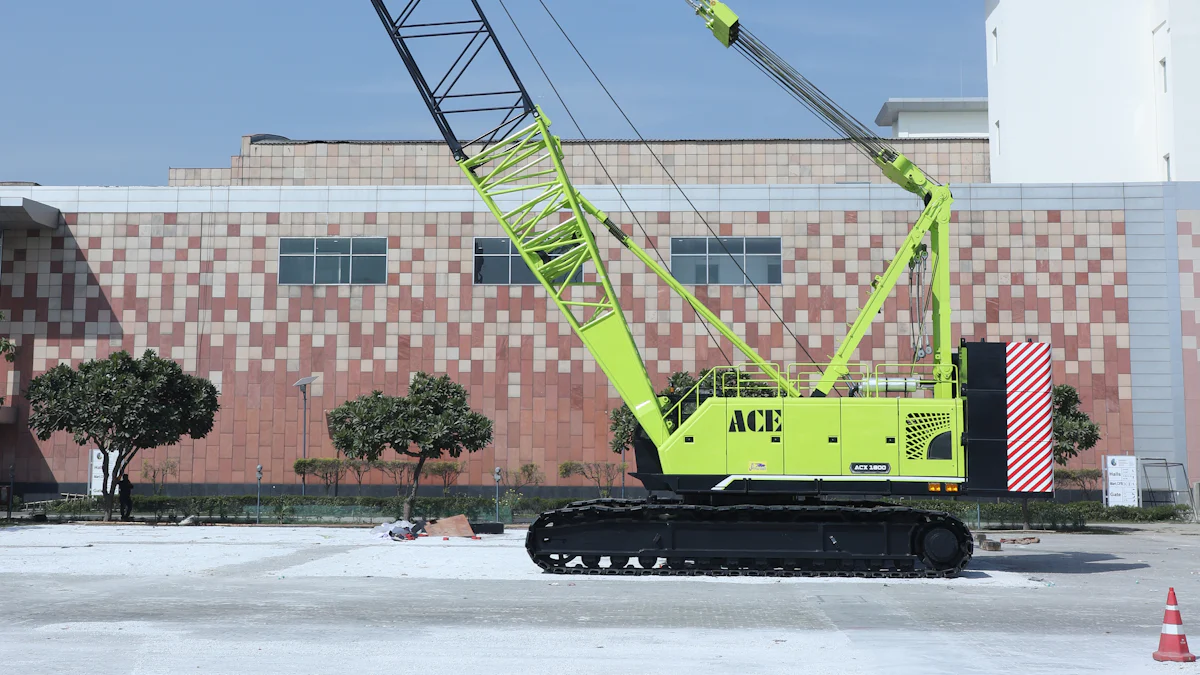
CVD SiC coating susceptors redefine high-temperature industrial processes by merging graphite’s thermal conductivity with silicon carbide’s chemical resistance and durability. This combination creates a robust solution for demanding environments. Industries like semiconductors and advanced manufacturing rely on these susceptors to achieve superior efficiency and reliability. Their ability to withstand extreme conditions while maintaining performance makes them indispensable in modern applications. By enhancing heat distribution and resisting corrosion, they ensure consistent results and long-term operational stability.
Key Takeaways
- CVD SiC coating susceptors combine graphite’s thermal conductivity with silicon carbide’s chemical resistance, making them ideal for high-temperature industrial applications.
- These susceptors enhance operational efficiency by ensuring uniform heat distribution, which is crucial for processes like semiconductor manufacturing.
- Their durability and resistance to wear and corrosion significantly extend their lifespan, reducing maintenance costs and downtime.
- CVD SiC coating susceptors are cost-effective, as their long-lasting performance minimizes the need for frequent replacements and lowers energy consumption.
- They play a vital role in emerging technologies, including renewable energy and aerospace, by providing reliable thermal management and chemical stability.
- The environmental benefits of these susceptors include reduced waste and energy efficiency, aligning with modern sustainability goals in industrial operations.
What is a CVD SiC Coating Susceptor?
Definition and Composition
A CVD SiC coating susceptor is a specialized component designed for high-temperature industrial applications.
The SiC coating not only protects the graphite core but also improves its performance in demanding environments. The coating diffuses into the graphite surface, forming a durable and well-adhering layer. This structure ensures stability during operations involving high temperatures and corrosive substances. The result is a robust susceptor that maintains its integrity and functionality over extended periods.
Role in High-Temperature Industrial Applications
In semiconductor manufacturing, these susceptors ensure uniform heat distribution within processing chambers, which is essential for producing high-quality CVD SiC coating wafers.
In advanced manufacturing, these susceptors support operations in high-temperature furnaces. Their thermal conductivity enables rapid and even heating, reducing processing times and improving efficiency. Additionally, their durability minimizes the need for frequent replacements, lowering operational costs.
Emerging technologies also benefit from the unique properties of CVD SiC coating susceptors. Their adaptability to various applications makes them indispensable in cutting-edge industries. By combining performance, durability, and cost-effectiveness, these susceptors have become a cornerstone of modern high-temperature industrial processes.
Key Properties of CVD SiC Coating
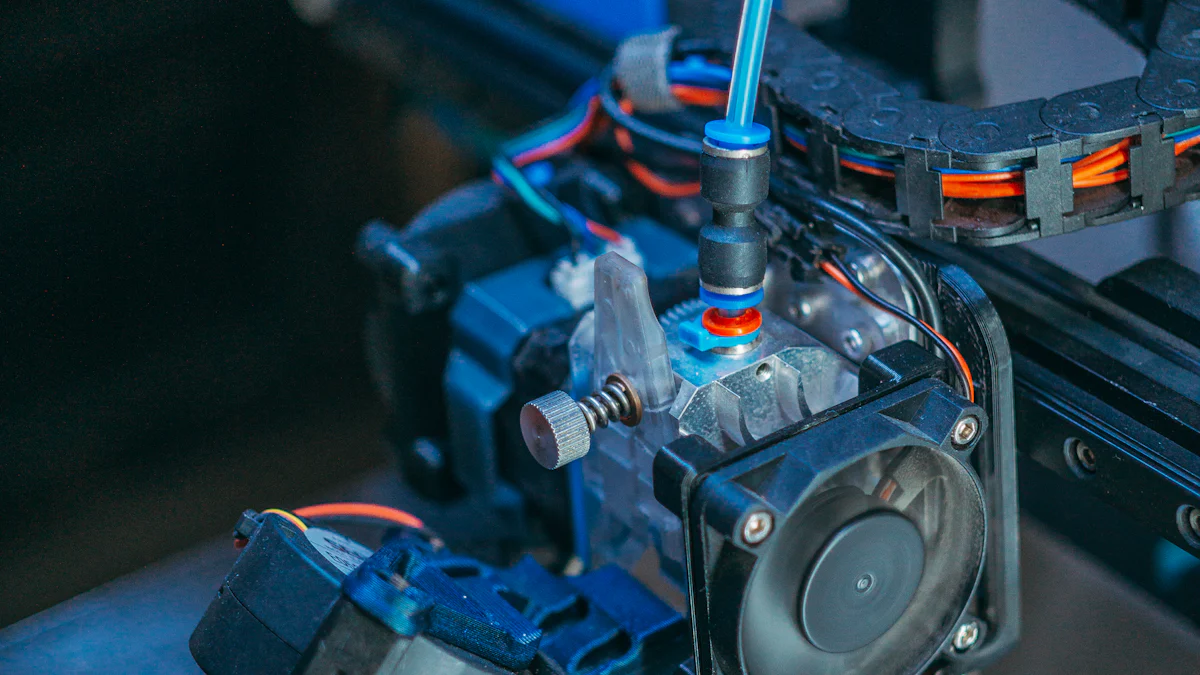
Physical Properties
CVD SiC coatings exhibit exceptional physical characteristics that make them ideal for high-temperature industrial applications.
The lightweight nature of the graphite core, combined with the robust SiC coating, creates a component that is both durable and easy to handle. This balance of strength and weight ensures that the susceptor maintains its structural integrity without adding unnecessary bulk to industrial systems. These physical properties collectively enable the CVD SiC coating susceptor to perform reliably under challenging conditions.
Chemical Properties
The chemical properties of CVD SiC coatings provide unparalleled protection in corrosive environments.
The inert nature of the SiC coating minimizes contamination risks, which is essential in industries requiring high levels of purity. The coating acts as a barrier, shielding the graphite core from reactive elements and maintaining the integrity of the susceptor. These chemical properties make the CVD SiC coating susceptor a reliable choice for processes that demand both durability and cleanliness.
Thermal Properties
CVD SiC coatings excel in thermal performance, making them indispensable in high-temperature applications. The coating enhances the thermal conductivity of the graphite substrate, enabling rapid and uniform heat distribution. This property ensures consistent processing temperatures, which is vital for achieving precise results in semiconductor and advanced manufacturing industries.
The thermal stability of silicon carbide allows the susceptor to endure extreme temperatures without losing its structural or functional integrity. This stability reduces the risk of thermal deformation, ensuring reliable performance over extended periods. Additionally, the coating’s ability to withstand thermal cycling minimizes wear and tear, further extending the lifespan of the susceptor.
The combination of these thermal properties ensures that the CVD SiC coating susceptor delivers efficient and consistent performance, even in the most demanding industrial environments.
Benefits of SiC-Coated Graphite Susceptors
Enhanced Performance and Efficiency
SiC-coated graphite susceptors significantly improve industrial performance by optimizing heat distribution and thermal management. The silicon carbide coating enhances the thermal conductivity of the graphite substrate, ensuring rapid and uniform heating. This capability reduces temperature inconsistencies, which is critical for achieving precise results in processes like semiconductor manufacturing. The uniform heat distribution also minimizes energy waste, contributing to higher operational efficiency.
The chemical resistance of the coating further boosts performance. It protects the susceptor from degradation caused by reactive gases and harsh environments. This protection ensures consistent functionality, even under demanding conditions. By maintaining stability and reliability, the CVD SiC coating susceptor becomes an essential component in high-temperature industrial applications.
Extended Lifespan and Durability
The durability of SiC-coated graphite susceptors sets them apart from traditional materials. The silicon carbide layer forms a robust barrier that shields the graphite core from wear, corrosion, and thermal stress. This protection extends the lifespan of the susceptor, reducing the frequency of replacements and downtime in industrial operations.
The mechanical stability of the coating ensures that the susceptor withstands repeated thermal cycling without cracking or deforming. This resilience is vital for industries that operate under extreme temperatures and fluctuating conditions. By maintaining structural integrity over time, these susceptors provide long-term value and reliability.
Cost-Effectiveness in Industrial Operations
SiC-coated graphite susceptors offer a cost-effective solution for industries requiring high-performance components. Their extended lifespan reduces the need for frequent replacements, lowering maintenance costs. The enhanced thermal efficiency of the coating minimizes energy consumption, leading to significant savings in operational expenses.
The ability of the susceptor to maintain performance under harsh conditions reduces the risk of production delays and equipment failures. This reliability translates into higher productivity and fewer disruptions. By combining durability, efficiency, and reliability, the CVD SiC coating susceptor delivers exceptional value for industrial applications.
Applications of CVD SiC Coating Susceptors
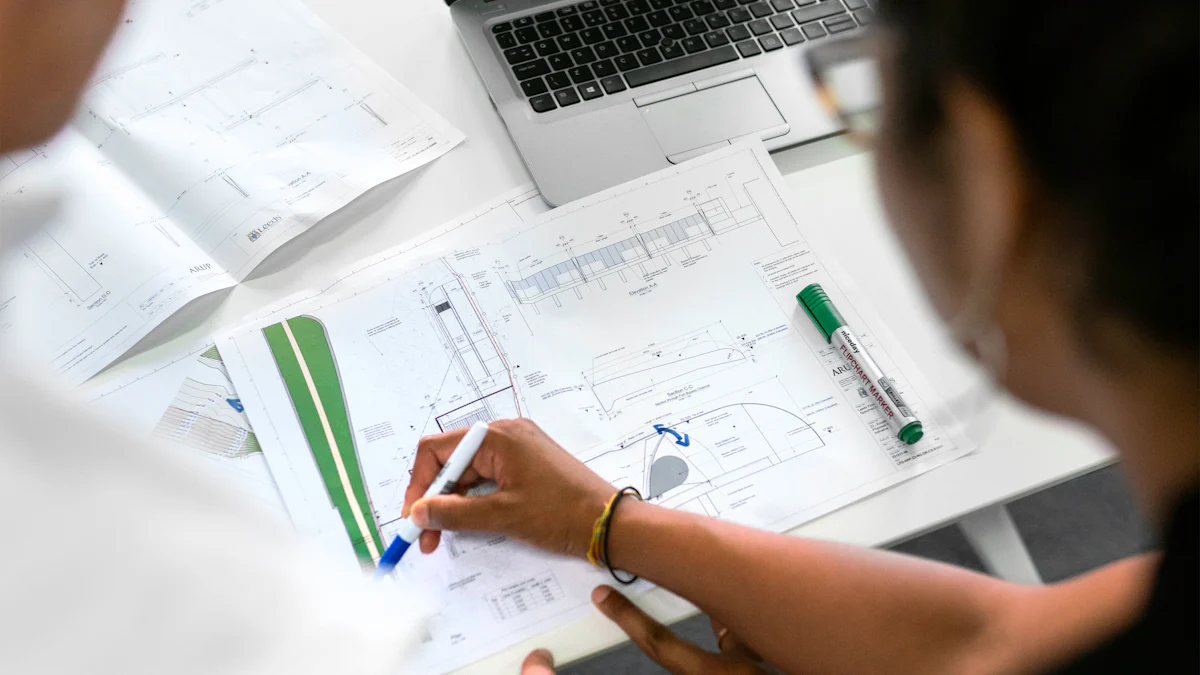
Semiconductor Manufacturing
CVD SiC coating susceptors play a pivotal role in semiconductor manufacturing. These components ensure precise thermal management during wafer production.
The chemical resistance of the silicon carbide coating protects the susceptor from reactive gases used in processes like Metal-Organic Chemical Vapor Deposition (MOCVD). This protection ensures the susceptor maintains its integrity and functionality over extended periods. Manufacturers rely on these susceptors to meet the stringent demands of semiconductor fabrication, where purity and precision are non-negotiable.
Advanced Manufacturing and High-Temperature Furnaces
In advanced manufacturing, CVD SiC coating susceptors support operations in high-temperature furnaces. Their exceptional thermal conductivity enables rapid heating, reducing processing times and improving overall efficiency. The ability to maintain consistent temperatures ensures reliable results in applications such as material synthesis and heat treatment.
The durability of the silicon carbide coating extends the lifespan of the susceptor, even under extreme thermal conditions. This durability reduces the frequency of replacements, lowering operational costs for manufacturers. Industries that depend on high-temperature processes benefit significantly from the performance and reliability of these susceptors.
Emerging Applications in Cutting-Edge Technologies
CVD SiC coating susceptors are finding new applications in emerging technologies.
In aerospace, their ability to withstand extreme temperatures and corrosive environments supports the development of advanced materials and components. As industries continue to innovate, the demand for reliable and high-performing susceptors grows. The unique properties of CVD SiC coating susceptors position them as indispensable tools in driving technological advancements.
Why CVD SiC Coating is a Game-Changer
Revolutionizing Industrial Performance and Reliability
CVD SiC coating susceptors have redefined the standards of industrial performance. Their ability to combine graphite’s thermal conductivity with silicon carbide’s chemical resistance ensures unmatched operational efficiency. These susceptors deliver uniform heat distribution, which enhances the precision of high-temperature processes. Industries relying on semiconductor manufacturing and advanced materials benefit significantly from this consistency.
The mechanical stability of the silicon carbide layer ensures that these susceptors endure extreme conditions without compromising functionality. This durability reduces the frequency of replacements, which minimizes downtime and boosts productivity. By maintaining structural integrity under thermal stress, they provide reliable performance over extended periods. Their role in improving operational reliability makes them indispensable in critical industrial applications.
The chemical resistance of the silicon carbide coating further enhances their reliability. It protects the graphite core from corrosive environments, ensuring long-term stability. This resistance also prevents contamination, which is crucial for industries requiring high levels of purity. By addressing these challenges, CVD SiC coating susceptors have revolutionized the way industries approach high-temperature operations.
Driving Innovation and Sustainability in Critical Industries
CVD SiC coating susceptors play a pivotal role in fostering innovation across various industries. Their adaptability allows them to meet the demands of emerging technologies, such as renewable energy and aerospace. For instance, in photovoltaic cell production, these susceptors enable precise thermal processing, which improves solar panel efficiency. Their contribution to advanced manufacturing processes supports the development of cutting-edge materials and components.
Sustainability has become a priority for modern industries, and these susceptors align with that goal. Their extended lifespan reduces waste generated by frequent replacements. The enhanced thermal efficiency minimizes energy consumption, which lowers the environmental impact of industrial operations. By promoting resource efficiency, they contribute to sustainable practices in high-temperature applications.
The versatility of these susceptors ensures their relevance in future technological advancements. Their ability to withstand extreme conditions and deliver consistent performance positions them as essential tools for innovation. As industries evolve, the demand for reliable and efficient solutions like CVD SiC coating susceptors will continue to grow.
CVD SiC coating susceptors represent a significant advancement in high-temperature industrial processes. Their unmatched durability, thermal efficiency, and chemical resistance make them indispensable for industries like semiconductors and advanced manufacturing. These susceptors enhance operational reliability by delivering consistent performance under extreme conditions. Their ability to optimize heat distribution and resist chemical degradation ensures long-term value. By driving innovation and improving efficiency, they have become essential tools for modern industrial applications. The transformative impact of the CVD SiC coating susceptor highlights its critical role in shaping the future of high-performance technologies.
FAQ
What is the primary purpose of a CVD SiC coating susceptor?
The primary purpose of a CVD SiC coating susceptor is to enhance the performance and durability of graphite substrates in high-temperature industrial applications. The silicon carbide (SiC) coating provides superior thermal conductivity, chemical resistance, and mechanical stability, making it essential for processes like semiconductor manufacturing and advanced material production.
How does the CVD process improve the quality of the SiC coating?
The chemical vapor deposition (CVD) process ensures a uniform and tightly bonded SiC layer on the graphite substrate.
Why is silicon carbide used as a coating material?
Silicon carbide is used due to its exceptional properties, including high thermal conductivity, excellent chemical resistance, and remarkable mechanical strength. These characteristics make it ideal for protecting graphite susceptors from wear, corrosion, and thermal stress in demanding industrial environments.
What industries benefit the most from CVD SiC coating susceptors?
Industries such as semiconductor manufacturing, advanced manufacturing, aerospace, and renewable energy benefit significantly from CVD SiC coating susceptors.
How do CVD SiC coating susceptors improve energy efficiency?
CVD SiC coating susceptors improve energy efficiency by enhancing heat distribution and thermal conductivity. The uniform heating reduces energy waste and shortens processing times, which lowers overall energy consumption in industrial operations.
Are CVD SiC coating susceptors cost-effective?
Yes, CVD SiC coating susceptors are cost-effective. Their extended lifespan reduces the need for frequent replacements, while their thermal efficiency minimizes energy costs. These factors contribute to significant savings in operational expenses over time.
Can CVD SiC coating susceptors withstand extreme temperatures?
CVD SiC coating susceptors can endure extreme temperatures without losing their structural or functional integrity. The thermal stability of silicon carbide ensures reliable performance even under intense thermal cycling and high-temperature conditions.
What makes CVD SiC coating susceptors environmentally friendly?
CVD SiC coating susceptors promote sustainability by reducing waste and energy consumption. Their long lifespan minimizes the frequency of replacements, while their thermal efficiency lowers the environmental impact of industrial processes. These features align with modern industries’ goals of resource efficiency and reduced carbon footprints.
How do CVD SiC coating susceptors ensure product quality in semiconductor manufacturing?
CVD SiC coating susceptors ensure product quality by providing uniform heat distribution and maintaining chemical purity. These factors minimize defects during wafer production, resulting in high-performance electronic devices that meet stringent industry standards.
Are there any emerging applications for CVD SiC coating susceptors?
Yes, emerging applications include their use in cutting-edge technologies such as photovoltaic cell production, advanced electronics, and aerospace material development. Their adaptability and unique properties make them indispensable in innovative fields requiring precision and reliability.