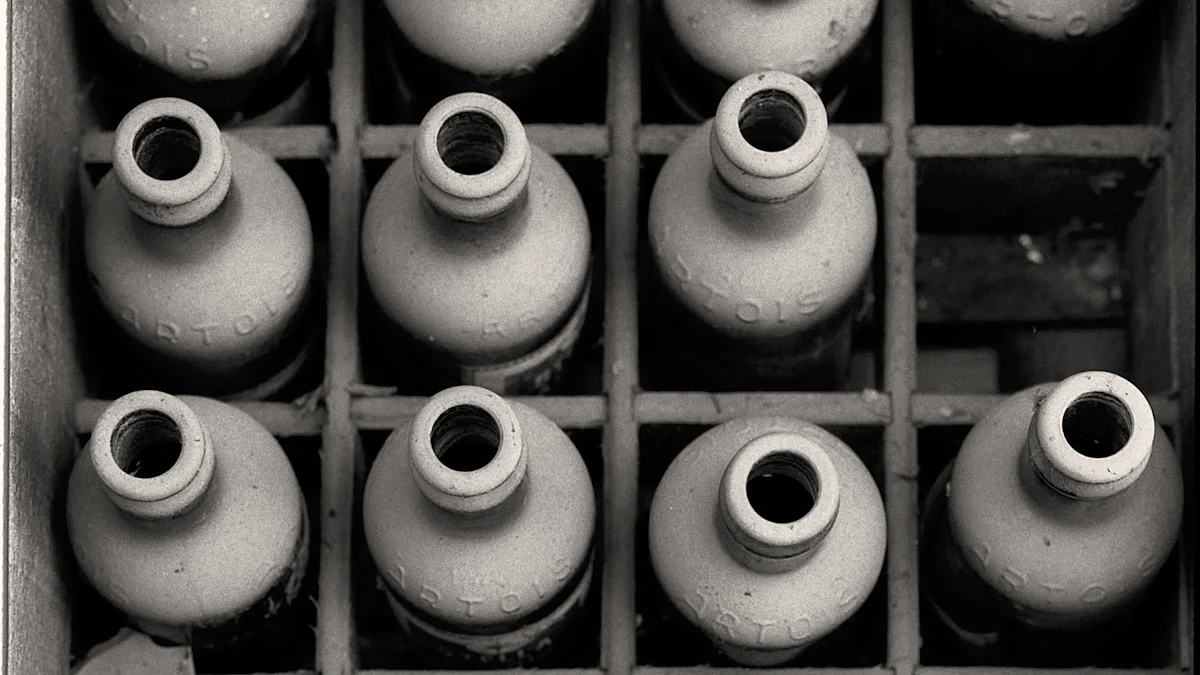
Silicon carbide (SiC) ceramic coatings, also known as SiC coatings, stand out due to their remarkable properties. These coatings exhibit exceptional hardness, ranking as the third hardest compound on Earth with a Mohs hardness of 13. This makes them highly resistant to wear and abrasion. Their thermal stability allows them to maintain integrity in environments reaching up to 1600°C. Additionally, their chemical resistance shields components from corrosive elements, ensuring durability in harsh conditions.
Industries like aerospace, automotive, and electronics rely on SiC coatings to enhance performance. In aerospace, they protect components exposed to extreme heat. Automotive manufacturers use them to improve engine and brake durability. Electronics benefit from their ability to dissipate heat and protect sensitive devices. These applications demonstrate the transformative impact of SiC ceramic coatings, leading to the question: what is SiC coating? The answer lies in their ability to provide superior protection and performance across various sectors.
Key Takeaways
- SiC ceramic coatings are very hard, ranking third on the Mohs scale.
- They resist wear and scratches, making them last longer.
- These coatings handle heat up to 1600°C without breaking down.
- This makes them useful in hot places like planes and power plants.
- SiC coatings resist chemicals, protecting parts from damage and rust.
- This helps parts last longer and work better over time.
- SiC coatings are light, helping planes and cars use less fuel.
- They save weight but still stay strong and durable.
- These coatings help cool electronics, stopping them from overheating.
- This keeps devices working well and safely for a long time.
- Industries save money with SiC coatings by needing fewer repairs.
- They also make important parts last much longer.
- New SiC coating ideas are helping renewable energy and the environment.
- SiC coatings save money over time by cutting replacements and boosting efficiency.
Overview of SiC Ceramic Coatings
What Are SiC Ceramic Coatings
SiC ceramic coatings are thin layers of silicon carbide applied to surfaces to enhance their performance in demanding environments. These coatings act as a protective barrier, shielding components from wear, heat, and chemical damage. Their exceptional hardness and thermal stability make them indispensable in industries requiring durability and reliability. From aerospace to electronics, SiC ceramic coatings ensure components perform optimally under extreme conditions.
Composition and Manufacturing Techniques
The composition of SiC ceramic coatings primarily involves silicon carbide, a compound of silicon and carbon. This material is renowned for its high purity and robust properties. Manufacturers use various techniques to produce these coatings, each tailored to specific applications.
Common Manufacturing Methods:
-
Reaction-bonded Silicon Carbide (RBSC):
This method occurs at lower temperatures, making it cost-effective. It produces ceramics suitable for applications like kiln furniture and wear-resistant components. However, the presence of free silicon can impact the final product’s quality. -
Sintered Silicon Carbide (SSC):
SSC involves high-temperature processing, resulting in ceramics with high purity and low porosity. These properties make SSC ideal for sealing components and protective gear like bulletproof vests. -
Recrystallized Silicon Carbide (RSIC):
RSIC uses high-temperature techniques to create ceramics with excellent thermal conductivity and shock resistance. Its low shrinkage and high porosity make it suitable for demanding industrial applications.
Manufacturing Method | Description |
---|---|
Reaction-bonded Silicon Carbide (RBSC) | Occurs at lower temperatures, suitable for various applications. |
Sintered Silicon Carbide (SSC) | Takes place at higher temperatures, providing enhanced material properties. |
Recrystallized Silicon Carbide (RSIC) | Involves higher purity silicon carbide products, offering superior performance in demanding environments. |
These methods allow SiC ceramic coatings to perform in environments containing gases like oxygen, hydrogen, and methane, as well as in processes like MOCVD and CVD thin film deposition.
Unique Characteristics of SiC Coatings
SiC ceramic coatings stand out due to their remarkable properties. Their high thermal conductivity ensures efficient heat dissipation, making them ideal for high-temperature applications. The exceptional hardness of these coatings provides a robust surface that resists wear and tear, extending the lifespan of components.
Additionally, SiC coatings offer unparalleled corrosion and oxidation resistance. They protect surfaces from corrosive elements and oxidative environments, maintaining their integrity over time. These coatings can withstand temperatures up to 1600°C, even at atmospheric pressure, making them suitable for extreme conditions.
SiC ceramic coatings are not just durable; they are also lightweight. This combination of strength and low weight makes them a preferred choice in industries like aerospace and automotive, where performance and efficiency are critical.
By combining these unique characteristics, SiC ceramic coatings deliver unmatched performance across a wide range of applications.
Key Scientific Properties of SiC Ceramic Coatings
Hardness and Wear Resistance
When it comes to hardness, silicon carbide stands out as one of the toughest materials available. Its hardness measures 9.5 on the Mohs scale, surpassing corundum and ranking just below diamond and boron carbide. This exceptional hardness stems from its unique crystal structure. The tightly bonded tetrahedral arrangement of silicon and carbon atoms creates a strong covalent bond, giving the material its incredible strength.
This hardness translates directly into wear resistance. SiC ceramic coatings excel in protecting surfaces from mechanical abrasion. For example:
- They resist scratches and surface damage in high-friction environments.
- They maintain their integrity even under prolonged exposure to abrasive forces.
- They are ideal for applications requiring durable materials, such as cutting tools and industrial machinery.
By using SiC ceramic coatings, industries can extend the lifespan of components, reduce maintenance costs, and improve overall efficiency.
Thermal Stability in Extreme Conditions
SiC ceramic coatings are engineered to perform in extreme heat. These coatings can withstand temperatures up to 1600°C at atmospheric pressure without degrading. This makes them indispensable in industries like aerospace and energy, where components face intense thermal stress.
The thermal stability of SiC coatings ensures that they maintain their structural integrity and performance even in the harshest conditions. For instance, in aerospace applications, they protect thermal protection systems and engine components from heat damage. In the energy sector, they enhance the durability of solar panels and nuclear reactor components.
This ability to endure extreme temperatures not only improves safety but also ensures consistent performance in critical operations.
Chemical Resistance and Corrosion Protection
SiC ceramic coatings offer unparalleled resistance to chemical attack. Their non-reactive nature shields surfaces from corrosive substances, including acids, alkalis, and oxidizing agents. This property makes them highly effective in environments where chemical exposure is unavoidable.
For example, in the automotive industry, these coatings protect engine and exhaust components from corrosion caused by exposure to fuel and exhaust gases. In industrial settings, they safeguard machinery and tools from chemical wear, ensuring long-term reliability.
The corrosion protection provided by SiC coatings also reduces the need for frequent replacements, saving both time and resources. Their ability to resist chemical damage makes them a preferred choice for industries seeking durable and reliable solutions.
SiC ceramic coatings combine hardness, thermal stability, and chemical resistance to deliver unmatched performance. These properties make them a cornerstone of modern industrial applications.
Electrical and Semiconducting Properties
Silicon carbide (SiC) ceramic coatings possess fascinating electrical and semiconducting properties. I find it remarkable how these coatings can function as semiconductors, bridging the gap between insulators and conductors. This unique characteristic allows SiC to play a critical role in modern electronics.
One of the standout features of SiC is its ability to modify electrical conductivity through doping. By introducing specific impurities into the material, manufacturers can tailor its conductivity to meet the needs of various applications. For instance, doped SiC coatings are widely used in power devices, sensors, and high-frequency electronics. This customization ensures that the coatings perform optimally in demanding environments.
To give you a clearer picture, here’s a quick overview of one of SiC’s key electrical properties:
Property | Value |
---|---|
Electrical Resistivity (@20°C) | 1MΩ.m |
This high resistivity highlights SiC’s ability to resist the flow of electric current under standard conditions. However, when doped, its conductivity can be adjusted to suit specific requirements. This versatility makes SiC coatings indispensable in industries like electronics and semiconductors.
Another fascinating aspect is how SiC coatings handle high-power applications. Their ability to dissipate heat efficiently ensures that electronic components remain cool, even under heavy loads. This property not only enhances performance but also extends the lifespan of devices.
SiC ceramic coatings combine electrical resistivity, semiconducting capabilities, and thermal management to deliver unmatched performance in electronic applications.
Lightweight and High Strength-to-Weight Ratio
SiC ceramic coatings are not just strong; they are also incredibly lightweight. This combination of properties makes them a game-changer in industries where weight reduction is crucial. I’ve seen how aerospace and automotive sectors benefit from this unique feature.
The strength-to-weight ratio of SiC coatings is among the highest in the materials world. Despite their lightweight nature, these coatings provide exceptional durability and resistance to mechanical stress. This means that components coated with SiC can withstand heavy loads without adding unnecessary weight.
In aerospace, for example, reducing weight is essential for improving fuel efficiency and overall performance. SiC coatings help achieve this by providing robust protection without compromising on weight. Similarly, in the automotive industry, lightweight components contribute to better fuel economy and reduced emissions.
The lightweight nature of SiC coatings doesn’t just improve efficiency; it also enhances safety. By reducing the overall weight of vehicles and aircraft, these coatings contribute to better handling and stability.
SiC ceramic coatings truly stand out as a material that combines strength, durability, and efficiency. Their high strength-to-weight ratio ensures that they remain a preferred choice for industries aiming to optimize performance while minimizing weight.
Industrial Applications of SiC Ceramic Coatings
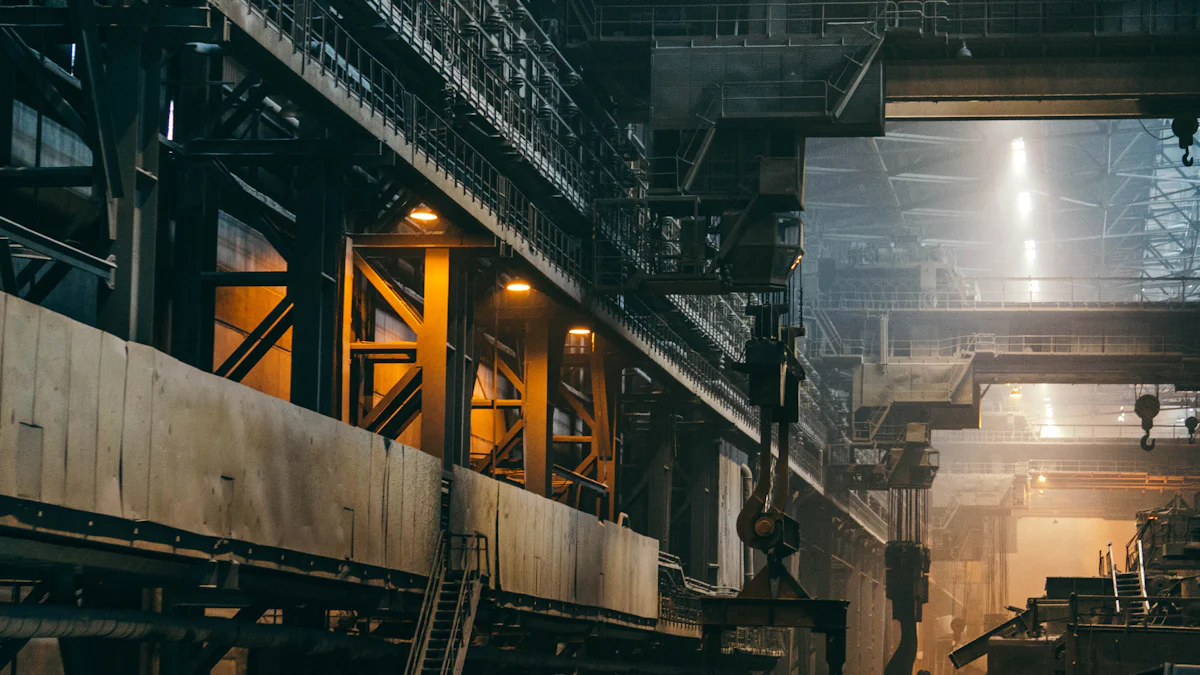
Aerospace Applications
Thermal Protection Systems
In aerospace, I’ve seen how SiC ceramic coatings revolutionize thermal protection systems. These coatings excel in maintaining structural integrity under extreme heat, making them indispensable for spacecraft and high-speed aircraft. Their unmatched thermal stability ensures that components remain intact even at temperatures exceeding 1600°C. Additionally, their low density contributes to significant weight reduction, which is critical for improving fuel efficiency and overall performance.
SiC coatings also provide excellent thermal insulation, protecting sensitive equipment from extreme temperatures. This combination of properties makes them a cornerstone in aerospace engineering.
Abrasion-Resistant Components
Abrasion resistance is another area where SiC ceramic coatings shine. I’ve observed their ability to withstand wear and tear in high-friction environments, such as turbine blades and engine components. Their increased hardness resists surface damage, prolonging the lifespan of these critical parts. Furthermore, their corrosion resistance shields components from harsh environmental conditions, reducing maintenance costs and ensuring long-term reliability.
Automotive Applications
Engine and Exhaust System Components
SiC ceramic coatings play a pivotal role in enhancing the durability of engine and exhaust system components. Their exceptional thermal stability allows them to withstand the high temperatures generated during combustion. This property ensures that engines operate efficiently without degradation over time. Additionally, their chemical resistance protects exhaust systems from corrosive gases, extending their service life.
By using SiC coatings, automotive manufacturers can improve engine performance while reducing maintenance requirements. This makes them a valuable asset in modern vehicle design.
Brake Discs and Rotors
Brake discs and rotors benefit immensely from SiC ceramic coatings. I’ve noticed how their high thermal conductivity aids in efficient heat dissipation, preventing overheating during braking. Their exceptional hardness enhances wear resistance, ensuring that brake components maintain their performance over extended periods.
- SiC coatings improve braking performance, providing more stable and reliable effects.
- They protect against corrosion, maintaining the integrity of brake systems in harsh conditions.
- The coatings contribute to a longer service life, reducing the need for frequent replacements.
These advantages make SiC ceramic coatings a preferred choice for high-performance and heavy-duty vehicles.
Electronics and Semiconductor Applications
Heat Dissipation in High-Power Electronics
In high-power electronics, thermal management is crucial. SiC ceramic coatings excel in this area due to their outstanding thermal conductivity and stability. I’ve seen how they efficiently dissipate heat, preventing localized overheating and ensuring consistent performance. Their low coefficient of thermal expansion minimizes thermal shock, making them ideal for applications with rapid temperature changes.
These coatings are widely used in heat dissipation systems, enhancing the reliability and efficiency of electronic devices.
Protective Coatings for Semiconductor Devices
Semiconductor devices require robust protection against environmental damage, and SiC ceramic coatings deliver on this front. Their increased hardness fortifies surfaces against wear and tear, while their corrosion resistance shields against harmful elements.
- High thermal conductivity ensures efficient heat dissipation, crucial for high-temperature applications.
- Oxidation resistance prevents degradation in oxidative environments.
- These coatings maintain their integrity under demanding conditions, extending the lifespan of semiconductor devices.
By incorporating SiC ceramic coatings, manufacturers can enhance the durability and performance of semiconductors, ensuring they meet the rigorous demands of modern technology.
Energy Sector Applications
Solar Panels and Photovoltaic Systems
I’ve observed how SiC ceramic coatings significantly improve the performance of solar panels and photovoltaic systems. These coatings offer several advantages that make them indispensable in renewable energy applications:
- Their self-cleaning properties, due to a low contact angle, reduce dirt accumulation. This ensures panels maintain peak efficiency over time.
- Their high durability and chemical resistance outperform traditional materials like fused silica and soda-lime glass.
- With 99.8% transparency, they allow maximum light absorption, ensuring minimal interference with photovoltaic efficiency.
These features make SiC ceramic coatings a game-changer in solar technology. By enhancing durability and efficiency, they contribute to the long-term reliability of solar energy systems.
Nuclear Reactor Components
In nuclear reactors, components face extreme conditions, including high temperatures and corrosive environments. SiC ceramic coatings provide the necessary protection to ensure these components perform reliably. Their thermal stability allows them to withstand intense heat without degrading. Additionally, their chemical resistance shields reactor parts from corrosive substances, extending their operational lifespan.
I’ve seen how these coatings enhance safety and efficiency in nuclear energy production. By protecting critical components, they reduce maintenance needs and improve the overall reliability of reactor systems.
Other Industrial Applications
Medical Devices
SiC ceramic coatings have found their way into the medical field, where precision and durability are paramount. These coatings protect medical devices from wear and corrosion, ensuring they remain functional over extended periods. For example, surgical tools coated with SiC maintain their sharpness and resist damage during repeated sterilization cycles.
Their biocompatibility also makes them suitable for implants and prosthetics. I’ve noticed how their lightweight nature and strength contribute to patient comfort and device longevity. These qualities make SiC coatings an essential material in modern medical technology.
Industrial Machinery and Tools
Industrial machinery and tools benefit immensely from the application of SiC ceramic coatings. Their increased hardness fortifies surfaces against wear and tear, while their corrosion resistance shields equipment from harsh chemicals. Thermal stability ensures these coatings maintain their integrity under high temperatures.
In practical applications, I’ve seen how silicon carbide’s hardness translates into superior performance. Cutting tools and grinding wheels coated with SiC retain their sharpness and structural integrity, even in abrasive environments. This durability reduces downtime and maintenance costs, leading to increased productivity.
The long-term benefits of SiC ceramic coatings extend beyond wear resistance. Equipment coated with this material experiences fewer repairs, resulting in significant cost savings and improved operational efficiency.
These advantages make SiC ceramic coatings a preferred choice for industries seeking reliable and durable solutions for their machinery and tools.
Advantages of SiC Ceramic Coatings Over Other Coatings
Comparison with Metal Coatings
I’ve often observed how metal coatings dominate industrial applications due to their strength and versatility. However, when compared to SiC ceramic coatings, they fall short in several critical areas:
- Increased Hardness: SiC ceramic coatings provide a much harder surface than metal coatings. This hardness enhances wear resistance, making them ideal for high-friction environments.
- Corrosion Resistance: Unlike metal coatings, which can corrode over time, SiC coatings shield surfaces from corrosive elements, ensuring long-term durability.
- Thermal Stability: SiC coatings maintain their integrity under extreme temperatures, while metal coatings may degrade or lose effectiveness.
These advantages make SiC ceramic coatings a superior choice for industries requiring high-performance materials. For example, in aerospace and automotive applications, their ability to withstand harsh conditions ensures reliability and efficiency.
Comparison with Polymer Coatings
Polymer coatings are widely used due to their affordability and ease of application. However, I’ve noticed that they lack the robustness of SiC ceramic coatings in demanding environments. Key differences include:
- SiC ceramic coatings are inorganic, while polymer coatings rely on organic resins. This distinction gives ceramic coatings superior resistance to heat, abrasion, and chemicals.
- Ceramic coatings can be customized for specific industrial needs, offering flexibility that polymer coatings cannot match.
- Polymer coatings degrade quickly under high temperatures or abrasive conditions, whereas SiC coatings excel in these scenarios.
In industries like electronics and energy, where components face extreme conditions, SiC ceramic coatings outperform polymer alternatives. Their durability and adaptability make them indispensable for critical applications.
Cost-Effectiveness and Durability
When evaluating the cost-effectiveness of SiC ceramic coatings, I always consider both direct and indirect costs. While the initial investment may seem higher, the long-term benefits far outweigh the expenses.
Aspect | Description |
---|---|
Direct Costs | Material feedstock, operator labor, or per-part fees charged by external coaters. |
Indirect Costs | Additional QA checks, increased inventory levels, training for CNC programmers, and storage needs. |
Benefits | Extended part life, improved performance, reduced maintenance, product differentiation, and material consolidation. |
Example of Savings | Switching to ceramic-coated tools resulted in fewer tool changes and improved finish quality, leading to overall cost savings. |
ROI Analysis Methods | Payback Period, Net Present Value (NPV), Internal Rate of Return (IRR), Total Cost of Ownership (TCO). |
I’ve seen how industries save significantly by switching to SiC ceramic coatings. For instance, tools coated with SiC require fewer replacements, reducing downtime and maintenance costs. Additionally, the improved performance and extended lifespan of components contribute to a higher return on investment.
SiC ceramic coatings combine durability, performance, and cost-effectiveness, making them a valuable asset for industries seeking long-term solutions.
Future Trends and Innovations in SiC Ceramic Coatings
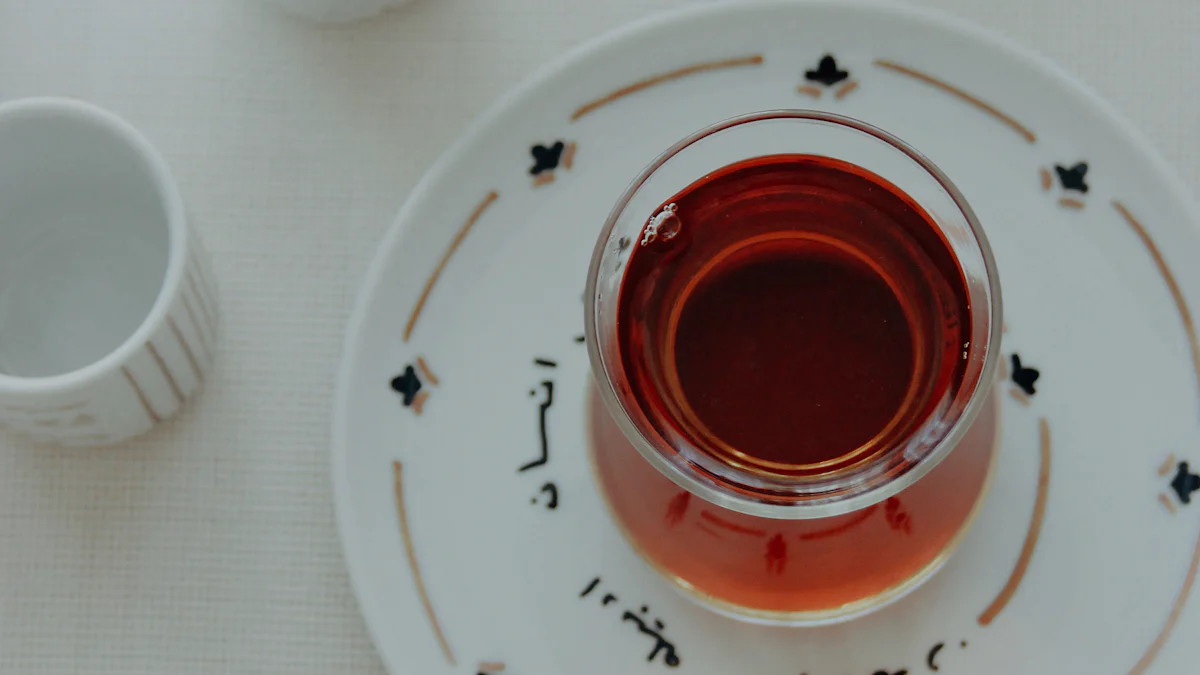
Emerging Applications in Renewable Energy
I’ve noticed a growing demand for SiC ceramic coatings in renewable energy technologies. These coatings are transforming the energy sector by enhancing the durability and efficiency of critical components. For instance, solar panels now rely on SiC coatings to endure extreme temperatures and harsh environmental conditions. This resilience ensures consistent performance, even in challenging climates.
The global shift toward sustainable energy sources has accelerated the adoption of SiC coatings. Their ability to withstand wear and corrosion makes them ideal for wind turbines and geothermal systems. By improving the longevity of these systems, SiC coatings contribute to the reliability of renewable energy infrastructure. As the world continues to prioritize sustainability, I expect SiC coatings to play an even larger role in advancing energy-efficient technologies.
Advancements in Coating Technologies
Recent advancements in coating technologies have significantly improved the performance of SiC ceramic coatings. I’ve observed how these innovations are addressing industry challenges and expanding the applications of these coatings. Some of the most notable advancements include:
- CVD SiC: This method enhances dimensional stability at high temperatures and improves resistance to thermal shock. It’s particularly useful in extreme environments.
- Diamond-like carbon films: These films act as sacrificial wear layers on electrostatic chucks, protecting electronic components and extending their service life.
- Textured ceramic coatings: These coatings improve particulate contamination control, which boosts efficiency in semiconductor manufacturing processes.
These advancements demonstrate the versatility of SiC coatings. By leveraging these technologies, industries can achieve higher performance and reliability in their operations.
Sustainability and Eco-Friendly Solutions
Sustainability has become a key focus in the development of SiC ceramic coatings. I’ve seen how manufacturers are innovating to make these coatings more eco-friendly. The table below highlights some of the latest efforts:
Aspect | Description |
---|---|
Energy consumption efficiency | SiC semiconductors achieve higher energy utilization efficiency, reducing overall energy consumption. |
Long life and reliability | High thermal stability and radiation resistance extend the service life of devices, minimizing e-waste. |
Energy saving and emission reduction | Applications in electric vehicles and LED lighting significantly lower energy consumption and emissions. |
Recycling | SiC’s durability allows for effective recycling, reducing environmental waste impact. |
These innovations align with global efforts to reduce environmental impact. For example, SiC coatings in electric vehicles help lower emissions while improving energy efficiency. Their recyclability further reduces waste, making them a sustainable choice for modern industries.
I believe that as sustainability becomes a priority, SiC ceramic coatings will continue to evolve. These coatings not only meet the demands of today’s industries but also pave the way for a greener future.
SiC ceramic coatings have revolutionized industrial applications with their unique scientific properties. Their high thermal conductivity ensures efficient heat dissipation, while exceptional hardness and corrosion resistance extend the lifespan of critical components. Oxidation resistance further enhances their durability in extreme environments. These qualities make them indispensable across industries like automotive, electronics, and energy.
The demand for these coatings continues to grow as industries prioritize efficiency and sustainability. For example, the automotive sector increasingly relies on them for powertrain components and battery systems, driven by the shift to electric vehicles. Similarly, electronics and energy sectors benefit from their ability to enhance performance and durability, as shown in the table below:
Industry Sector | Application of SiC Coatings | Reason for Demand Increase |
---|---|---|
Automotive | Powertrain components, battery systems | Shift towards electric and hybrid vehicles, need for durability and efficiency |
Electronics | Semiconductor devices | Demand for smaller, efficient devices requiring high-quality protective coatings |
Energy | Solar panels, energy-efficient technologies | Focus on renewable energy sources and performance enhancement |
Industrial | Chemical processing, heavy machinery | Emphasis on industrial efficiency and equipment longevity |
Future advancements promise to expand the applications of SiC ceramic coatings. Improved production techniques, such as advanced sintering and 3D printing, will reduce costs and increase accessibility. Multifunctional composite materials will address high-temperature demands, while environmentally friendly innovations will align with sustainability goals. Industries like aerospace, automotive, and semiconductors stand to benefit the most from these developments.
SiC ceramic coatings are not just a solution for today’s challenges but a foundation for tomorrow’s innovations. Their unmatched properties and potential for growth ensure they will remain a cornerstone of industrial progress.
FAQ
What industries benefit the most from SiC ceramic coatings?
SiC ceramic coatings are widely used in aerospace, automotive, electronics, and energy sectors. I’ve seen them enhance performance in high-temperature environments, protect against wear, and improve efficiency in renewable energy systems like solar panels and wind turbines.
How are SiC ceramic coatings applied?
Manufacturers use techniques like chemical vapor deposition (CVD), physical vapor deposition (PVD), and sintering. These methods ensure precise application, tailored to the specific needs of industries. I’ve noticed that CVD is particularly effective for high-performance applications.
Are SiC ceramic coatings environmentally friendly?
Yes, SiC coatings align with sustainability goals. Their durability reduces waste, while their use in renewable energy systems supports eco-friendly initiatives. I’ve observed how they contribute to energy efficiency in electric vehicles and solar technologies.
Can SiC ceramic coatings withstand extreme temperatures?
Absolutely. SiC coatings maintain integrity at temperatures up to 1600°C. I’ve seen them perform exceptionally well in aerospace and energy applications, where components face intense thermal stress.
What makes SiC ceramic coatings better than metal coatings?
SiC coatings offer superior hardness, corrosion resistance, and thermal stability. Unlike metal coatings, they don’t degrade in extreme conditions. I’ve found them to be more reliable for long-term use in harsh environments.
Are SiC ceramic coatings cost-effective?
While the initial cost may be higher, the long-term benefits outweigh the expense. I’ve seen industries save on maintenance and replacements due to the durability and efficiency of SiC coatings, making them a smart investment.
Do SiC ceramic coatings improve energy efficiency?
Yes, they enhance energy efficiency by reducing heat loss and improving thermal management. I’ve noticed their impact in electronics and renewable energy systems, where efficient heat dissipation is critical.
Can SiC ceramic coatings be customized for specific applications?
Yes, manufacturers can tailor SiC coatings to meet unique requirements. I’ve seen them modified for semiconductors, medical devices, and industrial tools, ensuring optimal performance in diverse applications.