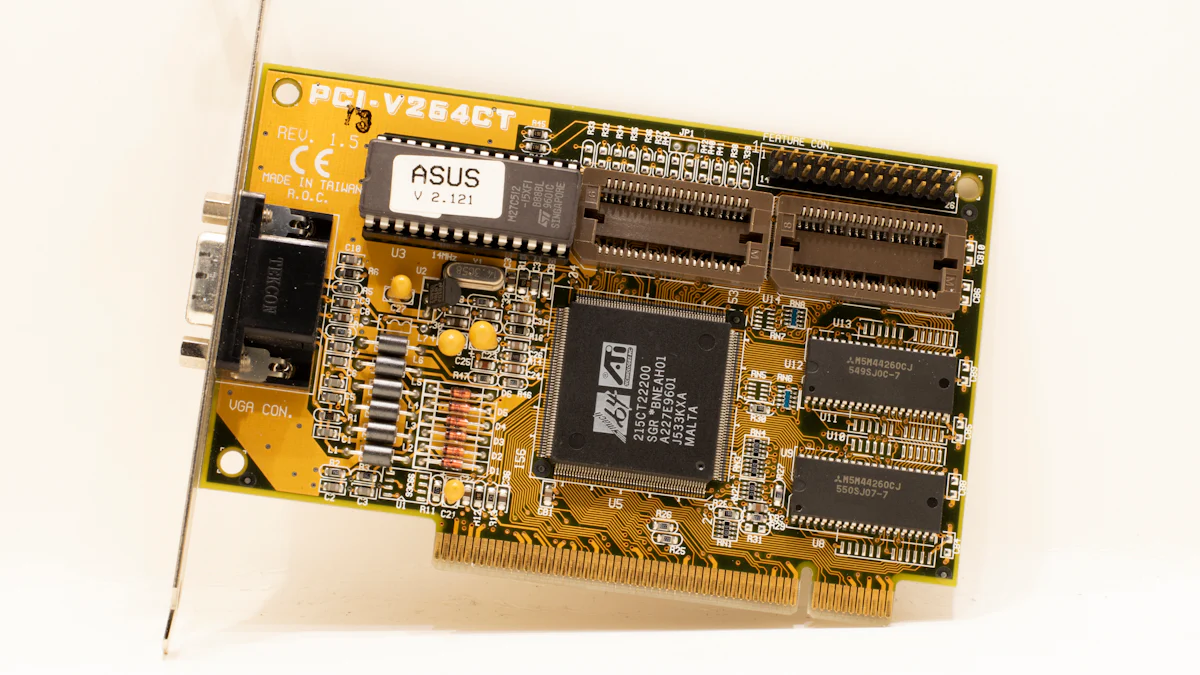
Silicon carbide (SiC) has revolutionized power electronics, offering unprecedented advancements in device performance. Its unique properties enable the development of more efficient and compact systems, crucial for modern applications. SiC’s high thermal conductivity and electrical efficiency surpass traditional materials, making it indispensable in various industries. The transformative impact of silicon carbide usage extends to enhancing energy conversion and management, particularly in electric vehicles and renewable energy systems. As a result, SiC continues to expand its applications, driving innovation and setting new standards in power electronics.
Key Takeaways
- Silicon carbide (SiC) significantly enhances power electronics by offering high thermal conductivity and electrical efficiency, leading to improved device performance.
- SiC devices operate at higher temperatures and voltages than traditional silicon, allowing for more compact and lightweight designs, especially beneficial in electric vehicles and renewable energy systems.
- The durability and reliability of silicon carbide make it a preferred choice for industries requiring long-lasting components, such as automotive and aerospace.
- Recent advancements in SiC processing techniques are improving production efficiency and reducing costs, paving the way for broader adoption in various applications.
- Silicon carbide is transforming renewable energy systems, particularly in solar inverters and wind turbines, by maximizing energy conversion and reducing operational costs.
- The integration of SiC technology with the Internet of Things (IoT) is set to enhance device performance and connectivity, making it crucial for future technological advancements.
- Ongoing research aims to further improve SiC material properties and expand its application areas, promising continued innovation in power electronics.
Overview of Silicon Carbide Properties and Advantages
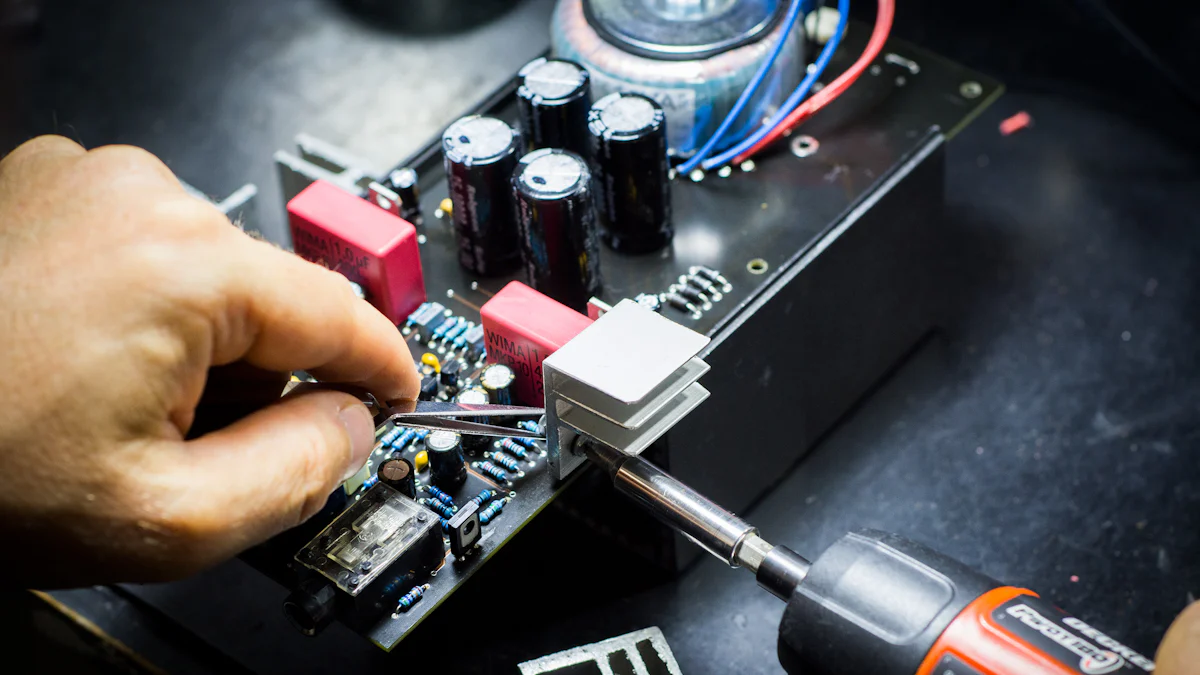
Unique Properties of SiC
Thermal Conductivity
Silicon carbide exhibits exceptional thermal conductivity, a critical property for power electronics. This material efficiently dissipates heat, ensuring devices operate at optimal temperatures. High thermal conductivity reduces the risk of overheating, which prolongs the lifespan of electronic components. Engineers value this property as it allows for the design of compact systems without compromising performance.
Electrical Efficiency
Electrical efficiency stands as another hallmark of silicon carbide. SiC’s wide bandgap enables devices to handle higher voltages and frequencies with minimal energy loss. This efficiency translates into lower power consumption and reduced operational costs. Industries benefit from SiC’s ability to enhance energy conversion processes, making it a preferred choice for modern power electronics applications.
Advantages Over Traditional Materials
Comparison with Silicon
When comparing silicon carbide to traditional silicon, several advantages emerge. SiC devices operate at higher temperatures and voltages, offering superior performance in demanding environments. Silicon carbide’s ability to switch at higher frequencies results in smaller and lighter components, which is crucial for applications like electric vehicles and renewable energy systems. These attributes make silicon carbide usage increasingly attractive in power electronics.
Durability and Reliability
Durability and reliability define silicon carbide’s appeal over conventional materials. SiC’s robust nature withstands harsh conditions, ensuring consistent performance over time. This reliability reduces maintenance needs and extends the service life of electronic systems. Industries that require long-lasting and dependable components, such as automotive and aerospace, increasingly turn to silicon carbide for its proven track record.
Analysis of Silicon Carbide Usage in Power Devices
SiC MOSFETs
Design and Characteristics
Silicon carbide usage in power devices has led to significant advancements, particularly in the design of SiC MOSFETs (Metal-Oxide-Semiconductor Field-Effect Transistors). These devices exhibit a unique structure that allows them to handle higher voltages and temperatures compared to traditional silicon-based MOSFETs. Engineers design SiC MOSFETs with a wide bandgap, which enhances their ability to operate efficiently under extreme conditions. This characteristic makes them ideal for applications requiring high power density and reliability.
Performance Metrics
The performance metrics of SiC MOSFETs highlight their superiority in power electronics. They offer reduced switching losses, which translates to higher efficiency and lower energy consumption. SiC MOSFETs also enable faster switching speeds, allowing for more compact and lightweight designs. These attributes contribute to improved overall system performance, making silicon carbide usage increasingly popular in industries such as automotive and renewable energy.
SiC IGBTs and ETOs
Design Innovations
Silicon carbide usage extends to the development of SiC IGBTs (Insulated Gate Bipolar Transistors) and ETOs (Emitter Turn-Off Thyristors). These devices incorporate innovative design features that enhance their performance in power electronics applications. SiC IGBTs, for instance, benefit from a robust structure that supports higher current densities and voltage ratings. This design innovation results in devices that can withstand harsh operating environments while maintaining efficiency.
Efficiency Improvements
Efficiency improvements in SiC IGBTs and ETOs are noteworthy. These devices exhibit lower conduction and switching losses compared to their silicon counterparts. The enhanced efficiency of SiC-based power devices leads to reduced thermal management requirements, which simplifies system design and lowers operational costs. As a result, industries increasingly adopt silicon carbide usage to achieve better energy conversion and management in power electronics systems.
Fabrication Processes and Technological Advancements
SiC Manufacturing Techniques
Substrate Production
Silicon carbide substrate production forms the foundation of SiC device fabrication. Manufacturers employ advanced techniques to create high-quality substrates that meet the stringent requirements of power electronics. They utilize methods such as physical vapor transport (PVT) and chemical vapor deposition (CVD) to produce SiC wafers. These processes ensure the substrates possess the necessary purity and structural integrity. The quality of the substrate directly impacts the performance and reliability of the final devices, making this step crucial in silicon carbide usage.
Device Fabrication
Device fabrication involves transforming SiC substrates into functional power electronic components. Engineers use processes like ion implantation and epitaxial growth to create the desired electrical properties. They meticulously design and etch the device structures to achieve optimal performance. The fabrication process also includes metallization, where conductive materials are deposited to form electrical contacts. This step ensures efficient current flow within the device. The precision and expertise involved in SiC device fabrication contribute significantly to the superior performance of silicon carbide-based power electronics.
Recent Technological Developments
Innovations in SiC Processing
Recent innovations in SiC processing have propelled the material’s adoption in power electronics. Researchers have developed new techniques to enhance the efficiency and scalability of SiC production. For instance, advancements in epitaxial growth have led to higher quality SiC layers with fewer defects. These improvements result in devices with better electrical characteristics and reliability. Additionally, innovations in doping methods have enabled more precise control over the material’s properties, further optimizing silicon carbide usage in various applications.
Challenges and Solutions
Despite its advantages, silicon carbide usage faces several challenges in manufacturing and application. One significant challenge is the high cost of SiC substrates compared to traditional silicon. However, ongoing research aims to reduce production costs through improved manufacturing techniques and economies of scale. Another challenge involves the complexity of processing SiC materials, which requires specialized equipment and expertise. To address this, industry collaborations and investments in research and development continue to drive technological advancements. These efforts aim to overcome existing barriers and unlock the full potential of silicon carbide in power electronics.
Real-World Applications and Case Studies
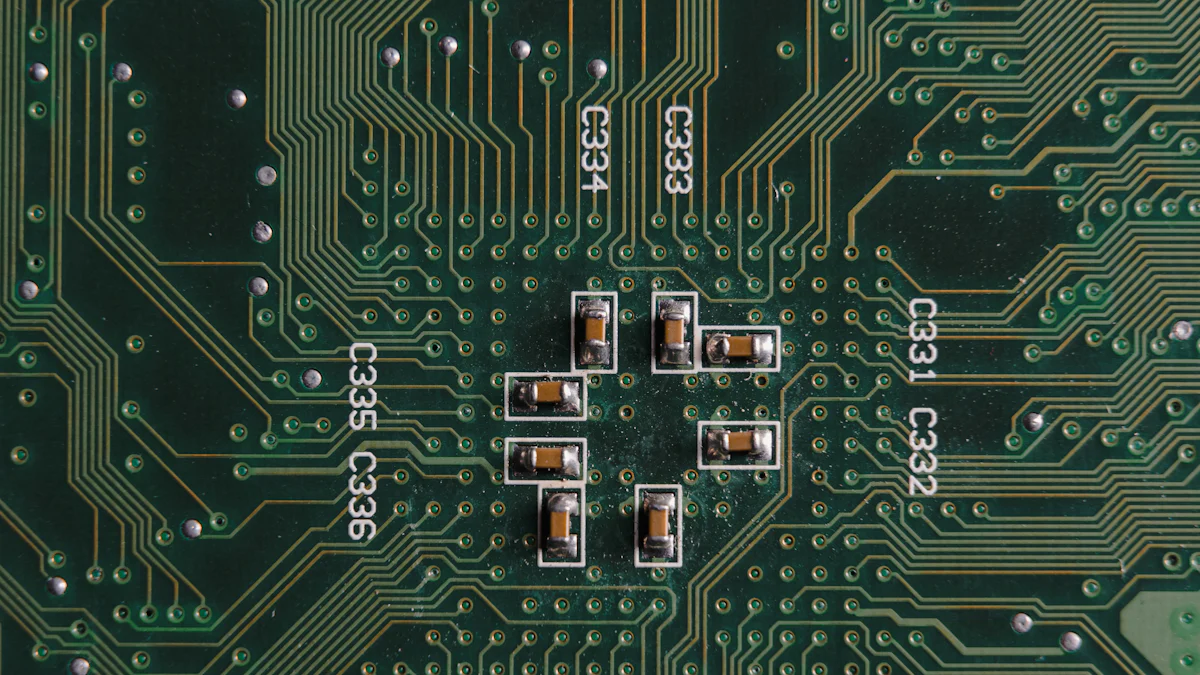
Automotive Industry
Electric Vehicles
Silicon carbide usage in the automotive industry has significantly impacted electric vehicles (EVs). Engineers utilize SiC components to enhance the efficiency of powertrains, which results in extended driving ranges. SiC’s ability to operate at higher temperatures and voltages allows for more compact and lightweight designs. This reduction in size and weight contributes to improved vehicle performance and energy efficiency. As a result, manufacturers increasingly adopt silicon carbide technology to meet the growing demand for efficient and sustainable transportation solutions.
Charging Infrastructure
The integration of silicon carbide in charging infrastructure has revolutionized the EV charging experience. SiC devices enable faster charging times by supporting higher power levels. This capability reduces the time required to recharge electric vehicles, making them more convenient for users. Additionally, SiC’s high thermal conductivity ensures reliable operation under continuous high-power conditions. Charging stations equipped with silicon carbide technology offer enhanced durability and efficiency, which supports the widespread adoption of electric vehicles.
Renewable Energy Systems
Solar Inverters
Silicon carbide usage in solar inverters has transformed the renewable energy landscape. SiC-based inverters exhibit superior efficiency, which maximizes energy conversion from solar panels. This efficiency reduces energy losses and increases the overall output of solar power systems. The compact design of SiC inverters also allows for easier installation and maintenance. As a result, solar energy systems benefit from reduced operational costs and improved performance, making them more attractive to both residential and commercial users.
Wind Turbines
In wind energy systems, silicon carbide components play a crucial role in enhancing performance. SiC devices improve the efficiency of power conversion processes within wind turbines. This improvement leads to higher energy yields and better utilization of wind resources. The robust nature of silicon carbide ensures reliable operation in harsh environmental conditions, such as extreme temperatures and high humidity. Consequently, wind energy systems equipped with SiC technology offer increased reliability and longevity, which supports the growth of renewable energy adoption worldwide.
Future Prospects and Ongoing Research
Emerging Trends in SiC Technology
Integration with IoT
Silicon carbide technology is poised to play a pivotal role in the integration with the Internet of Things (IoT). Engineers are leveraging SiC’s superior electrical properties to develop more efficient and reliable IoT devices. These devices require robust power management systems, which SiC can provide due to its high thermal conductivity and electrical efficiency. As IoT continues to expand across various sectors, SiC’s role in enhancing device connectivity and performance becomes increasingly significant.
Advancements in Miniaturization
The trend towards miniaturization in electronics has spurred advancements in silicon carbide technology. Researchers are focusing on reducing the size of SiC components while maintaining their performance capabilities. This miniaturization enables the development of compact and lightweight electronic systems, which are essential for modern applications such as wearable technology and portable devices. SiC’s ability to operate at higher temperatures and voltages without compromising efficiency makes it an ideal candidate for these emerging applications.
Research Directions
Enhancing Material Properties
Ongoing research aims to enhance the material properties of silicon carbide to further improve its performance in power electronics. Scientists are exploring new doping techniques and crystal growth methods to increase SiC’s electrical conductivity and thermal stability. These enhancements will enable the development of more efficient and durable electronic components. By improving SiC’s material properties, researchers hope to unlock new applications and expand its use in various industries.
Expanding Application Areas
The potential applications of silicon carbide continue to grow as researchers explore new areas for its use. SiC’s unique properties make it suitable for a wide range of industries, including aerospace, telecommunications, and healthcare. In aerospace, SiC can improve the efficiency and reliability of power systems in aircraft and spacecraft. In telecommunications, SiC’s high-frequency capabilities can enhance signal processing and data transmission. In healthcare, SiC’s biocompatibility and durability make it an attractive option for medical devices and implants. As research progresses, the application areas for silicon carbide are expected to expand, driving further innovation and adoption in power electronics.
Silicon carbide (SiC) offers transformative benefits in power electronics. Its high thermal conductivity and electrical efficiency enhance device performance, making it indispensable in industries like automotive and renewable energy. SiC’s ability to operate at higher temperatures and voltages allows for more compact and reliable systems. The material’s durability and efficiency drive innovation, setting new standards in power electronics. As research progresses, SiC’s potential to revolutionize the industry becomes increasingly evident, promising advancements in energy conversion and management across various applications.
FAQ
What is silicon carbide (SiC) and why is it important in power electronics?
Silicon carbide (SiC) is a semiconductor material known for its exceptional thermal conductivity and electrical efficiency. It plays a crucial role in power electronics by enabling devices to operate at higher temperatures and voltages. SiC’s unique properties allow for more efficient energy conversion and management, making it indispensable in industries such as automotive and renewable energy.
How does SiC compare to traditional silicon in power electronics?
SiC outperforms traditional silicon in several ways. It operates at higher temperatures and voltages, which enhances device performance in demanding environments. SiC also supports higher switching frequencies, resulting in smaller and lighter components. These advantages make SiC a preferred choice for modern power electronics applications.
What are the main applications of silicon carbide in the automotive industry?
In the automotive industry, silicon carbide is primarily used in electric vehicles (EVs) and charging infrastructure. SiC components improve the efficiency of EV powertrains, extending driving ranges and reducing size and weight. In charging stations, SiC enables faster charging times and ensures reliable operation under high-power conditions.
How does silicon carbide benefit renewable energy systems?
Silicon carbide enhances renewable energy systems by improving the efficiency of solar inverters and wind turbines. SiC-based inverters maximize energy conversion from solar panels, reducing energy losses and operational costs. In wind turbines, SiC components increase energy yields and ensure reliable operation in harsh conditions.
What are the challenges associated with silicon carbide usage?
The primary challenges of silicon carbide usage include high production costs and complex processing requirements. SiC substrates are more expensive than traditional silicon, and manufacturing SiC devices requires specialized equipment and expertise. Ongoing research aims to address these challenges by reducing costs and improving manufacturing techniques.
How is silicon carbide integrated with the Internet of Things (IoT)?
Silicon carbide technology enhances IoT devices by providing robust power management systems. SiC’s high thermal conductivity and electrical efficiency support the development of more efficient and reliable IoT devices. As IoT expands across various sectors, SiC’s role in improving device connectivity and performance becomes increasingly significant.
What advancements are being made in silicon carbide miniaturization?
Researchers focus on reducing the size of SiC components while maintaining their performance capabilities. This miniaturization enables the development of compact and lightweight electronic systems, essential for applications like wearable technology and portable devices. SiC’s ability to operate at higher temperatures and voltages makes it ideal for these emerging applications.
What future prospects exist for silicon carbide in power electronics?
Silicon carbide holds significant potential to revolutionize power electronics. Ongoing research aims to enhance SiC’s material properties and expand its application areas. As advancements continue, SiC is expected to drive innovation in energy conversion and management, setting new standards across various industries.
How does silicon carbide contribute to energy efficiency?
Silicon carbide contributes to energy efficiency by reducing power consumption and operational costs. Its wide bandgap allows devices to handle higher voltages and frequencies with minimal energy loss. This efficiency benefits industries by enhancing energy conversion processes, making SiC a preferred choice for modern power electronics applications.
What industries benefit most from silicon carbide technology?
Industries such as automotive, renewable energy, aerospace, telecommunications, and healthcare benefit significantly from silicon carbide technology. SiC’s unique properties improve the efficiency and reliability of power systems, making it suitable for a wide range of applications. As research progresses, SiC’s role in these industries is expected to grow, driving further innovation and adoption.