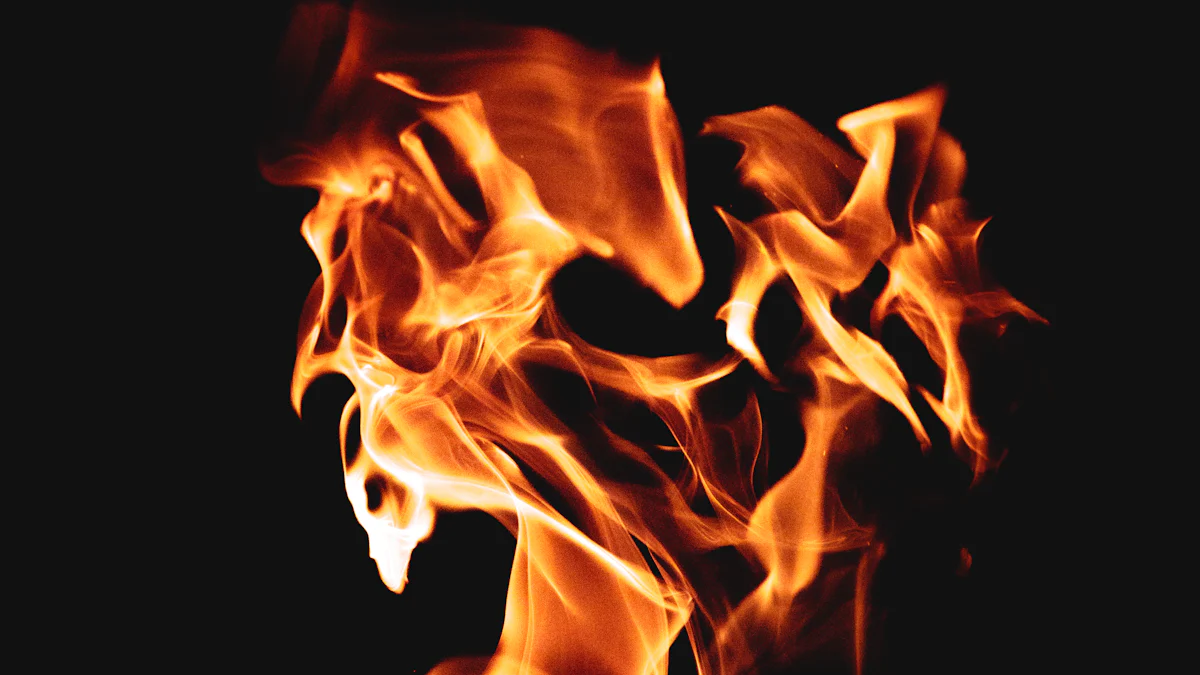
CVD TaC coating demonstrates exceptional performance in extreme heat environments due to its advanced material properties. The chemical vapor deposition (CVD) process ensures a uniform, high-purity layer of tantalum carbide, which provides remarkable thermal stability and resistance to oxidation. This coating remains stable at temperatures exceeding 2000°C, making it an ideal choice for applications requiring prolonged exposure to intense heat. Its ability to enhance the durability of components, such as those in aerospace and energy sectors, highlights its critical role in industries where reliability under harsh conditions is non-negotiable.
Key Takeaways
- CVD TaC coating offers exceptional thermal stability, remaining functional at temperatures exceeding 2000°C, making it ideal for extreme heat applications.
- The coating’s superior oxidation and corrosion resistance prolongs the lifespan of components, reducing maintenance costs in industries like aerospace and energy.
- With high thermal conductivity, CVD TaC coating efficiently dissipates heat, preventing localized overheating and enhancing performance in high-temperature reactors and furnaces.
- Its mechanical strength and durability ensure resistance to wear and thermal shock, making it a reliable choice for tools and components in demanding environments.
- CVD TaC coating outperforms other coatings, such as ceramics and metals, by maintaining structural integrity under thermal stress and providing longer-lasting protection.
- The versatility of CVD TaC coating allows it to bond effectively with various substrates, enhancing the reliability of critical components in aerospace and advanced manufacturing.
- Utilizing CVD TaC coating can lead to significant cost savings and improved productivity by reducing the frequency of tool replacements and enhancing operational efficiency.
Key Properties of CVD TaC Coating
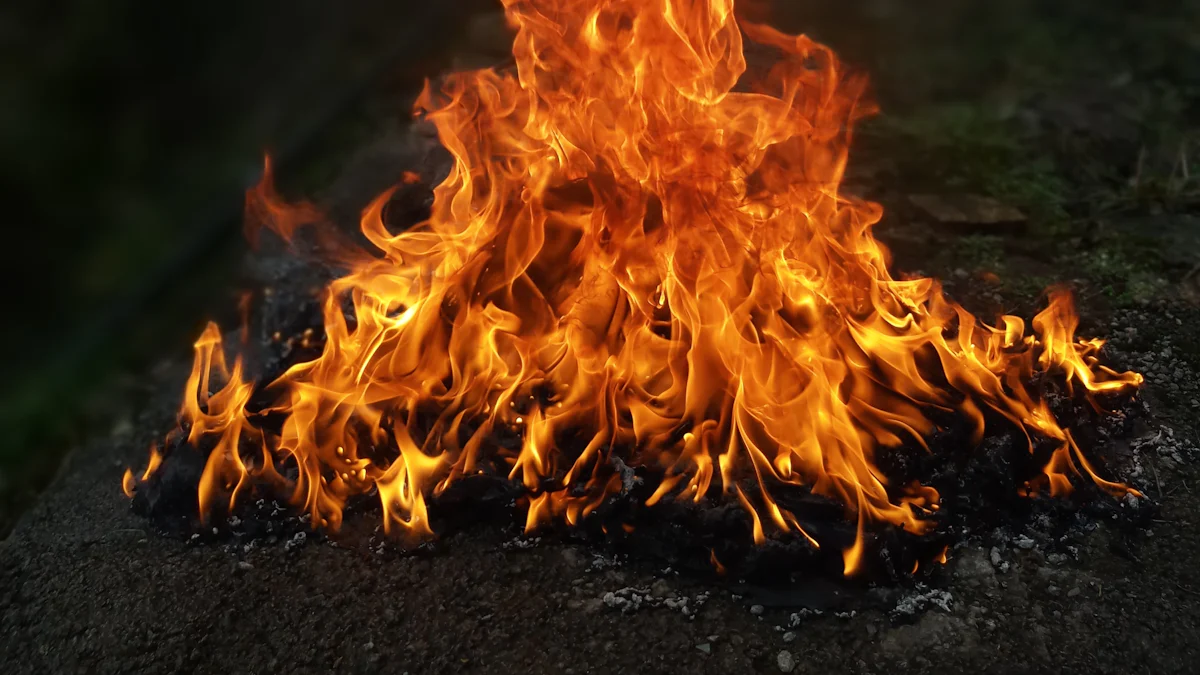
Exceptional Thermal Stability
High melting point of Tantalum Carbide (over 3800°F/2100°C).
Tantalum carbide (TaC) boasts one of the highest melting points among known compounds, reaching an impressive 3880°C (over 7000°F). This extraordinary thermal property makes CVD TaC coating a preferred choice for applications exposed to extreme heat. The high melting point ensures that the coating remains stable and functional even in the most demanding environments, such as aerospace and energy sectors.
Maintains structural integrity under prolonged heat exposure.
The chemical stability of tantalum carbide allows it to retain its structural integrity during extended exposure to high temperatures. Unlike many materials that degrade or deform under thermal stress, CVD TaC coating maintains its mechanical properties, ensuring consistent performance. This durability is critical for components like turbine blades and heat shields, which must endure prolonged heat without failure.
Superior Oxidation and Corrosion Resistance
Protective barrier against oxidation and chemical reactions at high temperatures.
CVD TaC coating forms a robust barrier that protects underlying materials from oxidation and chemical reactions. In high-temperature environments, oxidation can weaken materials and compromise their functionality. The tantalum carbide layer prevents oxygen and other reactive elements from penetrating the surface, preserving the integrity of the coated components.
Prolonged lifespan in corrosive and oxidative environments.
The exceptional corrosion resistance of tantalum carbide extends the lifespan of components operating in harsh conditions. Industries such as aerospace and advanced manufacturing benefit from this property, as it reduces maintenance costs and enhances reliability. By resisting both oxidation and chemical degradation, CVD TaC coating ensures long-term performance in environments where other materials fail.
High Thermal Conductivity
Efficient heat dissipation to prevent localized overheating.
Tantalum carbide exhibits significant thermal conductivity, measured at approximately 22 W·m-1·K−1. This property enables CVD TaC coating to dissipate heat efficiently, preventing localized overheating that could damage components. Effective heat management is essential in applications like high-temperature reactors and furnaces, where thermal gradients can lead to material failure.
Enhanced performance during thermal cycling.
Thermal cycling, which involves repeated heating and cooling, often causes stress and cracking in materials. CVD TaC coating excels in such conditions due to its low thermal expansion coefficient and high mechanical strength. These attributes minimize the risk of cracking or delamination, ensuring consistent performance over multiple cycles. This makes it an ideal solution for tools and molds used in high-temperature manufacturing processes.
Mechanical Strength and Durability
Resistance to wear, abrasion, and thermal shock in high-stress environments.
CVD TaC coating demonstrates exceptional resistance to wear and abrasion, making it a reliable choice for components exposed to high-stress environments. The high hardness of tantalum carbide, with a Mohs hardness rating of 9-10, ensures that the coating can withstand significant mechanical stress without degradation. This property is particularly valuable in industries like aerospace and advanced manufacturing, where tools and components frequently encounter abrasive forces.
Thermal shock resistance further enhances the durability of CVD TaC coating. Rapid temperature changes often cause materials to crack or fail due to uneven expansion and contraction. However, the low thermal expansion coefficient of tantalum carbide (6.6×10−6 K−1) minimizes these risks. This stability under thermal cycling ensures that the coating maintains its integrity, even in extreme conditions such as high-speed airflow erosion or ablation in aerospace applications.
Compatibility with various substrates for added strength and reliability.
The versatility of CVD TaC coating lies in its ability to bond effectively with a wide range of substrates. The chemical vapor deposition process creates a uniform and adherent layer of tantalum carbide on materials like graphite, carbon/carbon composites, and metals. This compatibility enhances the mechanical strength of the coated components, ensuring reliable performance in demanding applications.
For example, in the aerospace industry, CVD TaC coating improves the durability of graphite components used in spacecraft and aircraft. Its excellent chemical and mechanical compatibility with carbon-based materials ensures seamless integration, reducing the risk of delamination or failure. This adaptability makes it an indispensable solution for industries requiring robust and long-lasting coatings.
Comparison to Other High-Temperature Coating Materials
CVD TaC Coating vs. Ceramic Coatings
Higher melting point and better thermal conductivity.
Ceramic coatings, while widely used in high-temperature applications, often fall short when compared to CVD TaC coating. Tantalum carbide possesses a significantly higher melting point, exceeding 3800°F (2100°C), which surpasses most ceramics. This property ensures that CVD TaC coating remains stable and functional in environments where ceramic coatings may fail due to thermal degradation. Additionally, tantalum carbide exhibits superior thermal conductivity, enabling efficient heat dissipation. In contrast, ceramic coatings tend to have lower thermal conductivity, which can lead to localized overheating and material failure in critical applications.
Greater resistance to cracking under thermal stress.
Thermal stress often causes cracking in ceramic coatings, especially during rapid temperature changes. The low thermal expansion coefficient of tantalum carbide minimizes this risk, making CVD TaC coating more resistant to thermal shock. This advantage proves essential in industries like aerospace, where components endure extreme thermal cycling. Ceramic coatings, despite their widespread use, frequently struggle to maintain structural integrity under such conditions, limiting their reliability in demanding environments.
CVD TaC Coating vs. Metallic Coatings
Superior oxidation and corrosion resistance compared to metals like nickel or chromium.
Metallic coatings, such as those made from nickel or chromium, offer some degree of protection in high-temperature environments. However, they cannot match the oxidation and corrosion resistance of CVD TaC coating. Tantalum carbide forms a robust barrier that prevents oxygen and reactive elements from penetrating the surface, even at elevated temperatures. Metallic coatings, on the other hand, often oxidize or degrade over time, compromising the performance of the underlying material. This makes CVD TaC coating a more reliable choice for applications requiring long-term stability in oxidative and corrosive conditions.
Longer lifespan in extreme heat environments.
The durability of CVD TaC coating far exceeds that of metallic coatings in extreme heat. Metals like nickel and chromium may soften or lose their protective properties when exposed to prolonged high temperatures. In contrast, tantalum carbide maintains its structural integrity and chemical stability, ensuring a longer lifespan for coated components. This characteristic reduces maintenance costs and enhances operational efficiency, particularly in industries such as energy and advanced manufacturing.
CVD TaC Coating vs. Other Carbide Coatings
Higher thermal stability than tungsten carbide or silicon carbide.
Among carbide coatings, CVD TaC coating stands out due to its exceptional thermal stability. While tungsten carbide and silicon carbide are effective in certain high-temperature applications, they cannot withstand the same extreme conditions as tantalum carbide. The higher melting point of tantalum carbide ensures that CVD TaC coating remains functional in environments exceeding 2000°C, where other carbides may fail. This makes it an indispensable solution for applications requiring prolonged exposure to intense heat.
Better performance in applications requiring both heat and wear resistance.
Tantalum carbide offers a unique combination of heat and wear resistance, outperforming other carbide coatings. Tungsten carbide, though hard, lacks the same level of thermal stability, while silicon carbide may struggle with mechanical stress in high-temperature environments. CVD TaC coating excels in applications where components face both extreme heat and abrasive forces, such as turbine blades and high-temperature molds. Its ability to resist wear and maintain performance under thermal cycling further solidifies its superiority over other carbide coatings.
Real-World Applications of CVD TaC Coating
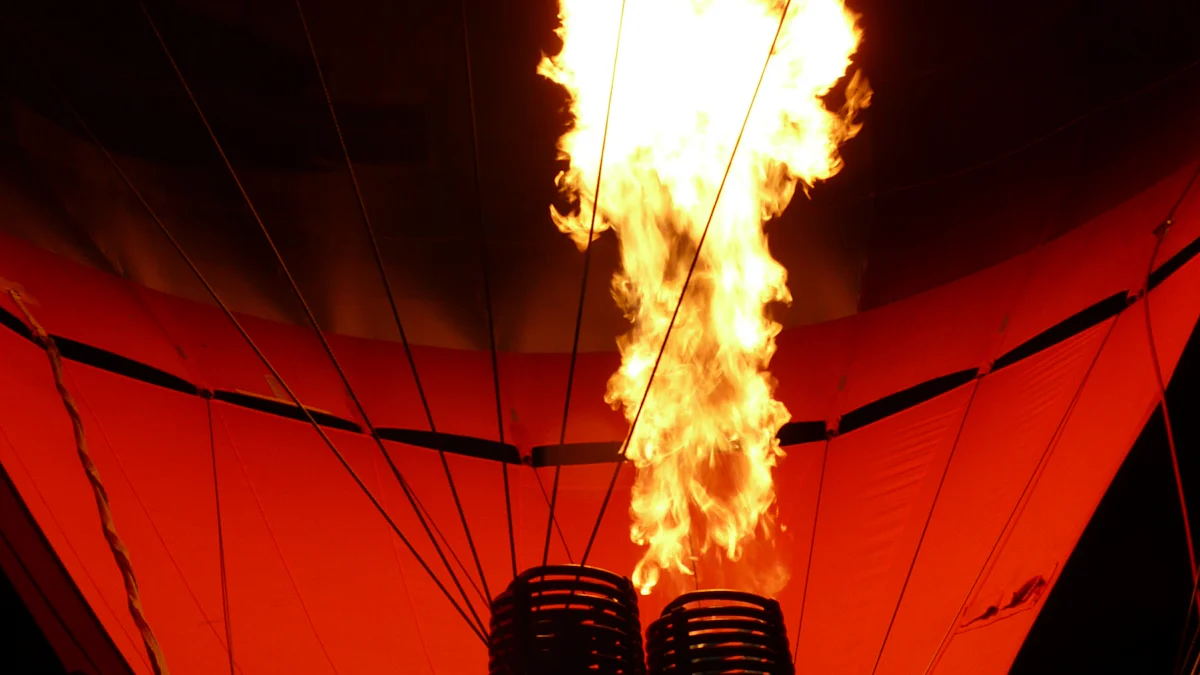
Aerospace Industry
Thermal protection for rocket nozzles and re-entry vehicle components.
The aerospace industry demands materials that can endure extreme thermal and mechanical stress. CVD TaC coating provides an exceptional solution for rocket nozzles and re-entry vehicle components. These parts face intense heat during propulsion and atmospheric re-entry. The high melting point of tantalum carbide ensures that the coating remains stable, even at temperatures exceeding 2000°C. Its superior oxidation resistance prevents material degradation caused by exposure to high-temperature oxygen-rich environments. This combination of properties enhances the reliability and safety of aerospace missions.
Enhanced durability for turbine blades and heat shields.
Turbine blades and heat shields in aircraft engines operate under extreme conditions, including high-speed airflow and rapid temperature fluctuations. CVD TaC coating protects these components by offering resistance to thermal shock and wear. Its ability to dissipate heat efficiently reduces the risk of localized overheating, which can compromise performance. Additionally, the coating’s mechanical strength ensures that turbine blades and heat shields maintain their structural integrity, even after prolonged use. This durability translates to reduced maintenance costs and extended service life for critical aerospace components.
Energy Sector
Coatings for components in high-temperature reactors and furnaces.
High-temperature reactors and industrial furnaces require materials that can withstand prolonged exposure to extreme heat and corrosive environments. CVD TaC coating excels in these applications by forming a robust barrier against oxidation and chemical reactions. Its chemical stability ensures that reactor and furnace components retain their functionality, even under harsh conditions. By protecting these components, the coating enhances operational efficiency and minimizes downtime caused by material failure.
Improved efficiency and lifespan of heat exchangers.
Heat exchangers play a vital role in energy systems by transferring heat between fluids. However, they often face challenges such as thermal cycling and corrosion. CVD TaC coating addresses these issues by providing excellent thermal conductivity and corrosion resistance. The coating’s ability to dissipate heat efficiently improves the performance of heat exchangers, while its protective properties extend their lifespan. This makes it an indispensable solution for energy applications where reliability and efficiency are paramount.
Advanced Manufacturing
Protection for tools and molds used in high-temperature processes.
Advanced manufacturing processes, such as metal casting and forging, involve high temperatures that can degrade tools and molds. CVD TaC coating protects these components by offering resistance to wear, abrasion, and thermal shock. Its high hardness ensures that tools and molds maintain their precision and functionality, even after repeated use. This protection reduces the frequency of tool replacement, leading to cost savings and improved productivity in manufacturing operations.
Increased reliability in additive manufacturing and powder metallurgy.
Additive manufacturing and powder metallurgy rely on precise control of high-temperature processes to produce complex components. CVD TaC coating enhances the reliability of equipment used in these techniques by providing thermal stability and resistance to chemical reactions. Its compatibility with various substrates ensures seamless integration with manufacturing tools, enabling consistent performance. This reliability supports the production of high-quality components, meeting the stringent demands of industries such as aerospace and energy.
CVD TaC coatings deliver unmatched performance in extreme heat applications due to their exceptional thermal stability, oxidation resistance, and mechanical strength. These coatings outperform alternative materials by maintaining durability and efficiency under intense conditions. Industries such as aerospace, energy, and advanced manufacturing rely on this technology to enhance the longevity and reliability of critical components. By resisting wear, corrosion, and thermal stress, CVD TaC coatings provide a cost-effective solution for demanding environments, ensuring consistent performance and value over time.