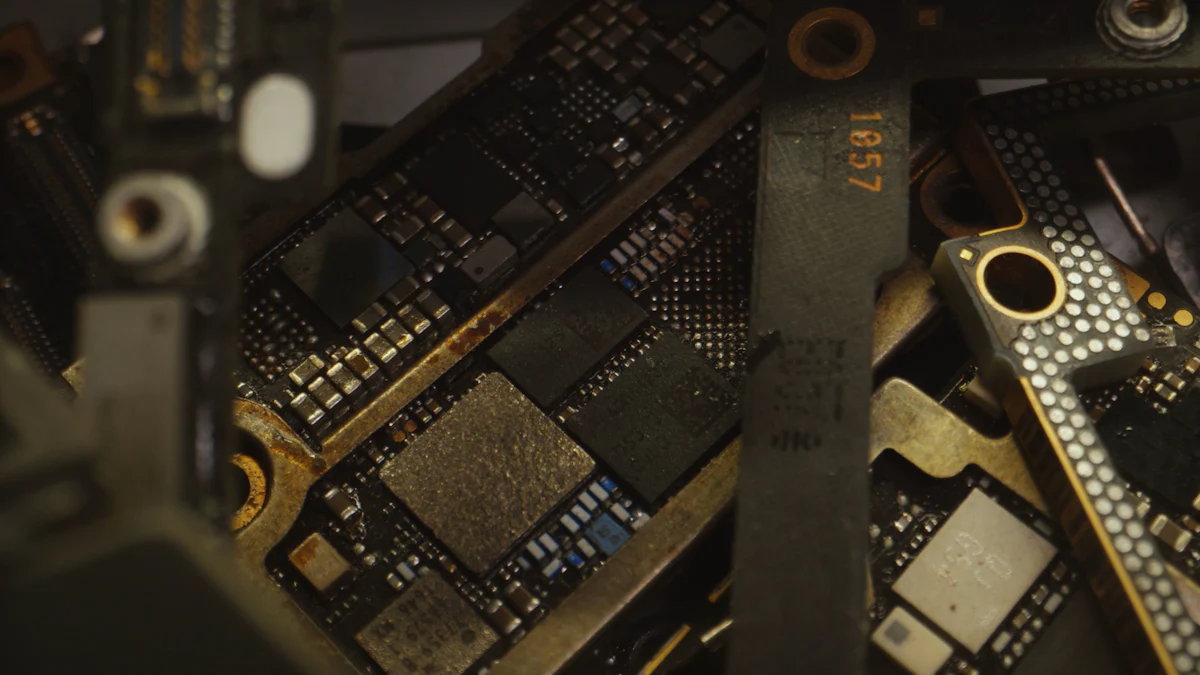
A wafer is a thin slice of semiconductor material, typically silicon, that serves as the foundation for creating integrated circuits. It undergoes multiple processes to form the base for microelectronic devices. In contrast, a chip is a small piece of silicon derived from a wafer, containing intricate circuits that power modern electronics. Together, they form the backbone of semiconductor technology. The wafer boat plays a crucial role in this process by securely holding and transporting wafers during fabrication, ensuring precision and efficiency in manufacturing.
Key Takeaways
- Wafers are the foundational elements in semiconductor manufacturing, serving as the substrate for creating integrated circuits.
- Chips, derived from wafers, are compact units that perform specific electronic functions, making them essential for modern technology.
- The purity and quality of wafers directly impact the performance and reliability of the chips produced from them.
Wafer boats are crucial for securely holding and transporting wafers during manufacturing, ensuring precision and preventing contamination.
Larger wafers increase production efficiency by allowing more chips to be produced from a single slice, reducing costs.
- Understanding the relationship between wafers and chips is key to grasping the complexities of semiconductor technology.
- Advancements in wafer and chip technology drive innovation across various industries, from consumer electronics to healthcare.
What is a Wafer?
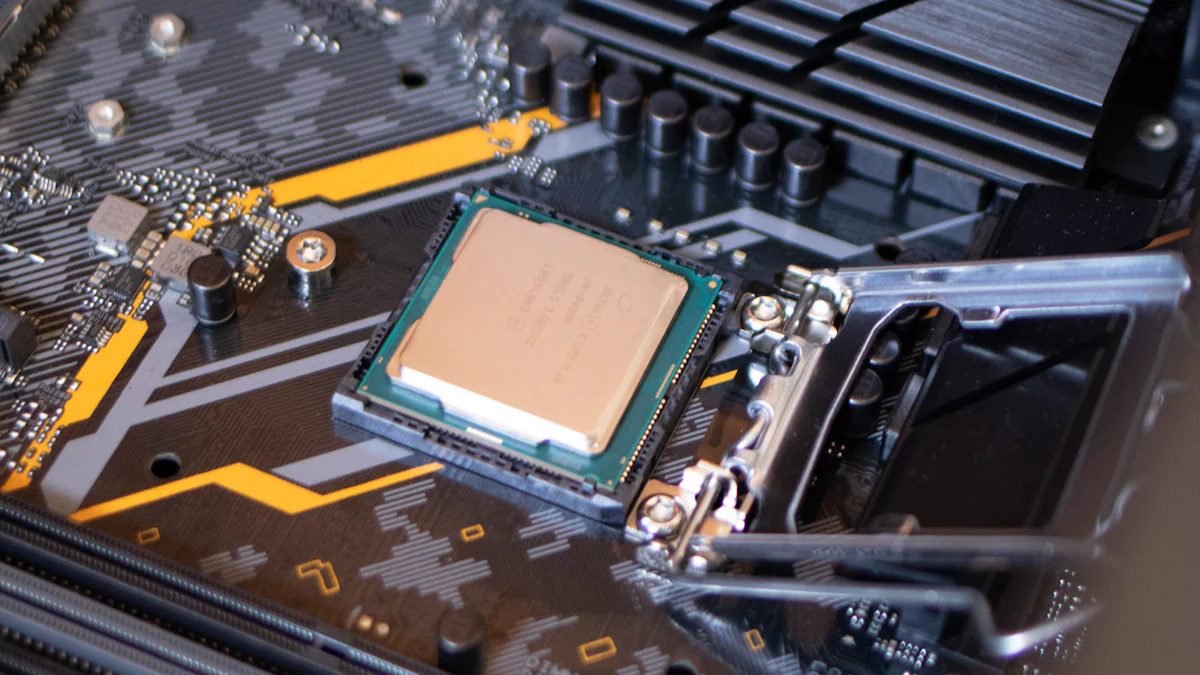
Definition and Material Composition of a Wafer
A wafer is a thin, flat disc made from high-purity semiconductor materials, with silicon being the most commonly used due to its exceptional electrical properties. Manufacturers create wafers by slicing single-crystal silicon ingots into thin slices using precision saws. These slices undergo rigorous chemical and mechanical processes to ensure a smooth surface and uniform thickness. The purity of the silicon plays a critical role in determining the performance and reliability of the semiconductor devices built on these wafers. Even minor impurities can significantly affect the electrical properties, making high-quality materials essential for production.
While silicon dominates the industry, other materials like gallium arsenide (GaAs), silicon carbide (SiC), and gallium nitride (GaN) are also used for specific applications. These materials cater to specialized needs, such as LED manufacturing or high-power electronic devices. The choice of material depends on the desired electrical characteristics and the application requirements.
Role of Wafers in Semiconductor Manufacturing
These steps ensure that the wafer’s surface is free from defects like scratches or contamination, which could compromise the performance of the final product.
How Wafers Serve as the Foundation for Chips
Wafers act as the substrate on which intricate electronic circuits are built. Through processes like photolithography, etching, and deposition, manufacturers imprint complex patterns onto the wafer’s surface. These patterns form the basis of the integrated circuits that power modern electronic devices. Once the circuits are complete, the wafer is diced into individual chips, each containing a unique set of circuits tailored for specific functions.
The size of the wafer directly impacts production efficiency. Larger wafers, such as the industry-standard 300mm diameter wafers, allow for more chips to be produced from a single slice. This reduces production costs and increases output, meeting the growing demand for advanced electronic devices. As technology advances, thinner wafers are becoming increasingly important for compact and energy-efficient devices, achieved through processes like wafer thinning or backgrinding.
What is a Chip?
Definition and Characteristics of a Chip
A chip, also known as a microchip or integrated circuit (IC), is a small piece of semiconductor material, typically silicon, that contains a network of electronic circuits. These circuits perform specific functions, such as processing data, storing information, or controlling devices. Chips are compact, lightweight, and highly efficient, making them essential components in modern electronics.
Manufacturers design chips with precision to meet the demands of various applications. Each chip consists of multiple layers of transistors, resistors, and capacitors, all interconnected to create a functional unit. The size of a chip can vary depending on its purpose, but advancements in technology have enabled the creation of smaller and more powerful chips. This miniaturization has revolutionized industries by enabling the development of portable and high-performance devices.
Role of Chips in Electronics
Chips play a pivotal role in powering electronic devices. They act as the brains of gadgets, enabling them to perform complex tasks with speed and accuracy. Without chips, modern technology would not exist in its current form.
How Chips are Created from Wafers
The journey of a chip begins with a wafer. Manufacturers use wafers as the base material to build intricate circuits. Through a series of processes, including photolithography, etching, and doping, they imprint patterns onto the wafer’s surface. These patterns define the functionality of the circuits.
Once the circuits are complete, the wafer undergoes a dicing process. Precision tools cut the wafer into individual chips, each containing a unique set of circuits. These chips then go through testing to ensure they meet quality standards before being packaged for use in electronic devices. This transformation from wafer to chip highlights the critical relationship between the two components in semiconductor manufacturing.
Examples of Chip Applications in Technology
Chips power a wide range of technologies that shape daily life. Some common applications include:
- Smartphones: Chips enable features like processing power, connectivity, and camera functionality.
- Computers: Central processing units (CPUs) and graphics processing units (GPUs) rely on chips for performance.
- Automobiles: Chips control systems such as navigation, safety features, and engine management.
- Healthcare Devices: Chips drive innovations in medical equipment, including diagnostic tools and wearable health monitors.
- Internet of Things (IoT): Chips connect smart devices, allowing seamless communication and automation.
"Chips are the building blocks of modern technology, enabling innovation across industries."
From powering everyday gadgets to advancing cutting-edge technologies, chips have become indispensable in the digital age. Their versatility and efficiency continue to drive progress in electronics and beyond.
Comparing Wafers and Chips
Differences in Material and Size
Wafers and chips differ significantly in their material composition and physical dimensions. A wafer is a large, circular disk made from high-purity semiconductor materials, such as silicon. Its diameter can range from 150mm to 300mm or more, depending on the manufacturing standards. The wafer’s size allows it to serve as the substrate for creating multiple chips simultaneously. In contrast, a chip is a much smaller unit, typically a few millimeters in size, that is cut from the wafer. Each chip contains intricate circuits designed for specific electronic functions.
The material purity of wafers plays a critical role in determining the performance of the chips derived from them. Even minor impurities in the wafer can compromise the functionality of the chips. Manufacturers ensure that wafers meet stringent quality standards to maintain the reliability of the final products. Chips, on the other hand, are the miniaturized end products that emerge from the wafer, encapsulating the advanced technology within a compact form.
Differences in Functionality
The functionality of wafers and chips also sets them apart. Wafers act as the foundation for semiconductor manufacturing. They provide the surface on which intricate electronic circuits are built through processes like photolithography and etching. Without wafers, the creation of chips would not be possible. Their role is foundational, serving as the starting point for all subsequent manufacturing steps.
Chips, however, are the functional units that power electronic devices. They perform specific tasks, such as processing data, storing information, or controlling systems. For example, a chip in a smartphone might handle tasks like running applications, managing connectivity, or processing images. While wafers are essential for the production process, chips are the components that directly enable the functionality of modern technology.
How Wafers and Chips Work Together in Semiconductor Technology
Wafers and chips share a symbiotic relationship in semiconductor technology. Wafers serve as the substrate on which chips are created, while chips represent the final products that emerge from the wafer. This interdependence highlights the importance of both components in the manufacturing process.
The journey begins with the wafer, which undergoes multiple processes to form the base for electronic circuits. Manufacturers use advanced techniques to imprint intricate patterns onto the wafer’s surface. These patterns define the functionality of the chips that will be produced. Once the circuits are complete, the wafer is diced into individual chips. Each chip is then tested, packaged, and integrated into electronic devices.
"Wafers and chips together drive technological advancements across industries, from consumer electronics to healthcare and automotive systems."
This collaboration between wafers and chips underscores their collective role in shaping the future of technology. Wafers provide the platform, while chips deliver the functionality, making them indispensable in the world of semiconductors.
What is a Wafer Boat?
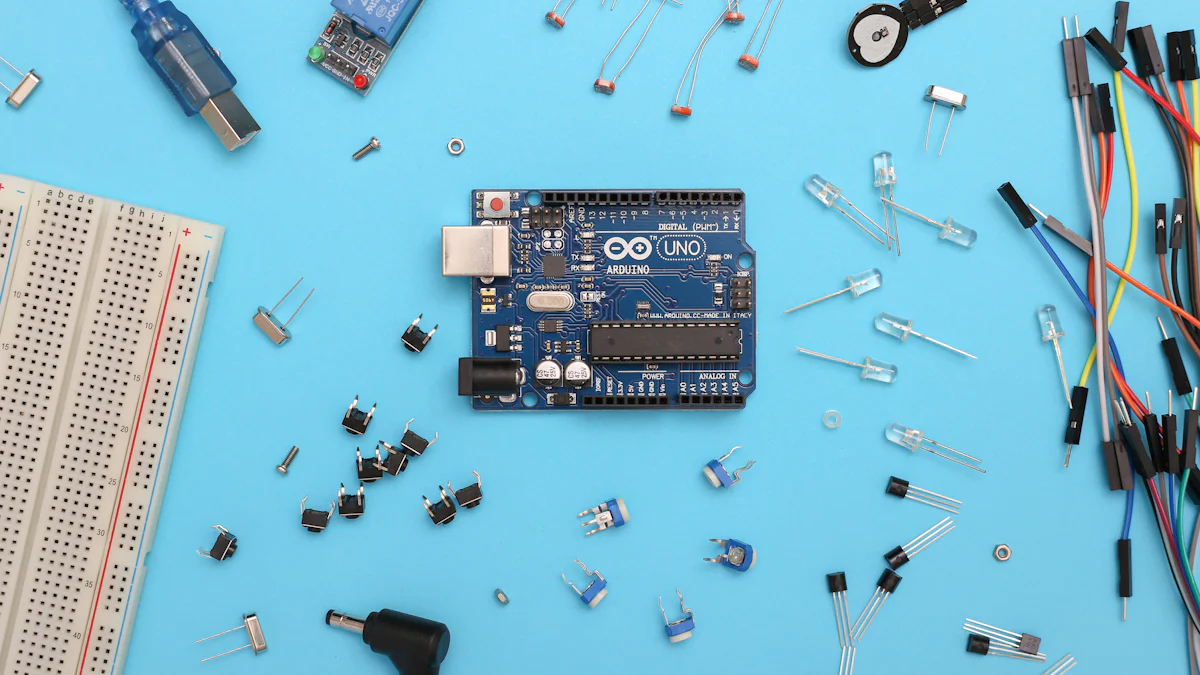
Definition and Purpose of a Wafer Boat
A wafer boat is a specialized device designed to securely hold and transport semiconductor wafers during various stages of the manufacturing process. Made from high-purity, temperature-resistant materials such as silicon carbide or quartz, it ensures that wafers remain stable and uncontaminated throughout high-precision operations. The design of a wafer boat prioritizes durability and precision, as it must withstand extreme temperatures and chemical environments without compromising the integrity of the wafers it carries.
The primary purpose of a wafer boat is to facilitate the safe handling of wafers during critical processes like oxidation, diffusion, and deposition. By providing a stable platform, it minimizes the risk of damage or contamination, which could otherwise compromise the performance of the final semiconductor devices. Its role extends beyond mere transportation; it acts as a crucial component in maintaining the efficiency and accuracy of semiconductor fabrication.
Role of Wafer Boats in Semiconductor Manufacturing
How Wafer Boats Hold and Transport Wafers
Wafer boats are engineered to hold multiple wafers simultaneously, ensuring efficient processing in semiconductor manufacturing facilities. Each wafer fits snugly into a designated slot within the boat, preventing movement or contact with adjacent wafers. This precise arrangement reduces the likelihood of scratches, contamination, or misalignment during handling.
The design of wafer boats often incorporates features that enhance their functionality. For instance, some wafer boats are compatible with advanced transfer tools that allow seamless movement between different equipment. A patented wafer boat transfer tool enables the transportation of multiple boats simultaneously, improving operational efficiency. This innovation eliminates the need for excessive manual handling, reducing the risk of errors and enhancing productivity.
Wafer boats also play a pivotal role in high-temperature processes. Their materials must endure extreme heat without deforming or releasing impurities. This resilience ensures that wafers remain in optimal condition, even during prolonged exposure to harsh environments.
Importance of Wafer Boats in High-Precision Processes
In semiconductor manufacturing, precision is paramount. Wafer boats contribute significantly to achieving this precision by maintaining the exact positioning of wafers during critical processes. For example, during oxidation or diffusion, the uniform spacing provided by the wafer boat ensures consistent exposure to gases or chemicals, resulting in uniform layer deposition across all wafers.
The importance of wafer boats becomes even more evident in high-density and high-integration semiconductor designs. As the demand for smaller and more powerful chips grows, the need for flawless wafer processing intensifies. Wafer boats help meet these stringent requirements by enabling precise control over wafer placement and movement. A patented method for positioning crystal boat lifting movement highlights the advancements in wafer boat technology, ensuring accurate unloading from vertical oxidation furnaces. Such innovations underscore the critical role wafer boats play in maintaining the quality and reliability of semiconductor devices.
"Wafer boats are not just carriers; they are enablers of precision and efficiency in semiconductor manufacturing."
By holding wafers securely and facilitating their seamless transport, wafer boats ensure that every step of the manufacturing process adheres to the highest standards. Their contribution to high-precision processes makes them indispensable in the production of advanced semiconductor technologies.
Wafers and chips form the backbone of semiconductor technology. Wafers act as the substrate for creating integrated circuits, while chips emerge as the final products that power electronic devices. This relationship highlights their critical roles in the electronics industry. The wafer boat ensures precision and efficiency during manufacturing by securely holding and transporting wafers through high-precision processes. Together, these components drive advancements in technology, enabling the production of innovative and reliable electronic devices.
FAQ
What is a wafer?
A wafer is a thin, circular slice of semiconductor material, typically silicon, that serves as the foundation for creating integrated circuits (ICs). These wafers undergo chemical and mechanical processes to ensure a smooth surface and uniform thickness. They act as the platform where intricate patterns of transistors, resistors, and interconnects are created during semiconductor fabrication. Wafers play a pivotal role in producing chips used in electronic devices like smartphones, computers, and automobiles.
"Wafers are the backbone of semiconductor technology, enabling the creation of advanced electronic components."
How are wafers related to chips and dies?
Wafers, chips, and dies are interconnected in semiconductor manufacturing. A wafer contains multiple chips, also known as dies, which are small sections of the wafer. Each die houses intricate circuits designed for specific functions. Manufacturers dice the wafer into individual dies, which then become chips after packaging. This relationship highlights the wafer as the starting point for creating chips that power modern electronics.
Why is silicon the most commonly used material for wafers?
Silicon dominates wafer production due to its exceptional semiconductor properties. It offers high purity, excellent electrical conductivity, and cost-effectiveness. Silicon’s abundance in nature, found in rocks and sand as silica or silicates, makes it an ideal choice. Its diamond cubic crystal structure ensures stability and precision during manufacturing, enabling the creation of reliable and efficient semiconductor devices.
What processes do wafers undergo during manufacturing?
Wafers go through several critical steps during manufacturing:
- Silicon Purification and Refining: Extracting high-purity silicon from raw materials.
- Single-Crystal Silicon Growth: Forming a single-crystal silicon ingot using methods like the Czochralski process.
- Wafer Formation: Slicing the ingot into thin wafers, followed by polishing and cleaning to achieve uniform thickness and a defect-free surface.
These processes ensure that wafers meet the stringent quality standards required for semiconductor production.
What is the role of a wafer boat in semiconductor manufacturing?
A wafer boat securely holds and transports wafers during various stages of semiconductor fabrication. Made from high-purity, temperature-resistant materials like silicon carbide or quartz, it ensures wafers remain stable and uncontaminated.
How do chips differ from wafers?
Wafers serve as the substrate for creating chips, while chips are the final products derived from wafers. A wafer is a large, circular disk containing multiple chips, whereas a chip is a small, rectangular piece cut from the wafer. Chips contain intricate circuits that perform specific functions, such as processing data or controlling devices, making them essential components in modern electronics.
What industries rely on semiconductor wafers?
Semiconductor wafers drive technological advancements across various industries, including: – Consumer Electronics: Smartphones, laptops, and gaming consoles. – Automotive: Advanced driver-assistance systems (ADAS) and engine management. – Healthcare: Diagnostic tools and wearable health monitors. – Energy: Silicon carbide dummy wafers and power management systems.
- Consumer Electronics: Smartphones, laptops, and gaming consoles.
- Automotive: Advanced driver-assistance systems (ADAS) and engine management.
- Healthcare: Diagnostic tools and wearable health monitors.
- Energy: Solar panels and power management systems.
Their versatility makes them indispensable in the modern digital age.
How does wafer size impact production efficiency?
Larger wafers, such as 300mm diameter wafers, allow manufacturers to produce more chips from a single slice. This increases production efficiency and reduces costs. As technology advances, thinner wafers are becoming essential for compact and energy-efficient devices, achieved through processes like wafer thinning or backgrinding.
What are some common applications of chips?
Chips power a wide range of technologies, including:
- Smartphones: Enabling processing power, connectivity, and camera functionality.
- Computers: Supporting CPUs and GPUs for performance.
- Automobiles: Managing navigation, safety features, and engine control.
- IoT Devices: Connecting smart devices for seamless communication.
"Chips are the building blocks of modern technology, driving innovation across industries."
Why is precision important in semiconductor manufacturing?
Precision ensures the reliability and performance of semiconductor devices. Processes like photolithography, etching, and doping require exact alignment and uniformity. Tools like wafer boats maintain the precise positioning of wafers, ensuring consistent results. High precision becomes even more critical as demand grows for smaller, more powerful chips in advanced technologies.