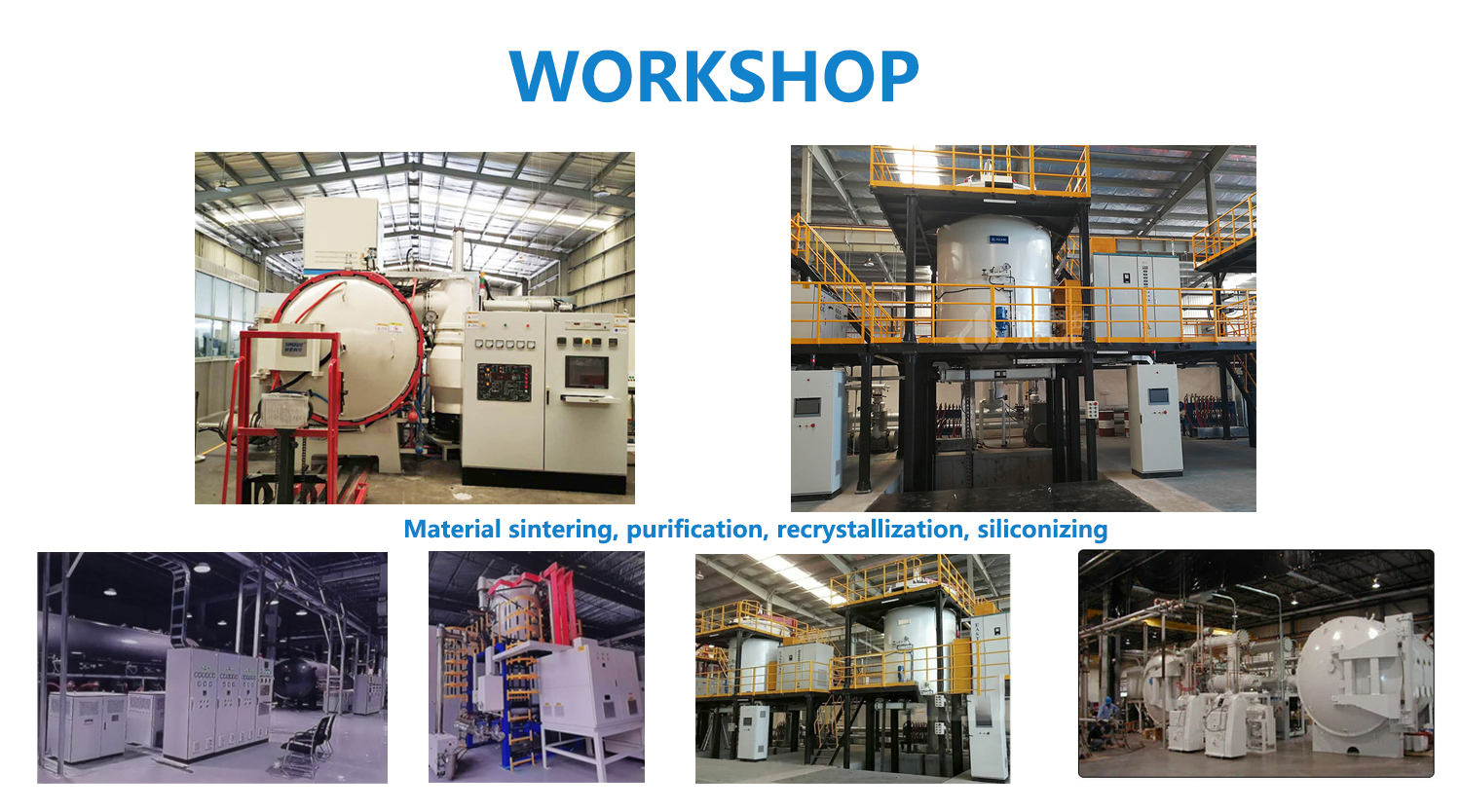
Deep UV-LED technology is advancing significantly with the introduction of the SiC Coated Susceptor for Deep UV-LED. This cutting-edge SiC Coated Susceptor enhances energy efficiency, heat management, and durability, revolutionizing various industries. In healthcare, it plays a vital role in disinfecting surfaces and air, while water treatment benefits from its chemical-free pathogen elimination capabilities. Manufacturing processes such as curing and sterilizing experience improved productivity with this innovation. Featuring advanced CVD SiC coatings, the 1600 C SiC Coated Susceptor is engineered to endure extreme conditions, delivering consistent and reliable performance. Its transformative impact spans multiple sectors, driving progress in essential applications.
Key Takeaways
- SiC coated susceptors help Deep UV-LEDs use less energy by managing heat better.
- They keep heat steady during production, which lowers LED defects.
- These susceptors are strong and can handle high heat and chemicals, lasting longer.
- SiC has high thermal conductivity (300 W/mK), which spreads heat well and stops overheating.
- They improve light brightness and evenness, important for cleaning water and killing germs.
- Picking the right susceptor means checking material, coating thickness, and LED fit.
- SiC coated susceptors cost more at first but save money later with less upkeep and better efficiency.
- The future looks bright for these susceptors, with new tech and more industries using them.
What Are SiC Coated Susceptors?
Definition and Composition
SiC coated susceptors are specialized components used in advanced semiconductor and LED manufacturing. They consist of a graphite base coated with a layer of silicon carbide (SiC). This combination creates a material that excels in both thermal conductivity and chemical resistance. The graphite core provides excellent heat transfer, while the SiC coating protects against chemical reactions and wear during high-temperature processes.
The manufacturing process for these susceptors involves chemical vapor deposition (CVD). This method ensures a high-purity SiC layer, which enhances the susceptor’s performance in extreme environments. The result is a durable and efficient component that meets the rigorous demands of modern semiconductor applications.
Role in Semiconductor Manufacturing
In semiconductor manufacturing, SiC coated susceptors play a critical role in processes like epitaxial growth and crystal formation. They are commonly used in metal-organic chemical vapor deposition (MOCVD) equipment, where they support and heat single-crystal substrates. Their thermal stability ensures uniform heating, which is essential for producing high-quality materials.
Compared to traditional materials like quartz or uncoated graphite, SiC coated susceptors offer superior durability. They maintain their structural integrity at high temperatures and resist damage from reactive gases. This reliability leads to consistent performance throughout the production cycle, reducing downtime and improving overall efficiency.
- Key advantages of SiC coated susceptors in semiconductor manufacturing include:
- Exceptional thermal stability for precise temperature control.
- Uniform heat distribution for better material quality.
- Resistance to chemical erosion, ensuring a longer lifespan.
Importance for Deep UV-LED Applications
Deep UV-LED technology relies on precision and efficiency, making SiC coated susceptors an essential component. These susceptors enhance energy efficiency by optimizing heat management during LED production. Their ability to withstand extreme temperatures ensures consistent performance, even in demanding conditions.
The SiC coating also improves light output and uniformity in Deep UV-LEDs. By providing a stable and chemically resistant surface, the susceptor minimizes defects during manufacturing. This results in LEDs with better performance and longer lifespans, which are crucial for applications like sterilization and water purification.
In 2025, industries continue to demand more efficient and durable solutions. SiC coated susceptors meet these needs, driving advancements in Deep UV-LED technology and enabling breakthroughs in healthcare, environmental protection, and electronics.
The Science Behind SiC Coating and Deep UV-LEDs
Chemical Vapor Deposition (CVD) Process
The Chemical Vapor Deposition (CVD) process is the backbone of creating high-quality SiC coatings. This method ensures that the SiC Coated Susceptor achieves its exceptional performance. The process involves two key steps:
- A gaseous compound undergoes a decomposition reaction.
- The elemental parts from this reaction combine on the surface of a substrate material.
This precise technique forms a uniform and high-purity SiC layer. The result is a coating that can handle extreme conditions while maintaining its integrity. Manufacturers rely on CVD because it produces a durable and efficient susceptor, perfect for demanding applications like Deep UV-LED production.
Thermal Conductivity and Heat Dissipation
SiC coatings excel in thermal conductivity, making them ideal for Deep UV-LED systems. Their ability to manage heat efficiently ensures that LEDs perform consistently, even in high-temperature environments. Compared to other materials, SiC stands out with a thermal conductivity of 300 W/mK. Here’s how it compares:
Material | Thermal Conductivity (W/mK) |
---|---|
SiC | 300 |
This high thermal conductivity allows SiC Coated Susceptors to dissipate heat effectively. They prevent overheating, which is crucial for maintaining the longevity and performance of Deep UV-LEDs. By optimizing heat management, these susceptors contribute to better energy efficiency and reliability in LED systems.
High-Temperature Oxidation Resistance
One of the standout features of SiC coatings is their resistance to oxidation at high temperatures. Studies have shown that SiC materials maintain their structure even when exposed to extreme heat. For instance:
- At temperatures exceeding 1000°C, SiC coatings demonstrate significant oxidation resistance.
- Experiments at 1200°C revealed only a minimal mass increase of 0.4 mg/m² due to oxidation.
- Research highlights that SiC materials outperform standard options in resisting oxidation.
This resistance ensures that the SiC Coated Susceptor remains reliable in harsh environments. Whether it’s in semiconductor manufacturing or Deep UV-LED production, this durability is a game-changer. It reduces wear and tear, extending the lifespan of the susceptor and improving overall efficiency.
Key Benefits of SiC Coated Susceptors for Deep UV-LEDs
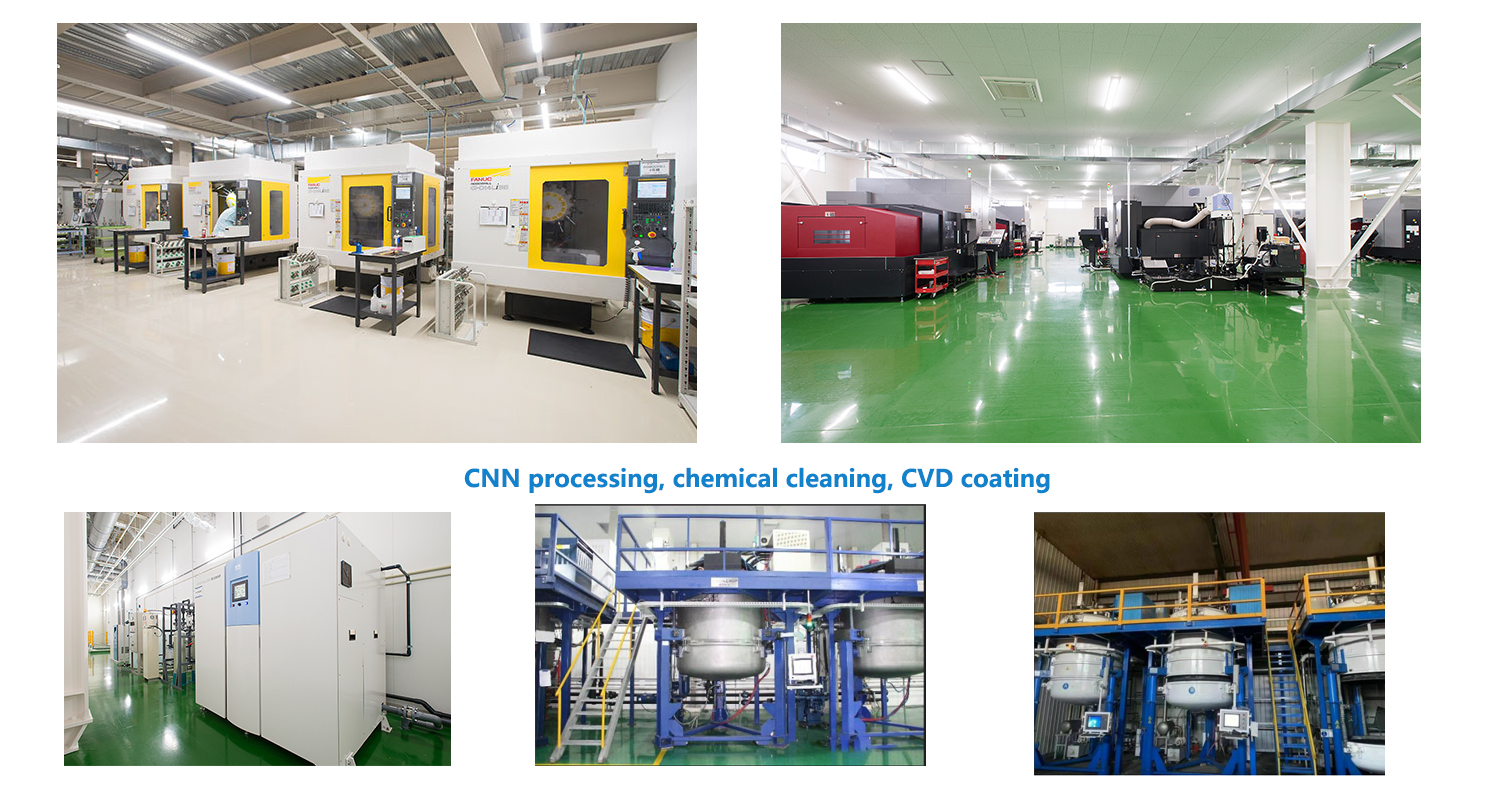
Enhanced Energy Efficiency
Energy efficiency is a top priority in Deep UV-LED technology, and SiC coated susceptors deliver on this front. Their high thermal conductivity ensures that heat is distributed evenly across the substrate. This prevents energy loss caused by overheating or uneven temperature zones. As a result, the LEDs operate at optimal efficiency, consuming less power while maintaining high performance.
The uniform heat distribution also improves the quality of the epitaxial layers during manufacturing. This leads to fewer defects and higher yields, which translates to reduced energy waste. By optimizing the production process and the performance of the LEDs, SiC coated susceptors help manufacturers achieve significant energy savings. This makes them an eco-friendly choice for industries aiming to reduce their carbon footprint.
Superior Thermal Management
Thermal management is critical for the reliability and longevity of Deep UV-LEDs. SiC coated susceptors excel in this area due to their exceptional thermal conductivity of 300 W/mK. This property allows them to dissipate heat efficiently, preventing hotspots that could damage the LEDs or compromise their performance.
The high thermal stability of SiC coatings ensures consistent temperature maintenance during the manufacturing process. This stability minimizes temperature fluctuations, which are a common cause of defects in semiconductor fabrication. By maintaining a uniform temperature, SiC coated susceptors enhance the quality of the substrates and improve light output and uniformity in the final LEDs. This makes them indispensable for applications requiring precision and reliability.
Increased Durability and Lifespan
Durability is another standout feature of SiC coated susceptors. They are designed to withstand extreme conditions, including high temperatures and chemically reactive environments. This makes them ideal for the demanding processes involved in Deep UV-LED production.
Several factors contribute to their impressive lifespan:
- They resist high temperatures and chemical environments, ensuring long-term reliability.
- Their optimized thermal management prevents temperature gradients that could harm the epitaxial layers.
- Their thermal expansion compatibility with AlN/GaN epitaxial wafers reduces the risk of wafer warping or cracking during the MOCVD process.
These features not only extend the lifespan of the susceptors but also improve the durability of the LEDs they help produce. This reliability reduces maintenance costs and downtime, offering long-term value to manufacturers.
Improved Light Output and Uniformity
Light output and uniformity are critical factors in Deep UV-LED performance. SiC coated susceptors play a pivotal role in enhancing these aspects, ensuring LEDs deliver consistent and high-quality illumination. By providing a stable and thermally efficient surface, these susceptors help manufacturers achieve better results during the production process.
One of the key ways SiC coated susceptors improve light output is by minimizing defects in the epitaxial layers. During the manufacturing process, even small temperature fluctuations can lead to imperfections in the crystal structure. These defects reduce the efficiency of the LEDs and can cause uneven light distribution. The superior thermal stability of SiC coated susceptors ensures a uniform temperature across the substrate, reducing the likelihood of such issues. This results in LEDs with higher brightness and better overall performance.
Uniformity in light output is equally important, especially for applications like sterilization and water purification. In these scenarios, uneven light can lead to inconsistent results, which may compromise the effectiveness of the process. SiC coated susceptors address this challenge by maintaining precise control over the heating process. Their high thermal conductivity ensures that every part of the substrate receives the same amount of heat, leading to uniform epitaxial growth. This translates to LEDs that emit light evenly across their surface, making them more reliable for critical applications.
Another advantage of using SiC coated susceptors is their ability to enhance the optical properties of Deep UV-LEDs. The smooth and chemically resistant surface of the susceptor reduces contamination during production. This helps maintain the purity of the materials used, which is essential for achieving optimal light output. Additionally, the durability of the SiC coating ensures that the susceptor remains effective over multiple production cycles, providing consistent results every time.
In 2025, industries continue to demand LEDs with better light output and uniformity. SiC coated susceptors meet these needs by offering a combination of thermal efficiency, durability, and precision. Their role in improving LED performance makes them an indispensable tool for manufacturers aiming to stay ahead in a competitive market.
Applications and Industry Trends in 2025
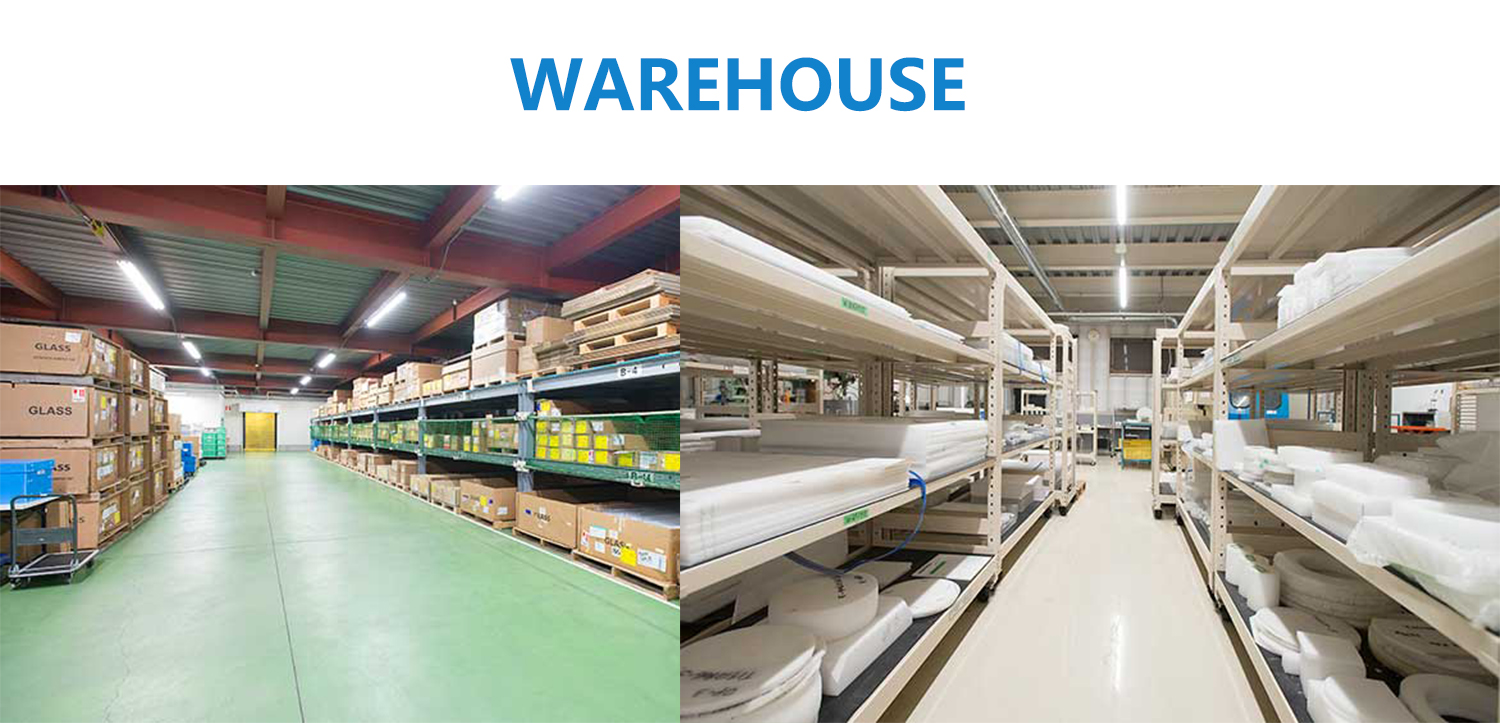
Healthcare and Sterilization
Deep UV-LEDs are transforming healthcare by offering effective sterilization solutions. Hospitals, clinics, and laboratories use these LEDs to disinfect surfaces and air. They help combat bacteria, viruses, and other harmful microorganisms. Continuous exposure to deep UV light inactivates pathogens, stopping them from spreading or replicating. This makes them a powerful tool in preventing infections.
Healthcare-associated infections (HAIs) remain a significant concern for patients and medical staff. To address this, facilities rely on UVC light for decontamination. It disinfects frequently touched surfaces and medical equipment that cannot be immersed in liquids. This ensures a safer environment for everyone involved.
The role of SiC Coated Susceptors in this process is crucial. They enhance the performance of Deep UV-LEDs by improving light output and uniformity. This ensures consistent sterilization, which is vital for healthcare applications.
Water and Air Purification
Clean water and air are essential for healthy living. Deep UV-LEDs play a key role in achieving this by providing chemical-free purification methods. In water treatment, these LEDs eliminate pathogens like bacteria and viruses without using harmful chemicals. This makes them an eco-friendly choice for both residential and industrial applications.
Air purification systems also benefit from Deep UV-LED technology. These systems use UV light to neutralize airborne contaminants, including allergens and microorganisms. This improves indoor air quality, making spaces safer and more comfortable.
SiC Coated Susceptors contribute to these advancements by ensuring the LEDs operate efficiently. Their ability to manage heat and maintain durability allows purification systems to run reliably over time. This makes them a valuable component in environmental protection efforts.
Semiconductor and Electronics Manufacturing
The semiconductor industry continues to adopt SiC Coated Susceptors for their superior thermal performance. Their high thermal conductivity ensures precise temperature control, which is essential for processes like epitaxial growth. Manufacturers use them in CVD and PECVD applications due to their thermal stability and durability.
As electronics become smaller, advanced packaging solutions are in high demand. SiC Coated Susceptors meet these needs by supporting miniaturization efforts. They also contribute to sustainability by offering longer lifespans and reducing waste.
Recent innovations in Deep UV-LED technology highlight the importance of these susceptors. They optimize epitaxial growth for LEDs in the <260nm wavelength range. Their thermal expansion compatibility with AlN/GaN wafers prevents warping or cracking, ensuring high-quality production. These features make them indispensable in modern semiconductor manufacturing.
Innovations in Deep UV-LED Technology
Deep UV-LED technology has come a long way in recent years. In 2025, it’s clear that innovation is driving this field forward. Engineers and researchers are constantly finding ways to make these LEDs more efficient, durable, and versatile. Let’s explore some of the most exciting advancements shaping the future of Deep UV-LEDs.
1. Breakthroughs in Wavelength Precision
Deep UV-LEDs now achieve wavelengths below 260nm with remarkable accuracy. This precision is essential for applications like sterilization and water purification. Manufacturers use advanced materials, such as aluminum nitride (AlN) and gallium nitride (GaN), to fine-tune the wavelength. SiC coated susceptors play a key role here. Their thermal expansion compatibility with AlN/GaN wafers ensures that the crystal structure remains intact during production. This leads to LEDs with consistent and reliable performance.
Tip: Wavelength precision is critical for industries that rely on targeted UV light, such as healthcare and environmental protection.
2. Enhanced Power Output
Modern Deep UV-LEDs deliver higher power output than ever before. This improvement allows them to cover larger areas or treat higher volumes of water and air. SiC coated susceptors contribute by optimizing heat management during the manufacturing process. Their high thermal conductivity ensures that the LEDs can handle increased power without overheating. This makes them ideal for demanding applications.
3. Miniaturization of LED Components
Smaller, more compact Deep UV-LEDs are becoming the norm. These miniaturized LEDs are perfect for portable devices, such as handheld sterilizers and compact air purifiers. SiC coated susceptors support this trend by enabling precise temperature control during production. This precision allows manufacturers to create smaller LEDs without compromising quality or performance.
4. Improved Durability and Lifespan
Durability is a top priority for Deep UV-LEDs, especially in industrial settings. Recent innovations focus on making these LEDs last longer, even in harsh environments. SiC coated susceptors enhance durability by resisting high temperatures and chemical reactions. This ensures that the LEDs remain functional over extended periods, reducing maintenance costs and downtime.
5. Integration with Smart Technologies
Smart technology is making its way into Deep UV-LED systems. IoT-enabled devices now monitor and control UV-LED performance in real time. These systems adjust power levels, track usage, and provide maintenance alerts. SiC coated susceptors ensure that the LEDs in these smart systems operate efficiently and reliably, even under varying conditions.
Note: The combination of smart technology and durable components like SiC coated susceptors is paving the way for more efficient and user-friendly UV-LED solutions.
In 2025, these innovations are transforming how industries use Deep UV-LEDs. From healthcare to electronics, the possibilities are endless. SiC coated susceptors remain at the heart of these advancements, enabling breakthroughs that push the boundaries of what’s possible.
How to Choose the Right SiC Coated Susceptor
Evaluating Material Quality and Coating Thickness
Choosing the right SiC coated susceptor starts with understanding its material quality. High-quality materials ensure better performance and longer lifespans, especially in demanding applications like Deep UV-LED production. But what exactly should you look for?
Here are some key factors to consider:
- Thermal conductivity: A susceptor with excellent heat transfer capabilities ensures efficient thermal management.
- Chemical stability: Resistance to chemical reactions is crucial for maintaining performance in harsh environments.
- Durability: A robust susceptor can withstand repeated use without degrading.
- Customization options: Tailored solutions can meet specific manufacturing needs.
Additionally, advanced SiC coated susceptors offer:
- Enhanced corrosion resistance for longer operational life.
- Superior thermal shock resistance to handle rapid temperature changes.
- Thermal expansion coefficients similar to graphite, reducing the risk of cracking.
Coating thickness also plays a vital role. A uniform and optimized SiC layer ensures consistent performance. Thicker coatings may provide better protection, but they can also increase costs. Manufacturers should strike a balance based on their specific requirements.
Compatibility with Deep UV-LED Systems
Not all susceptors are created equal, and compatibility with your Deep UV-LED system is non-negotiable. The susceptor must align with the thermal and mechanical properties of the materials used in your process. For example, SiC coated susceptors are ideal for AlN/GaN epitaxial wafers due to their matching thermal expansion coefficients. This compatibility minimizes the risk of wafer warping or cracking during high-temperature operations.
Another consideration is the operating temperature range. SiC coated susceptors can handle temperatures up to 1600°C, making them suitable for extreme conditions. However, ensure that your system can fully utilize this capability.
Lastly, think about the size and shape of the susceptor. Custom designs may be necessary to fit specific equipment or substrates. Working with a supplier that offers tailored solutions can save time and improve production efficiency.
Balancing Cost and Performance
Cost is always a factor, but it shouldn’t come at the expense of performance. SiC coated susceptors may have a higher upfront cost compared to traditional materials like graphite or quartz. However, their long-term benefits often outweigh the initial investment.
Aspect | SiC Coated Susceptors | Traditional Materials (Graphite/Quartz) |
---|---|---|
Durability | Enhanced | Moderate |
Thermal Stability | Superior | Lower |
Chemical Resistance | Excellent | Limited |
Initial Investment | Higher | Lower |
Maintenance Costs | Lower (due to longevity) | Higher (frequent replacements) |
Overall Cost Efficiency | Higher long-term savings | Lower long-term savings |
SiC coated susceptors excel in durability, thermal stability, and chemical resistance. These qualities reduce maintenance costs and downtime, making them a cost-effective choice over time. For manufacturers aiming to improve efficiency and reduce waste, the higher initial investment pays off in the long run.
When selecting a susceptor, weigh your budget against your operational needs. A well-chosen SiC coated susceptor can enhance productivity, reduce energy consumption, and deliver consistent results, making it a smart investment for any Deep UV-LED application.
Future Outlook for SiC Coated Susceptors in Deep UV-LEDs
Advancements in SiC Coating Technology
The future of SiC coating technology looks incredibly promising. Researchers are exploring new methods to make these coatings even better. Plasma-enhanced chemical vapor deposition (PECVD) is one area gaining attention. This technique improves the uniformity and adhesion of SiC coatings, making them more durable. High-density plasma CVD is another exciting development. It minimizes defects in the coating, resulting in higher-quality surfaces that enhance the performance of semiconductor devices.
Innovations in materials and manufacturing processes are also on the horizon. Engineers are experimenting with novel materials to optimize coating performance. These advancements could lead to SiC coatings that are more efficient and reliable than ever before. As these technologies evolve, they will open up new possibilities for SiC Coated Susceptors in Deep UV-LED applications.
Broader Industry Adoption
The adoption of SiC Coated Susceptors is expected to grow across multiple industries. Several factors are driving this trend. First, the demand for wide-bandgap semiconductors like SiC and GaN is rising. These materials are essential for high-performance electronics, and SiC Coated Susceptors play a key role in their production. Second, the global push for energy-efficient technologies is encouraging industries to adopt solutions that reduce energy consumption.
Emerging applications are also fueling this growth. Electric vehicles and renewable energy systems require advanced semiconductor devices, which SiC Coated Susceptors help manufacture. Supportive government policies and incentives are further accelerating this shift. As industries continue to prioritize sustainability and innovation, the use of SiC Coated Susceptors will only expand.
Challenges and Opportunities in 2025 and Beyond
While the future looks bright, challenges remain. The high cost of SiC Coated Susceptors can be a barrier for some manufacturers. However, the long-term benefits, such as durability and efficiency, often outweigh the initial investment. Opportunities for growth are abundant. The expanding market for SiC-based power devices presents a significant opportunity. These devices are in high demand for applications ranging from electric vehicles to industrial equipment.
Collaborations and partnerships could also drive innovation. By working together, companies can develop new technologies and reach broader markets. Diversifying the industries that use SiC Coated Susceptors is another way to unlock potential. From healthcare to aerospace, the possibilities are endless. Process optimization in MOCVD systems will further enhance product quality, attracting more customers seeking high-performance solutions.
The road ahead is filled with both challenges and opportunities. With continued innovation and strategic efforts, SiC Coated Susceptors are poised to play a pivotal role in shaping the future of Deep UV-LED technology.
SiC coated susceptors are reshaping the future of Deep UV-LED technology. Their precision thermal management, chemical resistance, and compatibility with advanced materials like AlN/GaN wafers make them indispensable for high-performance epitaxial growth. Industries increasingly rely on these susceptors to meet the rising demand for energy-efficient and durable solutions.
Continued innovation in SiC coating technology will address future challenges, such as the growing need for high-performance semiconductors in electric vehicles and renewable energy systems. By enhancing efficiency and sustainability, SiC coated susceptors will remain at the forefront of semiconductor advancements, driving progress across global industries.
Note: As industries evolve, adopting cutting-edge solutions like the SiC Coated Susceptor ensures they stay competitive and environmentally conscious.
FAQ
What is a SiC coated susceptor?
A SiC coated susceptor is a graphite-based component coated with silicon carbide. It’s used in semiconductor manufacturing to provide excellent heat transfer, chemical resistance, and durability. This makes it ideal for high-temperature processes like Deep UV-LED production.
Why is SiC coating important for Deep UV-LEDs?
SiC coating ensures superior thermal conductivity and chemical resistance. It helps maintain uniform temperatures during LED production, reducing defects and improving light output. This makes Deep UV-LEDs more efficient and reliable for applications like sterilization and water purification.
How does SiC improve energy efficiency in Deep UV-LEDs?
SiC’s high thermal conductivity (300 W/mK) ensures even heat distribution. This prevents energy loss from overheating or uneven temperatures. As a result, Deep UV-LEDs consume less power while maintaining optimal performance, making them energy-efficient.
Can SiC coated susceptors handle extreme temperatures?
Yes! SiC coated susceptors can withstand temperatures up to 1600°C. Their high-temperature oxidation resistance ensures they remain stable and reliable, even in the most demanding environments.
What industries benefit from SiC coated susceptors?
Industries like healthcare, water purification, and semiconductor manufacturing benefit the most. SiC coated susceptors enhance Deep UV-LED performance, making them essential for sterilization, clean water systems, and advanced electronics production.
Are SiC coated susceptors eco-friendly?
Absolutely! By improving energy efficiency and reducing waste during manufacturing, SiC coated susceptors support sustainable practices. They also enable chemical-free solutions like UV sterilization, which is safer for the environment.
How do I choose the right SiC coated susceptor?
Look for high thermal conductivity, chemical resistance, and durability. Ensure compatibility with your Deep UV-LED system and consider coating thickness. Balancing cost and performance is key to finding the best option for your needs.
What makes SiC coated susceptors better than traditional materials?
SiC coated susceptors outperform traditional materials like quartz or uncoated graphite. They offer superior durability, thermal stability, and chemical resistance. These features reduce maintenance costs and improve efficiency, making them a smarter long-term investment.
Tip: Always consult with a trusted supplier to ensure the susceptor meets your specific requirements.