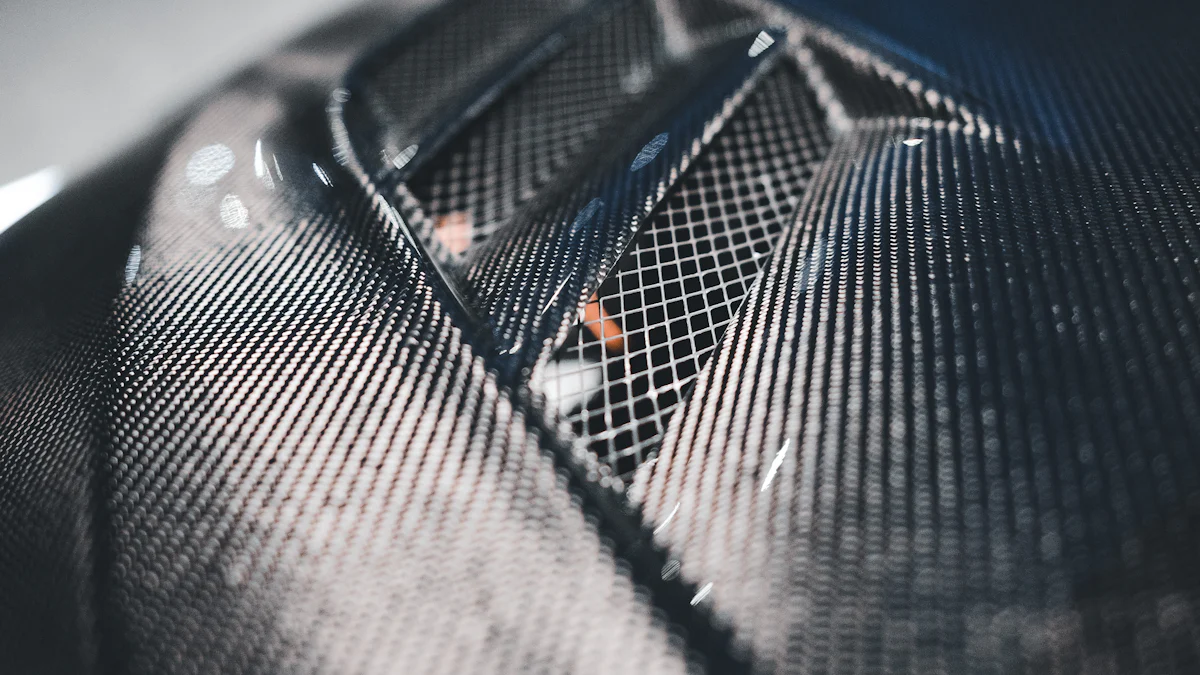
Choosing the right carbon fiber roll can make or break a project. It ensures the final product performs well and lasts longer. Every project has unique needs, so understanding the material’s properties is crucial. For instance, a 4×8 carbon fiber sheet might suit large-scale applications, while a 1/8 carbon fiber sheet works better for smaller, detailed designs. Knowing the differences between a carbon fiber carbon plate and other options helps in making informed decisions. The right choice guarantees durability and optimal performance, saving time and resources in the long run.
Key Takeaways
- Define your project’s purpose clearly to select the right carbon fiber roll that meets specific needs, whether for strength, flexibility, or aesthetics.
- Evaluate environmental conditions, such as temperature and humidity, to ensure the chosen carbon fiber roll performs reliably in its intended setting.
- Consider your budget carefully; investing in high-quality carbon fiber rolls can save money in the long run by reducing maintenance and replacement costs.
- Understand the differences between unidirectional and bidirectional carbon fiber rolls to choose the right type based on the required strength and application.
- Explore specialized carbon fiber roll variants like pre-preg, woven, and hybrid options to find the best fit for your project’s unique requirements.
- Consult with experts or manufacturers for tailored advice and insights, helping you avoid costly mistakes and ensuring project success.
- Test samples of carbon fiber rolls before making a full purchase to confirm their suitability for your specific application and performance needs.
- Verify the reputation of manufacturers to ensure you receive high-quality materials that meet industry standards and project demands.
Understanding Project Requirements
Defining the Purpose of Your Project
Every project starts with a clear purpose. Knowing what the carbon fiber component will do is the first step in choosing the right material. Will it provide structural support, or does it need to be lightweight and flexible? For example:
- If the project requires stiffness, a carbon fiber roll with high tensile strength is ideal.
- If flexibility is more important, a roll designed for pliability works better.
Think about the role the material will play. A racing car part needs strength and lightness, while a decorative piece might prioritize appearance. Matching the material to the project’s purpose ensures success.
Evaluating Environmental Conditions
Environmental factors can greatly affect how a carbon fiber roll performs. Temperature, humidity, and exposure to elements like UV light all play a role. Research shows that temperature changes can alter the mechanical properties of carbon fiber composites. For instance, medium temperatures often enhance impact strength, but extreme heat might reduce rigidity.
Consider where the final product will be used. Will it face high heat, like in an engine bay? Or will it be exposed to moisture, such as in marine environments? Choosing a roll that withstands these conditions ensures durability and reliability.
Budget Considerations
Budget is always a key factor in any project. Carbon fiber rolls come in a range of prices, depending on their type and quality. Pre-preg rolls, for example, are more expensive due to their advanced manufacturing process. On the other hand, unidirectional rolls might be more affordable for simpler applications.
It’s important to balance cost with performance. Spending more upfront on a high-quality roll can save money in the long run by reducing maintenance or replacement costs. However, for smaller or less demanding projects, a budget-friendly option might be the smarter choice.
Tip: Always compare prices from different suppliers and consider the total cost, including shipping and handling.
Types of Carbon Fiber Rolls
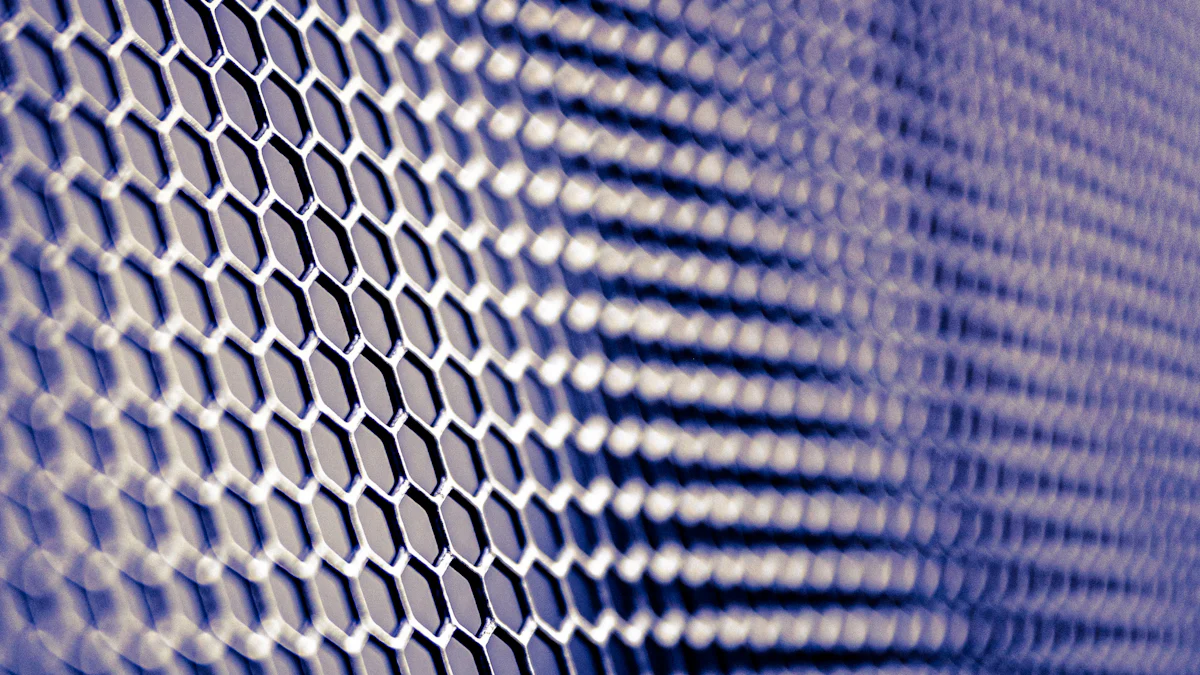
Unidirectional Carbon Fiber Rolls
Unidirectional carbon fiber rolls are designed with fibers running in a single direction. This unique alignment gives them exceptional tensile strength, making them ideal for projects requiring reinforcement along a specific axis. For example, they are often used to strengthen concrete or masonry structures by following the layout of existing rebar. Their ability to add tensile strength—1.5 times greater than #6 rebar—makes them a popular choice for structural applications.
Here’s a quick comparison to help understand their strength and applications better:
Type | Strength Characteristics | Applications |
---|---|---|
Unidirectional (UNI) | Fibers run in the same direction; tensile strength added is 1.5x greater than #6 rebar. | Best for strengthening concrete and masonry components, following the layout of existing rebar. |
These rolls are perfect for projects where strength in one direction is critical. However, they may not be the best choice for applications requiring multi-directional reinforcement.
Bidirectional Carbon Fiber Rolls
Bidirectional carbon fiber rolls, on the other hand, have fibers running in two directions—typically at 90-degree angles. This design provides balanced strength across both axes, making them versatile for a wide range of applications. They are commonly used for crack repairs or to provide confining strength within their width. With a design tensile capacity of 35,496 pounds per 12 inches, they offer impressive performance in demanding conditions.
Here’s how they compare to unidirectional rolls:
Type | Strength Characteristics | Applications |
---|---|---|
Bidirectional (BI) | Fibers run in two directions; design tensile capacity of 35,496 lbs per 12”. | Commonly used for crack repairs and providing confining strengths within its width. |
Bidirectional rolls are a great choice when a project requires strength in multiple directions. They are especially useful for repairs and reinforcement in areas prone to stress from various angles.
Pre-preg Carbon Fiber Rolls
Pre-preg carbon fiber rolls are pre-impregnated with resin, offering a perfect balance of fiber and resin content. This optimized ratio results in superior mechanical properties while keeping the material lightweight. These rolls are ideal for high-performance composite designs, such as those used in aerospace or automotive applications.
Some of the key advantages of pre-preg rolls include:
- Higher fiber-to-resin ratio, leading to better mechanical properties and reduced weight
- Consistent quality due to better control over resin content and distribution
- Less waste and environmental impact, as excess resin is removed during manufacturing
- Cleaner and safer working conditions, with minimal resin exposure
Additionally, pre-preg rolls provide enhanced bonding and consolidation of fibers during curing. This results in higher strength, stiffness, and overall performance compared to traditional carbon fiber cloth. While they may cost more upfront, their superior quality and efficiency often make them a worthwhile investment for advanced projects.
Tip: Pre-preg rolls are an excellent choice for projects requiring precision and high performance. Always store them properly to maintain their quality before use.
Other Variants of Carbon Fiber Rolls
Carbon fiber rolls come in many forms, each tailored to specific needs. Beyond unidirectional, bidirectional, and pre-preg options, there are other variants that offer unique benefits. Let’s explore a few of these specialized types.
Woven Carbon Fiber Rolls
Woven carbon fiber rolls feature fibers interlaced in a crisscross pattern. This weaving creates a fabric-like material that balances strength and flexibility. The most common weave patterns include plain weave and twill weave. Plain weave offers a uniform appearance and consistent strength, while twill weave provides a more textured look and slightly better drape.
These rolls are perfect for projects requiring both aesthetics and performance. For example, they’re often used in visible parts of cars, bikes, or even furniture. Their eye-catching pattern adds a sleek, modern touch while maintaining durability.
Hybrid Carbon Fiber Rolls
Hybrid carbon fiber rolls combine carbon fibers with other materials like Kevlar or fiberglass. This blend creates a composite material with unique properties. For instance, adding Kevlar improves impact resistance, while fiberglass reduces cost without sacrificing too much strength.
These rolls are ideal for applications where specific performance characteristics are needed. A good example is protective gear, where the material must absorb impacts while staying lightweight. Hybrid rolls also work well in sports equipment, offering a balance of strength, flexibility, and affordability.
Colored Carbon Fiber Rolls
Colored carbon fiber rolls are a great choice for projects where appearance matters. By incorporating pigments or dyed fibers, manufacturers create rolls in various colors without compromising performance. These rolls maintain the strength and lightweight properties of traditional carbon fiber while adding a pop of color.
They’re popular in custom automotive designs, consumer electronics, and even fashion accessories. Whether it’s a red carbon fiber phone case or a blue accent on a car, these rolls let designers get creative.
Textured Carbon Fiber Rolls
Textured carbon fiber rolls have unique surface finishes, such as matte, glossy, or embossed patterns. These textures enhance the material’s visual appeal and can also improve functionality. For example, an embossed surface might provide better grip or reduce glare.
These rolls are often used in high-end products like luxury watches, dashboards, or architectural elements. They combine style with practicality, making them a favorite for premium designs.
Note: When selecting a carbon fiber roll, consider how these variants align with your project’s goals. Each type offers distinct advantages, so understanding their properties ensures the best results.
Key Factors to Consider When Choosing a Carbon Fiber Roll
Strength and Durability
Strength and durability are two of the most important factors when selecting a carbon fiber roll. The material’s ability to withstand stress and resist wear directly impacts the success of your project. For example, aerospace components often require carbon fiber rolls with high tensile strength to endure extreme forces during flight. Similarly, construction projects may need rolls that can handle heavy loads without cracking or breaking.
When evaluating strength, consider the type of carbon fiber roll. Unidirectional rolls excel in providing strength along a single axis, while bidirectional rolls offer balanced strength in multiple directions. Durability also depends on the resin used in the composite. High-quality resins enhance the material’s resistance to environmental factors like moisture and UV exposure.
Choosing a roll with the right balance of strength and durability ensures your project remains reliable over time. Always match the material’s properties to the demands of your application.
Flexibility and Weight
Flexibility and weight play a crucial role in determining how a carbon fiber roll performs in specific applications. Lightweight materials are essential for projects where reducing overall weight is a priority, such as in automotive or aerospace designs. A lighter carbon fiber roll can improve fuel efficiency in vehicles or enhance the maneuverability of drones.
Flexibility, on the other hand, is vital for projects requiring the material to bend or conform to specific shapes. Woven carbon fiber rolls, for instance, provide a good balance of flexibility and strength, making them ideal for curved surfaces or intricate designs. Pre-preg rolls, while stiffer, can still offer some flexibility depending on the resin content and curing process.
By understanding the flexibility and weight requirements of your project, you can select a carbon fiber roll that meets both functional and performance needs. This ensures the material works seamlessly with your design.
Cost and Availability
Cost and availability often influence the final decision when choosing a carbon fiber roll. The price of carbon fiber typically ranges from 10to10 to 10to20 per pound, depending on the type and quality. Higher-quality rolls, such as pre-preg options, tend to fall at the upper end of this range due to their advanced manufacturing process and superior performance.
Here’s a quick breakdown of how cost correlates with quality:
- Lower-cost rolls: Suitable for less demanding projects, such as DIY or hobbyist applications.
- Mid-range rolls: Ideal for general-purpose use, offering a balance of affordability and performance.
- High-end rolls: Designed for advanced applications, providing exceptional strength, durability, and precision.
Availability can also vary based on the type of roll. Specialized options like hybrid or colored carbon fiber rolls may require sourcing from specific manufacturers. To avoid delays, it’s a good idea to check lead times and stock levels before starting your project.
Balancing cost with performance ensures you get the best value for your investment. Spending a little more upfront on a high-quality roll can save money in the long run by reducing maintenance or replacement costs.
Compatibility with Other Materials
When working on a project, it’s important to think about how a carbon fiber roll interacts with other materials. Compatibility plays a big role in ensuring the final product performs well and lasts longer. If the materials don’t work well together, it can lead to issues like weak bonds, uneven stress distribution, or even failure over time.
One key factor to consider is the adhesive or resin used to bond the carbon fiber roll to other surfaces. Not all adhesives work equally well with carbon fiber. For example, epoxy resins are a popular choice because they create strong, durable bonds. However, the type of resin should match the material it’s bonding to. Metals like aluminum or steel may require surface treatments to improve adhesion, while plastics might need a different approach.
Thermal expansion is another important consideration. Different materials expand and contract at different rates when exposed to temperature changes. If the carbon fiber roll and the other material have mismatched thermal properties, it can cause stress at the bond line. Over time, this stress might lead to cracks or delamination. To avoid this, choose materials with similar thermal expansion rates or use flexible adhesives that can absorb the stress.
Electrical conductivity is also worth thinking about. Carbon fiber is conductive, which can be an advantage or a challenge depending on the project. For example, in electronics, the conductivity of carbon fiber can interfere with circuits if not properly insulated. On the other hand, its conductivity can be useful in applications like electromagnetic shielding. Always check how the carbon fiber roll’s properties align with the needs of your project.
Finally, test the materials together before committing to a full-scale build. Small-scale tests can reveal potential issues and help you make adjustments early. This saves time and money while ensuring the final product meets your expectations.
Tip: Always consult with manufacturers or experts to confirm compatibility. They can provide valuable insights and recommend the best materials for your specific application.
Comparing Carbon Fiber Rolls for Different Applications
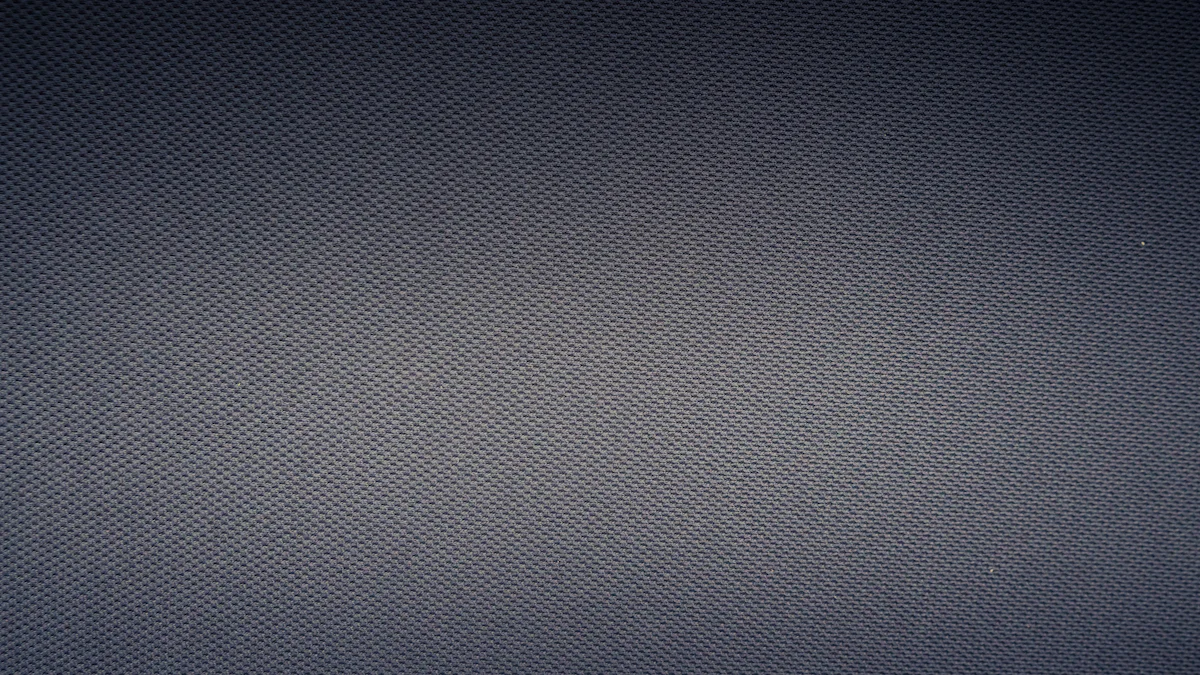
Aerospace and Aviation
Carbon fiber rolls play a vital role in aerospace and aviation projects. Engineers choose this material because it offers unmatched strength and lightness. Compared to steel, carbon fiber is stronger, yet it weighs much less than aluminum. This unique combination allows aircraft to reduce their overall weight by up to 20%. Lighter planes consume less fuel, which saves money and benefits the environment.
Another advantage is the ability to create complex shapes. Carbon fiber rolls make it easier to design aerodynamic structures that reduce drag. This improves fuel efficiency and enhances the aircraft’s performance. Additionally, fewer parts are needed during construction, which simplifies manufacturing and lowers production costs.
These properties make carbon fiber rolls the go-to material for building aircraft bodies, wings, and other critical components. Whether it’s a commercial jet or a spacecraft, the material ensures safety, efficiency, and durability.
Automotive and Motorsports
In the automotive and motorsports industries, carbon fiber rolls have revolutionized vehicle design. Their lightweight nature significantly improves fuel efficiency and overall performance. A lighter car accelerates faster and handles better, which is crucial in competitive motorsports.
The material’s strength-to-weight ratio also enhances safety. Carbon fiber adds structural integrity, making vehicles more resistant to crashes. This property is especially important in race cars, where high speeds demand maximum protection for drivers.
Another benefit is corrosion resistance. Unlike traditional materials, carbon fiber doesn’t rust, which increases a vehicle’s lifespan and reduces maintenance costs. From luxury cars to Formula 1 vehicles, carbon fiber rolls provide the perfect balance of performance, safety, and durability.
DIY and Hobbyist Projects
For DIY enthusiasts and hobbyists, carbon fiber rolls open up endless possibilities. These rolls are easy to work with and offer professional-grade results for small-scale projects. Whether you’re building a custom drone, crafting a unique bicycle frame, or designing a decorative piece, carbon fiber adds a sleek and modern touch.
Its lightweight and flexible nature make it ideal for creative designs. Hobbyists can shape it into intricate forms without compromising strength. Additionally, the material’s durability ensures that finished projects last longer, even with regular use.
Carbon fiber rolls also come in various styles, such as woven or colored options, allowing hobbyists to personalize their creations. With the right tools and a bit of creativity, anyone can achieve impressive results using this versatile material.
Industrial and Construction Applications
Carbon fiber rolls have become a game-changer in industrial and construction projects. Their unique properties make them a top choice for engineers and builders looking to improve performance and efficiency. Let’s explore how these rolls are transforming the industry.
Reinforcing Concrete Structures
Carbon fiber rolls are widely used to strengthen concrete. They provide additional tensile strength, which helps structures resist cracking and deformation. For example, engineers often apply unidirectional carbon fiber rolls to bridges and buildings to reinforce weak points. This method increases load-bearing capacity without adding significant weight.
Did you know? Studies show that carbon fiber reinforcement can extend the lifespan of concrete structures by up to 20 years. This makes it a cost-effective solution for long-term durability.
Repairing and Retrofitting
When it comes to repairing old or damaged structures, carbon fiber rolls are a go-to material. They are lightweight and easy to apply, which reduces labor costs and project timelines. Bidirectional rolls are especially useful for crack repairs, as they provide strength in multiple directions.
Here are some common applications:
- Strengthening aging bridges to meet modern safety standards
- Repairing cracks in walls, columns, and beams
- Retrofitting buildings to withstand earthquakes
These rolls allow engineers to upgrade structures without the need for heavy machinery or extensive demolition.
Building Lightweight Components
In industrial settings, carbon fiber rolls are used to create lightweight yet strong components. For instance, factories use them to build machine parts that need to handle high stress but remain easy to move. This reduces energy consumption and improves operational efficiency.
Tip: Woven carbon fiber rolls are ideal for creating components with complex shapes. Their flexibility makes them easy to mold into intricate designs.
Enhancing Corrosion Resistance
Traditional materials like steel often corrode when exposed to harsh environments. Carbon fiber, however, resists rust and chemical damage. This makes it perfect for projects in coastal areas or chemical plants. For example, hybrid carbon fiber rolls are used to build pipelines and storage tanks that need to withstand corrosive substances.
Material | Corrosion Resistance | Applications |
---|---|---|
Steel | Low | Prone to rust in marine environments |
Carbon Fiber Rolls | High | Ideal for pipelines, tanks, and seawalls |
Improving Energy Efficiency
Carbon fiber rolls also contribute to energy-efficient designs. In construction, they are used to create insulated panels that reduce heat transfer. This helps buildings maintain a stable temperature, lowering heating and cooling costs.
By combining strength, durability, and versatility, carbon fiber rolls have proven to be an invaluable resource in industrial and construction applications. Their ability to adapt to various needs ensures they remain a preferred choice for modern engineering challenges.
Practical Tips for Selecting the Right Carbon Fiber Roll
Consulting Experts or Manufacturers
When choosing a carbon fiber roll, reaching out to experts or manufacturers can save time and effort. These professionals have years of experience and can guide you toward the best option for your project. They understand the technical details, like tensile strength, flexibility, and resin compatibility, which might be hard to figure out on your own.
For example, if you’re working on a lightweight drone, an expert can recommend a roll that balances strength and weight. Manufacturers can also provide detailed specifications and answer questions about performance in specific conditions, like high heat or moisture.
Don’t hesitate to ask for advice. Many manufacturers offer free consultations or technical support. A quick conversation can help you avoid costly mistakes and ensure your project succeeds.
Testing Samples for Suitability
Before committing to a full purchase, testing samples is a smart move. Samples let you see how the material performs in real-world conditions. For instance, you can check if the roll bends easily or if it holds up under stress. This hands-on approach helps you confirm that the carbon fiber roll meets your project’s needs.
Start by ordering small sample sizes from different suppliers. Use these to test key factors like strength, flexibility, and compatibility with adhesives or other materials. If your project involves extreme conditions, like high temperatures or heavy loads, simulate these during testing.
Testing also helps you compare options. You might find that one roll offers better performance or is easier to work with than another. This step ensures you make an informed decision and get the best value for your money.
Tip: Keep notes during testing. Record how each sample performs so you can easily compare results later.
Verifying Manufacturer Reputation
Not all manufacturers deliver the same quality. Verifying a manufacturer’s reputation is crucial to ensure you receive a reliable carbon fiber roll. Start by researching online reviews and testimonials. Look for feedback from customers who used the material for similar projects.
Check if the manufacturer has certifications or awards that prove their expertise. For example, ISO certifications indicate that their products meet international quality standards. You can also ask about their production process. A reputable manufacturer will be transparent about how they make their rolls and the materials they use.
Another good sign is a strong track record. Companies with years of experience are more likely to produce consistent, high-quality products. If possible, visit their facility or request a virtual tour. This gives you a better idea of their capabilities and commitment to quality.
Note: Trustworthy manufacturers often provide warranties or guarantees. This shows confidence in their product and gives you peace of mind.
Choosing the right carbon fiber roll starts with understanding the project’s unique needs. Every detail matters, from the material’s properties to the environment it will face. Balancing key factors ensures the best results:
- Strength and Weight: Match the roll’s strength-to-weight ratio to the project’s demands.
- Flexibility and Durability: Pick a roll that meets the application’s flexibility and durability requirements.
- Cost Considerations: Compare options to find the most cost-effective solution.
For advanced applications, consider modulus types:
- High Modulus (HM): Perfect for maximum stiffness and minimal weight.
- Intermediate Modulus (IM): Offers a balance of stiffness and strength.
- Standard Modulus (SM): Delivers good strength at a lower cost.
Testing samples and consulting experts can simplify the decision-making process. Trusted manufacturers provide reliable materials and guidance, ensuring your project’s success.
FAQ
What is the difference between unidirectional and bidirectional carbon fiber rolls?
Unidirectional rolls have fibers aligned in one direction, offering strength along a single axis. Bidirectional rolls have fibers woven at 90-degree angles, providing balanced strength in multiple directions. Choose based on your project’s structural needs.
Can carbon fiber rolls be cut or shaped easily?
Yes, carbon fiber rolls can be cut and shaped using tools like scissors, rotary cutters, or diamond blades. Always wear protective gear to avoid inhaling dust or fibers during the process.
How do I store pre-preg carbon fiber rolls?
Store pre-preg rolls in a cool, dry place, ideally in a freezer. This prevents the resin from curing prematurely. Follow the manufacturer’s guidelines for storage temperature and shelf life.
Are carbon fiber rolls waterproof?
Yes, carbon fiber rolls are naturally waterproof. However, the resin used in the composite determines the overall water resistance. Use high-quality resins for projects exposed to moisture or water.
Can I paint or coat carbon fiber rolls?
Absolutely! You can paint or coat carbon fiber rolls to enhance their appearance or add protection. Use primers and paints designed for composites to ensure proper adhesion and durability.
What adhesive works best with carbon fiber rolls?
Epoxy adhesives work best for bonding carbon fiber rolls. They create strong, durable bonds and resist environmental factors like heat and moisture. Always test compatibility with other materials in your project.
Are carbon fiber rolls eco-friendly?
Carbon fiber rolls are durable and long-lasting, reducing the need for replacements. While their production isn’t entirely eco-friendly, their lightweight nature improves fuel efficiency in vehicles, indirectly benefiting the environment.
How do I know which carbon fiber roll suits my project?
Consider your project’s requirements, such as strength, flexibility, and environmental conditions. Consult experts or manufacturers for guidance. Testing samples can also help you find the perfect match.
Tip: Always prioritize quality and compatibility to ensure your project’s success.