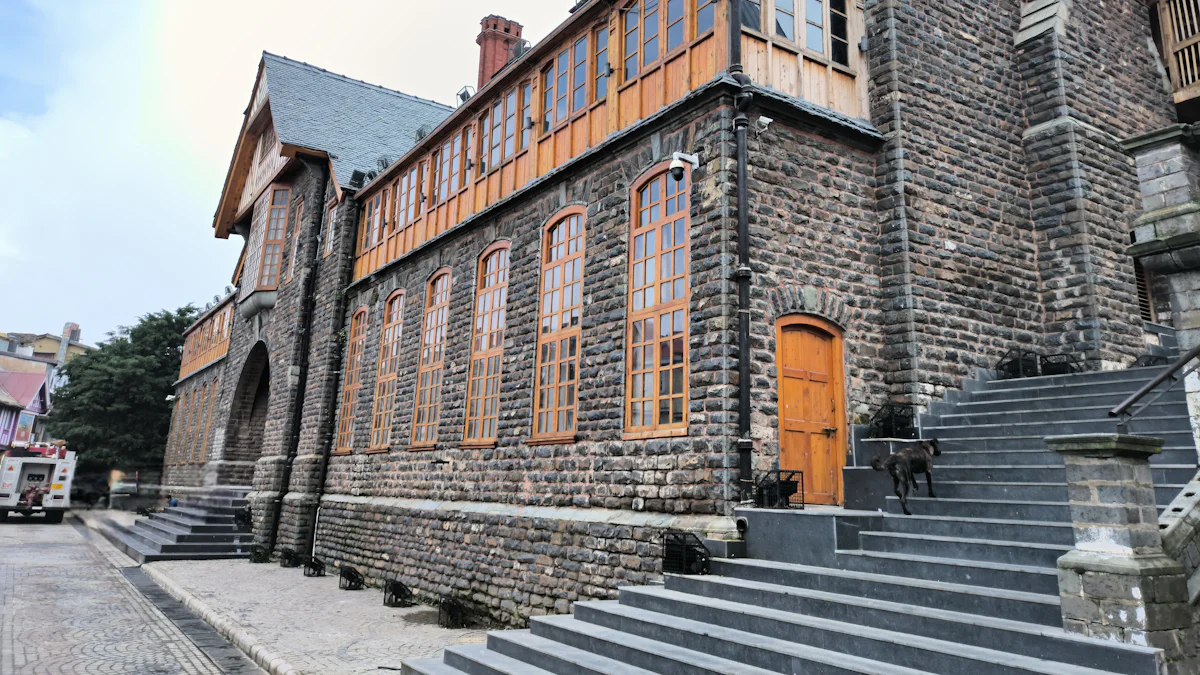
CVD SiC Coating represents a breakthrough in material science. These coatings consist of silicon carbide layers created through chemical vapor deposition. Their microstructures, which refer to the arrangement of grains and phases within the coating, play a critical role in performance. You can see how these structures influence properties like strength, durability, and resistance to extreme conditions. Understanding these microstructures allows you to select or design coatings that meet specific demands in advanced industries.
Key Takeaways
- CVD SiC Coating microstructures are crucial for determining the performance of coatings in various applications, influencing properties like strength and thermal resistance.
- There are three primary types of microstructures: columnar, equiaxed, and mixed, each offering unique benefits tailored to specific industrial needs.
- Understanding the deposition parameters, such as temperature and gas flow rate, allows you to control the microstructure and optimize coating performance.
- CVD SiC coatings excel in thermal resistance, mechanical strength, and chemical protection, making them ideal for demanding environments like aerospace and semiconductor manufacturing.
- Post-deposition treatments, such as annealing and polishing, can enhance the microstructure and overall performance of CVD SiC coatings.
- Recent advancements in CVD technology, including hybrid microstructures and real-time monitoring, are expanding the capabilities and applications of these coatings.
- By mastering the characteristics of CVD SiC microstructures, you can make informed decisions that improve efficiency and reliability in your projects.
Overview of CVD SiC Coating Microstructures
What Are CVD SiC Coating Microstructures?
CVD SiC Coating microstructures refer to the internal arrangement of grains, phases, and boundaries within the silicon carbide layer. These microstructures form during the chemical vapor deposition process and directly influence the coating’s properties. You can think of them as the "blueprint" that determines how the coating behaves under different conditions. The size, shape, and orientation of these structures impact critical factors like strength, thermal resistance, and durability. By understanding these microstructures, you gain insight into why CVD SiC Coating performs so well in demanding environments.
Key Types of Microstructures
CVD SiC Coating exhibits three primary types of microstructures. Each type offers unique characteristics that make it suitable for specific applications. Let’s explore these in detail.
Columnar Microstructures
Columnar microstructures consist of elongated grains that grow perpendicular to the substrate surface. These grains resemble vertical columns, giving the coating a distinct texture. This structure enhances thermal conductivity and mechanical strength. You often find columnar microstructures in applications requiring high thermal stability, such as aerospace components or semiconductor manufacturing tools. Their ability to withstand extreme temperatures makes them invaluable in these fields.
Equiaxed Microstructures
Equiaxed microstructures feature grains with roughly equal dimensions in all directions. This uniformity provides excellent isotropic properties, meaning the coating behaves consistently regardless of the direction of applied stress. You might encounter equiaxed microstructures in coatings designed for optical applications or energy systems. Their balanced properties ensure durability and reliability in environments where uniform performance is essential.
Mixed Microstructures
Mixed microstructures combine features of both columnar and equiaxed types. This hybrid structure offers a balance between the strengths of the other two. You get enhanced mechanical strength from the columnar grains and improved isotropic properties from the equiaxed grains. Mixed microstructures are versatile and adaptable, making them suitable for a wide range of industries. They provide a tailored solution when neither columnar nor equiaxed structures alone can meet the performance requirements.
Understanding these microstructures helps you select the right CVD SiC Coating for your specific needs. Each type serves a purpose, and knowing their differences ensures optimal performance in your application.
Properties of CVD SiC Microstructures
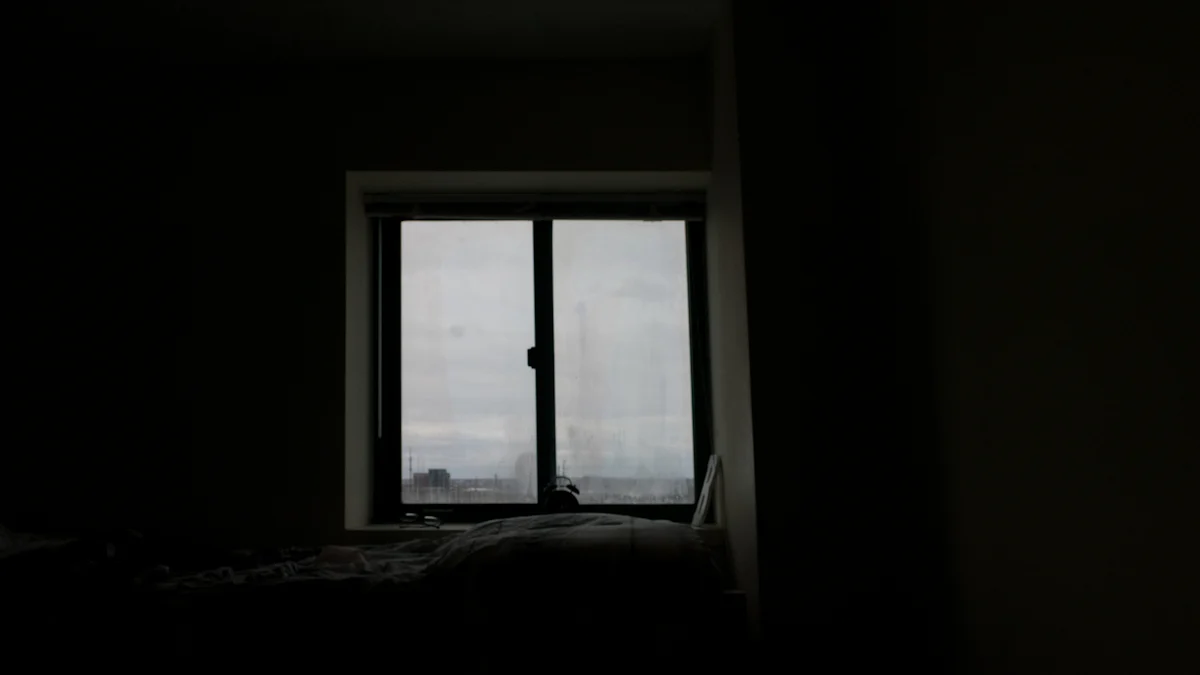
Thermal Resistance and Stability
CVD SiC Coating microstructures excel in thermal resistance. These coatings maintain their integrity even under extreme temperatures. The arrangement of grains within the microstructure plays a key role in this performance. Columnar microstructures, for instance, enhance heat dissipation, making them ideal for high-temperature environments. You can rely on these coatings to protect components in aerospace engines or semiconductor manufacturing tools. Their stability ensures consistent performance, even when exposed to rapid temperature changes.
Thermal stability also extends to long-term applications. The microstructures resist thermal degradation, which prevents cracking or warping over time. This durability makes them a dependable choice for industries requiring prolonged exposure to heat. By understanding the thermal properties of these microstructures, you can select coatings that meet your specific operational needs.
Mechanical Strength and Durability
The mechanical strength of CVD SiC Coating microstructures sets them apart. These coatings withstand significant mechanical stress without deforming or failing. The grain structure within the coating determines its ability to handle pressure. Columnar microstructures provide exceptional strength along specific directions, while equiaxed microstructures offer uniform strength in all directions. This versatility allows you to choose coatings tailored to your application.
Durability is another critical factor. These microstructures resist wear and tear, even in harsh conditions. Whether you need protection against abrasion or impact, these coatings deliver reliable performance. Mixed microstructures combine the strengths of both columnar and equiaxed types, offering a balanced solution for demanding environments. You can trust these coatings to extend the lifespan of your equipment and reduce maintenance costs.
Chemical Resistance and Corrosion Protection
CVD SiC Coating microstructures offer outstanding chemical resistance. These coatings act as a barrier against corrosive substances, protecting the underlying material. The dense and uniform grain arrangement prevents chemicals from penetrating the surface. This property is particularly valuable in industries like energy and power generation, where exposure to harsh chemicals is common.
Corrosion protection is another advantage. The microstructures resist oxidation and other chemical reactions that can degrade materials over time. This resistance ensures that your components remain functional and efficient, even in chemically aggressive environments. By choosing coatings with the right microstructure, you can safeguard your equipment and improve its performance in challenging conditions.
Understanding the properties of CVD SiC Coating microstructures helps you make informed decisions. Each property contributes to the coating’s overall performance, ensuring it meets the demands of your application.
Applications and Relevance of CVD SiC Coating
Aerospace Industry
You encounter some of the most demanding environments in aerospace applications. CVD SiC Coating plays a vital role in protecting components exposed to extreme temperatures, high pressures, and corrosive conditions. Its thermal resistance ensures that engine parts and heat shields maintain their integrity during operation. The coating’s mechanical strength prevents wear and tear, even under intense stress.
In addition, the lightweight nature of the coating contributes to fuel efficiency. By reducing the overall weight of components, you can enhance the performance of aircraft and spacecraft. The chemical resistance of the coating also protects critical parts from oxidation, ensuring long-term reliability. Whether you work with turbine blades or structural components, this coating delivers unmatched performance in aerospace environments.
Semiconductor Manufacturing
Precision is everything in semiconductor manufacturing. CVD SiC Coating provides the durability and stability you need for tools and equipment used in this industry. Its ability to withstand high temperatures ensures consistent performance during processes like chemical vapor deposition and etching. The coating’s smooth surface minimizes contamination, which is crucial for maintaining the purity of semiconductor wafers.
The microstructures of the coating also enhance its chemical resistance. This property protects equipment from corrosive gases and chemicals used in manufacturing. By using this coating, you can extend the lifespan of your tools and reduce maintenance costs. Its uniformity and reliability make it an essential material for achieving high-quality results in semiconductor production.
Energy and Power Generation
Energy systems often operate in harsh conditions. CVD SiC Coating offers the protection you need for components exposed to high temperatures, corrosive environments, and mechanical stress. In power plants, the coating enhances the efficiency and durability of turbines, heat exchangers, and other critical equipment. Its thermal stability ensures consistent performance, even during prolonged exposure to extreme heat.
The coating’s chemical resistance also plays a key role in energy applications. It prevents corrosion caused by exposure to fuels, gases, and other substances. This resistance reduces the risk of equipment failure, ensuring uninterrupted energy production. Whether you work in renewable energy or traditional power generation, this coating provides the reliability and performance you require.
CVD SiC Coating proves its relevance across industries by delivering unmatched protection and performance. Its unique properties make it an indispensable material for advanced applications.
Optical Applications
CVD SiC coatings play a crucial role in optical applications. Their unique microstructures provide exceptional properties that enhance the performance of optical systems. You can rely on these coatings for applications requiring high precision and clarity.
The smooth surface of CVD SiC coatings ensures minimal light scattering. This property makes them ideal for mirrors, lenses, and other optical components. The columnar microstructures, in particular, contribute to superior polishability. You achieve a reflective surface with minimal imperfections, which is essential for high-performance optical devices.
The thermal stability of these coatings also benefits optical systems. Optical components often operate in environments with fluctuating temperatures. CVD SiC coatings maintain their structural integrity under such conditions. This stability ensures consistent optical performance, even in demanding environments like space exploration or high-energy laser systems.
Chemical resistance further enhances their value in optical applications. These coatings protect optical components from corrosive substances, ensuring long-term durability. You can use them in environments where exposure to harsh chemicals or moisture is unavoidable. This protection reduces maintenance needs and extends the lifespan of your optical systems.
CVD SiC coatings offer unmatched advantages for optical applications. Their smoothness, thermal stability, and chemical resistance make them indispensable for achieving precision and reliability in advanced optical technologies.
Factors Influencing Microstructure Formation in CVD SiC Coating
Deposition Parameters
The deposition parameters in the chemical vapor deposition (CVD) process play a crucial role in shaping the microstructure of SiC coatings. You control these parameters to achieve the desired grain size, orientation, and density. Key factors include temperature, pressure, gas flow rate, and precursor composition.
-
Temperature: Higher temperatures promote grain growth, leading to larger grains and columnar microstructures. Lower temperatures, on the other hand, favor finer grains and equiaxed structures. You can adjust the temperature to tailor the coating for specific applications.
-
Pressure: The pressure inside the deposition chamber affects how the precursor gases react and deposit on the substrate. Low pressure often results in denser coatings with smoother surfaces. High pressure may lead to faster deposition but can compromise uniformity.
-
Gas Flow Rate: The flow rate of precursor gases determines the availability of reactive species during deposition. A controlled flow ensures uniform coating thickness and consistent microstructure. Uneven flow can create defects or variations in grain size.
-
Precursor Composition: The choice of precursors, such as silicon tetra-chloride and toluene, influences the chemical reactions during deposition. You can select specific precursors to produce coatings with unique properties, like enhanced thermal stability or chemical resistance.
By carefully managing these parameters, you can optimize the microstructure to meet the performance requirements of your application.
Substrate Material and Preparation
The substrate material and its preparation significantly impact the formation of CVD SiC microstructures. The substrate serves as the foundation for the coating, and its properties influence how the coating adheres and grows.
-
Material Compatibility: The substrate material must be compatible with the SiC coating to ensure strong bonding. Materials like graphite, silicon, and certain metals work well with CVD SiC. Incompatible substrates may lead to poor adhesion or defects in the coating.
-
Surface Roughness: The surface texture of the substrate affects the nucleation and growth of grains. A smooth surface promotes uniform grain formation, while a rough surface can lead to irregularities. You should prepare the substrate to achieve the desired surface finish.
-
Cleaning and Pre-Treatment: Contaminants on the substrate surface can interfere with the deposition process. Cleaning and pre-treating the substrate remove impurities and improve coating quality. Techniques like chemical cleaning or plasma treatment enhance adhesion and ensure a defect-free coating.
Proper substrate selection and preparation set the stage for creating high-quality CVD SiC coatings with precise microstructures.
Post-Deposition Treatments
Post-deposition treatments refine the microstructure and enhance the properties of CVD SiC coatings. These treatments allow you to address any imperfections and improve the coating’s performance.
-
Annealing: Heating the coating after deposition can relieve internal stresses and improve grain structure. Annealing also enhances optical properties, making the coating more transparent for applications like lenses and mirrors.
-
Polishing: Polishing smooths the surface of the coating, reducing roughness and improving reflectivity. This step is essential for optical and semiconductor applications where surface quality is critical.
-
Chemical Treatments: Exposing the coating to specific chemicals can modify its surface properties. For example, chemical etching can remove unwanted residues or create a textured surface for better adhesion in layered systems.
-
Thermal Cycling: Repeated heating and cooling cycles test the coating’s thermal stability and durability. This process ensures that the microstructure remains intact under fluctuating temperatures.
Post-deposition treatments give you the flexibility to fine-tune the coating for your specific needs. These steps enhance the overall performance and reliability of the CVD SiC coating in demanding environments.
By understanding and controlling these factors, you can achieve the ideal microstructure for your application. Each step, from deposition to post-treatment, contributes to the coating’s success.
Challenges and Innovations in CVD SiC Coating Microstructures
Common Challenges in Achieving Desired Microstructures
Creating the ideal microstructure in CVD SiC coatings presents several challenges. These obstacles often arise during the deposition process or due to external factors that influence the coating’s formation. Understanding these challenges helps you anticipate potential issues and refine your approach.
-
Controlling Grain Size and Orientation
Achieving consistent grain size and orientation can be difficult. Variations in deposition parameters, such as temperature or gas flow rate, often lead to uneven grain growth. This inconsistency affects the coating’s mechanical and thermal properties, reducing its overall performance.
-
Minimizing Defects
Defects like voids, cracks, or impurities frequently occur during deposition. These imperfections weaken the coating and compromise its durability. You must carefully monitor the deposition environment to reduce contamination and ensure uniformity.
-
Adhesion Issues
Poor adhesion between the coating and the substrate remains a common problem. Incompatible materials or inadequate surface preparation often result in weak bonding. This issue can lead to delamination, where the coating separates from the substrate under stress.
-
Balancing Performance Trade-offs
Optimizing one property, such as thermal resistance, may negatively impact another, like mechanical strength. For example, increasing grain size for better heat dissipation might reduce the coating’s toughness. You need to strike a balance to meet specific application requirements.
-
Scaling for Industrial Applications
Scaling the CVD process for large components or mass production introduces additional challenges. Maintaining uniform microstructures across larger surfaces requires precise control of deposition parameters. Any deviation can result in inconsistent coatings.
Addressing these challenges demands a deep understanding of the deposition process and the factors influencing microstructure formation. By identifying potential issues early, you can take corrective measures to achieve the desired results.
Recent Advancements in CVD SiC Coating Technology
Innovations in CVD SiC coating technology continue to push the boundaries of what these coatings can achieve. Researchers and engineers have developed new techniques and materials to overcome traditional limitations. These advancements enhance the performance and versatility of CVD SiC coatings.
-
Advanced Deposition Techniques
Modern CVD systems now offer greater control over deposition parameters. Techniques like plasma-enhanced CVD (PECVD) allow you to fine-tune the process for specific microstructures. PECVD uses plasma to activate chemical reactions, enabling lower deposition temperatures and improved uniformity.
-
Improved Precursor Materials
The development of high-purity precursors, such as silicon tetra-chloride and toluene, has improved coating quality. These materials produce fewer impurities during deposition, resulting in denser and more consistent microstructures. You can now achieve coatings with enhanced thermal and chemical resistance.
-
Real-Time Monitoring and Feedback Systems
Advanced monitoring tools provide real-time data on deposition conditions. Sensors track variables like temperature, pressure, and gas flow rate, allowing you to make immediate adjustments. This technology ensures precise control over the microstructure and reduces the risk of defects.
-
Hybrid Microstructures
Researchers have explored hybrid microstructures that combine the best features of columnar and equiaxed grains. These coatings offer a unique balance of strength, thermal stability, and isotropic properties. You can use hybrid microstructures to meet complex performance requirements in demanding applications.
-
Post-Deposition Enhancements
Innovations in post-deposition treatments have expanded the capabilities of CVD SiC coatings. Techniques like laser annealing improve grain structure and surface quality. Chemical modifications enhance the coating’s resistance to specific environmental factors, such as oxidation or moisture.
-
Sustainable and Cost-Effective Solutions
Efforts to reduce the environmental impact of CVD processes have led to more sustainable practices. Researchers are developing eco-friendly precursors and optimizing energy consumption during deposition. These advancements make CVD SiC coatings more accessible and cost-effective for a wider range of industries.
These innovations demonstrate the potential of CVD SiC coatings to address evolving industrial needs. By leveraging these advancements, you can achieve superior performance and unlock new applications for this versatile material.
Understanding CVD SiC coating microstructures equips you with the knowledge to optimize performance in demanding applications. These microstructures directly influence properties like strength, thermal stability, and chemical resistance, making them essential for advanced industries. By mastering their characteristics, you can select coatings that meet specific needs and improve efficiency.
Innovations in CVD SiC technology continue to expand possibilities. From hybrid microstructures to sustainable practices, these advancements pave the way for future breakthroughs. Staying informed about these developments ensures you remain at the forefront of material science and engineering.