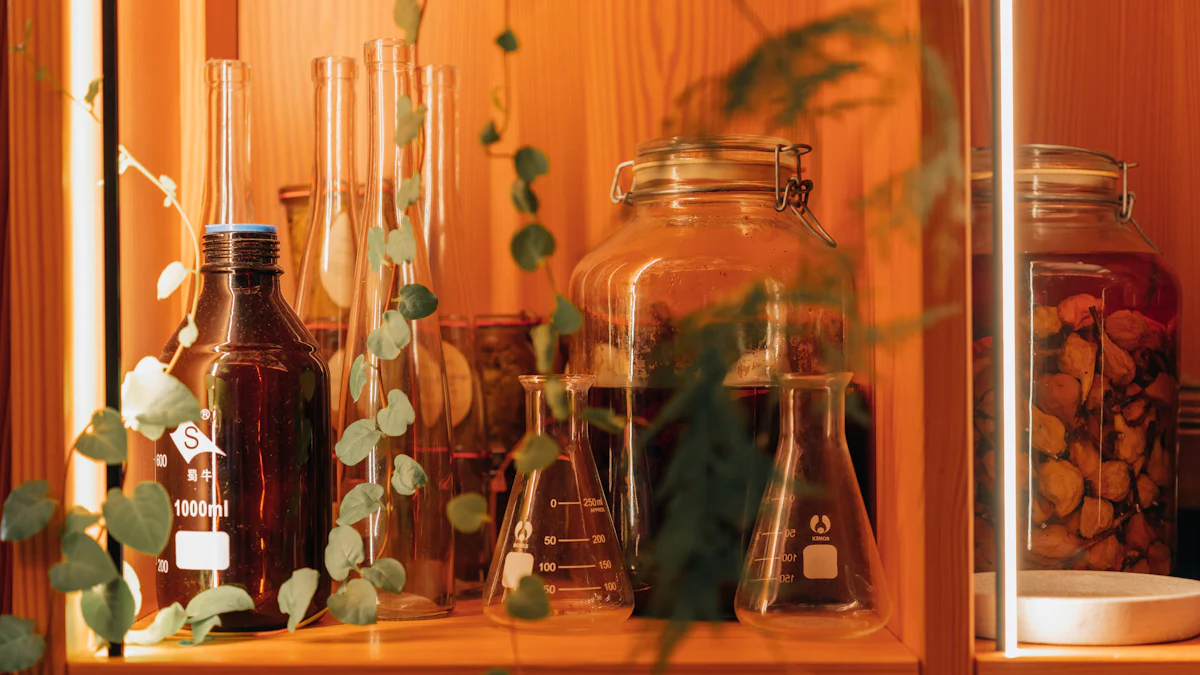
Silicon carbide (SiC) chemical trays have become indispensable in industries requiring high-performance materials. Their exceptional thermal conductivity, chemical resistance, and mechanical strength make them ideal for demanding applications such as semiconductor manufacturing, sintering, and chemical processing. These trays withstand extreme temperatures and harsh environments while maintaining structural integrity. Advanced manufacturing techniques now enhance their precision and durability, ensuring consistent results in critical processes. Selecting the right SiC chemical tray involves understanding these unique properties and aligning them with specific operational needs to optimize efficiency and reliability.
Key Takeaways
Understand your application needs: Assess the specific chemicals, temperatures, and mechanical loads your SiC tray will encounter to ensure optimal performance.
Prioritize chemical resistance: Choose trays that are compatible with the chemicals used in your processes to prevent contamination and damage.
- Evaluate thermal tolerance: Ensure the SiC tray can withstand the maximum operating temperatures of your application to maintain structural integrity.
- Consider load capacity: Select trays with sufficient mechanical strength to support the weight and type of materials during operation without deformation.
- Focus on manufacturing quality: Partner with reputable suppliers to guarantee high-quality trays that meet stringent production standards for reliability.
- Ensure accurate sizing: Measure the internal dimensions of your equipment carefully to avoid misalignment and inefficiencies during operation.
- Explore customization options: Work with manufacturers to tailor SiC trays to your specific needs, enhancing compatibility and operational efficiency.
Understanding Your Application Needs
Selecting the right SiC chemical tray begins with a thorough understanding of your application requirements. Each operational environment presents unique challenges, and the tray must meet these demands to ensure optimal performance and longevity. Below are the key factors to consider when evaluating your needs.
Chemical Resistance and Compatibility
Chemical resistance is a critical factor for any SiC chemical tray. Silicon carbide exhibits exceptional resistance to corrosion and chemical degradation, making it suitable for environments involving harsh chemicals. Its high chemical stability ensures that it can withstand exposure to acids, alkalis, and other reactive substances without compromising its structural integrity.
"Silicon carbide’s chemical resistance stems from its strong covalent bonds between silicon and carbon atoms, which create a highly stable crystal lattice."
When choosing a tray, assess the specific chemicals used in your processes. Ensure that the tray material is compatible with these substances to prevent reactions that could lead to contamination or damage. This compatibility not only protects the tray but also safeguards the materials being processed.
Temperature and Thermal Tolerance
Silicon carbide’s ability to endure extreme temperatures makes it indispensable in high-temperature applications. Its high thermal conductivity allows it to dissipate heat efficiently, reducing the risk of thermal stress. Additionally, its resistance to thermal shock ensures that it remains stable during rapid temperature fluctuations.
Industries such as semiconductor manufacturing and sintering often require materials that can perform reliably under intense heat. SiC chemical trays excel in these conditions, maintaining their mechanical strength and dimensional stability even at elevated temperatures. Always verify the maximum operating temperature of the tray to ensure it aligns with your application’s thermal demands.
Load Capacity and Mechanical Strength
The mechanical strength of silicon carbide is one of its defining characteristics. With a hardness comparable to diamond, SiC can withstand significant mechanical stress without deformation or failure. This makes it ideal for applications requiring high load-bearing capacity.
Evaluate the weight and type of materials the tray will support during operation. The tray must handle these loads without compromising its structural integrity. Silicon carbide’s abrasion resistance further enhances its durability, ensuring long-term performance even in demanding environments.
"Silicon carbide’s lightweight yet robust nature makes it a preferred choice for industries requiring both strength and efficiency."
By understanding these application-specific needs, you can select a SiC chemical tray that delivers reliability, efficiency, and longevity in your operational processes.
Material and Construction Considerations
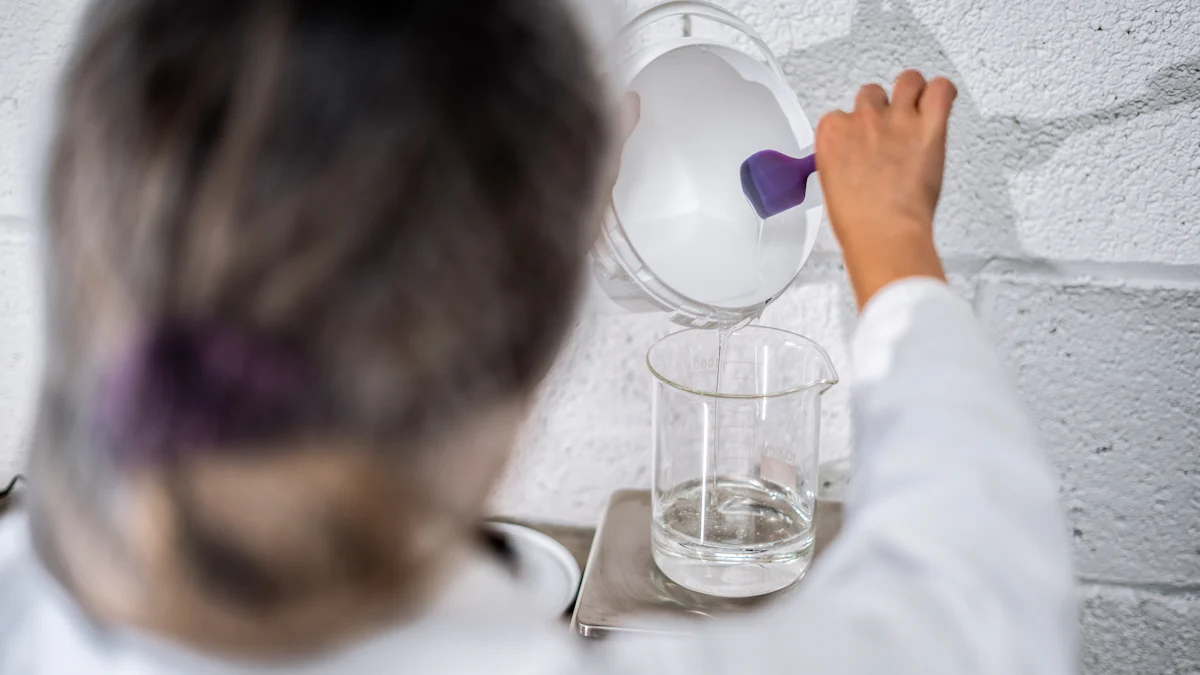
When selecting a SiC chemical tray, understanding the material’s inherent advantages and the importance of manufacturing quality ensures optimal performance and durability. These considerations directly impact the tray’s ability to meet the demands of various industrial applications.
Advantages of Silicon Carbide (SiC)
Silicon carbide stands out as a material of choice due to its exceptional properties. Its high hardness, comparable to diamond, provides superior wear resistance, making it ideal for environments with abrasive conditions. This durability ensures long-term use, even in demanding applications such as semiconductor manufacturing and sintering.
"Silicon carbide’s unique crystal structure contributes to its remarkable mechanical strength and thermal stability, enabling it to endure extreme conditions without compromising performance."
The material’s high thermal conductivity allows efficient heat dissipation, reducing the risk of thermal stress during high-temperature operations. This feature proves essential in industries like chemical processing and heat treatment, where maintaining consistent temperatures is critical. Additionally, SiC’s corrosion resistance ensures stability when exposed to aggressive chemicals, safeguarding both the tray and the materials it handles.
SiC trays also exhibit chemical inertness, preventing reactions with substances during processes. This property makes them suitable for applications involving acids, alkalis, and other reactive agents. Their lightweight yet robust nature further enhances their usability, offering ease of handling without sacrificing strength.
Importance of Manufacturing Quality
The quality of manufacturing plays a pivotal role in determining the performance and reliability of a SiC chemical tray. Precision in production ensures that the trays meet exact specifications, allowing seamless integration into existing systems. High-quality trays maintain consistent mechanical properties, even under extreme conditions, ensuring operational efficiency.
Manufacturers like Heeger Materials and Nextgen Advanced Materials INC emphasize advanced production techniques to enhance the trays’ durability and precision. Features such as high hardness, abrasion resistance, and stable mechanical properties at elevated temperatures result from meticulous manufacturing processes. These qualities make the trays suitable for critical applications, including integrated circuit production and furnace components.
"Investing in SiC trays from reputable suppliers guarantees not only superior material properties but also adherence to stringent quality standards."
Proper handling during storage and transportation further minimizes the risk of damage, preserving the tray’s integrity. Partnering with manufacturers who prioritize quality control ensures that the trays deliver consistent performance, reducing downtime and maintenance costs.
By focusing on the advantages of silicon carbide and the importance of manufacturing quality, industries can select SiC trays that align with their operational needs. This approach maximizes efficiency and ensures long-lasting performance in challenging environments.
Size and Dimension Requirements
Selecting the correct size and dimensions for a SiC chemical tray ensures seamless integration into existing systems and enhances operational efficiency. Proper measurements and design considerations prevent issues such as misalignment, inefficiency, or damage to materials during processing.
Accurate Measurements for Seamless Integration
Accurate measurements play a crucial role in ensuring that the SiC tray fits perfectly within the designated equipment or system. Misaligned trays can lead to inefficiencies, increased wear, or even damage to the materials being processed. Industries such as semiconductor manufacturing and solar battery production often require precise dimensions to maintain the integrity of their operations.
To achieve seamless integration, manufacturers recommend measuring the internal dimensions of the equipment where the tray will be used. This includes accounting for any additional components, such as wafer holders or support structures, that may affect the tray’s fit. Companies like Edgetech Industries and Heeger Materials specialize in providing customized SiC trays tailored to specific dimensional requirements, ensuring compatibility with various industrial applications.
"Precision in sizing not only enhances operational efficiency but also minimizes the risk of material loss or contamination during processing."
Additionally, verifying the thickness of the tray is essential. A tray that is too thin may compromise durability, while one that is too thick could hinder heat transfer or chemical interactions. By working with reputable suppliers, industries can obtain trays that meet exact specifications, ensuring optimal performance.
Stackability and Space Optimization
Stackability is another critical factor when selecting a SiC chemical tray, especially in industries where space optimization is a priority. Trays designed for stackability allow for efficient use of vertical space, reducing the overall footprint of storage or operational setups. This feature proves particularly beneficial in environments with limited space, such as laboratories or compact manufacturing facilities.
Silicon carbide trays, known for their lightweight yet robust nature, offer excellent stackability without compromising structural integrity. Manufacturers often design these trays with uniform dimensions and reinforced edges to facilitate stable stacking. For example, square-shaped SiC trays used in solar battery production are specifically crafted to maximize space utilization while maintaining durability.
"Stackable SiC trays streamline storage and transportation processes, reducing handling time and minimizing the risk of damage."
Space optimization also involves considering the arrangement of materials within the tray. Trays with well-planned layouts can accommodate more items per batch, increasing productivity and reducing operational costs. Industries such as sintering, chemical processing, and heat treatment benefit significantly from trays that combine stackability with efficient material arrangement.
By prioritizing accurate measurements and stackability, industries can ensure that their SiC chemical trays deliver both functionality and efficiency. These considerations not only enhance operational workflows but also contribute to long-term cost savings and improved performance.
Customization and Compatibility
Customization and compatibility play a pivotal role in ensuring that a SiC chemical tray meets the unique demands of various industries.
Tailored Solutions for Specific Applications
Industries such as semiconductor manufacturing, solar battery production, and chemical processing often require specialized trays to meet their unique operational needs. Manufacturers offer tailored solutions by customizing the size, shape, and design of silicon carbide trays. These customizations ensure that the trays align with specific applications, such as wafer processing, sintering, or heat treatment.
For example, in the LED industry, precise dimensions and configurations are essential to maintain product quality during manufacturing. Similarly, the solar industry benefits from square-shaped trays designed to optimize space utilization and improve productivity. Companies like Edgetech Industries and Heeger Materials specialize in creating high-purity, pressureless sintered SiC trays that cater to these specific requirements.
"Customization ensures that the tray not only fits the equipment but also enhances the overall efficiency of the process."
Tailored trays also address challenges such as handling aggressive chemicals or enduring extreme temperatures. By working closely with manufacturers, industries can specify the exact properties needed, such as enhanced corrosion resistance or increased thermal conductivity. This level of customization ensures that the trays perform reliably under demanding conditions.
Ensuring System Compatibility
System compatibility is critical when integrating a SiC chemical tray into existing equipment or processes. A mismatch in dimensions, material properties, or design can lead to inefficiencies, increased wear, or even equipment damage. To avoid these issues, industries must ensure that the tray aligns perfectly with their operational systems.
Manufacturers prioritize compatibility by adhering to strict quality standards and offering detailed consultations. For instance, companies like Nexgen Advanced Materials INC and Precise Ceramic emphasize the importance of stable mechanical properties and precise dimensions. These features allow the trays to integrate seamlessly into systems used for semiconductor wafer processing, ICP etching, or furnace components.
"Ensuring compatibility minimizes disruptions, reduces maintenance costs, and extends the lifespan of both the tray and the equipment."
Industries should also consider factors such as stackability and ease of handling when evaluating compatibility. Trays designed for efficient stacking not only save space but also streamline storage and transportation processes. This proves especially beneficial in compact facilities or high-volume production environments.
By focusing on customization and compatibility, industries can select SiC trays that meet their specific needs while ensuring smooth integration into their workflows. This approach maximizes efficiency, reduces operational risks, and enhances overall performance.
Selecting the best SiC chemical tray demands a strategic approach. Industries must evaluate application needs, material properties, and size requirements to ensure optimal performance. Silicon carbide’s durability, thermal stability, and resistance to corrosive environments make it indispensable for high-demand applications like semiconductor fabrication and chemical processing. Partnering with reputable manufacturers, such as Heeger Materials or Nextgen Advanced Materials, guarantees access to high-quality trays tailored to specific operational needs. These suppliers offer customization options and fast delivery, ensuring seamless integration and long-term reliability in critical processes.
FAQ
What are SiC trays used for in the powder metallurgy industry?
SiC trays serve as high-temperature-resistant surfaces in the powder metallurgy industry. They support uniform heating and cooling, ensuring consistent results during sintering and other thermal processes.
How are SiC trays utilized in semiconductor manufacturing?
SiC trays play a vital role in processes like epitaxy, diffusion, and oxidation.
What is the role of SiC trays in the solar industry?
SiC trays are essential in the production of photovoltaic cells and other solar energy components. They provide high thermal conductivity and stability, which are critical for processes requiring precise thermal control.
How do SiC trays benefit the glass and ceramic industry?
SiC trays are widely used in the glass and ceramic industry for firing and annealing processes. Their stability at high temperatures and resistance to thermal shocks ensure reliable performance during production.
Why are SiC trays important in laboratory equipment?
Laboratories rely on SiC trays for high-temperature experiments and processes. These trays act as containers or platforms for reactions and thermal treatments, offering excellent heat and corrosion resistance.
What makes SiC trays suitable for furnace components?
SiC trays are ideal for high-temperature furnaces and kilns. They function as support trays and components, handling extreme heat and thermal cycling without deforming, ensuring consistent furnace operations.
How are SiC trays used in metal casting?
In metal casting, SiC trays handle molten metals with ease. Their thermal shock resistance and durability allow them to withstand rapid temperature changes and mechanical stresses, ensuring reliable performance.
What advantages do SiC trays offer in chemical processing?
SiC trays excel in chemical processing industries by holding and transporting corrosive chemicals. Their chemical inertness and resistance to high temperatures make them perfect for handling aggressive substances.
Why are SiC trays preferred for sintering and heat treatment processes?
SiC trays are widely used in sintering and heat treatment processes due to their ability to withstand high temperatures. They provide uniform heat distribution, ensuring consistent results and precise thermal control.
What are the key characteristics of SiC trays according to leading manufacturers?
Manufacturers like Edgetech Industries and Nextgen Advanced Materials highlight the exceptional properties of SiC trays. These include high hardness, wear resistance, thermal conductivity, and stable mechanical properties under extreme conditions. Their corrosion resistance further enhances their suitability for demanding industrial applications.