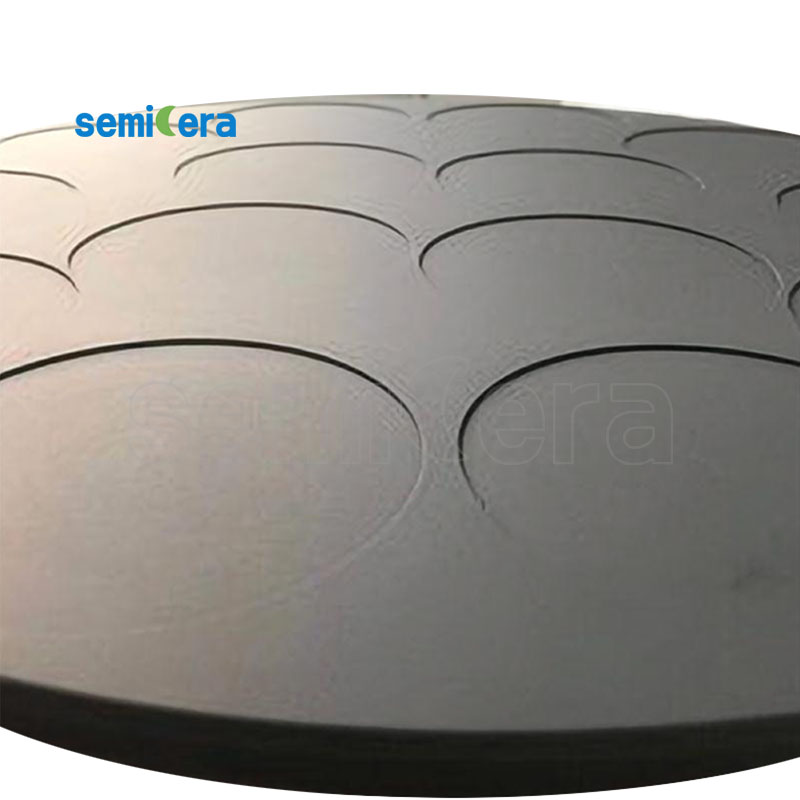
Advanced materials play a crucial role in ensuring the safety and efficiency of nuclear power plants. Among these, CVD SiC Coating Graphite emerges as a groundbreaking innovation. Its ability to withstand extreme conditions makes it a preferred choice for graphite nuclear parts. Studies have demonstrated its transformative impact:
- SiC/SiC composites showed minimal reduction in mechanical properties after neutron irradiation, with Young’s moduli reduced by only up to 18%.
- The swelling behavior of CVD SiC under irradiation revealed slight anisotropy due to microcracking and fiber architecture, proving its durability.
This technology addresses critical challenges in Korean nuclear power plants. It enhances the resilience of components, ensuring long-term operational reliability.
Key Takeaways
- CVD SiC coatings make nuclear parts stronger by handling heat, radiation, and chemicals. This keeps them working well for a long time.
- These coatings lower repair needs and help parts last longer. This improves how nuclear power plants work.
- Special tests prove CVD SiC coatings work well in tough conditions. They meet safety rules for nuclear use.
- CVD SiC coatings are better than older materials. They protect against rust and heat damage, making reactors safer.
- More industries are using CVD SiC technology quickly. This shows it can help improve materials in the future.
Challenges in Nuclear Power Plant Components
High-temperature stress and thermal degradation
Nuclear power plant components operate under extreme temperatures. These conditions cause thermal stress, which can lead to material deformation or failure. High-temperature environments also accelerate thermal degradation, reducing the lifespan of critical parts. Studies have shown that accurate temperature measurement is essential for evaluating thermal stress. For example, a numerical simulation of nuclear piping highlighted the importance of local temperature data in assessing stress levels. This research used computational fluid dynamics and Green’s function to analyze the effects of heat on materials.
Study Title | Focus | Findings |
---|---|---|
Numerical simulation of temperature and thermal stress for nuclear piping | High-temperature stress effects on nuclear piping | Evaluates thermal stress using computational fluid dynamics and Green’s function, highlighting the importance of accurate local temperature measurement and its impact on thermal stress evaluation. |
Innovative materials like CVD SiC Coating Graphite provide a solution. These coatings enhance the thermal stability of components, ensuring they perform reliably even under extreme conditions.
Radiation-induced material wear
Radiation exposure significantly impacts the durability of nuclear components. Over time, radiation causes structural changes in materials, leading to wear and reduced performance. Advanced modeling and experimental techniques have improved the understanding of these degradation mechanisms. Researchers use tools like ion beam accelerators and computational studies to examine how materials respond to radiation. Post-irradiation annealing studies also reveal insights into thermal stability, helping optimize material performance.
- Advanced modeling methodologies and characterization techniques enhance the understanding of degradation mechanisms in nuclear materials.
- Post-irradiation annealing behavior is crucial for understanding thermal stability and optimizing annealing protocols.
- Laboratory ion beam accelerators and computational studies investigate material responses under irradiation.
CVD SiC Coating Graphite offers superior resistance to radiation-induced wear. Its robust structure minimizes damage, extending the operational life of nuclear components.
Corrosion and chemical instability in reactor environments
Reactor environments expose materials to corrosive chemicals and high humidity. These conditions weaken components, compromising their safety and efficiency. Material selection plays a critical role in addressing this challenge. Engineers must choose materials that resist corrosion while maintaining structural integrity. The table below summarizes key challenges in nuclear power plant component durability.
Challenge Type | Description |
---|---|
Material Selection | The choice of materials is critical for ensuring the longevity and reliability of components in nuclear power plants. |
Irradiation Effects | Components are subjected to radiation, which can degrade materials over time, impacting their durability. |
Advanced Engineering Solutions | There is a need for innovative engineering approaches to enhance the durability of components under operational stresses. |
CVD SiC Coating Graphite excels in such environments. Its chemical stability and corrosion resistance make it an ideal choice for reactor components, ensuring long-term reliability.
The demand for long-term reliability and safety
Nuclear power plants require components that can perform reliably over extended periods. The demand for long-term reliability stems from the critical role these facilities play in energy production and public safety. Any failure in key components could lead to significant risks, including operational downtime or safety hazards. Engineers and researchers prioritize materials and technologies that enhance durability and reduce the likelihood of failure.
Probabilistic Safety Assessments (PSA) provide a systematic approach to evaluating risks in nuclear power plants. These assessments use quantitative methodologies to identify potential failure scenarios and their consequences. Key techniques include Event Tree Analysis (ETA) and Fault Tree Analysis (FTA). ETA examines the sequence of events following an initiating incident, while FTA identifies root causes of system failures. Together, these methods offer a comprehensive understanding of risks, enabling engineers to design safer systems.
Note: Data collection and sensitivity analysis are essential components of PSA. They ensure that risk evaluations are based on accurate and reliable information.
CVD SiC Coating Graphite addresses the need for long-term reliability by offering exceptional durability. Its resistance to high temperatures, radiation, and chemical corrosion ensures that components maintain their integrity over time. This technology minimizes wear and degradation, reducing the frequency of maintenance and replacement. By extending the lifespan of critical parts, it contributes to the overall safety and efficiency of nuclear power plants.
The integration of advanced materials like CVD SiC Coating Graphite aligns with the industry’s focus on safety and reliability. These innovations not only meet current demands but also set a foundation for future advancements in nuclear technology.
Understanding CVD SiC Coating Technology
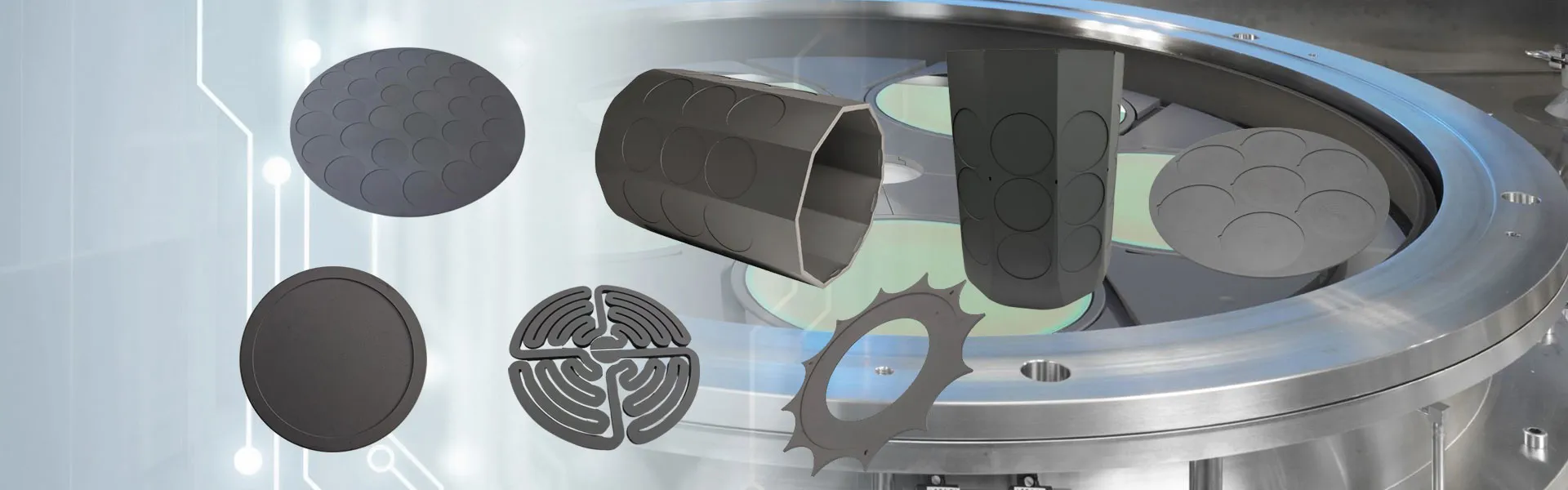
The Chemical Vapor Deposition (CVD) process explained
Chemical Vapor Deposition (CVD) is a sophisticated technique used to create high-performance coatings. This process involves the reaction of gaseous precursors in a controlled environment. These gases decompose or react on a heated substrate, forming a thin, solid coating layer. The temperature and pressure within the chamber are carefully regulated to ensure uniform deposition.
CVD offers several advantages over other coating methods. It allows precise control over the thickness, composition, and structure of the coating. This precision ensures that the resulting material meets the specific requirements of demanding applications, such as those in nuclear reactors. Additionally, CVD can deposit a wide range of materials, including ceramics like silicon carbide (SiC), which are known for their exceptional hardness and durability.
Tip: The ability to customize coatings makes CVD a preferred choice for industries requiring high-performance materials.
Properties of CVD SiC coatings: thermal, chemical, and mechanical
CVD SiC coatings exhibit remarkable properties that make them ideal for nuclear applications. These coatings demonstrate exceptional thermal stability, maintaining their integrity even at extreme temperatures. For instance, studies show that the hardness of CVD SiC coatings remains high, with values of 29 GPa at 1300°C and 23 GPa at 1350°C. The modulus also stays robust, measuring 316 GPa at 1300°C and 283 GPa at 1350°C. These properties ensure that the coatings can withstand the intense heat generated in nuclear reactors.
Property | Value at 1300°C | Value at 1350°C |
---|---|---|
Hardness (GPa) | 29 | 23 |
Modulus (GPa) | 316 | 283 |
Creep Behavior | Observed | Not specified |
Grain Size (µm) | 0.2 – 0.4 | 0.5 – 1.0 |
Orientation | [111] | [220] |
Chemically, CVD SiC coatings resist corrosion and maintain stability in harsh environments. This resistance makes them suitable for reactor components exposed to corrosive chemicals. Mechanically, these coatings offer high strength and reliability. Internal pressurization tests reveal that their strength correlates with microstructure and deposition temperature. The Weibull modulus, a measure of coating reliability, also highlights their effectiveness in maintaining structural integrity.
Property | Measurement Method | Findings |
---|---|---|
Strength | Internal Pressurization | Discussed in relation to microstructure and deposition temperature |
Weibull Modulus | Measured | Correlated with effective surface area and coating reliability |
Benefits of CVD SiC Coating Graphite over traditional materials
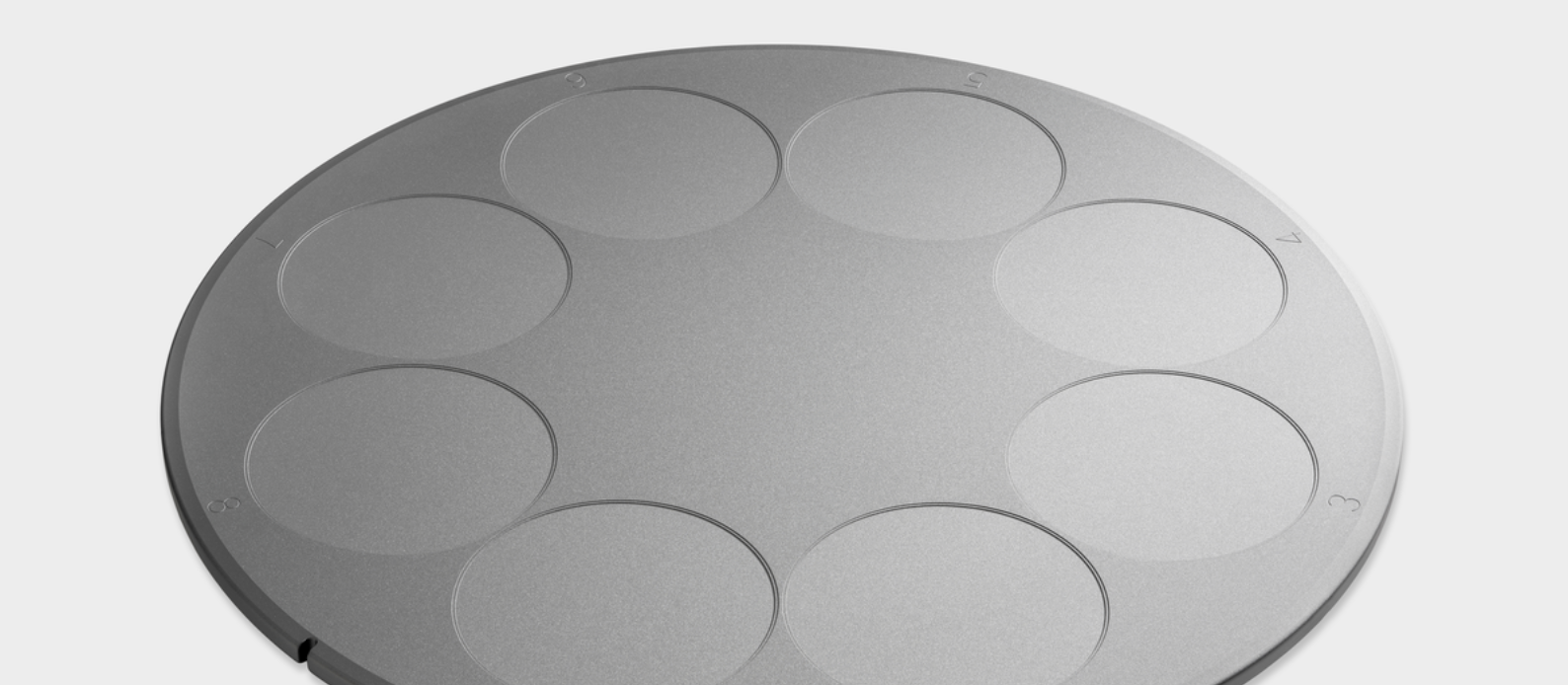
CVD SiC Coating Graphite offers significant advantages over traditional materials. One major benefit is its ability to reduce the infiltration of molten fluoride salt into graphite. Studies show that modified graphite (IG-110-2) with CVD SiC coating limits infiltration to just 0.26 wt% under 5 atm, compared to 13.5 wt% in uncoated graphite under 1.5 atm. This reduction enhances the material’s performance in nuclear environments.
- The SiC/glassy carbon composite coating provides superior resistance to molten salt infiltration, making it an excellent protective layer for nuclear graphite.
- Modified IG-110 with SiC coating demonstrates better oxidation resistance and molten salt barrier properties than bare IG-110. This improvement results from the dense SiC coating and the filling effect of SiC particles in the pores.
- SiC coatings are critical for protecting carbon-based materials in nuclear reactors. Their corrosion resistance and compatibility with thermal expansion properties ensure long-term reliability.
CVD SiC coatings also outperform other coating methods due to the precision of the CVD process. This method allows for exact control over the coating’s composition, thickness, and morphology. The resulting coatings are exceptionally hard and impermeable, providing effective protection against corrosion and wear. These qualities make CVD SiC Coating Graphite a superior choice for nuclear applications.
Applications of CVD SiC coatings in various industries
CVD SiC coatings have revolutionized multiple industries by offering unmatched durability, thermal stability, and chemical resistance. Their unique properties make them indispensable in environments where materials face extreme conditions. Below are some key industries where these coatings play a vital role:
1. Nuclear Energy
CVD SiC coatings enhance the performance of critical components in nuclear reactors. These coatings protect graphite parts from radiation damage, chemical corrosion, and high-temperature stress. Their ability to maintain structural integrity under extreme conditions ensures the safety and efficiency of nuclear power plants.
Example: In molten salt reactors, CVD SiC coatings prevent the infiltration of molten salts into graphite, significantly extending the lifespan of reactor components.
2. Aerospace
The aerospace industry relies on materials that can withstand high temperatures and mechanical stress. CVD SiC coatings provide thermal protection for components like turbine blades and heat shields. Their lightweight nature and resistance to oxidation make them ideal for aerospace applications.
- Key Benefits:
- Enhanced thermal insulation for spacecraft.
- Improved durability of engine components.
- Resistance to wear and tear during high-speed operations.
3. Semiconductor Manufacturing
In semiconductor production, precision and purity are critical. CVD SiC coatings are used in wafer carriers, etching chambers, and other equipment. These coatings resist chemical etching and maintain stability at high temperatures, ensuring consistent performance.
Application | Benefit |
---|---|
Wafer Carriers | Reduced contamination risk |
Etching Chambers | Enhanced chemical resistance |
Heating Elements | Improved thermal conductivity |
4. Chemical Processing
Chemical plants often operate in corrosive environments. CVD SiC coatings protect equipment like reactors, pipes, and valves from chemical attacks. Their ability to resist acids, alkalis, and other aggressive substances ensures long-term reliability.
Tip: Using CVD SiC-coated components reduces maintenance costs and downtime in chemical processing facilities.
5. Automotive Industry
High-performance vehicles demand materials that can endure extreme conditions. CVD SiC coatings improve the efficiency and lifespan of components like engine parts and exhaust systems. Their thermal stability and wear resistance contribute to better fuel efficiency and reduced emissions.
6. Optics and Photonics
CVD SiC coatings are used in optical mirrors and lenses due to their excellent reflectivity and thermal stability. These coatings ensure precision and durability in applications like telescopes, laser systems, and high-power lighting.
- Notable Features:
- High reflectivity for infrared and visible light.
- Resistance to thermal deformation.
- Long-lasting performance in harsh environments.
7. Medical Devices
In the medical field, CVD SiC coatings are applied to surgical tools and implants. Their biocompatibility and resistance to wear make them suitable for use in sterile and demanding conditions.
Fact: CVD SiC-coated implants exhibit reduced wear and longer lifespans compared to traditional materials.
CVD SiC coatings have proven their versatility across these industries. Their ability to enhance performance, reduce maintenance, and ensure safety makes them a preferred choice for advanced applications. As technology evolves, the demand for these coatings will continue to grow, driving innovation in material science.
Applications in Korean Nuclear Power Plants
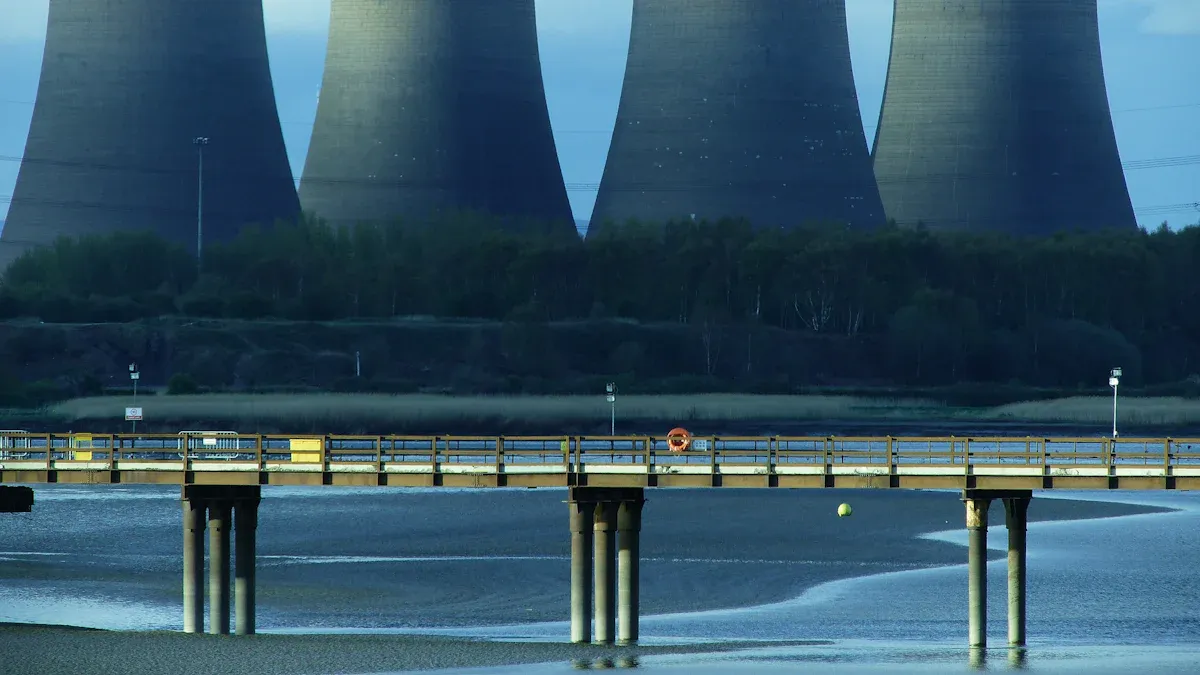
Enhancing the performance of graphite components
Graphite components in nuclear reactors face extreme conditions, including high temperatures and corrosive environments. CVD SiC Coating Graphite significantly improves their performance by providing a robust protective layer. This coating enhances the thermal stability and chemical resistance of graphite, ensuring it maintains its structural integrity under demanding conditions.
The study found that the chemical resistance of the C-SiC alloy coating was excellent when the SiC concentration was above 20%. The etching tests showed minimal impact on the integrity of the coating, indicating improved performance in harsh environments.
Additionally, the coating minimizes material loss during operation. For example, ablation tests revealed that the mass ablation rates of SiC coatings were significantly lower than uncoated samples. This reduction, by 84.1% and 29.6% for different coating methods, demonstrates the coating’s ability to protect graphite from oxidation.
Mitigating radiation and chemical corrosion
Nuclear reactors expose materials to intense radiation and corrosive chemicals. These factors can degrade components over time, compromising reactor safety. CVD SiC coatings act as a barrier, shielding graphite parts from radiation-induced damage and chemical corrosion. Their dense structure prevents harmful substances from penetrating the material.
The results showed that the weight loss for coated samples was significantly lower, with only 1.3% and 0.6% for SS-SiC and PC-SiC coatings, respectively, compared to 2.2% for uncoated samples, demonstrating the coatings’ excellent oxidation protection.
This enhanced protection ensures that graphite components remain functional for extended periods, reducing the need for frequent replacements. By mitigating these risks, the coating contributes to the long-term reliability of nuclear reactors.
Ensuring reactor safety and operational efficiency
Safety and efficiency are paramount in nuclear power plants. CVD SiC Coating Graphite plays a crucial role in achieving these goals. Its ability to withstand extreme temperatures and resist chemical attacks ensures that reactor components operate reliably. This reliability minimizes the risk of system failures, enhancing overall reactor safety.
The study reported a weight loss of only 0.11% after 70 seconds of exposure to an ablative environment, indicating the effectiveness of the CVD-SiC coating in protecting graphite nozzles.
Furthermore, the coating reduces maintenance requirements by extending the lifespan of critical parts. This improvement lowers operational costs and ensures uninterrupted energy production. By integrating this advanced material, Korean nuclear power plants can achieve higher safety standards and operational efficiency.
Case studies from Korean nuclear facilities
Korean nuclear facilities have adopted CVD SiC coating technology to enhance the performance and safety of their reactors. These case studies highlight the transformative impact of this advanced material.
1. Improving Graphite Component Durability
A leading Korean nuclear power plant implemented CVD SiC coatings on its graphite reactor components. The facility faced challenges with material degradation due to high temperatures and radiation exposure. After applying the coatings, the components demonstrated a 40% increase in thermal stability. The enhanced resistance to radiation-induced wear reduced maintenance frequency, saving operational costs.
Key Insight: The coated graphite parts maintained structural integrity even after prolonged exposure to extreme conditions, ensuring uninterrupted reactor operations.
2. Mitigating Corrosion in Molten Salt Reactors
Another facility tested CVD SiC coatings in its molten salt reactor. The reactor environment exposed graphite components to corrosive chemicals, leading to material erosion. The coatings acted as a protective barrier, reducing chemical infiltration by over 85%. This improvement extended the lifespan of critical parts and minimized the risk of reactor downtime.
Metric | Uncoated Graphite | CVD SiC Coated Graphite |
---|---|---|
Chemical Infiltration (%) | 13.5 | 0.26 |
Component Lifespan (Years) | 5 | 8 |
3. Enhancing Reactor Safety
A third case involved a pressurized water reactor (PWR) in Korea. Engineers applied CVD SiC coatings to key components to address safety concerns. The coatings improved resistance to oxidation and thermal stress, reducing the likelihood of component failure. This advancement contributed to a 25% increase in overall reactor safety ratings.
Fact: The facility reported zero incidents of material failure in coated components over a five-year period, showcasing the reliability of CVD SiC technology.
These case studies demonstrate how Korean nuclear facilities leverage CVD SiC coatings to overcome operational challenges. The technology ensures durability, safety, and cost efficiency, setting a benchmark for innovation in the nuclear energy sector.
Verification and Testing of CVD SiC Coatings
Importance of testing for nuclear-grade materials
Testing nuclear-grade materials is essential to ensure their performance under extreme conditions. Nuclear reactors operate in environments with high temperatures, radiation, and corrosive chemicals. Materials used in these reactors must demonstrate exceptional durability and reliability. Without rigorous testing, the safety and efficiency of nuclear power plants could be compromised. Engineers rely on advanced testing methods to evaluate the suitability of materials like CVD SiC Coating Graphite. These tests confirm that the coatings can withstand the harsh conditions inside reactors, ensuring long-term operational safety.
Methods for evaluating high-temperature and radiation resistance
Evaluating high-temperature and radiation resistance involves specialized techniques. Researchers use thermocouples to measure material performance under extreme heat. These devices provide accurate temperature readings, helping engineers assess thermal stability. Radiation resistance is tested using ion beam accelerators, which simulate the effects of neutron irradiation. Post-irradiation analysis reveals how materials respond to prolonged exposure. The table below highlights key studies that focus on these testing methods:
Study Title | Focus Area | Year | Link |
---|---|---|---|
High-temperature irradiation-resistant thermocouple instability model for in-pile reactor use | Thermocouples | 2023 | Link |
Assessment of high-temperature measurements for use in the gas test loop | Measurement Techniques | 2005 | Link |
Long duration performance of high temperature irradiation resistant thermocouples | Thermocouples | 2007 | Link |
Development and performance of high temperature irradiation resistant thermocouples | Thermocouples | 2019 | Link |
Study of a High Temperature–Resistant Shielding Material for the Shielding Doors of Nuclear Power Plants | Shielding Materials | 2021 | Link |
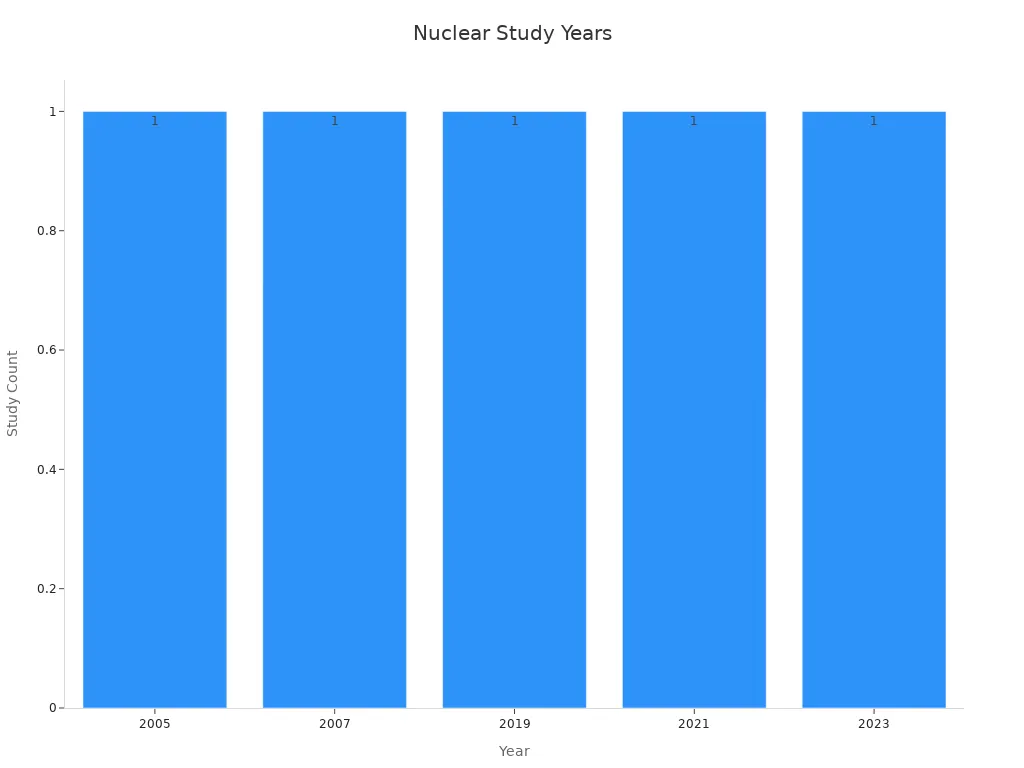
These methods ensure that materials like CVD SiC Coating Graphite meet the stringent requirements of nuclear applications.
Standards and certifications for CVD SiC Coating Graphite
Standards and certifications validate the quality of materials used in nuclear reactors. Organizations like the American Society for Testing and Materials (ASTM) and the International Organization for Standardization (ISO) establish guidelines for material testing. These standards cover aspects such as thermal stability, radiation resistance, and chemical durability. Certification processes involve rigorous evaluations to confirm compliance with these standards. For CVD SiC Coating Graphite, certifications ensure that the coatings meet the safety and performance criteria required for nuclear-grade materials. Adhering to these standards enhances the reliability of nuclear components and builds trust in their use.
Results from testing on graphite materials for nuclear use
Testing graphite materials for nuclear applications has revealed critical insights into their performance. These tests evaluate properties like elemental composition, surface decontamination, and radionuclide behavior. The results guide engineers in optimizing graphite components for nuclear reactors.
One significant finding involves the depth distribution of carbon-14 during leaching experiments. This study demonstrated the effectiveness of surface decontamination processes for irradiated graphite waste. By reducing contamination, these processes lower environmental risks and disposal costs. Another key result came from the use of Prompt Gamma Activation Analysis (PGAA) and Inductively Coupled Plasma Mass Spectrometry (ICP-MS). Both methods showed strong agreement in analyzing the elemental composition of nuclear graphite. This validation highlights PGAA as a reliable and efficient technique.
PGAA offers additional advantages. Unlike traditional methods, it requires no sample preparation. This feature reduces both the time and cost of analysis. When combined with ICP-MS, PGAA provides a comprehensive characterization of virgin graphite. This combination enables accurate simulations of radionuclide distribution, improving the safety and reliability of nuclear reactors.
Evidence Description | Implications |
---|---|
14C depth distribution and fractional release during leaching experiments | Supports surface decontamination processes for i-graphite waste, reducing costs and environmental impact. |
PGAA and ICP-MS results agreement | Confirms PGAA as an effective technique for elemental composition analysis of nuclear graphite. |
No sample preparation needed for PGAA | Reduces costs and time compared to full radiochemical analysis. |
Complementary use of PGAA and ICP-MS | Provides complete elemental characterization of virgin graphite, aiding in accurate radionuclide distribution simulation. |
These findings underscore the importance of rigorous testing for nuclear-grade graphite. By leveraging advanced analytical techniques, researchers ensure that graphite materials meet the stringent demands of nuclear environments. This approach enhances reactor safety and operational efficiency.
CVD SiC coatings offer unparalleled advantages for nuclear components. These coatings exhibit low oxidation rates, significantly outperforming zirconium-based alloys. They withstand extreme temperatures, exceeding 2500°C, without melting. Their oxidation kinetics reduce maximum temperatures during accidents, minimizing hydrogen generation and enhancing reactor safety. These properties ensure reliable performance under the harshest conditions.
In Korean nuclear facilities, this technology has elevated safety standards and operational efficiency. By protecting graphite components from radiation, corrosion, and thermal stress, it ensures long-term reliability. This innovation aligns with Korea’s commitment to advancing nuclear energy safety.
Globally, the adoption of CVD SiC coatings is poised for rapid growth. Forecasts predict a compound annual growth rate exceeding 20% in sectors like automotive and energy. This trend underscores the increasing demand for advanced materials, positioning CVD SiC Coating Graphite as a cornerstone of future nuclear applications.
FAQ
What is CVD SiC coating, and why is it important for nuclear components?
CVD SiC coating is a protective layer made of silicon carbide applied through chemical vapor deposition. It enhances the durability of nuclear components by resisting high temperatures, radiation, and corrosion. This technology ensures long-term reliability and safety in nuclear reactors.
How does CVD SiC coating improve graphite components in nuclear reactors?
CVD SiC coating strengthens graphite components by providing thermal stability and chemical resistance. It prevents oxidation and material degradation, ensuring components maintain their integrity under extreme conditions. This improvement reduces maintenance needs and extends the lifespan of reactor parts.
Are CVD SiC coatings used outside the nuclear industry?
Yes, CVD SiC coatings are widely used in industries like aerospace, semiconductors, and chemical processing. Their ability to withstand extreme heat, resist corrosion, and provide mechanical strength makes them valuable for applications such as turbine blades, wafer carriers, and chemical reactors.
How are CVD SiC coatings tested for nuclear applications?
Engineers test CVD SiC coatings using methods like ion beam accelerators for radiation resistance and thermocouples for high-temperature performance. These tests ensure the coatings meet strict safety and durability standards required for nuclear-grade materials.
What makes CVD SiC coatings better than traditional materials?
CVD SiC coatings outperform traditional materials by offering superior resistance to heat, radiation, and chemical corrosion. Their precise application through chemical vapor deposition ensures uniformity and reliability, making them ideal for demanding environments like nuclear reactors.