing.
- Recycled graphite reduces energy consumption and raw material demand.
- Graphite’s reusability decreases the need for energy-intensive manufacturing processes.
- Its lower energy requirements for processing make it an eco-friendly choice for large-scale applications.
By integrating these practices, manufacturers can produce high-quality semiconductors while reducing their environmental impact.
Future of Graphite Susceptors in Semiconductor Production
Trends in High-Performance Materials
The semiconductor industry constantly pushes the boundaries of material performance. Graphite susceptors are evolving to meet these demands. Several trends are shaping their future:
- Enhanced thermal performance is becoming a priority as manufacturers aim for higher efficiency and lower energy consumption.
- SiC coatings are gaining popularity in CVD and PECVD applications due to their unmatched thermal stability and durability.
- The rise of SiC-coated graphite susceptors in advanced packaging addresses the growing need for miniaturization and integration in electronic devices.
- Sustainability is a key focus, with SiC coatings extending the lifespan of susceptors and reducing waste.
- Advancements in SiC coating technologies are improving both performance and cost-effectiveness.
These trends highlight the industry’s commitment to innovation. By adopting high-performance materials, manufacturers can achieve better results while addressing environmental concerns.
Role in Next-Generation Semiconductor Technologies
Graphite susceptors are paving the way for next-generation semiconductor technologies. Their ability to withstand extreme conditions makes them indispensable in advanced manufacturing processes. Here’s how they contribute:
- They enable the production of smaller, faster, and more efficient devices, meeting the demands of modern electronics.
- Their unique properties enhance material quality, benefiting cutting-edge fields like quantum computing.
- TaC-coated graphite susceptors provide the thermal stability and mechanical strength needed for high-temperature applications.
- They play a crucial role in processes like silicon carbide epitaxial growth and chemical vapor deposition, essential for advanced semiconductor devices.
- Their versatility supports innovations in additive manufacturing and nanotechnology.
As technology advances, the role of graphite susceptors will only grow. Their contributions to emerging fields ensure they remain a cornerstone of semiconductor production.
Sustainability and Environmental Considerations
Sustainability is becoming a central focus in semiconductor manufacturing, and graphite susceptors are playing a significant role. Recent advancements in recycling have shown that reusing graphite reduces energy consumption by 30% compared to producing new material. This makes recycling a practical and eco-friendly solution.
The reusability of graphite components also minimizes the environmental footprint of semiconductor production. By decreasing the demand for raw materials and energy-intensive processes, manufacturers can reduce waste and conserve resources.
However, sustainability goes beyond recycling. Energy-efficient manufacturing processes and innovations in coating technologies are helping to lower the ecological impact of graphite susceptors. These efforts align with the industry’s broader goal of creating greener and more sustainable production methods.
By integrating these practices, manufacturers can produce high-quality semiconductors while protecting the environment. Graphite susceptors, with their reusability and energy efficiency, are a key part of this transformation.
Graphite susceptors have become indispensable in semiconductor production. Their ability to handle extreme heat and maintain chemical stability ensures consistent performance in high-temperature processes like silicon crystal growth.
Graphite’s chemical stability further enhances its role in thermal management. It resists degradation when exposed to high temperatures, ensuring long-term reliability. This makes it an ideal choice for applications such as silicon crystal growth, where thermal stability is crucial.
These components also deliver precision and cost-effectiveness. Their uniform heat distribution improves wafer quality, while their durability reduces maintenance costs. High-purity graphite prevents contamination during ion implantation, maintaining the integrity of the process.
High-purity graphite is a cornerstone material in high-temperature semiconductor processes, particularly in silicon crystal growth. Crucibles made from graphite provide the necessary thermal stability and chemical inertness to handle molten silicon.
Ongoing innovations continue to address challenges. SiC-coated susceptors enhance thermal resistance, while inductively heatable designs improve product consistency. Modular designs and advancements in gas flow systems optimize production, making graphite susceptors adaptable to evolving industry needs.
- SiC-coated susceptors reduce maintenance costs and downtime.
- Inductively heatable designs ensure uniform heat distribution.
- Modular designs allow scalability for different production needs.
As semiconductor technologies advance, graphite susceptors will remain a cornerstone of innovation, supporting the industry’s push for efficiency, precision, and sustainability.
FAQ
What are graphite susceptors used for in semiconductor manufacturing?
Graphite susceptors support wafers during high-temperature processes like CVD and epitaxy. They ensure uniform heat distribution, thermal stability, and precision, which are essential for producing high-quality semiconductor materials.
Why is graphite preferred over other materials?
Graphite offers excellent thermal conductivity, chemical stability, and mechanical strength. It withstands extreme temperatures and resists corrosion, making it ideal for semiconductor applications. Its lightweight nature also makes handling easier.
How do coatings improve graphite susceptors?
Coatings like silicon carbide (SiC) enhance thermal resistance, durability, and chemical stability. They protect the graphite from oxidation and extend its lifespan, ensuring reliable performance in demanding environments.
Can graphite susceptors be recycled?
Yes! Recycling graphite reduces energy consumption by 30% compared to producing new material. This eco-friendly practice minimizes waste and supports sustainable manufacturing.
Are graphite susceptors customizable?
Absolutely! Manufacturers can tailor graphite susceptors to meet specific needs, such as advanced LED production or next-gen semiconductor technologies. Custom designs improve precision and performance.
What makes graphite susceptors cost-effective?
Their durability reduces the need for frequent replacements. Coatings like SiC further extend their lifespan, lowering maintenance costs. This combination of longevity and reliability makes them a smart investment.
How do graphite susceptors contribute to sustainability?
Graphite’s reusability and energy efficiency make it an eco-friendly choice. Recycling and advanced coating technologies reduce waste and energy use, aligning with greener manufacturing practices.
What industries benefit from graphite susceptors?
Graphite susceptors are widely used in semiconductors, photovoltaics, and new energy sectors. Their role in high-temperature processes makes them indispensable for producing cutting-edge materials.
Tip: Investing in high-quality graphite susceptors ensures better performance and long-term savings.