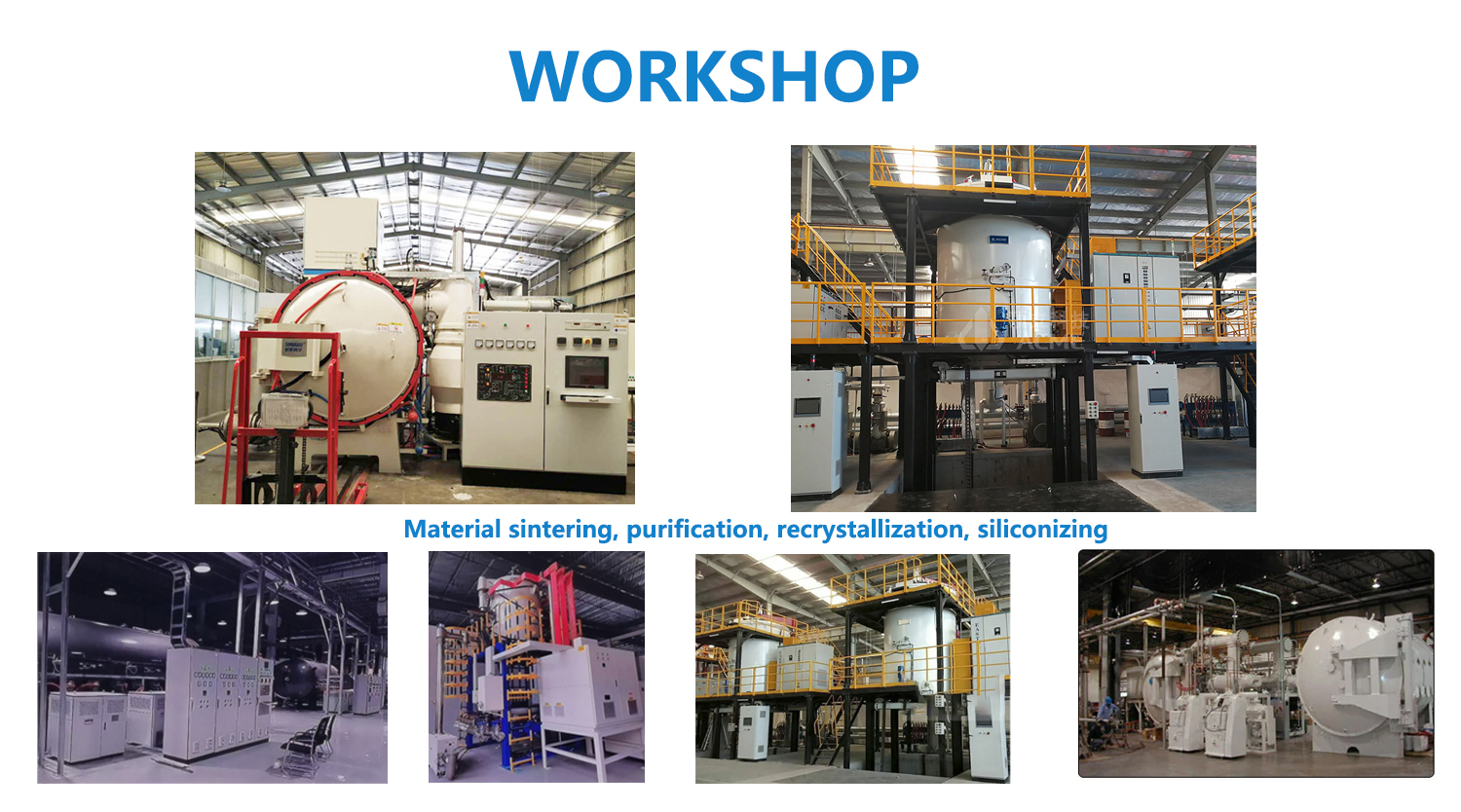
SiC coating carriers have transformed semiconductor manufacturing by addressing critical challenges in high-precision processes. Their robust Revêtement SiC ensures exceptional thermal stability and contamination resistance, making them indispensable for demanding applications. These SiC coating carriers enhance etching efficiency and precision while reducing particle generation, creating a clean surface for high-purity material deposition. Their durability minimizes maintenance needs, extending component lifespan and reducing costs. With advanced properties like resistance to oxidation and chemical corrosion, SiC coating carriers outperform traditional materials, ensuring reliable performance in extreme environments. This innovation supports consistent results, driving efficiency and quality in semiconductor production, particularly through the use of CVD SiC coating techniques.
Principaux enseignements
- SiC coating carriers help make semiconductors by staying strong under heat and avoiding contamination.
- They spread heat evenly, which is important for making good semiconductor devices.
- SiC coating carriers stop particles from forming, keeping surfaces clean for pure material layers.
- They last a long time and need less fixing, saving money and time.
- These carriers work well in very hot places, perfect for tough semiconductor tasks.
- Using SiC coating carriers saves money over time by needing less care and boosting work speed.
- SiC coating carriers make etching more accurate, helping produce more semiconductors.
- Their special features work for many uses, like car electronics and green energy systems.
Understanding SiC Coating Carriers
Composition and Properties of SiC Coating Carriers
SiC coating carriers are crafted using advanced chemical vapor deposition (CVD) techniques. This process deposits high-purity silicon carbide molecules onto materials like graphite, creating a robust protective layer. The resulting carriers exhibit exceptional physical and chemical properties that make them ideal for semiconductor manufacturing.
Key properties include high thermal conductivity, which ensures consistent temperature control during wafer processing. This feature is critical for forming uniform epitaxial layers. SiC coating carriers also resist oxidation and chemical corrosion, maintaining their integrity in harsh environments. Their durability extends their lifespan, reducing the need for frequent replacements.
Propriété | Description |
---|---|
High Thermal Conductivity | Ensures efficient heat management, crucial for maintaining wafer quality during high-temperature processes. |
Temperature Resistance | Withstands extreme temperatures, making them ideal for thermal management in semiconductor processes. |
Chemical Inertness | Acts as a robust barrier against chemical reactions and corrosion, ensuring carriers remain unaffected by harsh chemicals. |
Durabilité | Enhances resistance to wear, oxidation, and chemical corrosion, making them reliable for precision industries. |
These properties enable SiC coating carriers to perform reliably in demanding semiconductor applications.
Rôle dans la fabrication des semi-conducteurs
Revêtement SiC carriers play a vital role in semiconductor manufacturing by enhancing process efficiency and reliability. Their thermal stability ensures optimal processing temperatures, which is essential for high-precision operations like Rapid Thermal Processing (RTP) and Rapid Thermal Annealing (RTA). These carriers also maintain high purity, preventing contamination during wafer handling and chemical vapor deposition (CVD).
Their chemical resistance reduces the risk of reactions with processing materials, preserving the integrity of wafers. Additionally, SiC coating carriers minimize surface roughness and porosity, creating a cleaner environment for material deposition. This feature is particularly beneficial for epitaxial processes, where precise temperature control is necessary for uniform film growth. By excelling in these roles, SiC coating carriers contribute to consistent and high-quality semiconductor production.
Comparison with Traditional Carriers
SiC coating carriers outperform traditional carriers in several key areas. Traditional materials, such as quartz or uncoated graphite, often struggle to withstand the extreme conditions of semiconductor manufacturing. In contrast, SiC coated graphite carriers combine the lightweight strength of graphite with the protective properties of silicon carbide. This combination makes them ideal for high-temperature and chemically aggressive environments.
- SiC coating carriers offer superior thermal stability, allowing them to endure rapid temperature changes without compromising performance.
- Their mechanical strength and resistance to wear significantly extend their lifespan, reducing maintenance costs.
- The chemical inertness of SiC coatings ensures carriers remain unaffected by corrosive gases and harsh chemicals, unlike traditional materials.
These advantages make SiC coating carriers a more efficient and durable choice for modern semiconductor processes.
Benefits of SiC Coating Carriers
Enhanced Durability and Longevity
SiC coating carriers demonstrate exceptional durability, making them a reliable choice for semiconductor manufacturing. The combination of a lightweight graphite core and a silicon carbide coating enhances their resistance to wear, oxidation, and chemical corrosion. This robust structure ensures the carriers maintain their integrity even under demanding conditions.
- The SiC layer protects the graphite substrate from thermal shock and mechanical stress, ensuring long-term reliability.
- Research shows that SiC coatings significantly improve the wear resistance of graphite materials, reducing the need for frequent replacements.
- The silicon carbide coating extends the lifespan of carriers by preventing oxidation and degradation at high temperatures.
These features reduce downtime and operational costs for manufacturers, making SiC coating carriers a cost-effective solution. Their ability to perform consistently over extended periods is crucial for maintaining efficiency in semiconductor fabrication.
Superior Thermal Stability
SiC coating carriers excel in high-temperature environments due to their superior thermal stability. Their high thermal conductivity ensures efficient heat management, which is essential for maintaining wafer quality during processes like chemical vapor deposition (CVD).
- These carriers withstand extreme temperatures, making them ideal for thermal management in semiconductor manufacturing.
- The SiC coating resists oxidation and deformation, even during rapid temperature fluctuations.
- Their durability ensures reliable performance in demanding environments, reducing the risk of errors during production.
This thermal stability supports precise fabrication and functional control of semiconductor wafers, enhancing the overall efficiency of chip manufacturing.
Contamination and Erosion Resistance
SiC coating carriers provide outstanding resistance to contamination and erosion, ensuring a clean and stable platform for semiconductor processes. The silicon carbide layer acts as a barrier against chemical reactions, protecting the graphite core from oxidation and corrosion.
- The hard SiC coating minimizes particle generation, creating a smooth surface for high-purity material deposition.
- Its mechanical strength protects the carrier from wear, ensuring long-term reliability in harsh environments.
- The SiC layer maintains structural integrity under extreme temperatures, reducing deformation and contamination risks.
These properties make SiC coating carriers indispensable for processes like etching and deposition, where precision and cleanliness are critical. By reducing contamination and erosion, these carriers enhance the quality and consistency of semiconductor production.
Cost Efficiency in Long-Term Use
SiC coating carriers offer significant cost advantages over traditional alternatives in semiconductor manufacturing. Their unique properties reduce maintenance needs and operational disruptions, making them a cost-effective solution for long-term use. Manufacturers benefit from their ability to withstand harsh conditions, which minimizes wear and tear during demanding processes.
The high durability of SiC coatings ensures that carriers maintain their structural integrity even under extreme temperatures and chemical exposure. This durability reduces the frequency of replacements, saving manufacturers money over time. Additionally, the robust silicon carbide layer protects the graphite core from oxidation and mechanical stress, further extending the lifespan of the carriers.
Investing in SiC coating carriers leads to substantial long-term savings. Their superior thermal management capabilities enhance process efficiency, reducing energy consumption during high-temperature operations. This efficiency translates into lower operational costs for manufacturers.
Several factors contribute to the cost efficiency of SiC coating carriers:
- They require less frequent maintenance due to their resistance to erosion and contamination.
- Their ability to endure rapid temperature changes minimizes downtime caused by equipment failures.
- Their extended lifespan reduces the need for frequent replacements, lowering overall material costs.
Manufacturers also experience increased productivity with SiC coating carriers. Their reliability in harsh environments ensures uninterrupted operations, which helps maintain consistent production schedules. By reducing operational interruptions, these carriers allow manufacturers to optimize their resources and achieve higher output levels.
The initial investment in SiC coating carriers may appear higher than traditional options. However, their long-term benefits far outweigh the upfront costs. Over time, the reduced maintenance expenses, extended lifespan, and improved productivity result in significant cost savings. These advantages make SiC coating carriers an indispensable choice for modern semiconductor manufacturing.
Applications in Semiconductor Manufacturing
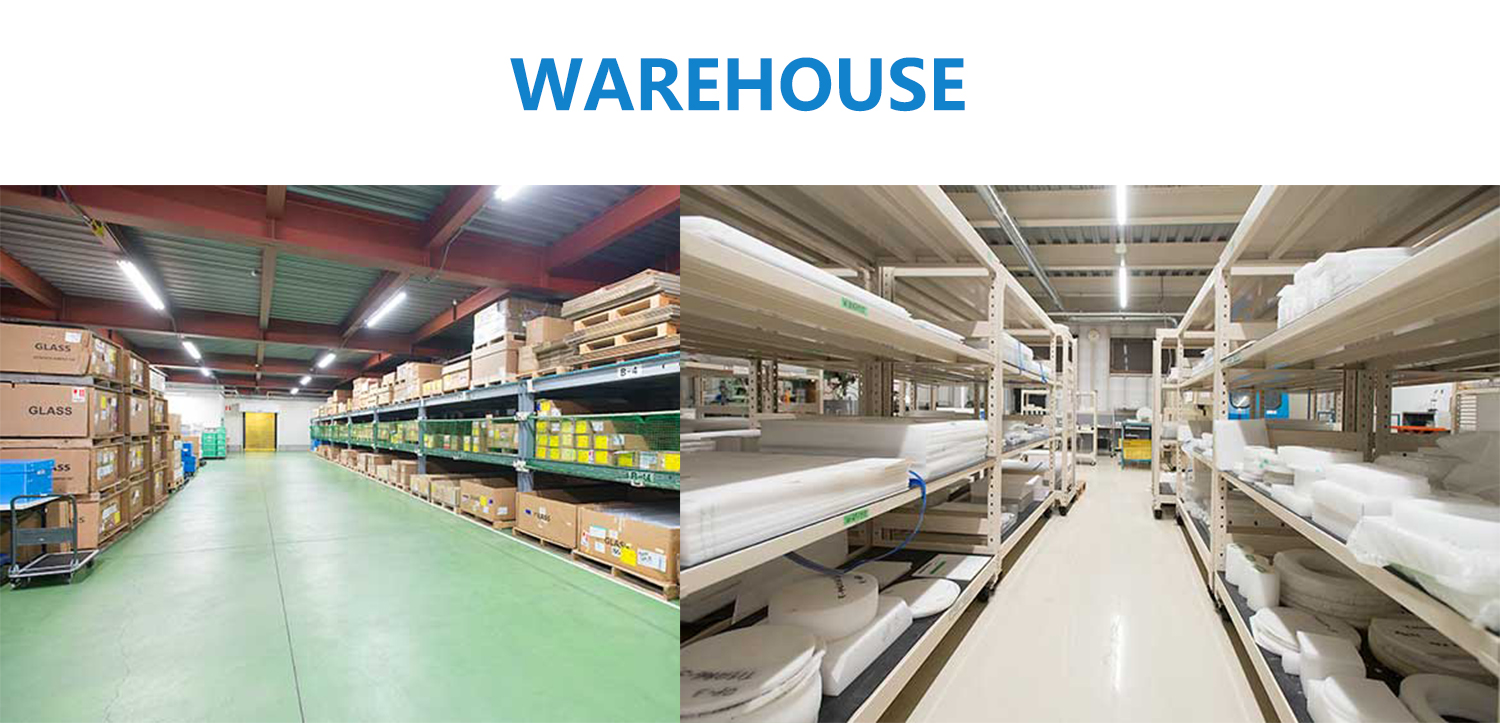
Wafer Processing and Handling
SiC coating carriers play a pivotal role in wafer processing and handling within semiconductor manufacturing. These carriers provide a stable platform for wafers during high-temperature processes, ensuring uniform heat distribution and minimizing thermal stress. The silicon carbide coating enhances thermal stability, allowing the carriers to withstand rapid temperature fluctuations without compromising structural integrity. This capability ensures consistent wafer quality, which is essential for producing reliable semiconductor devices.
In processes like Rapid Thermal Processing (RTP) and Rapid Thermal Annealing (RTA), SiC coating carriers maintain stability under varying thermal conditions. This stability supports the production of high-quality semiconductor chips by preventing deformation or contamination during critical stages. By offering a clean and controlled environment, these carriers contribute to the precision and reliability required in modern semiconductor fabrication.
High-Temperature Operations
SiC coating carriers excel in high-temperature operations, outperforming traditional materials in demanding environments. Their unique properties make them indispensable for processes requiring extreme thermal stability and durability.
- Stabilité thermique: The SiC coating provides excellent resistance to thermal shock, maintaining structural integrity under rapid temperature changes.
- Mechanical Strength: The combination of graphite’s strength and SiC’s hardness ensures durability against operational stress.
- Chemical Resistance: The SiC layer protects the graphite core from oxidation and corrosion, which is crucial in harsh environments.
These features enable SiC coating carriers to perform reliably in high-temperature processes like chemical vapor deposition (CVD) and plasma-enhanced chemical vapor deposition (PECVD). Their ability to endure extreme conditions minimizes downtime caused by equipment failures or replacements, ensuring uninterrupted production during high-volume manufacturing cycles.
Etching and Deposition Processes
SiC coating carriers are essential for etching and deposition processes in semiconductor manufacturing. The silicon carbide layer acts as a robust barrier against chemical reactions, protecting the graphite core from oxidation and erosion. This protection ensures the carriers maintain their structural integrity even in chemically aggressive environments.
The hard SiC coating minimizes particle generation, creating a smooth and clean surface for high-purity material deposition. This cleanliness is critical for processes like epitaxial growth, where precision and uniformity are paramount. By reducing contamination risks, SiC coating carriers enhance the quality and consistency of semiconductor devices.
Manufacturers benefit from the durability and reliability of these carriers during etching and deposition. Their resistance to wear and chemical corrosion extends their lifespan, reducing the need for frequent replacements. This longevity translates into cost savings and improved operational efficiency, making SiC coating carriers a preferred choice for advanced semiconductor processes.
Transport and Storage of Semiconductor Materials
The transport and storage of semiconductor materials demand precision and reliability. SiC coating carriers provide an ideal solution for these critical processes. Their advanced properties ensure the safe handling of delicate semiconductor components, maintaining their quality and performance.
Key Features Supporting Transport and Storage
-
Durability and Strength
SiC coating carriers exhibit exceptional mechanical strength. The silicon carbide layer protects the graphite core from physical damage during transport. This durability ensures that carriers withstand mechanical shocks and vibrations, safeguarding semiconductor materials. -
Contamination Resistance
The high-purity SiC coating acts as a barrier against contaminants. It prevents particle generation and chemical reactions, maintaining a clean environment for semiconductor materials. This feature is crucial for preserving the integrity of wafers and other sensitive components. -
Stabilité thermique
SiC coating carriers resist extreme temperature fluctuations. This property ensures that semiconductor materials remain stable during storage in varying environmental conditions. The carriers maintain their structural integrity, reducing the risk of thermal stress on stored components. -
Chemical Inertness
The silicon carbide layer resists corrosion from acids, alkalis, and other chemicals. This resistance ensures that carriers remain unaffected by exposure to harsh environments, providing long-term reliability.
Benefits for Semiconductor Manufacturers
Conseil : Proper transport and storage of semiconductor materials reduce production losses and improve efficiency.
- Enhanced Protection: SiC coating carriers shield semiconductor materials from physical and chemical damage. This protection minimizes the risk of defects during transport and storage.
- Extended Lifespan: The robust SiC coating ensures carriers remain functional over multiple cycles of use. This longevity reduces replacement costs for manufacturers.
- Improved Efficiency: The contamination resistance of SiC coating carriers eliminates the need for additional cleaning processes. This efficiency saves time and resources.
Comparison with Traditional Carriers
Fonctionnalité | SiC Coating Carriers | Traditional Carriers |
---|---|---|
Durabilité | High resistance to mechanical stress | Prone to wear and damage |
Contamination Resistance | Prevents particle generation | Higher risk of contamination |
Stabilité thermique | Withstands extreme temperature changes | Limited thermal resistance |
Chemical Resistance | Inert to corrosive agents | Susceptible to chemical reactions |
SiC coating carriers outperform traditional carriers in every aspect. Their advanced properties make them indispensable for the transport and storage of semiconductor materials.
Investing in SiC coating carriers ensures the safe handling of semiconductor components. Their reliability and efficiency support consistent production quality, making them a valuable asset for manufacturers.
Impact on Manufacturing Efficiency
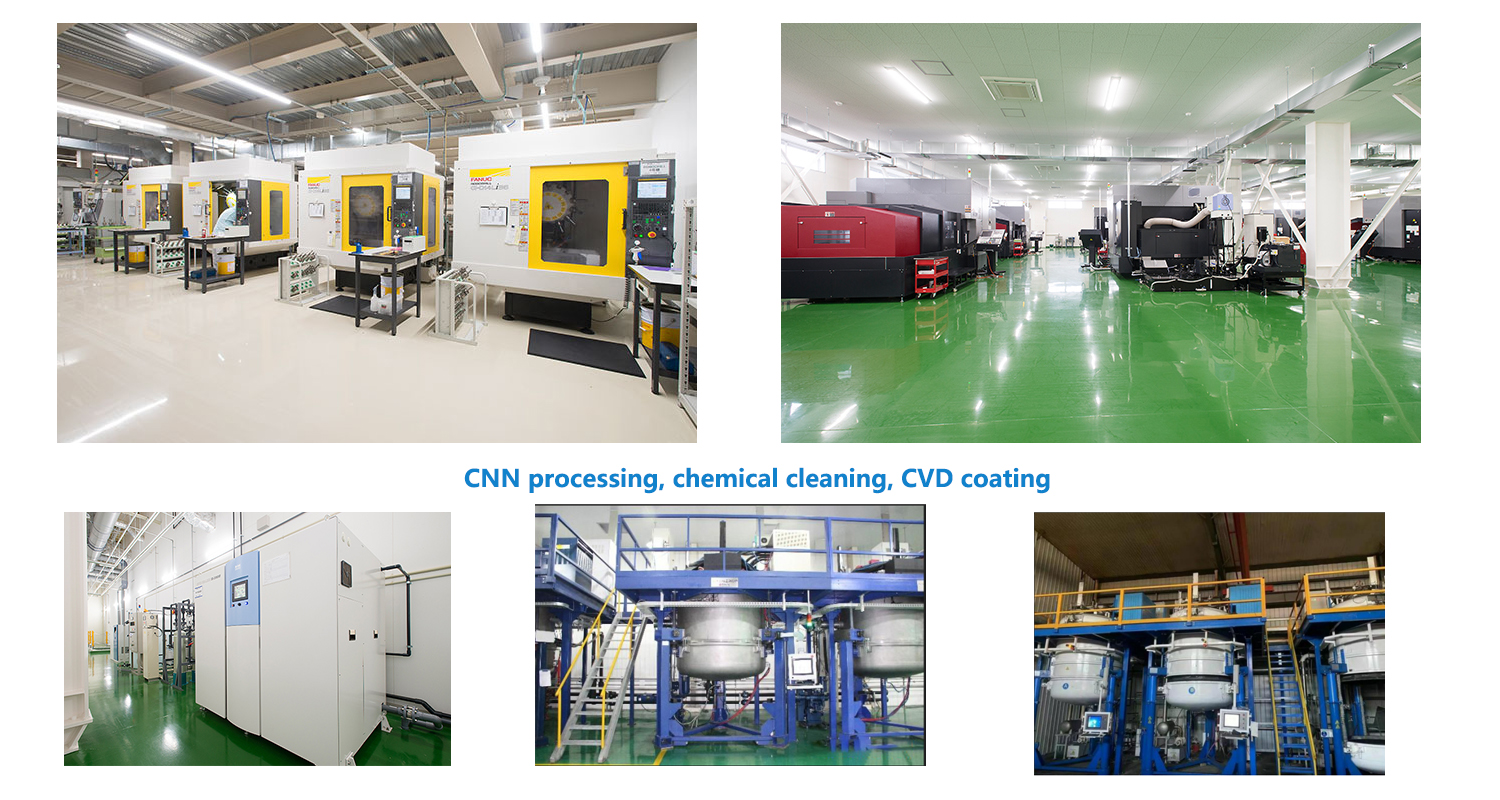
Reduced Downtime and Maintenance
SiC coating carriers significantly reduce downtime and maintenance in semiconductor manufacturing. Their robust silicon carbide layer protects the graphite core from wear and tear, even in high-temperature and chemically aggressive environments. This durability ensures that the carriers maintain their structural integrity over extended periods, minimizing the need for frequent replacements.
The carriers’ resistance to oxidation and corrosion further enhances their reliability. By preventing damage caused by exposure to harsh chemicals, they reduce the likelihood of equipment failures. Manufacturers benefit from uninterrupted production cycles, as the carriers consistently perform under demanding conditions.
Note: Reduced maintenance requirements allow manufacturers to allocate resources to other critical areas, such as process optimization and innovation.
The long-term use of SiC-coated carriers leads to substantial cost savings. Their ability to withstand rigorous manufacturing processes ensures fewer disruptions, enabling manufacturers to maintain efficient operations and meet production targets.
Higher Yield Rates and Consistency
SiC coating carriers play a crucial role in achieving higher yield rates and consistency in semiconductor production. Their thermal and chemical stability provides a reliable platform for wafer processing, reducing the risk of production errors. This stability ensures that each wafer receives uniform treatment, which is essential for producing functional semiconductor devices.
- The combination of graphite and silicon carbide enhances thermal conductivity, ensuring consistent heat distribution across wafers.
- Efficient heat transfer supports uniform film growth, a critical factor in achieving high-quality results.
- The carriers’ contamination resistance minimizes particle generation, creating a clean environment for material deposition.
Their ability to enhance etching efficiency and precision further contributes to higher yields. The robust protective layer withstands high temperatures and corrosive environments, ensuring consistent performance throughout the manufacturing process. This reliability allows manufacturers to produce more devices with fewer resources, improving overall efficiency.
Conseil: Consistent performance from SiC coating carriers reduces waste, helping manufacturers achieve sustainability goals while maintaining profitability.
Improved Product Quality
SiC coating carriers directly impact the quality of semiconductor devices. Their ability to provide a stable platform during high-temperature processes ensures uniform heat distribution, which minimizes thermal stress on wafers. This stability is critical for achieving precise and uniform etching patterns, a key factor in producing high-quality chips.
The carriers’ contamination resistance also plays a vital role in improving product quality. By preventing particle generation and chemical reactions, they create a clean surface for material deposition. This cleanliness ensures that wafers remain free from defects, resulting in reliable and high-performing semiconductor devices.
Callout: Manufacturers using SiC coating carriers report improved device performance due to enhanced precision and reduced contamination risks.
The long-term implications of using these carriers extend beyond immediate quality improvements. Their durability and reliability allow manufacturers to focus on innovation rather than equipment maintenance. This focus drives advancements in semiconductor technology, ensuring that products meet the evolving demands of the industry.
Streamlined and Reliable Production Processes
SiC coating carriers simplify semiconductor manufacturing by ensuring smooth and dependable workflows. Their advanced properties eliminate common inefficiencies, allowing manufacturers to achieve consistent results with minimal disruptions.
Minimized Process Interruptions
SiC coating carriers reduce interruptions during production. Their high durability and resistance to wear prevent frequent equipment failures. This reliability ensures that manufacturing lines operate without unexpected downtime. The carriers’ ability to withstand extreme temperatures and corrosive environments further enhances their dependability.
Conseil: Consistent equipment performance leads to uninterrupted production schedules, helping manufacturers meet tight deadlines.
Improved Workflow Efficiency
The thermal stability of SiC coating carriers supports precise temperature control during critical processes. This stability ensures uniform heat distribution, which is essential for producing high-quality semiconductor wafers. The carriers also resist contamination, maintaining a clean environment for material deposition. These features streamline workflows by reducing the need for additional cleaning or adjustments.
- Stabilité thermique: Maintains consistent processing conditions.
- Contamination Resistance: Prevents defects caused by particle generation.
- Durabilité: Reduces the frequency of carrier replacements.
These advantages allow manufacturers to optimize their resources and focus on innovation rather than troubleshooting.
Enhanced Process Reliability
SiC coating carriers provide a stable platform for semiconductor fabrication. Their robust silicon carbide layer protects against mechanical stress and chemical reactions. This protection ensures that carriers perform reliably under demanding conditions. Manufacturers benefit from consistent results, as the carriers maintain their structural integrity throughout multiple production cycles.
Fonctionnalité | Bénéfice |
---|---|
High Hardness | Prevents deformation during high-pressure processes. |
Chemical Inertness | Protects against corrosion, ensuring long-term reliability. |
Smooth Surface | Reduces particle adhesion, improving wafer quality. |
Callout: Reliable carriers reduce variability in production, ensuring that every batch meets quality standards.
Support for High-Volume Manufacturing
SiC coating carriers excel in high-volume production environments. Their ability to endure rigorous processes minimizes the need for maintenance, allowing manufacturers to maintain steady output levels. The carriers’ long lifespan reduces operational costs, making them a cost-effective choice for large-scale operations.
Investing in SiC coating carriers ensures streamlined production processes. Their reliability and efficiency support manufacturers in achieving consistent results, even under challenging conditions.
By integrating SiC coating carriers into their workflows, manufacturers can enhance productivity and maintain high standards of quality. These carriers represent a vital component in modern semiconductor manufacturing, driving efficiency and reliability across the industry.
Challenges and Considerations
Initial Investment and Cost Implications
SiC coating carriers require a higher initial investment compared to traditional carriers. This cost stems from the advanced materials and manufacturing processes involved in their production. The chemical vapor deposition (CVD) method used to create the silicon carbide coating ensures high purity and durability, but it also increases production expenses. Manufacturers must weigh these upfront costs against the long-term benefits, such as reduced maintenance and extended lifespan.
The durability of SiC coating carriers minimizes the need for frequent replacements, which offsets the initial expense over time. Their ability to withstand extreme temperatures and corrosive environments reduces operational disruptions, leading to cost savings in the long run. For high-volume semiconductor manufacturers, this investment proves valuable by enhancing efficiency and reliability. However, smaller operations may need to carefully evaluate their budget and production needs before adopting this technology.
Conseil: Manufacturers can calculate the total cost of ownership (TCO) to understand the long-term financial benefits of SiC coating carriers.
Integration with Existing Systems
Integrating SiC coating carriers into existing semiconductor manufacturing systems requires careful planning. These carriers often replace traditional materials like quartz or uncoated graphite, which may involve adjustments to equipment or processes. Manufacturers must ensure compatibility between the carriers and their current systems to avoid disruptions.
The lightweight nature of graphite cores combined with the robust SiC coating makes these carriers versatile. However, their unique properties, such as high thermal conductivity and chemical resistance, may necessitate recalibration of temperature controls or chemical handling protocols. Training staff to handle and maintain these carriers properly is another important consideration.
Callout: Proper integration ensures that manufacturers can fully leverage the benefits of SiC coating carriers without compromising production efficiency.
Maintenance and Operational Factors
SiC coating carriers require specific maintenance practices to ensure optimal performance. Regular inspections help identify early signs of wear or damage, allowing manufacturers to address issues before they escalate. Cleaning the carriers properly is essential to remove contaminants without harming the SiC coating. Using non-abrasive cleaning methods preserves the integrity of the protective layer.
Environmental factors also play a significant role in the performance of these carriers. High temperatures demand materials with excellent thermal stability, which the SiC coating provides. The impervious nature of the coating protects against oxidation and corrosion in chemically aggressive environments. However, improper storage can expose carriers to moisture or dust, potentially affecting their performance. Storing them in controlled environments mitigates these risks.
- Regular inspections detect wear or damage early.
- Proper cleaning methods prevent harm to the SiC coating.
- Adherence to operational guidelines minimizes mechanical stress.
- Controlled storage conditions reduce exposure to contaminants.
Note: Following these maintenance practices ensures that SiC coating carriers deliver consistent results and maintain their longevity.
By addressing these challenges and considerations, manufacturers can maximize the benefits of SiC coating carriers while minimizing potential risks. Proper planning and maintenance allow these carriers to enhance efficiency and reliability in semiconductor manufacturing.
Future of SiC Coating Carriers
Advancements in Material Science and Technology
Material science continues to drive the evolution of SiC coating carriers, enhancing their performance and expanding their applications. Researchers have developed innovative techniques to improve the properties of silicon carbide coatings, making them more efficient and reliable for semiconductor manufacturing.
- High Thermal Conductivity: Advanced SiC coatings now offer superior heat management, ensuring consistent wafer quality during high-temperature processes.
- Temperature Resistance: These coatings withstand extreme thermal conditions, making them ideal for demanding semiconductor applications.
- Chemical Inertness: The inert nature of SiC coatings protects against chemical reactions and corrosion, ensuring durability in harsh environments.
- Durabilité: Combining lightweight graphite with silicon carbide enhances resistance to wear, oxidation, and chemical corrosion, extending the lifespan of carriers.
These advancements enable SiC coating carriers to meet the rigorous demands of modern semiconductor processes. As material science progresses, manufacturers can expect even greater improvements in thermal stability, mechanical strength, and chemical resistance.
Expanding Applications in Advanced Semiconductor Processes
SiC coating carriers are finding new applications in advanced semiconductor processes, reflecting their versatility and reliability. Industries beyond traditional semiconductor manufacturing are adopting these carriers to meet their unique requirements.
- Automotive Sector: SiC coated carriers play a critical role in power electronics for electric vehicles. They enhance energy efficiency and contribute to the sustainability of automotive technologies.
- Systèmes d'énergies renouvelables: These carriers improve the reliability and lifespan of components in solar inverters and wind energy systems, supporting the growth of clean energy solutions.
- Telecommunications: The rise of 5G infrastructure and high-frequency devices has increased the demand for SiC coating carriers. Their stability and efficiency ensure reliable performance in communication systems.
These emerging applications highlight the growing importance of SiC coating carriers in diverse industries. Their ability to perform under extreme conditions makes them indispensable for cutting-edge technologies.
Potential for Cost Reductions and Broader Adoption
The initial cost of SiC coating carriers may seem high, but advancements in manufacturing techniques are paving the way for cost reductions. As production processes become more efficient, the affordability of these carriers is expected to improve, making them accessible to a wider range of manufacturers.
Conseil: Investing in SiC coating carriers now can lead to significant long-term savings due to their durability and reduced maintenance needs.
Broader adoption of SiC coating carriers will also benefit from their proven ability to enhance manufacturing efficiency. Their extended lifespan and resistance to wear reduce operational costs, while their reliability minimizes downtime. These advantages make them an attractive option for manufacturers seeking to optimize their processes.
As the semiconductor industry continues to evolve, SiC coating carriers are poised to play a pivotal role in shaping its future. Their unmatched properties and expanding applications ensure they remain at the forefront of technological innovation.
SiC coating carriers have revolutionized semiconductor manufacturing by addressing critical challenges in durability, thermal stability, and contamination resistance. These carriers enhance etching efficiency, reduce contamination risks, and ensure consistent performance in high-temperature environments. Their ability to create a clean and controlled platform for wafer processing improves product quality and boosts manufacturing efficiency.
As the semiconductor industry advances, SiC coating carriers will continue to drive innovation. Their durability and precision support high-volume production and advanced manufacturing techniques, ensuring they remain essential for meeting future demands. By investing in these carriers, manufacturers can achieve long-term cost savings and maintain a competitive edge.
FAQ
What are SiC coating carriers made of?
SiC coating carriers consist of a graphite core coated with high-purity silicon carbide. The chemical vapor deposition (CVD) process creates this robust layer, which enhances durability, thermal stability, and chemical resistance.
Why are SiC coating carriers important for semiconductor manufacturing?
These carriers improve manufacturing efficiency by providing thermal stability, contamination resistance, and durability. They ensure consistent wafer quality during high-temperature processes like etching and deposition.
How do SiC coating carriers reduce contamination?
The silicon carbide layer prevents particle generation and resists chemical reactions. This creates a clean surface for wafer processing, reducing defects and improving product quality.
Can SiC coating carriers withstand extreme temperatures?
Yes, they maintain integrity at temperatures up to 1600°C. Their high thermal conductivity ensures efficient heat management, making them ideal for high-temperature semiconductor processes.
What makes SiC coating carriers cost-efficient?
Their durability reduces the need for frequent replacements. They also minimize downtime and maintenance, leading to long-term savings for manufacturers.
Are SiC coating carriers compatible with existing systems?
Yes, they integrate well with most semiconductor manufacturing systems. However, manufacturers may need to adjust equipment settings to optimize performance.
What industries benefit from SiC coating carriers?
Semiconductor manufacturing, automotive electronics, renewable energy systems, and telecommunications all benefit from these carriers. Their reliability supports advanced technologies like 5G and electric vehicles.
How do SiC coating carriers improve product quality?
They provide a stable, contamination-free platform for wafer processing. This ensures uniform heat distribution and precise etching, resulting in high-quality semiconductor devices.
Conseil: Investing in SiC coating carriers enhances efficiency and reliability, making them a valuable asset for modern manufacturing.