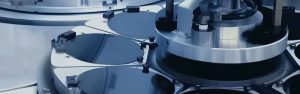
SiC coating on aluminum combines the strength of silicon carbide with the lightweight nature of aluminum. This silicon coating creates a protective layer that enhances the material’s durability and performance. Industries like aerospace and defense rely on this technology to meet demanding conditions.
The adoption of SiC coating has grown rapidly. In 2023, the Aluminum Silicon Carbide Heat Dissipation Materials market was valued at [120million]
This growth highlights the importance of the silicon carbide coating process in modern manufacturing.
The SiC coating process transforms aluminum into a high-performance material. It offers unmatched wear resistance, thermal conductivity, and corrosion protection. These qualities make it a game-changer for industries seeking efficiency and innovation.
Key Takeaways
- SiC coating makes aluminum stronger for tough uses like planes and cars.
- The market for SiC-coated aluminum is growing fast, reaching $325.4 million by 2030.
- SiC coatings protect aluminum from damage, heat, and rust, lasting longer.
- New methods, like special vapor techniques, make coating better and faster.
- Eco-friendly SiC coating lowers harm to nature and cuts production costs.
- Smart tech in factories speeds up making and improves product quality.
- SiC-coated aluminum is used in many things, like electric cars and medical tools.
- New ideas in science will make SiC coatings even better and easier to use.
What is SiC Coating on Aluminum?
Understanding Silicon Carbide (SiC)
Silicon carbide, often called SiC, is a material known for its exceptional strength and resilience. It stands out because of its high hardness, excellent thermal conductivity, and remarkable resistance to wear and corrosion. These qualities make it a top choice for industries that demand materials capable of withstanding extreme conditions.
SiC coatings bring several benefits to the table:
- They enhance the hardness of surfaces.
- They provide outstanding wear and corrosion resistance.
- They offer oxidation resistance, even in high-temperature environments.
- They can be applied to various materials, including metals, ceramics, and plastics.
These properties make silicon carbide a versatile and reliable option for coating applications. Whether it’s protecting components in aerospace or improving the durability of electronics, SiC delivers unmatched performance.
How SiC Coating Interacts with Aluminum
When SiC coating is applied to aluminum, the two materials form a powerful combination. Aluminum is lightweight and easy to work with, but it can be prone to wear and corrosion. SiC coating addresses these weaknesses by creating a protective layer on the aluminum surface.
This layer acts as a shield, enhancing the aluminum’s durability and resistance to harsh conditions. The coating also improves thermal conductivity, allowing aluminum components to handle high temperatures more effectively. This is especially important in industries like automotive and renewable energy, where heat management is critical.
By combining aluminum’s lightweight nature with the strength of SiC, manufacturers can create components that are both efficient and long-lasting. This interaction has revolutionized how aluminum is used in demanding applications.
The Importance of SiC Coating for Aluminum
SiC coating transforms aluminum into a high-performance material. Without this coating, aluminum might struggle in environments with extreme heat, friction, or exposure to corrosive substances. SiC coating ensures that aluminum can thrive in these conditions.
Industries like aerospace, automotive, and electronics rely on this technology to meet their performance standards. For example, SiC-coated aluminum components in electric vehicles help improve energy efficiency and extend the lifespan of critical parts. In renewable energy systems, the coating protects aluminum structures from corrosion caused by harsh weather.
The importance of SiC coating lies in its ability to unlock aluminum’s full potential. It allows manufacturers to use aluminum in ways that were previously impossible, opening the door to innovation across multiple industries.
Benefits of SiC Coating
Superior Durability and Wear Resistance
SiC coating significantly enhances the durability of aluminum. Its high hardness and thermal stability make it an excellent choice for applications requiring wear resistance. Unlike other coatings like titanium nitride (TiN) or diamond-like carbon (DLC), SiC coating provides superior protection against abrasion and mechanical stress. This makes it ideal for industries where components face constant friction or heavy loads.
For example, in manufacturing, SiC-coated aluminum tools last longer and maintain their performance even under extreme conditions. The coating acts as a shield, reducing wear and extending the lifespan of aluminum parts. This durability ensures that industries can rely on SiC-coated components for consistent performance over time.
Enhanced Thermal and Electrical Conductivity
SiC coating doesn’t just protect aluminum—it also improves its thermal and electrical properties. Aluminum already has good conductivity, but the addition of SiC takes it to the next level. The coating allows heat to dissipate more efficiently, which is crucial in industries like electronics and automotive manufacturing.
In electric vehicles, for instance, SiC-coated aluminum components help manage heat generated by batteries and motors. This prevents overheating and ensures optimal performance. Similarly, in electronics, the coating improves the efficiency of heat sinks and other components, keeping devices cool and functional. By enhancing conductivity, SiC coating enables aluminum to perform better in high-temperature environments.
Corrosion Protection in Extreme Conditions
Corrosion can be a major challenge for aluminum, especially in harsh environments. SiC coating provides a robust solution by forming a protective barrier that resists chemical reactions and environmental damage. This makes it invaluable in industries where corrosion resistance is critical.
Some industries that benefit from this protection include:
- Automobile: Lightweight aluminum alloys gain added strength and resistance to road salts and moisture.
- Aviation: Aircraft components withstand exposure to varying temperatures and humidity levels.
- Maritime: Marine applications benefit from the coating’s ability to resist saltwater corrosion.
By preventing corrosion, SiC coating ensures that aluminum components remain reliable and efficient, even in the toughest conditions. This protection reduces maintenance costs and extends the lifespan of critical parts.
Lightweight and High-Performance Advantages
The combination of silicon carbide and aluminum creates a material that’s both lightweight and incredibly strong. This unique pairing offers a perfect balance for industries that demand high performance without adding unnecessary weight. Think about airplanes or electric vehicles. Every pound matters when it comes to efficiency and fuel savings. That’s where SiC-coated aluminum shines.
In aerospace, lightweight materials are essential for reducing fuel consumption and improving flight range. SiC coating enhances aluminum’s strength and durability, making it ideal for structural components like wings and fuselage parts. These parts need to handle extreme stress while staying as light as possible. The coating also protects against wear and corrosion, ensuring these components last longer in challenging environments.
Automotive applications benefit just as much. Electric vehicles, for example, rely on lightweight materials to maximize battery efficiency. SiC-coated aluminum not only reduces the overall weight of the vehicle but also improves the performance of critical parts like battery housings and heat exchangers. This means better energy efficiency and longer-lasting components, which are crucial for modern EVs.
The secret lies in how SiC particles enhance aluminum’s mechanical properties. They boost strength, elasticity, and wear resistance, all while maintaining the material’s lightweight nature. This makes SiC-coated aluminum a game-changer for industries that need to balance performance with efficiency. Whether it’s a car speeding down the highway or a satellite orbiting Earth, this material delivers unmatched results.
Another advantage is its versatility. SiC-coated aluminum can be used in everything from high-speed trains to renewable energy systems. Its lightweight nature makes it easier to transport and install, while its high performance ensures reliability in demanding conditions. This combination of benefits opens up endless possibilities for innovation across industries.
By combining the best of both worlds—lightweight design and high performance—SiC-coated aluminum is setting new standards. It’s not just about making things lighter; it’s about making them better, stronger, and more efficient. This is why so many industries are turning to this advanced material to meet their toughest challenges.
SiC Coating Application Techniques
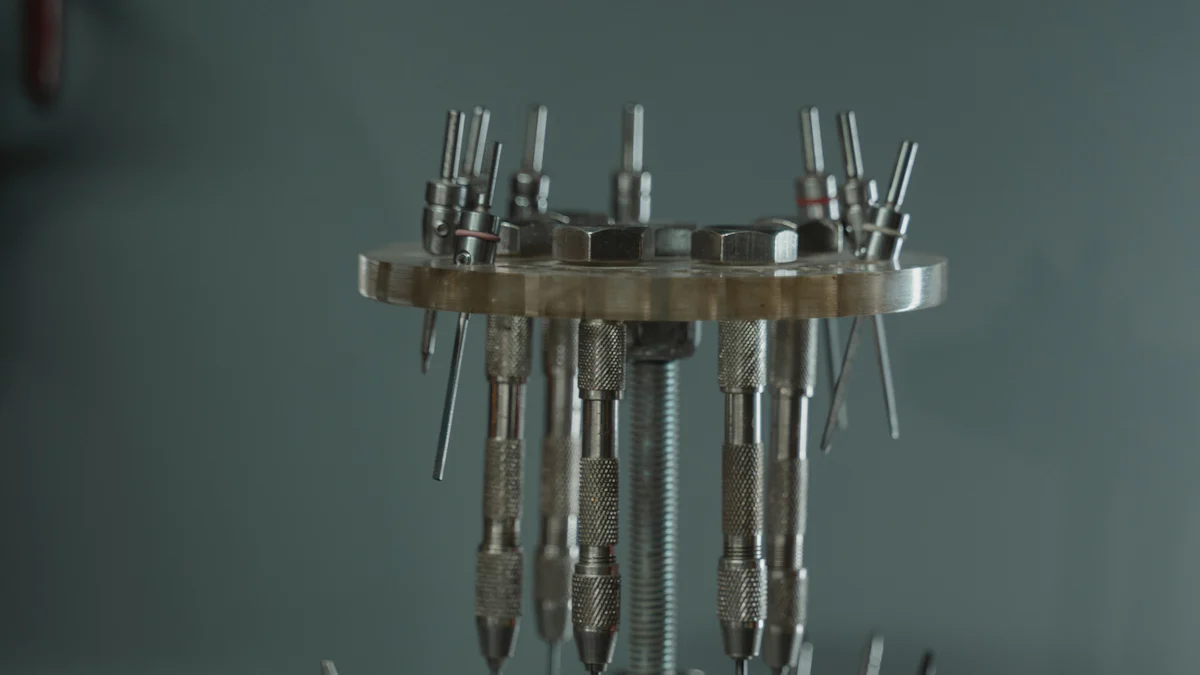
Overview of Coating Methods
Applying SiC coating to aluminum involves several advanced techniques. Each method has unique advantages and challenges, making them suitable for different applications. Here’s a quick comparison of the most commonly used methods:
Technique | Advantages | Challenges |
---|---|---|
Chemical Vapor Deposition (CVD) | Good adhesion, suitable for complex shapes, precise control over coating properties | Hazardous materials, high costs, low raw material utilization |
Physical Vapor Deposition (PVD) | Precise control over thickness and composition, dense coatings | High equipment costs, slow deposition rate, insufficient adhesion |
Spraying Technique | Simple and cost-effective | Weak adhesion, poorer uniformity, lower oxidation resistance |
Electrochemical Deposition | Uniform coating growth, applicable in specific fields | Limited to specific applications, may require additional processing |
Chemical Vapor Deposition (CVD)
CVD is a popular choice for applying SiC coating. It involves a chemical reaction that deposits a thin, uniform layer of silicon carbide onto the aluminum surface. This method works well for complex shapes and ensures excellent adhesion. However, it requires hazardous materials and can be expensive due to high preparation costs.
Physical Vapor Deposition (PVD)
PVD uses a vacuum environment to deposit SiC onto aluminum. This technique offers precise control over the coating’s thickness and composition, making it ideal for high-precision applications. Despite its benefits, PVD can struggle with uniform coverage and adhesion. The process also demands costly equipment and takes longer to complete.
Plasma Spray Coating
Plasma spray coating is a simpler and more cost-effective method. It involves spraying molten SiC particles onto the aluminum surface. While this technique is easy to implement, it often results in weaker adhesion and less uniform coatings. It may also provide lower resistance to oxidation compared to other methods.
Challenges in Achieving Optimal Coating
Applying SiC coating to aluminum isn’t without its hurdles. One major challenge is ensuring strong adhesion between the coating and the aluminum substrate. Techniques like spraying often struggle with this, leading to weaker bonds. Another issue is achieving uniform coverage, especially for complex shapes. Methods like PVD and CVD excel in precision but come with high costs and slower production rates.
Environmental concerns also play a role. Some methods, such as CVD, use hazardous chemicals that require careful handling and disposal. Additionally, the high energy consumption of these processes can impact sustainability efforts. Overcoming these challenges requires innovative solutions that balance performance, cost, and environmental impact.
Innovations in Application Processes
Recent advancements have addressed many of the challenges in SiC coating application. For instance, plasma-enhanced chemical vapor deposition (PECVD) has improved coating precision and efficiency. This technique combines the benefits of CVD with enhanced control, making it a game-changer for industries requiring high-performance coatings.
Automation and artificial intelligence (AI) have also revolutionized the process. AI-driven systems optimize production parameters, reducing errors and increasing scalability. These systems ensure consistent quality while lowering operational costs.
Nanotechnology is another exciting development. Researchers have created nanoscale SiC coatings that enhance wear resistance and thermal conductivity. These coatings offer superior performance while using fewer materials, making them both cost-effective and sustainable.
Innovation Type | Description |
---|---|
Advanced Deposition Techniques | Techniques like plasma-enhanced chemical vapor deposition (PECVD) improve coating precision and efficiency. |
Automation and AI | AI-driven systems optimize production parameters, reducing human error and increasing scalability. |
Nanotechnology | Development of nanoscale SiC coatings enhances properties like wear resistance and thermal conductivity. |
These innovations are paving the way for more efficient, cost-effective, and environmentally friendly SiC coating processes. They ensure that industries can continue to rely on this technology for high-performance applications.
Advancements in SiC Coating Technology in 2025
Breakthroughs in Coating Efficiency
In 2025, advancements in SiC coating technology have made the process faster and more precise. Industries now benefit from cutting-edge deposition techniques that ensure uniform coatings with minimal waste. These methods improve the overall quality of the coating, making it more durable and reliable.
Automation has also played a big role in boosting efficiency. AI-driven systems now monitor and adjust production parameters in real time. This reduces errors and speeds up the process, allowing manufacturers to meet growing demand without compromising quality.
Nanotechnology has taken SiC coating to the next level. Engineers have developed nanoscale coatings that enhance wear resistance and thermal conductivity. These coatings use fewer materials while delivering superior performance, making them both efficient and sustainable.
- Key advancements in 2025 include:
- Advanced deposition techniques for better precision.
- AI and automation for faster, more consistent production.
- Nanoscale coatings with enhanced properties.
These breakthroughs ensure that SiC coating remains a top choice for industries requiring high-performance materials.
Cost-Effective and Scalable Solutions
Scaling SiC coating applications has become more affordable in 2025. Countries around the world have adopted innovative approaches to reduce costs and improve accessibility.
Country | Advancements in SiC Coating Applications |
---|---|
China | Large-scale production focusing on lowering costs and improving techniques. |
Germany | Development of high-performance coatings for industrial applications. |
India | Focus on energy-efficient applications and improving accessibility. |
Japan | Integration of SiC coatings into next-gen semiconductor devices for enhanced performance. |
These solutions outperform traditional methods in both speed and cost. Traditional processes often require expensive equipment and take longer to complete. In contrast, modern techniques are faster and use fewer resources, leading to significant savings. This makes SiC coating more accessible to industries of all sizes.
Eco-Friendly and Sustainable Coating Methods
Sustainability has become a priority in SiC coating technology. In 2025, manufacturers are adopting eco-friendly methods that reduce environmental impact. For example, plasma-enhanced chemical vapor deposition (PECVD) uses less energy and produces fewer emissions compared to older techniques.
Recycling has also gained traction. Companies now reclaim and reuse materials during the coating process, minimizing waste. This approach not only benefits the environment but also lowers production costs.
Nanotechnology contributes to sustainability as well. Nanoscale coatings require fewer raw materials, reducing resource consumption. These coatings also last longer, which means fewer replacements and less waste over time.
Tip: Choosing sustainable SiC coating methods not only helps the planet but also saves money in the long run.
By focusing on eco-friendly practices, the industry is paving the way for a greener future while maintaining high performance.
Integration with Smart Manufacturing Technologies
Smart manufacturing has transformed how industries produce and innovate. SiC coating technology has embraced this shift, integrating seamlessly with advanced manufacturing systems. This integration has unlocked new possibilities for efficiency, precision, and scalability.
How Smart Manufacturing Enhances SiC Coating
Smart manufacturing uses technologies like IoT (Internet of Things), AI, and robotics to optimize production. These tools make SiC coating processes faster and more reliable. For example, IoT sensors monitor coating conditions in real time. They track temperature, pressure, and material flow, ensuring consistent quality.
AI systems analyze this data to predict and prevent issues. If a problem arises, the system adjusts the process automatically. This reduces waste and downtime. Robotics also plays a key role. Robots handle repetitive tasks like applying coatings, improving speed and accuracy.
Note: Smart manufacturing doesn’t just improve efficiency. It also reduces human error, making the process safer and more sustainable.
Benefits of Integration
The combination of SiC coating and smart manufacturing offers several advantages:
- Improved Precision: Automated systems ensure uniform coatings, even on complex shapes.
- Faster Production: Robotics and AI speed up the process, meeting high demand.
- Cost Savings: Reduced waste and energy use lower production costs.
- Scalability: Smart systems adapt to different production scales with ease.
Technology Used | Benefit to SiC Coating Process |
---|---|
IoT Sensors | Real-time monitoring for consistent quality |
AI Systems | Predictive adjustments to prevent errors |
Robotics | Faster, more accurate application of coatings |
Digital Twins | Simulations to optimize coating parameters |
Real-World Applications
Industries are already seeing the impact of this integration. In aerospace, manufacturers use digital twins to simulate SiC coating on aircraft parts. This helps them find the best parameters before production begins. In electronics, IoT-enabled systems ensure heat sinks receive precise coatings, improving device performance.
Automotive companies also benefit. AI-driven robots apply SiC coatings to EV components, enhancing durability and efficiency. These examples show how smart manufacturing makes SiC coating more effective and accessible.
Tip: Companies adopting smart manufacturing gain a competitive edge. They produce better products faster and at lower costs.
The integration of SiC coating with smart manufacturing technologies is shaping the future of production. It combines innovation with practicality, delivering results that meet the demands of modern industries.
Applications of SiC-Coated Aluminum
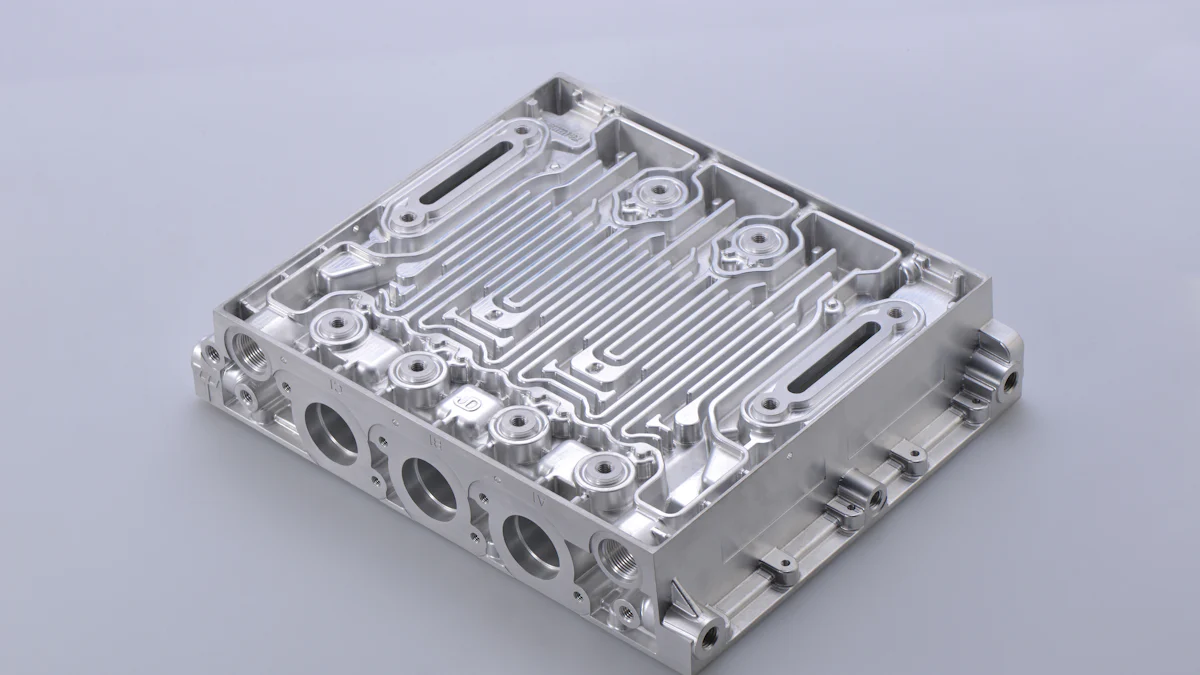
Aerospace and Defense Applications
SiC-coated aluminum has become a cornerstone in aerospace and defense industries. Its unique properties make it ideal for high-performance structural components. Aircraft manufacturers use SiC-coated aluminum matrix composites (AMCs) in critical parts like landing gear, high-pressure seals, and even seats. These composites offer higher strength and stiffness, allowing them to perform well in extreme conditions.
One of the biggest advantages is weight reduction. SiC-coated aluminum components are up to 30% lighter than traditional materials. This weight savings translates to better fuel efficiency and improved flight range. The addition of SiC also enhances the hardness and tensile strength of aluminum, making it suitable for parts that endure high stress.
Thermal spray deposition techniques are often used to apply SiC coatings in aerospace. These coatings improve surface properties without compromising the aluminum’s flexibility. This balance of strength and ductility is crucial for aircraft parts that face constant wear and tear.
In defense, SiC-coated aluminum plays a role in creating lightweight yet durable armor and structural components. Its ability to resist corrosion and wear ensures long-lasting performance, even in harsh environments.
Automotive and Electric Vehicle Components
The automotive industry has embraced SiC-coated aluminum for its ability to enhance performance while keeping vehicles lightweight. Electric vehicles (EVs), in particular, benefit greatly from this technology. SiC-coated aluminum is used in battery housings, heat exchangers, and motor components. These parts need to handle high temperatures and mechanical stress, and SiC coating ensures they perform reliably.
Lightweight materials are essential for improving EV efficiency. By reducing the overall weight of the vehicle, SiC-coated aluminum helps extend battery life and increase driving range. It also improves the durability of critical components, reducing the need for frequent replacements.
In traditional vehicles, SiC-coated aluminum is used in engine parts and braking systems. The coating’s wear resistance ensures these components last longer, even under heavy use. Its corrosion resistance also makes it ideal for parts exposed to moisture and road salts.
Automotive manufacturers are also exploring SiC-coated aluminum for lightweight chassis and structural components. This innovation could lead to safer, more fuel-efficient vehicles in the future.
Electronics and Semiconductor Devices
SiC-coated aluminum has revolutionized the electronics and semiconductor industries. Its excellent thermal conductivity makes it a top choice for heat sinks and other cooling components. These parts play a critical role in preventing electronic devices from overheating.
In semiconductor manufacturing, SiC-coated aluminum is used in wafer handling and processing equipment. The coating’s hardness and wear resistance ensure these tools maintain their precision over time. This is especially important in industries like telecommunications and computing, where even minor defects can cause significant issues.
The lightweight nature of SiC-coated aluminum also makes it easier to integrate into compact electronic devices. From smartphones to advanced medical equipment, this material helps improve performance without adding bulk.
As technology advances, the demand for efficient and reliable materials continues to grow. SiC-coated aluminum meets this demand by offering a combination of durability, conductivity, and lightweight design. It’s no wonder this material has become a staple in modern electronics.
Renewable Energy Systems
SiC-coated aluminum is transforming renewable energy systems by improving efficiency and durability. Solar power inverters and wind turbine generators rely on this advanced material to handle the intense heat and mechanical stress they face daily. The coating enhances aluminum’s thermal management capabilities, allowing these systems to operate more efficiently.
In solar power systems, heat dissipation is critical. Aluminum silicon carbide (AlSiC) composites, a type of metal matrix composite (MMC), excel in this area. They help solar inverters manage heat more effectively, which extends their lifespan and reduces maintenance needs. This means fewer interruptions and lower costs for solar energy providers.
Wind turbines also benefit from SiC-coated aluminum. The generators inside these turbines produce significant heat during operation. SiC coatings improve heat dissipation, ensuring the components stay cool and function reliably. This not only boosts performance but also minimizes wear and tear, leading to longer-lasting equipment.
Did You Know?
SiC-coated aluminum reduces the need for frequent repairs in renewable energy systems. This makes it a cost-effective choice for companies aiming to maximize their return on investment.
The lightweight nature of SiC-coated aluminum adds another advantage. It simplifies the installation process for solar panels and wind turbines. Lighter materials are easier to transport and assemble, which speeds up deployment. This is especially important as the world shifts toward renewable energy at a rapid pace.
By combining durability, efficiency, and lightweight design, SiC-coated aluminum is helping renewable energy systems meet the demands of a growing industry. It’s a material that not only supports sustainability but also drives innovation.
Medical Equipment and Devices
SiC-coated aluminum is making waves in the medical field, where precision and reliability are non-negotiable. Medical devices often operate in challenging environments, requiring materials that can withstand wear, corrosion, and sterilization processes. SiC coatings provide the perfect solution.
Surgical tools, for example, benefit greatly from this technology. The coating enhances the durability of aluminum instruments, ensuring they remain sharp and effective through repeated use. It also resists corrosion from sterilization chemicals, which helps maintain the tools’ integrity over time.
Diagnostic equipment, like MRI machines and CT scanners, also incorporates SiC-coated aluminum. These devices generate heat during operation, and the coating’s excellent thermal conductivity helps manage it. This ensures the equipment runs smoothly, providing accurate results without overheating.
Tip for Healthcare Providers:
Using SiC-coated aluminum in medical devices can reduce maintenance costs and improve patient outcomes by ensuring reliable performance.
Another area where this material shines is in prosthetics and implants. Its lightweight nature makes it ideal for creating comfortable, durable prosthetic limbs. The coating also protects against wear, ensuring the devices last longer and perform better.
SiC-coated aluminum is revolutionizing medical technology. It combines strength, precision, and reliability, making it an invaluable resource for healthcare professionals. From surgical tools to advanced diagnostic machines, this material is setting new standards in the industry.
The Future of SiC Coating
Emerging Trends in Material Science
Material science continues to push the boundaries of what’s possible with SiC coating. Researchers are exploring new ways to make the coating process more precise and efficient. Advanced deposition techniques, like plasma-enhanced chemical vapor deposition (PECVD), are leading the charge. These methods allow for better control over the coating’s thickness and properties, ensuring a flawless finish every time.
Automation and artificial intelligence (AI) are also making waves. AI systems can now monitor and adjust production settings in real time. This ensures consistent results, even when scaling up for larger projects. It’s like having a smart assistant that guarantees every batch meets the highest standards.
Nanotechnology is another game-changer. Scientists are developing nanoscale SiC coatings that offer improved wear resistance and thermal conductivity. These ultra-thin coatings use fewer materials but deliver better performance. They’re perfect for industries that demand lightweight yet durable solutions.
Expanding Industrial Applications
SiC coating is finding its way into more industries than ever before. Aerospace and automotive sectors have already embraced it, but other fields are catching on. Renewable energy systems, for instance, rely on SiC-coated aluminum to improve the efficiency of solar panels and wind turbines. The coating helps manage heat and reduces wear, making these systems more reliable.
Electronics manufacturers are also taking notice. SiC-coated components are ideal for heat sinks and other cooling systems. They keep devices running smoothly, even under heavy use. Medical equipment is another area where this technology shines. From surgical tools to diagnostic machines, SiC coating ensures durability and precision.
Even industries like construction and maritime are exploring its potential. SiC-coated materials can withstand harsh environments, making them perfect for bridges, ships, and offshore platforms. The possibilities are endless as more sectors discover the benefits of this advanced material.
Overcoming Challenges for Broader Adoption
While SiC coating offers incredible advantages, some challenges remain. Cost has been a barrier for smaller companies, but advancements in technology are helping to bring prices down. Scalable solutions, like automated production lines, make it easier for businesses to adopt this technology without breaking the bank.
Environmental concerns are another hurdle. Traditional coating methods can be energy-intensive and produce waste. However, newer techniques like PECVD are more eco-friendly. They use less energy and generate fewer emissions, aligning with global sustainability goals.
Education and awareness also play a role. Many industries are still unaware of how SiC coating can transform their operations. By showcasing its benefits and addressing misconceptions, manufacturers can encourage broader adoption.
The future of SiC coating looks bright. With ongoing innovations and expanding applications, it’s set to become a cornerstone of modern industry.
SiC coating on aluminum has redefined material performance across industries. It combines strength, durability, and lightweight design, making it a go-to solution for demanding applications. From aerospace to renewable energy, this technology has unlocked new possibilities.
In 2025, advancements like nanoscale coatings and AI-driven processes have simplified production. These innovations make SiC coating more efficient, cost-effective, and eco-friendly.
Looking ahead: SiC coating’s potential continues to grow. Its expanding applications promise to shape the future of manufacturing, energy, and technology. The possibilities are endless!
FAQ
What is SiC coating, and why is it important?
SiC coating is a protective layer made of silicon carbide applied to materials like aluminum. It enhances durability, wear resistance, and thermal conductivity. This makes it essential for industries needing lightweight, high-performance materials that can handle extreme conditions.
How does SiC coating improve aluminum?
SiC coating strengthens aluminum by adding a hard, protective layer. It boosts resistance to wear, corrosion, and heat. This combination allows aluminum to perform better in demanding applications like aerospace, automotive, and electronics.
Is SiC coating environmentally friendly?
Yes! Modern SiC coating methods, like plasma-enhanced chemical vapor deposition (PECVD), use less energy and produce fewer emissions. Recycling materials during the process also reduces waste, making it a sustainable choice for industries.
Can SiC-coated aluminum be used in electric vehicles?
Absolutely! SiC-coated aluminum is perfect for electric vehicles. It improves battery housings, heat exchangers, and motor components by enhancing durability and heat management. This helps extend battery life and boosts overall efficiency.
What industries benefit the most from SiC-coated aluminum?
Industries like aerospace, automotive, electronics, renewable energy, and medical equipment benefit greatly. SiC-coated aluminum offers lightweight strength, heat resistance, and corrosion protection, making it ideal for these demanding fields.
How is SiC coating applied to aluminum?
Techniques like chemical vapor deposition (CVD), physical vapor deposition (PVD), and plasma spray coating are commonly used. Each method has unique advantages, such as precision or cost-effectiveness, depending on the application.
Is SiC coating expensive?
While traditional methods can be costly, advancements in 2025 have made SiC coating more affordable. Scalable solutions and automation have reduced production costs, making it accessible to more industries.
Can SiC-coated aluminum handle extreme environments?
Yes, it can! SiC-coated aluminum thrives in harsh conditions. It resists corrosion, wear, and high temperatures, making it reliable for aerospace, marine, and renewable energy applications.
Tip: If you need a material that’s lightweight yet tough, SiC-coated aluminum is a great choice!