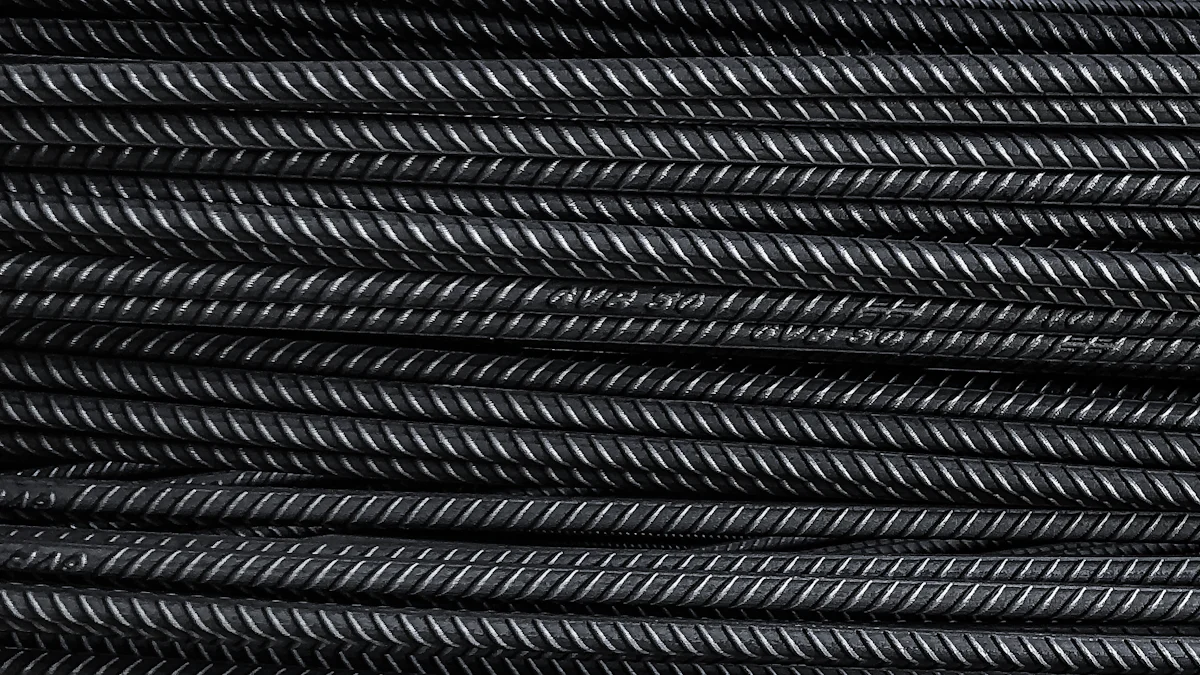
Verstärkter Kohlenstoff-Verbund ist ein bemerkenswertes Material bekannt für seine außergewöhnliche Festigkeit und Haltbarkeit. Durch die Integration von Kohlenstofffasern, die fünfmal stärker und doppelt so steif wie Stahl sind, mit einer Kohlenstoffmatrix bildet sie eine kohlenstofffaserverstärkter kohlenstoffverbund in der Lage, extreme Bedingungen zu erhalten. Dieses fortschrittliche Material bietet hervorragende Wärmebeständigkeit, so dass es eine bevorzugte Wahl für Luft- und Tiefbauanwendungen. Beim Vergleich carbon composite vs carbon fiber, der verstärkte Kohlenstoff-Kohlenstoff-Verbund zeichnet sich durch sein überlegenes Festigkeits-zu-Gewicht-Verhältnis und einzigartige Eigenschaften aus. Einblick in was ist kohlenstoff-kohlenstoff-verbund unterstreicht seine unverzichtbare rolle in industrien, die präzision und widerstand fordern, wo die leistung die kohlenstoffpreis.
Wichtigste Erkenntnisse
- Verstärkter Kohlenstoff-Kohlenstoff-Verbund kombiniert Kohlenstofffasern mit einer Kohlenstoff-Matrix, bietet außergewöhnliche Festigkeit und Wärmebeständigkeit, so dass es ideal für Luft- und Raumfahrt und fortschrittliche engineering-anwendungen.
- Die Herstellung von Kohlenstofffasern ist von entscheidender Bedeutung; die Auswahl der richtigen Art und deren Anordnung verbessert die leistung von verbundwerkstoffen unter stress und extremen bedingungen.
- Die Tränkung von Kohlenstofffasern mit Harz ist ein wichtiger Schritt, der eine starke Bindung und gleichmäßige Struktur gewährleistet, wodurch die Stufe für den Carbonisierungsprozess eingestellt wird, der das Harz in eine robuste Kohlenstoffmatrix verwandelt.
- Die Verdichtung durch wiederholte Zyklen der Imprägnierung und Karbonisierung erhöht die Dichte und Festigkeit des Verbundes, wodurch es hohen Temperaturen und mechanischen Belastungen standhält.
- Endbearbeitung und Oberflächenbehandlungen verbessern die Form des Verbundwerkstoffes und schützen sie vor Umweltfaktoren, gewährleisten Haltbarkeit und Zuverlässigkeit in anspruchsvollen Anwendungen.
- Das Verständnis des sorgfältigen Herstellungsprozesses von verstärktem Kohlenstoffverbund unterstreicht seine unverzichtbare Rolle in Industrien, in denen Leistung und Präzision kritisch sind.
Schritt 1: Herstellung der Kohlefaser
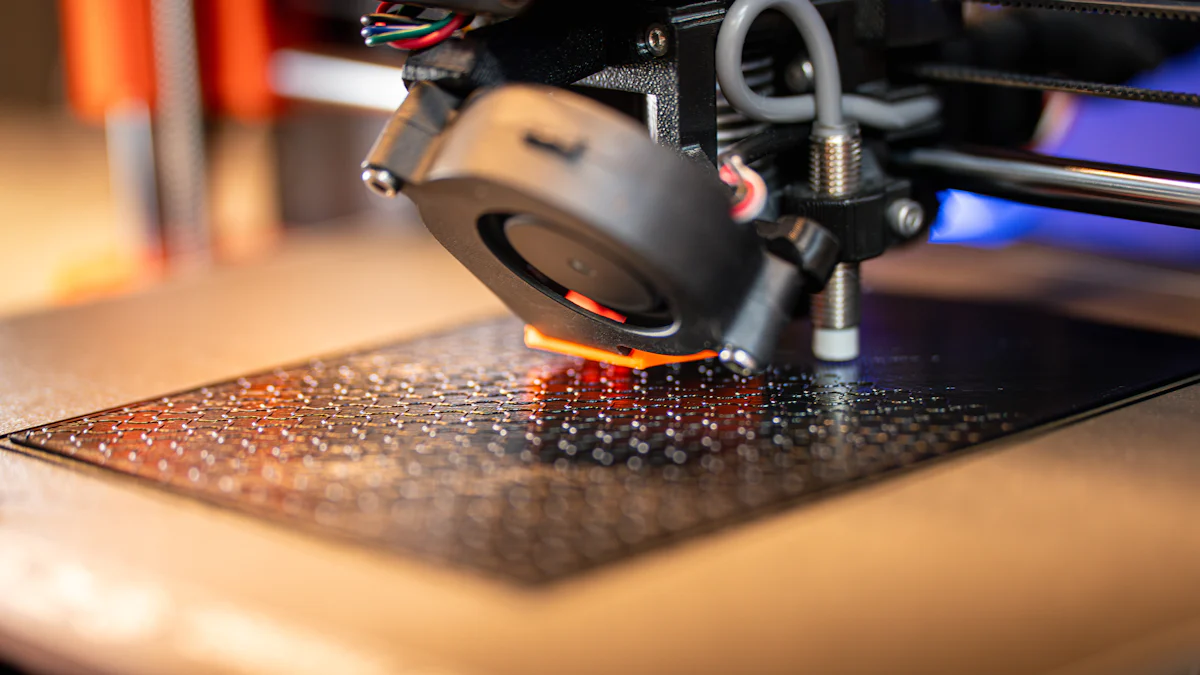
Die Gründung einer kohlenstoff-verbundwerkstoff liegt in seinen Kohlenstofffasern. Diese Fasern dienen als Rückgrat und verleihen dem Material eine außergewöhnliche Festigkeit und Steifigkeit. Die Herstellung dieser Fasern erfordert eine sorgfältige Auswahl und präzise Anordnung, um sicherzustellen, dass der endgültige Verbund den gewünschten Leistungsstandards entspricht.
Auswählen und Anordnen von Kohlefasern
Arten von Kohlenstofffasern, die in verstärktem Kohlenstoffverbund eingesetzt werden
Kohlenstofffasern kommen in verschiedenen Formen und bieten jeweils einzigartige Eigenschaften. Hochfeste Fasern, oft in Luft- und Raumfahrtanwendungen eingesetzt, liefern eine überlegene Zugfestigkeit. Andererseits zeichnen sich hochmodulige Fasern durch Steifigkeit aus, was sie ideal für Anwendungen mit Steifigkeitsanforderungen macht. Hersteller wählen häufig Fasern auf Basis der spezifischen Anforderungen des Verbunds, wie Wärmebeständigkeit oder mechanische Leistung.
Kohlenstofffasern werden üblicherweise mit anderen Materialien kombiniert, um ihre Eigenschaften zu verbessern. Zum Beispiel, wenn sie mit Graphit gemischt, schaffen sie einen Verbund, der extremen Temperaturen standhalten kann. Diese Kombination ist besonders wertvoll in Industrien wie Luft- und Raumfahrt, wo Materialien harte Umgebungen ertragen müssen, ohne die strukturelle Integrität zu beeinträchtigen.
Verfahren zur Anordnung von Fasern zur Gewährleistung der strukturellen Integrität
Die korrekte Anordnung von Kohlenstofffasern ist entscheidend für eine optimale Leistung. Hersteller verwenden mehrere Methoden, um die Fasern auszurichten, um sicherzustellen, dass der Verbund Stress effektiv handhaben kann. Gemeinsame Techniken umfassen:
- Unidirektionale Ausrichtung: Fasern sind in einer einzigen Richtung angeordnet, um die Festigkeit entlang dieser Achse zu maximieren. Dieses Verfahren wird häufig in Anwendungen eingesetzt, die eine hohe Zugfestigkeit erfordern.
- Weben oder Geflecht: Fasern sind verkettet, um eine gewebeartige Struktur zu schaffen. Dieser Ansatz verbessert die Langlebigkeit und bietet eine multidirektionale Stärke.
- Schichtung: Mehrere Faserlagen werden in unterschiedlichen Orientierungen gestapelt. Diese Technik ausgeglichen Festigkeit und Steifigkeit in allen Richtungen.
Jedes Anordnungsverfahren trägt zur Gesamtleistung des Verbunds bei. So bietet die unidirektionale Ausrichtung eine außergewöhnliche Stärke in einer Richtung, während gewebte Strukturen ausgewogenere Eigenschaften bieten. Durch die Anpassung der Anordnung an die Anwendung stellen die Hersteller sicher, dass der Verbund bestimmten Anforderungen entspricht.
"Die Anordnung von Kohlenstofffasern wirkt direkt auf die mechanischen Eigenschaften des Verbundes, was es zu einem kritischen Schritt im Herstellungsprozess macht. „
Schritt 2: Erstellen der Carbon Matrix
Die kohlenstoffmatrix bildet den wesentlichen rahmen, der die kohlenstofffasern in einer kohlenstoff-verbundwerkstoff. Dieser Schritt beinhaltet zwei kritische Prozesse: Imprägnieren der Fasern mit Harz und Umwandlung des Harzes in Kohlenstoff durch Carbonisierung. Diese Verfahren gewährleisten, dass der Verbund seine bemerkenswerte Festigkeit und thermische Stabilität erreicht.
Tränkende Fasern mit Harz
Der Imprägniervorgang beginnt durch Rätteln der Kohlenstofffasern mit einem Harz, das als Vorstufe für die Kohlenstoffmatrix fungiert. Dieser Schritt ist entscheidend für die Schaffung einer einheitlichen und stabilen Struktur.
Rolle des Harzes als Vorstufe für die Kohlenstoffmatrix
Harz dient als Grundlage für die Kohlenstoffmatrix. Sie durchdringt die Zwischenräume zwischen den Kohlenstofffasern und sorgt für eine starke Bindung und gleichmäßige Verteilung. Üblicherweise verwendete Harze sind Phenol- und Epoxidharze, die für ihre hohe Temperaturen und mechanische Beanspruchung bekannt sind. Nach dem Auftragen hält das Harz nicht nur die Fasern an Ort und Stelle, sondern bereitet sie auch auf die nächste Stufe der Transformation vor.
„Die Rolle des Harzes erstreckt sich über die Verklebung hinaus; es setzt die Stufe für den Carbonisierungsprozess, wo es in eine robuste Kohlenstoffmatrix verwandelt. „
Hersteller kontrollieren die Harzanwendung sorgfältig, um Leerstellen oder Schwachstellen im Verbund zu vermeiden. Techniken wie vakuumgestützte Imprägnierung oder druckgestützte Methoden sorgen für eine gründliche Sättigung. Diese Methoden verbessern die strukturelle Integrität und Leistungsfähigkeit des Verbundwerkstoffes unter extremen Bedingungen.
Karbonisierungsprozess
Nach der Imprägnierung erfährt das Harz eine Carbonisierung, ein Verfahren, das es in Kohlenstoff umwandelt. Diese Transformation ist unerlässlich, um die Hochtemperaturbeständigkeit und Haltbarkeit des Verbundwerkstoffes zu erreichen.
Erwärmen und Harz in Kohlenstoff umwandeln
Der Carbonisierungsprozess beinhaltet die Erwärmung der harzgetränkten Fasern in einer kontrollierten Umgebung. Dabei zersetzt sich das Harz, löst flüchtige Verbindungen ab und hinterlässt eine feste Kohlenstoffstruktur. Dieser Schritt erfordert Präzision, um die Kohlenstoffmatrix ohne Defekte zu gewährleisten.
"Low-Temperatur-Pyrolyse, ein in verschiedenen Branchen untersuchtes Verfahren, zeigt die Bedeutung der kontrollierten Erwärmung bei der Umwandlung von organischen Materialien in stabile Kohlenstoffstrukturen. „
Die resultierende Kohlenstoffmatrix erhöht die Fähigkeit des Verbundes, extreme Hitze und mechanische Belastung zu erhalten. Diese Eigenschaft macht es für Anwendungen wie Flugzeug-Bremsscheiben unverzichtbar, wo Materialien unter intensiven Bedingungen zuverlässig arbeiten müssen.
Durch die Kombination von Harzimprägnierung mit präziser Carbonisierung schaffen Hersteller eine Kohlenstoffmatrix, die die Festigkeit der Kohlenstofffasern ergänzt. Diese Synergie führt zu einer kohlenstoff-verbundwerkstoff in der lage, die anforderungen der fortschrittlichen ingenieur- und luftfahrtindustrie zu erfüllen.
Schritt 3: Verdichtung und Fertigstellung
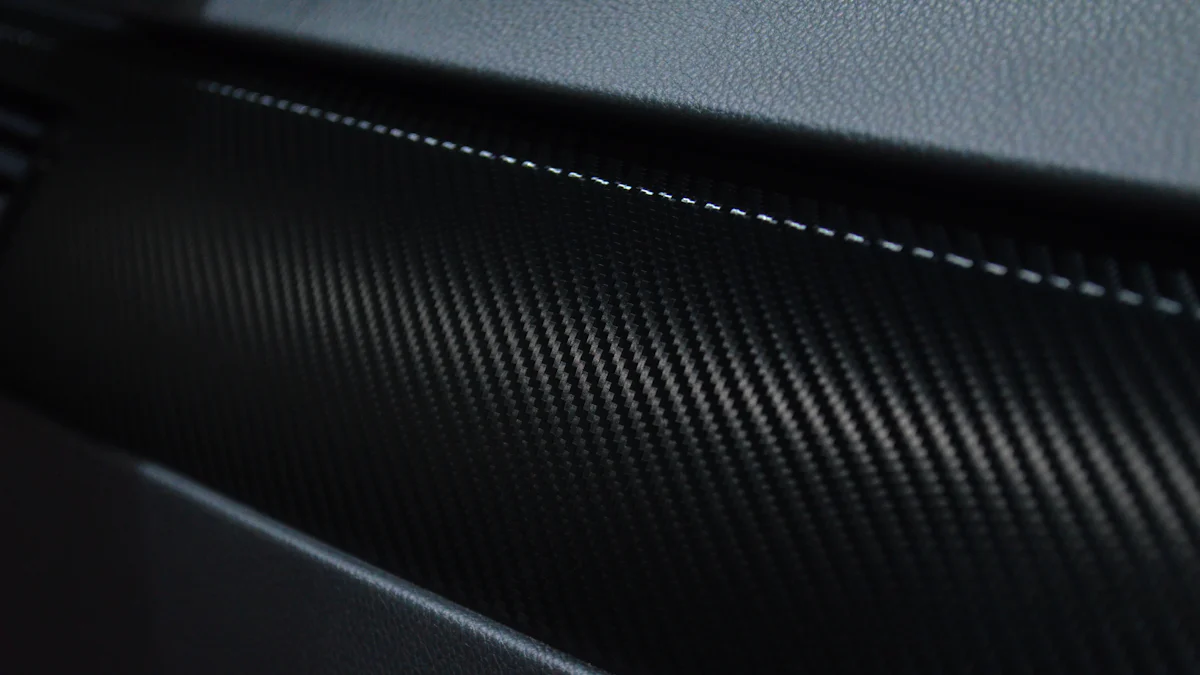
Der letzte Schritt zur Schaffung eines kohlenstoff-verbundwerkstoff bedeutet Verdichtung und Veredelung. Diese Stufe verbessert die Dichte, Festigkeit und Oberflächeneigenschaften des Materials, um sicherzustellen, dass es den strengen Anforderungen der fortschrittlichen Anwendungen entspricht. Hersteller verwenden präzise Techniken, um die gewünschten strukturellen und funktionalen Eigenschaften zu erreichen.
Wiederholte Imprägnierung und Carbonisierung
Die Verdichtung beginnt mit wiederholten Zyklen der Imprägnierung und Karbonisierung. Diese Zyklen füllen die Poren innerhalb des Verbundes, erhöhen ihre Dichte und mechanische Festigkeit.
Erreichen der gewünschten Dichte und Festigkeit
Hersteller imprägnieren den Verbund mit kohlenstoffreichen Substanzen, wie Pechs oder Harzen. Diese Materialien durchdringen die poröse Struktur, füllen Leerstellen und verstärken die Matrix. Nach Imprägnierung wird der Verbund bei hohen Temperaturen verkohlt. Dieses Verfahren wandelt das imprägnierte Material in Kohlenstoff um und verfestigt die Struktur weiter.
„Der Verdichtungsprozess beinhaltet oft mehrere Zyklen, um die Gleichmäßigkeit zu gewährleisten und die Variabilität in den Eigenschaften des Verbundes zu beseitigen. „
Es werden auch fortgeschrittene Techniken, wie z.B. Chemical Vapor Infiltration (CVI) oder Chemical Vapor Deposition (CVD) eingesetzt. Diese Methoden führen Kohlenstoff aus gasförmigen Vorläufern ein, lagern sie innerhalb des Verbundes ab. CVI und CVD verbessern die thermische und mechanische Leistung des Materials, wodurch es für extreme Umgebungen geeignet ist.
Die wiederholten Imprägnier- und Karbonisierungszyklen ermöglichen es den Herstellern, die Dichte und Festigkeit des Verbundes zu verfeinern. Diese Präzision sorgt dafür, dass das Material hohen Belastungen und Temperaturbedingungen standhält und es für Luft- und Industrieanwendungen unverzichtbar macht.
Endbearbeitung und Oberflächenbehandlung
Sobald die gewünschte Dichte und Festigkeit erreicht wird, wird der Verbund durch eine abschließende Bearbeitung und Oberflächenbehandlung durchgeführt. Diese Schritte verfeinern die Form des Materials und verbessern seine Oberflächeneigenschaften.
Schlichten und Aufbringen von Schutzbeschichtungen
Die Bearbeitung beinhaltet das Schneiden, Schleifen und Formen des Verbundes, um spezifische Konstruktionsanforderungen zu erfüllen. Hersteller verwenden fortschrittliche Werkzeuge und Techniken, um präzise Abmessungen und glatte Oberflächen zu erreichen. Dieser Schritt sorgt dafür, dass der Verbund nahtlos in seine bestimmungsgemäße Anwendung passt.
Nach der Bearbeitung werden Oberflächenbehandlungen angewendet, um den Verbund vor Umweltfaktoren zu schützen. Schutzbeschichtungen wie Siliziumkarbid oder Keramikschichten verbessern die Beständigkeit des Materials gegen Oxidation und Verschleiß. Diese Beschichtungen verlängern die Lebensdauer des Verbundes und halten seine Leistung unter harten Bedingungen.
„Die Oberflächenbehandlungen spielen eine entscheidende Rolle bei der Erhaltung der Integrität des Verbundes, insbesondere in Hochtemperatur- und korrosiven Umgebungen. „
Die Kombination aus Bearbeitung und Oberflächenbehandlung gewährleistet, dass der Verbund sowohl funktionale als auch ästhetische Standards erfüllt. Diese Finishing-Touchse präparieren das Material für den Einsatz in anspruchsvollen Branchen, wo Zuverlässigkeit und Haltbarkeit an erster Stelle stehen.
Durch den Abschluss der Verdichtungs- und Veredelungsprozesse schaffen die Hersteller kohlenstoff-verbundwerkstoff die in Festigkeit, Hitzebeständigkeit und Haltbarkeit übertrifft. Dieses fortschrittliche Material treibt die Innovation in den Bereichen Luft- und Raumfahrt, Automotive und anderen Hochleistungssektoren weiter voran.
Verstärkter Kohlenstoff-Kohlenstoff-Verbund entsteht als bahnbrechendes Material durch seine sorgfältige Herstellung. Durch die Herstellung von Kohlenstofffasern, die Schaffung der Kohlenstoffmatrix und die Verdichtung und Veredelung erreicht dieser Verbund eine unvergleichliche Festigkeit und thermische Beständigkeit. Seine Anwendungen erstrecken sich über Industrien wie Luft- und Raumfahrt, Motorsport und Tiefbau, wo Präzision und Haltbarkeit an erster Stelle stehen. Zum Beispiel, Motorsport nutzen dieses Material, um Gewicht zu reduzieren, unter Beibehaltung der strukturellen Integrität, Verbesserung der Leistung auf der Strecke. Das Verständnis der Schaffung von verstärktem Kohlenstoff-Kohlenstoff-Verbund unterstreicht die Innovation, die Fortschritte in der Technik und Technologie vorantreibt.
FAQ
Welche Formen der Kohlefaserverstärkung gibt es?
Kohlenstofffaserverstärkung besteht in mehreren Formen, die jeweils auf spezielle Anwendungen zugeschnitten sind. Gemeinsame Typen umfassen kohlenstofffaserverstärkte Polymere (CFRPs), die kohlenstofffasern mit einer polymermatrix für leichte und starke materialien kombinieren. Kohlefaserverbunde kohlenstofffasern mit verschiedenen matrizen integrieren und bieten vielseitigkeit in mechanischen und thermischen eigenschaften. Verstärkte Kohlenstoff-Kohlenstoff-Verbundwerkstoffe zeichnen sich durch ihre fähigkeit, extreme temperaturen zu ertragen, so dass sie ideal für luft- und hochleistungstechnik.
Wie unterscheidet sich verstärkter Kohlenstoff-Kohlenstoff-Verbund von anderen Kohlenstoff-Verbundwerkstoffen?
Verstärkter Kohlenstoff-Kohlenstoff-Verbund zeichnet sich durch seine einzigartige Kombination aus Kohlenstofffasern und einer Kohlenstoffmatrix aus. Diese Struktur bietet außergewöhnliche Wärmebeständigkeit und mechanische Festigkeit. Im Gegensatz zu anderen Kohlenstoff-Verbundwerkstoffen, die Polymer- oder Keramikmatrizen verwenden können, zeichnen sich verstärkte Kohlenstoff-Kohlenstoff-Verbunde in Hochtemperatur-Umgebungen wie Flugzeugbremsanlagen und Raketendüsen aus.
Warum ist der Karbonisierungsprozess in der Herstellung wesentlich?
Der Carbonisierungsprozess verwandelt Harz in Kohlenstoff, wodurch die robuste Kohlenstoffmatrix entsteht, die die Fasern bindet. Dieser Schritt sorgt dafür, dass der Verbund seine Hochtemperaturstabilität und mechanische Festigkeit erreicht. Ohne Karbonisierung würde das Material die für anspruchsvolle Anwendungen erforderliche Haltbarkeit und Leistung nicht ausreichen.
„Die Karbonisierung ist der Eckpfeiler der verstärkten Kohlenstoff-Kohlenstoff-Verbundproduktion, die es dem Material ermöglicht, extremen Bedingungen standzuhalten. „
Welche Branchen profitieren am meisten von verstärkten Kohlenstoff-Kohlenstoff-Verbundwerkstoffen?
Industrien, die Materialien mit hohen Festigkeits-zu-Gewichtsverhältnissen und thermischer Widerstandskraft benötigen, profitieren deutlich. Aerospace setzt auf diese Verbundwerkstoffe für Bauteile wie Hitzeschilde und Bremsscheiben. Motorsport nutzen sie, um das Fahrzeuggewicht zu reduzieren und gleichzeitig die strukturelle Integrität zu erhalten. Andere Sektoren, wie Halbleiter und Metallurgie, nutzen auch ihre fortschrittlichen Eigenschaften für spezialisierte Anwendungen.
Wie werden Kohlenstofffasern angeordnet, um strukturelle Integrität zu gewährleisten?
Hersteller arrangieren Kohlenstofffasern nach Methoden wie unidirektionale ausrichtung, weben oder geflechtund schichtung. Unidirektionale Ausrichtung maximiert die Festigkeit entlang einer einzigen Achse, während das Weben eine multidirektionale Haltbarkeit schafft. Die Schichtung gleicht Festigkeit und Steifigkeit in allen Richtungen aus. Diese Anordnungen gewährleisten, dass der Verbund den spezifischen Leistungsanforderungen entspricht.
Welche Rolle spielt Harz im Herstellungsprozess?
Harz wirkt als Vorstufe für die Kohlenstoffmatrix. Es sättigt die Kohlenstofffasern, wodurch eine gleichmäßige Struktur und starke Bindung entsteht. Während der Carbonisierung wandelt sich das Harz in Kohlenstoff um und bildet die Matrix, die die mechanischen und thermischen Eigenschaften des Verbundes verbessert. Harze wie Phenol und Epoxy werden häufig für ihre Wärmebeständigkeit und Stabilität verwendet.
Wie verbessert die Verdichtung die Eigenschaften des Verbundes?
Die Verdichtung beinhaltet wiederholte Zyklen der Imprägnierung und Karbonisierung. Diese Zyklen füllen die Poren innerhalb des Verbundes, erhöhen ihre Dichte und Festigkeit. Fortgeschrittene Techniken wie Chemische Vapor Infiltration (CVI) die Leistung des Materials durch Ablagerung von Kohlenstoff aus gasförmigen Vorläufern weiter verbessern. Dieses Verfahren gewährleistet, dass der Verbund hohe Belastungen und Temperaturbedingungen ertragen kann.
Welche Oberflächenbehandlungen werden auf verstärkte Kohlenstoff-Kohlenstoff-Verbundwerkstoffe angewendet?
Oberflächenbehandlungen schützen den Verbund vor Umweltfaktoren wie Oxidation und Verschleiß. Hersteller wenden Beschichtungen wie Siliziumkarbid or keramikschichten zur Verbesserung der Korrosionsbeständigkeit und hohen Temperaturen. Diese Behandlungen verlängern die Lebensdauer des Materials und halten seine Leistung unter harten Bedingungen.
Warum ist verstärkter Kohlenstoff-Kohlenstoff-Verbund teuer?
Der Herstellungsprozess umfasst mehrere präzise Schritte, einschließlich Carbonisierung, Verdichtung und Oberflächenbehandlung. Jeder Schritt erfordert fortschrittliche Technologie und Know-how und trägt zu den Kosten des Materials bei. Seine außergewöhnlichen Eigenschaften, wie Hitzebeständigkeit und Stärke, rechtfertigen jedoch die Investitionen für Industrien, die Hochleistungsmaterialien fordern.
Können verstärkte Kohlenstoff-Kohlenstoff-Verbundwerkstoffe für spezielle Anwendungen angepasst werden?
Ja, Hersteller können die Eigenschaften des Verbundes durch Anpassung von Faseranordnungen, Harztypen und Verdichtungszyklen anpassen. Die Individualisierung stellt sicher, dass das Material den einzigartigen Anforderungen von Anwendungen entspricht, sei es für den Luft- und Raumfahrt-, Motorsport- oder Industrieeinsatz. Diese Flexibilität unterstreicht die Vielseitigkeit und den Wert des Materials im fortgeschrittenen Engineering.