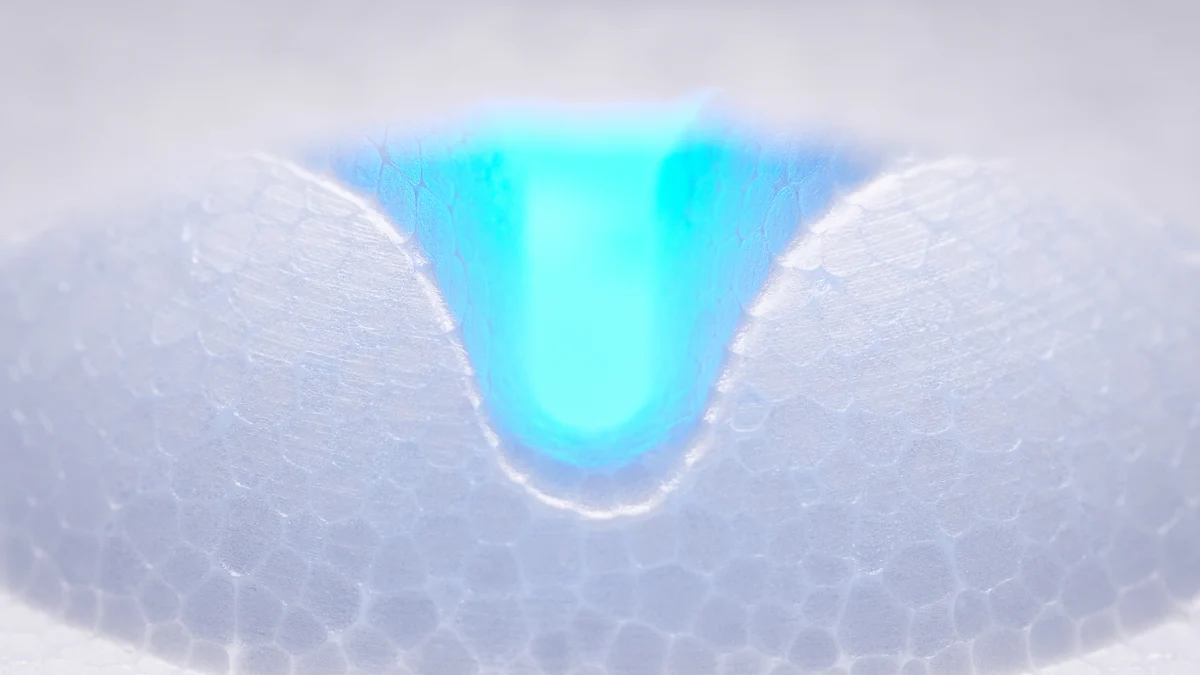
Choosing the right si wafer susceptor plays a vital role in semiconductor manufacturing. It directly impacts the performance and quality of your processes. You need to evaluate factors like material properties, thermal behavior, and cost to ensure the susceptor meets your requirements. Each manufacturing setup demands specific compatibility, making it essential to align the susceptor with your process. A systematic approach helps you make confident decisions that enhance efficiency and yield.
Key Takeaways
- Evaluate compatibility: Ensure the susceptor aligns with your specific semiconductor process to minimize disruptions and enhance efficiency.
- Prioritize material quality: Choose high-purity materials like silicon carbide or graphite for better thermal stability and chemical resistance.
- Assess thermal performance: Look for a susceptor that distributes heat evenly to avoid defects and ensure consistent results in your manufacturing.
- Match size and shape: Ensure the susceptor fits your wafer specifications and equipment setup to prevent inefficiencies in production.
- Consider cost-effectiveness: Focus on the total cost of ownership, balancing initial investment with long-term durability and performance benefits.
- Test before purchase: Conduct trials to validate the susceptor’s performance in your environment, ensuring it meets your operational needs.
- Explore customization: If your process has unique requirements, consider custom susceptors to achieve optimal compatibility and results.
Understanding Si Wafer Susceptors
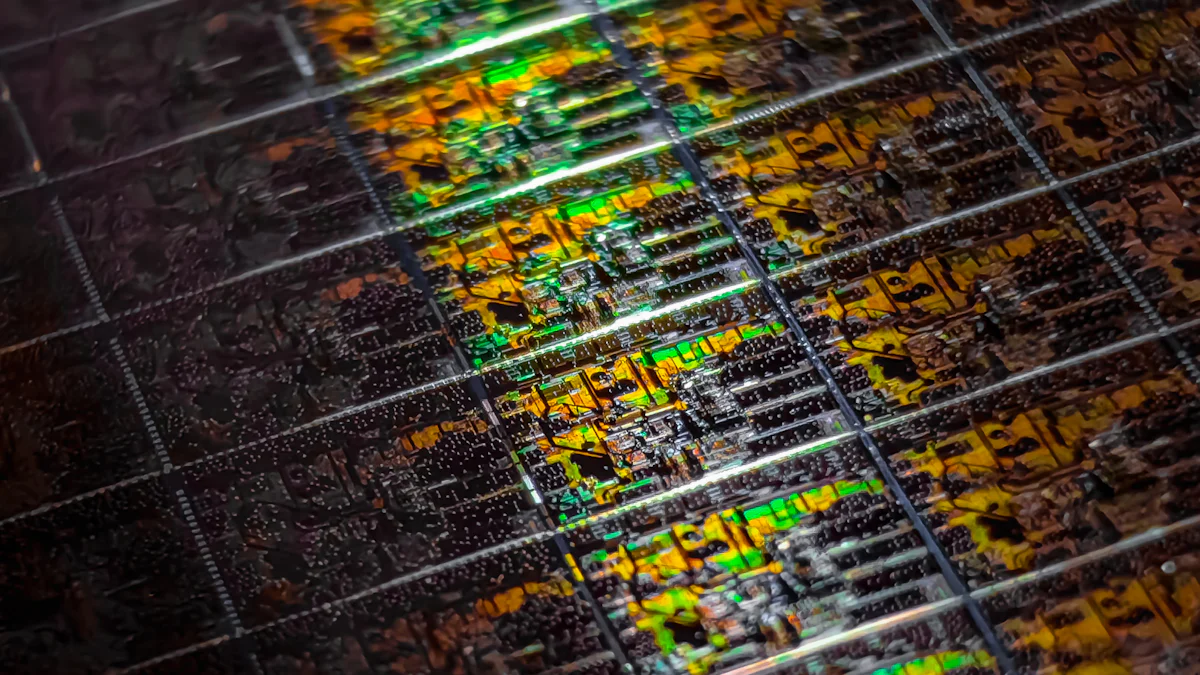
What is a Si Wafer Susceptor?
Manufacturers design these susceptors using materials such as graphite or silicon carbide to withstand extreme temperatures and maintain thermal stability.
The primary function of a susceptor is to transfer heat uniformly to the wafer. This uniform heating is essential for achieving consistent results in thin-film deposition or other semiconductor processes. Additionally, the susceptor’s surface condition plays a vital role in ensuring proper adhesion and uniformity of the deposited layers. By maintaining precise control over temperature and surface properties, the susceptor helps improve the quality and yield of semiconductor devices.
Why Are Si Wafer Susceptors Critical in Semiconductor Manufacturing?
Silicon wafer susceptors are indispensable in semiconductor manufacturing due to their impact on process efficiency and product quality. They enable precise temperature control, which is crucial for creating uniform layers on the wafer. Without a reliable susceptor, you risk uneven heating, which can lead to defects in the final product.
The material and design of the susceptor also influence its performance. High-purity materials like silicon carbide or graphite ensure chemical resistance and thermal stability, even under extreme conditions. This durability allows the susceptor to withstand repeated use without compromising its effectiveness. Furthermore, the susceptor’s compatibility with your specific manufacturing process ensures seamless integration with your equipment and production requirements.
In addition to thermal performance, the susceptor’s size and shape must align with your wafer specifications. A well-matched susceptor minimizes errors and maximizes efficiency. By selecting the right susceptor, you can enhance the overall yield and reliability of your semiconductor manufacturing process.
Key Factors to Consider When Choosing a Si Wafer Susceptor
Compatibility with Your Process
You must ensure that the silicon wafer susceptor aligns with your specific manufacturing process. Different semiconductor processes, such as chemical vapor deposition (CVD) or epitaxy, require varying temperature profiles and operational conditions. A susceptor designed for one process may not perform well in another. Evaluate your equipment and production requirements carefully. Check if the susceptor integrates seamlessly with your existing setup. This step minimizes disruptions and ensures smooth operation.
Additionally, consider the type of wafers you use. The susceptor must accommodate the size, thickness, and material of your wafers. A mismatch can lead to inefficiencies or defects in your final product. By prioritizing compatibility, you enhance both the efficiency and reliability of your manufacturing process.
Material Selection and Purity
The material of the susceptor plays a significant role in its performance. High-purity materials like silicon, graphite, or silicon carbide are ideal choices. These materials offer excellent thermal stability and chemical resistance, even under extreme conditions. Impurities in the material can compromise the quality of your wafers. Always opt for susceptors made from high-grade materials to maintain consistency in your processes.
Each material has unique properties that suit specific applications. For instance, silicon carbide provides superior durability and thermal conductivity, making it suitable for high-temperature operations. Graphite, on the other hand, offers excellent machinability and cost-effectiveness. Select a material that aligns with your process requirements and long-term goals.
Thermal Properties and Cooling Profile
Thermal performance is a critical factor when choosing a si wafer susceptor. The susceptor must distribute heat evenly across the wafer to ensure uniform processing. Uneven heating can result in defects, reducing the quality of your semiconductor devices. Assess the thermal conductivity and heat capacity of the susceptor material. These properties determine how effectively the susceptor manages temperature changes during operation.
The cooling profile of the susceptor also impacts its performance. Rapid cooling can cause thermal stress, leading to cracks or deformation. A well-designed susceptor maintains a stable cooling profile, preserving its structural integrity over time. Evaluate the thermal properties and cooling behavior of the susceptor to achieve optimal results in your manufacturing process.
Size, Shape, and Surface Condition
The size and shape of the susceptor must align with your wafer specifications and equipment setup. A mismatch can disrupt your manufacturing process and lead to inefficiencies. Measure your wafers and processing equipment carefully. Ensure the susceptor fits seamlessly into your production line. Standard sizes may work for many applications, but custom dimensions might be necessary for unique setups.
The surface condition of the susceptor plays a critical role in achieving high-quality results. A smooth and uniform surface ensures proper adhesion and deposition of thin films. Irregularities or defects on the surface can cause inconsistencies in the final product. Inspect the surface finish of the susceptor before making a purchase. Look for options that meet the specific requirements of your application. Polished or coated surfaces may offer additional benefits, such as enhanced durability or reduced contamination risks.
Cost-Effectiveness and Longevity
Balancing performance and cost is essential when selecting a susceptor. High-quality materials like silicon carbide or graphite may have a higher upfront cost, but they often provide better durability and thermal stability. This longevity reduces the need for frequent replacements, saving you money in the long run. Evaluate the total cost of ownership rather than focusing solely on the initial price.
Consider the manufacturing process and material quality when assessing cost-effectiveness. Susceptors made with precision and high-purity materials tend to perform better and last longer. Cheaper alternatives may seem appealing, but they can compromise the efficiency and yield of your production. Invest in a susceptor that aligns with your budget while meeting your performance requirements. A well-chosen susceptor enhances both the reliability and profitability of your semiconductor manufacturing process.
Types of Si Wafer Susceptors and Their Applications
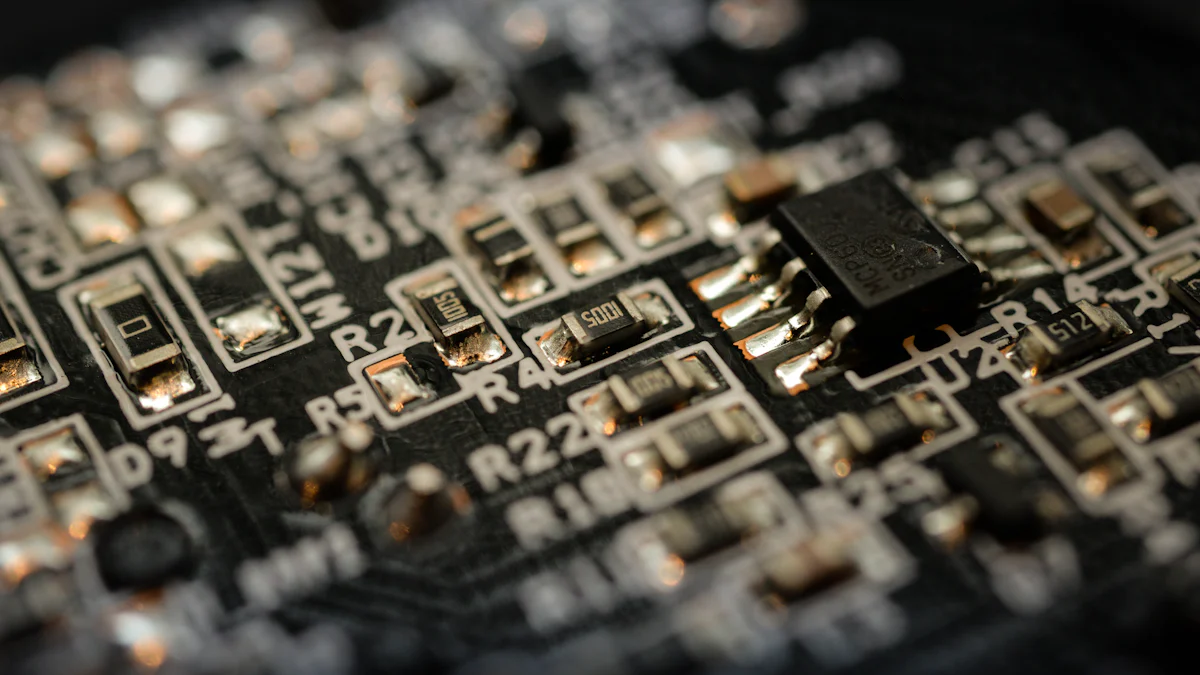
Single Wafer Susceptors
Single wafer susceptors are designed to hold and process one wafer at a time. These susceptors excel in applications requiring high precision and uniformity. You often find them in processes like chemical vapor deposition (CVD) or epitaxy, where maintaining consistent temperature and film thickness is critical. The single-wafer design allows for better control over heating and cooling profiles, ensuring optimal results for each wafer.
These susceptors are ideal for advanced semiconductor manufacturing, where quality takes precedence over quantity. Their ability to provide uniform heat distribution makes them a preferred choice for producing high-performance devices. If your process demands meticulous attention to detail and precision, single wafer susceptors offer an excellent solution.
Batch Wafer Susceptors
Batch wafer susceptors are built to handle multiple wafers simultaneously. This design increases throughput, making them suitable for high-volume production environments. You can use these susceptors in processes like diffusion or oxidation, where processing multiple wafers under similar conditions is necessary. Their ability to accommodate several wafers at once reduces processing time and enhances efficiency.
Batch susceptors often feature robust materials like graphite or silicon carbide to withstand the thermal stress of repeated cycles. They are a cost-effective option for manufacturers aiming to balance productivity with performance. If your goal is to maximize output without compromising quality, batch wafer susceptors provide a practical choice.
Specialized and Custom Susceptors
Specialized and custom susceptors cater to unique manufacturing needs. These susceptors are tailored to specific applications, offering solutions that standard designs cannot provide. You might require a custom susceptor if your process involves unconventional wafer sizes, shapes, or materials. Manufacturers can modify the susceptor’s design, material, or surface condition to meet your exact specifications.
Specialized susceptors are often used in research and development or niche semiconductor applications. They allow you to experiment with new processes or optimize existing ones. By investing in a custom susceptor, you can address challenges unique to your production line and achieve superior results.
"The choice of susceptor can impact the efficiency and yield of the semiconductor manufacturing process, making it crucial to select one that aligns with your production goals."
Understanding the types of si wafer susceptor and their applications helps you make informed decisions. Whether you prioritize precision, productivity, or customization, selecting the right susceptor ensures your manufacturing process runs smoothly and efficiently.
How to Match a Si Wafer Susceptor to Your Needs
Step 1: Define Your Manufacturing Requirements
Start by identifying the specific needs of your manufacturing process. Consider the type of semiconductor process you use, such as chemical vapor deposition (CVD) or epitaxy. Each process has unique requirements for temperature, pressure, and material compatibility. Determine the size and shape of the wafers you process. Ensure the susceptor can accommodate these dimensions without causing misalignment or inefficiencies.
Evaluate the thermal performance your process demands. Uniform heat distribution is critical for achieving consistent results. Identify the cooling profile that aligns with your operational needs to avoid thermal stress or deformation. By clearly defining these requirements, you create a solid foundation for selecting the right si wafer susceptor.
Step 2: Research and Compare Options
Explore the available options in the market. Look for susceptors made from high-purity materials like silicon carbide, graphite, or silicon. These materials offer excellent thermal stability and chemical resistance. Compare their properties to determine which one aligns best with your process. For instance, silicon carbide provides superior durability, while graphite offers cost-effectiveness.
Check the specifications of each susceptor. Focus on factors like size, shape, surface condition, and thermal conductivity. Ensure the susceptor integrates seamlessly with your existing equipment. Read reviews or case studies to understand how different susceptors perform in real-world applications. By researching thoroughly, you gain insights that help you make an informed decision.
Step 3: Test and Validate Performance
Before finalizing your purchase, test the susceptor in your manufacturing environment. Conduct trials to evaluate its performance under actual operating conditions. Monitor how well it distributes heat and maintains thermal stability. Check for any signs of uneven heating or defects in the processed wafers.
Inspect the susceptor’s durability during repeated cycles. Ensure it withstands the thermal stress of your process without compromising its structural integrity. Validate its compatibility with your equipment and production line. Testing allows you to identify potential issues early and ensures the susceptor meets your expectations. Once validated, you can proceed with confidence, knowing the susceptor will enhance your manufacturing efficiency and yield.
Step 4: Make a Well-Informed Purchase
Making a well-informed purchase ensures you get the best value and performance from your silicon wafer susceptor. After defining your requirements, researching options, and testing performance, you are ready to finalize your decision. Follow these steps to make a confident and educated purchase:
-
Evaluate Supplier Credibility
Choose a supplier with a proven track record in the semiconductor industry. Look for manufacturers or vendors known for producing high-quality susceptors. Check their certifications, customer reviews, and case studies. A reliable supplier provides consistent quality and dependable customer support.
-
Request Detailed Specifications
Ask for detailed technical specifications of the susceptor. Review the material composition, thermal properties, and surface finish. Ensure the specifications align with your manufacturing needs. This step helps you verify that the susceptor meets your process requirements before committing to a purchase.
-
Compare Pricing and Value
Compare prices from multiple suppliers. Focus on the total value rather than just the cost. A higher-priced susceptor made from durable, high-purity materials may save you money over time by reducing replacements and improving yield. Balance your budget with the long-term benefits of quality and performance.
-
Inquire About Customization Options
If your process has unique requirements, ask about customization. Many suppliers offer tailored solutions for specific applications. Custom susceptors can address challenges like unconventional wafer sizes or specialized thermal profiles. Investing in a custom option ensures optimal compatibility with your production line.
-
Review Warranty and Support Services
Check the warranty terms and after-sales support offered by the supplier. A good warranty protects your investment and provides peace of mind. Reliable support services ensure quick resolution of any issues, minimizing downtime in your manufacturing process.
-
Place a Trial Order
If possible, start with a small trial order. Use this opportunity to test the susceptor in your production environment. Confirm that it performs as expected and integrates seamlessly with your equipment. A trial order reduces risk and helps you validate your choice before scaling up.
"A well-informed purchase is not just about cost; it’s about ensuring the susceptor aligns with your goals for efficiency, quality, and yield."
By following these steps, you can confidently select a silicon wafer susceptor that meets your needs. A thoughtful purchase decision enhances your manufacturing process and contributes to the success of your semiconductor production.
Choosing the right si wafer susceptor requires careful evaluation of key factors. You need to assess compatibility with your process, material properties, thermal performance, and cost. Understanding the different types of susceptors and their specific applications helps you align your choice with your manufacturing needs. A structured approach simplifies the decision-making process. By following these steps, you can enhance efficiency, improve product quality, and achieve optimal results in your semiconductor production.
FAQ
What is the primary purpose of a silicon wafer susceptor?
A silicon wafer susceptor holds and supports wafers during high-temperature semiconductor processes. It ensures uniform heat distribution, which is essential for achieving consistent results in processes like chemical vapor deposition (CVD) or epitaxy.
How do I determine the right material for my susceptor?
High-purity materials like silicon carbide, graphite, or silicon offer excellent thermal stability and chemical resistance.
Why is thermal performance important when selecting a susceptor?
Thermal performance ensures even heat distribution across the wafer. Uneven heating can cause defects in the final product. Assess the susceptor’s thermal conductivity and cooling profile to maintain consistent quality and avoid thermal stress.
Can I use a standard susceptor for all semiconductor processes?
No, you cannot. Different processes, such as CVD or diffusion, require specific susceptors tailored to their temperature profiles and operational conditions. Always choose a susceptor compatible with your specific process to ensure optimal performance.
What factors should I consider regarding the size and shape of a susceptor?
The susceptor’s size and shape must match your wafer dimensions and equipment setup. A mismatch can disrupt your production line and reduce efficiency. Measure your wafers and processing equipment carefully before selecting a susceptor.
How does the surface condition of a susceptor affect manufacturing?
The surface condition impacts the adhesion and uniformity of deposited films. A smooth and defect-free surface ensures high-quality results. Inspect the susceptor’s surface finish to meet the specific requirements of your application.
Are custom susceptors worth the investment?
If your process has specific needs, investing in a custom silicon epitaxy susceptors can enhance efficiency and yield.
How can I ensure the susceptor integrates with my existing equipment?
Check the susceptor’s specifications, including size, shape, and material compatibility. Ensure it aligns with your equipment’s requirements. Testing the susceptor in your production environment helps confirm seamless integration.
What is the best way to balance cost and performance when choosing a susceptor?
Focus on the total cost of ownership rather than just the initial price. High-quality materials may have a higher upfront cost but offer better durability and performance. Evaluate long-term benefits like reduced replacements and improved yield to make an informed decision.
How do I validate the performance of a susceptor before purchasing?
Conduct trials in your manufacturing environment. Monitor heat distribution, thermal stability, and durability during repeated cycles. Testing ensures the susceptor meets your expectations and performs well under actual operating conditions.