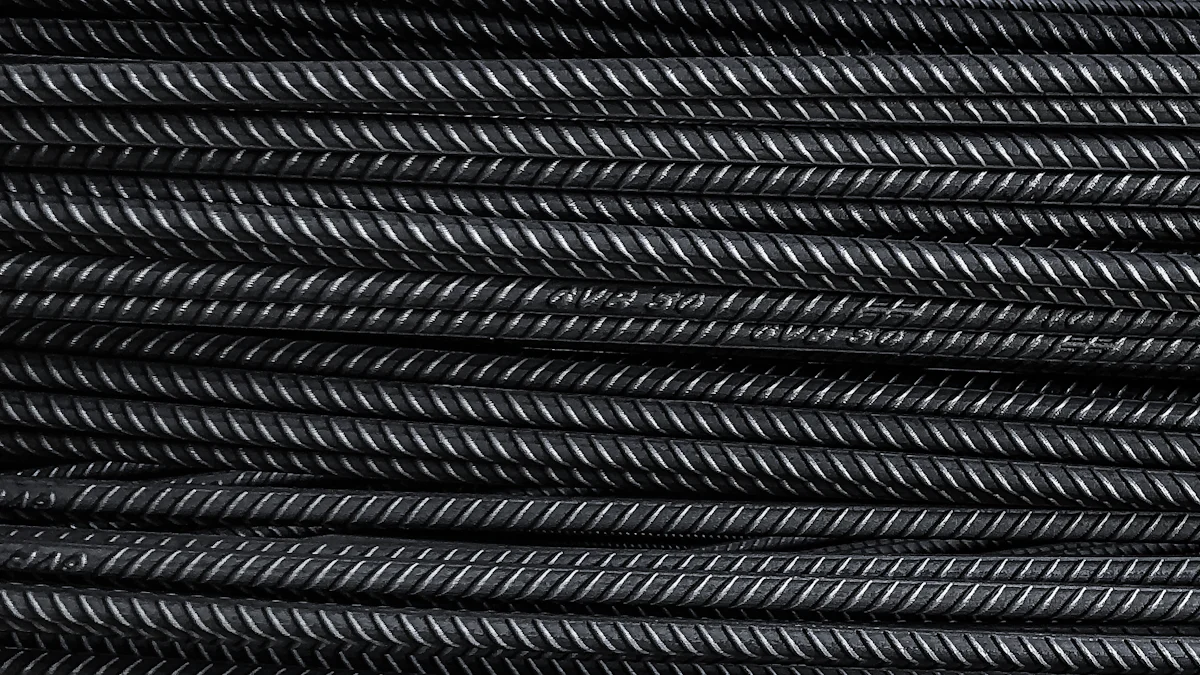
Composite carbone renforcé est un matériau remarquable connu pour sa résistance et sa durabilité exceptionnelles. En intégrant des fibres de carbone, qui sont cinq fois plus fortes et deux fois plus rigides que l'acier, avec une matrice de carbone, il forme une composite carbone renforcé fibre de carbone capable de supporter des conditions extrêmes. Ce matériau avancé offre une résistance à la chaleur exceptionnelle, ce qui en fait un choix privilégié pour les applications aérospatiales et techniques de pointe. En comparant carbon composite vs carbon fiber, le carbone composite renforcé se distingue par son rapport résistance-poids supérieur et ses propriétés uniques. La connaissance qu'est-ce que le carbone composite souligne son rôle indispensable dans les industries exigeant précision et résilience, où la performance justifie prix du carbone renforcé.
Principaux enseignements
- Le carbone composite renforcé combine des fibres de carbone avec une matrice de carbone, offrant une résistance exceptionnelle à la chaleur et à la résistance, ce qui le rend idéal pour l'aérospatiale et applications techniques avancées.
- La préparation des fibres de carbone est cruciale; choisir le bon type et les organiser correctement améliore la performance composite sous contrainte et les conditions extrêmes.
- L'imprégnation des fibres de carbone avec de la résine est une étape clé qui assure une forte liaison et une structure uniforme, fixant le stade du processus de carbonisation qui transforme la résine en une matrice de carbone robuste.
- La densité par cycles répétés d'imprégnation et de carbonisation augmente la densité et la résistance des composites, ce qui lui permet de résister à des températures élevées et à des contraintes mécaniques.
- L'usinage final et les traitements de surface améliorent la forme du composite et le protègent des facteurs environnementaux, assurant ainsi durabilité et fiabilité dans les applications exigeantes.
- Comprendre le processus de fabrication méticuleux du carbone composite renforcé souligne son rôle indispensable dans les industries où la performance et la précision sont critiques.
Étape 1: Préparation des fibres de carbone
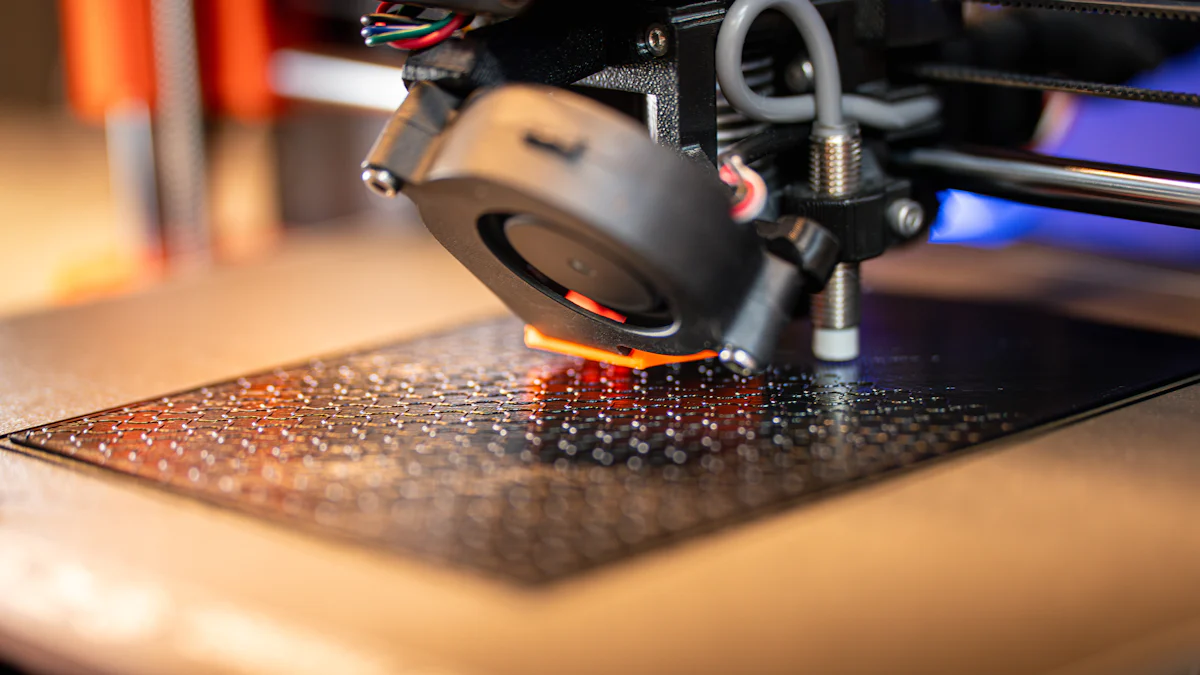
La fondation d'un reinforced carbon carbon composite réside dans ses fibres de carbone. Ces fibres servent d'épine dorsale, fournissant au matériau sa force et sa rigidité exceptionnelles. La préparation de ces fibres nécessite une sélection soigneuse et un arrangement précis pour s'assurer que le composite final respecte les normes de performance souhaitées.
Choisir et arranger les fibres de carbone
Types de fibres de carbone utilisées dans le carbone composite renforcé
Les fibres de carbone se présentent sous différentes formes, chacune offrant des propriétés uniques. Les fibres à haute résistance, souvent utilisées dans les applications aérospatiales, offrent une résistance supérieure à la traction. D'autre part, les fibres à haut module excellent dans la rigidité, ce qui les rend idéales pour les applications nécessitant une rigidité. Les fabricants choisissent souvent les fibres en fonction des exigences spécifiques du composite, comme la résistance à la chaleur ou les performances mécaniques.
Les fibres de carbone sont généralement combinées avec d'autres matériaux pour améliorer leurs propriétés. Par exemple, lorsqu'ils sont mélangés au graphite, ils créent un composite capable de résister aux températures extrêmes. Cette combinaison est particulièrement utile dans des industries comme l'aérospatiale, où les matériaux doivent supporter des environnements difficiles sans compromettre l'intégrité structurelle.
Méthodes d'organisation des fibres pour assurer l'intégrité structurale
Il est essentiel d'organiser correctement les fibres de carbone pour obtenir des performances optimales. Les fabricants utilisent plusieurs méthodes pour aligner les fibres, garantissant que le composite peut gérer le stress efficacement. Les techniques courantes comprennent:
- Alignement unidirectionnel: Les fibres sont disposées dans une seule direction pour maximiser la résistance le long de cet axe. Cette méthode est souvent utilisée dans les applications nécessitant une forte résistance à la traction.
- Tissage ou tressage: Les fibres sont entrelacées pour créer une structure en tissu. Cette approche améliore la durabilité et offre une force multidirectionnelle.
- Calibrage: Plusieurs couches de fibres sont empilées dans différentes orientations. Cette technique équilibre résistance et rigidité dans toutes les directions.
Chaque méthode d'arrangement contribue à la performance globale des composites. Par exemple, l'alignement unidirectionnel offre une force exceptionnelle dans une direction, tandis que les structures tissées offrent des propriétés plus équilibrées. En adaptant l'arrangement à l'application, les fabricants s'assurent que le composite répond à des exigences spécifiques.
L'arrangement des fibres de carbone affecte directement les propriétés mécaniques du composite, ce qui en fait une étape critique dans le processus de fabrication. (en milliers de dollars)
Étape 2: Création de la matrice carbone
Le matrice carbone forme le cadre essentiel qui lie les fibres de carbone reinforced carbon carbon composite. Cette étape implique deux processus critiques : l'imprégnation des fibres avec la résine et la conversion de la résine en carbone par la carbonisation. Ces processus assurent au composite une résistance et une stabilité thermique remarquables.
Imprégnant fibre avec résine
Le processus d'imprégnation commence par saturer les fibres de carbone avec une résine, qui agit comme précurseur de la matrice de carbone. Cette étape est cruciale pour créer une structure uniforme et stable.
Rôle de la résine comme précurseur de la matrice de carbone
La résine sert de base à la matrice de carbone. Il pénètre les espaces entre les fibres de carbone, assurant une liaison forte et une distribution uniforme. Les résines couramment utilisées comprennent les résines phénoliques et époxy, connues pour leur capacité à résister à des températures élevées et à des contraintes mécaniques. Une fois appliquée, la résine non seulement maintient les fibres en place, mais les prépare également pour la prochaine étape de transformation.
Le rôle de la résine s'étend au-delà de la liaison; il établit le stade du processus de carbonisation, où il se transforme en une matrice de carbone robuste. (en milliers de dollars)
Les fabricants contrôlent soigneusement l'application de résine pour éviter les vides ou les points faibles dans le composite. Des techniques telles que l'imprégnation sous vide ou les méthodes assistées par pression assurent une saturation complète. Ces méthodes améliorent l'intégrité et la performance structurales composites dans des conditions extrêmes.
Processus de carbonisation
Après imprégnation, la résine subit une carbonisation, un processus qui la convertit en carbone. Cette transformation est essentielle pour atteindre la résistance à haute température composite et la durabilité.
Chauffage et conversion de résine en carbone
Le processus de carbonisation consiste à chauffer les fibres imprégnées de résine dans un environnement contrôlé. Les températures varient généralement de 1 000 °C à 2 000 °C. Pendant ce processus, la résine se décompose, libérant des composés volatils et laissant derrière elle une structure en carbone solide. Cette étape nécessite de la précision pour s'assurer que la matrice de carbone se forme sans défauts.
La pyrolyse à basse température, une méthode étudiée dans différentes industries, démontre l'importance du chauffage contrôlé pour transformer les matériaux organiques en structures de carbone stables. (en milliers de dollars)
La matrice de carbone qui en résulte améliore la capacité des composites à supporter une chaleur extrême et une contrainte mécanique. Cette propriété la rend indispensable pour des applications comme les disques de frein d'aéronef, où les matériaux doivent fonctionner de manière fiable dans des conditions intenses.
En combinant imprégnation de résine avec carbonisation précise, les fabricants créent une matrice de carbone qui complète la résistance des fibres de carbone. Cette synergie se traduit par reinforced carbon carbon composite capable de répondre aux exigences des industries de pointe de l'ingénierie et de l'aérospatiale.
Étape 3: Densification et finition
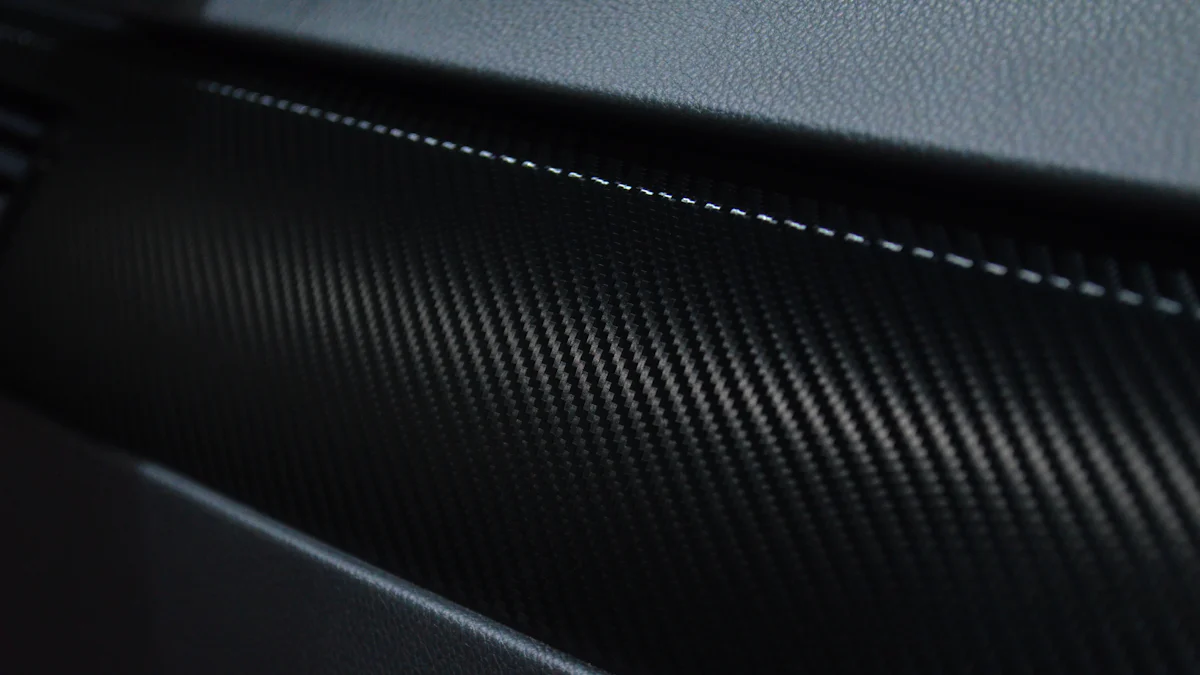
La dernière étape de la création reinforced carbon carbon composite implique la densification et la finition. Cette étape améliore la densité, la résistance et les propriétés de surface du matériau, en s'assurant qu'il répond aux exigences rigoureuses des applications avancées. Les fabricants utilisent des techniques précises pour atteindre les caractéristiques structurelles et fonctionnelles souhaitées.
Imprégnation et carbonisation répétées
La densité commence par des cycles répétés d'imprégnation et de carbonisation. Ces cycles remplissent les pores du composite, augmentant sa densité et sa résistance mécanique.
Réalisation de la densité et de la force souhaitées
Les fabricants imprègnent le composite de substances riches en carbone, telles que des emplacements ou des résines. Ces matériaux pénètrent la structure poreuse, remplissent les vides et renforcent la matrice. Après imprégnation, le composite subit une carbonisation à haute température. Ce procédé convertit le matériau imprégné en carbone, solidifiant davantage la structure.
Le processus de densification implique souvent plusieurs cycles pour assurer l'uniformité et éliminer la variabilité des propriétés composites. (en milliers de dollars)
Des techniques avancées, telles que l'infiltration de vapeur chimique (CVI) ou le dépôt de vapeur chimique (CVD), sont également utilisées. Ces méthodes introduisent le carbone des précurseurs gazeux, le déposant dans le composite. CVI et CVD améliorent les performances thermiques et mécaniques du matériau, le rendant adapté aux environnements extrêmes.
Les cycles répétés d'imprégnation et de carbonisation permettent aux fabricants d'affiner la densité et la résistance des composites. Cette précision permet au matériau de résister à des conditions de contrainte et de température élevées, ce qui le rend indispensable pour les applications aérospatiales et industrielles.
Usinage final et traitement de surface
Une fois atteint la densité et la résistance souhaitées, le composite subit l'usinage final et le traitement de surface. Ces étapes améliorent la forme du matériau et améliorent ses propriétés de surface.
Façonnage et application de revêtements de protection
L'usinage consiste à couper, à broyer et à façonner le composite pour répondre à des exigences de conception spécifiques. Les fabricants utilisent des outils et des techniques avancés pour obtenir des dimensions précises et des surfaces lisses. Cette étape garantit que le composite s'intègre parfaitement dans son application prévue.
Après usinage, des traitements de surface sont appliqués pour protéger le composite des facteurs environnementaux. Les revêtements protecteurs, tels que les couches de carbure de silicium ou de céramique, améliorent la résistance du matériau à l'oxydation et à l'usure. Ces revêtements prolongent la durée de vie du composite et maintiennent sa performance dans des conditions difficiles.
Les traitements de surface jouent un rôle crucial dans la préservation de l'intégrité du composite, en particulier dans les environnements à haute température et corrosifs. (en milliers de dollars)
La combinaison d'usinage et de traitement de surface garantit que le composite répond aux normes fonctionnelles et esthétiques. Ces touches de finition préparent le matériau pour une utilisation dans des industries exigeantes, où la fiabilité et la durabilité sont primordiales.
En complétant les processus de densification et de finition, les fabricants reinforced carbon carbon composite qui excelle dans la force, la résistance à la chaleur et la durabilité. Ce matériel de pointe continue de stimuler l'innovation dans les secteurs de l'aérospatiale, de l'automobile et d'autres secteurs de haute performance.
Le carbone composite renforcé émerge comme un matériau révolutionnaire grâce à son procédé de fabrication minutieux. En préparant des fibres de carbone, en créant la matrice de carbone et en complétant la densification et la finition, ce composite atteint une résistance thermique inégalée. Ses applications s'étendent à des industries comme l'aérospatiale, le sport automobile et le génie civil, où la précision et la durabilité sont primordiales. Par exemple, les sports motorisés tirent parti de ce matériau pour réduire le poids tout en maintenant l'intégrité structurale, en améliorant les performances sur la piste. Comprendre la création d'un composite carbone renforcé souligne l'innovation qui stimule les progrès en ingénierie et en technologie.
FAQ
Quelles sont les formes de renforcement de la fibre de carbone ?
Le renforcement en fibre de carbone existe sous plusieurs formes, chacune adaptée à des applications spécifiques. Les types courants comprennent: polymères renforcés de fibres de carbone (PRFC), qui combinent des fibres de carbone avec une matrice polymère pour des matériaux légers et forts. Composés de fibres de carbone intégrer des fibres de carbone avec différentes matrices, offrant une polyvalence dans les propriétés mécaniques et thermiques. Composés carbonés renforcés se démarquent par leur capacité à supporter des températures extrêmes, les rendant idéales pour l'aérospatiale et l'ingénierie haute performance.
En quoi le carbone composite renforcé diffère-t-il des autres carbone composites?
Le composite carbone-carbone renforcé se distingue par sa combinaison unique de fibres de carbone et d'une matrice carbone. Cette structure offre une résistance thermique et mécanique exceptionnelle. Contrairement à d'autres composites carbone, qui peuvent utiliser des matrices polymère ou céramique, les composites carbone-carbone renforcés excellent dans les environnements à haute température, tels que les systèmes de freinage des avions et les buses de fusée.
Pourquoi le procédé de carbonisation est-il essentiel dans la fabrication?
Le processus de carbonisation transforme la résine en carbone, créant la matrice de carbone robuste qui lie les fibres. Cette étape permet au composite d'atteindre sa stabilité à haute température et sa résistance mécanique. Sans carbonisation, le matériau manquerait de durabilité et de performance pour des applications exigeantes.
La carbonisation est la pierre angulaire de la production de composite carbone-carbone renforcée, permettant au matériau de résister à des conditions extrêmes. (en milliers de dollars)
Quelles industries bénéficient le plus des composites carbone-carbone renforcés?
Les industries qui ont besoin de matériaux avec des rapports résistance-poids élevés et une résistance thermique sont très bénéfiques. Aéronautique s'appuie sur ces composites pour les composants comme les boucliers thermiques et les disques de frein. Les sports mécaniques les utilisent pour réduire le poids des véhicules tout en maintenant l'intégrité structurelle. D'autres secteurs, comme les semi-conducteurs et la métallurgie, tirent également parti de leurs propriétés avancées pour des applications spécialisées.
Comment les fibres de carbone sont-elles disposées pour assurer l'intégrité structurelle?
Les fabricants arrangent les fibres de carbone en utilisant des méthodes comme alignement unidirectionnel, tissage ou tressageet couche. L'alignement unidirectionnel maximise la résistance sur un seul axe, tandis que le tissage crée une durabilité multidirectionnelle. La couche équilibre la résistance et la rigidité dans toutes les directions. Ces arrangements garantissent que le composite satisfait aux exigences de rendement spécifiques.
Quel rôle la résine joue-t-elle dans le processus de fabrication?
La résine agit comme précurseur de la matrice de carbone. Il sature les fibres de carbone, créant une structure uniforme et une liaison forte. Pendant la carbonisation, la résine se transforme en carbone, formant la matrice qui améliore les propriétés mécaniques et thermiques composites. Les résines comme le phénolique et l'époxy sont couramment utilisées pour leur résistance à la chaleur et leur stabilité.
Comment la densification améliore-t-elle les propriétés composites ?
La densification implique des cycles répétés d'imprégnation et de carbonisation. Ces cycles remplissent les pores du composite, augmentant sa densité et sa résistance. Techniques avancées comme Infiltration de vapeur chimique (CVI) améliorer encore la performance du matériau en déposant du carbone à partir de précurseurs gazeux. Ce processus permet au composite de supporter des conditions de stress et de température élevées.
Quels traitements de surface sont appliqués aux composites carbonés renforcés?
Les traitements de surface protègent le composite des facteurs environnementaux comme l'oxydation et l'usure. Les fabricants appliquent des revêtements tels que carbure de silicium ou couches céramiques améliorer la résistance à la corrosion et aux températures élevées. Ces traitements prolongent la durée de vie du matériau et maintiennent sa performance dans des conditions difficiles.
Pourquoi un composite carbone-carbone renforcé coûte cher?
Le processus de production comporte plusieurs étapes précises, dont la carbonisation, la densification et le traitement de surface. Chaque étape nécessite une technologie et une expertise avancées, contribuant au coût du matériel. Cependant, ses propriétés exceptionnelles, telles que la résistance à la chaleur et la résistance, justifient l'investissement pour les industries exigeant des matériaux de haute performance.
Les composites carbone-carbone renforcés peuvent-ils être personnalisés pour des applications spécifiques?
Oui, les fabricants peuvent adapter les propriétés composites en adaptant les arrangements fibreux, les types de résine et les cycles de densification. La personnalisation garantit que le matériau répond aux exigences uniques des applications, que ce soit pour l'aérospatiale, le sport automobile ou l'utilisation industrielle. Cette flexibilité met en évidence la polyvalence et la valeur du matériau en ingénierie avancée.