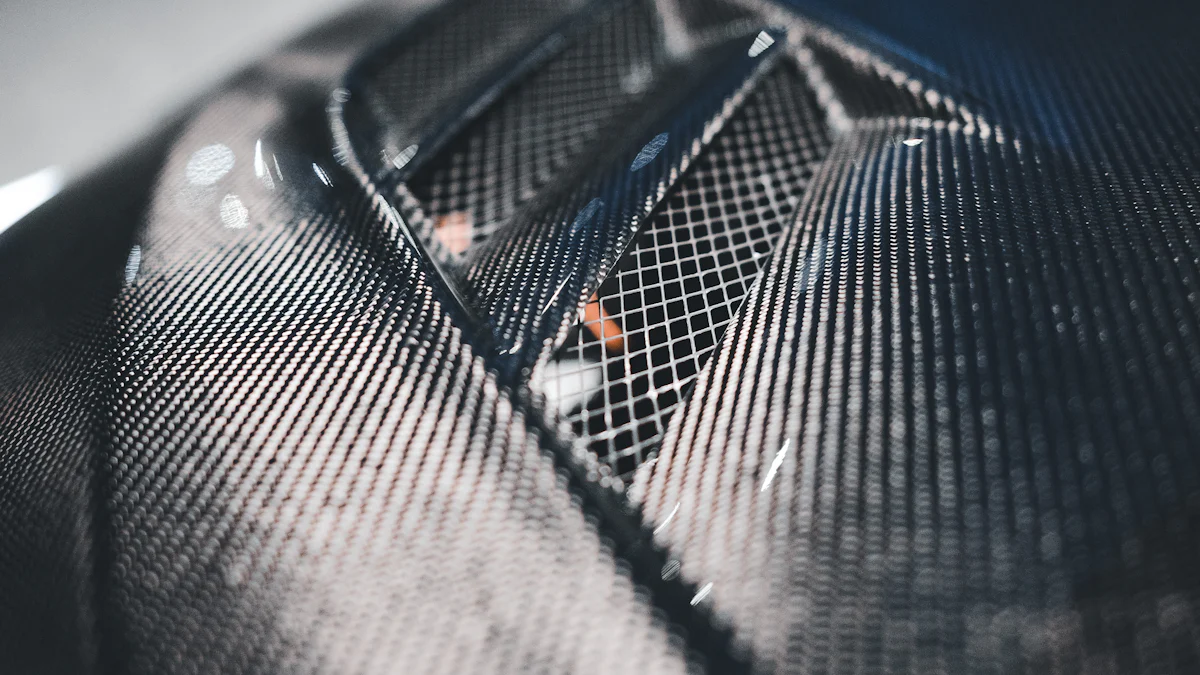
Kohlenstofffaser-Kohlenstoffplatten sind fortschrittliche Materialien aus Kohlenstofffasern, die in einer Kohlenstoffmatrix eingebettet sind. Diese Platten sind für ihre außergewöhnliches festigkeits-gewichtsverhältnis, korrosionsbeständigkeit und langfristige haltbarkeit. Ihre Leichtigkeit macht sie unverzichtbar in Industrien, die Hochleistungsmaterialien benötigen.
Zu den wichtigsten Eigenschaften gehören:
- Hohes Festigkeits-Gewichtsverhältnis, leichter noch stärker als Stahl.
- Korrosionsbeständigkeit, Gewährleistung der Langlebigkeit in rauen Umgebungen.
- Vielseitigkeit bei extremen Bedingungen, wie hohen Temperaturen oder Druck.
Anwendungen erstrecken sich über Luft-, Automobil- und Sportgeräte. Zum Beispiel, sie das flugzeuggewicht zu reduzieren und strukturelle integrität zu erhalten, verbessern kraftstoffeffizienz in fahrzeugen und schaffen leistungsstarke sportausrüstung.
Beim Herstellungsverfahren werden Kohlenstofffasern mit einem Harz oder einer Matrix geschichtet, das Material ausgehärtet und nachverarbeitende Schritte durchgeführt, um die gewünschte Form und Oberfläche zu erreichen. Dieser sorgfältige Prozess sorgt für die Produktion von hoher Qualität carbon carbon composites für vielfältige anwendungen.
Wichtigste Erkenntnisse
- Carbonfaser-Kohlenstoffplatten bieten eine überlegene Festigkeit-zu-Gewicht-Verhältnis, so dass sie ideal für anwendungen in der luft- und raumfahrt, automotive, und sportausrüstung.
- Die herstellungsprozess ist eine sorgfältige schichtung aus kohlenstofffasern mit harz, gefolgt von der aushärtung, um haltbarkeit und leistung zu gewährleisten.
- Qualitätskontrolle ist entscheidend; regelmäßige Inspektionen und mechanische Tests helfen, die Integrität und Zuverlässigkeit von Kohlefaserprodukten zu erhalten.
- Innovationen in der Automatisierung und fortschrittlichen Materialien treiben die Produktionskosten herunter und erweitern die Anwendungen von Kohlefaserplatten.
- Für DIY-Enthusiasten ist die Investition in richtige Werkzeuge und Sicherheitsgetriebe unerlässlich, um leistungsstarke Carbonfaserkomponenten zu schaffen.
Übersicht über Carbon Fiber Carbon Plates
Zusammensetzung und Eigenschaften
Carbon Fibers und Carbon Matrix
Kohlenstofffaser-Kohlenstoffplatten bestehen aus zwei Primärkomponenten: Kohlenstofffasern und einer Kohlenstoffmatrix. Kohlenstofffasern sind dünne Stränge von Kohlenstoffatomen, die in einer kristallinen Struktur miteinander verbunden sind und eine außergewöhnliche Zugfestigkeit und Steifigkeit bieten. Die Kohlenstoffmatrix, oft ein Harz oder Polymer, bindet diese Fasern zusammen, wodurch ein Verbundmaterial entsteht, das leicht und dennoch unglaublich langlebig ist. Diese Kombination führt zu einem wesentlich leichteren Material als Metalle wie Aluminium oder Stahl und bietet überlegene mechanische Eigenschaften.
Die einzigartige Zusammensetzung dieser Platten sorgt auch für Korrosionsbeständigkeit und Stabilität bei Temperaturschwankungen. Diese Eigenschaften machen sie ideal für anwendungen, die eine langfristige haltbarkeit erfordern und minimale wartung.
Key Features
Kohlenstofffaser Kohlenstoffplatten zeichnen sich durch ihre bemerkenswerten Eigenschaften aus:
- Gewichtsverhältnis: Diese Platten sind viel stärker als Stahl, während sie deutlich leichter sind, so dass sie ideal für gewichtsempfindliche Anwendungen.
- Wärmebeständigkeit: Sie halten strukturelle Integrität auch bei extremen Temperaturen, die für die Luft- und Raumfahrt und Raumexploration von entscheidender Bedeutung sind.
- Korrosionsbeständigkeit: Im Gegensatz zu Metallen widerstehen diese Platten Rost und chemischen Abbau, wodurch die Langlebigkeit in rauen Umgebungen gewährleistet ist.
- Fatigue Widerstand: Sie übertreffen traditionelle Materialien wie Stahl und Aluminium trotz wiederholter Beanspruchung ohne Ausfall.
Anwendungen
Luft- und Raumfahrt und Verteidigung
Kohlenstofffaser-Kohlenstoffplatten spielen eine wichtige Rolle in der Luftfahrt- und Verteidigungsindustrie. Aircraft-Komponenten wie Rumpfpaneele, Flügelholme und Schwanzabschnitte profitieren von ihrer Leichtigkeit und reduzieren das Gesamtgewicht von bis 75%. Diese Gewichtsreduktion verbessert die Kraftstoffeffizienz und Nutzlastkapazität. Bei Raumfahrzeugen werden diese Platten aufgrund ihrer außergewöhnlichen Wärmebeständigkeit und strukturellen Integrität unter extremen Bedingungen in Hitzeschilden und Antriebssystemen eingesetzt.
Automobil und Motorsport
Im Automobilbereich verbessern Kohlenstofffaser-Kohlenstoffplatten die Fahrzeugleistung durch Gewichtsreduzierung bis zu 60%. Diese Reduktion verbessert die Kraftstoffeffizienz um ca. 25% und ermöglicht schlankere, aerodynamischere Designs. Hochleistungsfahrzeuge, einschließlich Elektroautos, nutzen diese Platten, um die Lebensdauer der Batterie zu verlängern und die Sicherheit zu verbessern, indem sie Stoßenergie bei Kollisionen absorbieren. Ihre Steifigkeit erhöht auch die Stabilität bei Hochgeschwindigkeitsmanövern und macht sie im Motorsport unverzichtbar.
Industrielle und Sportgeräte
Branchen und Sportproduzenten nutzen Carbonfaserplatten für ihr Festigkeits-zu-Gewichtsverhältnis. In industriellen Anwendungen bieten sie dauerhafte Lösungen für Maschinen und Geräte, die extremen Bedingungen ausgesetzt sind. Sportartikel wie Fahrräder, Tennisschläger und Golfschläger nutzen diese Platten, um hohe Leistung ohne unnötiges Gewicht zu liefern. Ihre Fähigkeit, wiederholten Stress zu widerstehen, sorgt für Zuverlässigkeit und Langlebigkeit in anspruchsvollen Umgebungen.
Material und Ausrüstung für die Herstellung
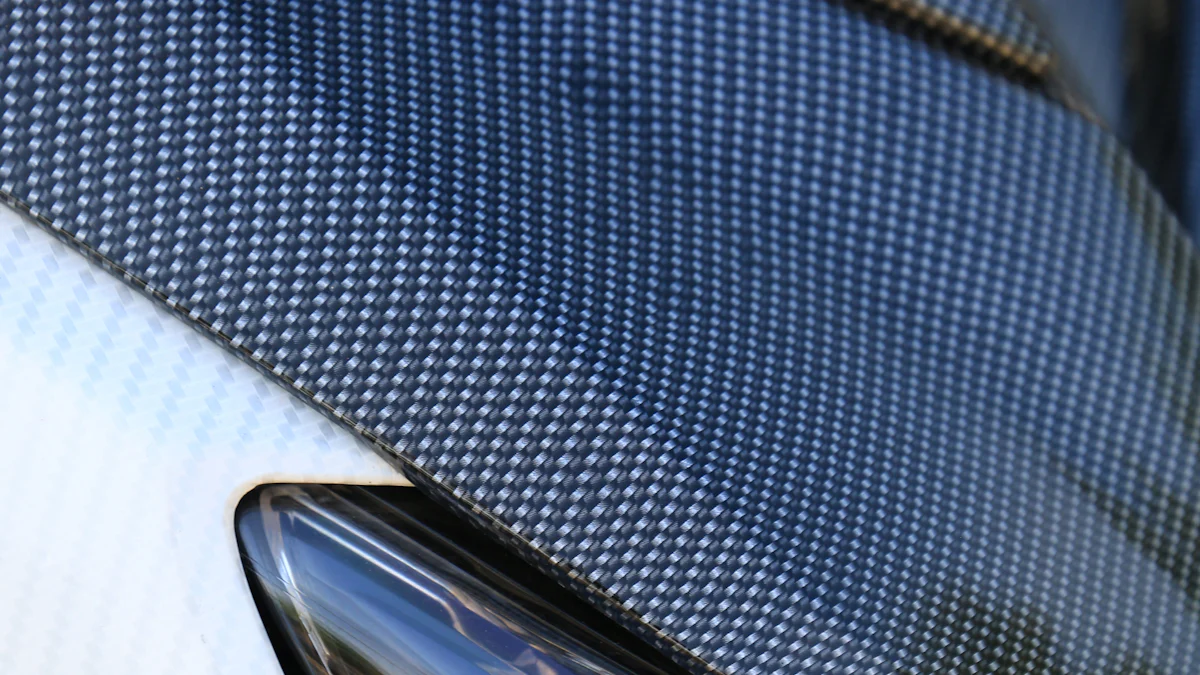
Material
Arten von Carbon Fibers
Kohlenstofffasern sind das Rückgrat von carbon fiber carbon plate produktion. Hersteller verwenden in erster Linie zwei arten von kohlenstofffasern, jedes bietet einzigartige eigenschaften und anwendungen:
Art der Kohlefaser | Rohmaterial | Merkmale | Anwendungen |
---|---|---|---|
PAN-basierte Kohlefaser | PAN (Polyacrylnitril) | Hohe Zugfestigkeit, hoher elastischer Modul | Luft- und Raumfahrt, Industriefelder, Sportprodukte |
Pitch-basierte Kohlefaser | Öl- und Kohlestich | Varianten von niedrigem bis ultrahochelastischem Modul, hohe thermische/elektrische Leitfähigkeit | Hohe Steifigkeitskomponenten, spezialisierte Anwendungen |
PAN-basierte Fasern dominieren aufgrund ihrer überlegenen Festigkeit und Vielseitigkeit, während Pitch-basierte Fasern in Anwendungen mit hoher Steifigkeit oder Leitfähigkeit ausgezeichnet sind.
Harze und Matrixmaterialien
Harze binden Kohlenstofffasern zusammen und bilden eine robuste Verbundstruktur. Üblicherweise verwendete Harze sind:
Resin | Pros | Negativ | Heilung |
---|---|---|---|
Epoxyd | Höchste Festigkeit, leichte, lange Haltbarkeit | Aufwändig, empfindlich auf Temperaturschwankungen | Erfordert spezifische Härter, oft wärmegehärtet |
Polyester | Einfach zu bedienen, UV-beständig, kostengünstig | Niedrige Festigkeit, begrenzte Korrosionsbeständigkeit | Härtungen mit einem Katalysator (MEKP) |
Vinylester | Kombiniert die Leistung von Epoxy mit den Kosten von Polyestern | Niedrigere Festigkeit als Epoxy, höhere Kosten als Polyester | Härtungen mit einem Katalysator (MEKP) |
Epoxidharze werden aufgrund ihrer Festigkeit und Haltbarkeit für Hochleistungsanwendungen bevorzugt.
Additive für verbesserte Eigenschaften
Additive verbessern die Leistungsfähigkeit von Kohlefaserplatten. Zu den üblichen Zusatzstoffen gehören:
- Nanopartikel: Verbesserung der Wärme- und elektrischen Leitfähigkeit.
- Flammschutzmittel: Feuerwiderstand erhöhen.
- UV Stabilisatoren: Schutz vor Sonneneinstrahlung.
Diese Additive maßen die Materialeigenschaften an, um den spezifischen Anforderungen der Industrie gerecht zu werden.
Ausrüstung
Molds und Lay-Up Tools
Formkörper formen die Kohlefaserschichten in die gewünschte Form. Lay-up-Werkzeuge unterstützen die Anordnung der Fasern in präzisen Orientierungen und optimieren die mechanischen Eigenschaften des Endproduktes.
Autoklaven und Öfen
Autoklaven und Öfen spielen eine wichtige Rolle in aushärten von kohlenstofffaserplatten:
- Autoklaven wenden kontrollierte Wärme und Druck an, wodurch eine gleichmäßige Verklebung und Eliminierung von Leerstellen gewährleistet wird.
- Öfen regulieren den Luftstrom, um konstante Temperaturen zu halten, Fehler wie Blasen oder unvollständige Aushärtung zu verhindern.
Die richtige Aushärtung erhöht die Festigkeit und Haltbarkeit des Verbundmaterials.
Schneid- und Fertigwerkzeuge
Genaue Schneidwerkzeuge sorgen für präzise Abmessungen von Kohlefaserplatten. Finishing-Tools verfeinern die Kanten und Oberflächen, die Platten für Endanwendungen vorzubereiten. Diese Werkzeuge tragen zur Gesamtqualität und Leistungsfähigkeit des fertigen Produktes bei.
Schritt für Schritt Fertigungsprozess
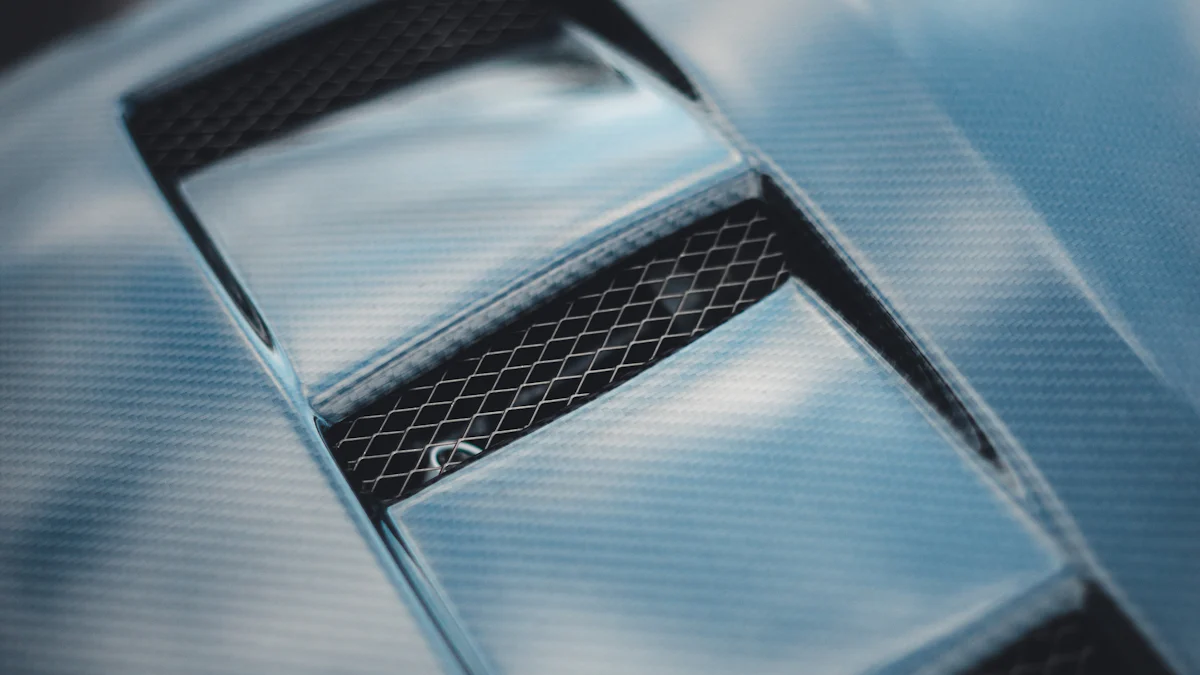
Herstellung der Materialien
Carbon Fiber Production und Carbonization
Die Herstellung von Kohlenstofffasern beginnt mit als vorläufer bekannter polymerer einsatzstoff, typischerweise Polyacrylnitril (PAN). Der Prozess beinhaltet mehrere Schlüsselschritte:
- Precursorpräparation: Die Vorstufe wird durch Vermischen mit anderen Materialien hergestellt.
- Spinning: Die Mischung wird in fasern versponnen, die grundstruktur bildet.
- Stabilisierung: Die Fasern werden chemisch verändert, um die thermische Stabilität zu verbessern.
- Karbonisierung: Die Fasern sind auf Temperaturen zwischen 1000°C und 3,000°C erhitzt in einer sauerstofffreien Umgebung. Dieser Schritt entfernt nicht-Kohlenstoffatome und lässt dicht gebundene Kohlenstoffketten.
- Surface Treatment: Die Fasern werden zur Verbesserung der Haftung mit dem Matrixharz behandelt.
Dieses Verfahren gewährleistet die strukturelle Integrität und hohe Leistung der in carbon fiber carbon plate herstellung.
Herstellung des Harzes oder der Matrix
Das Harz oder Matrixmaterial bindet die Kohlenstofffasern zusammen und bildet einen Verbund. Hersteller wählen den Harztyp anhand der Anwendungsanforderungen sorgfältig aus. Das Herstellungsverfahren umfasst:
- Um die korrektes verhältnis von harz zu härter für eine optimale aushärtung.
- Mischadditive, wie Flammschutzmittel oder UV-Stabilisatoren, zur Verbesserung spezifischer Eigenschaften.
- Eine gleichmäßige Konsistenz zur Vermeidung von Defekten bei der Schichtung.
Layering und Shaping
Wet Lay-Up Methode
Das nasse Auflegeverfahren beinhaltet das manuelle Auftragen von Harz auf Kohlefaserschichten. Diese Technik führt typischerweise zu einem Faser-Harz-Verhältnis von 40:60, wodurch der Verbund schwerer, aber für weniger gewichtsempfindliche Anwendungen geeignet ist. Es ist kostengünstig und ideal für kleine Produktion.
Preprepretation
Prepreg-Lamination verwendet vorimprägnierte Kohlefaserplatten mit einem kontrollierten Harzgehalt. Dieses Verfahren erreicht a faser-zu-harz-verhältnis von etwa 60:40, die Herstellung leichterer und stärkerer Verbundstoffe. Die Schichten werden in Formen gestapelt und sorgen für eine präzise Ausrichtung für optimale mechanische Eigenschaften.
Infusions-Prozess
Bei dem Harzinfusionsverfahren werden trockene Kohlenstofffasern in eine Form gegeben und anschließend Harz unter Vakuumdruck eingebracht. Dieses Verfahren erreicht auch ein Faser-Harz-Verhältnis von 60:40. Es minimiert Leerstellen und sorgt für gleichbleibende Qualität, so dass es für leistungsstarke Anwendungen geeignet ist.
Heilung und Verfestigung
Autoclave Curing
Die Autoklavenhärtung wendet Wärme und Druck auf das Schichtmaterial an. Dieses Verfahren eliminiert Lufttaschen und sorgt für eine gleichmäßige Verbindung zwischen Kohlenstofffasern und Harz. Die kontrollierte Umgebung erhöht die Festigkeit und Haltbarkeit der letzten Carbonfaserplatte.
Ofen Aushärten
Bei der Ofenhärtung wird das Verbundmaterial in einer geregelten Luftstromumgebung erwärmt. Dieses Verfahren ist weniger teuer als die Autoklavenhärtung und wird oft für größere Komponenten verwendet. Eine ordnungsgemäße Temperaturregelung verhindert Fehler wie unvollständiges Aushärten oder Harzblasen.
Nachbearbeitung
Schneiden und Schneiden
Trimmen und Schneiden sind wesentliche Schritte bei der Nachbearbeitung von Kohlefaserplatten. Diese Prozesse verfeinern die Abmessungen und Kanten des Materials, so dass es präzise Spezifikationen erfüllt. Aufgrund der hohen Festigkeit und Härte der Kohlefaser verlassen sich die Hersteller auf spezialisierte Werkzeuge wie diamant-beschichtete schneidwerkzeuge und hartmetallbohrer. Diese Werkzeuge minimieren Verschleiß und halten Genauigkeit während des Betriebs.
Ebenso wichtig ist die Steuerung der Verarbeitungsparameter. Die Einstellung von Schnittgeschwindigkeit, Vorschubgeschwindigkeit und Schnitttiefe verhindert Defekte wie Delaminierung oder Reißen. Die Betreiber müssen diese Parameter genau überwachen, um saubere Schnitte zu erzielen und die strukturelle Integrität des Materials zu erhalten. Die richtige Handhabung während dieser Stufe sorgt dafür, dass die Kohlefaserplatte ihre mechanischen Eigenschaften und ästhetischen Reiz behält.
Oberflächenbehandlung und Beschichtung
Oberflächenbehandlung verbessert das Aussehen und die Leistung von Kohlefaserplatten. Dieser Schritt beginnt oft mit dem Polieren, das die Oberfläche glättet und alle Unvollkommenheiten aus dem Härtungsprozess entfernt. Polierte Oberflächen verbessern nicht nur die visuelle Reiz des Materials, sondern bereiten sie auch auf spätere Beschichtungen vor.
Beschichtungsanwendungen bieten zusätzlichen Schutz und Funktionalität. Hersteller verwenden Schutzschichten, um das Material vor Umweltfaktoren wie UV-Strahlung, Feuchtigkeit und chemischer Exposition zu schützen. Diese Beschichtungen verlängern die Lebensdauer des Produktes und halten seine Leistung bei anspruchsvollen Bedingungen. In einigen Fällen werden funktionale Beschichtungen, wie antistatische oder hitzebeständige Schichten, den spezifischen Anforderungen der Industrie zugesetzt.
Durch die Kombination von präzisen Schneid-, Schneid- und Oberflächenbehandlungen stellen Hersteller sicher, dass das Endprodukt höchsten Qualitätsstandards entspricht. Diese Nachbearbeitungstechniken spielen eine entscheidende Rolle bei der Bereitstellung von langlebigen und zuverlässigen Kohlefaserkomponenten für verschiedene Anwendungen.
Qualitätskontrolle und Fertigstellung
Inspektion und Prüfung
Visuelle Inspektion für Defekte
Visuelle Inspektion dient als erste Verteidigungslinie in der Qualitätskontrolle. Techniker untersuchen die Kohlefaserplatten für Oberflächenunregelmäßigkeiten, wie Risse, Hohlräume oder Delaminierung. Dieser Schritt stellt sicher, dass das Material ästhetische und strukturelle Standards erfüllt, bevor es auf fortgeschrittene Tests geht. Regelmäßige Inspektionen während der Herstellung helfen, Fehler frühzeitig zu identifizieren, Abfall zu reduzieren und gleichbleibende Qualität zu gewährleisten.
In-Service-Inspektionen und Wartung spielen auch eine wichtige Rolle im Lifecycle Management. Diese Inspektionen überwachen den Zustand von Kohlefaserkomponenten im Laufe der Zeit und gewährleisten ihre Zuverlässigkeit in anspruchsvollen Anwendungen. Schadensbeurteilungen nach Vorkommnissen, wie Auswirkungen oder extremen Stress, helfen zu bestimmen, ob Reparaturen oder Ersatz notwendig sind.
Mechanische Prüfung (z.B. Zugfestigkeit, thermische Beständigkeit)
Mechanische Tests bewerten die Leistung von Kohlefaserplatten unter verschiedenen Bedingungen. Gemeinsame Methoden umfassen:
- Ultraschallprüfung: Erkennt interne Fehler, indem er Schallwellen durch das Material sendet.
- Röntgenprüfung: Erkennt versteckte Defekte, wie Leerstellen oder Risse, mit bildgebender Technologie.
- Sensorüberwachung: Verfolgen Sie Temperatur- und Druckänderungen während des Gebrauchs, so dass das Material wie erwartet auskommt.
Diese Tests messen kritische Eigenschaften wie Zugfestigkeit, thermische Beständigkeit und Ermüdungsleistung. Durch die Kombination dieser Techniken stellen Hersteller sicher, dass jede Platte Industriestandards für Sicherheit und Haltbarkeit erfüllt.
Surface Finishing
Polieren und Beschichten
Die Polierung verbessert das Aussehen und die Glätte der Kohlefaserplatten. Dieser Prozess entfernt Oberflächenunvollkommenheiten, wodurch ein einheitliches Finish, das sowohl Ästhetik als auch Funktionalität verbessert. Nach dem Polieren gelten Hersteller beschichtungen zum schutz des materials aus umweltfaktoren.
Beschichtungen dienen mehreren Zwecken, darunter UV-Schutz, Feuchtigkeitsbeständigkeit und chemische Abschirmung. Spezialisierte Oberflächenvorbereitung sorgt für eine starke Haftung zwischen der Beschichtung und der Kohlefaser. Bei der Galvanisierung wird beispielsweise die Platte in eine Elektrolytlösung eingetaucht und ein Gleichstrom zur Abscheidung einer Schutzmetallschicht aufgebracht. Nachbehandlungen, wie Spülen und Aushärten, verbessern die Haltbarkeit weiter.
Schutzschichten für Langlebigkeit
Schutzschichten die lebensdauer von kohlefaser verlängern platten, indem sie sie vor Verschleiß schützen. Die Wahl der Oberfläche hängt von der Anwendung ab:
Ausführung | Beschreibung | Durability | Anwendungen |
---|---|---|---|
Matte Finish | Niedrige Porosität, versteckt Fingerabdrücke, Kratzer weniger sichtbar | Gut haltbar | Geeignet für die meisten Anwendungen |
Gloss Finish | Glatte reflektierende Optik, zeigt Unvollkommenheiten im Laufe der Zeit | Weniger langlebig | Empfohlen für kosmetische Anwendungen |
Matte Finishes sind ideal für industrielle und funktionale Anwendungen, Glanzlacke passen zu kosmetischen Anwendungen. Durch die Auswahl des passenden Finishs stellen Hersteller sicher, dass die Platten sowohl Leistungs- als auch ästhetische Anforderungen erfüllen.
Herausforderungen und Innovationen in der Fertigung
Gemeinsame Herausforderungen
Hohe Herstellungskosten
Die Herstellung von Kohlefaser-Kohlenstoffplatten beinhaltet erhebliche Kosten, die ihre Annahme in der Industrie begrenzen können. Mehrere Faktoren tragen zu diesen hohen Kosten bei:
- Der Luft- und Raumfahrtsektor wertet die Kosten des Materials gegen seine leistungsvorteile, wie verbesserte kraftstoffeffizienz und erweiterte flugreichweite.
- In der industriellen Automatisierung wiegen Ingenieure den Kosten von Kohlefaser gegen Vorteile wie schnellere Produktionsgeschwindigkeiten und reduzierten Maschinenverschleiß.
- Materialauswahl erfordert oft Ausgleichskosten mit Leistungsgewinnen, was die Erschwinglichkeit zu einer kritischen Betrachtung macht.
Trotz dieser Herausforderungen investieren die Industrien weiterhin in Kohlefaser aufgrund seines unvergleichlichen Festigkeits-zu-Gewicht-Verhältnisses und seiner Haltbarkeit.
Komplexität des Verfahrens
Das Herstellungsverfahren für Kohlefaser-Kohlenstoffplatten ist aufwendig und erfordert in jedem Stadium Präzision. Von der Karbonisierung bis zur Aushärtung verlangt jeder Schritt spezielle Ausrüstung und Know-how. Fehler bei der Schichtung oder Aushärtung können zu Defekten wie Leerstellen oder Delaminierungen führen, die die Leistung des Materials beeinträchtigen. Diese Komplexität erhöht die Produktionszeit und die Kosten, so dass es für die Hersteller wichtig ist, fortschrittliche Techniken zu übernehmen, um den Betrieb zu optimieren.
Innovationen
Automatisierung und Robotik
Automatisierung und Robotik verwandeln die Produktion von Kohlefaser-Kohlenstoffplatten durch effizienz und präzision steigern. Zu den wichtigsten Fortschritten gehören:
- Automatisierte Fiber Placement (AFP), die Ablagerungen über 100 pfund material pro stunde, deutlich steigende produktionsraten.
- Leichte Roboterendeffektoren, die Geschwindigkeit und Genauigkeit verbessern und Motor- und Aktuatorlasten reduzieren.
- Anlagen, die Automatisierung nutzen, erreichen schnellere Reaktionszeiten, geringere Produktionskosten und verbesserte zuverlässigkeit bei fertigungsprozessen.
Diese Innovationen ermöglichen es den Herstellern, qualitativ hochwertige Platten zu reduzierten Kosten zu produzieren und sie für verschiedene Anwendungen zugänglich zu machen.
Erweiterte Materialien und Techniken
Neue Entwicklungen in Materialien und Techniken verbessern die Eigenschaften von Kohlenstofffaser-Kohlenstoffplatten. Zum Beispiel:
- Produkt von Carbitex CX6 verwendet ein speziell entwickeltes Bindemittel, um die Flexibilität von Kohlefaserlaminaten zu verbessern, ohne die Zugfestigkeit zu beeinträchtigen. Diese Innovation hat sich bei hochpräzisen Anwendungen wie Schuhkomponenten bewährt, bei denen der Krafttransfer kritisch ist.
- Carbon faserverstärkte Polyetheretherketone (CFR-PEEK)-Platten bieten leichte, biokompatible Lösungen für medizinische Geräte. Ihre Radioluzenz sorgt für eine klare Abbildung, während ihre Haltbarkeit die langfristigen Kosten reduziert.
Diese Fortschritte erweitern die potenziellen Anwendungen von Kohlenstofffaser-Kohlenstoffplatten und machen sie unverzichtbar in Industrien wie Luft- und Raumfahrt, Automotive und Healthcare.
Herstellung kohlenstofffaserplatten beinhaltet einen sorgfältigen Prozess, der qualitativ hochwertige Ergebnisse sicherstellt. Zu den wichtigsten Schritten gehören herstellung von prepre-materialien, Optimierung von Aushärtungsparametern und Durchführung von Echtzeit-Qualitätskontrolle zur Erkennung von Defekten. Nachbearbeitung, wie Beschneiden und Oberflächenbehandlung, erfordert präzise Werkzeuge und Techniken, um die Integrität des Materials zu erhalten.
Die Qualitätskontrolle spielt eine entscheidende Rolle, um die Leistung und Zuverlässigkeit dieser Platten zu gewährleisten. Für hochfeste Anwendungen sind präzise Harz-Faser-Verhältnisse und gleichmäßige Imprägnierung unerlässlich. Die Echtzeit-Überwachung während der Aushärtung verbessert die Qualität durch frühzeitige Identifizierung potenzieller Fehler.
Innovation treibt Fortschritte in diesem Bereich weiter voran. Nachhaltige Produktionsmethoden und fortschrittliche Recyclingtechniken machen diese Materialien zugänglicher. Bei der Entwicklung von Industrien werden Carbonfaserplatten an der Spitze technologischer und nachhaltiger Lösungen bleiben.
Für diejenigen, die daran interessiert sind, ihre eigenen Projekte zu starten, stehen Ressourcen wie richtige Schneidwerkzeuge, Sicherheitsgetriebe und Klebeoptionen zur Verfügung. Durch die Nutzung dieser Werkzeuge können Einzelpersonen helfen, dauerhafte und leistungsstarke Komponenten für verschiedene Anwendungen zu schaffen.
Die Vielseitigkeit und Haltbarkeit von Kohlefaserplatten machen sie in der Industrie unverzichtbar. Durch die Beherrschung des Herstellungsprozesses und die Einbindung von Innovation können Leser das volle Potenzial dieses bemerkenswerten Materials freischalten.
FAQ
Was sind Kohlenstofffaser-Kohlenstoffplatten aus?
Kohlefaserplatten besteht aus Kohlenstofffasern, die in einer Kohlenstoffmatrix eingebettet sind. Die Fasern bieten Festigkeit und Steifigkeit, während die Matrix sie zusammen bindet, wodurch ein leichtes, aber langlebiges Verbundmaterial, das für Hochleistungsanwendungen geeignet ist.
Wie werden Kohlenstofffaser-Kohlenstoffplatten in der Luft- und Raumfahrt verwendet?
In der Luft- und Raumfahrt reduzieren diese Platten das Flugzeuggewicht unter Beibehaltung der strukturellen Integrität. Sie sind verwendet in rumpfplatten, flügelholme und hitzeschilde, verbesserung der kraftstoffeffizienz und leistung unter extremen bedingungen.
Was ist der Unterschied zwischen PAN-basierten und Pitch-basierten Kohlenstofffasern?
PAN-basierte Fasern bieten hohe Zugfestigkeit und Vielseitigkeit, so dass sie ideal für allgemeine Anwendungen. Pitch-basierte Fasern bieten eine überlegene Steifigkeit und Wärmeleitfähigkeit, die spezialisierte Anwendungen wie hochpräzise Komponenten passen.
Warum ist die Aushärtung im Herstellungsprozess wichtig?
Die Aushärtung erstarrt das Harz und verbindet es mit den Kohlenstofffasern. Dieser Schritt sorgt dafür, dass der Verbund seine gewünschte Festigkeit, Haltbarkeit und Beständigkeit gegenüber Umweltfaktoren wie Hitze und Feuchtigkeit erreicht.
Kann Kohlefaser Kohlenstoffplatten recycelt werden?
Ja, Recyclingmethoden wie Pyrolyse wiederherstellen Kohlenstofffasern aus gebrauchten Verbunden. Diese Fasern können in weniger anspruchsvollen Anwendungen wiederverwendet werden, Nachhaltigkeit fördern und Abfall in Fertigungsprozessen reduzieren.