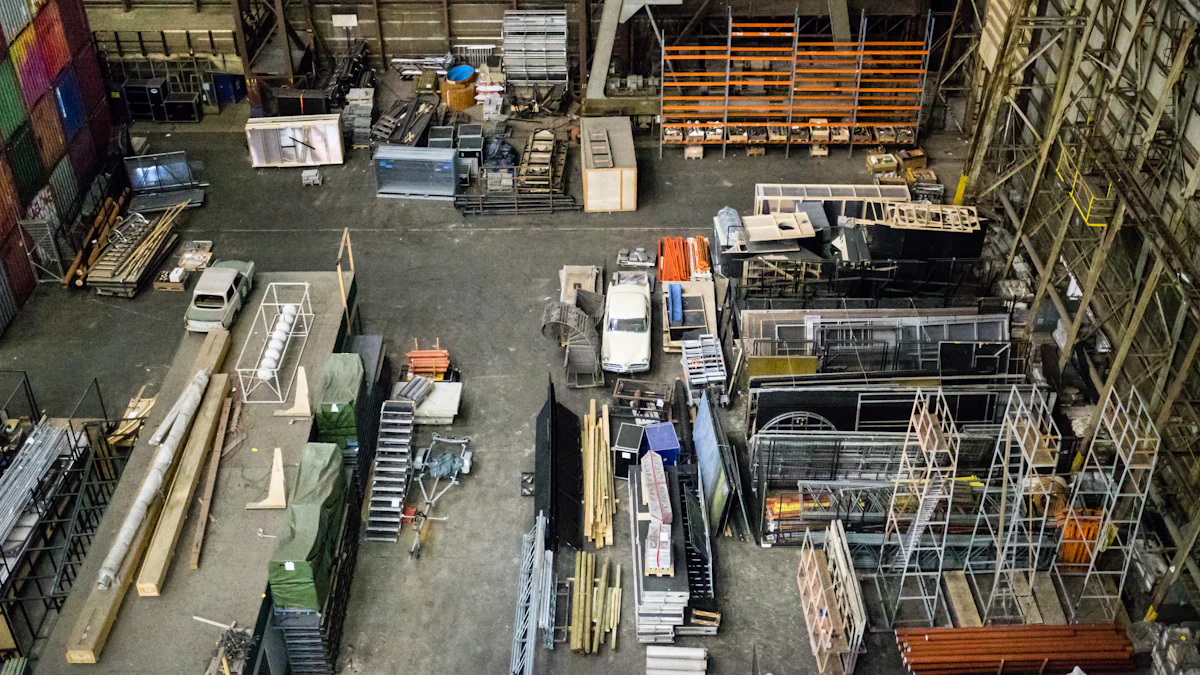
Carrier gases play a crucial role in shaping the growth of GaN epitaxy carrier processes. They influence the growth rate, surface morphology, and defect density of the material. For instance, different gases like oxygen, nitrogen, and air can significantly alter these characteristics. Oxygen, for example, can achieve a growth rate of 10.3 nm/min, while nitrogen results in a slower rate of 2.4 nm/min. The choice of carrier gas directly impacts the quality of GaN films, making it essential to understand their effects for optimizing material quality and enhancing device performance.
Key Takeaways
- Carrier gases are essential in GaN epitaxy, influencing growth rate, surface quality, and defect density.
- Choosing the right carrier gas, such as hydrogen or nitrogen, can significantly enhance the quality of GaN films, impacting their performance in electronic devices.
- Hydrogen acts as a reducing agent, minimizing defects and improving surface smoothness, making it a preferred choice for high-quality GaN production.
- Nitrogen provides a stable growth environment, ensuring even distribution of precursor materials, which is crucial for consistent film quality.
- Optimizing carrier gas flow rates and compositions can lead to superior material properties and increased production efficiency.
- The selection of carrier gases not only affects manufacturing quality but also has implications for cost-effectiveness and environmental sustainability.
- Future trends indicate a shift towards hydrogen as a primary carrier gas due to its reliability and the growing demand for eco-friendly production methods.
Overview of GaN Epitaxial Growth
The Epitaxial Growth Process
Epitaxial growth forms the backbone of semiconductor manufacturing. It involves depositing a crystalline layer on a substrate, ensuring that the new layer mimics the substrate’s crystal structure. In the case of GaN, this process is pivotal for creating high-quality films used in electronic devices. The growth typically occurs in a controlled environment, where temperature, pressure, and gas composition are meticulously managed. By maintaining these conditions, manufacturers can achieve uniform layers with minimal defects. This precision is crucial because even minor imperfections can significantly impact the performance of the final product.
Key Factors in GaN Growth
Several factors influence the success of GaN epitaxial growth. First, the choice of substrate plays a vital role. Common substrates include sapphire, silicon carbide, and silicon. Each offers distinct advantages and challenges. For instance, sapphire provides excellent thermal stability, while silicon offers cost-effectiveness.
Second, the growth temperature must be carefully controlled. Higher temperatures can enhance the quality of the GaN layer but may also increase the risk of defects.
Third, the type and flow rate of carrier gases, such as hydrogen or nitrogen, directly affect the growth rate and surface morphology. These gases help transport the precursor materials to the substrate, facilitating the chemical reactions necessary for growth.
Lastly, reactor pressure and doping levels can also impact the process. By optimizing these factors, manufacturers can produce GaN films with superior electrical and optical properties, paving the way for advanced electronic applications.
Role of Carrier Gases in GaN Epitaxy
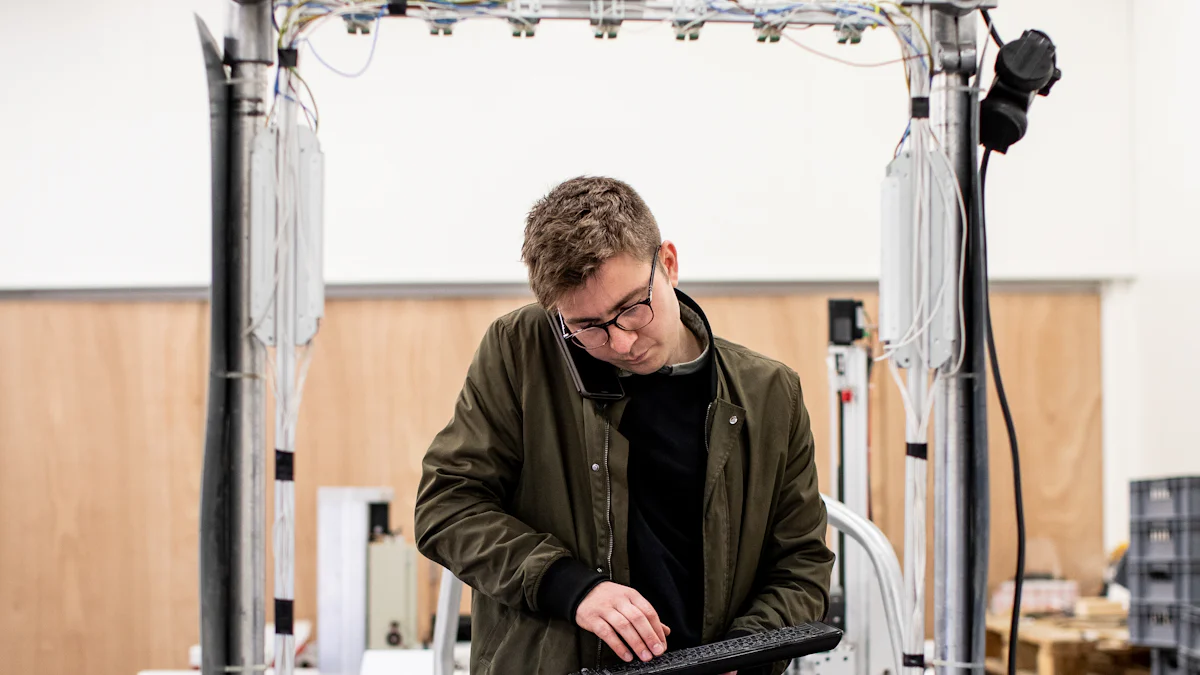
Function in Epitaxial Growth
Carrier gases serve as the unsung heroes in the world of GaN epitaxy. They transport the precursor materials to the substrate, ensuring that the chemical reactions necessary for growth occur efficiently. Imagine them as the delivery trucks in a bustling city, bringing essential supplies to where they’re needed most. Without these gases, the growth process would stall, much like a city without its supply chain.
In the context of GaN epitaxy, carrier gases like hydrogen and nitrogen play pivotal roles. Hydrogen, for instance, acts as a reducing agent, helping to remove unwanted oxygen from the growth environment. This action minimizes the formation of defects, leading to higher-quality GaN films. On the other hand, nitrogen serves as an inert carrier, providing a stable environment for the growth process. By maintaining a consistent flow, it ensures that the precursor materials reach the substrate evenly, promoting uniform layer formation.
Impact on Growth Characteristics
The choice of carrier gas doesn’t just influence the growth process; it also shapes the characteristics of the resulting GaN films. Different gases can lead to variations in growth rate, surface morphology, and defect density. For example, using hydrogen as a carrier gas can enhance the smoothness of the GaN surface, resulting in films with fewer imperfections. This improvement occurs because hydrogen helps to etch away any roughness during growth, leaving behind a polished finish.
Moreover, the type of carrier gas can affect the crystal quality of the GaN films. Studies have shown that the presence of oxygen in the carrier gas can significantly improve crystal quality by reducing defects like oxygen vacancies. This finding highlights the importance of selecting the right gas composition for achieving optimal material properties.
Types of Carrier Gases and Their Effects
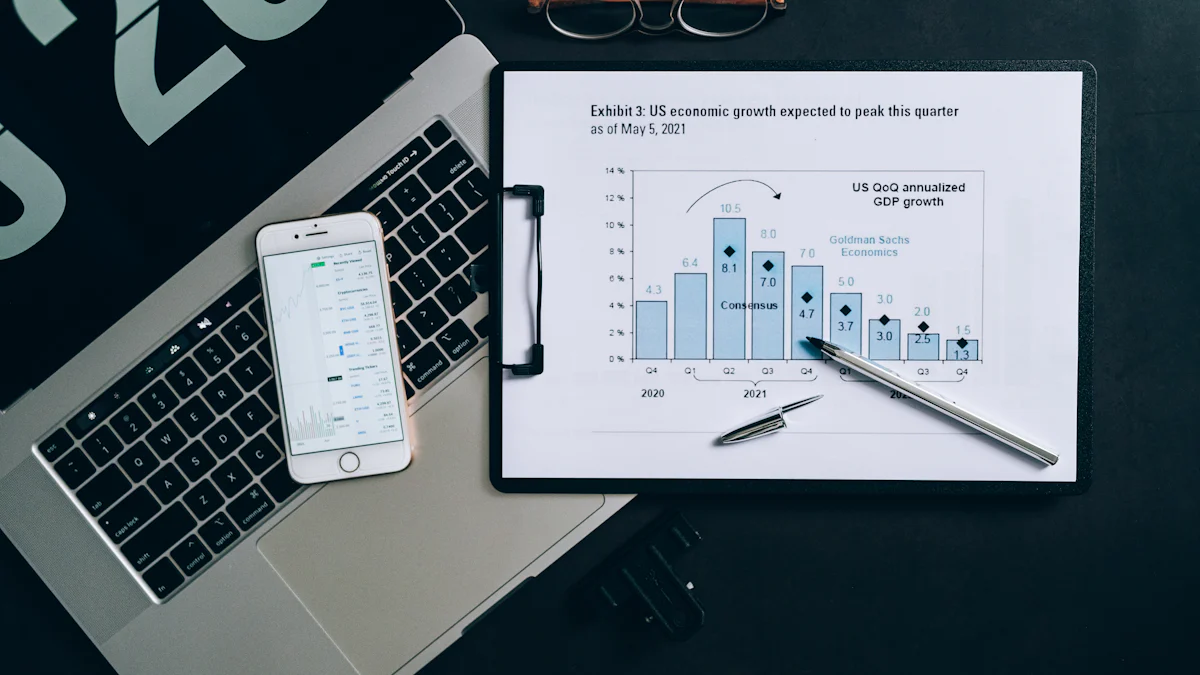
Hydrogen as a Carrier Gas
Hydrogen plays a significant role in the GaN epitaxy carrier process. It acts as a reducing agent, which helps in removing unwanted oxygen from the growth environment. This action reduces the formation of defects, leading to higher-quality GaN films. In hydride vapor phase epitaxy (HVPE), hydrogen serves as the primary carrier gas. It enhances the smoothness of the GaN surface by etching away any roughness during growth. This results in films with fewer imperfections and improved crystal quality.
Moreover, hydrogen’s ability to maintain a clean growth environment makes it a preferred choice for many manufacturers. It ensures that the precursor materials reach the substrate efficiently, promoting uniform layer formation. This consistency is crucial for achieving optimal material properties and enhancing device performance.
Nitrogen as a Carrier Gas
Nitrogen, on the other hand, serves as an inert carrier gas in the GaN epitaxy carrier process. It provides a stable environment for the growth process, ensuring that the precursor materials are evenly distributed across the substrate. In organometallic vapor phase epitaxy (OMVPE), nitrogen is commonly used as the carrier gas. It facilitates the incorporation of carbon into the GaN films, which can influence the optical properties of the material.
The use of nitrogen as a carrier gas can lead to variations in growth rate and surface morphology. While it may not enhance the smoothness of the GaN surface as hydrogen does, it offers a stable and controlled growth environment. This stability is essential for producing GaN films with consistent quality and performance.
Mechanisms of Influence by Carrier Gases
Chemical Reactions
Carrier gases play a vital role in the chemical reactions that occur during GaN epitaxial growth. They act as facilitators, ensuring that the necessary chemical processes take place efficiently. For instance, hydrogen, a common carrier gas, serves as a reducing agent. It helps remove unwanted oxygen from the growth environment, which minimizes the formation of defects. This action leads to higher-quality GaN films with improved crystal structures.
In addition to reducing agents, carrier gases can also influence the incorporation of other elements into the GaN films. Nitrogen, for example, can facilitate the incorporation of carbon, which affects the optical properties of the material. By carefully selecting the type and composition of carrier gases, manufacturers can control the chemical reactions that occur during growth. This control allows them to tailor the properties of the GaN films to meet specific application requirements.
Physical Interactions
Beyond chemical reactions, carrier gases also impact the physical interactions during GaN epitaxial growth. These gases help transport precursor materials to the substrate, ensuring even distribution across the surface. This distribution is crucial for achieving uniform layer formation and minimizing surface roughness.
Hydrogen, in particular, enhances the smoothness of the GaN surface by etching away any roughness during growth. This etching process results in films with fewer imperfections and a polished finish. On the other hand, nitrogen provides a stable environment that supports consistent growth rates and surface morphology.
The flow rate and pressure of carrier gases also play a significant role in physical interactions. By adjusting these parameters, manufacturers can influence the growth rate and quality of the GaN films. A higher flow rate may increase the growth rate, while a lower pressure can enhance the crystal quality. Understanding these physical interactions allows manufacturers to optimize the growth process and produce GaN films with superior performance characteristics.
Practical Implications of Carrier Gas Selection
Choosing the right carrier gas in GaN epitaxy isn’t just a technical decision; it has real-world implications that ripple through various industries. The selection process involves weighing factors like cost, availability, and performance. Let’s dive into how these choices impact industrial applications and what the future holds for carrier gas selection.
Industrial Applications
In the world of semiconductor manufacturing, the choice of carrier gas can make or break the efficiency of production processes. Industries rely on gases like hydrogen and nitrogen to ensure high-quality GaN films. Hydrogen, for instance, is favored for its ability to produce smoother surfaces and reduce defects. This quality makes it a go-to option for manufacturers aiming for top-notch electronic components.
Nitrogen, on the other hand, offers a stable environment for growth, which is crucial for maintaining consistent quality across large-scale productions. Its cost-effectiveness compared to other gases like helium makes it an attractive choice for industries looking to optimize their budgets without compromising on quality.
The implications extend beyond just cost and quality. The choice of carrier gas also affects the environmental footprint of the manufacturing process. Hydrogen, being a clean gas, aligns with the growing demand for sustainable practices in industrial applications. As industries continue to innovate, the role of carrier gases in shaping efficient and eco-friendly production methods becomes increasingly significant.
Future Trends in Carrier Gas Selection
Looking ahead, the landscape of carrier gas selection is poised for exciting changes. As technology advances, the demand for more efficient and cost-effective solutions grows. One trend gaining traction is the shift towards hydrogen as a primary carrier gas. With helium prices skyrocketing and its availability dwindling, industries are exploring hydrogen as a viable alternative. Hydrogen generators offer a reliable and safer option, reducing dependency on high-pressure gas cylinders.
Moreover, the push for sustainability is driving research into new carrier gases that minimize environmental impact. Innovations in gas chromatography highlight the potential for gases like nitrogen to replace traditional options, offering both economic and ecological benefits.
Industries are also focusing on optimizing the flow rates and compositions of carrier gases to enhance the growth characteristics of GaN films. This optimization not only improves material quality but also boosts the overall efficiency of production processes.
The choice of carrier gas in GaN epitaxy carrier processes plays a pivotal role in determining the quality and efficiency of the resulting films. Each gas offers distinct benefits and challenges, impacting factors like crystal quality and growth rate. For instance, using oxygen can significantly enhance the crystal quality of GaN films. By strategically selecting the appropriate carrier gas, manufacturers can optimize material properties, reduce defects, and improve device performance. This careful selection not only addresses industrial challenges but also paves the way for advancements in semiconductor technology.
FAQ
What are the challenges in generating single crystal nanowires (NWs)?
Creating single crystal NWs involves several hurdles. The choice of substrate plays a crucial role, as does the nature and thickness of the metal catalyst used. Agglomeration and growth temperature also impact the process. Additionally, the V/III ratio, reactor pressure, and carrier gas flow must be carefully controlled to ensure successful growth.
How does the Qromis Substrate Technology (QST) substrate structure benefit epitaxial growth?
The QST substrate structure is specifically designed for epitaxial growth. It features a coefficient of thermal expansion (CTE) that closely matches the epitaxial layers grown on it. This alignment minimizes stress and defects, leading to higher quality films.
What advantages does hydride vapor phase epitaxy (HVPE) offer for growing GaN bulk crystals?
HVPE stands out due to its relatively simple equipment and process. It allows for the production of large-sized crystals at a high growth rate while maintaining low impurity levels. These attributes make HVPE a promising method for producing GaN substrates.
How do different carrier gases influence the growth of gallium oxide (Ga2O3) thin films?
Carrier gases significantly affect the crystal quality of epitaxial layers. For instance, using O2 as a carrier gas results in the highest quality epitaxial film for Ga2O3. This highlights the importance of selecting the appropriate gas to achieve desired material properties.
What were the growth conditions and results for Si-doped GaN layers under Condition A?
Under Condition A, Si-doped GaN layers exhibited electron mobilities ranging from 600 to 700 cm²/Vs. The electron densities were between 1 and 2 × 10¹⁷ electrons/cm³. These conditions demonstrate the potential for achieving specific electrical characteristics in GaN films.
Why is hydrogen a preferred carrier gas in GaN epitaxy?
Hydrogen acts as a reducing agent, removing unwanted oxygen from the growth environment. This reduction minimizes defect formation, resulting in higher-quality GaN films. Its ability to maintain a clean growth environment makes it a favored choice among manufacturers.
What role does nitrogen play as a carrier gas in GaN epitaxy?
Nitrogen serves as an inert carrier gas, providing a stable environment for the growth process. It ensures even distribution of precursor materials across the substrate. While it may not enhance surface smoothness like hydrogen, it supports consistent growth rates and quality.
How do carrier gases impact the physical interactions during GaN epitaxial growth?
Carrier gases transport precursor materials to the substrate, ensuring even distribution. This distribution is crucial for uniform layer formation. Hydrogen enhances surface smoothness by etching away roughness, while nitrogen provides stability for consistent growth.
What are the practical implications of choosing the right carrier gas in industrial applications?
Selecting the appropriate carrier gas affects production efficiency and quality. Hydrogen offers smoother surfaces and fewer defects, ideal for high-quality components. Nitrogen provides cost-effectiveness and stability, crucial for large-scale productions. The choice also impacts the environmental footprint of manufacturing processes.
What future trends are emerging in carrier gas selection for GaN epitaxy?
Industries are shifting towards hydrogen due to its reliability and safety. The push for sustainability drives research into new gases that minimize environmental impact. Optimizing flow rates and compositions enhances growth characteristics, improving material quality and production efficiency.