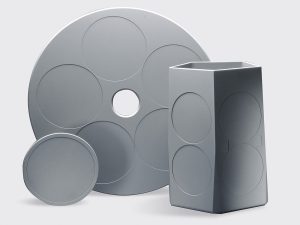
Have you ever wondered how aluminum can handle tough environments without wearing out? The secret lies in silicon carbide coating. This advanced coating makes aluminum surfaces harder and more resistant to damage. It protects against wear, corrosion, and even extreme heat. The result? Aluminum that lasts longer and performs better, even in demanding conditions. The sic coating process creates a durable layer that transforms aluminum into a material ready for challenges. Whether it’s for aerospace, automotive, or industrial use, silicon carbide coating on aluminum is a game-changer.
Key Takeaways
- Silicon carbide coating makes aluminum stronger and more durable. It is very hard and resists wear, perfect for tough conditions.
- This coating stops aluminum from rusting and handles high heat well. It helps parts last longer and work better in industries like planes and cars.
- You can add silicon carbide coating using methods like spraying or chemical processes. Each method works best for certain uses.
- Using silicon carbide coating costs more at first. But it saves money later by needing fewer repairs and replacements.
- Not all aluminum parts need this coating. Check your project needs to see if this protection is worth it.
What is Silicon Carbide Coating?
Silicon carbide coating is like a superhero suit for aluminum. It adds a layer of protection that makes aluminum tougher, more durable, and ready to take on challenging environments. But what makes this coating so special? Let’s dive into its properties and how it’s applied.
Properties of Silicon Carbide
Hardness and Thermal Conductivity
Silicon carbide is incredibly hard—almost as hard as diamond! This means it can resist scratches and wear like a champ. Plus, it has excellent thermal conductivity, which helps it handle high temperatures without breaking a sweat. Imagine aluminum parts staying cool and strong even in extreme heat. That’s the magic of silicon carbide.
Corrosion and Wear Resistance
This coating doesn’t just stop at hardness. It also protects aluminum from corrosion and wear. Whether it’s exposure to harsh chemicals or constant friction, silicon carbide keeps aluminum surfaces intact. It’s like giving aluminum a shield against the elements.
Here’s a quick look at the standout properties of silicon carbide:
Property | Description |
---|---|
Hardness and Wear Resistance | Remarkable hardness, surpassed only by diamond, providing exceptional wear resistance. |
Thermal Stability | Maintains structural integrity at temperatures exceeding 1600°C (2912°F). |
Chemical Inertness | High resistance to chemical attack, impervious to most acids, alkalis, and organic solvents. |
Oxidation Resistance | Excellent resistance to oxidation, maintaining integrity in oxygen-rich environments. |
Electrical and Thermal Conductivity | Varying degrees of conductivity, allowing tailoring for different applications. |
Application Methods
Thermal Spraying
One common way to apply silicon carbide coating is through thermal spraying. This method involves spraying molten silicon carbide onto the aluminum surface. It’s quick and effective, making it a popular choice for industrial applications. However, it works best for simpler shapes.
Chemical Vapor Deposition (CVD)
For more precise and uniform coatings, chemical vapor deposition (CVD) is the go-to method. In this process, gases containing silicon and carbon are introduced into a chamber. These gases break down and form a thin, even layer of silicon carbide on the aluminum. While CVD offers excellent results, it requires specialized equipment and can be more expensive.
Here’s a comparison of common application methods:
Method | Description |
---|---|
Chemical Vapor Deposition (CVD) | Involves introducing silicon- and carbon-containing gases into a chamber where they decompose to form a coating. Allows precise control over coating properties but has high costs and safety concerns. |
Physical Vapor Deposition (PVD) | Uses thermal evaporation or sputtering to deposit silicon carbide. Provides control over thickness and composition but can struggle with uniformity on complex shapes and has high equipment costs. |
Spraying Technique | Involves spraying liquid materials onto the substrate and curing them. It is cost-effective but results in weaker adhesion and lower performance. |
Electrochemical Deposition | Utilizes electrochemical reactions to deposit silicon carbide from a solution. Allows for uniform growth and is used in specialized applications like sensors and batteries. |
Silicon carbide coating combines incredible properties with advanced application methods. It’s no wonder this coating is a game-changer for aluminum durability.
How Does Silicon Carbide Coating Improve Aluminum Durability?
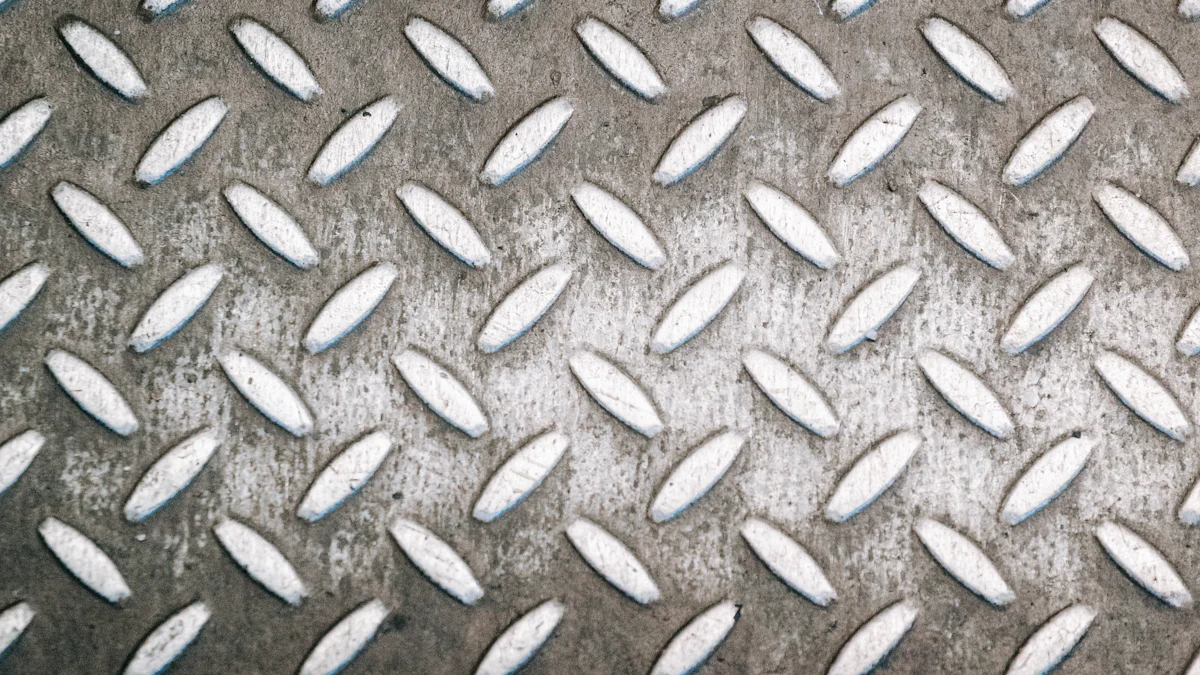
Surface Hardness
Resistance to wear and tear
Have you ever noticed how some materials seem to wear out quickly while others stay strong? That’s where surface hardness comes into play. Silicon carbide coating makes aluminum incredibly hard, almost like giving it armor. This hardness helps aluminum resist scratches, dents, and other damage caused by everyday wear and tear. Whether it’s heavy machinery or moving parts, the coating ensures the aluminum stays in top shape for much longer.
Comparison with uncoated aluminum
Let’s compare coated and uncoated aluminum. Without silicon carbide coating, aluminum is softer and more prone to damage. It can scratch easily and wear down over time. But with the coating, the surface becomes much tougher. It’s like the difference between walking barefoot and wearing sturdy boots—you’re just better protected.
Corrosion Resistance
Protection in harsh environments
Corrosion can be a nightmare for aluminum, especially in tough environments. Silicon carbide coating acts as a shield, protecting aluminum from moisture, chemicals, and other corrosive elements. In one study, researchers tested silicon carbide-coated AA2014 aluminum alloy using potentiodynamic polarization and electrochemical impedance spectroscopy. The results were amazing—the coating reduced the corrosion rate by 99.8%! That’s a huge improvement, thanks to the coating’s compact structure and chemical stability.
Benefits for marine and industrial use
This corrosion resistance is a game-changer for industries like marine and manufacturing. Imagine aluminum parts exposed to salty seawater or harsh chemicals. Without protection, they’d corrode quickly. But with silicon carbide coating, they last much longer, saving time and money on replacements.
Thermal Stability
Performance under high temperatures
High temperatures can weaken many materials, but not silicon carbide-coated aluminum. The coating keeps aluminum stable and strong, even in extreme heat. This makes it perfect for applications where heat resistance is critical. For example, in electric vehicles, silicon carbide-coated components handle high temperatures and voltages with ease, improving efficiency.
Applications requiring heat resistance
The thermal stability of silicon carbide coating benefits several industries:
- Electric Vehicles: Power modules and inverters perform better in hot conditions.
- Aerospace: Aircraft engine parts stay reliable under intense heat.
- Automotive: Brake discs and engine components handle high-performance demands.
- Chemical Processing: Equipment resists heat and corrosive substances.
This versatility makes silicon carbide coating a valuable upgrade for aluminum in demanding environments.
Abrasion and Impact Resistance
Prevention of surface damage
Have you ever dropped something heavy onto a metal surface and noticed the dents or scratches it leaves behind? I’ve seen it happen countless times, and it’s frustrating. That’s where silicon carbide coating steps in to save the day. This coating creates a tough, protective layer on aluminum that resists abrasion and impact. It’s like giving aluminum a suit of armor.
When aluminum parts face constant friction or sudden impacts, they’re at risk of surface damage. Think about moving parts in machinery or tools that scrape against rough surfaces. Without protection, the aluminum would wear down quickly. But with the coating, the surface stays smooth and intact. It’s amazing how much abuse coated aluminum can handle without showing signs of wear.
Longevity of aluminum components
Let’s talk about durability. Aluminum is already a great material, but it has its limits. Over time, repeated impacts and abrasions can weaken it. I’ve seen uncoated aluminum parts fail sooner than expected because of this. But when you add silicon carbide coating, the story changes.
The coating not only prevents damage but also extends the life of aluminum components. Imagine a piece of equipment that lasts twice as long because its aluminum parts are protected. That’s a huge win for anyone looking to save money and reduce downtime. Whether it’s in heavy machinery, vehicles, or industrial tools, this coating ensures aluminum components stay reliable for years.
In short, silicon carbide coating doesn’t just protect aluminum—it transforms it into a long-lasting, high-performance material.
Applications of Silicon Carbide Coated Aluminum
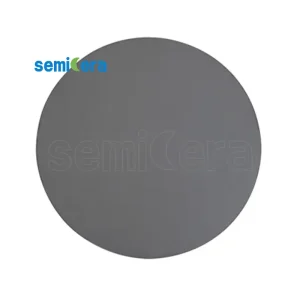
When I think about the versatility of silicon carbide-coated aluminum, I can’t help but marvel at how many industries it benefits. From airplanes to cars to cutting-edge electronics, this coating transforms aluminum into a powerhouse material. Let’s explore some of its most exciting applications.
Aerospace Industry
Lightweight, durable components
In aerospace, every ounce matters. Aluminum is already lightweight, but adding silicon carbide coating makes it incredibly durable too. This combination is perfect for aircraft components like structural parts and turbine blades. These parts need to be strong enough to handle extreme conditions while keeping the aircraft light for better fuel efficiency.
High-temperature performance
Airplanes face intense heat, especially in engines and exhaust systems. Silicon carbide-coated aluminum thrives in these high-temperature environments. It resists thermal shock, meaning it won’t crack or warp when temperatures change suddenly. This reliability is why aerospace engineers trust it for critical components.
Automotive Sector
Engine parts and heat exchangers
Cars demand materials that can handle heat, wear, and corrosion. Silicon carbide coating steps up to the challenge. It’s commonly used on engine components, turbine blades, and exhaust systems. These parts face constant friction and high temperatures, but the coating keeps them performing like new.
Improved fuel efficiency
Here’s something cool: by protecting aluminum parts, silicon carbide coating helps reduce weight and improve fuel efficiency. Lighter, more durable components mean engines don’t have to work as hard. That’s a win for both performance and the environment.
Electronics and Semiconductors
Heat sinks and protective casings
Electronics generate heat, and managing that heat is crucial. Silicon carbide-coated aluminum makes excellent heat sinks, pulling heat away from sensitive components. It’s also used for protective casings, shielding delicate parts from damage.
Enhanced thermal management
I’ve seen how this coating improves thermal management in semiconductors. It handles heat so well that devices can run faster and more efficiently. Whether it’s a computer processor or a power module, silicon carbide-coated aluminum keeps things cool and reliable.
Industrial Applications
When I think about industrial applications, I’m amazed at how silicon carbide-coated aluminum transforms tools and equipment. It’s like giving them a superpower—making them tougher, longer-lasting, and ready for the harshest conditions. Let me show you how this coating works wonders in manufacturing and chemical processing.
Manufacturing Tools and Equipment
In manufacturing, tools take a beating. They cut, grind, and shape materials all day long. Without proper protection, they wear out fast. That’s where silicon carbide-coated aluminum steps in. It boosts tool performance and extends their lifespan. I’ve seen it make a huge difference in tools like cutting blades, drill bits, and machining equipment.
Here’s a quick look at some tools that benefit from silicon carbide coatings:
Tool Type | Description |
---|---|
Uncoated Tungsten Carbide | Standard cutting tool for various materials. |
Polycrystalline Diamond (PCD) | Preferred for high-volume SiCp/Al composites. |
High-Speed Steel (HSS) | Commonly used for general machining tasks. |
Cubic Boron Nitride (CBN) | Effective for hard materials. |
Single-Crystal Diamond (SCD) | High-performance tool for precision work. |
TiN-Coated Hard Carbide | Enhances tool life and performance. |
CVD Diamond | Suitable for high-speed machining. |
Multilayer-Coated Carbide | Offers improved wear resistance. |
These tools last longer and perform better with silicon carbide coatings. It’s like upgrading from a regular hammer to a precision-engineered power tool.
Chemical Processing Environments
Chemical processing environments are no joke. They’re full of corrosive substances that can destroy unprotected materials. I’ve seen how silicon carbide-coated aluminum thrives in these settings. The coating resists oxidation, even in oxygen-rich environments. It also stands strong against acids, alkalis, and organic solvents.
This makes it perfect for equipment like reactors, heat exchangers, and storage tanks. Imagine a piece of equipment that doesn’t corrode or weaken, even after years of exposure to harsh chemicals. That’s the kind of reliability silicon carbide coatings bring to the table.
In industries where downtime costs money, this durability is a game-changer. It keeps operations running smoothly and reduces the need for constant repairs or replacements. For me, that’s the ultimate win.
Potential Limitations and Considerations
Cost Implications
Higher initial investment
Let’s talk about cost. Silicon carbide coating isn’t cheap. The process requires advanced materials and specialized techniques, which drive up the price. For large-scale projects, the initial investment can feel steep. I’ve seen businesses hesitate because of this upfront cost. However, it’s important to remember that quality often comes at a price.
Long-term cost benefits
Here’s the good news: the benefits outweigh the initial expense. Silicon carbide-coated aluminum lasts much longer than uncoated alternatives. That means fewer replacements and less downtime. Over time, the savings add up. I’ve seen companies save thousands by investing in durable, coated components. It’s like buying a high-quality tool—it costs more upfront but pays off in the long run.
Technical Challenges
Complexity of application
Applying silicon carbide coating isn’t simple. The process demands precision and expertise. For example, the coating must bond perfectly with the aluminum surface. If it doesn’t, the results won’t meet expectations.
Challenge | Description |
---|---|
Cost and Scalability | The high cost of SiC coatings, especially for large-scale applications, poses a significant challenge. |
Substrate Compatibility | Successful deposition depends on the compatibility between SiC coatings and aluminum substrates. |
Multifunctional Coatings | Development of coatings that combine multiple properties is a focus, which may affect application methods. |
Need for specialized equipment
The equipment required for this process is no joke. For instance, the SiC3 coating uses a high-temperature, very high-purity Chemical Vapor Deposition (CVD) reactor.
The SiC3 coating is applied using a high temperature, very high purity Chemical Vapor Deposition (CVD) reactor.
This kind of setup isn’t something you’ll find in every facility. It requires significant investment and expertise to operate.
Suitability for Applications
Not ideal for all aluminum components
While silicon carbide coating works wonders, it’s not a one-size-fits-all solution. Some aluminum components don’t need this level of protection. For example, parts used in low-stress environments might not benefit enough to justify the cost.
Factors to consider when choosing this coating
When deciding if this coating is right for your project, think about the environment and performance requirements. Will the aluminum face high temperatures, corrosion, or heavy wear? If so, silicon carbide coating is a great choice. If not, a simpler solution might work just fine.
In the end, it’s all about finding the right balance between cost, performance, and application needs.
Silicon carbide coating truly transforms aluminum into a high-performance material. Its incredible hardness and wear resistance make it stand out, while its chemical inertness and oxidation resistance ensure durability in harsh environments. I’ve seen how this coating enhances aluminum’s ability to handle extreme conditions, from high temperatures to corrosive chemicals.
What’s even more exciting is its versatility. Industries like aerospace, automotive, and electronics rely on it for lightweight, durable, and heat-resistant components. Sure, there are some challenges, but the long-term benefits far outweigh them. For me, investing in silicon carbide coating is a smart move for anyone looking to boost aluminum’s performance and lifespan.
FAQ
What makes silicon carbide coating so durable?
Silicon carbide is almost as hard as diamond. This hardness gives it incredible resistance to scratches, wear, and impact. It also handles extreme temperatures and corrosive environments without breaking down. I like to think of it as a superhero shield for aluminum.
Can silicon carbide coating be applied to all aluminum parts?
Not every aluminum part needs this coating. It works best for components exposed to high stress, heat, or corrosion. For low-stress applications, simpler coatings might do the job. I always recommend evaluating the specific needs of your project.
How does silicon carbide coating improve heat resistance?
Silicon carbide has excellent thermal stability. It keeps aluminum strong and intact even at high temperatures. This makes it perfect for industries like aerospace and automotive, where heat resistance is critical. I’ve seen it perform flawlessly in extreme conditions.
Is silicon carbide coating environmentally friendly?
Yes, it’s a sustainable choice. By extending the lifespan of aluminum parts, it reduces waste and the need for replacements. Plus, its durability helps improve energy efficiency in applications like vehicles and electronics. That’s a win for the planet and your wallet.
How long does silicon carbide coating last?
It depends on the application, but I’ve seen it last for years, even in harsh environments. Its resistance to wear, corrosion, and heat ensures aluminum components stay reliable for a long time. Proper maintenance can make it last even longer.