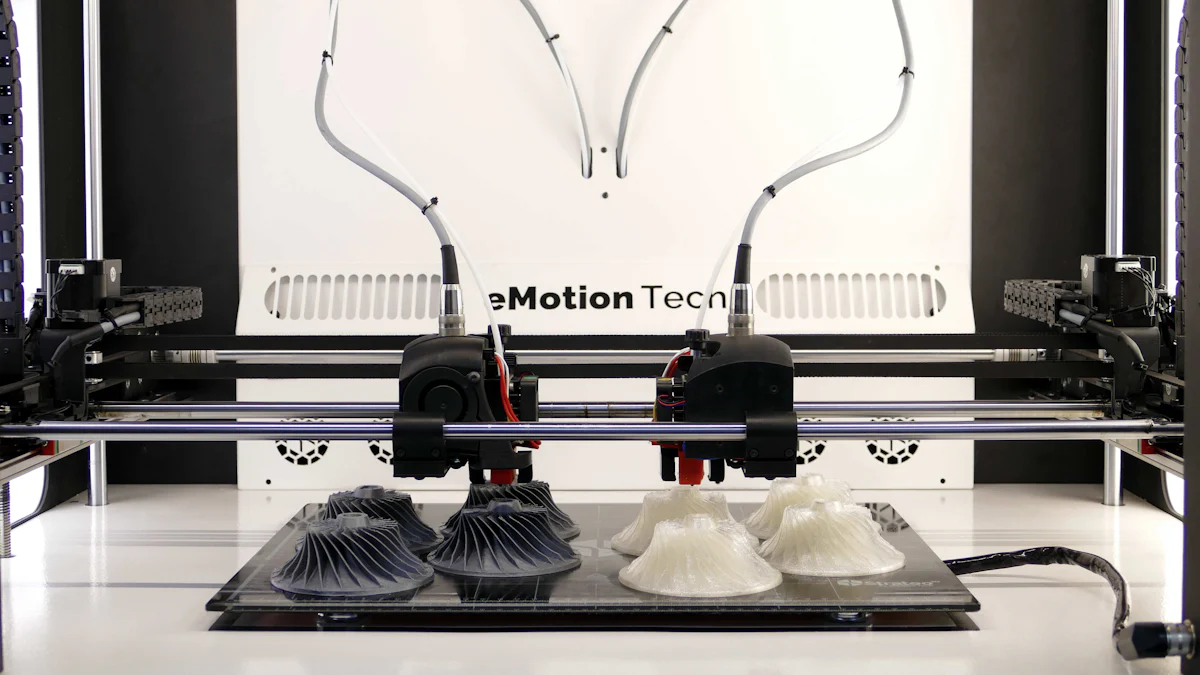
The demand for hochreine siliziumkarbidbeschichtung hat sich über Branchen wie Halbleiter, Luft- und Raumfahrt und erneuerbare Energien hinweg entwickelt. Der globale Markt, geschätzt bei Im Jahr 2023 werden 765 Mio. USD prognostiziert, um bis 2032 2,31 Mrd. USD zu erreichen. Dieses Wachstum resultiert aus seinen außergewöhnlichen Eigenschaften wie geringe dichte, hohe festigkeit, und Korrosionsbeständigkeit in extremen Umgebungen. Zum Beispiel, SIC coating für die halbleiterherstellung wesentlich ist, wobei silicon carbide coated susceptors spielen aufgrund ihrer thermischen Stabilität eine entscheidende Rolle. Produktdifferenzen verstehen sichert Branchen auswählen sic coated susceptors und beschichtungen, die spezifischen leistungs- und haltbarkeitsanforderungen entsprechen.
Wichtigste Erkenntnisse
- Rein Siliziumkarbid-Beschichtungen sind wichtig für industrien wie halbleiter, raum und saubere energie wegen ihrer großen eigenschaften.
- Diese Beschichtungen sind sehr hart, griff wärme gut, und widerstehen rost, so dass sie perfekt für harte bedingungen.
- Die Wahl der richtigen Beschichtung bedeutet, zu wissen, wie es Wärme, Chemikalien und Verschleiß behandelt.
- Kosten Materie; reine Beschichtungen kosten zunächst mehr, aber länger, Geld sparen im Laufe der Zeit.
- Die Verwendung und Pflege für diese Beschichtungen hilft ihnen, länger in Fabriken zu halten.
- Spezielle Methoden wie Chemical Vapor Deposition (CVD) machen Beschichtungen rein und sogar, Verbesserung der Funktionsweise.
- Benutzerdefinierte Beschichtungen können auf spezielle Bedürfnisse angepasst werden, so dass sie für bestimmte Arbeitsplätze besser funktionieren.
- Sicherheit und Umwelt sind wichtig; diese Beschichtungen sind in der Regel sicher und reduzieren Abfall und Verschmutzung.
Übersicht der hochwirksamen Silicon Carbide Beschichtungen
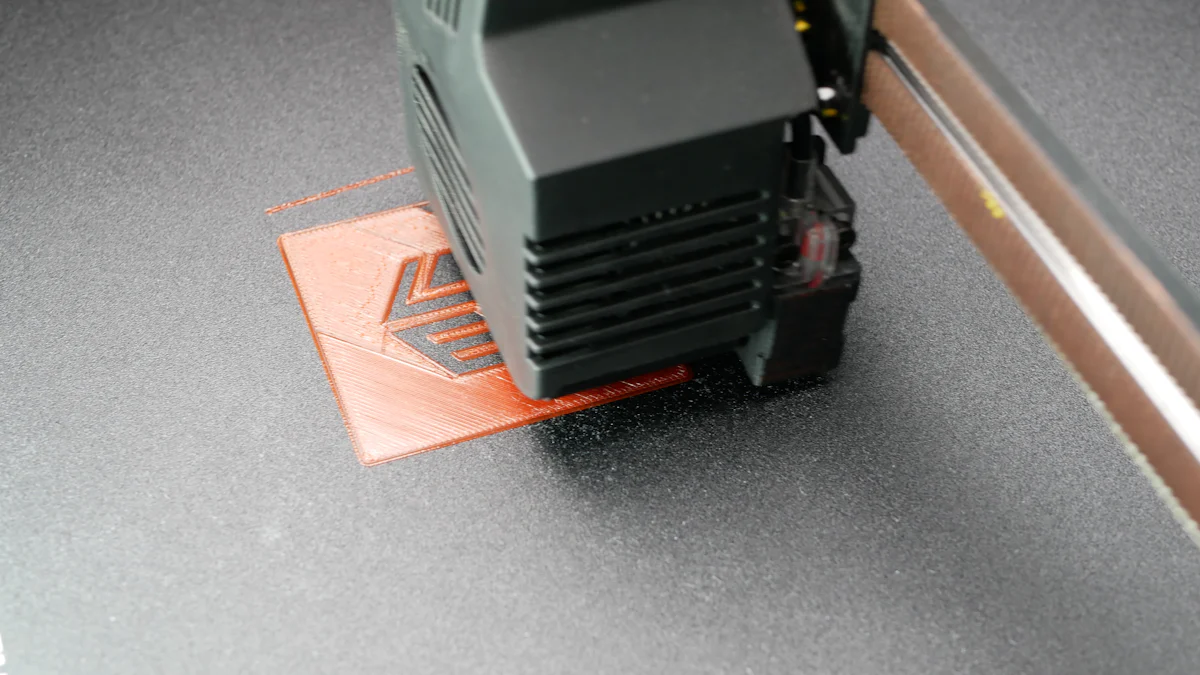
Was sind High-Purity Silicon Carbide Beschichtungen?
Hochreine Siliziumkarbidbeschichtungen werden erweitert schutzschichten entwickelt, um die Leistung und Haltbarkeit von industriellen Komponenten zu verbessern. Diese Beschichtungen bestehen aus Siliziumkarbid, einer für seine außergewöhnliche Härte und thermische Stabilität bekannten Verbindung. Die einzigartigen Eigenschaften des Materials machen es ideal für Anwendungen, die eine Beständigkeit gegen extreme Temperaturen, Korrosion und Verschleiß erfordern.
Um seine definierenden Merkmale besser zu verstehen, beachten Sie die folgende Tabelle:
Eigentum | Wert |
---|---|
Dichte | 3200 kg |
Kristallstruktur | 3C (kubisch; β) |
Porosität | 0% (Heliumleck dicht) |
Größe | 1 bis 5 μm |
Visuelle Erscheinung | Grau, Satin zu langweilig |
Wärmeausdehnung (RT -400°C) | 4,2 x 10-6m.K-1 |
Wärmeleitfähigkeit (@20°C) | 200 W.m-1.K-1 |
Elastisches Modul | 450GPa |
Elektrische Widerstandsfähigkeit (@20°C) | 1MΩ.m |
Diese Beschichtungen sind nicht nur optisch deutlich, sondern auch sehr anpassbar, mit einstellbaren Kristallgrößen und Oberflächenrauhigkeit, um spezifische industrielle Anforderungen zu erfüllen.
Schlüsseleigenschaften und Vorteile
Die Vorteile von hochreinen Siliziumkarbidbeschichtungen ergeben sich aus ihren bemerkenswerten Eigenschaften. Diese Beschichtungen weisen eine außergewöhnliche Härte, Korrosionsbeständigkeit und die Beständigkeit gegen hohe Temperaturen auf. Sie bieten auch hohe dichte, die Korrosionsbeständigkeit erhöht und die Lebensdauer der Bauteile verlängert. Ihre ausgezeichnete Abdeckung sorgt für gleichmäßige Dicke, auch in schwer zugänglichen Bereichen.
So wirken Siliciumcarbidbeschichtungen als Schutzbarriere, was die Haltbarkeit von Stahlbauteilen deutlich verbessert. Dies macht sie in rauen Industrieumgebungen unschätzbar. Zusätzlich, ihre geringe dichte und hohe festigkeit bieten strukturelle Integrität, während Gewicht zu minimieren. Diese Eigenschaften machen sie unverzichtbar in Industrien wie Luft- und Raumfahrt und erneuerbare Energien.
Gemeinsame Anwendungen Across Industries
Semiconductor Manufacturing
Bei der Halbleiterherstellung spielen hochreine Siliziumkarbidbeschichtungen eine entscheidende Rolle. Sie werden in Suszeptoren und anderen Komponenten verwendet, die eine außergewöhnliche thermische Stabilität erfordern. Diese Beschichtungen gewährleisten eine präzise Temperaturregelung bei der Waferverarbeitung, was für die Herstellung hochwertiger Halbleiter von entscheidender Bedeutung ist.
Luft- und Raumfahrt und Verteidigung
Die luft- und raumfahrt sektoren verlassen sich auf diese Beschichtungen für ihre unübertroffene Härte und thermische Stabilität. Komponenten wie Übergewichte und Raketennasekegel profitieren von ihrer Fähigkeit, extremen Bedingungen standzuhalten. Seit den 1980er Jahren sind diese Beschichtungen integraler Bestandteil von Luft- und Raumfahrtfortschritten.
Erneuerbare Energiesysteme
Erneuerbare Energiesysteme wie Solarpaneele und Windenergieanlagen nutzen hochreine Siliziumkarbidbeschichtungen für ihre Haltbarkeit und Beständigkeit gegenüber Umweltfaktoren. Diese Beschichtungen schützen Bauteile vor Verschleiß und Korrosion und gewährleisten eine langfristige Effizienz und Zuverlässigkeit.
Weitere aufstrebende Anwendungen
Über die traditionellen Branchen hinaus finden diese Beschichtungen Verwendung in medizinischen Geräten, Automobilkomponenten und Leistungselektronik. So verbessern sie beispielsweise die Leistung von chirurgischen Instrumenten und Implantaten durch ihre Biokompatibilität und Stärke. Im Automobilbereich verbessern sie die Haltbarkeit von Fahrzeugteilen. Leistungselektronik profitieren von der Anwendung in Halbleiter- und Industriekomponenten.
Schlüsselkriterien für Vergleich
Performance Metrics
Thermal Resistance
Die thermische Beständigkeit ist bei der Auswertung hochreiner Siliziumkarbidbeschichtungen ein entscheidender Faktor. Diese Beschichtungen zeichnen sich durch Hochtemperatur-Umgebungen aus, wobei Temperaturen bis 1600°C standhalten. Dies macht sie ideal für Anwendungen im Halbleiterbau und in der Luft- und Raumfahrt, wo Bauteile extremer Hitze ausgesetzt sind. Ich habe festgestellt, dass ihre Fähigkeit, Strukturintegrität unter solchen Bedingungen zu erhalten, eine gleichbleibende Leistung und Zuverlässigkeit gewährleistet.
Chemical Stability
Die chemische Stabilität bestimmt, wie gut eine Beschichtung in aggressiven Umgebungen ausführt. Hochreine Siliziumkarbidbeschichtungen, insbesondere solche mit β-SiC, bleiben auch bei hochkorrosiven Bedingungen stabil. Diese Stabilität gewährleistet Zuverlässigkeit in Industrien wie erneuerbarer Energie, wo Komponenten harten Chemikalien ausgesetzt sind. Die nachstehende Tabelle verdeutlicht die Auswirkungen der chemischen Stabilität und verschleißfestigkeit auf leistung:
Eigentum | Auswirkungen auf die Leistung |
---|---|
Abnutzungswiderstand | β-SiC weist eine höhere Härte und Verschleißfestigkeit auf, was die Haltbarkeit bei Anwendungen verbessert. |
Chemical Stability | β-SiC bleibt unter aggressiven Bedingungen stabil und sorgt für Zuverlässigkeit in verschiedenen Umgebungen. |
Wear and Abrasion Resistance
Verschleißfestigkeit ist ein weiteres herausragendes Merkmal dieser Beschichtungen. Ihre außergewöhnliche Härte, die auf β-SiC zurückzuführen ist, erhöht die Haltbarkeit bei anspruchsvollen Anwendungen. So profitieren beispielsweise Bauteile in Luft- und Raumfahrt und Verteidigung von dieser Eigenschaft, da sie den Verschleiß reduziert und die Lebensdauer verlängert. Dieser Widerstand minimiert auch Wartungsbedarf, Zeit und Ressourcen sparen.
Kosten und Erschwinglichkeit
Die Kosten spielen bei der Auswahl der richtigen Beschichtung eine wichtige Rolle. Während hochreine Siliziumkarbid-Beschichtungen höhere Kosten haben können, überwiegen ihre langfristigen Vorteile oft die anfängliche Investition. Ihre Haltbarkeit reduziert die Häufigkeit der Ersetzungen, was zu Kosteneinsparungen im Laufe der Zeit führt. Ich empfehle die Gesamtkosten des Eigentums und nicht nur den Anfangspreis bei der Beurteilung dieser Beschichtungen.
Durability and Longevity
Langlebigkeit und Langlebigkeit sind wesentlich, um die Effizienz von industriellen Komponenten zu gewährleisten. Hochwertige Siliziumkarbidbeschichtungen bieten mehrere Vorteile:
- Hohe Temperaturbeständigkeit bis 1600°C.
- Ausgezeichnete chemische Beständigkeit.
- Hervorragende Verschleißfestigkeit.
- Hohe Festigkeit.
Diese Eigenschaften verlängern die Lebensdauer von Bauteilen, insbesondere in rauen Umgebungen. Beispielsweise schützen Beschichtungen mit hoher Korrosions- und Wärmebeständigkeit Graphitkomponenten und gewährleisten eine optimale Leistung im Laufe der Zeit. Die folgende Tabelle gibt zusätzliche Einblicke in die Haltbarkeit:
Erzeugnis | Langlebigkeit und Langlebigkeit Einblicke |
---|---|
Hochsilizium Antioxidationsbeschichtung | Verbessert die Oxidationsbeständigkeit bis zu 85% bei hohen Temperaturen; begrenzte Informationen über langfristige Haltbarkeit und Leistung unter unterschiedlichen Bedingungen. |
Ich habe festgestellt, dass, während diese Beschichtungen in der Haltbarkeit hervorragend sind, sie spezielle Bedingungen für eine optimale Leistung erfordern. Richtige Anwendung und Wartung sind entscheidend für die Maximierung ihrer Lebensdauer.
Anwendungsspezifische Eignung
Die Bestimmung der Eignung von hochreinen Siliziumkarbidbeschichtungen für bestimmte Anwendungen hängt von mehreren kritischen Faktoren ab. Diese Beschichtungen müssen die einzigartigen Anforderungen jeder Branche erfüllen und eine optimale Leistung und Zuverlässigkeit gewährleisten.
Einige der schlüsselfaktoren, die die anwendungsspezifische eignung beeinflussen enthalten:
- Härte
- Verschleißfestigkeit
- Korrosionsbeständigkeit
- Wärmeausdehnungskoeffizient
- Reinheitsgrad
- Herstellungsverfahren
Beispielsweise zeichnen sich α-SiC-Beschichtungen in nicht oxidierenden und leicht sauren Umgebungen aus. Andererseits zeigen β-SiC-Beschichtungen eine überlegene Korrosionsbeständigkeit bei aggressiven oxidierenden und stark alkalischen Bedingungen. Diese Vielseitigkeit macht β-SiC zu einer bevorzugten Wahl für Industrien, die eine robuste chemische Stabilität erfordern.
Das Herstellungsverfahren spielt auch eine wesentliche Rolle bei der Bestimmung der Leistung der Beschichtung. Gemeinsame Techniken umfassen:
- Chemische Gasphasenabscheidung (CVD)
- Physikalische Gasphasenabscheidung (PVD)
- Sprühtechniken
- Elektrochemische Abscheidung
- Slurry Beschichtung Sinter
Jedes Verfahren bietet deutliche Vorteile. So produziert CVD Beschichtungen mit außergewöhnlicher Reinheit und Gleichmäßigkeit, was sie ideal für Halbleiteranwendungen macht. Im Gegensatz dazu bieten Spritztechniken kostengünstige Lösungen für Großprojekte.
Die Anpassung der Eigenschaften der Beschichtung mit den Anforderungen der Anwendung sorgt für langfristige Effizienz und Haltbarkeit. So profitieren beispielsweise Luft- und Raumfahrtkomponenten von Beschichtungen mit hoher Verschleißfestigkeit und thermischer Stabilität, während erneuerbare Energiesysteme Korrosionsbeständigkeit und Langlebigkeit priorisieren.
Environmental and Safety Considerations
Bei der Auswahl hochreiner Siliziumkarbidbeschichtungen werden Umwelt- und Sicherheitsaspekte immer wichtiger. Industrien müssen die Umweltauswirkungen der Produktions-, Applikations- und Entsorgungsprozesse der Beschichtung bewerten.
Hochreine Siliziumkarbidbeschichtungen sind in der Regel umweltfreundlich durch ihre Haltbarkeit und lange Lebensdauer. Durch die Verringerung der Häufigkeit der Ersetzungen minimieren diese Beschichtungen den Abfall- und Ressourcenverbrauch. Darüber hinaus produzieren viele Aufbereitungsmethoden, wie CVD und PVD, minimale Emissionen, die auf Nachhaltigkeitsziele ausgerichtet sind.
Sicherheit ist ein weiterer kritischer Faktor. Diese Beschichtungen müssen strengen Sicherheitsstandards entsprechen, um sicherzustellen, dass sie keine Risiken für die Arbeitnehmer oder die Umwelt darstellen. Beispielsweise sollte der Anwendungsprozess die Exposition gegenüber schädlichen Chemikalien oder Partikeln minimieren. Während der Abscheidungsphase der Beschichtung sind richtige Belüftungs- und Schutzeinrichtungen erforderlich.
Darüber hinaus erhöht die chemische Stabilität der Beschichtungen die Sicherheit, indem gefährliche Reaktionen in aggressiven Umgebungen verhindert werden. Diese Eigenschaft ist besonders wertvoll in Industrien wie erneuerbarer Energie, in denen Komponenten mit harten Chemikalien ausgesetzt sind.
Durch die Priorisierung von Umwelt- und Sicherheitsaspekten können Industrien hochreine Siliziumkarbidbeschichtungen annehmen, die sowohl auf Leistungs- als auch auf Nachhaltigkeitsziele ausgerichtet sind.
Detaillierter Vergleich der Top-Produkte
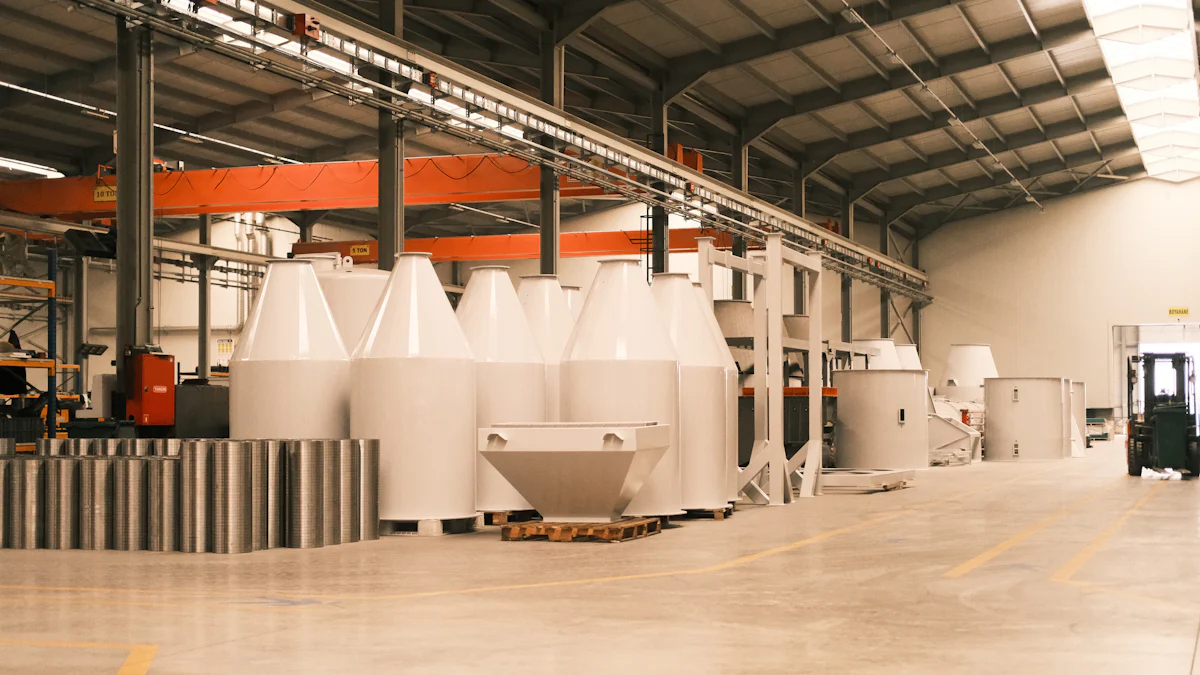
Produkt 1: SiC3 hohe Reinheit Beschichtung
Schlüsselangaben
Die hohe Reinheit von SiC3 Die Beschichtung zeichnet sich durch außergewöhnliche Materialeigenschaften aus. Ich habe seine wichtigsten Spezifikationen in der folgenden Tabelle für Klarheit zusammengefasst:
Eigentum | Wert |
---|---|
Dichte | 3200 kg |
Kristallstruktur | 3C (kubisch; β) |
Porosität | 0% (Heliumleck dicht) |
Größe | 1 bis 5 μm |
Visuelle Erscheinung | Grau, Satin zu langweilig |
Wärmeausdehnung (RT -400°C) | 4,2 x 10-6m.K-1 |
Wärmeleitfähigkeit (@20°C) | 200 W.m-1.K-1 |
Elastisches Modul | 450GPa |
Elektrische Widerstandsfähigkeit (@20°C) | 1MΩ.m |
Diese Beschichtung bietet auch anpassbare Kristallgrößen, ausgezeichnete Haftung auf Materialien wie Graphit und die Temperaturbeständigkeit bis zu 1600° C.
Vor- und Nachteile
Ich habe festgestellt, dass die SiC3-Beschichtung in mehreren Bereichen übertrifft, aber es hat ein paar Einschränkungen. Hier ist ein schneller Vergleich:
Vorteile | Disadvantages |
---|---|
Hohe Dichte verbessert die Korrosionsbeständigkeit und Langlebigkeit. | Maximale Teilgröße auf 360mm begrenzt. |
Ausgezeichnete Deckung, auch in Sacklöchern. | Limitierte Anpassung für Nischenanwendungen. |
Hohe Reinheit mit niedrigen N2-Absorptionsgasen erreicht. | N/A |
Einstellbare Oberflächenrauhigkeit für spezifische Bedürfnisse. | N/A |
Ideale Anwendungsfälle
Die SiC3-Beschichtung ist ideal für Industrien, die eine hohe thermische und chemische Stabilität erfordern. Ich empfehle es für die Halbleiterfertigung, wo seine Reinheit und Gleichmäßigkeit die Waferverarbeitung verbessern. Es ist auch eine gute Wahl für Luft- und Raumfahrtanwendungen, dank seiner Fähigkeit, extremen Temperaturen und Verschleiß standzuhalten.
Produkt 2: Nanomakers High Purity Silicon Carbid Coating
Schlüsselangaben
Nanomakers’ Beschichtung ist für seine nanoskalige Präzision und fortschrittliche Abscheidetechniken bekannt. Dieses Produkt bietet:
- Hohe Reinheit und minimale Verschmutzung.
- Überlegene Wärmeleitfähigkeit, so dass es für hitzeintensive Anwendungen geeignet ist.
- Ausgezeichnete Haftung auf Metallen und Keramik.
- Beständigkeit gegen Oxidation und chemischen Abbau.
Vor- und Nachteile
Nanomakers’ Beschichtung bietet mehrere Vorteile, aber ich habe auch einige Herausforderungen beobachtet:
- Pros:
- Außergewöhnliche nanoskalige Uniformität.
- Hohe thermische und chemische Beständigkeit.
- Vielfältige Anwendungsmethoden, einschließlich CVD und PVD.
- Negativ:
- Höhere Kosten durch fortschrittliche Fertigungsprozesse.
- Begrenzte Verfügbarkeit in Großprojekten.
Ideale Anwendungsfälle
Diese Beschichtung funktioniert am besten in hochpräzisen Industrien wie Leistungselektronik und medizinischen Geräten. Seine nanoskalige Uniformität macht es zu einer Top-Auswahl für Anwendungen, die genaue Standards erfordern, wie Mikroelektronik und fortschrittliche Optik.
Produkt 3: Washington Mills Silikon Carbide Beschichtung
Schlüsselangaben
Washington Mills bietet eine kostengünstige Lösung mit robusten Materialeigenschaften. Zu den wichtigsten Merkmalen gehören:
- Niedrige Dichte kombiniert mit hoher Festigkeit.
- Ausgezeichnete Korrosionsbeständigkeit in sauren und alkalischen Umgebungen.
- Verbesserte Oxidationsbeständigkeit, erhöhte Haltbarkeit bis zu 85%.
Vor- und Nachteile
Ich habe die wichtigsten Vorteile und Nachteile dieses Produkts unten skizziert:
Vorteil/Rückkehr | Beschreibung |
---|---|
Verbesserte Oxidationsbeständigkeit | Verbessert die Leistung in Hochtemperatur-Umgebungen. |
Niedrige Kosten | Erschwinglich und einfach anzuwenden. |
Potential Blister Formation | Kann Blister während des Erhitzens, beeinflussen Beschichtung Integrität. |
Begrenzte langfristige Haltbarkeit | Unzureichende Daten über die Leistung unter unterschiedlichen Bedingungen. |
Ideale Anwendungsfälle
Die Beschichtung von Washington Mills ist eine praktische Wahl für Industrien, die Kosteneffizienz priorisieren. Ich empfehle es für erneuerbare Energiesysteme, wo seine Korrosionsbeständigkeit eine langfristige Zuverlässigkeit gewährleistet. Es kann jedoch nicht die beste Option für Anwendungen sein, die extreme Haltbarkeit oder Präzision erfordern.
Produkt 4: Fortgeschrittene keramische Beschichtungen
Schlüsselangaben
Advanced Ceramic Coatings bieten eine einzigartige Kombination aus Haltbarkeit und Funktionalität. Diese Beschichtungen dienen dazu, Oberflächen vor Umweltschäden zu schützen und gleichzeitig ihre Leistung zu steigern. Zu den wichtigsten Merkmalen gehören:
- Hohe Haltbarkeit, dauerhafter Schutz.
- Hydrophobe Eigenschaften, die Wasser abstoßen und die Reinigung vereinfachen.
- Beständigkeit gegen UV-Strahlen, Fading und Verfärbung zu verhindern.
- Protection against chemical stains caused by pollutants.
Diese Beschichtungen verbessern auch die visuelle Anziehung von Oberflächen durch Hinzufügen von Tiefe und Glanz. Ihre einfache Wartung macht sie eine bevorzugte Wahl für Industrien, die sowohl Funktionalität als auch Ästhetik erfordern.
Vor- und Nachteile
Ich habe beobachtet, dass Advanced Ceramic Coatings mehrere Vorteile bieten, aber sie haben auch Einschränkungen. Hier ist eine Aufschlüsselung:
Vorteile:
- Vereinfacht die Reinigung durch Reduktion der Verklebung von Verunreinigungen.
- Reduziert Wartungsfrequenz, Sparzeit und Ressourcen.
- Schutz vor Umweltschäden, wie UV-Strahlen und chemischen Flecken.
Einschränkungen:
- Kann Kratzer, Drallmarken oder Steinchips nicht verhindern.
- Wasserzeichen können verbleiben, wenn Wasser auf der Oberfläche verdampft.
- Regelmäßiges Waschen ist immer noch notwendig, um das Aussehen zu erhalten.
Ideale Anwendungsfälle
Advanced Ceramic Coatings sind ideal für Industrien, die den Oberflächenschutz und die Ästhetik priorisieren. Ich empfehle sie für Automotive-Anwendungen, wo sie Farbe vor Fading schützen und ihren Glanz verbessern. Sie eignen sich auch für Luft- und Raumfahrt, wo Haltbarkeit und Wartungsfreundlichkeit kritisch sind. Darüber hinaus arbeiten diese Beschichtungen gut in erneuerbaren Energiesystemen und schützen Bauteile vor Umweltverschleiß und -rissen.
Produkt 5: Custom High Purity Silicon Carbide Beschichtungen
Schlüsselangaben
Maßgeschneiderte hochreine Siliziumkarbidbeschichtungen bieten maßgeschneiderte Lösungen für spezifische industrielle Anforderungen. Diese Beschichtungen können in Bezug auf Kristallgröße, Oberflächenrauhigkeit und elektrische Widerstandsfähigkeit angepasst werden. Die folgende Tabelle zeigt einige der Anpassungsmöglichkeiten:
Eigentum | Anpassungsoptionen |
---|---|
Größe | Steuerung zur gewünschten Oberflächenrauhigkeit |
Elektrische Widerstandsfähigkeit | Optimiert für spezifische Anwendungen |
Diese Beschichtungen führen in Hochtemperatur-Umgebungen hervorragend aus, trotz Temperaturen bis zu 1600°C. Größere Kristallgrößen verbessern ihre Leistung in hitzeintensiven Prozessen und machen sie vielseitig für verschiedene Branchen.
Vor- und Nachteile
Benutzerdefinierte hochreine Siliziumkarbid-Beschichtungen in vielen Bereichen, aber sie kommen auch mit Herausforderungen. Hier ist eine Zusammenfassung:
Pros | Negativ |
---|---|
Hervorragende Verschleißfestigkeit | Höhere Kosten im Vergleich zu anderen Bodenaggregaten |
Hohe Temperaturbeständigkeit bis 1600°C | Möglicherweise hohe Produktionskosten |
Hervorragende chemische Beständigkeit | Schwer zu erzeugen als Beschichtung |
Geeignet für verschiedene industrielle Anwendungen | Begrenzte Informationen zu spezifischen Anwendungen |
Ausgezeichnete Korrosionsbeständigkeit in rauen Umgebungen | Tendenz zum Abbau ohne richtigen Schutz |
Ideale Anwendungsfälle
Maßgeschneiderte hochreine Siliziumkarbidbeschichtungen sind ideal für Industrien, die spezialisierte Lösungen benötigen. Ich empfehle sie für die Halbleiterfertigung, wo eine präzise Kontrolle über Oberflächeneigenschaften unerlässlich ist. Sie arbeiten auch gut in Luft- und Raumfahrtanwendungen und bieten hohe Verschleißfestigkeit und thermische Stabilität. Darüber hinaus sind diese Beschichtungen für erneuerbare Energiesysteme geeignet, wo Haltbarkeit und chemische Beständigkeit kritisch sind.
Vergleichende Analyse
Zusammenfassung der wichtigsten Unterschiede
When comparing hochreine siliziumkarbidbeschichtungen, Ich bemerkte, dass jedes Produkt einzigartige Stärken auf bestimmte industrielle Bedürfnisse zugeschnitten bietet. Zum Beispiel, NTST Silicon Carbide Beschichtungen zeichnen sich durch ihre geringe Dichte und hohe Festigkeit aus und machen sie ideal für leichte Anwendungen. Sie können jedoch in rauen Umgebungen abbauen, was ihren Einsatz unter extremen Bedingungen begrenzt. Hochsilizium Antioxidationsbeschichtungen in verbesserung der Oxidationsbeständigkeit bis zu 85%, aber sie können blister während der erwärmung bilden, die ihre integrität beeinflusst.
Siliziumkarbid-Verbundbeschichtungen einen wirksamen Korrosionsschutz bieten und Restspannungen reduzieren. Traditionelle Lackierungen erfordern jedoch hohe Sintertemperaturen, die mit niedrigschmelzenden Metallen unverträglich sein können. Lebenslauf SiC beschichtete Sauger bieten unübertroffene Temperatur und chemische Beständigkeit, aber ihre hohen Produktionskosten und begrenzte Anwendungsdaten machen sie weniger zugänglich. Endlich, SIGRAFIEN SiC Beschichtungen liefern eine ausgezeichnete wärmeleitfähigkeit und korrosionsbeständigkeit, aber sie erfordern spezifische bedingungen für eine optimale anwendung.
Hier ist ein schneller Vergleich dieser Produkte:
Erzeugnis | Zusammensetzung | Vorteile | Disadvantages |
---|---|---|---|
NTST Silicon Carbide Beschichtungen | Reines SiC, SiC Cermet, SiC-B4C | Niedrige Dichte, hohe Festigkeit, ausgezeichnete Korrosionsbeständigkeit | Schwierig zu produzieren, Tendenz zu degradieren in rauen Umgebungen |
Hochsilizium Antioxidationsbeschichtung | Hochsiliziumkarbid, Chrom, Bindemittel | Verbessert die Oxidationsbeständigkeit bis zu 85% | Potenzial für Blisterbildung während der Heizung, begrenzte langfristige Haltbarkeit |
Siliziumkarbid-Verbundbeschichtung | Siliciumcarbid | Effektiver Korrosionsschutz, reduziert restspannung | Traditionelle Emailbeschichtungen erfordern hohe Sintertemperaturen, mögliche Unverträglichkeit mit niedrigschmelzenden Metallen |
Lebenslauf SiC beschichteter Suszeptor | Lebenslauf SiC | Hohe Temperaturbeständigkeit, ausgezeichnete chemische Beständigkeit | Begrenzte Informationen über spezifische Anwendungen, potenziell hohe Produktionskosten |
SIGRAFIEN SiC Beschichtung | Dense SiC Beschichtung | Hohe Korrosions- und Wärmebeständigkeit, ausgezeichnete Wärmeleitfähigkeit | Potentielle hohe Aufwand an Anwendung, erfordert besondere Bedingungen |
Ähnliche Produkte Across
Trotz ihrer Unterschiede teilen diese Beschichtungen mehrere gemeinsame Merkmale, die sie in der Industrie unverzichtbar machen. Alle Produkte weisen eine außergewöhnliche thermische Stabilität auf, so dass sie in Hochtemperatur-Umgebungen zuverlässig arbeiten können. Ihre hohe Korrosionsbeständigkeit gewährleistet auch bei chemisch aggressiven Bedingungen Haltbarkeit. Darüber hinaus sind diese Beschichtungen entworfen, um die Lebensdauer von industriellen Komponenten zu verbessern, wodurch die Wartungskosten im Laufe der Zeit reduziert werden.
Eine andere Ähnlichkeit liegt in ihrer Vielseitigkeit. Ob im Halbleiterbau, in der Luft- und Raumfahrt oder in den erneuerbaren Energiesystemen eingesetzt, diese Beschichtungen passen sich an verschiedene Anwendungen an. Die meisten von ihnen nutzen auch fortschrittliche Abscheidungstechniken wie Chemical Vapor Deposition (CVD) oder Physical Vapor Deposition (PVD), um Gleichmäßigkeit und hohe Reinheit zu gewährleisten.
Vergleichstabelle der Eigenschaften und Leistung
Um ein klareres Bild zu liefern, habe ich die Merkmale und Leistung dieser Beschichtungen in der folgenden Tabelle zusammengefasst:
Feature/Performance Metric | NTST Silicon Carbide Beschichtungen | Hochsilizium Antioxidation Beschichtung | Silicon Carbide/Enamel Composite Coating | Lebenslauf SiC beschichteter Suszeptor | SIGRAFIEN SiC Beschichtung |
---|---|---|---|---|---|
Thermal Resistance | Ausgezeichnet | Gut | Mäßig | Ausgezeichnet | Ausgezeichnet |
Korrosionsbeständigkeit | Hoch | Hoch | Hoch | Hoch | Hoch |
Abnutzungswiderstand | Hoch | Mäßig | Mäßig | Hoch | Hoch |
Kosten | Mäßig | Niedrig | Mäßig | Hoch | Hoch |
Anwendung Vielseitigkeit | Hoch | Mäßig | Mäßig | Hoch | Hoch |
Ease der Herstellung | Mäßig | Hoch | Niedrig | Niedrig | Mäßig |
Diese Tabelle zeigt, wie jedes Produkt auf spezifische industrielle Anforderungen ausgerichtet ist. Beispielsweise zeichnen sich NTST-Beschichtungen durch Verschleißfestigkeit aus, während SIGRAFINE-Beschichtungen eine überlegene Wärmeleitfähigkeit bieten. Durch das Verständnis dieser Unterscheidungen können Branchen das am besten geeignete Produkt für ihre Bedürfnisse auswählen.
Leitfaden zur Entscheidungsfindung
Hochreine Siliziumkarbidbeschichtungen sind im Jahr 2025 unverzichtbar geworden und treiben Fortschritte in Industrien wie Halbleitern, Luft- und Raumfahrt und erneuerbaren Energien. Ihre außergewöhnlichen Eigenschaften – Wärmebeständigkeit, Korrosionsbeständigkeit und Verschleißfestigkeit – sind für Hochleistungsanwendungen von entscheidender Bedeutung.
Aus meiner Analyse bietet jedes Produkt einzigartige Stärken. Beispielsweise zeichnen sich SiC3-Beschichtungen durch ihre Reinheit und Gleichmäßigkeit in der Halbleiterfertigung aus. Mittlerweile bieten hochsilizium-Antioxidationsbeschichtungen kostengünstige Lösungen für den Kohlenstoffstahlschutz.
Aspect | Details |
---|---|
Anwendungen | Halbleiter, Luft- und Raumfahrt, Heiztechnologien |
Vorteile | Hohe Dichte, ausgezeichnete Abdeckung, einstellbare Oberflächenrauhigkeit |
Limitations | Maximale Teilgröße begrenzt auf 360mm, mögliche Anpassung Einschränkungen |
Wenn auswahl eines produkts, Ich empfehle, seine Eigenschaften auf die spezifischen Bedürfnisse Ihrer Branche auszurichten. Für Luft- und Raumfahrt priorisieren Beschichtungen mit Härte und thermischer Stabilität. Für Halbleiter konzentrieren Sie sich auf Reinheit und präzise Abscheideverfahren. Durch das Verständnis dieser Nuancen können Sie langfristige Effizienz und Zuverlässigkeit gewährleisten.
FAQ
Was macht hochreine Siliziumkarbidbeschichtungen einzigartig?
Hochreine Siliziumkarbidbeschichtungen zeichnen sich durch ihre außergewöhnliche härte, thermische stabilitätund Korrosionsbeständigkeit. Diese Eigenschaften machen sie ideal für anspruchsvolle industrielle Anwendungen wie Halbleiter und Aerospace.
Wie wähle ich die richtige Beschichtung für meine Industrie?
Ich empfehle, die spezifischen Bedürfnisse Ihrer Branche zu bewerten, wie thermische Beständigkeit, chemische Stabilität und Verschleißfestigkeit. Die Anpassung dieser Anforderungen an die Eigenschaften der Beschichtung sorgt für eine optimale Leistung.
Sind diese Beschichtungen umweltfreundlich?
Ja, die meisten hochreinen Siliziumkarbidbeschichtungen sind umweltfreundlich. Ihre Langlebigkeit reduziert Abfall und fortschrittliche Abscheidemethoden wie CVD produzieren minimale Emissionen, die auf Nachhaltigkeitsziele ausgerichtet sind.
Können diese Beschichtungen extremen Temperaturen standhalten?
Absolut! Hochreine Siliziumkarbidbeschichtungen können Temperaturen bis zu 1600°C halten. Das macht sie perfekt für anwendungen in hochwärmeumgebungen wie halbleiterbau und luftraum.
Welche Branchen profitieren am meisten von diesen Beschichtungen?
Branchen wie Halbleiter, Luft- und Raumfahrt, Erneuerbare Energien und medizinische Geräte profitieren deutlich. Diese Beschichtungen verbessern die Haltbarkeit, verbessern die Leistung und gewährleisten die Zuverlässigkeit bei harten Bedingungen.
Wie lange dauern diese Beschichtungen typischerweise?
Die Lebensdauer hängt von der Anwendung und Wartung ab. Ihre außergewöhnliche Haltbarkeit verlängert jedoch oft die Lebensdauer von Bauteilen und reduziert den Bedarf an häufigen Austauschen.
Sind benutzerdefinierte Beschichtungen wert die Investition?
Benutzerdefinierte Beschichtungen bieten maßgeschneiderte Lösungen für spezifische Bedürfnisse. Während sie mehr Kosten im Voraus, ihre langfristigen Vorteile, wie verbesserte Leistung und Haltbarkeit, oft rechtfertigen die Investition.
Was ist die beste Anwendungsmethode für diese Beschichtungen?
Chemical Vapor Deposition (CVD) ist die effektivste Methode zur Erzielung hoher Reinheit und Gleichmäßigkeit. Andere Verfahren wie PVD oder Sprühen können jedoch groß- oder kostenempfindliche Projekte entsprechen.