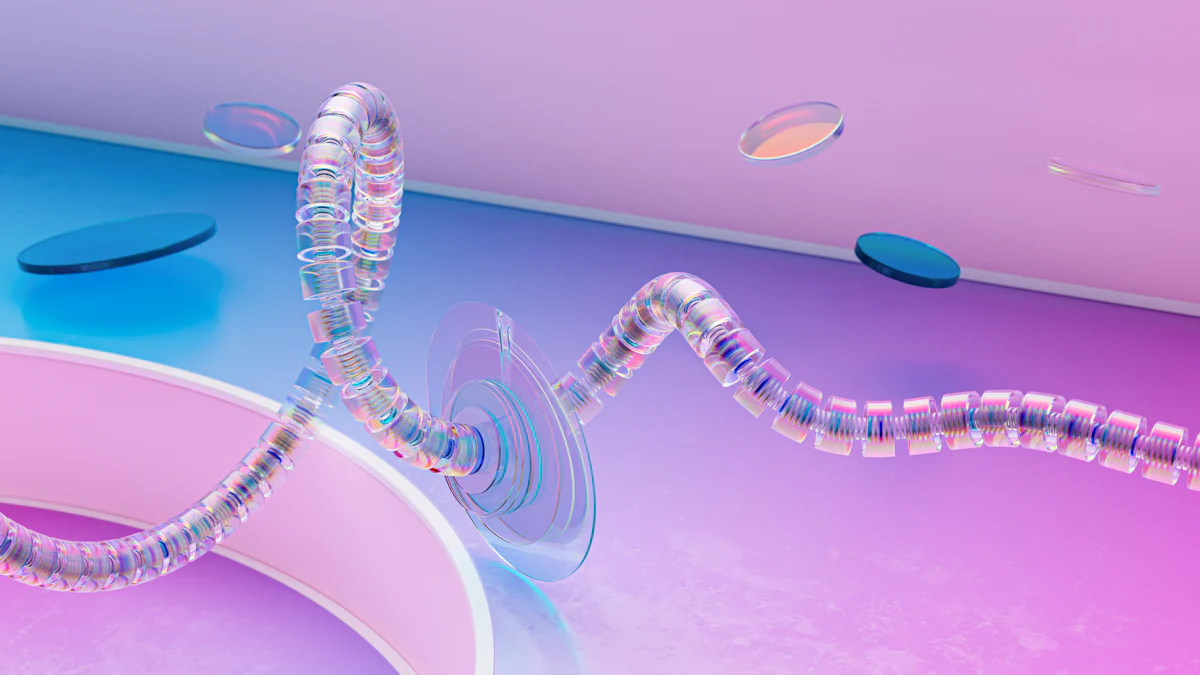
CvD SiC coatings play a pivotal role in materials science due to their exceptional properties. These coatings exhibit remarkable durability, ensuring long-lasting performance in demanding environments. Their thermal stability allows them to withstand extreme temperatures without degradation. Additionally, their chemical resistance protects materials from corrosion and oxidation. Industries such as aerospace, electronics, and energy rely on these coatings to enhance the performance and lifespan of critical components. By combining advanced technology with unique material characteristics, CvD SiC coatings continue to revolutionize modern engineering applications.
Key Takeaways
- CvD SiC coatings are known for their exceptional durability, thermal stability, and chemical resistance, making them ideal for demanding environments.
- Industries such as aerospace, electronics, and energy rely on CvD SiC coatings to enhance the performance and lifespan of critical components.
- The Chemical Vapor Deposition (CvD) process ensures high purity and uniformity in coatings, which is essential for precision applications.
- Despite their advantages, the production of CvD SiC coatings faces challenges such as high costs, slow deposition rates, and the need for strict control over production conditions.
- Emerging technologies like plasma-enhanced deposition and AI-driven automation are set to improve the efficiency and scalability of CvD SiC coating production.
- The versatility of CvD SiC coatings is leading to new applications in fields like healthcare and renewable energy, highlighting their adaptability and value.
- Ongoing research and development are crucial for overcoming current limitations and unlocking the full potential of CvD SiC coatings in modern engineering.
What Are CvD SiC Coatings?
Defining CvD (Chemical Vapor Deposition)
Chemical Vapor Deposition (CvD) is a process used to create thin films or coatings on a substrate. It involves the chemical reaction of gaseous precursors, which deposit a solid material onto the surface. This method ensures high purity and uniformity in the resulting coating. The process typically occurs in a controlled environment, where temperature and pressure are carefully regulated. CvD is widely used in industries requiring precision and durability, such as aerospace and electronics. Its ability to produce dense, defect-free coatings makes it a preferred choice for advanced applications.
Understanding Silicon Carbide (SiC)
Silicon Carbide (SiC) is a compound of silicon and carbon known for its exceptional physical and chemical properties. It exhibits high hardness, thermal conductivity, and resistance to wear and corrosion. These characteristics make SiC an ideal material for demanding environments. SiC can withstand extreme temperatures without losing its structural integrity, making it suitable for high-performance applications. In addition, its chemical stability ensures protection against oxidation and harsh chemicals. When combined with CvD, SiC coatings enhance the performance and longevity of materials in various industries.
Applications of CvD SiC Coatings in Materials Science
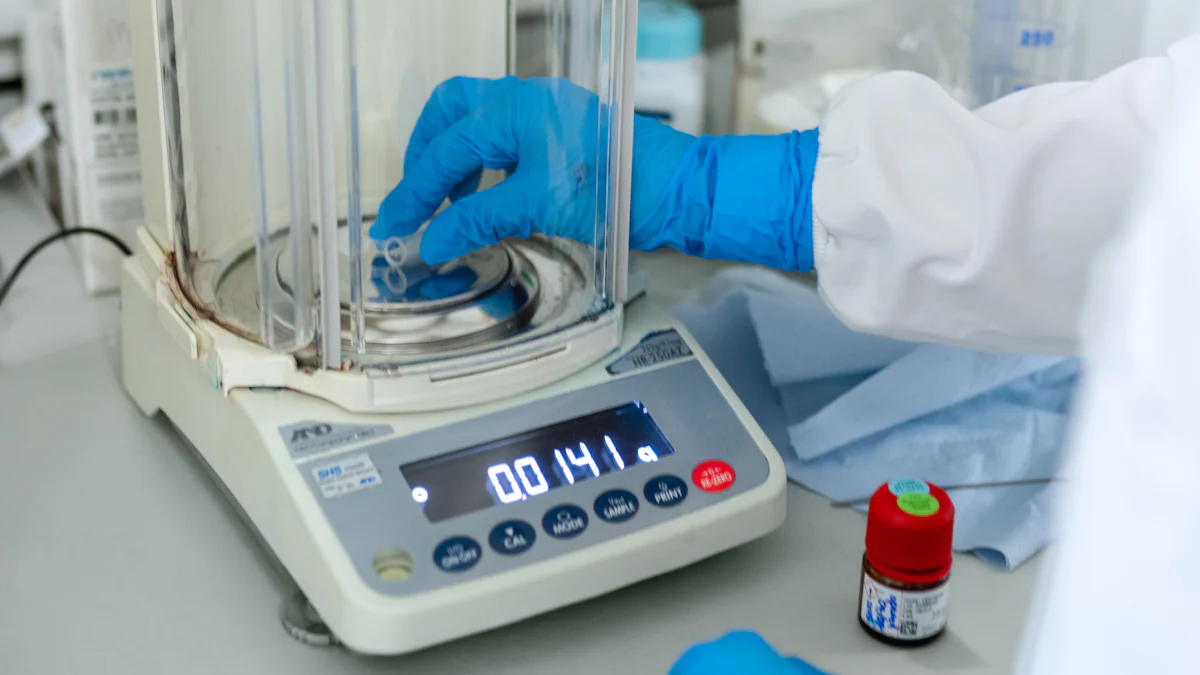
Aerospace Industry
The aerospace industry demands materials that can endure extreme conditions. CvD SiC coatings enhance the performance of components exposed to high temperatures and mechanical stress. These coatings protect turbine blades, engine parts, and structural components from oxidation and wear. Their lightweight nature also contributes to fuel efficiency in aircraft. Reflector materials in satellites and space telescopes benefit from the high thermal stability and precision of CvD SiC coatings. By improving durability and reliability, these coatings play a critical role in advancing aerospace technology.
Electronics and Semiconductor Industry
In the electronics and semiconductor industry, precision and reliability are essential. CvD SiC coatings provide excellent thermal conductivity, which helps manage heat in high-performance devices. They protect sensitive components from chemical corrosion and physical damage. Manufacturers use these coatings on substrates for microchips, sensors, and optical devices. The ability to produce defect-free, uniform layers ensures consistent performance in electronic applications. As devices become smaller and more complex, CvD SiC coatings continue to meet the industry’s evolving demands.
Energy Sector
The energy sector benefits significantly from the unique properties of CvD SiC coatings. These coatings improve the efficiency and lifespan of components in power plants, including turbines and heat exchangers. Their resistance to high temperatures and corrosive environments makes them ideal for renewable energy systems, such as solar panels and wind turbines. In nuclear energy, CvD SiC coatings enhance the safety and durability of reactor components. By increasing the reliability of energy systems, these coatings support the global transition to sustainable energy solutions.
Advantages of CvD SiC Coatings
Durability and Longevity
CvD SiC coatings significantly enhance the durability of materials. Their exceptional hardness protects surfaces from wear and mechanical damage, even under intense stress. This feature makes them ideal for applications in industries where components face constant friction or impact. The longevity of these coatings reduces the need for frequent replacements, saving both time and resources. By maintaining structural integrity over extended periods, they ensure reliable performance in critical environments. Many industries rely on these coatings to extend the lifespan of their equipment and improve operational efficiency.
Thermal and Chemical Stability
CvD SiC coatings exhibit remarkable thermal stability, allowing them to perform effectively in extreme temperatures. They resist thermal degradation, making them suitable for high-temperature applications such as turbines and reactors. Their chemical stability provides robust protection against corrosion and oxidation. This resistance ensures that materials remain unaffected by harsh chemicals or oxidizing agents. These properties make CvD SiC coatings indispensable in environments where both heat and chemical exposure are prevalent. Their ability to maintain performance under such conditions highlights their value in advanced engineering solutions.
Production Process of CvD SiC Coatings
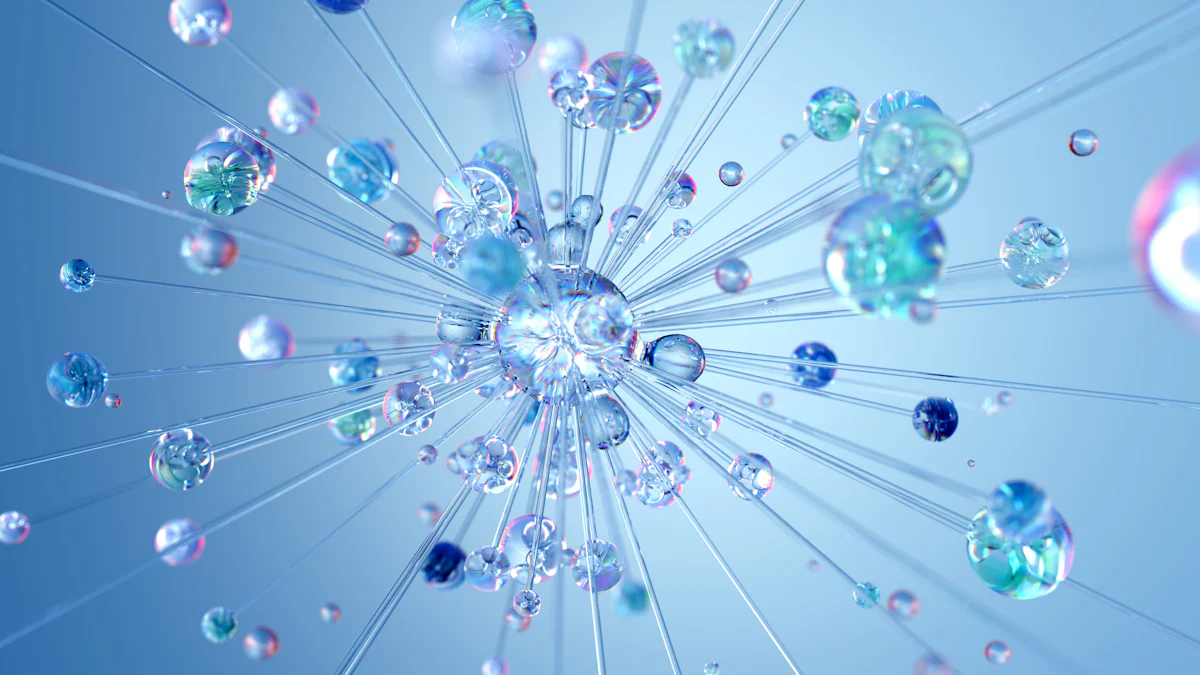
Overview of the CvD Process
The production of CvD SiC coatings relies on the Chemical Vapor Deposition (CvD) technique. This process begins with the introduction of gaseous precursors into a reaction chamber. High temperatures inside the chamber trigger a chemical reaction, causing silicon carbide to form and deposit onto the substrate. The controlled environment ensures uniformity and precision in the coating. Engineers carefully regulate parameters such as temperature, pressure, and gas flow rates to achieve the desired coating thickness and quality.
The CvD process produces coatings with exceptional purity and density. The absence of porosity enhances the mechanical strength and durability of the material. This method also allows for the deposition of thin, defect-free layers, making it suitable for applications requiring high precision. The versatility of the CvD process enables the coating of complex geometries, ensuring comprehensive coverage even on intricate surfaces. These characteristics make CvD an essential technique in advanced materials engineering.
Challenges in Production
Despite its advantages, the production of CvD SiC coatings presents several challenges. The high temperatures required for the process demand specialized equipment and materials capable of withstanding extreme conditions. Maintaining a controlled environment throughout the deposition process requires precise monitoring and adjustments, which can increase operational complexity.
The choice of precursors significantly impacts the quality of the final coating. Selecting the appropriate gases and ensuring their purity is critical to achieving optimal results. Impurities in the precursors can lead to defects in the coating, compromising its performance. Additionally, the deposition rate of silicon carbide is relatively slow, which can extend production times and limit scalability.
Cost remains another significant challenge. The equipment and energy required for the CvD process contribute to high production expenses. Scaling up the process for industrial applications often involves substantial investment, making it less accessible for smaller manufacturers. Researchers continue to explore ways to optimize the process, reduce costs, and improve efficiency to address these limitations.
Challenges and Limitations
Cost and Scalability
The production of CvD SiC coatings involves significant expenses. The high temperatures required for the chemical vapor deposition process demand advanced equipment, which increases initial investment costs. Energy consumption during the process further adds to operational expenses. These factors make the technology less accessible for smaller manufacturers or industries with limited budgets.
Scaling up the production of CvD SiC coatings presents additional challenges. The deposition rate of silicon carbide remains relatively slow, which limits the volume of coatings produced within a given timeframe. Increasing production capacity often requires substantial modifications to existing systems, leading to higher costs. Manufacturers must also ensure that scaling up does not compromise the quality or uniformity of the coatings. These constraints hinder the widespread adoption of CvD SiC coatings in industries that require large-scale applications.
Material and Process Limitations
The choice of materials used in the CvD process directly impacts the quality of the final coating. Gaseous precursors must meet strict purity standards to prevent defects in the deposited layers. Impurities in the precursors can lead to inconsistencies, reducing the performance and reliability of the coatings. Identifying and sourcing high-quality precursors often proves challenging and costly.
The CvD process itself has inherent limitations. Maintaining precise control over temperature, pressure, and gas flow rates requires sophisticated monitoring systems. Any deviation from optimal conditions can result in uneven coatings or structural flaws. Additionally, the process struggles to accommodate certain substrate materials that cannot withstand the high temperatures involved. These restrictions limit the range of applications for CvD SiC coatings, particularly in industries requiring diverse material compatibility.
Researchers continue to explore innovative solutions to address these challenges. Advances in precursor development, process optimization, and equipment design aim to reduce costs and expand the applicability of CvD SiC coatings. Overcoming these limitations will play a crucial role in unlocking the full potential of this technology.
Future Trends and Developments
Emerging Technologies
The field of CvD SiC coatings continues to evolve with the integration of emerging technologies. Researchers are exploring advanced deposition techniques to improve coating precision and efficiency. Innovations such as plasma-enhanced chemical vapor deposition (PECVD) are gaining attention for their ability to lower processing temperatures while maintaining high-quality coatings. These advancements make it possible to coat temperature-sensitive substrates, expanding the range of materials that can benefit from CvD SiC coatings.
Automation and artificial intelligence (AI) are also transforming the production process. AI-driven systems optimize parameters like gas flow rates and temperature settings, ensuring consistent results. Automation reduces human error and increases production speed, making the process more scalable. These technologies pave the way for cost-effective manufacturing, addressing one of the primary challenges in the industry.
Nanotechnology is another area driving innovation. Researchers are developing nanoscale SiC coatings with enhanced properties, such as improved wear resistance and thermal conductivity. These coatings offer superior performance in applications requiring extreme precision, such as microelectronics and advanced optics. The integration of nanotechnology highlights the potential for CvD SiC coatings to meet the demands of next-generation engineering solutions.
Expanding Applications
The versatility of CvD SiC coatings is leading to their adoption in new and diverse industries. In the medical field, these coatings are being investigated for use in surgical instruments and implants. Their biocompatibility and resistance to wear make them ideal for enhancing the durability and safety of medical devices. This application demonstrates the potential of CvD SiC coatings to improve healthcare technologies.
The automotive industry is also recognizing the benefits of these coatings. Electric vehicle (EV) manufacturers are using CvD SiC coatings to enhance the performance of power electronics and battery components. The coatings improve thermal management and protect against chemical degradation, contributing to the efficiency and longevity of EV systems. This development supports the growing demand for sustainable transportation solutions.
In the realm of renewable energy, CvD SiC coatings are finding applications in advanced solar panels and wind turbine components. Their ability to withstand harsh environmental conditions ensures reliable performance in renewable energy systems. These coatings play a crucial role in advancing clean energy technologies, aligning with global efforts to reduce carbon emissions.
The expansion of CvD SiC coatings into these sectors underscores their adaptability and value. As industries continue to innovate, the demand for high-performance materials like CvD SiC coatings will only increase. This trend highlights the importance of ongoing research and development to unlock new possibilities for this transformative technology.
CvD SiC coatings have transformed materials science by offering unmatched durability, thermal stability, and chemical resistance. These coatings enhance the performance of critical components across industries, including aerospace, electronics, and energy. Their ability to withstand extreme conditions ensures reliability in demanding applications. Ongoing research continues to refine their production processes and expand their applications. Emerging technologies and innovative approaches promise to unlock new possibilities for this advanced material. CvD SiC coatings represent a cornerstone of modern engineering, driving progress and shaping the future of high-performance materials.