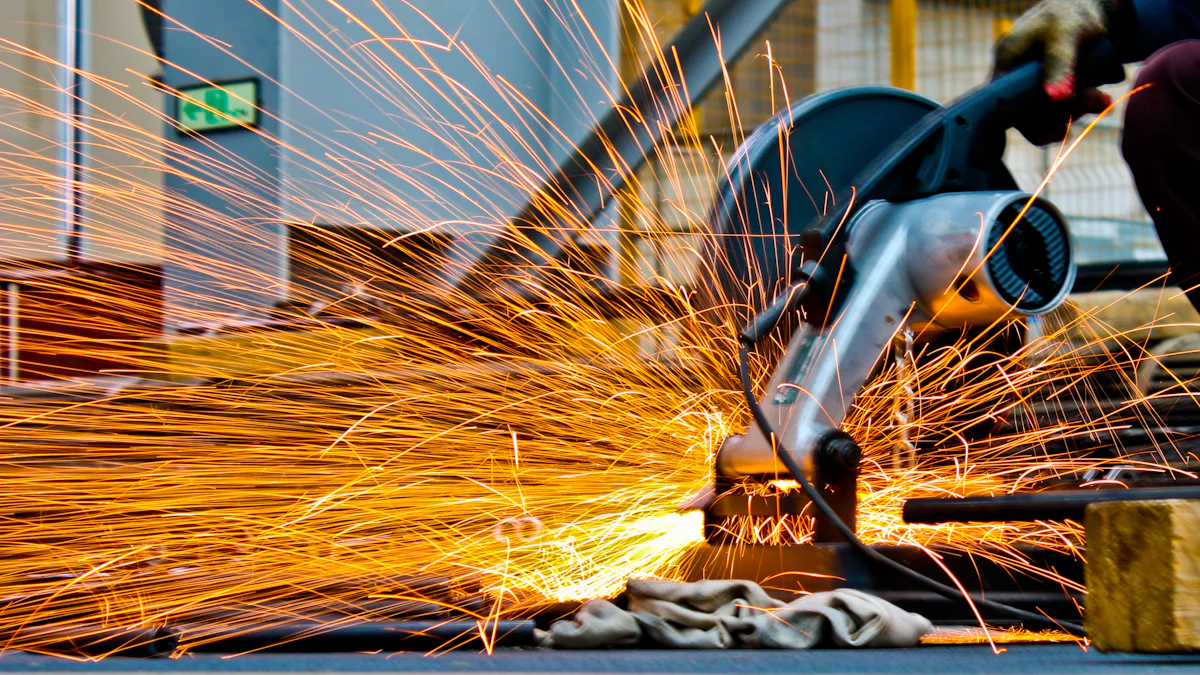
Industries face constant challenges in environments that demand exceptional material performance. CVD SiC coatings provide a groundbreaking solution by delivering unmatched durability, thermal resistance, and corrosion protection. These coatings excel where conventional materials often fail, ensuring reliability under extreme conditions. Their ability to maintain structural integrity and resist wear makes them indispensable for applications requiring high precision and longevity. By addressing critical limitations of traditional materials, CVD SiC coatings have become a transformative choice for industries seeking advanced performance and efficiency.
Key Takeaways
- CVD SiC coatings offer unmatched durability and thermal resistance, making them ideal for extreme environments where conventional materials fail.
- The chemical vapor deposition process ensures a uniform and defect-free coating, enhancing the performance of various substrates.
- These coatings excel in wear resistance and can achieve ultra-smooth finishes, crucial for precision engineering applications.
- Industries such as aerospace, semiconductor manufacturing, and energy production benefit significantly from the reliability and efficiency provided by CVD SiC coatings.
- Despite their advantages, challenges like high production costs and material compatibility need to be addressed for broader adoption.
- Ongoing innovations in deposition techniques and substrate compatibility are paving the way for expanded applications of CVD SiC coatings in diverse fields.
- Investing in CVD SiC coatings can lead to reduced maintenance costs and improved operational efficiency in demanding industrial applications.
What Are CVD SiC Coatings?
Definition and Key Characteristics
CVD SiC coatings, or chemical vapor deposition silicon carbide coatings, represent a cutting-edge material solution. These coatings consist of silicon carbide, a compound known for its exceptional hardness, thermal stability, and chemical resistance. The CVD process creates a uniform and dense layer of SiC on various substrates, enhancing their performance in extreme environments.
Key characteristics of CVD SiC coatings include high durability, excellent corrosion resistance, and superior thermal conductivity. They also exhibit remarkable wear resistance, making them ideal for applications requiring long-lasting performance. Additionally, these coatings can achieve an ultra-smooth surface finish, which is critical for precision engineering and advanced manufacturing processes.
CVD SiC coatings stand out due to their ability to maintain structural integrity under high temperatures and resist chemical degradation in harsh environments. This makes them a preferred choice for industries like aerospace, semiconductor manufacturing, and energy production.
How CVD SiC Coatings Are Made
The production of CVD SiC coatings involves a highly controlled chemical vapor deposition process. Manufacturers introduce a mixture of silicon- and carbon-containing gases into a reaction chamber. At elevated temperatures, these gases react and deposit a thin, uniform layer of silicon carbide onto the substrate. This process ensures a defect-free coating with consistent properties.
The CVD method allows for precise control over the coating’s thickness and composition. This level of precision ensures that the coating meets specific application requirements. Unlike traditional coating methods, CVD SiC coatings can be applied at relatively lower temperatures, reducing the risk of defects and preserving the mechanical properties of the underlying material.
The final step often involves polishing the coating to achieve a high surface finish. This enhances its performance in applications requiring minimal friction or high optical clarity. The combination of advanced manufacturing techniques and the inherent properties of silicon carbide makes CVD SiC coatings a superior alternative to conventional materials.
Why Conventional Materials Fall Short
Limitations in High-Temperature and Corrosive Environments
Conventional materials often fail to perform in extreme conditions. High temperatures weaken their structural integrity, leading to deformation or failure. Metals, for instance, lose strength when exposed to prolonged heat, making them unsuitable for applications requiring thermal stability. Polymers and other non-metallic materials degrade even faster under such conditions.
Corrosive environments present another significant challenge. Many traditional materials, including metals like steel and aluminum, corrode when exposed to harsh chemicals or moisture. This corrosion reduces their lifespan and compromises their reliability. Protective coatings applied to these materials often wear off over time, leaving the substrate vulnerable to damage.
Conventional materials lack the chemical resistance and thermal stability needed for demanding applications. Their inability to withstand these conditions limits their use in industries like aerospace, energy, and semiconductor manufacturing.
Challenges with Wear, Abrasion, and Surface Finish
Wear and abrasion significantly impact the performance of traditional materials. Repeated mechanical stress causes surface degradation, reducing efficiency and increasing maintenance costs. Metals and alloys, while durable, often develop scratches or grooves under abrasive conditions. This wear compromises their functionality and shortens their operational life.
Achieving a high-quality surface finish also poses challenges for conventional materials. Many materials cannot be polished to the ultra-smooth finishes required for precision engineering. Rough surfaces increase friction, reduce efficiency, and limit their use in advanced applications. For example, in semiconductor manufacturing, even minor surface imperfections can disrupt processes and lower product quality.
Traditional materials struggle to meet the demands of modern industries. Their limitations in wear resistance and surface finish hinder their ability to deliver consistent performance in high-precision environments.
Advantages of CVD SiC Coatings
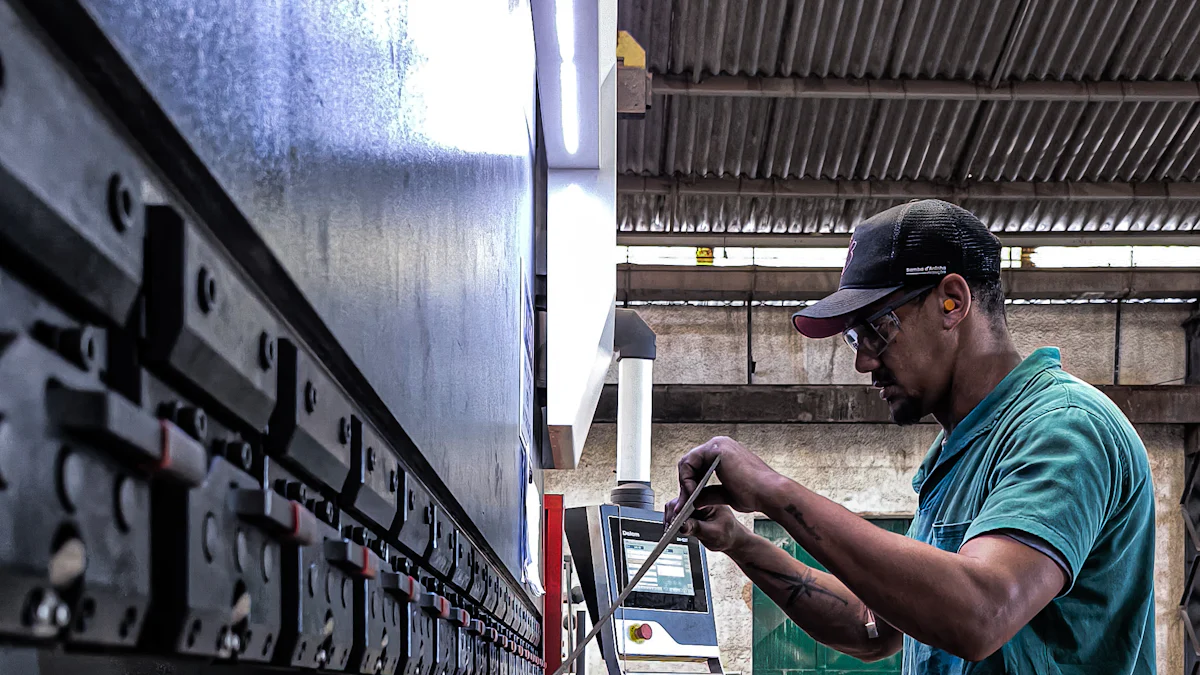
Superior Durability and Hardness
CVD SiC coatings exhibit exceptional durability, making them ideal for demanding applications. Their inherent hardness surpasses that of most conventional materials, including metals and alloys. This hardness allows them to resist scratches, dents, and other forms of mechanical damage. Industries that require materials to endure prolonged wear and tear benefit significantly from this property.
The dense structure of CVD SiC coatings enhances their ability to withstand abrasive environments. Unlike traditional materials, these coatings maintain their integrity even under continuous mechanical stress. This durability reduces the need for frequent replacements, lowering maintenance costs and improving operational efficiency.
The superior hardness of CVD SiC coatings ensures long-lasting performance in industries such as aerospace, energy, and semiconductor manufacturing.
Exceptional Thermal and Chemical Stability
CVD SiC coatings excel in environments where extreme temperatures and harsh chemicals are present. Their thermal stability allows them to retain their structural properties even at elevated temperatures. Unlike metals, which often weaken under heat, these coatings provide consistent performance in high-temperature applications.
Their chemical resistance further sets them apart. CVD SiC coatings act as a barrier against corrosive substances, protecting the underlying material from degradation. This property makes them invaluable in industries exposed to aggressive chemicals, such as semiconductor manufacturing and energy production.
CVD SiC coatings outperform conventional materials by offering unmatched stability in both thermal and chemical environments. This reliability ensures their effectiveness in critical applications.
High Surface Finish and Precision Engineering Benefits
CVD SiC coatings achieve an ultra-smooth surface finish through advanced polishing techniques. This high-quality finish minimizes friction, enhancing efficiency in precision engineering applications. Conventional materials often fail to reach this level of smoothness, limiting their use in industries requiring exacting standards.
The ability to produce a flawless surface benefits industries like semiconductor manufacturing, where even minor imperfections can disrupt processes. Additionally, the high surface finish improves optical clarity, making these coatings suitable for applications involving lenses and mirrors.
The precision and smoothness of CVD SiC coatings enable their use in cutting-edge technologies, where accuracy and performance are paramount.
Applications of CVD SiC Coatings
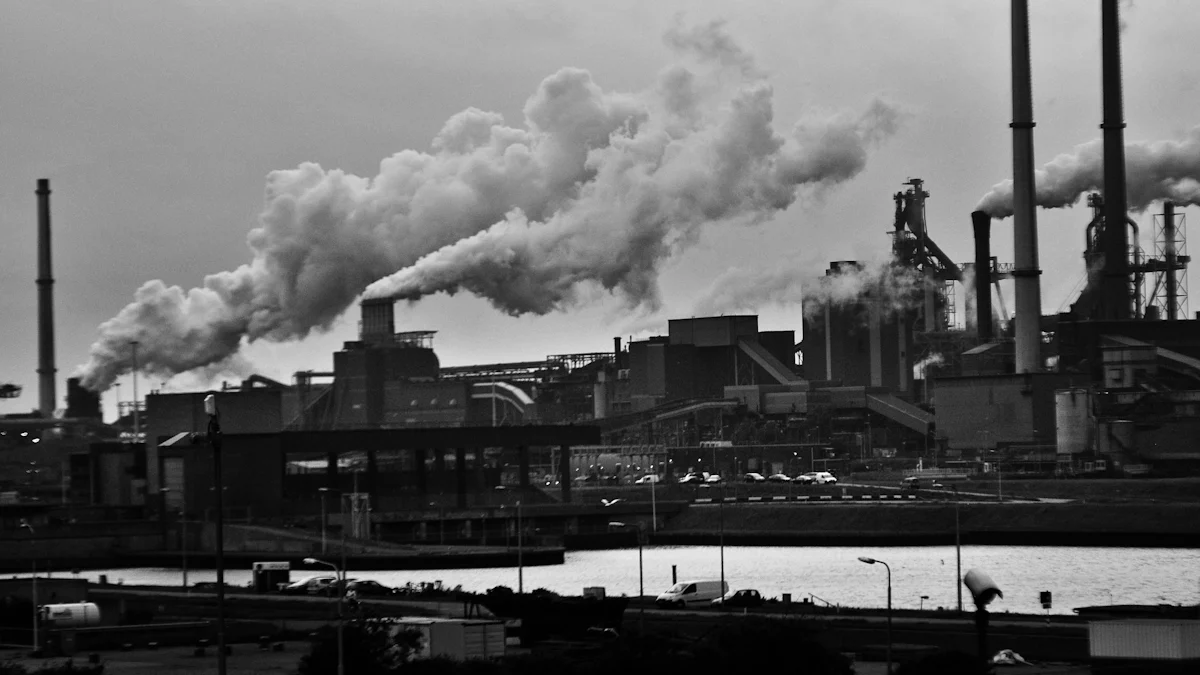
Semiconductor Manufacturing
CVD SiC coatings play a critical role in semiconductor manufacturing. The industry demands materials that can withstand extreme conditions while maintaining precision. These coatings provide exceptional thermal stability, ensuring consistent performance during high-temperature processes like chemical vapor deposition and etching. Their chemical resistance protects equipment from corrosive gases and chemicals used in semiconductor fabrication.
The ultra-smooth surface finish of CVD SiC coatings enhances the quality of semiconductor wafers. It minimizes contamination risks, which is essential for achieving high yields in production. Manufacturers rely on these coatings to extend the lifespan of critical components, reducing downtime and maintenance costs. Their ability to meet stringent purity and performance standards makes them indispensable in this field.
Semiconductor manufacturing benefits significantly from the durability, stability, and precision offered by CVD SiC coatings.
Aerospace and Defense
The aerospace and defense sectors require materials that can endure harsh environments and mechanical stress. CVD SiC coatings provide unmatched durability and thermal resistance, making them ideal for applications such as turbine blades, heat shields, and optical components. Their lightweight nature, combined with superior hardness, enhances the performance of aerospace systems without adding unnecessary weight.
In defense applications, these coatings protect sensitive equipment from wear, corrosion, and extreme temperatures. Their ability to maintain structural integrity under high stress ensures reliability in critical missions. Additionally, the high surface finish of CVD SiC coatings improves the efficiency of optical systems used in surveillance and targeting technologies.
Aerospace and defense industries rely on CVD SiC coatings for their ability to enhance performance and ensure reliability in demanding conditions.
Energy and Power Generation
Energy and power generation industries face challenges from high temperatures, corrosive environments, and mechanical wear. CVD SiC coatings address these issues by providing exceptional thermal and chemical stability. They protect components like heat exchangers, turbines, and reactors from degradation, ensuring long-term performance and efficiency.
These coatings also improve the durability of equipment used in renewable energy systems, such as solar panels and wind turbines. Their resistance to wear and corrosion reduces maintenance needs, lowering operational costs. In nuclear power plants, CVD SiC coatings act as a barrier against radiation and chemical exposure, enhancing safety and reliability.
Energy and power generation sectors benefit from the protective and performance-enhancing properties of CVD SiC coatings, making them a valuable asset in modern energy systems.
Challenges and Future Potential of CVD SiC Coatings
Current Limitations and Production Challenges
Despite their remarkable properties, CVD SiC coatings face certain limitations that hinder their widespread adoption. One significant challenge lies in the complexity of the production process. The chemical vapor deposition method requires precise control over temperature, gas flow, and reaction conditions. This level of precision increases manufacturing costs and limits scalability for mass production. Industries often find it difficult to justify the higher initial investment compared to conventional materials.
Another limitation involves the time-intensive nature of the coating process. The deposition of a uniform and defect-free layer takes considerable time, which slows down production rates. Additionally, the equipment required for CVD processes demands regular maintenance and calibration, further adding to operational expenses.
Material compatibility also poses challenges. Not all substrates can withstand the high temperatures involved in the deposition process. While CVD SiC coatings can be applied at relatively lower temperatures compared to other methods, certain materials may still experience thermal stress or deformation. This restricts the range of applications where these coatings can be effectively utilized.
Addressing these production challenges is essential for making CVD SiC coatings more accessible and cost-effective for a broader range of industries.
Innovations and Expanding Applications
Ongoing innovations in the field of material science aim to overcome the current limitations of CVD SiC coatings. Researchers are exploring advanced deposition techniques to reduce production time and costs. For instance, the development of hybrid methods that combine chemical vapor deposition with other technologies shows promise in enhancing efficiency. These advancements could make the coatings more affordable without compromising their quality.
Efforts to expand the compatibility of CVD SiC coatings with diverse substrates are also underway. Scientists are experimenting with modified deposition processes that operate at even lower temperatures. This approach could enable the application of these coatings on a wider variety of materials, opening up new possibilities for their use.
The potential applications of CVD SiC coatings continue to grow as industries recognize their unique benefits. In the medical field, these coatings could protect surgical instruments and implants from wear and corrosion. The automotive industry may adopt them for components exposed to high temperatures and mechanical stress, such as engine parts and exhaust systems. Emerging technologies, including quantum computing and advanced optics, could also benefit from the precision and durability offered by these coatings.
The future of CVD SiC coatings looks promising as innovations address current challenges and unlock new opportunities for their application.
CVD SiC coatings deliver exceptional performance in durability, thermal resistance, and chemical stability. These qualities position them as a superior alternative to conventional materials. Industries increasingly adopt these coatings to address challenges that traditional materials cannot overcome. Their ability to enhance efficiency and reliability makes them indispensable in demanding applications. Although cost and production complexity remain obstacles, ongoing innovations continue to refine their manufacturing processes. These advancements promise a transformative future, expanding the potential of CVD SiC coatings across diverse industries.