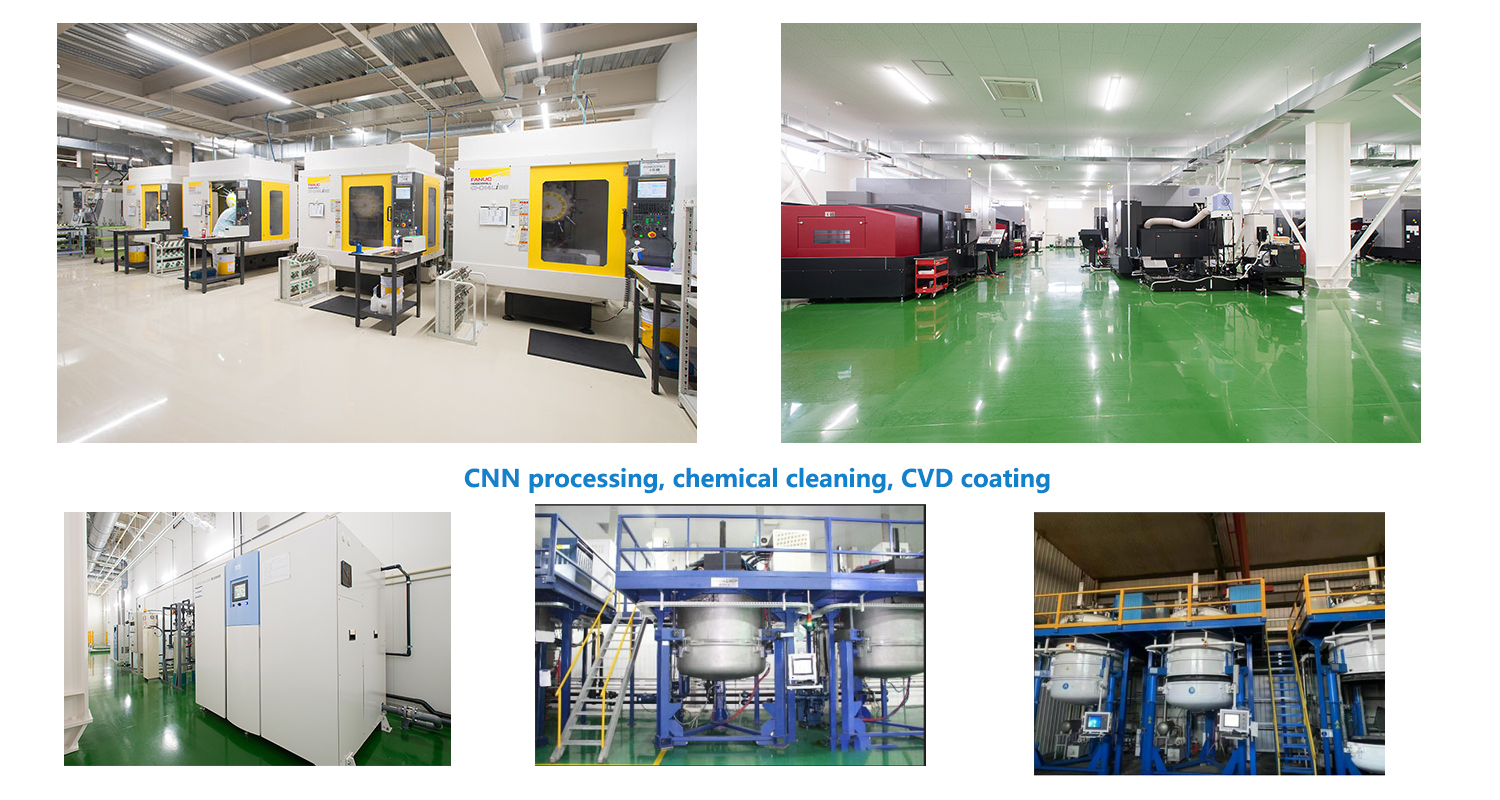
Sintered silicon carbide wafer boats are essential components in high-tech industries, offering unparalleled performance and reliability. The Reaktionsgesintertes Siliziumkarbid-Waferboot, crafted with advanced SiC-Beschichtung, exemplifies the superior qualities of silicon carbide, a material celebrated for its exceptional strength and durability. These wafer boats are designed to withstand extreme conditions, making them indispensable in semiconductor manufacturing. As a cornerstone of semiconductor ceramics, the Reaction sintered silicon carbide wafer boat ensures precision and efficiency in even the most demanding processes. This innovative technology underscores the critical role of silicon carbide in modern industrial applications.
Wichtigste Erkenntnisse
- Sintered silicon carbide boats resist heat and chemicals very well.
- They stay strong at over 1000°C, working reliably in tough tasks.
- Their strength and hardness make them durable under heavy use.
- These boats resist rust and wear, perfect for harsh environments.
- They can be customized to fit different industrial needs easily.
- Using them saves money over time with less maintenance needed.
- They help the environment by reducing waste and saving energy.
- High-tech industries need these boats for their strong performance.
Unique Properties of Sintered Silicon Carbide Wafer Boats
High Thermal and Chemical Resistance
Sintered silicon carbide wafer boats excel in environments requiring exceptional thermal and chemical resistance. These boats demonstrate remarkable thermal conductivity, measured at 126 W/m·K, which ensures efficient heat transfer during high-temperature processes. Their thermal shock resistance of 450°C allows them to endure rapid temperature changes without cracking or deforming. This makes them ideal for semiconductor manufacturing, where precision and stability are critical.
The material’s thermal stability is another standout feature. It can withstand extreme temperatures exceeding 1000°C without warping, ensuring long-term reliability. Additionally, sintered silicon carbide offers excellent heat dissipation, preventing the formation of thermal hotspots. This property ensures even temperature distribution, which is essential for maintaining the integrity of delicate semiconductor components. Furthermore, its high resistance to chemical corrosion allows it to perform reliably in aggressive chemical environments, such as those involving reactive dopant gases.
Exceptional Mechanical Strength and Hardness
Sintered silicon carbide wafer boats are renowned for their superior mechanical strength and hardness. These properties make them highly durable and capable of withstanding the mechanical stresses of industrial applications. The material’s hardness ranges between 2550 and 2800 Knoop, placing it among the hardest ceramics available. This ensures resistance to wear and deformation, even under heavy loads.
The flexural strength of sintered silicon carbide ranges from 59 to 108 kpsi, while its compressive strength reaches an impressive 550 kpsi. These values highlight its ability to endure both bending and compressive forces without failure. Compared to reaction-bonded silicon carbide, the sintered variant offers significantly higher compressive strength and hardness, as shown in the table below:
Eigentum | Sintered Silicon Carbide | Reaction Bonded Silicon Carbide |
---|---|---|
Compressive Strength | 3680 MPa | Lower than sintered variant |
Knoop Hardness | 2810 | Lower than sintered variant |
These mechanical properties make sintered silicon carbide wafer boats a reliable choice for demanding applications, including those in semiconductor and aerospace industries.
Superior Corrosion and Abrasion Resistance
The sintered silicon carbide wafer boat also stands out for its exceptional resistance to corrosion and abrasion. This property ensures durability in harsh environments, such as those involving acids or abrasive materials. The material’s corrosion resistance makes it particularly suitable for applications in chemical processing and refining, where exposure to aggressive substances is common.
Its wear resistance is equally impressive, allowing it to perform reliably in environments with high levels of friction or abrasive particles. This makes it an excellent choice for components like bushings, plates, and sandblasting nozzles. The table below summarizes these features:
Feature | Beschreibung |
---|---|
Korrosionsbeständigkeit | Outstanding resistance, particularly in acids, ideal for valve applications. |
Abnutzungswiderstand | Excellent wear resistance, suitable for demanding environments. |
Application | Proven success in chemical processing, refining, mining, and pulp and paper processing. |
These properties ensure that sintered silicon carbide wafer boats maintain their performance and integrity over extended periods, even in the most challenging conditions.
Outstanding Thermal Conductivity and Oxidation Resistance
Sintered silicon carbide wafer boats exhibit exceptional thermal conductivity and oxidation resistance. These properties make them indispensable in industries that demand high performance under extreme conditions. The material’s thermal conductivity, measured at 126 W/m·K, ensures efficient heat transfer. This capability allows wafer boats to maintain stable temperatures during high-temperature processes, which is critical in semiconductor manufacturing.
Efficient heat dissipation prevents overheating and ensures uniform temperature distribution. This feature reduces the risk of thermal stress, which can compromise the integrity of delicate components. The ability to manage heat effectively also enhances the overall efficiency of industrial processes. For example, in semiconductor production, consistent thermal performance ensures precise wafer handling and processing.
Oxidation resistance further enhances the durability of sintered silicon carbide wafer boats. The material forms a protective oxide layer when exposed to high temperatures, which shields it from further oxidation. This property allows the wafer boats to maintain their structural integrity even in oxygen-rich environments. Industries such as aerospace and energy production benefit significantly from this feature, as it ensures long-term reliability in harsh operating conditions.
Anmerkung: The oxidation resistance of sintered silicon carbide extends its lifespan, reducing the need for frequent replacements. This contributes to cost savings and operational efficiency.
The combination of thermal conductivity and oxidation resistance makes sintered silicon carbide wafer boats suitable for a wide range of applications. They perform reliably in quenching furnace tubes, radiant tubes, and heating elements. These components often operate in extreme environments, where consistent performance is essential.
Industries also value the material’s ability to withstand rapid temperature changes. Thermal shock resistance ensures that the wafer boats do not crack or deform when exposed to sudden temperature fluctuations. This feature is particularly important in processes that involve rapid heating and cooling cycles.
Benefits of Using Sintered Silicon Carbide Wafer Boats
Enhanced Efficiency in Semiconductor Manufacturing
Sintered silicon carbide wafer boats significantly improve efficiency in semiconductor manufacturing. Their enhanced thermal stability ensures consistent performance even at extreme temperatures exceeding 1000°C. This stability prevents warping and maintains the structural integrity of the wafer boats during high-temperature processes. Additionally, their excellent heat dissipation capabilities prevent the formation of thermal hotspots, ensuring uniform temperature distribution.
These wafer boats also reduce contamination risks. Their resistance to oxidation and chemical corrosion ensures that wafers remain pure throughout the manufacturing process. This property is critical in semiconductor production, where even minor impurities can compromise the quality of the final product. Furthermore, the durability of sintered silicon carbide wafer boats minimizes the need for frequent replacements, leading to uninterrupted production cycles.
Key efficiency improvements include:
- Enhanced thermal stability and heat dissipation.
- Reduced contamination risks, maintaining wafer purity.
- Improved process efficiency and increased durability.
Cost-Effectiveness and Long-Term Reliability
Although sintered silicon carbide wafer boats may have higher initial costs, their long-term cost-effectiveness makes them a preferred choice for many industries. Their extended lifespan reduces the need for frequent replacements, resulting in lower overall lifecycle costs. Additionally, their durability minimizes maintenance requirements, further contributing to cost savings.
The compatibility of these wafer boats with existing equipment enhances production efficiency. This compatibility reduces the likelihood of production delays and ensures higher yields. The table below highlights the cost-effectiveness of sintered silicon carbide wafer boats:
Nachweisart | Beschreibung |
---|---|
Durability | Extended lifespan lowers lifecycle costs. |
Maintenance | Reduced maintenance needs save costs. |
Compatibility | Seamless integration with equipment enhances yield. |
These factors make sintered silicon carbide wafer boats a reliable and economical solution for industries seeking long-term performance.
Versatility Across Various Industrial Applications
The versatility of sintered silicon carbide wafer boats extends their utility across multiple industries. In semiconductor manufacturing, they play a crucial role in diffusion processes that require precise temperature control. Their thermal stability and chemical resistance make them indispensable in electronics production.
In photovoltaic manufacturing, these wafer boats ensure high-performance material handling during thermal processes like LPCVD and PECVD. Their mechanical strength and resistance to harsh environments also make them suitable for applications in metallurgy, machinery, and new energy sectors.
Examples of their versatility include:
- Semiconductor manufacturing, particularly in diffusion processes.
- Photovoltaic manufacturing, ensuring precise thermal control.
- Electronics production, where chemical resistance is essential.
- Applications in metallurgy, machinery, and building materials.
The adaptability of sintered silicon carbide wafer boats demonstrates their value across diverse industrial processes. Their ability to perform reliably in demanding environments highlights their importance in modern manufacturing.
Customizability for Specific Industrial Needs
Sintered silicon carbide wafer boats offer unmatched flexibility in design, making them suitable for a wide range of industrial applications. Manufacturers can customize these wafer boats to meet the specific demands of different processes, ensuring optimal performance and efficiency. This adaptability allows industries to achieve precise results, even in the most challenging environments.
Tailored Dimensions and Configurations
One of the key advantages of sintered silicon carbide wafer boats lies in their ability to be manufactured in various shapes, sizes, and configurations. Engineers can design wafer boats with specific dimensions to fit seamlessly into existing equipment. This eliminates the need for costly modifications to machinery.
For example, semiconductor manufacturers often require wafer boats with precise slot spacing to accommodate wafers of varying thicknesses. Custom designs ensure that the wafers remain securely in place during high-temperature processes, reducing the risk of damage. Similarly, industries like photovoltaics and lithium battery production benefit from wafer boats tailored to their unique thermal and mechanical requirements.
Tipp: Custom dimensions not only improve compatibility but also enhance the overall efficiency of industrial processes.
Material Enhancements for Specialized Applications
Sintered silicon carbide wafer boats can also be customized with material enhancements to suit specific operating conditions. For instance, industries that deal with highly corrosive chemicals may require wafer boats with additional coatings to further enhance chemical resistance. Similarly, applications involving extreme temperatures can benefit from designs that optimize thermal conductivity and oxidation resistance.
These material modifications ensure that the wafer boats maintain their performance and durability, even under harsh conditions. This level of customization makes them a preferred choice for industries such as aerospace, chemical processing, and energy production.
Examples of Customization Options
The table below highlights some common customization options available for sintered silicon carbide wafer boats:
Customization Option | Beschreibung | Application Example |
---|---|---|
Slot Spacing | Adjusted to fit wafers of varying thicknesses | Semiconductor manufacturing |
Coatings | Enhanced chemical resistance | Chemical processing and refining |
Thermal Optimization | Improved heat dissipation and conductivity | Photovoltaic and lithium battery production |
Shape and Size Adjustments | Designed to fit specific equipment | Aerospace and defense applications |
Benefits of Customization
Customizable wafer boats provide several benefits to industries. They improve process efficiency by ensuring compatibility with existing systems. Tailored designs also reduce the likelihood of equipment malfunctions, leading to fewer production delays. Additionally, customization enhances the lifespan of the wafer boats, resulting in long-term cost savings.
By offering tailored solutions, sintered silicon carbide wafer boats meet the diverse needs of modern industries. This adaptability ensures that they remain a vital component in high-tech manufacturing processes.
Applications of Sintered Silicon Carbide Wafer Boats
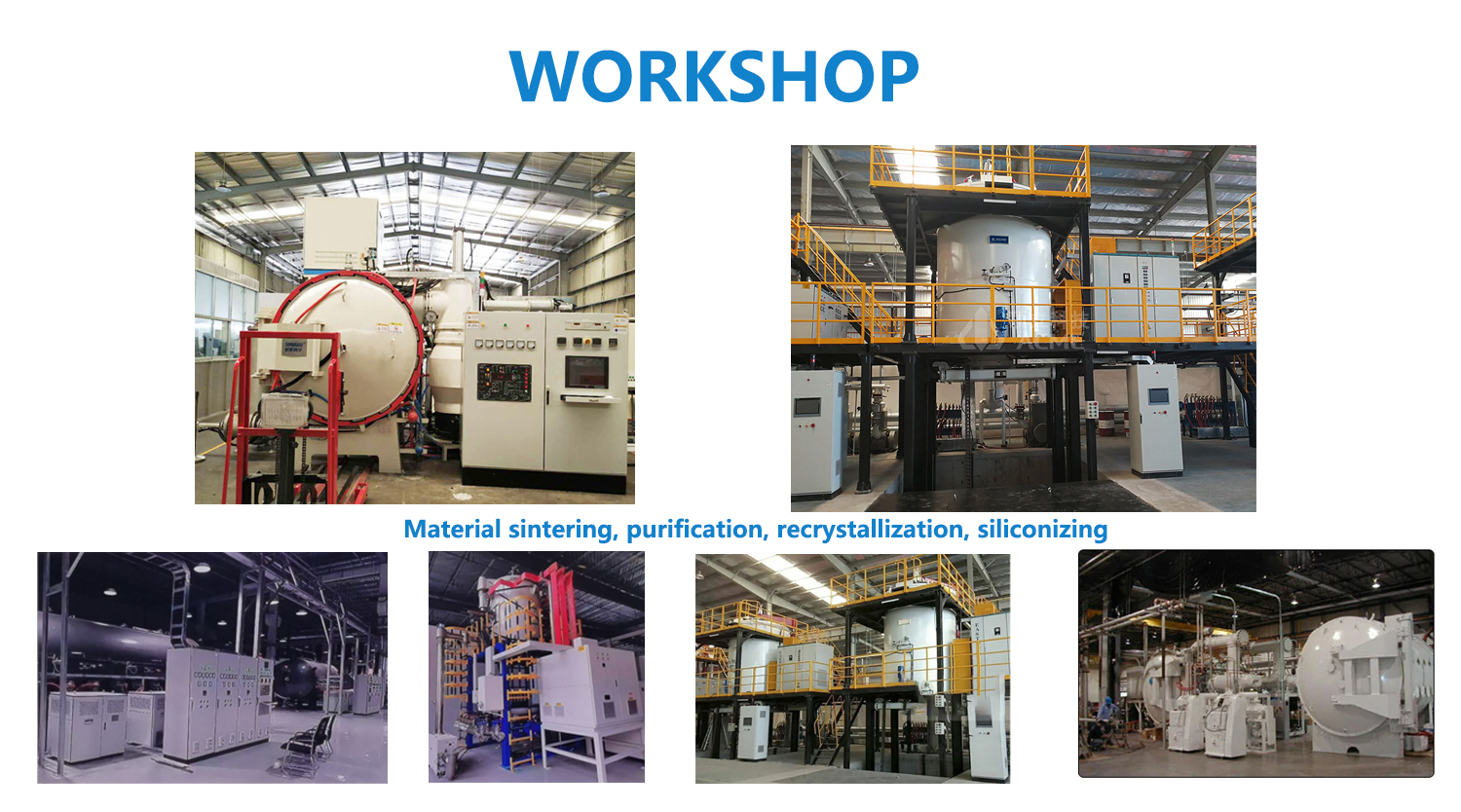
Semiconductor and Electronics Manufacturing
Sintered silicon carbide wafer boats play a vital role in semiconductor and electronics manufacturing. These wafer boats provide the precision and reliability required for handling delicate wafers during high-temperature processes. Their exceptional thermal stability ensures consistent performance, even in extreme conditions. This stability prevents warping and maintains the structural integrity of the wafer boats, which is essential for producing high-quality semiconductor components.
The chemical resistance of sintered silicon carbide also makes it ideal for environments involving reactive gases. These gases are often used in processes like chemical vapor deposition (CVD) and diffusion. The wafer boats resist corrosion, ensuring that the wafers remain uncontaminated throughout the manufacturing process. This property is critical for maintaining the purity of semiconductors, where even minor impurities can affect performance.
In addition, the mechanical strength of these wafer boats allows them to withstand the stresses of repeated use. This durability reduces the need for frequent replacements, leading to cost savings and uninterrupted production cycles. Their ability to handle rapid temperature changes further enhances their reliability, making them indispensable in the semiconductor industry.
Photovoltaic and Lithium Battery Production
Sintered silicon carbide wafer boats contribute significantly to the efficiency of photovoltaic and lithium battery production. Their superior mechanical strength and thermal stability make them a preferred choice over traditional quartz components. These wafer boats exhibit resistance to thermal shock and chemical corrosion, ensuring durability in demanding environments.
Key advantages include:
- Superior mechanical strength and thermal stability compared to quartz.
- Resistance to thermal shock and chemical corrosion, enhancing durability.
- Lifespan over five times that of quartz materials, reducing maintenance and downtime.
- Cost savings and improved production efficiency in photovoltaic manufacturing.
These properties make sintered silicon carbide wafer boats essential for processes like low-pressure chemical vapor deposition (LPCVD) and plasma-enhanced chemical vapor deposition (PECVD). Their ability to maintain consistent performance under extreme conditions ensures the production of high-quality photovoltaic cells and lithium batteries.
Aerospace and Defense Applications
The aerospace and defense industries benefit greatly from the unique properties of sintered silicon carbide wafer boats. These industries require materials that can perform reliably in extreme environments. Sintered silicon carbide meets these demands with its superior heat resistance, thermal uniformity, and durability against chemical cleaning.
Feature | Advantage in Aerospace and Defense Applications |
---|---|
Superior heat resistance | Essential for high-temperature environments |
Thermal uniformity | Ensures consistent performance across components |
High durability against chemical cleaning | Maintains integrity in harsh cleaning processes |
These features make sintered silicon carbide wafer boats suitable for applications such as thermal shielding, high-temperature testing, and precision component handling. Their ability to maintain structural integrity under extreme conditions ensures reliability in critical aerospace and defense operations.
Chemical and Energy Sector Uses
Sintered silicon carbide wafer boats play a crucial role in the chemical and energy sectors. Their exceptional material properties make them indispensable for processes that demand high performance and reliability. These industries often operate in harsh environments, where materials face extreme temperatures, corrosive chemicals, and abrasive conditions. Sintered silicon carbide meets these challenges with unmatched durability and efficiency.
Applications in Chemical Processing
Chemical processing facilities rely on sintered silicon carbide wafer boats for their resistance to chemical corrosion. These boats perform exceptionally well in environments involving strong acids, alkalis, and other reactive substances. Their ability to withstand such conditions ensures long-term reliability and reduces the risk of equipment failure.
Key applications in chemical processing include:
- Reactor Linings: Protecting reactors from corrosive chemicals.
- Heat Exchangers: Ensuring efficient heat transfer in aggressive environments.
- Pumps and Valves: Providing wear-resistant components for fluid handling systems.
Anmerkung: The corrosion resistance of sintered silicon carbide extends the lifespan of equipment, reducing maintenance costs and downtime.
Contributions to the Energy Sector
The energy sector benefits greatly from the thermal and mechanical properties of sintered silicon carbide wafer boats. These boats excel in high-temperature environments, making them ideal for applications in power generation and renewable energy production.
Examples of energy sector uses include:
- Coal Gasification: Withstanding the abrasive and corrosive conditions of gasification reactors.
- Solar Energy Systems: Enhancing the efficiency of photovoltaic cell production.
- Nuclear Power Plants: Serving as durable components in high-temperature systems.
The material’s thermal conductivity ensures efficient heat management, while its oxidation resistance maintains structural integrity over time. These features contribute to safer and more efficient energy production processes.
Advantages in Harsh Environments
Sintered silicon carbide wafer boats outperform traditional materials like metals and quartz in harsh environments. Their superior abrasion resistance makes them suitable for handling abrasive slurries and particulates. Additionally, their lightweight nature simplifies installation and reduces operational strain on equipment.
Feature | Benefit | Example |
---|---|---|
Korrosionsbeständigkeit | Prevents damage from acids and alkalis | Chemical reactors and pipelines |
Thermische Stabilität | Maintains performance at extreme temperatures | Solar and nuclear energy systems |
Abrasion Resistance | Reduces wear in abrasive environments | Coal gasification and mining |
Tipp: Industries can enhance efficiency and reduce costs by replacing traditional materials with sintered silicon carbide components.
The chemical and energy sectors demand materials that can endure extreme conditions while maintaining performance. Sintered silicon carbide wafer boats meet these requirements, making them a valuable asset in modern industrial processes.
Why Sintered Silicon Carbide Wafer Boats Outperform Other Materials
Comparison with Quartz and Graphite
Sintered silicon carbide wafer boats surpass quartz and graphite in durability and performance. Their ability to endure extreme temperatures exceeding 1000°C without warping ensures reliable support for semiconductor wafers during processing. Unlike quartz, which deforms under high heat, silicon carbide maintains its structural integrity, making it ideal for advanced manufacturing processes.
These wafer boats also excel in thermal stability and heat dissipation. They prevent thermal hotspots, which are critical for consistent diffusion in semiconductor production. Quartz materials, by contrast, often fail to provide the same level of thermal efficiency. Additionally, the lifespan of sintered silicon carbide exceeds that of quartz by more than five times, reducing maintenance costs and downtime.
Graphite, while commonly used in industrial applications, lacks the strength and chemical resistance of silicon carbide. Sintered silicon carbide boats resist corrosive environments and maintain optimal performance, even in aggressive chemical mediums. This makes them a superior choice for industries requiring precision and reliability.
Key advantages of sintered silicon carbide over quartz and graphite include:
- Higher strength and thermal stability.
- Resistance to warping and deformation at extreme temperatures.
- Longer lifespan, leading to reduced maintenance costs.
Advances in Reaction Sintering Technology
Reaction sintering technology has revolutionized the production of silicon carbide wafer boats. This advanced process combines high-purity silicon carbide with innovative manufacturing techniques to create components with exceptional material properties. The result is a wafer boat that offers unmatched thermal conductivity, mechanical strength, and chemical resistance.
Modern reaction sintering methods enhance the density and uniformity of silicon carbide, ensuring consistent performance across various applications. These advancements also allow for the production of wafer boats with precise dimensions and complex geometries. This level of precision is essential for industries like semiconductor manufacturing, where even minor deviations can impact product quality.
The integration of cutting-edge technology into the sintering process has also improved the oxidation resistance of silicon carbide. This ensures that wafer boats maintain their structural integrity, even in oxygen-rich environments. By leveraging these technological advancements, manufacturers can produce wafer boats that meet the demanding requirements of high-tech industries.
Adaptability to Emerging High-Tech Industries
Sintered silicon carbide wafer boats demonstrate remarkable adaptability to emerging high-tech industries. Their durability minimizes maintenance needs, while their efficiency contributes to cost optimization by maximizing yield and reducing rework. These qualities make them indispensable in sectors experiencing rapid growth, such as semiconductor manufacturing.
Aspect | Beschreibung |
---|---|
Durability | High resistance to wear and tear minimizes maintenance needs. |
Efficiency | Contributes to cost optimization by maximizing yield and minimizing rework. |
Sustainability | Long service life reduces waste and lowers material consumption. |
Market Growth | Rapid growth in demand for high-performance wafer carrier trays in semiconductor manufacturing. |
The versatility of sintered silicon carbide extends to applications in renewable energy, aerospace, and defense. For example, their use in photovoltaic cell production enhances efficiency and reduces material waste. In aerospace, their thermal stability ensures reliable performance in extreme environments. These qualities position sintered silicon carbide wafer boats as a key component in the future of high-tech manufacturing.
Tipp: Industries can achieve greater efficiency and sustainability by adopting sintered silicon carbide wafer boats for their advanced processes.
Challenges and Considerations in Using Sintered Silicon Carbide Wafer Boats
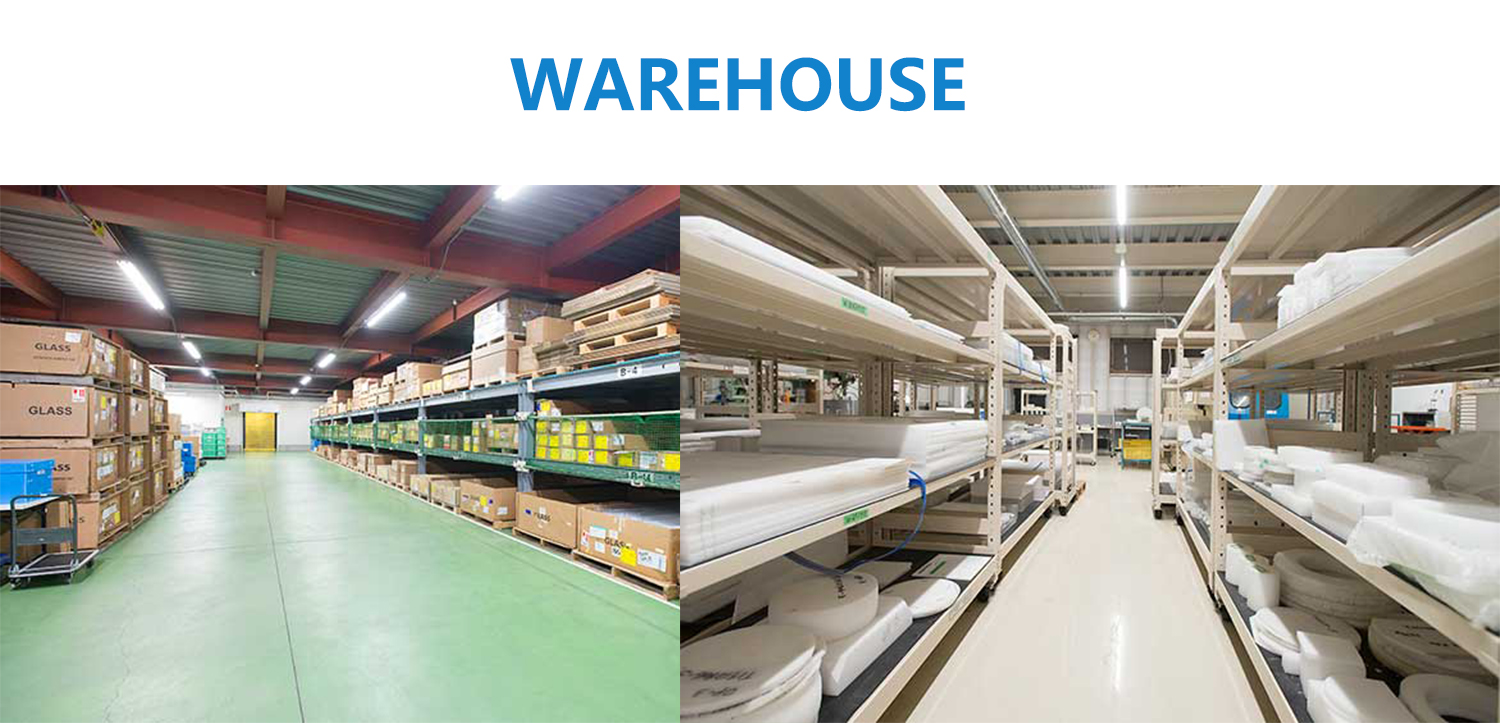
Manufacturing Complexity and Cost
Producing a sintered silicon carbide wafer boat involves advanced manufacturing techniques. The process requires precision and high-purity materials to achieve the desired properties. Methods like reaction sintering and hot isostatic pressing (HIP) enhance the material’s density and mechanical strength. However, these techniques demand specialized equipment and expertise, which increases production costs.
The high cost of raw silicon carbide also contributes to the overall expense. Manufacturers must source high-purity silicon carbide to ensure the wafer boats meet industry standards. This material guarantees durability and performance but adds to the financial burden. Additionally, the intricate designs of wafer boats require precise engineering, further raising production costs.
Despite these challenges, the long-term benefits of durability and efficiency often outweigh the initial investment. Industries that prioritize reliability and performance find these wafer boats to be a cost-effective solution over time.
Industry Adoption and Scalability
The adoption of sintered silicon carbide wafer boats depends on several factors. Industries must evaluate the compatibility of these boats with their existing equipment and processes. For example, the wafer boat’s design must align with specific wafer sizes and manufacturing systems. This ensures seamless integration and optimal performance.
Scalability also plays a crucial role in adoption. Manufacturers must balance production efficiency with quality control to meet growing demand. Advanced techniques like HIP improve the material’s properties, making it suitable for large-scale applications. However, scaling up production requires significant investment in technology and infrastructure.
The table below highlights key factors influencing adoption and scalability:
Faktor | Beschreibung |
---|---|
Manufacturing Techniques | Hot isostatic pressing (HIP) enhances density and mechanical properties, ensuring durability under extreme conditions. |
Material Quality | High-purity silicon carbide ensures durability and optimal performance. |
Design Compatibility | The boat must align with specific wafer sizes and manufacturing equipment. |
Thermische Stabilität | Resistance to rapid temperature changes is critical for reliability. |
Operational Cost Reduction | Durability and efficiency reduce maintenance needs and replacement frequency. |
These factors demonstrate the importance of strategic planning in adopting sintered silicon carbide wafer boats. Industries must consider both technical and economic aspects to ensure successful implementation.
Balancing Performance with Environmental Sustainability
Sustainability has become a critical consideration in modern manufacturing. Industries must balance the performance of sintered silicon carbide wafer boats with their environmental impact. The production process consumes significant energy, which raises concerns about carbon emissions. Manufacturers must explore energy-efficient methods to reduce their environmental footprint.
Recycling and reusability offer potential solutions. Silicon carbide’s durability allows for extended use, minimizing waste. Additionally, advancements in recycling technology could enable the recovery of materials from used wafer boats. This approach aligns with global efforts to promote sustainable practices in manufacturing.
Industries can also adopt eco-friendly coatings and treatments to enhance the wafer boats’ performance. These innovations reduce the need for frequent replacements, further supporting sustainability goals. By prioritizing environmental considerations, manufacturers can contribute to a greener future while maintaining high performance.
The Future of Sintered Silicon Carbide Wafer Boats
Trends in Semiconductor and High-Tech Manufacturing
The demand for advanced materials like sintered silicon carbide wafer boats continues to grow in semiconductor and high-tech industries. Several trends are driving this growth:
- The increasing complexity of semiconductor devices requires materials that can endure extreme conditions.
- Manufacturers seek high-performance materials to enhance the efficiency of their processes.
- Durability has become a priority to reduce downtime and improve production reliability.
These trends highlight the critical role of sintered silicon carbide wafer boats in meeting the evolving needs of modern manufacturing. Their ability to withstand high temperatures and resist chemical corrosion makes them indispensable in producing next-generation semiconductor devices. The market for these wafer boats reflects this demand, with projections showing significant growth. For instance, the SiC Boat market, valued at [101millionin2023](https://reports.valuates.com/market−reports/QYRE−Auto−6B12632/global−sic−boat),isexpectedtoreach101 million in 2023](https://reports.valuates.com/market-reports/QYRE-Auto-6B12632/global-sic-boat), is expected to reach 101millionin2023](https://reports.valuates.com/market−reports/QYRE−Auto−6B12632/global−sic−boat),isexpectedtoreach207.5 million by 2030, growing at a compound annual growth rate (CAGR) of 10.5%. Globally, the silicon carbide wafer boats market is projected to expand from [16.5billionin2023](https://www.cnvetenergy.com/ja/silicon−carbide−wafer−boat−comparison−2024/)to16.5 billion in 2023](https://www.cnvetenergy.com/ja/silicon-carbide-wafer-boat-comparison-2024/) to 16.5billionin2023](https://www.cnvetenergy.com/ja/silicon−carbide−wafer−boat−comparison−2024/)to36.21 billion by 2031. This growth underscores the increasing reliance on these materials in high-tech industries.
Role in Sustainable and Energy-Efficient Processes
Sustainability has become a key focus in manufacturing, and sintered silicon carbide wafer boats contribute significantly to this goal. Their design prioritizes longevity, reducing the frequency of replacements and minimizing material waste. This durability not only lowers operational costs but also supports eco-friendly practices by decreasing the environmental impact of manufacturing processes.
In addition, these wafer boats enhance energy efficiency in semiconductor production. Their superior thermal conductivity ensures optimal heat transfer, reducing energy consumption during high-temperature processes. By maintaining consistent performance, they help manufacturers achieve higher yields with less energy input. These qualities make sintered silicon carbide wafer boats a cornerstone of sustainable and energy-efficient manufacturing.
Potential for Recycling and Reusability
The potential for recycling and reusability further enhances the value of sintered silicon carbide wafer boats. Their exceptional durability allows for extended use, reducing the need for frequent replacements. This longevity aligns with global efforts to promote circular economy practices in manufacturing.
Advancements in recycling technology could enable the recovery of silicon carbide from used wafer boats, creating opportunities for material reuse. This approach not only conserves resources but also reduces waste, contributing to a greener manufacturing ecosystem. Industries adopting these practices can achieve both economic and environmental benefits, reinforcing the importance of sintered silicon carbide wafer boats in sustainable development.
Sintered silicon carbide wafer boats play a pivotal role in advancing semiconductor manufacturing and other high-tech industries. Their unique properties make them indispensable in precision applications.
- Excellent thermal stability allows them to endure extreme temperatures exceeding 1000°C without warping.
- High mechanical strength ensures reliable support for wafers during processing.
- Strong chemical resistance maintains wafer purity in corrosive environments.
These wafer boats align with the growing demand for precision and efficiency. They enhance wafer quality and process efficiency, which is vital as devices become smaller and more powerful. Their durability and stability under extreme conditions ensure long-term reliability. As industries continue to innovate, sintered silicon carbide wafer boats will remain essential for meeting future technological challenges.
Anmerkung: Choosing the right wafer boat, considering material purity and design compatibility, can lead to significant cost savings and improved performance.