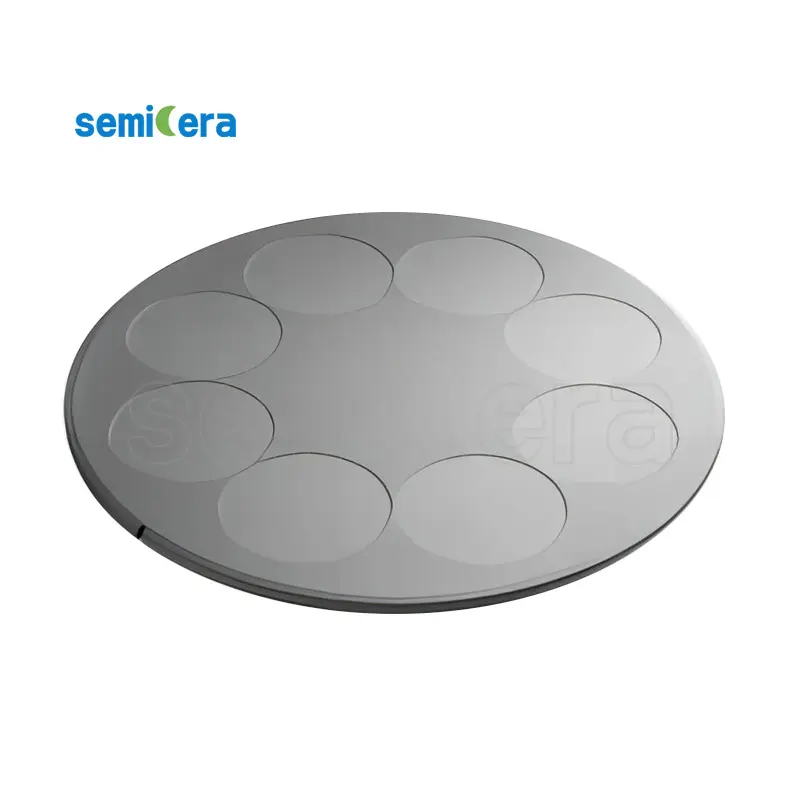
Offshore wind turbines operate in harsh marine environments where corrosion, wear, and extreme weather pose significant challenges. Saltwater exposure accelerates material degradation, while mechanical stress and operational noise create persistent wear issues. Studies have revealed that offshore wind farms can disturb marine life and seabird populations, emphasizing the need for durable solutions. SiC Coatings offer unmatched protection against these challenges. Their application, such as silicon carbide spray coating or silicon carbide ceramic coating, ensures enhanced resistance to wear and corrosion. For components like stainless steel, silicon carbide coating on stainless steel provides long-lasting durability, making it a preferred choice for offshore applications. If you’re looking for sic coatings near me, consider the benefits of SiC Coatings for your projects.
Key Takeaways
- SiC coatings keep wind turbine parts safe from rust, damage, and bad weather, making them last longer.
- These coatings help save money on repairs by making important parts like blades and gearboxes work for more years.
- SiC coatings make turbines work better by cutting down friction, which helps them produce more energy and run smoothly.
- SiC coatings are very strong and handle heat well, so they are perfect for tough ocean conditions and prevent parts from breaking.
- Using SiC coatings is good for the planet because it lowers waste and pollution from wind energy systems.
Challenges in Offshore Wind Turbine Environments
Corrosion from saltwater exposure
Offshore wind turbines constantly face saltwater exposure, which accelerates corrosion. The high salinity in marine environments reacts with metal components, leading to rust and material degradation. Over time, this weakens the structural integrity of critical parts like turbine towers and fasteners. Protective coatings, such as SiC coatings, act as a barrier against these corrosive elements. By preventing direct contact with saltwater, these coatings significantly reduce the risk of corrosion and extend the lifespan of components.
Wear and tear from mechanical stress
Mechanical stress is another major challenge for offshore wind turbines. Rotating blades, gearboxes, and bearings endure continuous wear due to high-speed operations and fluctuating loads. This wear can lead to cracks, erosion, and eventual failure of components. Regular inspections help identify these issues early.
Inspection Method | Purpose | Frequency of Inspections |
---|---|---|
Visual Inspections | Spot surface issues like cracks and erosion using drones or cameras. | At least twice per year, more after weather events |
Non-Destructive Testing (NDT) | Detect subsurface defects without damaging the blade. | As needed, especially after operational anomalies |
Routine Inspections | Thorough examinations of major components for wear and tear. | Two to three times a year, or more frequently |
SiC coatings enhance wear resistance by providing a hard, durable surface that minimizes abrasion and mechanical damage. This reduces the frequency of repairs and ensures smoother operations.
Damage from extreme weather conditions
Extreme weather conditions, such as hurricanes and storms, pose significant risks to offshore wind turbines. High winds and heavy precipitation can strain turbine components and disrupt energy production. Studies have shown that atmospheric stability influences turbine performance. For example:
- Magnusson and Smedman observed larger velocity deficits behind turbines under stable atmospheric conditions.
- Hansen et al. found that increased stability led to greater power losses.
- Pan et al. reported that offshore wind farms reduced heavy precipitation during Hurricane Harvey by inducing horizontal divergence.
SiC coatings provide thermal stability and resistance to high-temperature oxidation, ensuring that turbines can withstand harsh weather without compromising performance. These coatings play a vital role in maintaining the reliability of offshore wind turbines in extreme conditions.
High maintenance demands and costs
Offshore wind turbines require frequent maintenance due to the harsh marine environment. The combination of saltwater exposure, mechanical stress, and extreme weather accelerates wear and tear on critical components. These factors increase the demand for both scheduled and unscheduled maintenance, leading to higher operational costs.
Maintenance activities often involve significant expenses. The analysis of offshore wind turbine maintenance costs highlights several key factors:
- Scheduled maintenance includes routine inspections and part replacements, which require specialized equipment and skilled technicians.
- Unscheduled maintenance, caused by unexpected failures, results in downtime and additional repair costs.
- Outage periods during repairs reduce energy production, impacting overall efficiency and profitability.
Condition monitoring systems (CMS) help manage these costs effectively. These systems detect early signs of component failure, allowing operators to address issues before they escalate. By reducing downtime and optimizing maintenance schedules, CMS minimizes financial losses and improves turbine reliability.
SiC coatings play a crucial role in addressing high maintenance demands. Their exceptional durability reduces the frequency of repairs and replacements. For example, SiC-coated bearings and gearboxes experience less wear, extending their operational lifespan. This lowers the need for unscheduled maintenance and ensures consistent energy output.
By combining advanced coatings with proactive maintenance strategies, offshore wind farms can significantly reduce costs. This approach not only enhances the economic viability of wind energy but also supports the long-term sustainability of renewable energy systems. SiC coatings provide a practical solution for operators seeking to optimize performance while minimizing maintenance demands.
Properties of SiC Coatings
Exceptional hardness and wear resistance
SiC coatings are renowned for their exceptional hardness, which enhances the durability of offshore wind turbine components. With a hardness value of 40 GPa, these coatings outperform many traditional materials. This superior hardness minimizes surface damage caused by mechanical stress and abrasion. For example, experimental results show that adding SiC to aluminum alloys significantly increases tensile strength and reduces wear rates. A study on Al 3103 with SiC revealed that the specific wear rate decreased by 50% when the SiC content reached 10%. This demonstrates how SiC coatings provide robust protection against wear, ensuring longer-lasting performance in demanding environments.
Material Type | Tensile Strength | Hardness | Specific Wear Rate |
---|---|---|---|
Al 3103 with SiC | Superior | Increased with SiC weight | Decreased by 50% up to 10%wt SiC |
Corrosion resistance in marine environments
Marine environments expose wind turbine components to saltwater, which accelerates corrosion. SiC coatings act as a protective barrier, preventing saltwater from reaching the underlying material. This resistance to corrosion ensures that components like turbine blades, fasteners, and gearboxes maintain their structural integrity over time. SiC coatings are also widely used in other industries, such as oil and gas, where they extend equipment life by reducing wear and corrosion. Their application in offshore wind turbines highlights their ability to withstand harsh conditions while reducing maintenance needs.
- Key benefits of SiC coatings in corrosion resistance:
- Prevents rust and material degradation.
- Extends the lifespan of critical components.
- Reduces maintenance frequency and costs.
Thermal stability and high-temperature oxidation resistance
Offshore wind turbines often face extreme temperature fluctuations. SiC coatings provide excellent thermal stability, ensuring reliable performance even under high temperatures. Testing data confirms that SiC coatings remain stable up to 600 °C. Annealing experiments further reveal that coatings with higher silicon concentrations exhibit improved oxidation resistance at 700 °C. Additionally, nanoindentation tests show that the hardness of SiC coatings increases to 40 GPa after annealing at 400 °C. These findings highlight the ability of SiC coatings to maintain their mechanical properties and resist oxidation, even in challenging thermal conditions.
Test Condition | Observations | Implications |
---|---|---|
Annealing at 600 °C | Si–ta-C coatings stable | Indicates thermal stability up to 600 °C |
Annealing at 700 °C | Improved stability with higher Si | Suggests enhanced oxidation resistance |
Hardness after 400 °C | Increased to 40 GPa | Correlates with improved durability |
By combining hardness, corrosion resistance, and thermal stability, SiC coatings provide unmatched protection for offshore wind turbine components. These properties ensure reliable operation, reduced maintenance, and extended service life.
Low friction and high abrasion resistance
SiC coatings offer exceptional low friction and high abrasion resistance, making them ideal for offshore wind turbine components. These properties ensure smoother operations and reduce wear caused by constant mechanical contact.
Low friction minimizes energy loss during turbine operation. When components like bearings and gearboxes experience less friction, they operate more efficiently. This efficiency translates to improved energy output and reduced operational strain. For example, SiC-coated bearings exhibit a significant reduction in friction coefficients compared to uncoated alternatives. This improvement enhances the overall performance of wind turbines.
High abrasion resistance protects components from damage caused by harsh environmental factors. Offshore wind turbines face abrasive forces from airborne particles, salt spray, and mechanical stress. SiC coatings create a durable surface that resists these forces, preventing material degradation. Studies show that SiC-coated surfaces maintain their integrity even after prolonged exposure to abrasive conditions.
Did You Know?
SiC coatings have a friction coefficient as low as 0.1, making them one of the most effective solutions for reducing wear in high-stress environments.
The combination of low friction and high abrasion resistance also reduces maintenance needs. Components coated with SiC require fewer repairs and replacements, lowering operational costs. Operators benefit from extended service intervals and improved reliability.
Property | Benefit | Example Application |
---|---|---|
Low Friction | Reduces energy loss | Bearings and gearboxes |
High Abrasion Resistance | Protects against environmental wear | Turbine blades and fasteners |
SiC coatings provide a practical solution for enhancing the durability and efficiency of offshore wind turbines. Their ability to withstand abrasive forces and reduce friction ensures long-lasting performance in challenging marine environments.
Applications of SiC Coatings in Offshore Wind Turbines
Protecting turbine blades from erosion and weathering
Turbine blades in offshore wind farms endure constant exposure to harsh environmental conditions. Salt spray, airborne particles, and high-speed winds cause erosion and wear over time. These factors reduce the efficiency of the blades and shorten their lifespan. SiC Coatings provide a durable protective layer that shields the blades from these damaging elements. Their exceptional hardness and abrasion resistance prevent surface degradation, ensuring the blades maintain their aerodynamic performance. By reducing erosion, these coatings also minimize the need for frequent repairs, lowering maintenance costs and improving energy output.
Enhancing the durability of bearings and gearboxes
Bearings and gearboxes are critical components in wind turbines. They experience continuous mechanical stress due to high-speed rotations and fluctuating loads. This stress often leads to wear, overheating, and eventual failure. SiC Coatings enhance the durability of these components by reducing friction and providing a hard, wear-resistant surface. The low friction properties of these coatings improve operational efficiency, while their thermal stability ensures reliable performance under varying temperatures. SiC-coated bearings and gearboxes last longer, reducing downtime and maintenance demands. This improvement directly contributes to the overall reliability of offshore wind turbines.
Coating fasteners and connectors to prevent corrosion
Fasteners and connectors play a vital role in maintaining the structural integrity of wind turbines. However, their constant exposure to saltwater makes them highly susceptible to corrosion. SiC Coatings act as a protective barrier, preventing saltwater from reaching the metal surface. They also serve as sacrificial anodes, further enhancing corrosion resistance. This dual mechanism significantly extends the lifespan of fasteners and connectors, reducing the risk of structural failures.
Mechanism/Benefit | Description |
---|---|
Protective Barrier | Coatings serve as a barrier between the metallic surface and the environment, preventing corrosion. |
Sacrificial Anode | Coatings can act as sacrificial anodes, enhancing corrosion resistance. |
Increased Lifespan | Coatings can extend the life of the surface and the equipment by shielding against environmental damage. |
By protecting these essential components, SiC Coatings ensure the long-term stability and safety of offshore wind turbines.
Real-world examples of SiC-coated components
SiC coatings have demonstrated their effectiveness in real-world applications, particularly in offshore wind turbines. These coatings have been applied to various critical components, showcasing their ability to enhance durability and performance.
- Turbine Blades:
Offshore wind farms in Europe have adopted SiC coatings to protect turbine blades from erosion caused by high-speed winds and salt spray. For example, a wind farm in the North Sea reported a significant reduction in blade surface wear after applying SiC coatings. The blades maintained their aerodynamic efficiency, resulting in improved energy output over time. - Bearings and Gearboxes:
SiC-coated bearings and gearboxes have been used in offshore turbines to address wear and friction issues. A case study from a wind farm off the coast of Denmark highlighted the benefits of these coatings. The coated components experienced less mechanical stress, reducing the frequency of maintenance and extending their operational lifespan. - Fasteners and Connectors:
In Japan, SiC coatings have been applied to fasteners and connectors in offshore turbines to combat corrosion from saltwater exposure. Operators observed that the coated fasteners retained their structural integrity even after years of operation in harsh marine conditions. This application minimized the risk of structural failures and reduced maintenance costs.
Note: These examples underline the versatility of SiC coatings in addressing the unique challenges of offshore wind turbines. By protecting critical components, these coatings ensure reliable performance and long-term cost savings.
SiC coatings continue to gain recognition as a reliable solution for enhancing the durability of offshore wind turbine components. Their real-world success demonstrates their potential for wider adoption in renewable energy systems.
Benefits of SiC Coatings for Offshore Wind Turbines
Reduced maintenance and repair costs
SiC coatings significantly reduce the maintenance and repair costs of offshore wind turbines. These coatings create a durable barrier that protects components from corrosion, wear, and environmental damage. Operators spend less on frequent repairs and replacements, as SiC-coated parts last longer than uncoated ones. For example, fasteners and connectors coated with SiC resist saltwater corrosion, reducing the need for unscheduled maintenance. By lowering repair demands, these coatings help operators allocate resources more efficiently, improving the economic viability of wind farms.
Improved operational efficiency and energy output
SiC coatings enhance the operational efficiency of wind turbines by reducing friction and wear on critical components. Bearings and gearboxes coated with SiC operate more smoothly, minimizing energy loss during turbine rotation. This improvement translates to higher energy output and better performance. The following table highlights key metrics that demonstrate the impact of SiC coatings on turbine efficiency:
Metric Description | Improvement Percentage | Notes |
---|---|---|
Lifespan extension of SiC-coated turbine blades | 15-20% | Compared to uncoated parts, reducing maintenance costs. |
Heat transfer efficiency in coal-fired plants | Up to 15% | Results in reduced fuel consumption and emissions. |
Net efficiency in thermal power stations | 3-5% | Achieved savings of approximately 50,000 tons of coal annually per 1GW capacity. |
Although the table includes data from other industries, it underscores the potential of SiC coatings to improve energy efficiency across various applications. In offshore wind turbines, these coatings ensure consistent energy production, even under harsh conditions.
Extended lifespan of critical components
SiC coatings extend the lifespan of critical turbine components by protecting them from environmental and mechanical stress. Turbine blades, bearings, and fasteners coated with SiC resist erosion, corrosion, and abrasion. This durability ensures that components remain functional for longer periods, reducing the frequency of replacements. For instance, SiC-coated turbine blades maintain their structural integrity despite constant exposure to salt spray and high-speed winds. By prolonging the life of these components, SiC coatings contribute to the long-term reliability and sustainability of offshore wind energy systems.
Contribution to sustainability and reduced environmental impact
SiC coatings play a vital role in promoting sustainability and reducing the environmental impact of offshore wind turbines. These coatings enhance the efficiency and durability of turbine components, which directly supports the goals of renewable energy systems.
One of the key contributions of SiC coatings is their ability to extend the lifespan of turbine components. By protecting parts like blades, bearings, and fasteners from corrosion and wear, these coatings reduce the need for frequent replacements. This minimizes the consumption of raw materials and energy required for manufacturing new components. As a result, the overall carbon footprint of wind turbine operations decreases.
Fact: Studies show that extending the lifespan of turbine components by just 10% can significantly reduce the environmental impact of wind farms over their operational lifetime.
SiC coatings also improve the energy efficiency of wind turbines. Their low friction properties reduce energy losses during operation, allowing turbines to generate more electricity with the same input. This increased efficiency means that fewer turbines are needed to produce the same amount of energy, which helps conserve natural resources and reduces the environmental footprint of wind farm installations.
Additionally, the durability of SiC coatings lowers maintenance demands. Offshore wind turbines often require specialized vessels and equipment for repairs, which consume fuel and emit greenhouse gases. By reducing the frequency of maintenance, SiC coatings help cut down on these emissions, contributing to cleaner and more sustainable energy production.
The Future of SiC Coatings in Offshore Wind Energy
Innovations in SiC coating technology
Recent advancements in SiC coating technology are transforming the renewable energy sector. Chemical vapor deposition (CVD) techniques now produce high-quality SiC films with minimal defects, ensuring superior performance. Researchers have also integrated materials like graphene into SiC coatings, reducing thermal resistance by up to 30%. This innovation enhances the ability of components to withstand extreme conditions.
Automated systems, such as laser-assisted chemical vapor deposition (LACVD), are streamlining production processes. These systems improve precision, reduce costs, and increase scalability, making SiC coatings more accessible for large-scale applications. Additionally, environmentally friendly methods, including water-based and solvent-free processes, align with global sustainability goals. These developments highlight the potential of SiC coatings to meet the growing demands of offshore wind energy systems.
Potential for wider adoption in renewable energy systems
The renewable energy sector is rapidly expanding, driven by the need to reduce carbon emissions and modernize power grids. SiC coatings play a crucial role in this transition. Their high efficiency, thermal conductivity, and ability to handle high voltages make them ideal for power electronics in wind, solar, and energy storage systems.
Market projections indicate significant growth for SiC applications. By 2029, the silicon carbide market is expected to reach $3.99 billion, with a compound annual growth rate (CAGR) of 26.2%. This growth reflects the increasing adoption of SiC in energy-efficient solutions, including electric vehicles and renewable energy systems. As production techniques improve, costs will decrease, further encouraging the use of SiC coatings across various industries.
Advancing offshore wind turbine reliability and performance
SiC coatings enhance the reliability and performance of offshore wind turbines by addressing critical challenges. Their exceptional durability protects components from corrosion, wear, and extreme weather. This protection reduces maintenance demands and ensures consistent energy production.
SiC also improves the efficiency of power converters and inverters, which are essential for energy storage systems. Faster switching speeds and reduced energy losses make SiC a preferred material for companies focused on clean energy solutions. These advantages position SiC coatings as a key technology for advancing the reliability and sustainability of offshore wind energy.
SiC Coatings provide a reliable solution to the challenges faced by offshore wind turbines. These coatings protect components from corrosion, wear, and extreme weather, ensuring long-term durability. By reducing maintenance needs, they lower operational costs and improve energy efficiency. Their ability to extend the lifespan of critical parts makes them essential for sustainable wind energy systems. Adopting this technology supports the cost-effectiveness and reliability of offshore wind farms, paving the way for a cleaner energy future.
FAQ
What makes SiC coatings suitable for offshore wind turbines?
SiC coatings excel in harsh marine environments due to their exceptional hardness, corrosion resistance, and thermal stability. These properties protect turbine components from saltwater, mechanical stress, and extreme weather, ensuring long-term durability and reduced maintenance needs.
How do SiC coatings improve energy efficiency?
SiC coatings reduce friction on critical components like bearings and gearboxes. This minimizes energy loss during turbine operation, leading to smoother performance and higher energy output. Their low friction properties make them ideal for improving operational efficiency in offshore wind turbines.
Can SiC coatings withstand extreme weather conditions?
Yes, SiC coatings offer excellent thermal stability and high-temperature oxidation resistance. These features enable turbine components to endure extreme weather, including high winds and heavy precipitation, without compromising performance or reliability.
Are SiC coatings environmentally friendly?
SiC coatings contribute to sustainability by extending the lifespan of turbine components and reducing maintenance demands. This minimizes the need for replacements, conserving raw materials and energy. Additionally, their efficiency-enhancing properties lower the environmental footprint of wind farm operations.
Where can SiC coatings be applied on wind turbines?
SiC coatings can protect turbine blades, bearings, gearboxes, fasteners, and connectors. These applications shield components from corrosion, wear, and abrasion, ensuring reliable performance and longer service life in offshore environments.