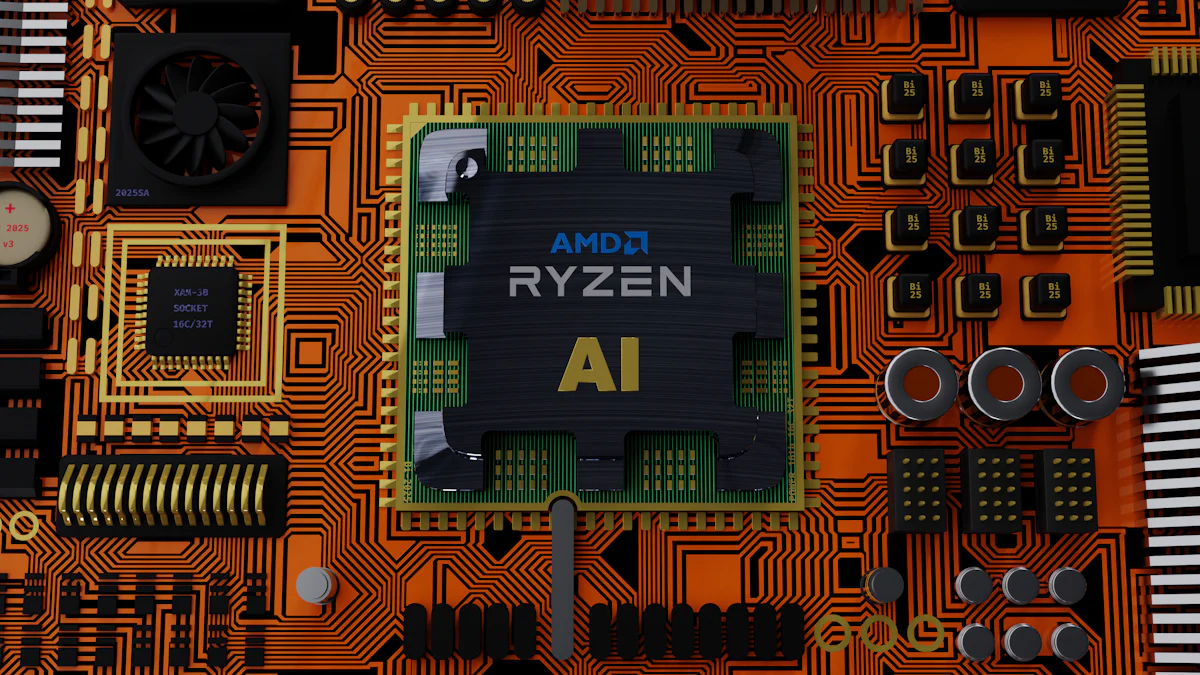
Selecting the right wafer boat plays a pivotal role in semiconductor manufacturing. It ensures precise wafer alignment, minimizes defects, and enhances overall yield. For instance, silicon carbide wafer boats, known for their exceptional mechanical properties, provide superior durability and reliability during high-temperature processes. Additionally, advanced designs reduce wafer backside faults, preventing defect redistribution that could compromise neighboring wafers. By optimizing process efficiency and maintaining product quality, the wafer boat becomes an indispensable component in achieving consistent manufacturing performance.
Key Takeaways
- Choosing the right wafer boat is crucial for optimizing semiconductor manufacturing, impacting yield and product quality.
- Material selection is key; silicon carbide is ideal for high-temperature processes, while quartz is best for ultra-clean environments.
- Proper sizing and capacity of wafer boats enhance efficiency and prevent misalignment during processing.
- Regular maintenance and inspections of wafer boats can extend their lifespan and ensure consistent performance.
- Consulting with suppliers for customization options can improve compatibility with specific equipment and processes.
- Testing wafer boats for compatibility and performance before purchase minimizes risks of defects and operational inefficiencies.
- Investing in high-quality materials may have a higher upfront cost but leads to long-term savings through reduced maintenance and improved reliability.
Understanding Wafer Boats and Their Role in Semiconductor Manufacturing
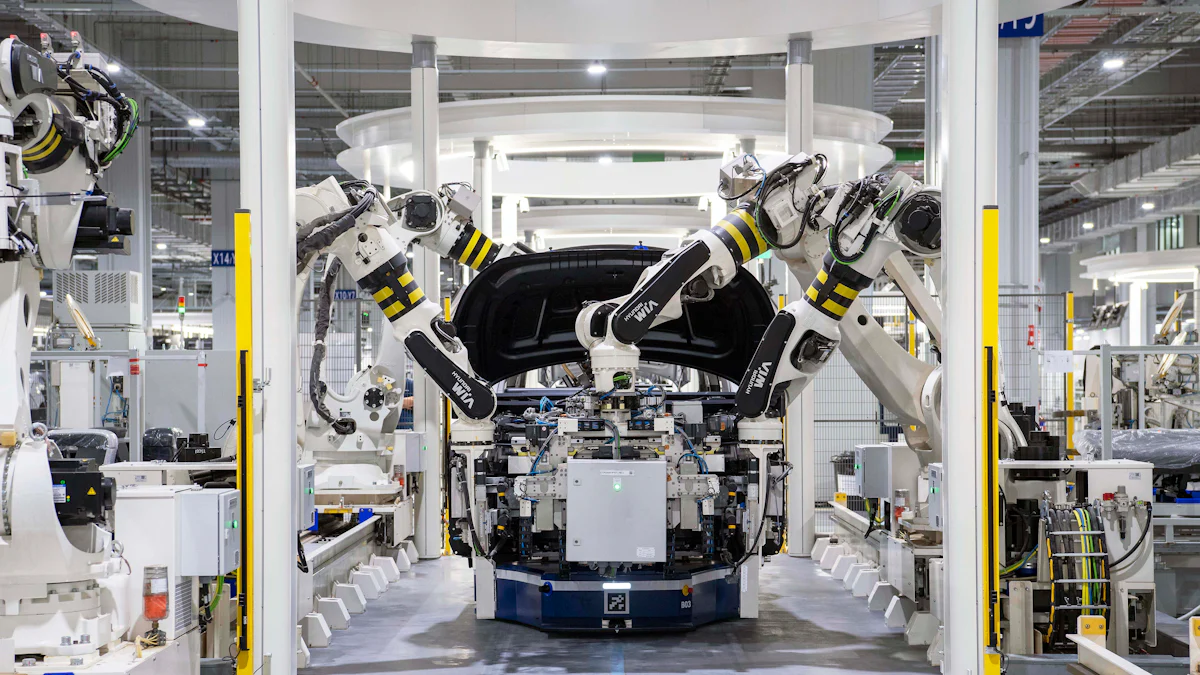
What Is a Wafer Boat?
A wafer boat is a specialized component used in semiconductor manufacturing to securely hold and transport wafers during various processing steps. These boats ensure precise alignment and stability, which are critical for achieving consistent results in high-precision environments. Typically, wafer boats are designed to accommodate multiple wafers simultaneously, optimizing space and efficiency within processing equipment.
The construction of wafer boats often involves advanced materials like silicon carbide or high-purity ceramics. These materials provide the necessary mechanical strength and thermal stability to withstand the demanding conditions of semiconductor processes. For instance, silicon carbide wafer boats, known for their exceptional purity (up to 99.99%), offer superior resistance to heat and plasma, making them ideal for high-temperature applications.
The Purpose of Wafer Boats in Semiconductor Processes
Wafer boats play a vital role in ensuring the smooth execution of semiconductor manufacturing processes. They serve as carriers that protect wafers from contamination and physical damage during critical operations such as diffusion, ion implantation, and etching. By maintaining the structural integrity of wafers, these boats help minimize defects and improve overall yield.
In addition to providing physical support, wafer boats contribute to process efficiency. Their design ensures uniform exposure of wafers to processing environments, such as gases or plasma, which is essential for achieving consistent results. For example, during crystal growth or diffusion processes, the precise arrangement of wafers within the boat allows for even distribution of heat and chemicals, enhancing the quality of the final product.
Common Materials Used in Wafer Boats
The choice of material for wafer boats significantly impacts their performance and durability. Manufacturers commonly use materials that exhibit high thermal resistance, chemical stability, and mechanical strength. Some of the most widely used materials include:
- Silicon Carbide (SiC): Known for its excellent mechanical properties, silicon carbide offers higher strength and stiffness compared to carbon-based materials. Its recrystallized structure enhances durability, making it suitable for handling delicate wafers during transport and processing.
- Quartz: Ultra-high purity quartz, with a working temperature of up to 1200°C, is another popular choice. It provides exceptional thermal resistance and is often used in applications requiring minimal particle generation.
- Graphite: Graphite wafer boats are valued for their lightweight nature and thermal conductivity. They are often used in processes where rapid heating and cooling cycles are required.
- Ceramics: High-purity ceramics, such as those made from silicon carbide, are frequently used in single-wafer applications. These materials ensure minimal contamination and excellent plasma resistance.
Each material offers unique advantages, allowing manufacturers to select the most suitable option based on specific process requirements. For instance, Semicorex’s Silicon Carbide Wafer Boat combines ultra-high purity with outstanding heat resistance, making it an ideal choice for semiconductor processing equipment.
Exploring Types of Wafer Boats and Their Applications
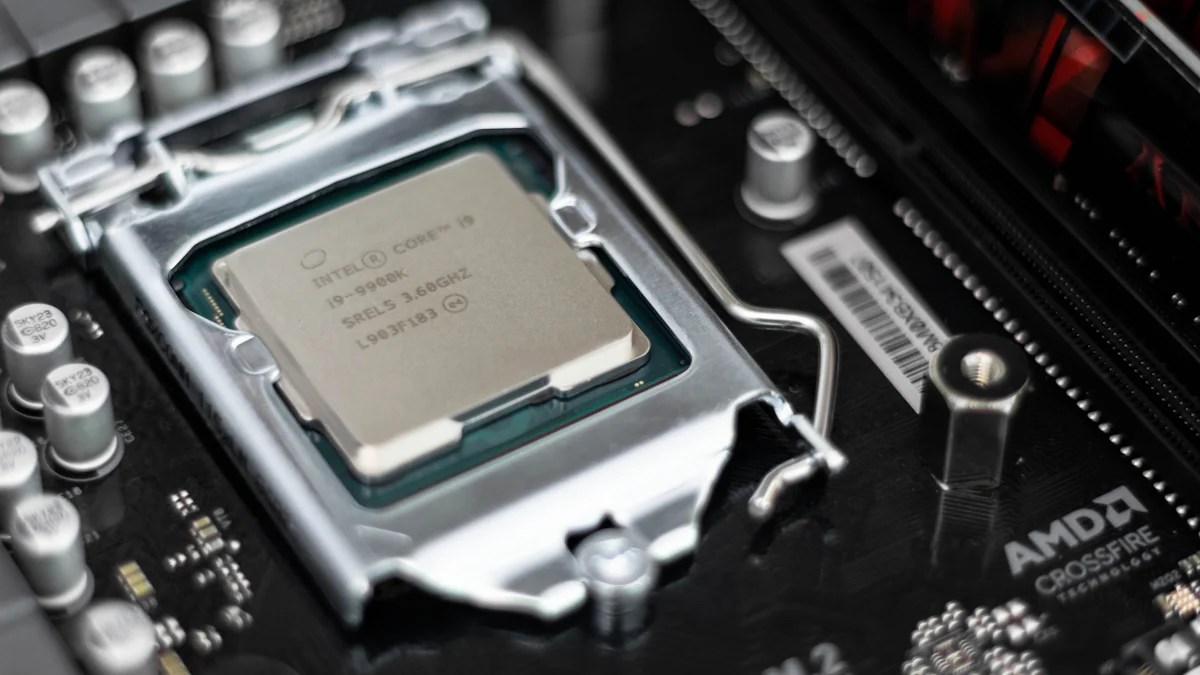
Quartz Wafer Boats
Quartz wafer boats are widely recognized for their exceptional thermal resistance and high purity. These boats can withstand temperatures up to 1200°C, making them ideal for processes that demand extreme heat stability. Their precise fabrication tolerances ensure accurate wafer alignment, which is critical for maintaining uniformity during semiconductor manufacturing.
Quartz boats also minimize particle generation, reducing the risk of contamination. This feature makes them a preferred choice for applications requiring ultra-clean environments, such as diffusion and oxidation processes. Manufacturers often rely on quartz wafer boats when working with sensitive wafers that demand minimal interaction with impurities.
Key Advantage: Quartz wafer boats combine strong heat resistance with precise design, ensuring reliable performance in high-temperature and contamination-sensitive processes.
Silicon Carbide (SiC) Wafer Boats
Silicon carbide wafer boats stand out due to their superior mechanical properties. They exhibit high strength and stiffness, which provide excellent durability during demanding semiconductor processes. The recrystallized structure of silicon carbide enhances its resistance to thermal shock and chemical corrosion, making it suitable for high-temperature applications.
These boats also share a similar expansion coefficient with silicon wafers. This compatibility reduces faults on the wafer backside, preventing defect redistribution and improving overall yield. Silicon carbide wafer boats are often used in plasma etching and ion implantation processes, where their robustness ensures consistent performance.
Key Advantage: Silicon carbide wafer boats offer unmatched durability and thermal stability, making them indispensable for high-precision and high-temperature semiconductor applications.
Graphite Wafer Boats
Graphite wafer boats are valued for their lightweight nature and excellent thermal conductivity. These characteristics enable rapid heating and cooling cycles, which are essential for processes like crystal growth and annealing. Graphite’s unique properties also contribute to improving the quality of silicon wafers, enhancing their performance in solar energy conversion.
Despite their lightweight design, graphite boats maintain structural integrity under high temperatures. Their ability to handle thermal stress without deformation makes them a reliable option for various semiconductor manufacturing stages. Additionally, graphite wafer boats are cost-effective, offering a balance between performance and affordability.
Key Advantage: Graphite wafer boats deliver efficient thermal management and cost-effectiveness, making them a versatile choice for diverse semiconductor processes.
Metal Wafer Boats
Metal wafer boats offer a unique combination of strength, durability, and thermal conductivity, making them a reliable choice for specific semiconductor manufacturing processes. These boats are typically constructed from high-performance metals such as stainless steel, molybdenum, or titanium. Their robust structure ensures stability and resistance to deformation, even under extreme thermal and mechanical stress.
Metal wafer boats excel in applications requiring high mechanical strength and precise wafer handling. Their ability to maintain structural integrity under repeated thermal cycling makes them suitable for processes like annealing and chemical vapor deposition (CVD). Additionally, the metallic composition allows for efficient heat transfer, ensuring uniform temperature distribution across wafers.
Key Advantage: Metal wafer boats provide exceptional mechanical stability and thermal conductivity, making them ideal for demanding semiconductor processes that require consistent performance.
Benefits of Metal Wafer Boats
- High Strength and Durability: Metal boats resist wear and deformation, ensuring long-term reliability in high-stress environments.
- Thermal Conductivity: Metals like molybdenum and titanium facilitate efficient heat transfer, promoting uniform processing conditions.
- Corrosion Resistance: Certain metal alloys, such as stainless steel, offer excellent resistance to chemical corrosion, reducing the risk of contamination.
- Customizability: Manufacturers can design metal wafer boats to meet specific size and capacity requirements, enhancing their versatility.
Applications of Metal Wafer Boats
Metal wafer boats are commonly used in processes where mechanical stability and thermal efficiency are critical. These include:
- Annealing: The robust structure of metal boats withstands the high temperatures and rapid cooling cycles involved in annealing processes.
- Chemical Vapor Deposition (CVD): Their thermal conductivity ensures even heat distribution, improving the quality of deposited films.
- Diffusion Processes: Metal boats provide reliable support for wafers during diffusion, minimizing the risk of misalignment or damage.
While metal wafer boats offer numerous advantages, their suitability depends on the specific requirements of the manufacturing process. By evaluating factors such as material compatibility, thermal resistance, and cost, manufacturers can determine whether metal wafer boats align with their operational needs.
Key Considerations When Choosing a Wafer Boat
Material Compatibility with Your Process
Selecting the right material for a wafer boat is crucial to ensure compatibility with specific semiconductor manufacturing processes. Each material offers unique properties that cater to different operational requirements. For instance, silicon carbide (SiC) wafer boats exhibit exceptional thermal and chemical resistance, making them ideal for high-temperature processes like diffusion and ion implantation. Their recrystallized structure enhances durability, ensuring safe handling of delicate wafers.
Quartz wafer boats, on the other hand, provide ultra-high purity and minimal particle generation, which are essential for processes requiring contamination-free environments. Graphite wafer boats excel in rapid heating and cooling cycles due to their superior thermal conductivity. Manufacturers must evaluate the chemical exposure and temperature conditions of their processes to determine the most suitable material. A mismatch in material compatibility can lead to contamination, reduced yield, or equipment damage.
Tip: Always consult with suppliers or manufacturers to confirm the material’s suitability for your specific application.
Size and Capacity Requirements
The size and capacity of a wafer boat directly impact its efficiency and functionality. Semiconductor manufacturing often involves processing multiple wafers simultaneously, so the boat must accommodate the required number of wafers without compromising alignment or stability. Customized wafer boats, such as those offered by MSE Supplies, feature precisely designed slots to securely hold wafers in place, preventing movement during critical operations.
Manufacturers should consider the dimensions of their equipment and the wafer sizes they handle. Oversized boats may not fit into processing chambers, while undersized ones could limit throughput. Additionally, the spacing between wafers within the boat plays a vital role in ensuring uniform exposure to heat and chemicals. Properly sized wafer boats optimize process efficiency and reduce the risk of defects.
Key Insight: Customization options allow manufacturers to tailor wafer boats to their specific size and capacity needs, enhancing operational precision.
Thermal and Chemical Resistance
Thermal and chemical resistance are essential attributes of a high-quality wafer boat. Semiconductor processes often involve extreme temperatures and exposure to corrosive chemicals. Materials like silicon carbide and quartz excel in these conditions due to their robust thermal stability and resistance to chemical degradation. For example, silicon carbide wafer boats can withstand high temperatures while maintaining structural integrity, making them suitable for processes such as crystal growth and etching.
Chemical resistance ensures that the wafer boat does not react with processing chemicals, which could lead to contamination or material degradation. Quartz boats, known for their inertness, are often used in oxidation processes where chemical purity is critical. Manufacturers must assess the thermal and chemical demands of their processes to select a wafer boat that can endure these challenges without compromising performance.
Pro Tip: Regular maintenance and inspection of wafer boats can help identify wear and tear caused by thermal or chemical stress, ensuring consistent performance over time.
Equipment and Automation Compatibility
Ensuring compatibility between wafer boats and semiconductor manufacturing equipment is critical for seamless operations. Wafer boats must align with the dimensions and specifications of the processing chambers to avoid operational inefficiencies. For instance, customized silicon carbide (SiC) wafer boats feature precisely designed slots that securely hold wafers in place, preventing misalignment during automated processes. This design enhances the integration of wafer boats with advanced machinery, such as robotic arms and automated wafer handling systems.
Automation compatibility also depends on the material properties of the wafer boat. Materials like silicon carbide exhibit high stiffness and strength, which ensure stability during rapid movements in automated environments. These properties reduce the risk of wafer damage, particularly in high-speed manufacturing lines. Additionally, the thermal and chemical resistance of materials like quartz and SiC ensures that wafer boats can endure the demanding conditions of automated processes without compromising performance.
Tip: Manufacturers should consult equipment specifications and collaborate with suppliers to confirm that wafer boats meet the requirements of their automated systems. This proactive approach minimizes downtime and enhances production efficiency.
Cost and Durability
Cost and durability are key factors when selecting a wafer boat. While initial costs may vary depending on the material and design, long-term durability significantly impacts overall value. For example, semiconductor silicon carbide wafer boats offer exceptional mechanical properties, including higher strength and stiffness compared to carbon-based materials. This durability reduces the frequency of replacements, lowering maintenance costs over time.
Quartz wafer boats, known for their high purity and thermal resistance, provide excellent performance in contamination-sensitive processes. Although they may have a higher upfront cost, their ability to maintain structural integrity under extreme conditions ensures a longer lifespan. Similarly, graphite wafer boats deliver cost-effectiveness by balancing lightweight construction with efficient thermal conductivity, making them suitable for processes requiring rapid heating and cooling cycles.
When evaluating cost, manufacturers should also consider the potential impact of wafer boat failure on production. A poorly chosen wafer boat may lead to wafer defects, equipment damage, or process inefficiencies, resulting in higher operational costs. Investing in high-quality materials like silicon carbide or quartz ensures reliable performance and minimizes the risk of costly disruptions.
Key Insight: Prioritizing durability and material quality over initial cost can lead to significant savings in the long run. High-performance wafer boats not only enhance process efficiency but also reduce the need for frequent replacements, ensuring a better return on investment.
Step-by-Step Guide to Selecting the Right Wafer Boat
Identifying Your Process Requirements
The first step in selecting the right wafer boat involves understanding the specific needs of your semiconductor manufacturing process. Each process has unique requirements, such as temperature ranges, chemical exposure, and wafer dimensions. For instance, high-temperature processes like diffusion or ion implantation demand materials with exceptional thermal resistance, such as silicon carbide. On the other hand, processes requiring ultra-clean environments may benefit from quartz wafer boats due to their minimal particle generation.
Manufacturers must also consider the size and thickness of the wafers being processed. Wafers that are too large or too thin for the chosen wafer boat may experience stress or bending, leading to potential damage. Additionally, the number of wafers processed simultaneously should align with the boat’s capacity to ensure stability and prevent misalignment during operations. By clearly defining these requirements, manufacturers can narrow down their options and focus on wafer boats that meet their operational demands.
Tip: Create a checklist of process-specific requirements, including temperature, chemical exposure, wafer size, and capacity, to streamline the selection process.
Researching and Comparing Wafer Boat Options
Once the process requirements are identified, the next step involves researching and comparing available wafer boat options. Manufacturers should evaluate the materials, designs, and features of different wafer boats to determine their suitability for specific applications. For example, silicon carbide boats reduce friction between the wafer and the boat, minimizing faults on the wafer backside. This feature enhances yield and ensures consistent product quality.
When comparing options, it is essential to assess the durability and resistance of each material. Materials like quartz and silicon carbide offer excellent thermal and chemical resistance, making them ideal for demanding processes. Additionally, the design of the wafer boat plays a crucial role in maintaining wafer alignment and preventing sliding during processing. Boats with precisely designed slots provide better stability and reliability.
Pro Tip: Use a comparison chart to evaluate the pros and cons of each wafer boat material and design. Focus on factors like thermal resistance, chemical stability, and cost-effectiveness.
Consulting with Manufacturers or Suppliers
After narrowing down the options, consulting with manufacturers or suppliers provides valuable insights into the performance and compatibility of wafer boats. Reputable suppliers often have extensive knowledge of semiconductor manufacturing processes and can recommend the most suitable wafer boat for specific applications. They can also provide detailed specifications, such as material composition, thermal limits, and design features.
During consultations, manufacturers should inquire about customization options. Custom wafer boats tailored to specific equipment dimensions or process requirements can enhance operational efficiency. Suppliers may also offer testing services to ensure the selected wafer boat performs optimally under real-world conditions. This step minimizes the risk of incompatibility and ensures a seamless integration into existing manufacturing systems.
Key Insight: Collaborating with experienced suppliers not only simplifies the selection process but also ensures access to high-quality wafer boats that meet industry standards.
Testing for Compatibility and Performance
Testing wafer boats for compatibility and performance ensures they meet the specific demands of semiconductor manufacturing processes. Manufacturers must evaluate how well the selected wafer boat integrates with existing equipment and withstands operational conditions. This step minimizes risks such as wafer misalignment, contamination, or process inefficiencies.
To begin, manufacturers should conduct fit tests to confirm that the wafer boat aligns with the dimensions of processing chambers and automation systems. Misaligned boats can disrupt operations, leading to wafer damage or reduced yield. For example, wafer boats designed with precise slots prevent wafers from sliding during processing, ensuring stability and reliability.
Performance testing involves exposing the wafer boat to actual process conditions, such as high temperatures or chemical environments. Materials like silicon carbide demonstrate exceptional thermal resistance, maintaining structural integrity under extreme heat. Similarly, quartz boats excel in contamination-sensitive processes due to their ultra-high purity. Testing under real-world conditions verifies whether the material and design meet the required standards.
Pro Tip: Collaborate with suppliers to access testing services or prototypes. This approach allows manufacturers to assess the wafer boat’s performance before committing to a full-scale purchase.
Additionally, manufacturers should monitor the wafer boat’s impact on wafer quality. For instance, silicon wafer boats reduce friction between the wafer and the boat, minimizing backside faults. This feature enhances yield and ensures consistent product quality. By analyzing test results, manufacturers can identify potential issues and make informed adjustments.
Finalizing Your Purchase and Maintenance Plan
After completing compatibility and performance testing, manufacturers can finalize their purchase by selecting a wafer boat that meets all operational requirements. Key factors to consider include material durability, cost-effectiveness, and long-term reliability. High-quality materials like silicon carbide or quartz may have a higher upfront cost but offer superior performance and longevity, reducing replacement frequency.
When finalizing the purchase, manufacturers should also evaluate customization options. Custom-designed wafer boats tailored to specific equipment or process needs enhance efficiency and precision. Suppliers often provide detailed specifications and recommendations to ensure the chosen wafer boat aligns with manufacturing goals.
Key Insight: Investing in a durable and compatible wafer boat reduces operational disruptions and enhances overall productivity.
A comprehensive maintenance plan is essential to extend the lifespan of wafer boats and maintain consistent performance. Regular inspections help identify wear and tear caused by thermal or chemical stress. Cleaning protocols should align with the material’s properties to avoid damage. For example, quartz boats require gentle handling to preserve their high-purity surface, while silicon carbide boats benefit from periodic checks for structural integrity.
Manufacturers should also establish a schedule for replacing wafer boats based on usage patterns and process demands. Proactive maintenance minimizes the risk of unexpected failures, ensuring uninterrupted production.
Pro Tip: Partnering with suppliers for maintenance support or replacement parts streamlines the upkeep process and ensures access to high-quality components.
Choosing the right wafer boat is essential for optimizing semiconductor manufacturing processes. The selection impacts efficiency, product quality, and equipment performance. Key factors like material, size, and compatibility should guide the decision-making process. A systematic evaluation ensures that the chosen wafer boat aligns with specific operational needs. Investing in a high-quality wafer boat delivers long-term benefits, including reduced maintenance costs, improved yield, and enhanced reliability. Manufacturers who prioritize these considerations position themselves for sustained success in a competitive industry.
FAQ
What is the primary function of a wafer boat?
A wafer boat holds and transports wafers during semiconductor manufacturing processes. It ensures precise alignment and stability, which are essential for achieving consistent results in high-precision environments. By securely holding wafers, it minimizes contamination and physical damage.
How do I determine the best material for my wafer boat?
The choice of material depends on the specific requirements of your manufacturing process. For high-temperature applications, silicon carbide offers excellent thermal resistance and durability. Quartz is ideal for ultra-clean environments due to its high purity. Graphite works well for processes requiring rapid heating and cooling cycles. Manufacturers should evaluate their process conditions, such as temperature and chemical exposure, to select the most suitable material.
Tip: Consult with suppliers to confirm material compatibility with your specific application.
Can wafer boats be customized for specific equipment?
Yes, many manufacturers offer customization options for wafer boats. Custom designs ensure compatibility with specific equipment dimensions and process requirements. For example, customized slots can securely hold wafers in place, preventing misalignment during automated processes. Customization enhances operational efficiency and precision.
What are the advantages of silicon carbide wafer boats?
Silicon carbide wafer boats provide exceptional thermal and chemical resistance. They maintain structural integrity under extreme temperatures, making them suitable for high-temperature processes like diffusion and ion implantation. Their recrystallized structure enhances durability, reducing faults on the wafer backside and improving yield.
How do I ensure my wafer boat is compatible with automation systems?
To ensure compatibility, manufacturers should verify that the wafer boat aligns with the dimensions and specifications of their automated equipment. Materials like silicon carbide, known for their stiffness and strength, perform well in high-speed automated environments. Collaborating with suppliers to confirm specifications minimizes operational inefficiencies.
What maintenance practices extend the lifespan of wafer boats?
Regular inspections and cleaning help maintain wafer boat performance. Cleaning protocols should match the material’s properties. For instance, quartz boats require gentle handling to preserve their high-purity surface. Periodic checks for wear and tear caused by thermal or chemical stress ensure consistent performance. Establishing a replacement schedule based on usage patterns prevents unexpected failures.
Are quartz wafer boats suitable for all semiconductor processes?
Quartz wafer boats excel in processes requiring ultra-clean environments and high thermal resistance. They are commonly used in diffusion and oxidation processes. However, they may not be ideal for applications involving rapid heating and cooling cycles, where graphite boats perform better. Manufacturers should assess process-specific requirements before selecting quartz.
How does the size of a wafer boat impact manufacturing efficiency?
The size of a wafer boat affects its capacity and alignment within processing equipment. Boats that are too large may not fit into chambers, while undersized ones could limit throughput. Properly sized boats ensure uniform exposure to heat and chemicals, optimizing process efficiency and reducing defects.
What factors influence the cost of a wafer boat?
Material, design, and durability significantly impact the cost of a wafer boat. High-quality materials like silicon carbide or quartz may have a higher upfront cost but offer long-term reliability and reduced maintenance expenses. Manufacturers should consider the potential impact of wafer boat failure on production when evaluating cost.
Why is testing important before purchasing a wafer boat?
Testing ensures that the wafer boat meets the specific demands of the manufacturing process. Fit tests confirm compatibility with equipment dimensions, while performance tests evaluate the boat’s ability to withstand operational conditions. Testing minimizes risks such as wafer misalignment, contamination, or process inefficiencies, ensuring optimal performance.