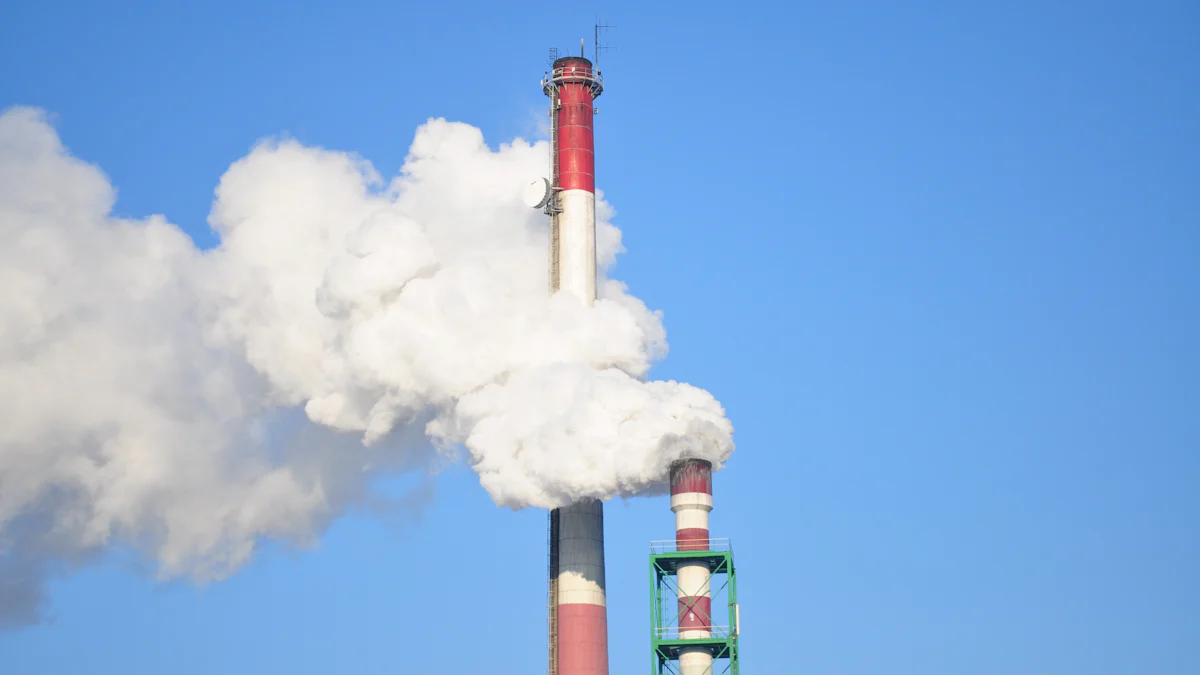
Durability plays a pivotal role in industrial applications, where materials face extreme conditions and demanding processes. SiC coated graphite carriers emerge as a groundbreaking solution, offering exceptional resilience in harsh environments. These carriers combine the strength of graphite with the protective properties of silicon carbide, ensuring superior performance. Industries such as semiconductor manufacturing rely on these carriers to maintain high efficiency and reliability. Their ability to resist wear, oxidation, and contamination makes them indispensable for critical operations, extending equipment lifespan and reducing maintenance costs.
Key Takeaways
- SiC coated graphite carriers combine the lightweight strength of graphite with the protective properties of silicon carbide, making them ideal for extreme industrial conditions.
- The exceptional thermal stability of SiC coatings allows these carriers to withstand rapid temperature changes, ensuring reliability in high-temperature processes like semiconductor manufacturing.
- Their mechanical strength and resistance to wear and chemical corrosion significantly extend the lifespan of the carriers, reducing maintenance costs and operational disruptions.
- Precision engineering in the design of SiC coated graphite carriers minimizes defects during critical operations, enhancing overall production efficiency.
- Regular maintenance practices, such as inspections and proper cleaning, are essential to maximize the longevity and performance of SiC coated graphite carriers.
- Industries such as semiconductor manufacturing, aerospace, and chemical processing benefit greatly from the durability and reliability of SiC coated graphite carriers, making them a cost-effective solution.
Understanding SiC Coated Graphite Carriers
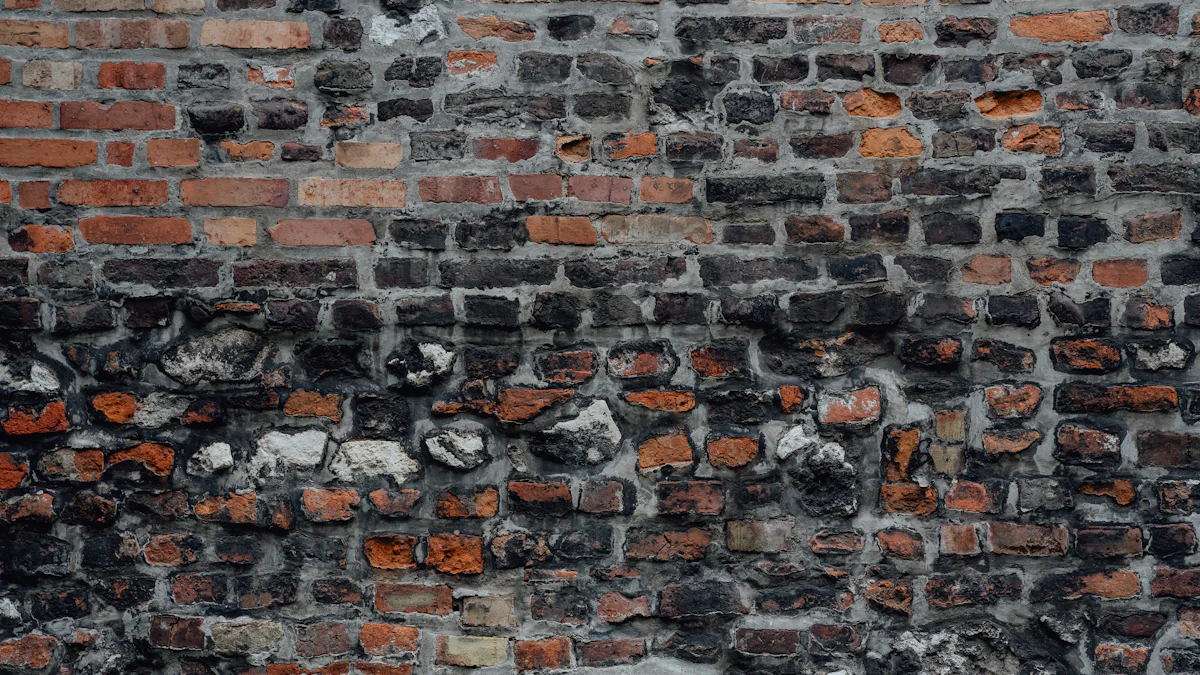
Composition and Structure
SiC coated graphite carriers combine two advanced materials to achieve exceptional performance. The core consists of highly purified isotropic graphite, known for its lightweight nature and excellent thermal conductivity. This graphite core undergoes a precise coating process using silicon carbide (SiC), typically applied through the Chemical Vapor Deposition (CVD) method. This process ensures a uniform and fine SiC layer that adheres tightly to the graphite substrate.
The SiC coating enhances the carrier’s properties by adding a robust protective layer. Silicon carbide, with its high melting point and superior hardness, provides resistance to wear, oxidation, and chemical corrosion. This combination of materials results in a carrier that can withstand extreme temperatures and harsh environments, making it ideal for demanding industrial applications.
Key Features Enhancing Durability
Several features contribute to the durability of SiC coated graphite carriers, ensuring their reliability in critical operations:
-
Thermal Stability: The SiC coating offers exceptional resistance to thermal shock, maintaining structural integrity even under rapid temperature changes. This makes the carriers suitable for high-temperature processes like semiconductor manufacturing and epitaxy.
-
Mechanical Strength: The combination of graphite’s inherent strength and the SiC coating’s hardness ensures superior mechanical durability. This allows the carriers to endure operational stress without deformation or damage.
-
Chemical Resistance: The impervious nature of the SiC layer protects the graphite core from chemical reactions, including oxidation and corrosion. This feature is particularly valuable in environments involving aggressive chemicals or reactive gases.
-
Precision Engineering: Manufacturers like Mersen design these carriers with exact specifications to ensure uniformity and alignment during processes such as wafer handling. This precision minimizes defects and enhances the overall efficiency of production.
-
Long Lifespan: The robust construction and resistance to wear extend the lifespan of these carriers, reducing the need for frequent replacements. This durability translates into cost savings and improved operational efficiency.
SiC coated graphite carriers stand out as a reliable solution for industries requiring high-performance materials. Their unique composition and advanced features make them indispensable in applications where durability and precision are paramount.
Properties That Contribute to Durability
Thermal Resistance
Thermal resistance plays a crucial role in the durability of SiC coated graphite carriers. The silicon carbide (SiC) coating provides exceptional heat resistance, enabling these carriers to maintain their structural integrity under extreme temperatures.
The low thermal expansion of graphite, combined with the high melting point of SiC, ensures minimal deformation during rapid temperature fluctuations. This synergy allows the carrier to withstand thermal shocks without compromising its functionality. Furthermore, the SiC layer enhances thermal conductivity, ensuring uniform heat distribution across the carrier’s surface. This characteristic reduces the risk of localized overheating, which could otherwise lead to material degradation.
Scientific Research Findings: Studies highlight that SiC coatings significantly enhance the thermal stability of graphite materials, making them indispensable for advanced semiconductor fabrication processes.
Mechanical Strength
Mechanical strength is another defining feature of SiC coated graphite carriers. The combination of a robust graphite core and a hard SiC coating creates a carrier capable of withstanding substantial operational stress.
The SiC coating’s superior hardness protects the graphite substrate from wear and abrasion, extending the carrier’s lifespan. This durability is essential in applications where repeated use and constant handling are required. Additionally, the precise engineering of these carriers ensures dimensional stability, which is critical for maintaining alignment and accuracy in high-precision operations.
Scientific Research Findings: Research confirms that SiC coatings effectively improve the wear resistance of graphite materials, ensuring long-term reliability in harsh environments.
Chemical Stability
Chemical stability is a key factor contributing to the longevity of SiC coated graphite carriers. The impervious nature of the SiC layer shields the graphite core from chemical reactions, including oxidation and corrosion. This resistance is vital in environments involving aggressive chemicals or reactive gases, such as those found in semiconductor and aerospace industries.
The SiC coating acts as a barrier, preventing contaminants from penetrating the graphite substrate. This protection ensures that the carrier retains its structural and functional properties over time. Moreover, the high purity of the SiC layer minimizes the risk of contamination during sensitive processes, such as wafer fabrication.
Scientific Research Findings: Studies indicate that SiC coatings provide excellent corrosion resistance, enhancing the durability of graphite materials in chemically aggressive settings.
The combination of thermal resistance, mechanical strength, and chemical stability makes SiC coated graphite carriers a reliable choice for demanding industrial applications. These properties ensure consistent performance, reduce maintenance requirements, and extend the lifespan of the carriers, making them a cost-effective solution for industries requiring high durability.
Factors Influencing the Durability of SiC Coated Graphite Carriers
Environmental Conditions
Environmental factors significantly impact the durability of SiC coated graphite carriers. High-temperature environments, such as those found in semiconductor manufacturing, demand materials that can withstand extreme heat without degradation. The silicon carbide coating provides excellent thermal stability, ensuring the carrier maintains its structural integrity under such conditions. However, exposure to rapid temperature fluctuations can challenge even the most durable materials. The low thermal expansion of graphite, combined with the high melting point of silicon carbide, minimizes the risk of cracking or warping during these fluctuations.
In addition to temperature, chemical exposure also plays a critical role. Industries involving reactive gases or aggressive chemicals require carriers with robust chemical resistance. The impervious nature of the SiC coating protects the graphite core from oxidation and corrosion, ensuring long-term reliability. Dust, moisture, and other environmental contaminants can also affect performance. Proper maintenance and storage conditions help mitigate these risks, preserving the carrier’s functionality over time.
Operational Stress
Operational stress directly influences the lifespan of SiC coated graphite carriers. Repeated handling, heavy loads, and mechanical impacts during industrial processes can cause wear and tear. The combination of a strong graphite core and a hard silicon carbide coating ensures these carriers endure such stresses without significant damage. This mechanical strength is essential for applications requiring precision and consistency, such as wafer handling in semiconductor production.
The frequency and intensity of use also determine the carrier’s durability. Continuous operation in demanding environments accelerates material fatigue. Regular inspections and adherence to operational guidelines can help identify early signs of wear, preventing unexpected failures. Proper alignment and handling techniques further reduce stress on the carrier, extending its service life.
Material and Coating Quality
The quality of materials and coatings used in manufacturing directly affects the durability of SiC coated graphite carriers. High-purity isotropic graphite forms the foundation of a reliable carrier. This type of graphite offers superior thermal conductivity and structural stability, making it an ideal substrate for silicon carbide coatings. The coating process, typically performed using the Chemical Vapor Deposition (CVD) method, must ensure a uniform and tightly bonded SiC layer. Any inconsistencies in the coating can compromise the carrier’s performance and lifespan.
Manufacturers prioritize precision engineering to meet industry standards. Variations in raw material quality or production techniques can lead to differences in durability. For instance, silicon carbide carriers outperform conventional graphite carriers in high-temperature applications due to their enhanced thermal properties. These carriers also exhibit better resistance to wear and chemical exposure, making them a preferred choice for demanding industries.
Market Insight: The final price of SiC coated graphite carriers reflects the quality of raw materials and the precision of the manufacturing process. Investing in high-quality carriers ensures long-term cost savings by reducing maintenance and replacement needs.
By understanding these factors, industries can optimize the use of SiC coated graphite carriers, ensuring consistent performance and extended service life. Proper selection, maintenance, and operational practices play a vital role in maximizing their durability.
Applications of SiC Coated Graphite Carriers in Demanding Industries
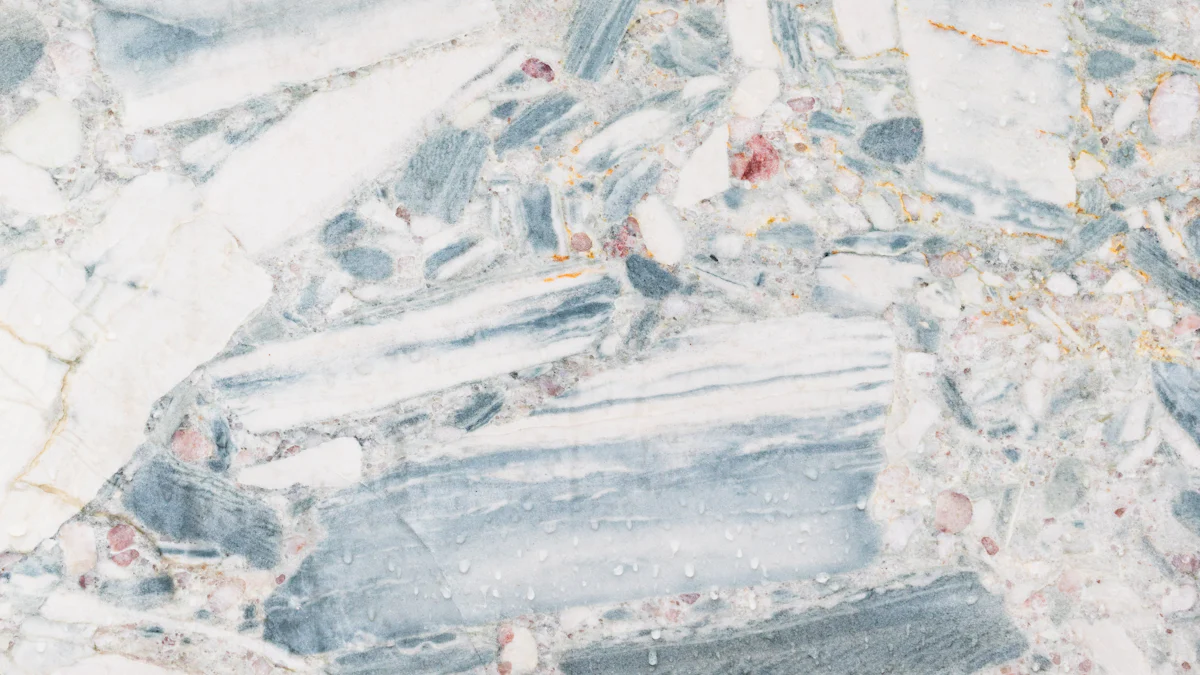
Semiconductor Manufacturing
The semiconductor industry demands precision and reliability in every stage of production. SiC coated graphite carriers play a pivotal role in processes such as epitaxy, chemical vapor deposition (CVD), and rapid thermal processing (RTP). These carriers provide a stable platform for wafers, ensuring uniform heat distribution and minimizing contamination risks. The ultra-high purity of the SiC coating prevents impurities from interfering with the delicate fabrication of semiconductor devices.
The exceptional thermal conductivity of these carriers ensures consistent temperature control, which is critical for forming epitaxial layers on wafers. Their resistance to oxidation and chemical corrosion further enhances their suitability for semiconductor manufacturing. For instance, products like the SGL Carbon SIGRAFINE SiC-Coated Graphite Wafer Carrier are specifically engineered to meet the rigorous demands of this industry. These carriers maintain structural integrity under extreme conditions, ensuring long-term reliability and efficiency.
Industry Insight: The use of SiC coated graphite carriers in semiconductor manufacturing reduces maintenance needs and extends equipment lifespan, making them a cost-effective solution for high-precision applications.
High-Temperature Environments
High-temperature environments require materials that can withstand extreme heat without compromising performance. SiC coated graphite carriers excel in such conditions due to their superior thermal stability and resistance to thermal shock. The combination of a graphite core and a silicon carbide coating allows these carriers to endure rapid temperature fluctuations without cracking or warping.
Applications in high-temperature environments include aerospace, heating technologies, and industrial furnaces. The CVD silicon carbide coating provides a dense, impervious layer that protects the graphite substrate from oxidation and wear. This makes the carriers ideal for processes involving high-energy plasma or reactive gases. Their ability to maintain structural integrity under harsh conditions ensures consistent performance and reduces downtime in critical operations.
Product Highlight: CVD silicon carbide-coated graphite trays, known for their mirror-like surfaces and ultra-high purity, are widely used in high-vacuum and high-temperature settings, ensuring optimal performance in demanding applications.
Other Industrial Applications
Beyond semiconductors and high-temperature environments, SiC coated graphite carriers find applications in various other industries. Their chemical resistance and durability make them suitable for use in chemical processing, where exposure to aggressive chemicals is common. The impervious SiC layer protects the graphite core, ensuring long-term reliability even in corrosive settings.
In the energy sector, these carriers support processes that involve high thermal loads and mechanical stress. Their lightweight nature and robust construction make them an excellent choice for applications requiring both strength and precision. Additionally, industries focusing on ultra-clean environments, such as medical device manufacturing, benefit from the carriers’ ability to minimize contamination risks.
Market Insight: The versatility of SiC coated graphite carriers allows them to adapt to diverse industrial needs, providing a reliable solution for applications requiring high durability and precision.
SiC coated graphite carriers demonstrate exceptional durability through their unique combination of thermal resistance, mechanical strength, and chemical stability. These properties enable them to withstand harsh environments and demanding industrial processes. Their ability to resist wear, oxidation, and corrosion ensures extended lifespans and consistent performance in critical applications.
Industries like semiconductor manufacturing benefit significantly from these carriers. They enhance thermal management, maintain structural integrity, and ensure process purity. By reducing maintenance needs and operational disruptions, SiC coated graphite carriers provide a cost-effective and reliable solution for high-performance requirements. Their role in advancing industrial efficiency remains indispensable.
FAQ
What are SiC coated graphite carriers?
SiC coated graphite carriers are advanced industrial components combining a graphite core with a silicon carbide (SiC) coating. The graphite provides lightweight properties and excellent thermal conductivity, while the SiC coated graphite carriers enhances durability by offering resistance to wear, oxidation, and chemical corrosion.
Why are SiC coated graphite carriers preferred in semiconductor manufacturing?
Semiconductor manufacturing demands precision, reliability, and contamination-free processes. SiC coated graphite carriers meet these requirements by providing a stable platform for wafers during processes like chemical vapor deposition (CVD) and epitaxy. The ultra-high purity of the SiC coating prevents impurities from interfering with wafer fabrication. Additionally, their thermal stability ensures consistent temperature control, which is critical for forming epitaxial layers.
How does the SiC coating enhance the durability of graphite carriers?
The SiC coating acts as a protective layer that shields the graphite core from external factors. It provides exceptional resistance to thermal shock, mechanical stress, and chemical reactions. This coating also prevents oxidation and corrosion, ensuring the carrier maintains its structural integrity over time. The combination of these properties significantly extends the lifespan of the carriers, making them a cost-effective solution for demanding applications.
What industries benefit from using SiC coated graphite carriers?
SiC coated graphite carriers are essential in several industries, including:
- Semiconductor manufacturing: Used in wafer handling and high-precision processes.
- Aerospace: Suitable for high-temperature and high-vacuum environments.
- Chemical processing: Resistant to aggressive chemicals and reactive gases.
- Heating technologies: Ideal for industrial furnaces and plasma-based applications.
Their versatility makes them a reliable choice for any industry requiring durable and high-performance materials.
How do environmental conditions affect the performance of these carriers?
Environmental factors such as temperature, chemical exposure, and contaminants can influence the performance of SiC coated graphite carriers. High temperatures demand materials with excellent thermal stability, which the SiC coating provides. The impervious nature of the coating protects against oxidation and corrosion in chemically aggressive settings. Proper maintenance and storage conditions help mitigate risks from dust, moisture, and other contaminants.
What maintenance practices ensure the longevity of SiC coated graphite carriers?
To maximize the lifespan of SiC coated graphite carriers, industries should follow these maintenance practices:
- Regular inspections to identify early signs of wear or damage.
- Proper cleaning to remove contaminants without damaging the SiC coating.
- Adherence to operational guidelines to minimize mechanical stress.
- Storage in controlled environments to prevent exposure to moisture or dust.
These practices help maintain the carrier’s functionality and reduce the need for frequent replacements.
Are there any alternatives to SiC coated graphite carriers?
While alternatives like pure graphite or ceramic carriers exist, they often lack the combined benefits of SiC coated graphite carriers. Pure graphite may not offer sufficient chemical resistance, and ceramics can be brittle under mechanical stress. SiC coated graphite carriers provide a balanced solution with superior thermal, mechanical, and chemical properties, making them the preferred choice for demanding applications.
How does the quality of materials impact the performance of these carriers?
A uniform and tightly bonded SiC coating, typically applied through the Chemical Vapor Deposition (CVD) method, enhances durability.
What makes SiC coated graphite carriers a cost-effective solution?
SiC coated graphite carriers offer a long lifespan due to their resistance to wear, oxidation, and chemical corrosion. This durability reduces the frequency of replacements and maintenance costs. Their ability to maintain consistent performance in critical applications minimizes operational disruptions, further contributing to cost savings. Industries benefit from their reliability and efficiency, making them a valuable investment.
Who are the leading manufacturers of SiC coated graphite carriers?
Several manufacturers specialize in producing high-quality SiC coated graphite carriers. Companies like Mersen and SGL Carbon are recognized for their precision-engineered products tailored to meet industry standards. These manufacturers prioritize material quality and advanced coating techniques to ensure durability and performance. Market trends indicate a growing demand for these carriers, reflecting their importance in industrial applications.