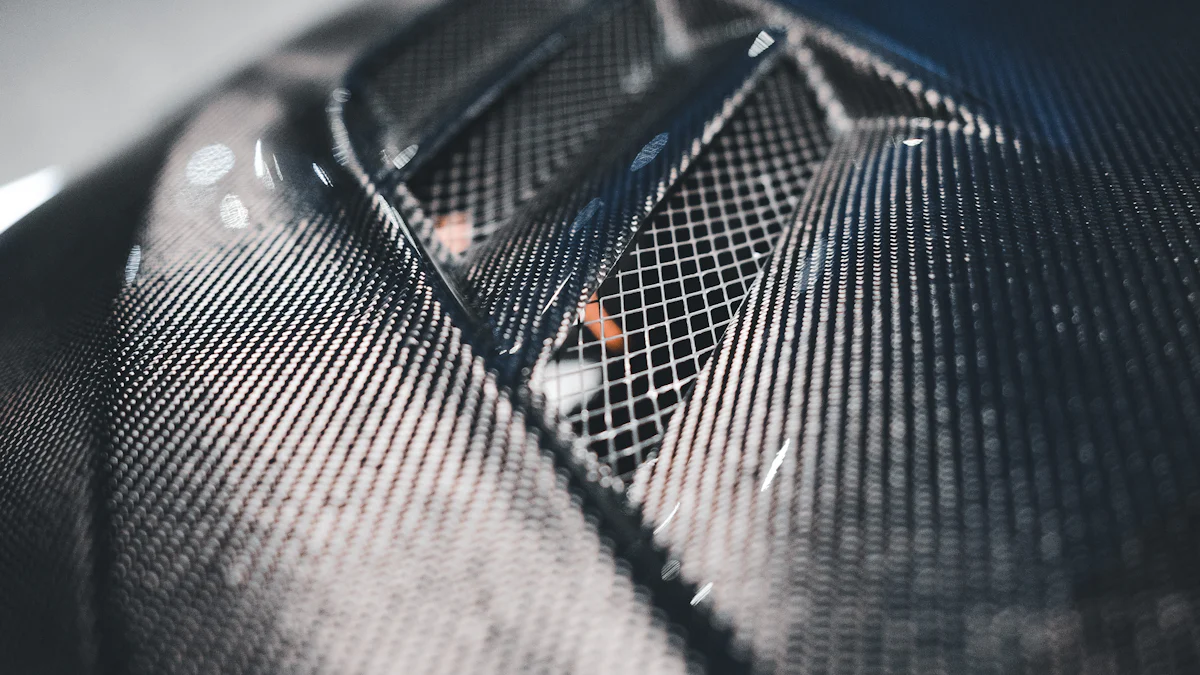
A 4×8 carbon fiber sheet is a lightweight yet incredibly strong material widely used in various industries. Its unique composition combines carbon fibers with a polymer matrix, resulting in a product that offers exceptional strength-to-weight ratios. Unlike traditional materials like steel or aluminum, it resists corrosion and performs reliably in extreme conditions. These sheets also exhibit thermal stability, making them ideal for high-temperature environments. Their flexibility allows for creative designs, while their durability ensures long-term performance. From aerospace to construction, industries rely on these sheets for innovative solutions.
The versatility of carbon fiber extends beyond sheets. Products like the carbon fiber roll and the 1/8 carbon fiber sheet cater to specialized applications, offering tailored solutions for diverse needs. Additionally, materials like the silicon carbide ceramic plate complement carbon fiber in high-performance settings, enhancing durability and resistance to wear.
Key Takeaways
- 4×8 carbon fiber sheets are lightweight yet incredibly strong, making them ideal for applications in aerospace and automotive industries where reducing weight enhances fuel efficiency.
- These sheets resist corrosion and perform reliably in extreme conditions, ensuring durability in marine and construction applications, thus minimizing maintenance costs.
- The thermal and electrical conductivity of carbon fiber sheets allows for effective insulation and controlled conductivity, broadening their use in energy storage and robotics.
- Customization options, including thickness, fiber orientation, and surface finish, enable tailored solutions for specific design and functional requirements across various industries.
- The environmental benefits of carbon fiber sheets, such as lower energy consumption during production and reduced transportation emissions, align with the growing demand for sustainable materials.
- Proper handling and maintenance, including safe cutting techniques and regular cleaning, are essential to maximize the longevity and performance of carbon fiber sheets.
- 4×8 carbon fiber sheets are versatile and compatible with other materials, enhancing their functionality in diverse applications from sports equipment to medical devices.
- Investing in carbon fiber sheets may have higher upfront costs, but their long-term durability and efficiency lead to significant savings and reduced waste over time.
Key Features and Benefits of 4×8 Carbon Fiber Sheets
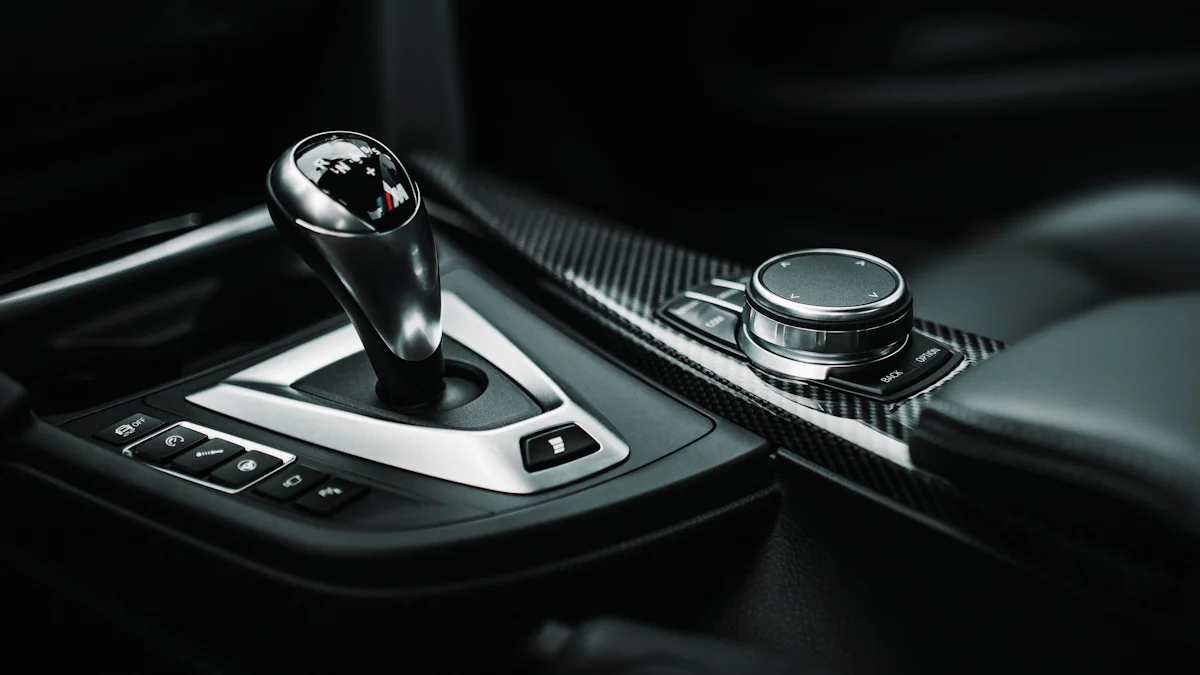
Lightweight and High Strength
The lightweight nature of 4×8 carbon fiber sheets sets them apart from traditional materials like steel or aluminum. These sheets weigh significantly less while offering a superior strength-to-weight ratio. This unique combination allows them to support heavy loads without adding unnecessary weight. For industries like aerospace and automotive, this feature translates to enhanced fuel efficiency and improved performance.
For example, in the aerospace sector, carbon fiber sheets are used in aircraft components to reduce weight while maintaining structural integrity. Similarly, the automotive industry incorporates these sheets into body panels and reinforcements, ensuring safety without compromising on weight reduction.
Industry | Application Description |
---|---|
Aerospace | Utilizes carbon fiber sheets for components in aircraft, enhancing fuel efficiency and performance. |
Automotive | Used for body panels and structural reinforcements to reduce weight while maintaining safety. |
Sports Equipment | Incorporated in high-performance bicycles, tennis rackets, and golf clubs to improve performance and reduce weight. |
Marine Applications | Employed for boat hulls and components, benefiting from resistance to saltwater corrosion and lightweight nature. |
Architectural Design | Used in contemporary designs for structural elements and facades, leveraging aesthetic and functional attributes. |
The ease of handling and transporting 4×8 carbon fiber sheets further enhances their appeal. Despite their light weight, these sheets resist bending or breaking under pressure, making them a reliable choice for demanding applications.
Durability and Resistance to Corrosion
Durability is another hallmark of 4×8 carbon fiber sheets. Unlike metals, these sheets do not rust or corrode, even in environments with high humidity or chemical exposure. This property makes them ideal for marine applications, where saltwater corrosion poses a significant challenge.
In addition to marine uses, industries like construction and architecture benefit from the corrosion resistance of carbon fiber sheets. They are often used in structural reinforcements and decorative panels, ensuring longevity and minimal maintenance.
The ability to withstand harsh conditions without degrading ensures that 4×8 carbon fiber sheets remain a cost-effective and sustainable solution for long-term projects.
Thermal and Electrical Conductivity
The thermal conductivity of 4×8 carbon fiber sheets depends on the orientation of the fibers. Along the fibers, they exhibit high conductivity, while across the fibers, conductivity remains low. This unique characteristic allows these sheets to act as effective insulators, maintaining stable temperatures in various applications.
In the automotive and aerospace sectors, this property enhances energy efficiency by reducing heat loss. It also ensures that components remain stable under extreme temperature fluctuations.
Additionally, the electrical conductivity of carbon fiber sheets makes them suitable for specialized applications requiring controlled conductivity levels. This feature broadens their use in industries like robotics and energy storage, where precision and reliability are critical.
Aesthetic Appeal and Customization Options
The 4×8 carbon fiber sheet stands out not only for its performance but also for its striking aesthetic appeal. Its unique, high-tech appearance makes it a preferred choice for industries that prioritize both functionality and design. The glossy finish of these sheets enhances their visual appeal, making them suitable for luxury applications such as high-end automotive interiors, consumer electronics, and architectural elements.
Customization options further elevate the versatility of these sheets. Manufacturers offer a wide range of features to meet specific design and functional requirements.
Customization Feature | Options |
---|---|
Size | 300X200mm, 500X400mm, 500X500mm, 500X600mm, Sample |
Thickness | 0.5mm to 10.0mm |
Fiber Orientation | 0°/45°/90°/-45° |
Surface Finish | Glossy, Matte, Forged |
Weave | 1K, 3K, 6K, 12K, 24K |
Colors | Black or any color from RAL, including Blue, Gold, Green, and Purple |
These options allow designers and engineers to tailor the sheets to their specific needs. For example, the choice of fiber orientation can optimize strength in certain directions, while the variety of colors and finishes ensures compatibility with diverse aesthetic preferences.
- The glossy finish provides a professional appearance for visible applications.
- Custom colors enhance visual appeal, making them ideal for luxury goods.
- Unique weaves, such as 3K or 12K, add texture and depth to the surface, creating a sophisticated look.
The ability to combine functionality with visual elegance makes 4×8 carbon fiber sheets a top choice for industries like automotive, architecture, and consumer electronics.
Environmental Benefits and Sustainability
The environmental advantages of using 4×8 carbon fiber sheets make them a sustainable alternative to traditional materials like steel or aluminum. Their production process consumes less energy, resulting in a lower carbon footprint. Additionally, precise engineering during manufacturing minimizes waste, reducing excess material and promoting resource efficiency.
The lightweight nature of these sheets contributes to reduced transportation emissions. Vehicles and aircraft incorporating carbon fiber components require less fuel, leading to a smaller environmental impact. Over time, this feature supports global efforts to reduce greenhouse gas emissions.
Durability further enhances their sustainability. Structures made with carbon fiber require fewer replacements, minimizing waste and conserving resources. For example, in the construction industry, carbon fiber sheets provide long-lasting reinforcements, reducing the need for frequent repairs or replacements.
- The excellent insulation properties of carbon fiber improve energy efficiency in buildings.
- Reduced energy consumption for heating and cooling lowers the environmental impact of residential and commercial structures.
By combining durability, energy efficiency, and reduced emissions, 4×8 carbon fiber sheets align with the growing demand for eco-friendly materials. Their adoption across industries reflects a commitment to sustainability without compromising performance.
Applications of 4×8 Carbon Fiber Sheets Across Industries
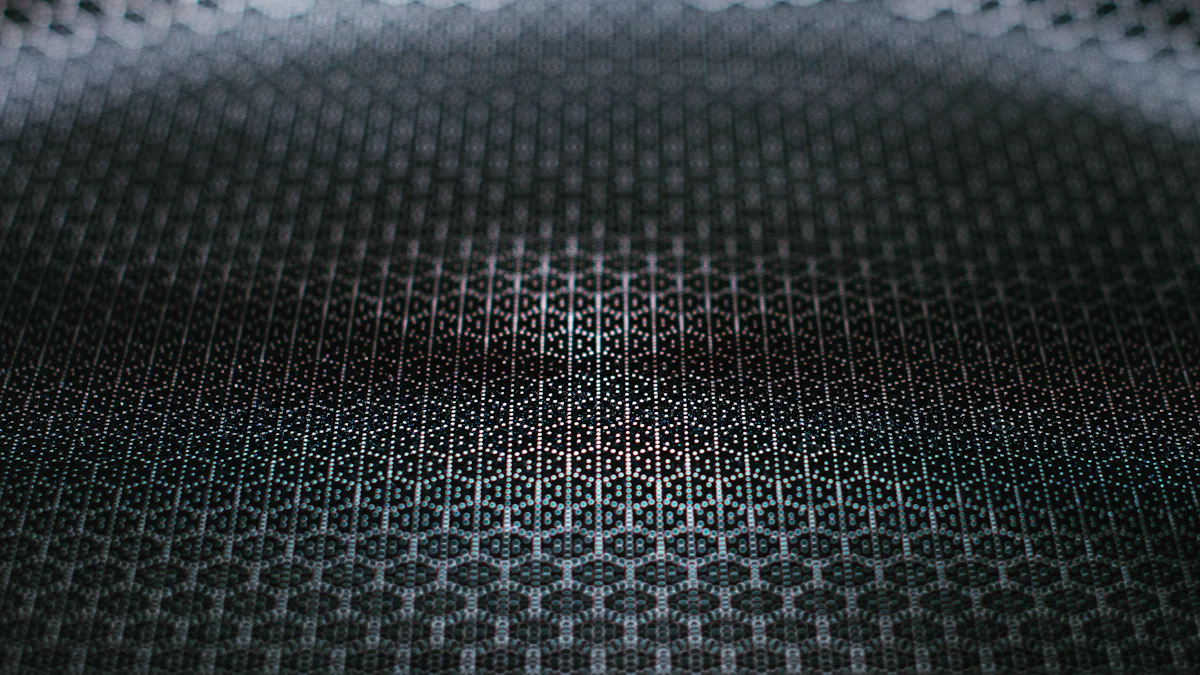
Aerospace Industry
Aircraft Components
The aerospace industry relies heavily on 4×8 carbon fiber sheets for their lightweight and high-strength properties. These sheets are used in constructing aircraft interiors, including seats, overhead compartments, and flooring. Their ability to reduce weight without compromising strength enhances fuel efficiency and overall performance.
For example, structural components like wing spars and fuselage panels benefit from the superior strength-to-weight ratio of carbon fiber sheets. This feature allows aircraft to carry heavier payloads while consuming less fuel.
The corrosion resistance of these sheets ensures durability in high-altitude environments, where exposure to moisture and temperature fluctuations is common. Their use in aircraft components demonstrates their ability to meet the stringent demands of the aerospace sector.
Spacecraft Structures
Spacecraft require materials that can withstand extreme conditions, including high temperatures and radiation. Carbon fiber sheets excel in these environments due to their thermal stability and resistance to wear. Engineers use them in constructing spacecraft structures such as satellite panels and rocket casings.
The lightweight nature of these sheets reduces the overall mass of spacecraft, making launches more cost-effective. Their durability ensures that critical components remain intact during extended missions in space.
The versatility of carbon fiber sheets makes them indispensable in advancing aerospace technology, from commercial aviation to space exploration.
Automotive Industry
Lightweight Vehicle Parts
The automotive industry incorporates 4×8 carbon fiber sheets to create lightweight vehicle parts. These sheets are used in body panels, roofs, and hoods, significantly reducing the overall weight of vehicles. This reduction improves fuel efficiency and lowers emissions, aligning with global sustainability goals.
For instance, electric vehicles benefit from carbon fiber sheets by extending their range through weight reduction. Traditional vehicles also achieve better mileage and handling due to the lighter components.
The high strength-to-weight ratio of these sheets ensures that they can bear substantial loads without adding unnecessary mass. This feature enhances both performance and safety in modern vehicles.
Performance Enhancements
High-performance vehicles, including sports cars and racing cars, utilize carbon fiber sheets for their superior mechanical properties. These sheets improve aerodynamics by allowing for sleek, lightweight designs.
Unlike traditional materials, carbon fiber does not rust or degrade over time. This durability makes it a cost-effective choice for long-term automotive applications.
The use of carbon fiber sheets in performance enhancements highlights their role in pushing the boundaries of automotive engineering.
Construction and Architecture
Structural Reinforcements
In construction, 4×8 carbon fiber sheets provide structural reinforcements for buildings and bridges. Their high tensile strength makes them ideal for strengthening concrete and steel structures.
Engineers use these sheets to retrofit aging infrastructure, extending its lifespan and improving safety. Their lightweight nature simplifies installation, reducing labor costs and project timelines.
The corrosion resistance of carbon fiber sheets ensures that reinforced structures remain durable in harsh environments, including coastal areas and industrial zones.
Decorative Panels
Architects value the aesthetic appeal of carbon fiber sheets for decorative panels in modern buildings. These panels offer a sleek, high-tech appearance that complements contemporary designs.
Customization options, such as glossy finishes and unique weaves, allow architects to create visually striking facades and interiors. The lightweight nature of these panels also reduces the load on building structures.
The combination of functionality and design makes carbon fiber sheets a preferred choice for innovative architectural projects.
Marine Industry
Boat Hulls and Decks
The marine industry benefits significantly from the use of 4×8 carbon fiber sheets in boat hulls and decks. These sheets offer a combination of lightweight construction and exceptional strength, making them ideal for marine vessels. Their lightweight nature enhances speed and maneuverability, which is crucial for both recreational and commercial boats.
Carbon fiber sheets resist saltwater corrosion, ensuring long-lasting performance in harsh marine environments. This property reduces maintenance costs and extends the lifespan of vessels.
Boat manufacturers often use these sheets to construct durable and efficient hulls and decks. Their ability to withstand the rigors of marine conditions makes them a preferred choice for modern shipbuilding.
Corrosion-Resistant Components
Marine environments expose materials to constant moisture and salt, leading to corrosion. Carbon fiber sheets provide a solution by offering excellent resistance to these elements. This resistance ensures that components like rudders, masts, and other structural parts remain intact over time.
The durability of carbon fiber sheets reduces the need for frequent replacements, making them a cost-effective option for marine applications. Their lightweight properties also contribute to fuel efficiency, as vessels require less energy to operate.
By combining strength, corrosion resistance, and lightweight construction, carbon fiber sheets play a vital role in advancing marine technology.
Sports and Recreation
High-Performance Equipment
Athletes and sports enthusiasts rely on high-performance equipment made from 4×8 carbon fiber sheets. These sheets are used to manufacture items like bicycle frames, tennis rackets, and golf clubs. Their lightweight and strong properties enhance performance, allowing athletes to achieve better results.
For example, carbon fiber bicycle frames improve speed and agility due to their reduced weight. Tennis rackets made from this material offer better control and power, giving players a competitive edge.
The use of carbon fiber in sports equipment demonstrates its ability to combine functionality with performance, making it a top choice for professionals and hobbyists alike.
Custom Sports Gear
Customization is a key trend in the sports industry, and carbon fiber sheets enable the creation of tailored sports gear. Manufacturers can design equipment with specific dimensions, weights, and finishes to meet individual needs.
Custom sports gear, such as personalized golf clubs or unique bicycle designs, enhances user experience and satisfaction. The aesthetic appeal of carbon fiber also adds a premium touch to these products.
By offering both performance and personalization, carbon fiber sheets continue to revolutionize the sports and recreation sector.
Energy Sector
Wind Turbine Blades
The energy sector leverages 4×8 carbon fiber sheets in the production of wind turbine blades. These blades require materials that are both lightweight and strong to maximize efficiency. Carbon fiber sheets meet these requirements, enabling turbines to generate more energy with less wear and tear.
The lightweight nature of carbon fiber reduces the load on turbine structures, improving their operational lifespan. This feature supports the growing demand for renewable energy solutions.
By contributing to the development of efficient wind turbines, carbon fiber sheets play a crucial role in advancing sustainable energy technologies.
Energy Storage Solutions
Carbon fiber sheets also find applications in energy storage systems. Their thermal and electrical conductivity makes them suitable for use in battery casings and other energy storage components.
These sheets enhance the durability and efficiency of energy storage solutions, ensuring reliable performance over time. Their lightweight properties also simplify transportation and installation.
The integration of carbon fiber sheets into energy systems highlights their versatility and importance in the renewable energy landscape.
Medical Applications
Prosthetics
The medical field has embraced the use of 4×8 carbon fiber sheets in prosthetics due to their lightweight and durable properties. These sheets provide the strength needed to support body weight while remaining light enough for comfortable daily use. Their high strength-to-weight ratio ensures that prosthetic limbs can handle significant stress without compromising mobility.
Carbon fiber’s adaptability allows manufacturers to design prosthetics tailored to individual needs. Patients benefit from custom-fit solutions that enhance comfort and functionality. Additionally, the material’s resistance to wear and corrosion ensures long-lasting performance, even under challenging conditions.
For example, athletes using carbon fiber prosthetics experience improved agility and endurance. The lightweight nature of these prosthetics reduces fatigue, enabling users to perform at their best.
The use of carbon fiber in prosthetics highlights its ability to combine functionality with user comfort, making it a preferred choice in modern medical applications.
Surgical Instruments
Surgical instruments made from 4×8 carbon fiber sheets offer several advantages over traditional materials. These instruments are lightweight, reducing strain on surgeons during lengthy procedures. Their non-corrosive nature ensures that they remain sterile and functional after repeated use.
Carbon fiber’s thermal stability also plays a crucial role in surgical environments. Instruments made from this material maintain their structural integrity under high-temperature sterilization processes. This feature ensures reliability and safety during critical medical procedures.
The precision and durability of carbon fiber surgical instruments make them ideal for advanced medical techniques. Surgeons rely on these tools for their accuracy and ease of handling, which contribute to better patient outcomes.
By integrating carbon fiber into surgical instruments, the medical industry continues to enhance the efficiency and effectiveness of healthcare delivery.
Robotics and Drone Manufacturing
Lightweight Frames
The robotics and drone industries prioritize lightweight materials to improve performance and efficiency. 4×8 carbon fiber sheets meet these requirements by offering a high strength-to-weight ratio. This property allows drones and robots to carry heavier payloads without adding unnecessary weight.
For instance, drones constructed with carbon fiber frames achieve greater flight stability and longer operational times. The reduced weight minimizes energy consumption, enhancing overall efficiency.
Carbon fiber’s lightweight nature also simplifies the design and assembly of robotic systems. Engineers can create compact, agile robots capable of performing complex tasks in various environments.
Durable Components
Durability is essential in robotics and drone manufacturing, where components often face harsh conditions. Carbon fiber sheets provide exceptional resistance to corrosion, making them suitable for use in high-humidity or chemically exposed environments.
For example, drones operating in coastal areas benefit from carbon fiber’s ability to withstand saltwater exposure. Similarly, robots used in industrial settings remain functional despite exposure to chemicals or extreme temperatures.
The thermal stability of carbon fiber ensures that components maintain their performance under fluctuating temperatures. This feature enhances the reliability of drones and robots in demanding applications.
- Key Advantages of Carbon Fiber in Robotics and Drones:
- Lightweight construction improves efficiency and performance.
- High strength-to-weight ratio supports substantial loads.
- Corrosion resistance ensures durability in diverse environments.
- Thermal stability maintains structural integrity under extreme conditions.
By leveraging the unique properties of carbon fiber, the robotics and drone industries continue to push the boundaries of innovation and functionality.
Practical Considerations for Selecting 4×8 Carbon Fiber Sheets
Evaluating Material Properties
Thickness and Weight
When selecting a 4×8 carbon fiber sheet, thickness and weight play a crucial role in determining its suitability for specific applications. Thicker sheets provide greater rigidity and strength, making them ideal for structural reinforcements or heavy-duty components. Conversely, thinner sheets offer flexibility and are better suited for lightweight applications such as drone frames or decorative panels.
The weight of the sheet directly impacts its performance. Lightweight sheets reduce the overall load in industries like aerospace and automotive, enhancing fuel efficiency and maneuverability. Evaluating these factors ensures the material aligns with the intended use, balancing performance with practicality.
Strength-to-Weight Ratio
The strength-to-weight ratio is a defining characteristic of carbon fiber sheets. This property determines how much load the material can bear relative to its weight. Applications requiring high durability, such as wind turbine blades or prosthetics, benefit from materials with superior strength-to-weight ratios.
Other factors, such as weave pattern and fiber orientation, also influence this ratio. For instance:
- Weave Pattern: Affects the sheet’s flexibility and strength.
- Fiber Orientation: Determines strength in specific directions.
By understanding these properties, engineers can select sheets that meet performance requirements while minimizing unnecessary weight.
Surface Finish Options
Glossy vs. Matte
Surface finish significantly impacts both the aesthetics and functionality of a 4×8 carbon fiber sheet. Glossy finishes enhance visual appeal, making them popular in luxury automotive interiors and high-end consumer electronics. Matte finishes, on the other hand, reduce glare and provide a subtle appearance, making them suitable for industrial or functional applications.
Finish Type | Characteristics |
---|---|
Glossy | Enhances visual appeal, suitable for aesthetic applications |
Matte | Reduces glare, provides a subtle appearance, suitable for industrial applications |
Textured vs. Smooth
Textured and smooth finishes offer additional customization options. Textured surfaces improve grip and are often used in sports equipment or tool handles. Smooth finishes, however, provide a sleek, polished look, ideal for decorative panels or luxury goods.
Selecting the right surface finish depends on the intended application. For example, a glossy, smooth finish may suit a high-performance sports car, while a matte, textured finish might be better for industrial machinery.
Cost-Effectiveness and Budgeting
Cost-effectiveness is a critical consideration, especially for large-scale projects. While carbon fiber sheets may seem expensive initially, their long-term durability offsets the upfront cost. Their resistance to wear and corrosion reduces the need for frequent replacements, resulting in significant savings over time.
For large-scale applications, such as construction or energy projects, the durability of carbon fiber sheets ensures consistent performance, minimizing maintenance expenses. Balancing cost with performance allows industries to maximize value without compromising quality.
Compatibility with Other Materials
4×8 carbon fiber sheets exhibit remarkable compatibility with a wide range of materials, making them a versatile choice for diverse industrial applications. Their ability to integrate seamlessly with metals, plastics, and composites enhances their functionality and broadens their scope of use. Engineers and designers leverage this adaptability to create innovative solutions across industries.
Metals
Carbon fiber sheets pair effectively with metals such as aluminum, titanium, and steel. This combination balances the lightweight properties of carbon fiber with the strength and durability of metals. For example, aerospace engineers often bond carbon fiber sheets to aluminum frames to reduce weight while maintaining structural integrity.
Tip: When combining carbon fiber with metals, using appropriate adhesives or fasteners ensures a secure bond and prevents galvanic corrosion.
Metal Type | Benefits of Combination |
---|---|
Aluminum | Lightweight and corrosion-resistant, ideal for aerospace and automotive applications. |
Titanium | High strength and heat resistance, suitable for extreme environments. |
Steel | Exceptional durability, often used in construction and heavy machinery. |
Plastics
Carbon fiber sheets also integrate well with high-performance plastics like polycarbonate and ABS (Acrylonitrile Butadiene Styrene). This pairing creates components that are both lightweight and impact-resistant. Industries such as consumer electronics and robotics benefit from this combination, as it allows for the production of durable yet lightweight casings and frames.
Note: To achieve optimal results, manufacturers often use co-molding techniques or specialized adhesives when bonding carbon fiber to plastics.
Composites
Combining carbon fiber sheets with other composite materials enhances their mechanical properties. For instance, hybrid composites that blend carbon fiber with fiberglass offer improved flexibility and cost-effectiveness. These materials find applications in wind turbine blades, sports equipment, and marine components.
Example: In the marine industry, hybrid composites provide the perfect balance of strength and elasticity, ensuring durability in harsh environments.
Adhesives and Bonding Agents
The compatibility of carbon fiber sheets with various bonding agents further simplifies their integration with other materials. Epoxy resins, polyurethane adhesives, and cyanoacrylates are commonly used to create strong, durable bonds. These adhesives ensure that the sheets maintain their structural integrity even under stress.
Practical Considerations
When combining carbon fiber sheets with other materials, several factors influence the outcome:
- Thermal Expansion: Materials with different thermal expansion rates may require specialized bonding techniques to prevent delamination.
- Surface Preparation: Proper cleaning and sanding of surfaces improve adhesion and ensure a secure bond.
- Load Distribution: Engineers must consider load distribution to prevent stress concentrations at bonding points.
By understanding these factors, industries can maximize the performance and longevity of carbon fiber-based assemblies. The ability of 4×8 carbon fiber sheets to complement other materials underscores their value as a cornerstone of modern engineering.
Installation and Maintenance Best Practices for 4×8 Carbon Fiber Sheets
Cutting and Shaping Techniques
Tools and Equipment
Cutting and shaping a 4×8 carbon fiber sheet requires precision and the right tools. Using appropriate equipment ensures clean cuts and prevents damage to the material. The following tools are highly recommended:
- Hand Saws: Hacksaws or coping saws equipped with metal-cutting blades are ideal for straight cuts. A blade with a higher teeth-per-inch (TPI) count produces smoother edges.
- Rotary Tool: A rotary tool, such as a Dremel, fitted with a diamond-coated cutting wheel, is effective for intricate cuts and curves.
- Angle Grinder: For straight lines, an angle grinder with a standard metal-cutting abrasive wheel offers efficiency and precision.
Each tool serves a specific purpose, allowing users to tailor their approach based on the complexity of the project.
Safety Precautions
Safety is paramount when working with carbon fiber sheets. The cutting process generates fine dust particles that can irritate the skin and respiratory system. To ensure safety:
- Wear protective gloves to prevent skin irritation.
- Use a dust mask or respirator to avoid inhaling carbon fiber particles.
- Work in a well-ventilated area or use a vacuum system to minimize airborne dust.
- Always secure the sheet firmly to prevent movement during cutting.
Adhering to these precautions protects both the user and the material, ensuring a safe and efficient process.
Bonding and Assembly
Adhesives and Fasteners
Proper bonding and assembly techniques enhance the structural integrity of carbon fiber applications. Epoxy resins are the most commonly used adhesives due to their strong bonding capabilities and compatibility with carbon fiber. For mechanical assembly, stainless steel or titanium fasteners are preferred to prevent corrosion.
When applying adhesives:
- Clean the bonding surfaces thoroughly to remove dust and grease.
- Use clamps or weights to maintain pressure during curing.
- Follow the manufacturer’s instructions for curing times and temperatures.
For fasteners, pre-drilling holes with a carbide-tipped drill bit prevents cracking or delamination.
Avoiding Common Mistakes
Mistakes during bonding and assembly can compromise the performance of the material. To avoid common errors:
- Do not over-tighten fasteners, as this may damage the sheet.
- Avoid using incompatible adhesives that could weaken the bond.
- Ensure even pressure distribution to prevent warping or uneven bonding.
Attention to detail during assembly ensures the longevity and reliability of the finished product.
Maintenance and Longevity
Cleaning and Care
Regular cleaning preserves the appearance and performance of a 4×8 carbon fiber sheet. A soft cloth with mild soap and water effectively removes dirt and grime. For stubborn stains, specialized carbon fiber cleaners are available.
Best practices for cleaning include:
- Avoid abrasive materials or harsh chemicals that could scratch or damage the finish.
- Test any cleaner on a small, inconspicuous area before full application.
Routine cleaning not only maintains the sheet’s aesthetic appeal but also extends its lifespan.
Repairing Damages
Despite its durability, carbon fiber may sustain minor damages over time. Small scratches can be polished out using fine-grit sandpaper and a polishing compound. For more significant damage, such as cracks or delamination, epoxy resin can be used to fill and reinforce the affected area.
Steps for effective repair:
- Sand the damaged area to remove loose fibers.
- Apply epoxy resin evenly and allow it to cure completely.
- Sand and polish the surface for a smooth finish.
Timely repairs prevent further deterioration and ensure the material remains functional for years.
4×8 carbon fiber sheets stand out as a game-changing material across industries due to their unmatched combination of strength, lightweight properties, and durability. Their ability to resist corrosion and perform under extreme temperatures makes them indispensable in demanding environments.
Key Takeaways:
- These sheets reduce structural weight, leading to cost savings in construction and transportation.
- Their strength minimizes material usage, enhancing efficiency and sustainability.
Industries like aerospace and automotive have embraced carbon fiber sheets for their ability to improve fuel efficiency and safety. As technology advances, exploring their potential in emerging fields promises even greater innovation.
FAQ
What are 4×8 carbon fiber sheets made of?
4×8 carbon fiber sheets consist of carbon fibers embedded in a polymer matrix. This combination creates a lightweight yet strong material with excellent durability and resistance to environmental factors like corrosion and temperature fluctuations.
How do carbon fiber sheets compare to traditional materials like steel?
Carbon fiber sheets offer a superior strength-to-weight ratio compared to steel. They are lighter, more corrosion-resistant, and easier to handle. These properties make them ideal for industries requiring high performance and efficiency.
Can carbon fiber sheets be customized for specific applications?
Yes, manufacturers offer customization options, including thickness, size, surface finish, and fiber orientation. These features allow engineers and designers to tailor the sheets for specific functional and aesthetic requirements.
Are carbon fiber sheets environmentally friendly?
Carbon fiber sheets contribute to sustainability by reducing energy consumption during production and transportation. Their durability minimizes waste, while their lightweight nature enhances fuel efficiency in vehicles and aircraft, lowering emissions.
What industries benefit most from using carbon fiber sheets?
Industries like aerospace, automotive, construction, and sports benefit significantly. These sheets improve performance, reduce weight, and enhance durability in applications ranging from aircraft components to sports equipment.
How should carbon fiber sheets be maintained?
Regular cleaning with mild soap and water preserves their appearance and performance. Avoid abrasive materials or harsh chemicals. For minor damages, sanding and epoxy resin repairs restore functionality and aesthetics.
Are carbon fiber sheets suitable for outdoor use?
Yes, carbon fiber sheets resist corrosion, UV exposure, and temperature fluctuations, making them ideal for outdoor applications like marine components, wind turbine blades, and architectural panels.
What tools are required to cut carbon fiber sheets?
Cutting carbon fiber sheets requires tools like hand saws, rotary tools, or angle grinders with diamond-coated or metal-cutting blades. Proper safety equipment, including gloves and masks, ensures safe handling during the process.