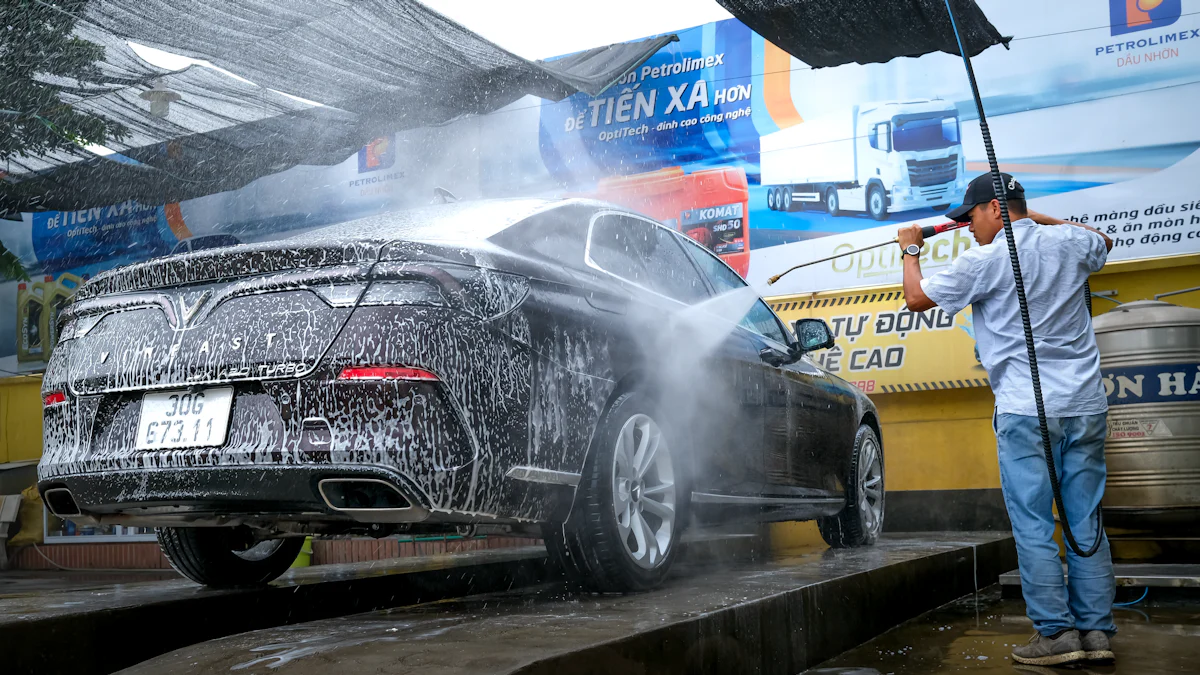
CVD SiC Coating stands out as a high-performance solution for industries requiring durability and precision. This coating forms through a process called chemical vapor deposition, where gaseous chemicals react to create a solid silicon carbide layer. The result is a coating with exceptional thermal resistance, chemical stability, and wear protection. Its unique properties make it indispensable in demanding applications like aerospace and semiconductor manufacturing. By understanding how this coating is made, you can appreciate the expertise and technology behind its creation.
Key Takeaways
- CVD SiC Coating is created through a precise chemical vapor deposition process, resulting in a durable and high-performance silicon carbide layer.
- Proper substrate selection and thorough cleaning are crucial for ensuring effective adhesion and quality of the coating.
- Calibrating equipment and conducting trial runs are essential steps to prevent defects and ensure consistent results during the deposition process.
- Controlling reaction conditions like temperature and gas flow rates is vital for achieving the desired coating thickness and properties.
- Post-deposition treatments, including controlled cooling and quality inspections, enhance the durability and functionality of the coating.
- CVD SiC Coating is widely used in industries such as aerospace and semiconductors due to its exceptional thermal resistance and chemical stability.
- Customizing the coating through optional finishing processes allows it to meet specific application requirements, making it a versatile solution.
Preparation Phase for CVD SiC Coating
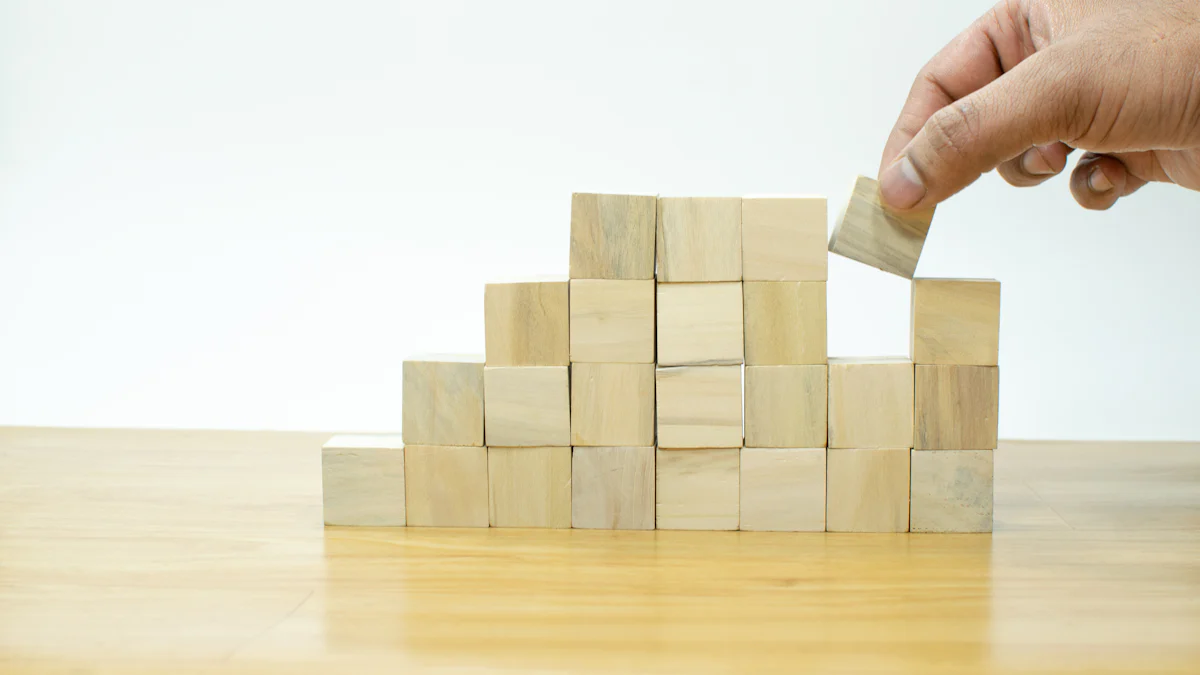
The preparation phase lays the foundation for a successful CVD SiC Coating process. Each step in this phase ensures that the substrate and equipment are ready for precise deposition. Proper preparation minimizes errors and enhances the quality of the final coating.
Substrate Selection and Cleaning
Choosing the right substrate is critical. You must select a material that can withstand high temperatures and chemical reactions during the coating process. Common substrates include metals, ceramics, and graphite. Each material offers unique properties that suit specific applications.
Once you select the substrate, cleaning becomes essential. Contaminants like dust, grease, or residues can interfere with the coating process. Cleaning methods often involve ultrasonic baths, chemical solvents, or plasma cleaning. These techniques remove impurities and create a pristine surface for the coating to adhere to effectively.
Surface Preparation Techniques
Surface preparation goes beyond cleaning. It involves modifying the substrate to enhance adhesion and ensure uniform coating. Techniques like mechanical polishing or sandblasting smooth out irregularities and improve surface texture. In some cases, chemical etching is used to create micro-level roughness, which promotes better bonding between the substrate and the silicon carbide layer.
You must also consider the substrate’s geometry. Complex shapes may require additional preparation steps to ensure even coating coverage. Proper surface preparation directly impacts the durability and performance of the CVD SiC Coating.
Equipment Setup and Calibration
The equipment setup is a crucial step in the preparation phase. You need to ensure that all components of the chemical vapor deposition system are functioning correctly. This includes the reaction chamber, gas delivery system, and heating elements. Regular maintenance and inspection prevent equipment malfunctions during the process.
Calibration ensures precision. You must calibrate temperature controls, gas flow rates, and pressure settings to meet the specific requirements of the coating process. Accurate calibration guarantees consistent results and prevents defects in the final coating.
Before starting the deposition process, conduct a trial run. This helps identify potential issues and allows you to make adjustments. A well-prepared system ensures a smooth transition to the next phase of the CVD SiC Coating process.
Deposition Process in CVD SiC Coating
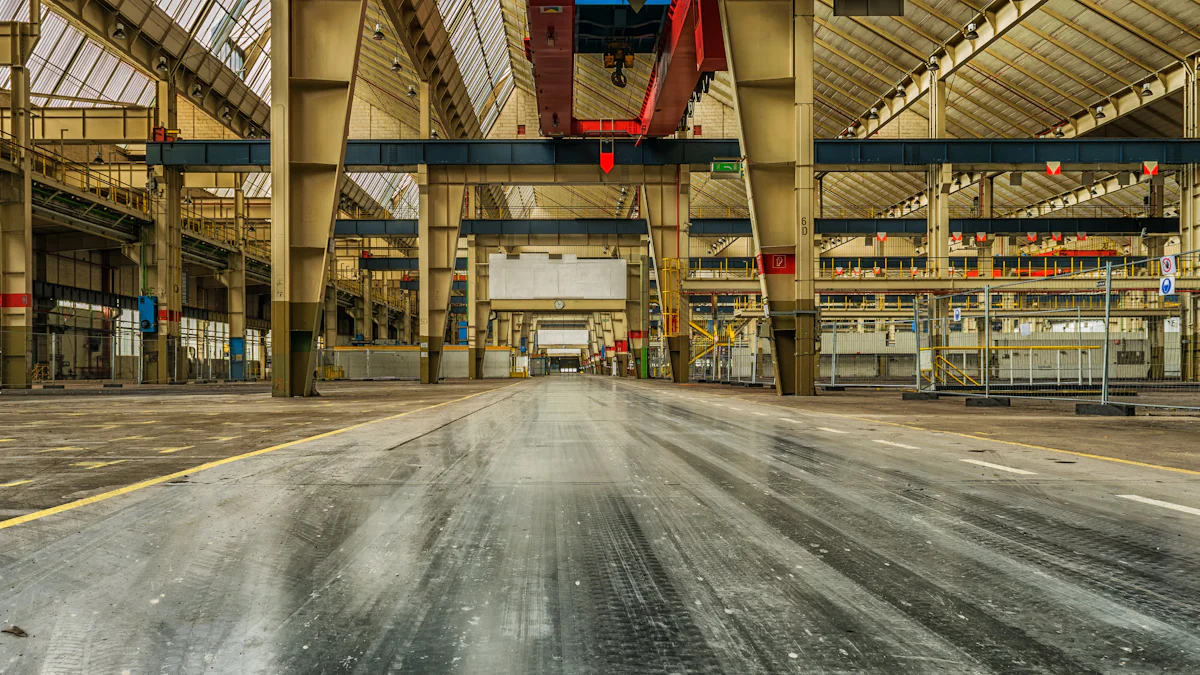
The deposition process is the heart of creating a high-quality CVD SiC Coating. This phase involves precise control over chemical reactions to ensure the formation of a uniform and durable silicon carbide layer. Understanding the steps and conditions of this process helps you appreciate the advanced technology behind it.
Overview of the Chemical Vapor Deposition Method
Chemical vapor deposition (CVD) is a sophisticated method that transforms gaseous precursors into a solid coating. During this process, you heat the substrate inside a reaction chamber to a specific temperature. Gaseous chemicals, introduced into the chamber, react at the surface of the substrate. These reactions result in the deposition of a thin, solid layer of silicon carbide.
This method allows you to control the thickness and composition of the coating with remarkable precision. The ability to create uniform layers makes CVD ideal for applications requiring high-performance coatings. By mastering this method, you can achieve consistent results for even the most demanding industrial needs.
Materials and Gases Used in the Process
The materials and gases you use play a critical role in the success of the CVD process. Methyltrichlorosilane (MTS) is a common precursor for producing silicon carbide coatings. When combined with hydrogen gas, MTS decomposes at high temperatures to form silicon carbide. This reaction also releases byproducts like hydrochloric acid, which must be safely managed.
You must ensure the purity of the gases to avoid contamination. Impurities can compromise the quality of the coating and lead to defects. The choice of materials and gases depends on the specific requirements of the application. For example, some processes may require additional gases to modify the properties of the coating.
Reaction Conditions and Parameters
The reaction conditions determine the efficiency and quality of the CVD SiC Coating. Temperature, pressure, and gas flow rates are the key parameters you must control. The substrate temperature typically ranges between 1000°C and 1500°C, depending on the desired coating properties. Maintaining a stable temperature ensures consistent chemical reactions.
Pressure inside the reaction chamber also affects the deposition process. Low-pressure CVD systems are often used to achieve better uniformity and adhesion. Gas flow rates must be carefully calibrated to provide the right balance of reactants. Too much or too little gas can disrupt the reaction and result in uneven coatings.
Monitoring these parameters throughout the process is essential. Advanced sensors and control systems help you maintain optimal conditions. By fine-tuning these variables, you can produce coatings with exceptional performance characteristics.
Mechanism of Silicon Carbide Formation
The formation of silicon carbide during the CVD process relies on precise chemical reactions. You begin by introducing gaseous precursors, such as methyltrichlorosilane (MTS) and hydrogen, into the reaction chamber. These gases interact at high temperatures, typically between 1000°C and 1500°C, to initiate the deposition process. The heat breaks down the MTS molecules, releasing silicon and carbon atoms. These atoms combine on the substrate’s surface to form a solid layer of silicon carbide.
The reaction occurs in a controlled environment to ensure uniformity. The substrate’s heated surface acts as a catalyst, promoting the chemical bonding of silicon and carbon. This bonding creates a crystalline structure that gives the coating its strength and durability. The process also produces byproducts, such as hydrochloric acid, which you must safely remove to maintain the purity of the coating.
The growth of the silicon carbide layer depends on the balance of reactants. You must carefully regulate the gas flow rates and reaction time to achieve the desired thickness and composition. A steady supply of precursors ensures continuous deposition, while precise temperature control prevents defects like cracks or uneven layers. By mastering these conditions, you can produce a high-quality CVD SiC Coating with exceptional performance characteristics.
Post-Deposition Treatment of CVD SiC Coating
The post-deposition treatment phase ensures the durability and functionality of the CVD SiC Coating. This stage refines the coating, eliminates potential defects, and prepares it for its intended application. By following these steps, you can enhance the coating’s performance and reliability.
Controlled Cooling to Prevent Thermal Stress
Cooling the coated substrate requires careful attention. Rapid temperature changes can cause thermal stress, leading to cracks or warping in the silicon carbide layer. To avoid this, you must implement a controlled cooling process. Gradually reducing the temperature allows the coating and substrate to adjust without damage.
You can use specialized cooling systems to regulate the rate of temperature decrease. These systems maintain uniform cooling across the entire surface, ensuring consistent results. Monitoring the cooling process is essential. Any deviation can compromise the structural integrity of the coating. Controlled cooling not only prevents defects but also enhances the coating’s long-term stability.
Inspection and Quality Control Methods
Inspection plays a vital role in verifying the quality of the CVD SiC Coating. You need to examine the coating for uniformity, thickness, and adhesion. Advanced tools like scanning electron microscopes (SEM) and optical profilometers help you detect surface irregularities and defects.
Non-destructive testing methods, such as ultrasonic testing or X-ray diffraction, allow you to assess the coating’s internal structure without causing damage. These techniques ensure that the coating meets the required specifications. Regular quality control checks during this phase help you identify and address issues early.
You should also perform adhesion tests to evaluate how well the coating bonds to the substrate. Poor adhesion can lead to peeling or flaking, reducing the coating’s effectiveness. By conducting thorough inspections, you can guarantee a high-quality product that meets industry standards.
Optional Finishing for Specific Applications
Some applications require additional finishing steps to tailor the coating’s properties. Polishing the surface can improve smoothness and reduce friction, which is essential for components in high-precision machinery. Etching or texturing may be necessary to enhance the coating’s performance in specific environments.
You might also apply secondary coatings or treatments to modify the silicon carbide layer’s characteristics. For example, adding a protective layer can increase resistance to extreme conditions. These optional finishing processes depend on the coating’s intended use and the demands of the application.
By customizing the coating through finishing, you can meet the unique requirements of various industries. This flexibility makes CVD SiC Coating a versatile solution for challenging environments.
Applications and Benefits of CVD SiC Coating
Industrial Applications in Aerospace, Semiconductors, and More
You can find CVD SiC Coating in a wide range of industries due to its exceptional properties. In aerospace, it protects critical components from extreme temperatures and harsh environments. Jet engine parts and spacecraft systems benefit from its ability to withstand thermal stress and resist wear. This coating ensures reliability in high-performance applications where failure is not an option.
In the semiconductor industry, CVD SiC Coating plays a vital role in manufacturing processes. It provides a protective layer for equipment exposed to corrosive chemicals and high temperatures. Its chemical stability ensures precision and consistency, which are essential for producing advanced electronic devices. You can also see its use in wafer carriers and other tools that demand durability and cleanliness.
Beyond aerospace and semiconductors, this coating serves industries like automotive, energy, and medical technology. It enhances the lifespan of components in harsh conditions, such as those found in power plants or chemical processing facilities. Its versatility makes it a valuable solution for any application requiring superior performance and reliability.
Key Benefits: Durability, Thermal Resistance, and Chemical Stability
CVD SiC Coating offers unmatched durability. You can rely on it to protect surfaces from wear and tear, even in the most demanding environments. Its hardness ensures long-lasting performance, reducing the need for frequent replacements or repairs. This durability translates into cost savings and improved efficiency for your operations.
Thermal resistance is another key advantage. The coating maintains its integrity at extremely high temperatures, making it ideal for applications involving intense heat. You can trust it to perform consistently, whether in aerospace engines or industrial furnaces. Its ability to handle thermal stress prevents cracking or deformation, ensuring reliable operation.
Chemical stability sets this coating apart. It resists corrosion from acids, alkalis, and other aggressive substances. This property makes it indispensable in industries where exposure to harsh chemicals is unavoidable. You can count on it to protect equipment and maintain performance, even in challenging chemical environments.
By choosing CVD SiC Coating, you gain access to a solution that combines these benefits. Its unique properties enhance the performance, safety, and longevity of components across various industries. Whether you need protection from heat, wear, or chemicals, this coating delivers results you can depend on.
The journey of creating CVD SiC Coating involves three critical phases: preparation, deposition, and post-deposition treatment. Each phase demands precision and attention to detail to ensure a high-quality coating. This process plays a vital role in industries like aerospace and semiconductors, where durability and performance are essential. By mastering this technology, you contribute to advancements in high-performance applications. The expertise required for this process highlights the importance of skilled professionals and advanced equipment in delivering reliable results.
FAQ
What is CVD SiC Coating?
CVD SiC Coating refers to a silicon carbide layer created through chemical vapor deposition.
Why is CVD SiC Coating preferred over other coatings?
You should choose CVD SiC Coating for its superior properties. It offers exceptional thermal resistance, wear protection, and chemical stability. These qualities make it ideal for industries like aerospace and semiconductors, where performance and reliability are critical.
What materials can serve as substrates for CVD SiC Coating?
You can use various materials as substrates, including metals, ceramics, and graphite. The choice depends on the application and the substrate’s ability to withstand high temperatures and chemical reactions during the coating process.
How thick is the typical CVD SiC Coating?
The thickness of CVD SiC Coating varies based on the application. You can control the thickness during the deposition process, typically ranging from a few micrometers to several hundred micrometers. This flexibility allows customization for specific needs.
Is the CVD SiC Coating process environmentally friendly?
The process requires careful management of byproducts like hydrochloric acid. With proper handling and advanced equipment, you can minimize environmental impact. Many manufacturers implement safety measures to ensure compliance with environmental standards.
Can CVD SiC Coating be applied to complex shapes?
Yes, you can coat complex shapes using the CVD process. Proper surface preparation and precise control of reaction conditions ensure uniform coverage, even on intricate geometries. This capability makes it suitable for components with challenging designs.
How do you ensure the quality of CVD SiC Coating?
Quality assurance involves thorough inspection and testing. You can use tools like scanning electron microscopes and non-destructive testing methods to check for uniformity, adhesion, and structural integrity. Regular quality control ensures the coating meets industry standards.
What industries benefit most from CVD SiC Coating?
Industries like aerospace, semiconductors, automotive, and energy benefit significantly from CVD SiC Coating. Its durability, thermal resistance, and chemical stability make it indispensable for applications in harsh environments.
How long does the CVD SiC Coating process take?
The duration depends on factors like substrate size, desired coating thickness, and reaction conditions. While the process can take several hours, the precise control ensures a high-quality coating that justifies the time investment.
Can CVD SiC Coating be customized for specific applications?
Yes, you can customize the coating through optional finishing steps. Polishing, etching, or adding secondary layers can tailor the coating’s properties to meet unique requirements. This adaptability makes it a versatile solution for various industries.